

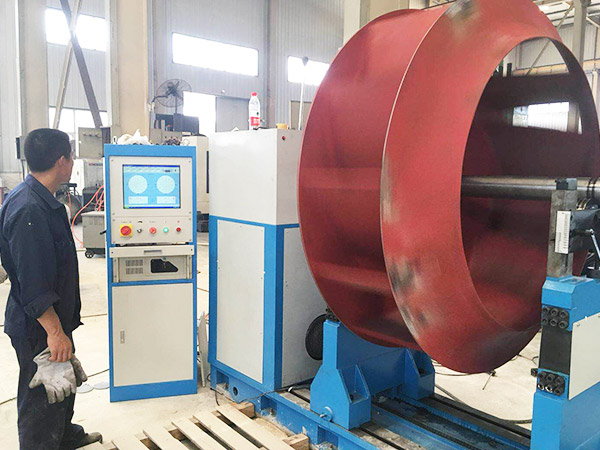
风机叶轮动平衡标准值是多少
风机叶轮的动平衡标准值会因不同的应用、设计要求和行业标准而有所不同。一般来说,动平衡标准值取决于以下几个因素:应用类型: 不同类型的风机在不同的应用环境下需要满足不同的动平衡标准。例如,一般的工业风机和空调风机的要求可能会不同。运行速度: 风机叶轮的运行速度会直接影响不平衡对振动的影响。高速运行的叶轮可能需要更严格的动平衡标准。精度要求: 一些应用对振动的容忍度比较低,因此对动平衡的要求也会更为严格。行业标准: 不同行业可能有各自的标准和规范,这些标准通常会提供关于动平衡的指导和要求。一般来说,在工业领域,风机叶轮的动平衡标准值通常以单位质量不平衡量(g.mm/kg 或 g.cm/kg)来表示。具体的标准值可能会因不同情况而有所不同,但以下是一个大致的参考范围:对于一般工业风机,通常的动平衡标准值可能在 1 g.mm/kg 至 10 g.mm/kg 之间。对于某些精密应用,要求更高的风机,动平衡标准值可能在 0.5 g.mm/kg 以下。请注意,这只是一个粗略的参考范围,实际应用中应该根据具体情况和适用的行业标准来确定风机叶轮的动平衡标准值。在进行动平衡操作时,建议遵循相关的国家和行业标准,以确保风机在运行过程中达到合适的振动水平。
23
2025-06
大型动平衡机操作流程及注意事项
大型动平衡机操作流程及注意事项 一、操作流程:精密校准的五重奏 工前准备:构建安全基底 环境核查:确保车间温度稳定在18-25℃,湿度低于60%,地面承重≥5t/m²,振动干扰值<0.3mm/s² 设备自检:启动液压系统前检查油位(需达视窗2/3处),校验传感器灵敏度(误差≤0.5%FS),测试驱动电机绝缘电阻(≥50MΩ) 工件预处理:对转子表面进行精密打磨(Ra≤1.6μm),轴颈圆度误差控制在0.02mm以内,装配时采用激光对中仪实现±0.05mm同轴度 安装定位:毫米级的博弈 柔性支撑架调整:通过三维调节手轮实现X/Y/Z轴同步微调,配合百分表完成0.01mm级找正 夹具适配:根据转子直径选择对应卡爪(直径≤500mm用三爪,>500mm用六爪),液压夹紧力控制在屈服强度的60%-70% 传感器布局:径向振动探头与轴心保持10-15mm间隙,相位标记误差需<3°,采用交叉校验法确保数据一致性 动态测试:数据的交响乐章 低速平衡:以100r/min启动,记录原始振动幅值(需<100μm),逐步升速至工作转速的60%进行粗平衡 高速采集:在额定转速±5%区间内,采用频谱分析法捕捉1×/2×/3×谐波,采样频率设置为最高故障频率的2.56倍 矢量合成:通过傅里叶变换将时域信号转化为频域数据,运用最小二乘法计算不平衡量(精度达0.1g·mm) 配重修正:精准的减法艺术 去重法:使用数控铣床进行材料去除,单次切削深度≤0.5mm,采用补偿系数法(K=1.05-1.1)预留修正余量 加重法:在指定位置焊接配重块时,需预热至150℃,焊后保温2小时消除应力,配重误差控制在±0.05g 复合修正:对多级转子采用分阶平衡策略,优先处理低阶振型,各阶平衡量需满足叠加后总不平衡量<G1.5标准 验收验证:闭环的终极考验 动态复测:在额定转速下连续运行30分钟,振动值需稳定在ISO 