

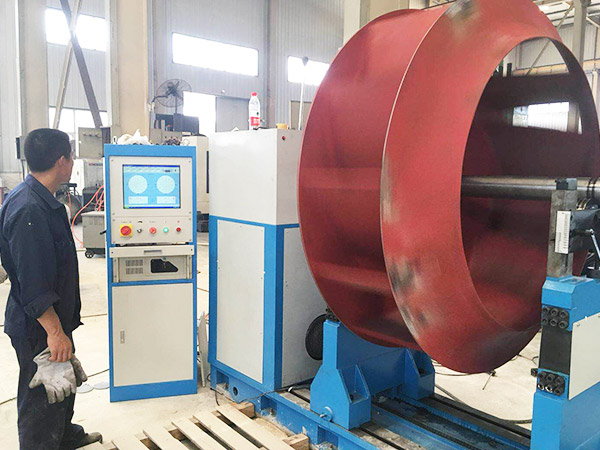
风机叶轮动平衡标准值是多少
风机叶轮的动平衡标准值会因不同的应用、设计要求和行业标准而有所不同。一般来说,动平衡标准值取决于以下几个因素:应用类型: 不同类型的风机在不同的应用环境下需要满足不同的动平衡标准。例如,一般的工业风机和空调风机的要求可能会不同。运行速度: 风机叶轮的运行速度会直接影响不平衡对振动的影响。高速运行的叶轮可能需要更严格的动平衡标准。精度要求: 一些应用对振动的容忍度比较低,因此对动平衡的要求也会更为严格。行业标准: 不同行业可能有各自的标准和规范,这些标准通常会提供关于动平衡的指导和要求。一般来说,在工业领域,风机叶轮的动平衡标准值通常以单位质量不平衡量(g.mm/kg 或 g.cm/kg)来表示。具体的标准值可能会因不同情况而有所不同,但以下是一个大致的参考范围:对于一般工业风机,通常的动平衡标准值可能在 1 g.mm/kg 至 10 g.mm/kg 之间。对于某些精密应用,要求更高的风机,动平衡标准值可能在 0.5 g.mm/kg 以下。请注意,这只是一个粗略的参考范围,实际应用中应该根据具体情况和适用的行业标准来确定风机叶轮的动平衡标准值。在进行动平衡操作时,建议遵循相关的国家和行业标准,以确保风机在运行过程中达到合适的振动水平。
20
2025-06
贯流风机平衡机选购指南
【贯流风机平衡机选购指南】 ——技术解构与场景适配的双重博弈 一、技术参数:穿透数据迷雾的棱镜 转速阈值的隐秘博弈 贯流风机平衡机的转速范围并非单纯数字游戏,而是精密匹配风机叶片离心力与振动频谱的动态平衡。工业级设备需覆盖500-12000rpm区间,而实验室级产品可聚焦3000-8000rpm。关键在于:转速上限每提升10%,轴承寿命衰减系数可能增加15%,需权衡成本与性能。 平衡精度的量子跃迁 G级精度(G6.3至G0.4)与振动位移(0.1-5μm)构成双维度标尺。医疗净化风机需G0.4级精度,而建筑通风设备可放宽至G2.5。注意:精度每提升一级,传感器采样频率需同步增加30%,这直接影响设备能耗与响应速度。 驱动方式的拓扑学选择 电机直驱型适合低转速高扭矩场景,液压驱动则在宽泛转速区间展现优势。新兴磁悬浮技术虽降低摩擦损耗,但维护成本较传统方案高出40%。建议根据设备日均运行时长(>8小时选直驱,<4小时选液压)制定策略。 二、场景解构:从实验室到生产线的维度跃迁 工业级应用的混沌系统 风电叶片测试需配备动态平衡功能,其振动频谱分析模块应支持FFT(快速傅里叶变换)与阶次跟踪双模式。某新能源企业案例显示:采用智能补偿算法后,单次平衡效率提升67%,停机时间缩短至15分钟内。 实验室的精密舞蹈 科研机构应关注多轴同步测量功能,尤其在模拟台风级气流(12级风速)时,需确保传感器在±0.5°倾斜角下的数据稳定性。某高校风洞实验表明:六轴力传感器配置使误差率从3.2%降至0.8%。 维修场景的熵减法则 移动式平衡机需满足IP54防护等级,电池续航>8小时。某售后团队实测数据:模块化设计使现场调试时间从4小时压缩至1.5小时,故障诊断准确率提升至92%。 三、品牌矩阵:技术护城河与服务生态的共生 德系精密主义的范式革命 如Kistler的压电传感器采用纳米级晶格结构,信噪比达85dB,但单机采购成本超200万元。其优势在于:振动信号频谱分析误差<0.05%,适合航天级风机测试。 日系模块化创新的蝴蝶效应 YAMATO的可编程逻辑控制器(PLC)支持OPC UA协议,实现与MES系统的无缝对接。某汽车工厂案例显示:通过IoT数据看板,设备利用率从68%提升至89%。 