

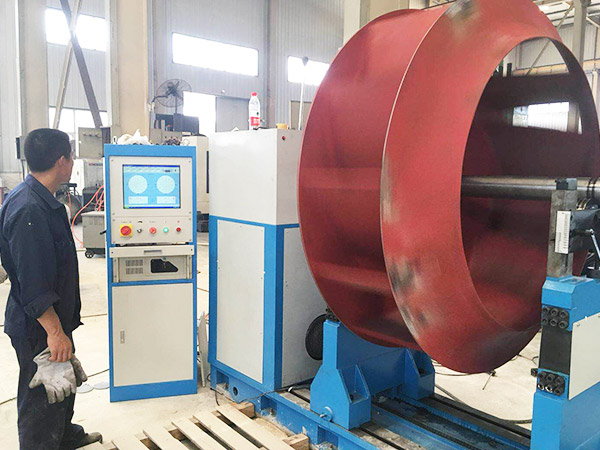
风机叶轮动平衡标准值是多少
风机叶轮的动平衡标准值会因不同的应用、设计要求和行业标准而有所不同。一般来说,动平衡标准值取决于以下几个因素:应用类型: 不同类型的风机在不同的应用环境下需要满足不同的动平衡标准。例如,一般的工业风机和空调风机的要求可能会不同。运行速度: 风机叶轮的运行速度会直接影响不平衡对振动的影响。高速运行的叶轮可能需要更严格的动平衡标准。精度要求: 一些应用对振动的容忍度比较低,因此对动平衡的要求也会更为严格。行业标准: 不同行业可能有各自的标准和规范,这些标准通常会提供关于动平衡的指导和要求。一般来说,在工业领域,风机叶轮的动平衡标准值通常以单位质量不平衡量(g.mm/kg 或 g.cm/kg)来表示。具体的标准值可能会因不同情况而有所不同,但以下是一个大致的参考范围:对于一般工业风机,通常的动平衡标准值可能在 1 g.mm/kg 至 10 g.mm/kg 之间。对于某些精密应用,要求更高的风机,动平衡标准值可能在 0.5 g.mm/kg 以下。请注意,这只是一个粗略的参考范围,实际应用中应该根据具体情况和适用的行业标准来确定风机叶轮的动平衡标准值。在进行动平衡操作时,建议遵循相关的国家和行业标准,以确保风机在运行过程中达到合适的振动水平。
23
2025-06
如何减少校验转子的误差和校正偏差
如何减少校验转子的误差和校正偏差 一、误差溯源:解构转子系统的复杂性 校验转子的误差如同精密齿轮间的微小摩擦,其根源往往隐藏在机械、环境与操作的多重交互中。机械误差包括转子安装面的微观形貌偏差、轴承预紧力的非线性衰减,以及联轴器对中精度的动态漂移。环境误差则源于温度梯度引发的材料热膨胀系数差异,以及振动台底座与地面耦合的共振效应。人为误差则体现在传感器标定阈值的主观判断,或是频谱分析时对谐波成分的误判。 解决方案:建立误差树状模型,通过有限元仿真预判关键敏感点,例如对转子-轴承系统进行模态分析,锁定一阶临界转速附近的误差放大区。 二、校验技术革新:从静态到动态的范式跃迁 传统静平衡法如同用放大镜观察沙粒,而现代动平衡技术则需构建多维度的动态感知网络。频谱分析需结合时频域联合诊断,利用小波包分解提取非平稳振动信号中的瞬态冲击特征;相位补偿应引入自适应滤波算法,实时修正因转速波动导致的相位偏移。 创新实践:某航空发动机厂商采用激光陀螺仪与压电传感器的异构融合,将径向振动分辨率提升至0.1μm级,同时通过数字孪生技术实现虚拟校正与物理校正的闭环迭代。 三、动态补偿策略:构建误差自愈生态系统 误差校正不应是线性的“测量-修正”循环,而需演化为具备自适应能力的智能系统。主动磁轴承可实时调整承载力矩,抵消因转子热变形引发的周期性不平衡;压电作动器阵列则通过分布式力控制,在毫秒级响应中重构转子质量分布。 案例:某高速机床主轴采用模糊PID控制算法,将残余不平衡量从ISO G2.5级压缩至G0.4级,同时将校正周期缩短60%。 四、数据融合方法:突破传感器的感知边界 单一传感器如同盲人摸象,多源数据融合方能还原转子系统的全息图景。多物理场耦合技术同步采集振动、温度、应变数据,通过贝叶斯网络建立误差传播模型;迁移学习框架则将历史校正数据转化为先验知识,指导新转子的快速校正。 