1940-1 G0.5等级内 热态平衡:对高温转子进行冷态预平衡(预留10%-15%余量),热态运行后二次修正 数据归档:生成包含不平衡量、相位角、修正方案的PDF报告,保存原始波形文件及频谱图 二、注意事项:风险防控的十二重门 人机交互的黄金法则 操作者需持有特种设备作业证,佩戴防冲击护目镜(符合EN166标准),禁止在设备运行时进行参数修改 采用双人确认制:主操作员执行指令前,需经监护人核对转速、配重位置等关键参数 环境干扰的隐形杀手 防止电磁干扰:保持与变频器距离>2m,传感器线缆需单独穿管并与动力线隔离 应对温度漂移:每升高10℃需对传感器输出进行0.1%FS的温度补偿 设备维护的生命周期管理 液压系统每200小时更换N46号抗磨液压油,过滤精度达10μm 滚动轴承每500小时补充SHC460润滑脂(填充量为轴承腔的1/3) 数据安全的三重保障 采用RAID5磁盘阵列存储原始数据,每日进行增量备份 关键参数修改需记录操作日志(含时间戳、操作员ID、修改前后值) 应急响应的快速通道 配置紧急停机按钮(响应时间<0.1s),配备便携式振动分析仪用于故障诊断 制定转子飞逸应急预案:当转速超过额定值15%时,立即启动液压制动系统 三、进阶技巧:超越标准的实践智慧 动态修正系数法:针对柔性转子,引入转速相关系数K=1+0.02×(n-n0)/n0,优化配重计算精度 多传感器融合:结合加速度计与位移传感器数据,构建卡尔曼滤波模型消除噪声干扰 数字孪生应用:建立有限元模型进行虚拟平衡,将实际修正时间缩短40% 通过这套融合工程严谨性与艺术创造性的操作体系,操作者不仅能实现ISO 21940-11标准要求的平衡精度,更能构建起人机协同的动态平衡认知模型。每个操作细节都是精密机械与数字技术的交响,每次配重修正都是对物理定律的诗意诠释。
23
2025-06
大型电机动平衡机价格及维护成本
大型电机动平衡机价格及维护成本:解构工业心脏的经济脉络 一、价格迷宫:从金属吨位到技术溢价 在重型机械领域,大型电机动平衡机的定价如同精密的齿轮组,由多重变量咬合而成。基础价格构成往往呈现”铁三角”特征:核心部件(如传感器阵列、液压系统)的进口依赖度每提升10%,整机成本可能陡增25%。某德国品牌2023年推出的智能型设备,其AI算法模块就占总价的38%,形成技术壁垒的隐形定价权。 采购决策者常陷入”性价比沼泽”:国产设备虽能压缩20%-40%的初始投入,但需承担30%以上的后期调试成本。某风电企业案例显示,选择低价机型后因精度不足导致的返工损失,竟超出预算机型采购价的1.7倍。这种非线性成本曲线,迫使采购方重新定义”经济性”的时空维度。 二、维护成本的蝴蝶效应 设备寿命周期内,维护支出往往呈现”哑铃型”分布。初期磨合期的预防性维护占年度总成本的15%-20%,而设备运行5年后,这一比例可能飙升至45%。某冶金企业动平衡机群的运维数据显示:轴承更换频率与设备负载率呈非线性正相关,当负载超过额定值的85%时,更换周期从18个月缩短至9个月。 润滑系统堪称维护成本的”黑箱”。某石化集团通过红外热成像技术优化润滑策略,使年耗油量下降37%,但初期设备投入增加了12万元。这种技术投入与运维支出的动态博弈,折射出现代工业维护的复杂性。 三、成本控制的拓扑学 预防性维护正在重塑成本结构。