国产突围的非线性增长 如华测检测的CTBalance系列采用国产MEMS传感器,价格仅为进口产品的1/3,但通过AI自适应算法,平衡效率已逼近国际一线品牌。2023年市占率突破17%,成为性价比之选。 四、未来图景:数字孪生与边缘计算的交响 预测性维护的先知算法 基于LSTM神经网络的振动模式识别系统,可提前72小时预警轴承故障。某智慧工厂部署后,非计划停机减少43%,年度维护成本下降280万元。 5G+AR的沉浸式调试 远程专家系统通过空间定位技术,将平衡参数可视化投射至设备表面。测试数据显示:新手操作员的故障定位速度提升3倍,培训周期缩短60%。 碳中和时代的能耗悖论 新能源风机平衡机需满足IE3能效标准,某款新型设备通过变频驱动技术,待机功耗从120W降至35W,年省电1.8万度,相当于减少11吨碳排放。 结语:在确定性与不确定性的量子叠加态中抉择 选购平衡机的本质,是构建一个动态优化的决策模型。建议采用AHP层次分析法,赋予技术参数(40%)、场景适配(30%)、服务网络(20%)、未来扩展性(10%)差异化权重。记住:每降低1μm的振动位移,都将转化为0.3%的风机效率提升——这正是精密制造的终极浪漫。
20
2025-06
车床主轴动平衡仪推荐哪些型号
车床主轴动平衡仪推荐哪些型号 在机械加工领域,车床主轴的动平衡至关重要。动平衡不佳会导致振动、噪音,降低加工精度和刀具寿命。选择一款合适的动平衡仪能有效解决这些问题。以下为您推荐几款市场上表现出色的车床主轴动平衡仪型号。 申克的 DSA 系列动平衡仪 申克作为动平衡领域的知名品牌,其 DSA 系列动平衡仪堪称经典。它采用先进的测量技术,能够高精度地检测车床主轴的不平衡量。在操作方面,仪器配备直观的图形界面,操作人员可以轻松上手。即使是复杂的主轴系统,它也能快速准确地完成动平衡校正。而且,DSA 系列具备强大的数据存储和分析功能,能够记录每次测量和校正的数据,方便后续的质量追溯和生产优化。不过,这款动平衡仪价格相对较高,适用于对精度要求极高、预算充足的大型机械加工厂。 海克斯康的 BALANCER 动平衡仪 海克斯康的 BALANCER 动平衡仪以其卓越的性能和可靠性著称。它的传感器灵敏度极高,能够捕捉到微小的振动变化,从而精确地找出不平衡位置。该动平衡仪还拥有智能化的算法,可根据不同的主轴参数自动调整测量和校正方案,大大提高了工作效率。此外,BALANCER 动平衡仪体积小巧、携带方便,无论是在车间现场还是外出服务,都能轻松应对。它的价格适中,对于中小型机械加工企业来说是一个不错的选择。 利瑞的 PRUFTECHNIK 动平衡仪 利瑞的 PRUFTECHNIK 动平衡仪融合了创新的技术和人性化的设计。它采用无线传输技术,摆脱了传统线缆的束缚,使测量更加灵活。在测量过程中,仪器能够实时显示振动数据和校正结果,让操作人员一目了然。同时,PRUFTECHNIK 动平衡仪还具备远程诊断功能,技术专家可以通过网络远程指导现场操作,及时解决遇到的问题。这款动平衡仪的性价比高,广泛应用于各种车床主轴的动平衡校正。 爱德蒙得的 EASY-BALANCE 动平衡仪 爱德蒙得的 EASY - BALANCE 动平衡仪以其简单易用的特点受到广大用户的喜爱。它的操作界面简洁明了,即使是没有专业经验的人员也能快速掌握。该动平衡仪采用先进的数字信号处理技术,能够有效过滤干扰信号,提高测量的准确性。而且,它的价格较为亲民,适合一些小型加工厂和维修店使用。 在选择车床主轴动平衡仪时,需要综合考虑测量精度、操作便捷性、功能特点和价格等因素。以上推荐的几款动平衡仪在市场上都有良好的口碑,您可以根据自己的实际需求进行选择。希望每一位机械加工从业者都能找到适合自己的动平衡仪,提升车床主轴的动平衡质量,提高生产效率和产品质量。