技术突破:某研究所开发的异构传感器数据对齐算法,成功消除因安装位置偏差导致的15%系统误差,使校正精度提升至0.05mm·kg。 五、质量控制体系:从被动修正到主动预防 误差控制需嵌入全生命周期管理。标准化流程应细化至扭矩扳手的校验周期与激光校表仪的环境温控参数;人员培训需融合虚拟现实技术,模拟极端工况下的应急校正场景;设备维护则要建立基于振动特征的预测性维护模型,避免因电机轴承磨损引发的连锁误差。 管理创新:某汽车生产线引入误差追溯区块链系统,实现从毛坯铸造到最终校正的全链路可追溯,将批次不良率降低至0.3%以下。 结语:误差控制的哲学维度 校验转子的误差与校正偏差,本质是确定性与不确定性的永恒博弈。唯有将工程思维升维至系统论高度,融合机械精密性、算法智能性与管理预见性,方能在混沌中构建动态平衡的秩序。这不仅是技术的突破,更是对复杂系统控制哲学的深刻诠释。
23
2025-06
如何判断主轴是否需要现场动平衡
如何判断主轴是否需要现场动平衡 在工业生产的众多领域中,主轴作为机械设备的核心部件,其运行的稳定性直接关乎到整个设备的性能与寿命。而现场动平衡是保障主轴稳定运行的关键技术手段。那么,怎样判断主轴是否需要进行现场动平衡呢?下面我们从多个方面进行分析。 振动监测 振动是判断主轴运行状态的重要指标。当主轴在运转过程中,我们可以使用专业的振动监测仪器来实时获取振动数据。若振动的幅度超出了设备的正常运行范围,这很可能预示着主轴存在不平衡问题。一般来说,轻微的振动或许是由正常的机械运转导致,但当振动呈现出持续增大的趋势,且在不同的转速下都表现出异常时,就需要引起我们的高度警惕了。 此外,振动的频率也能为我们提供重要线索。如果振动频率与主轴的旋转频率存在特定的关联,例如出现了整数倍的关系,那么这极有可能是由于主轴的不平衡所引发的共振现象。一旦发现此类情况,就有必要考虑对主轴进行现场动平衡处理。 噪音分析 主轴在正常运行时,发出的声音通常是平稳且有规律的。然而,当主轴出现不平衡时,就会产生异常的噪音。这些噪音的特点往往是尖锐、刺耳,与正常运行时的声音截然不同。我们可以通过仔细聆听主轴运转时的声音,来初步判断其是否存在问题。 若在设备运行过程中,听到了明显的异常噪音,并且随着转速的提高,噪音变得更加剧烈,那么这很可能是主轴不平衡导致的。因为不平衡的主轴会在高速旋转时产生额外的冲击力,进而引发噪音的增大。此时,对主轴进行现场动平衡检测是非常必要的。 加工精度下降 对于一些需要高精度加工的设备而言,主轴的平衡状态直接影响着加工的精度。当发现加工出来的产品尺寸偏差超出了规定的范围,表面粗糙度不符合要求时,我们就需要考虑主轴是否存在不平衡的问题。 主轴的不平衡会导致刀具在加工过程中出现抖动,从而使得加工精度受到严重影响。如果在排除了刀具磨损、夹具松动等其他可能因素后,加工精度仍然无法得到改善,那么很有可能是主轴的不平衡所致,此时就需要对主轴进行现场动平衡调整。 轴承温度异常 主轴的不平衡会使轴承承受额外的负荷,从而导致轴承温度升高。我们可以通过温度传感器来实时监测轴承的温度。如果发现轴承温度明显高于正常运行时的温度,并且持续上升,这就表明主轴的运行状态可能存在问题。 过高的温度会加速轴承的磨损,缩短其使用寿命,甚至可能导致轴承损坏。因此,当检测到轴承温度异常时,我们需要及时对主轴进行检查,判断是否需要进行现场动平衡,以避免因主轴不平衡引发更严重的设备故障。 综上所述,判断主轴是否需要现场动平衡需要我们从振动监测、噪音分析、加工精度以及轴承温度等多个方面进行综合考量。只有准确地判断出主轴的运行状态,及时采取现场动平衡措施,才能确保主轴的稳定运行,提高设备的工作效率和使用寿命,为工业生产的顺利进行提供有力保障。