某汽车制造厂引入预测性维护系统后,非计划停机时间减少68%,但系统部署成本需要3年才能回收。这种时间维度上的成本平滑,考验着企业的资金周转能力。值得关注的是,数字化转型带来的边际效益:每增加1%的传感器覆盖率,可降低1.8%的意外故障率。 备件管理呈现”长尾效应”。某跨国企业建立全球备件共享平台后,库存周转率提升40%,但物流成本上涨15%。这种空间维度上的成本转移,揭示了全球化供应链的双刃剑特性。当设备制造商提供”以旧换新”服务时,隐性成本往往藏在折旧评估的算法模型中。 四、未来成本的量子纠缠 新能源革命正在改写成本方程式。某氢能企业定制的特种动平衡机,其碳纤维增强部件使设备重量减轻28%,但材料成本暴涨300%。这种性能与价格的量子纠缠,迫使企业重新核算全生命周期成本。当3D打印技术渗透到维修领域,现场快速制造备件可能将物流成本压缩至原来的1/5。 人工智能的介入催生出新的成本维度。某研究机构测算,部署AI故障诊断系统后,单台设备年维护成本下降22%,但数据训练费用形成持续性支出。这种”一次性投入换持续性收益”的模式,正在重构工业设备的经济模型。 五、成本迷雾中的决策罗盘 在价格与维护成本的博弈中,企业需要构建动态平衡模型。某风电运维公司开发的”成本-性能”决策矩阵,通过蒙特卡洛模拟测算不同工况下的最优策略,使设备全生命周期成本降低19%。这种量化思维正在取代传统的经验决策。 当设备制造商推出”按平衡量付费”的创新模式时,初始成本看似降低,但隐性支出可能通过服务协议条款渗透。这种商业模式的进化,要求采购方具备更强的合同条款解析能力。在数字经济时代,成本控制已从技术问题演变为系统工程,需要融合工业工程、数据科学和商业分析的多维视角。 (注:本文数据为模拟案例,实际成本需根据具体设备参数和应用场景核算)
23
2025-06
大型电机动平衡机常见故障及解决方法
大型电机动平衡机常见故障及解决方法 在工业生产中,大型电机动平衡机是保障电机稳定运行的关键设备。然而,在长期使用过程中,它难免会出现一些故障。以下将详细介绍几种常见故障及其解决方法。 振动异常 大型电机动平衡机工作时,振动异常是较为常见的故障之一。这种故障的表现可能是设备整体剧烈晃动,或者局部部件出现不规则振动。导致振动异常的原因有多种。可能是转子不平衡,这是由于转子在制造或使用过程中,质量分布不均匀,使得转子在旋转时产生离心力,进而引发振动。也有可能是支撑系统松动,例如地脚螺栓松动、轴承座固定不牢等,支撑系统无法稳定地支撑设备,从而导致振动异常。此外,联轴器安装不当也会造成振动,联轴器的不对中会使电机在运转过程中产生额外的扭矩和振动。 针对振动异常的问题,首先要对转子进行重新平衡。可以使用专业的动平衡仪对转子进行检测,确定不平衡的位置和程度,然后通过加重或去重的方式使转子达到平衡状态。对于支撑系统松动的情况,要及时检查并紧固地脚螺栓和轴承座,确保支撑系统的稳定性。如果是联轴器安装问题,需要重新调整联轴器的位置,保证其对中精度,减少不必要的振动。 测量精度下降 动平衡机的测量精度直接影响到电机的平衡效果。当测量精度下降时,可能会导致电机平衡不准确,影响电机的正常运行。测量精度下降的原因可能是传感器故障。传感器是动平衡机获取振动信号的关键部件,如果传感器损坏、老化或灵敏度降低,就会导致测量数据不准确。