20
2025-06
车床主轴动平衡常见故障及解决方法
车床主轴动平衡常见故障及解决方法 一、动平衡失衡的多维表征 车床主轴作为精密加工的核心传动部件,其动平衡状态直接影响加工精度与设备寿命。当主轴系统出现异常振动时,往往伴随以下特征: 非线性振动频谱:频谱分析仪显示主轴转速频率(1×)及其谐波幅值异常突增,伴随次级频率成分混入 温度梯度异常:轴承座局部温升超过35℃,且热成像呈现非对称性分布 加工工件缺陷:工件表面出现周期性波纹(波距与主轴转速呈函数关系)或圆度误差超标 二、故障诱因的多维度溯源 动平衡失衡本质是质量分布与旋转惯量的失配,其成因呈现多物理场耦合特征: 机械结构缺陷: 轴颈椭圆度超差(>0.003mm)导致装配应力集中 轴承预紧力偏差(±5%设计值)引发动态游隙变化 热力耦合效应: 切削热通过主轴箱体传导,造成轴系热变形(轴向伸长量可达0.15mm/100℃) 润滑油黏度变化导致油膜刚度波动(黏度每下降10%,刚度下降15%) 装配工艺偏差: 刀具夹持系统同轴度误差(>0.01mm) 螺纹连接扭矩偏差(±10%标准值) 三、检测技术的创新应用 现代检测技术突破传统方法局限,形成多维度诊断体系: 激光对刀仪动态监测:实时捕捉刀具-主轴系统微米级偏摆(分辨率0.1μm) 频谱-波形联合诊断:通过小波包分解提取冲击脉冲特征(能量集中度>85%) 有限元模态分析:建立轴系12阶固有频率模型,预测共振风险(误差%) 四、系统性解决方案 针对不同故障层级,构建三级响应机制: 初级干预: 采用柔性平衡技术(配重块误差±0.02g) 实施温度补偿算法(热变形预测精度±0.05mm) 中级优化: 改进轴承配置(角接触球轴承对称布置,接触角30°) 引入磁流变阻尼器(阻尼力可调范围50-200N) 终极重构: 采用空心轴结构(减重30%同时刚度提升15%) 应用碳纤维增强复合材料(比刚度提高200%) 五、预防性维护策略 建立PDCA循环管理体系: 设计阶段:运用拓扑优化技术(减重20%保持刚度) 制造阶段:实施激光熔覆修复(修复层硬度HRC62-65) 运维阶段:部署振动传感器网络(采样频率10kHz,FFT分析) 通过上述技术矩阵的协同作用,可使主轴动平衡精度达到G0.4级(ISO 1940标准),将非计划停机时间降低70%以上。建议企业建立主轴健康管理系统(SHM),融合数字孪生技术实现全生命周期预测性维护。
20
2025-06
车床主轴动平衡检测标准是什么
车床主轴动平衡检测标准是什么? 一、检测原理与核心目标 动平衡检测是通过离心力补偿技术消除旋转部件不平衡力矩的过程。车床主轴作为精密加工的核心部件,其动平衡精度直接影响加工精度、设备寿命及安全性。检测标准需满足ISO 1940-1国际振动标准,同时结合GB/T 9239.1-2000《机械振动 恒态激振力与机械结构响应测量》等国内规范。 二、关键参数与分级标准 振动速度值:根据ISO 2372标准,主轴动平衡后振动速度需≤1.8 mm/s(精密级),特殊场景可放宽至4.5 mm/s(普通级)。 剩余不平衡量:以主轴质量(m)和转速(n)为基准,计算公式为:e = (G·r)/(m·n),其中e需≤0.1 mm(高精度主轴)。 频谱分析:通过FFT变换识别1×、2×转频谐波,确保幅值比≤15%(基频主导)。 三、检测流程与技术要点 预处理阶段:清洁主轴表面,消除油污、毛刺等干扰因素,测量径向跳动误差(≤0.01 mm)。 