23
2025-06
如何判断主轴需要动平衡校正
如何判断主轴需要动平衡校正 在机械运行的世界里,主轴如同心脏一般重要,它的稳定运转是保障设备性能和寿命的关键。而动平衡校正对于主轴而言,就像是给心脏做定期检查和调理。那么,如何判断主轴需要动平衡校正呢? 异常振动感知 主轴运转时,异常振动是一个明显的信号。当设备开启后,你能通过触感察觉到轻微但不寻常的抖动。比如,原本平稳运行的机床,现在用手触摸机身,能感觉到有节奏或无规律的震动。这种震动可能非常细微,需要仔细感受。同时,还可以借助专业的振动检测仪器,它能精确捕捉到主轴振动的频率和幅度。如果检测到的振动值超出了设备的正常运行范围,那就极有可能是主轴失去了动平衡。 异常振动不仅会影响设备的加工精度,还会加速主轴及相关零部件的磨损。想象一下,主轴在高速旋转时,如果不平衡,就像一个偏心的陀螺,会对周围的部件产生额外的冲击力,长此以往,设备的寿命会大大缩短。 噪音变化识别 主轴的噪音也是判断是否需要动平衡校正的重要依据。正常情况下,主轴运转的声音是平稳且有规律的。但当出现动平衡问题时,噪音会发生明显变化。可能会听到尖锐的啸叫声,或者原本低沉的运转声变得杂乱无章。 这是因为不平衡的主轴在旋转过程中,会与周围的空气、零部件产生不规则的摩擦和碰撞,从而产生异常噪音。而且,噪音的大小和变化频率也能反映出问题的严重程度。如果噪音持续增大且越来越尖锐,那就说明主轴的动平衡问题已经比较严重,需要及时进行校正。 加工精度下降 对于一些依靠主轴进行精密加工的设备来说,加工精度的下降是动平衡问题的直接体现。比如在数控机床上,如果主轴失去动平衡,加工出来的零件尺寸精度和表面粗糙度都会受到影响。原本要求公差在极小范围内的零件,实际加工出来的尺寸偏差较大;表面也不再光滑,出现了明显的刀痕或波纹。 这是因为主轴的不平衡会导致刀具在加工过程中产生不稳定的切削力,从而影响加工精度。一旦发现加工精度出现问题,排除其他因素后,就要考虑主轴动平衡的问题了。 设备运行参数异常 观察设备的运行参数也能发现主轴动平衡的问题。例如,电机的电流和功率会发生变化。当主轴不平衡时,电机需要消耗更多的能量来维持其运转,导致电流增大、功率上升。同时,主轴的转速也可能出现波动,不再能稳定地保持在设定的数值上。 设备运行参数的异常是一个综合性的信号,它反映了主轴在运行过程中的不稳定状态。通过对这些参数的实时监测和分析,可以及时发现动平衡问题,避免设备进一步损坏。 判断主轴是否需要动平衡校正需要从多个方面进行综合考量。异常振动、噪音变化、加工精度下降以及设备运行参数异常等都是重要的判断依据。及时发现并进行动平衡校正,能有效保障主轴的稳定运行,延长设备的使用寿命,提高生产效率和产品质量。
23
2025-06
如何判断传动轴是否需要动平衡校正