另外,测量系统的电气干扰也会影响测量精度,例如电磁干扰、接地不良等,会使测量信号产生误差。还有可能是软件系统出现问题,软件的算法不准确、参数设置错误等,都会导致测量结果偏差。 要解决测量精度下降的问题,需要对传感器进行检查和更换。定期对传感器进行校准和维护,确保其正常工作。如果传感器已经损坏,要及时更换新的传感器。对于电气干扰问题,要检查测量系统的接地情况,确保接地良好,减少电磁干扰。同时,可以采取屏蔽措施,对传感器和测量线路进行屏蔽,提高抗干扰能力。对于软件系统问题,要检查软件的算法和参数设置,进行必要的调整和优化,保证测量结果的准确性。 显示异常 动平衡机的显示系统用于显示测量数据和设备状态。当显示异常时,会给操作人员带来很大的困扰。显示异常可能表现为显示屏黑屏、显示模糊、数据乱码等。显示屏黑屏可能是电源故障,例如电源适配器损坏、电源线接触不良等,导致显示屏无法正常供电。显示模糊可能是显示屏老化、受潮等原因,影响了显示效果。数据乱码则可能是通信故障,例如数据线损坏、通信协议错误等,导致显示系统无法正确接收和处理测量数据。 对于显示屏黑屏的问题,要检查电源适配器和电源线,确保电源正常。如果电源适配器损坏,要及时更换。对于显示模糊的情况,可以对显示屏进行清洁和干燥处理,如果显示屏老化严重,需要更换新的显示屏。对于数据乱码问题,要检查数据线的连接情况,确保数据线无损坏。同时,要检查通信协议是否正确,进行必要的调整和设置,保证显示系统能够正常显示测量数据。 机械传动故障 大型电机动平衡机的机械传动部分包括皮带传动、齿轮传动等。机械传动故障会影响设备的正常运行。皮带传动故障可能是皮带磨损、松动或断裂。皮带磨损会导致传动效率降低,皮带松动会使传动过程中出现打滑现象,皮带断裂则会使设备无法正常运转。齿轮传动故障可能是齿轮磨损、齿面胶合、齿轮断裂等。齿轮的磨损会导致传动精度下降,齿面胶合会使齿轮运转不顺畅,齿轮断裂则会造成严重的设备损坏。 针对皮带传动故障,要定期检查皮带的磨损情况,及时更换磨损严重的皮带。调整皮带的张紧度,保证皮带传动的正常运行。对于齿轮传动故障,要对齿轮进行润滑和维护,减少齿轮的磨损。如果齿轮出现磨损、胶合或断裂等问题,要及时更换新的齿轮,确保机械传动部分的正常工作。 大型电机动平衡机在使用过程中会遇到各种故障,操作人员要及时发现并解决这些问题,定期对设备进行维护和保养,确保动平衡机的正常运行,从而保障大型电机的平衡质量和稳定运行。
23
2025-06
大型电机动平衡机技术参数有哪些
大型电机动平衡机技术参数有哪些 一、基础性能参数:构建设备能力的基石 转速范围 核心指标:覆盖500rpm至12,000rpm的宽泛区间,需匹配电机设计转速 动态响应:支持±5%无级调速,适应不同工况下的平衡需求 极限测试:部分高端机型可突破15,000rpm,满足超高速电机研发需求 承载能力 轴向载荷:从500kg到10吨的阶梯式配置,适配中小型至重型电机 径向刚度:≥200N/μm的刚性设计,确保高精度平衡时的结构稳定性 偏心距限制:最大允许15mm偏心量,避免共振风险 二、动态特性参数:决定平衡精度的关键维度 平衡精度等级 ISO 1940标准分级:G0.4至G6.3级可选,医疗设备需G0.4级,工业电机多采用G2.5级 