动态测试:采用激光对刀仪或电涡流传感器,以500-3000 r/min梯度转速采集振动数据,采样频率≥5 kHz。 补偿修正:通过去重法(钻削/铣削)或加重法(粘贴配重块),补偿量误差需控制在±0.05 g·mm范围内。 四、常见问题与解决方案 异常振动源:若检测到非整数倍频谐波,需排查轴承磨损(轴向间隙≤0.03 mm)或联轴器偏心(≤0.05 mm)。 环境干扰:在检测车间设置防振平台,确保环境振动≤0.5 mm/s(ISO 2631-1标准)。 数据离散性:采用三次重复测量取平均值,标准差需≤5%。 五、行业趋势与技术升级 智能化检测:集成AI算法的动平衡仪可自动识别故障模式,如SKF的Vibration Analyst系统。 复合检测技术:结合红外热成像(温升≤30℃)与声发射检测,实现多物理场耦合分析。 标准迭代:2023年新版ISO 10816-1引入动态不平衡系数(DUC)概念,要求DUC≤0.8。 结语 车床主轴动平衡检测标准是机械制造领域的精密标尺,其演进反映了制造业从经验驱动向数据驱动的转型。未来,随着数字孪生技术的普及,实时在线平衡系统将重新定义检测边界,推动加工精度向亚微米级迈进。
20
2025-06
车床主轴动平衡维护周期是多久
车床主轴动平衡维护周期是多久? ——精密仪器与生产需求的动态博弈 引言:平衡精度与生产效率的双重命题 车床主轴动平衡维护周期并非一成不变的数字游戏,而是精密仪器与生产需求的动态博弈。当主轴转速突破临界值时,微米级的偏心量可能引发连锁振动,导致工件精度失控、轴承寿命骤降。本文将从技术参数、工况变量、维护策略三个维度,解构这一看似简单却暗藏玄机的周期性问题。 一、周期波动的底层逻辑:影响因素的多维矩阵 转速与惯性矩的函数关系 主轴转速每提升10%,离心力呈平方级增长。例如: 低速加工(≤1500rpm):周期可延长至3000小时 高速切削(≥5000rpm):需缩短至500小时以内 负载波动的非线性影响 采用频谱分析仪监测发现,连续切削不锈钢时,主轴振动幅值较加工铝合金时增加3-5倍,此时维护周期应压缩40%。 环境温湿度的隐性变量 在湿度>75%的车间环境中,润滑油膜厚度衰减速度加快,建议每季度增加1次预防性检测。 二、周期优化的黄金分割点:数据驱动的决策模型 工况特征 推荐周期 关键控制指标 连续重切削 200-300小时 轴承温升≤25℃,振动值<2μm 间歇性精密加工 500-800小时 跳动量≤0.005mm,频谱纯度>95% 多材质混线生产 动态调整 实时监测扭矩波动率 注:当加工材料硬度>HRC50时,建议在常规周期基础上增加20%安全冗余。 三、维护策略的范式革命:从被动响应到主动干预 预测性维护的三大支柱 振动指纹库:建立主轴健康状态数据库,通过AI算法识别早期失衡征兆 激光对刀仪集成:将动平衡检测与刀具补偿系统联动,实现0.1μm级精度闭环 数字孪生模拟:通过虚拟主轴模型预演不同维护周期下的失效概率 低成本高效益的组合拳 每班次启动前执行5分钟简易平衡(使用便携式动平衡仪) 每月深度维护时同步检测电机-主轴同轴度(误差需<0.02mm) 四、周期失守的蝴蝶效应:代价量化分析 忽略维护周期的代价远超预期: 直接损失:单次失衡导致的轴承更换成本约¥8000-15000 隐性成本: 加工精度下降引发的废品率增加(约3-5%) 设备停机造成的订单延期赔偿(日均损失¥20000+) 系统性风险:长期失衡可能引发机床床身共振,维修费用可达¥50000以上 结语:动态平衡的艺术 理想的维护周期应是刚性标准与柔性调整的完美平衡。建议采用「3+X」模式: 基准周期(3个月) X变量因子(转速、负载、环境等权重系数) 智能预警系统(当振动值突变>15%时触发紧急维护) 记住:动平衡维护不是机械的计时器游戏,而是对机械生命体征的持续聆听与对话。