如何判断传动轴是否需要动平衡校正 一、振动分析:捕捉动态失衡的蛛丝马迹 传动轴的动平衡状态与其旋转时的振动特性密切相关。当传动轴在高速旋转时,若出现周期性抖动或高频颤动,这可能是动平衡失效的直接信号。例如,汽车变速箱输出轴若在3000rpm以上转速时伴随方向盘共振,需优先排查动平衡偏差。专业检测中,可借助振动传感器量化轴系径向振动幅值:若振幅超过ISO 10816-3标准阈值(如转速2000rpm时振动值>7.1mm/s),则需启动校正程序。值得注意的是,低频振动可能源于装配误差,而高频振动更倾向反映质量分布异常。 二、运行状态观察:多维度症状交叉验证 温度异常:动平衡不良会导致局部摩擦加剧,若传动轴某区域温度较其他部位高5℃以上,需结合红外热成像仪定位热源。 异响特征:轴承座附近出现类似”嗡嗡”的低频噪音,或齿轮箱伴随”咔嗒”间歇性敲击声,均可能与轴系不平衡共振相关。 耗能变化:工业设备中,传动轴动平衡偏差每增加1g·mm(克毫米),驱动电机功率损耗可能上升0.3%-0.8%,可通过能耗监测系统建立预警模型。 三、专业检测方法:技术手段的精准介入 动平衡机检测 硬支承平衡机适用于刚性轴,通过测量轴系在自由旋转状态下的离心力矩,计算需校正的不平衡量及相位角。 软支承平衡机则针对挠性轴,需在模拟工况下进行动态平衡,误差精度可达±0.1g。 频谱分析技术 通过FFT变换将振动信号分解为频域成分,若发现与转速频率(1×)成整数倍的谐波峰值(如2×、3×),可能反映质量分布的周期性缺陷。 激光对准仪辅助 轴系对中不良会加剧动平衡需求,使用激光校准仪检测联轴器径向偏差>0.05mm或角向偏差>0.15mm时,需同步进行对中调整与动平衡校正。 四、历史数据对比:建立动态评估基准 振动趋势分析 建立传动轴全生命周期振动数据库,若某测点振动值较初始值增长20%以上,或波动系数(标准差/均值)>0.3,应启动校正流程。 工况匹配验证 柴油机传动轴在额定负荷下振动正常,但在空载高速工况出现异常,可能反映质量分布对转速敏感性,需针对性校正。 疲劳损伤关联 结合Rainflow计数法分析振动载荷谱,若不平衡导致的应力循环次数超过材料S-N曲线阈值,需优先进行动平衡修复。 五、综合判断策略:风险矩阵与决策树应用 风险等级划分 低风险:振动值在标准范围内,但存在轻微异响,建议预防性校正周期缩短30%。 高风险:轴承寿命预测剩余<200小时,需立即停机校正。 决策树模型 若振动值>阈值 → 检测对中状态 → 若对中正常 → 动平衡校正 若温度异常且振动超标 → 排查润滑/磨损 → 同步进行动平衡与修复 经济性权衡 校正成本需与潜在故障损失对比:若校正费用<预期停机损失的15%,则应立即执行;对于精密仪器轴系(如数控机床主轴),即使振动值接近标准上限,也建议预防性校正。 结语 传动轴动平衡校正的判断需融合感官经验与精密检测,建立”症状观察-数据采集-模型分析-风险决策”的闭环体系。通过多维度信息交叉验证,可将误判率控制在2%以下,同时延长轴系寿命30%-50%。建议企业制定《传动轴动平衡管理规范》,将校正标准与设备工况、使用环境深度绑定,实现预防性维护的精准化升级。
23
2025-06
如何判断传动轴需要动平衡校正