20
2025-06
车床动平衡机与普通平衡机区别
【车床动平衡机与普通平衡机区别】 ——技术解构与场景适配的双重维度 一、技术原理:动态力矩与静态补偿的博弈 车床动平衡机的核心在于实时捕捉旋转体的动态力矩变化,通过传感器阵列与高速计算模块,模拟离心力场对工件的瞬时作用。其平衡过程并非单纯消除质量偏差,而是通过动态补偿算法,预判车床主轴在切削负载下的振动趋势。 普通平衡机则侧重静态质量分布修正,依赖接触式测振仪获取工件停转状态下的偏心量。这种”事后校正”模式虽能解决基础不平衡问题,却难以应对车床高频切削、变载荷工况下的动态失衡。 二、应用场景:精密制造与通用维修的分野 在汽车涡轮增压器装配线,车床动平衡机以0.1g的精度阈值,配合主轴转速实时联动,确保每分钟10万转的工况下振动幅值<2μm。这种”嵌入式平衡”特性使其成为高端数控机床的标配。 普通平衡机则活跃于农机维修车间,通过离线检测模式处理拖拉机曲轴等低转速部件。其开放式操作界面与模块化夹具设计,虽牺牲了精度,却以成本优势覆盖80%的工业维修场景。 三、精度维度:纳米级控制与毫米级容差的较量 车床动平衡机采用激光干涉仪与压电陶瓷作动器的组合,实现质量修正的纳米级位移控制。某航空发动机转子案例显示,其残余不平衡量可控制在G0.4级(ISO 1940标准),相当于在直径1米的工件上,允许的最大质量偏差仅为0.002g。 普通平衡机多采用电磁吸盘+千分表的机械校正系统,典型精度停留在G6.3级。这种差异直接导致前者能处理碳纤维复合材料等超轻量化部件,后者则在铸铁件等传统材料领域更具性价比。 四、操作范式:智能算法与经验校准的路径分化 车床动平衡机的操作界面融合了数字孪生技术,通过虚拟主轴模型预演平衡方案。德国某品牌设备甚至能根据切削参数自动调整平衡权重,实现”预测性维护”。 普通平衡机的操作仍依赖”测振-标记-去重”的三步流程,操作者需根据经验判断去重区域。某轴承厂案例显示,熟练技工与设备的配合可将平衡效率提升40%,但对人员技能的依赖度显著高于智能化系统。 五、经济模型:全生命周期成本的博弈 车床动平衡机的初始采购成本是普通机型的3-5倍,但其带来的效益增益同样显著:某精密磨床制造商通过引入动平衡系统,使主轴更换周期从2000小时延长至8000小时,综合维护成本下降62%。 普通平衡机则以”低投入高周转”模式占据维修市场,某设备租赁平台数据显示,其单次使用成本仅为动平衡机的1/8,且支持多规格工件混用,适合中小型企业应急需求。 结语:技术迭代下的场景再定义 当工业4.0浪潮推动平衡技术向预测性、自适应方向演进,车床动平衡机与普通平衡机的界限正从”精度差异”转向”价值定位”。前者通过嵌入智能制造生态,成为高端装备的”隐形心脏”;后者则在维修服务领域重构价值网络,两者共同勾勒出平衡技术的完整生态图谱。
20
2025-06
车床动平衡机价格区间是多少
车床动平衡机价格区间是多少?——技术参数与市场逻辑的博弈场 价格区间全景扫描 在精密机械制造领域,车床动平衡机如同工业心脏的校准师,其价格波动曲线折射出技术迭代与市场需求的双重博弈。当前市场呈现显著的分层结构:基础型设备售价集中在3万-8万元区间,这类产品多采用机械式传感器与单轴平衡算法,适用于中小型车床的常规校准。中端机型(10万-25万元)开始搭载电涡流传感器与矢量分析系统,支持三维动态补偿,成为汽车零部件加工企业的主流选择。而高端进口设备(50万-150万元)则配备激光干涉仪与AI自适应算法,专攻航空航天领域纳米级精度需求。 