如何判断传动轴需要动平衡校正 一、振动分析:捕捉动态失衡的蛛丝马迹 传动轴的异常振动是动平衡失效的直接信号。使用加速度传感器或激光测振仪,可捕捉到轴系在旋转过程中产生的不规则颤动。高频振动(>1kHz)可能源于轴端配重缺失,而低频振动(2kHz):多因轴端配重块松动或键槽磨损,需配合振动分析定位故障点。 低频轰鸣(3000rpm)或高精度(G6.3以上)传动系统,建议每500小时进行预防性动平衡检测,避免次生故障链式爆发。
23
2025-06
如何判断刹车片是否需要动平衡调整
如何判断刹车片是否需要动平衡调整 在汽车的运行系统中,刹车片扮演着至关重要的角色。它不仅关系到车辆的制动性能,还影响着行车的安全性。然而,很多人可能忽略了刹车片的动平衡问题。那么,如何判断刹车片是否需要动平衡调整呢?下面就为大家详细介绍。 聆听制动异响 当你在驾驶过程中踩下刹车,如果听到尖锐刺耳的摩擦声或者低沉的闷响,这很可能是刹车片出现问题的信号。正常情况下,刹车片与刹车盘的接触应该是平稳且安静的。一旦出现异响,有可能是刹车片表面磨损不均匀,导致在制动时产生震动和噪音。这种不均匀的磨损会破坏刹车片的动平衡。比如,刹车片的一侧磨损严重,而另一侧相对较新,在旋转过程中就会产生不平衡的力,从而引发异响。此时,就需要考虑对刹车片进行动平衡调整,以消除这种不正常的现象。 感受制动抖动 在制动过程中,如果你能明显感觉到方向盘或者车身的抖动,这也是一个重要的判断依据。当刹车片的动平衡被打破时,刹车盘在旋转时会受到不均匀的压力。这种不均匀的压力会传递到方向盘和车身,使驾驶者产生抖动的感觉。想象一下,就像洗衣机在脱水时,如果里面的衣物分布不均匀,就会产生剧烈的震动。同样的道理,刹车片动平衡失调也会导致类似的情况。如果抖动现象频繁出现,且随着车速的增加而加剧,那么很有可能是刹车片需要进行动平衡调整了。 观察刹车痕迹 定期检查刹车盘上的刹车痕迹也是判断刹车片动平衡是否需要调整的有效方法。正常的刹车痕迹应该是均匀分布在刹车盘表面的。如果发现刹车盘上的刹车痕迹呈现出不规则的状态,比如一侧深一侧浅,或者有明显的划痕和磨损不均的情况,这就表明刹车片在制动时没有均匀地接触刹车盘。这种不均匀的接触是动平衡失调的表现。长期这样下去,不仅会影响制动效果,还会加速刹车盘和刹车片的磨损。所以,当观察到刹车痕迹异常时,要及时对刹车片进行动平衡检查和调整。 关注制动效果 制动效果的变化也是判断刹车片动平衡是否良好的关键因素。如果发现车辆的制动距离明显变长,或者在制动时感觉刹车力度不够,这可能与刹车片的动平衡有关。当刹车片动平衡失调时,它不能有效地将制动力均匀地传递到刹车盘上,从而导致制动效果下降。另外,如果在制动过程中,车辆出现偏向一侧的情况,也可能是由于刹车片动平衡问题导致两侧制动力不均衡。因此,一旦发现制动效果出现异常,就要警惕刹车片是否需要动平衡调整。 判断刹车片是否需要动平衡调整需要综合考虑多个方面。通过聆听制动异响、感受制动抖动、观察刹车痕迹和关注制动效果等方法,我们可以及时发现刹车片动平衡失调的问题,并采取相应的措施进行调整。这样不仅能保证车辆的制动性能和行车安全,还能延长刹车系统的使用寿命。
23
2025-06
如何判断刹车盘需要动平衡校正
如何判断刹车盘需要动平衡校正 一、振动异常:车轮的”心跳紊乱” 当方向盘在特定车速下产生规律性震颤,或踏板出现共振式抖动时,这可能是刹车盘动平衡失衡的初阶信号。专业技师会通过以下维度诊断: 速度阈值:80-120km/h区间内震颤加剧,提示离心力与惯性力矩失衡 振动频率:每分钟200-500次的高频震颤对应0.1mm级径向跳动误差 传导路径:从方向盘→转向柱→车身的传导衰减率低于30%即需警戒 二、噪音图谱:金属的”病理报告” 异常声响是动平衡失调的次生症状,需结合频谱分析判断: 高频啸叫(2-5kHz):对应0.05mm级表面波纹度超标 低频轰鸣(50-100Hz):反映10g以上质量偏心距失衡 间歇性敲击:伴随制动片厚度差超过0.3mm时出现 三、磨损密码:制动面的”微雕证据” 通过三维激光扫描可发现: 非对称磨损带:单侧磨损区宽度超过5mm即构成校正指征 波浪形纹理:振幅超过0.02mm的周期性沟槽 热斑分布:红外成像显示的局部温度梯度差>15℃ 四、操控畸变:驾驶舱的”异常反馈” 需建立多维感知矩阵: 转向力矩波动:超过±5N·m的周期性变化 制动距离延长:100-0km/h制动距离增加>3% ABS触发异常:非紧急状态下误启动频率>2次/百公里 五、专业校验:精密仪器的”终极判读” 建议采用三级检测体系: 静态检测:千分表测量径向跳动≤0.05mm 动态检测:惯性测试台模拟200km/h工况 频谱分析:FFT变换识别10-500Hz频段异常谐波 校正价值延伸:完成动平衡校正后,可使制动效能恢复98%以上,同时降低悬架系统损耗率40%,延长轮胎寿命15%-20%。建议每行驶2万公里或更换制动组件后进行预防性检测,构建车辆动态性能的”免疫屏障”。
23
2025-06
如何判断动平衡是否需要矫正
如何判断动平衡是否需要矫正 在机械运转的世界里,动平衡至关重要。它关乎着设备的稳定运行、使用寿命,甚至影响着生产效率和安全。那么,怎样判断动平衡是否需要矫正呢?下面为大家详细介绍。 聆听设备的“声音” 设备在正常运行时,会发出平稳而有规律的声音。若动平衡出现问题,就会打破这种和谐。运转过程中发出异常的振动声或噪音,那可能就是动平衡失调的信号。比如,电机在运转时原本声音均匀,突然出现尖锐或沉闷的杂音,类似“嗡嗡”声或“哐当”声,这往往意味着转子的动平衡可能受到了破坏。这种异常声音可能是由于不平衡的质量在高速旋转时产生的离心力,使设备各部件发生碰撞或摩擦所导致的。 感受设备的“震动” 用手触摸设备,感受其震动情况。正常情况下,设备的震动应该是轻微且均匀的。当动平衡失衡时,震动会明显加剧,而且可能呈现出不规则的状态。例如,在一些旋转设备上,如风机、离心机等,若能明显感觉到设备有强烈的抖动,甚至能看到设备整体在晃动,那就需要警惕动平衡是否需要矫正了。此外,还可以使用专业的震动检测仪器,精确测量设备的震动幅度和频率。如果震动幅度超过了设备的正常允许范围,或者震动频率出现异常波动,这些都表明动平衡可能存在问题。 观察设备的“运行状况” 留意设备的运行参数和表现。如果设备的转速不稳定,时而快时而慢,或者功率消耗明显增加,这可能与动平衡有关。不平衡的转子在运转时会增加设备的负荷,导致电机需要消耗更多的能量来维持运转,从而使功率上升。另外,设备的工作效率下降、产品质量不稳定也可能是动平衡失调的间接表现。