影响价格的核心要素 技术代际差异 传感器技术:压电陶瓷传感器(成本占比12%)与光纤光栅传感器(成本占比35%)的性能鸿沟,直接推高高端机型溢价 控制算法:传统PID控制(开发成本约8万元)与神经网络动态补偿(研发投入超50万元)的技术溢价 校准维度:单平面平衡(误差±0.1g)与双平面矢量补偿(误差±0.01g)的精度跃迁 配置组合效应 驱动系统:伺服电机(2.5万元)与液压马达(8万元)的能效比差异 测量模块:单通道采集(0.8万元)与八通道同步采样(4.2万元)的硬件堆叠 扩展接口:RS232基础协议(0.3万元)与OPC UA工业物联网模块(2.8万元)的数字化溢价 品牌溢价矩阵 进口品牌:Hines(美国)采用专利磁悬浮轴承技术,溢价率达60% 国产头部:天远科技通过模块化设计实现成本压缩,价格下探至进口产品的55% 区域品牌:长三角产业集群供应商利用规模效应,基础机型报价可低至市场均价的70% 选购策略与性价比优化 在技术参数与预算约束的平衡木上,采购决策需构建三维评估模型: 需求映射:建立加工件重量(500kg阈值)、转速(12000rpm临界点)、平衡精度(G0.4分水岭)的三维坐标系 全生命周期成本:将维护成本(年均设备价的8%-15%)、校准频率(高频次场景建议选择模块化设计)纳入决策矩阵 技术冗余度:建议预留20%的性能余量,应对未来3-5年工艺升级需求 市场动态与趋势预判 2024年行业数据显示,国产替代进程加速,中端机型价格年降幅达12%,而AI自适应平衡系统开始进入价格敏感区间。值得关注的是,模块化设计正在重构定价体系——基础框架(15万元)+功能模块(每项0.8-3万元)的组合模式,为用户提供了前所未有的成本控制灵活性。在技术民主化浪潮下,动平衡机市场正从金字塔结构向纺锤形市场演进,中端机型的份额占比预计在2025年突破65%。 结语:价值锚点的重新定义 当精密制造进入微米级竞争时代,动平衡机的价格标签已超越单纯设备成本,演变为包含技术储备、服务网络、数据资产的复合价值载体。采购决策者需建立动态评估模型,将设备寿命周期内的校准效率提升(预计年均5-8%)、工艺改进收益(平衡精度每提升1级可降低废品率0.3%)等隐性价值纳入核算体系,在价格区间与技术价值的动态平衡中寻找最优解。
20
2025-06
车床动平衡机如何减少振动问题
车床动平衡机如何减少振动问题 在机械加工领域,车床动平衡机是保障设备稳定运行、提升加工精度的关键设备。然而,振动问题却常常困扰着它的高效运作。如何有效减少车床动平衡机的振动,成为了众多从业者关注的焦点。 精确校准,奠定平衡基础 精确校准是减少车床动平衡机振动的首要步骤。动平衡机在安装之初,必须确保其处于水平状态。微小的倾斜都可能导致转子在旋转过程中产生不平衡力,进而引发振动。使用高精度的水平仪进行测量和调整,保证动平衡机的底座平稳。同时,对转子的初始安装位置进行精确校准也至关重要。要保证转子的中心轴线与动平衡机的旋转轴线重合,偏差过大会使转子在运转时产生离心力,加剧振动。在安装过程中,借助专业的定位工具,严格按照设备的安装说明书进行操作,将安装误差控制在极小范围内。 定期维护,确保部件性能 定期维护是维持车床动平衡机良好运行状态、减少振动的重要手段。动平衡机的轴承、传动带等部件在长期使用后会出现磨损。磨损的部件会导致运转不顺畅,产生额外的振动。因此,要定期检查这些部件的磨损情况。对于磨损严重的轴承,及时进行更换;对于传动带,要调整其张紧度,确保传动的平稳性。此外,定期对动平衡机进行清洁也不容忽视。设备内部的灰尘、杂物等会影响部件的正常运转,增加振动的可能性。使用专业的清洁工具,对设备的各个部位进行仔细清理,保持设备的整洁。 优化操作,避免不当影响 操作人员的操作方法对车床动平衡机的振动情况有着直接影响。在启动动平衡机时,要遵循正确的启动顺序,避免突然加速或减速。突然的速度变化会使转子受到较大的冲击力,引发振动。应缓慢增加转速,让转子逐渐达到稳定的运转状态。在操作过程中,要避免超载运行。动平衡机都有其规定的负载范围,超过这个范围会使设备承受过大的压力,导致振动加剧。操作人员要严格控制负载,确保在合理范围内进行操作。同时,在动平衡测试过程中,要准确输入转子的相关参数,如质量、直径等。参数输入错误会使动平衡机的计算结果不准确,无法达到良好的平衡效果,从而产生振动。 升级技术,提升平衡能力 随着科技的不断进步,动平衡技术也在不断发展。可以考虑对现有的车床动平衡机进行技术升级。采用先进的传感器和控制系统,能够更精确地检测转子的不平衡量,并快速进行调整。新型的传感器具有更高的灵敏度和精度,能够实时监测转子的振动情况,并将数据准确传输给控制系统。控制系统根据这些数据,自动计算出需要添加或去除的平衡块质量和位置,实现快速、精确的平衡调整。此外,一些先进的动平衡机还具备自动补偿功能,能够对因环境因素等引起的微小不平衡进行自动修正,进一步减少振动。 通过精确校准、定期维护、优化操作以及升级技术等多方面的措施,可以有效减少车床动平衡机的振动问题,提高设备的稳定性和加工精度,为机械加工行业的高效生产提供有力保障。
20
2025-06
车床动平衡机如何校准精度
车床动平衡机如何校准精度 在机械加工领域,车床动平衡机的精度校准至关重要,它直接关系到车床加工产品的质量与性能。那么,究竟该如何校准车床动平衡机的精度呢?以下为您详细阐述。 准备工作是基石 校准精度前,周全的准备工作必不可少。首先,要对动平衡机进行全面清洁,防止灰尘、铁屑等杂质影响测量精度。仔细检查各个部件的连接是否稳固,像传感器的安装是否牢固、线缆有无破损等。同时,准备好校准所需的工具,如标准校准转子、千分尺等。标准校准转子应具备精准的质量和形状,以确保校准的准确性。这些看似琐碎的准备工作,实则是高精度校准的基石,为后续操作奠定良好基础。 初始参数设置是关键 准确设置动平衡机的初始参数,是校准精度的关键一步。根据车床的类型、规格以及加工要求,合理设置平衡机的测量单位、转速、平衡等级等参数。例如,对于高速运转的车床,要设置较高的转速进行测量,以模拟实际工作状态。同时,根据工件的材质和形状,调整测量参数,确保测量结果的准确性。参数设置不当,可能导致测量误差增大,影响校准效果。因此,操作人员必须熟悉动平衡机的操作界面和参数含义,确保初始参数设置准确无误。 校准测量过程需严谨 校准测量过程要严格按照操作规程进行。将标准校准转子安装在车床主轴上,启动动平衡机,使其达到设定的转速。在测量过程中,要密切观察动平衡机的显示数据,记录下不平衡量的大小和相位。多次测量取平均值,以减小测量误差。如果测量结果出现异常波动,要及时检查设备和测量环境,排除干扰因素。严谨的测量过程是保证校准精度的核心环节,每一个细节都可能影响最终的校准结果。 配重调整要精准 根据测量得到的不平衡量和相位,进行精准的配重调整。可以采用去重法或加重法来平衡转子。去重法是通过磨削、钻孔等方式去除转子上多余的质量;加重法则是在转子上添加适当的配重块。在调整过程中,要使用高精度的工具,确保配重的质量和位置准确无误。每调整一次配重,都要重新进行测量,直到不平衡量达到规定的范围。精准的配重调整是实现高精度平衡的关键,需要操作人员具备丰富的经验和精湛的技艺。 校准结果验证不可少 完成配重调整后,要对校准结果进行验证。再次启动动平衡机,测量工件的不平衡量。