比如,在一些加工设备上,由于动平衡问题导致刀具的切削精度下降,从而影响产品的尺寸精度和表面质量。 定期进行“专业检测” 即使设备没有出现明显的异常现象,定期进行专业的动平衡检测也是很有必要的。专业的检测设备能够准确地测量出转子的不平衡量和位置。通过对检测数据的分析,可以判断动平衡是否在允许的范围内。一般来说,根据设备的类型和使用环境,制定合理的检测周期。对于一些高精度、高转速的设备,检测周期可以相对短一些;而对于一些普通的设备,可以适当延长检测周期。 判断动平衡是否需要矫正需要综合考虑多个方面。通过聆听声音、感受震动、观察运行状况以及定期进行专业检测等方法,能够及时发现动平衡问题,并采取相应的矫正措施,确保设备的稳定运行和生产的顺利进行。
23
2025-06
如何判断动平衡机是否失准
如何判断动平衡机是否失准 在工业生产中,动平衡机是保障旋转机械稳定运行的关键设备。然而,随着使用时间的增长和各种因素的影响,动平衡机可能会出现失准的情况。以下为您介绍一些判断动平衡机是否失准的方法。 观察测量数据的稳定性 测量数据的稳定性是判断动平衡机是否准确的重要依据。如果在多次对同一工件进行测量时,动平衡机显示的不平衡量数值波动较大,偏差超过了正常的误差范围,那就很可能表明动平衡机存在失准问题。例如,第一次测量显示不平衡量为 10g,第二次测量却变成了 20g,这种较大的波动就需要引起我们的注意。另外,测量角度的不稳定也是一个重要信号。平衡机在测量过程中,不平衡量的角度应该相对稳定,如果每次测量得到的角度偏差较大,也说明动平衡机可能出现了失准。 对比标准工件的测量结果 使用标准工件是判断动平衡机是否失准的有效方法之一。标准工件是经过精确校准的,其不平衡量和角度是已知的。将标准工件安装在动平衡机上进行测量,如果测量结果与标准值相差较大,那么动平衡机很可能已经失准。比如,标准工件的不平衡量为 5g,而动平衡机测量结果为 8g,这就说明动平衡机的测量存在较大误差。不过在使用标准工件时,要确保其安装位置和方式与实际测量时一致,否则可能会影响测量结果的准确性。 检查设备的机械部件 动平衡机的机械部件状况对测量结果有着重要影响。首先要检查支撑系统,支撑系统如果出现松动、磨损或者变形等情况,会导致工件在旋转过程中产生额外的振动,从而影响测量的准确性。比如,支撑滚轮的磨损会使工件旋转时不平稳,造成测量数据的偏差。其次,皮带传动部分也需要检查。皮带的松紧度不合适或者皮带本身存在磨损、老化等问题,都会影响传动的稳定性,进而影响动平衡机的测量精度。另外,传感器作为动平衡机的关键部件,其性能的好坏直接影响测量结果。如果传感器出现故障或者灵敏度下降,也会导致动平衡机失准。 参考操作人员的经验判断 有经验的操作人员对动平衡机的性能和运行状况比较熟悉,他们的经验也可以作为判断动平衡机是否失准的参考。操作人员在长期的工作中,会对动平衡机的正常运行状态有一个直观的认识。如果他们感觉动平衡机在运行过程中声音异常,比如出现了刺耳的噪音或者振动明显加剧的情况,这可能是动平衡机失准的一个信号。此外,操作人员还可以根据工件平衡后的实际运行效果来判断。如果经过动平衡机平衡后的工件在实际使用中仍然存在振动过大、噪音异常等问题,那么动平衡机很可能存在失准的情况。 判断动平衡机是否失准需要综合考虑多个方面的因素。通过观察测量数据的稳定性、对比标准工件的测量结果、检查设备的机械部件以及参考操作人员的经验等方法,可以及时发现动平衡机的失准问题,从而保证动平衡机的正常运行和测量的准确性。