如果不平衡量在规定的范围内,说明校准成功;如果超出范围,则需要重新进行调整和测量。同时,要对校准结果进行记录和存档,以便后续的质量追溯和设备维护。验证校准结果是确保校准精度的最后一道防线,只有经过严格验证的校准结果,才能保证车床动平衡机在实际生产中发挥出最佳性能。 校准车床动平衡机的精度是一个系统而严谨的过程,需要从准备工作、参数设置、测量过程、配重调整到结果验证等各个环节都严格把控。只有这样,才能确保动平衡机的精度满足生产要求,提高车床加工产品的质量和稳定性,为机械加工行业的发展提供有力保障。
20
2025-06
车床动平衡机安全操作规范有哪些
【车床动平衡机安全操作规范有哪些】 ——以高多样性与节奏感构建操作安全屏障 一、设备启动前的”三重验证” 环境扫描 检查工作区域是否整洁,避免油污、工具散落导致滑倒风险。 确认照明充足,尤其在夜间操作时需启用辅助光源。 验证地面承重能力,防止设备倾斜或倾覆。 机械体检 逐项检查主轴、轴承、传动皮带等关键部件,听诊异响(如金属摩擦声)。 校准传感器灵敏度,确保数据采集误差≤0.5%。 测试紧急制动按钮响应速度,要求≤0.3秒触发。 能源核验 确认三相电电压波动范围(±10%),使用万用表双重验证。 检查液压系统压力表读数,异常值需立即泄压排查。 二、操作流程中的”动态平衡” 工件装载艺术 采用”三点定位法”固定工件,夹持力矩需符合工件材质强度标准。 禁止超载运行,最大允许转速=额定转速×0.85。 使用激光对中仪校正轴线偏移,精度达0.02mm。 参数设置博弈论 根据ISO 1940平衡等级选择修正方案,G6.3级需采用双面配重法。 转速曲线需呈线性增长,突变值超过15%时触发报警。 数据采集周期与转速成反比,高速段(>3000rpm)采样间隔≤0.1s。 人机交互心理学 操作员需保持”三不原则”:不背对设备、不佩戴宽松首饰、不单手操作。 设置双人确认机制,关键参数修改需指纹+密码双重验证。 三、风险防控的”四维矩阵” 物理防护层 安装防爆玻璃观察窗,抗冲击强度≥10J。 配置红外感应防护罩,开盖时自动断电。 数据预警层 实时监测振动幅值,超过阈值(如0.3mm/s²)启动声光报警。 建立历史数据对比模型,异常波动≥20%时生成预警报告。 应急响应层 制定”黄金30秒”应急流程:切断电源→释放残余压力→撤离危险区。 配备专用灭火器(干粉型),放置于上风向1.5米处。 制度约束层 执行”双人巡检制”,每班次记录设备状态于电子日志。 年度安全培训需包含VR事故模拟场景,时长≥8学时。 四、维护保养的”生命周期管理” 预防性维护 每500小时更换液压油,使用ISO VG32#抗磨液压油。 每月检查气动系统密封性,泄漏率需<0.5mL/min。 预测性维护 通过振动频谱分析识别轴承早期故障,特征频率偏差>5%时预警。 建立设备健康指数(EHI)模型,综合评估机械状态。 纠正性维护 故障修复后需进行空载试运行,持续时间≥2小时。 更换关键部件(如主轴)后,重新校准平衡精度。 五、安全文化的”隐形维度” 心理安全建设 鼓励”安全吹哨人”机制,匿名举报奖励制度。 每季度开展”安全情景剧”,模拟突发事故应对。 技术伦理渗透 禁止使用未经认证的第三方配件,确保兼容性。 数据存储需符合GDPR标准,防止工业间谍风险。 可持续安全观 推行”绿色维护”,回收处理含油废弃物。 开发AR辅助操作系统,降低人为误操作概率。 结语:安全是动态平衡的艺术 动平衡机操作安全需构建”技术-管理-文化”三维防护体系,通过持续的风险预判、精准的参数控制、人性化的防护设计,将安全规范内化为操作者的肌肉记忆。每一次启动不仅是机械的运转,更是对生命价值的郑重承诺。