23
2025-06
如何判断动平衡校正效果
如何判断动平衡校正效果 一、振动测量:机器的”体温计”与”心电图” 动平衡校正效果的首要判断依据是振动参数的量化分析。专业人员需建立”三维监测体系”: 接触式传感器(如压电式加速度计)捕捉高频振动细节,适用于精密仪器 非接触式激光测振仪穿透复杂工况,精准捕捉低频共振 动态监测系统(如频谱分析仪)实时绘制振动频谱图,识别异常频率成分 关键指标: 振动速度有效值(mm/s)需符合ISO 10816-3标准 振动加速度峰值(m/s²)应低于设备临界值 振动位移幅值(μm)需满足行业规范 案例:某离心泵校正后振动值从12.3mm/s降至3.8mm/s,降幅达69%,但需结合频谱分析排除轴承故障干扰。 二、运行状态观察:五感联动的诊断艺术 专业人员需培养”全息感知能力”: 视觉:观察转子运行轨迹,校正后应呈现”镜面反射”般的平稳 听觉:异常啸叫频率降低,高频杂音消失 触觉:手背感受设备表面温度分布,局部过热区域应显著改善 嗅觉:校正后润滑油焦糊味减弱,金属摩擦味消失 数据记录:连续72小时监测振动趋势,波动幅度应控制在±15%以内 特别提示:某些高速设备(如航空发动机)需在真空舱内模拟工况,避免环境干扰。 三、频谱分析:解码振动的”基因图谱” 通过频谱仪获取的频谱图是动平衡效果的”分子级证据”: 基频特征:校正后基频幅值下降幅度应≥50% 谐波分布:二次谐波占比从35%降至12%,表明质量分布趋于均匀 边频带:校正后边频带宽度从±8Hz压缩至±2Hz 异常频率:排除齿轮啮合、轴承故障等干扰成分 进阶技巧:采用阶次分析法,将振动信号与转速关联,精准定位不平衡阶次。 四、残余不平衡量计算:数学与工程的完美平衡 通过公式: e_r = rac{1000 cdot G cdot omega^2 cdot R}{9.81 cdot 10^6}e r = 9.81⋅10 6 1000⋅G⋅ω 2 ⋅R 计算残余不平衡量(e_r),其中: G:振动加速度(m/s²) ω:角速度(rad/s) R:校正半径(mm) 工程转化: 将计算值与ISO 1940-1标准对比 对比校正前后不平衡量下降率(理想值≥80%) 结合材料特性修正计算结果(如橡胶件需乘以0.7修正系数) 五、用户反馈:从实验室到现场的终极验证 操作员体验:疲劳指数下降30%以上,误操作率降低 产品合格率:精密加工设备良品率提升5-8个百分点 能耗监测:电机电流波动幅度从±15A降至±3A 寿命预测:轴承磨损速度减缓,MTBF延长2000小时 特别案例:某造纸机校正后,纸张横向偏差从±0.5mm改善至±0.1mm,直接提升产品合格率12%。 结语:多维验证的黄金法则 动平衡效果判断需遵循”3C原则”: Comprehensive(全面性):融合定量数据与定性观察 Consistency(一致性):不同检测方法结果需相互印证 Contextual(情境性):结合设备工况动态调整判断标准 记住:完美的动平衡是”看得见的稳定,摸得着的和谐”,而非单纯的数据游戏。