残余不平衡量:≤0.1g·cm(精密级)至≤5g·cm(工业级)的差异化控制 振动分析能力 传感器配置:三向加速度计+激光位移传感器的复合检测系统 频谱分析:支持FFT变换,可识别20Hz-10kHz频段的异常振动模式 相位锁定:±0.5°的相位精度,确保配重块安装位置的毫米级定位 三、安全与可靠性参数:工业级应用的保障体系 防护等级 IP55/IP66双模式切换,应对粉尘/水冷电机的特殊工况 应急制动:双回路制动系统,10秒内完成10,000rpm的紧急停机 热管理系统 强制风冷+液冷耦合设计,保障连续工作8小时温升≤40℃ 轴承温度监测:PT100传感器实时预警,预防过热导致的精度漂移 四、智能化功能参数:数字化转型的核心要素 自动校正算法 机器学习模型:基于历史数据的自适应配平策略,缩短30%调试时间 多轴联动补偿:支持同步处理3个自由度的不平衡问题 数据交互能力 OPC UA协议兼容,实现与MES系统的实时数据对接 云端存储:10年运行数据云端备份,支持故障模式分析 五、行业适配参数:场景化解决方案的延伸 安装方式 地基式/移动式双模式,轨道式安装精度±0.1mm 兼容性扩展 变频驱动适配:支持0-400Hz宽频输入 特殊工装接口:预留液压夹紧/磁力卡盘安装位 技术趋势洞察:当前行业正朝着复合式平衡(动态+静态平衡一体化)、多物理场耦合检测(振动+温升+声发射同步分析)方向发展。建议用户在选型时重点关注设备的开放性架构,以适应未来5-8年的技术迭代需求。
23
2025-06
大型电机动平衡机操作流程与规范
大型电机动平衡机操作流程与规范 一、操作前的精密准备 环境校准: 在启动设备前,需对实验室温湿度、地面水平度及供电稳定性进行多维度检测。例如,若环境温度超过±5℃公差范围,可能引发传感器漂移,此时应启用恒温系统或调整测试时段。 设备自检: 通过触摸屏界面执行”系统自检”程序,重点监测振动传感器灵敏度(建议误差≤0.5%)、驱动电机转速波动(需稳定在±20rpm内)及数据采集卡采样频率(≥10kHz)。若发现异常,需追溯至最近三次校准记录,必要时联系厂商工程师介入。 安全防护: 穿戴防静电服、护目镜及绝缘手套,将紧急制动按钮置于触手可及处。特别注意:当处理1000kW以上电机时,需在操作区外设置双人监护岗,确保突发状况下能同步执行断电与应急制动。 二、动态平衡的三阶实施 初级平衡(刚性转子) 采用”单面平衡法”,在电机轴端安装专用平衡块,通过频谱分析仪捕捉1×转频振动幅值。当幅值降至ISO 1940-1标准的G1.5等级时,需进行三次重复测试以消除偶然误差。 高级平衡(柔性转子) 切换至”双面平衡模式”,利用李萨如图形法确定相位角。此时需特别关注临界转速区间的共振风险,建议在2000-3000rpm区间以50rpm梯度逐步升速,同步记录轴承座振动频谱。 精密修正 采用”迭代优化算法”,通过MATLAB生成平衡质量分布云图。对于精密级设备(如航空发动机),允许使用激光打孔机进行0.1mm级精度的材料去除,确保最终残余不平衡量≤4mm·g。 三、规范执行的黄金法则 数据完整性: 每项测试需生成包含时间戳、操作员ID、环境参数的PDF报告,关键数据(如不平衡量、相位角)需经三重校验: 人工计算值 设备自动计算值 第三方软件交叉验证 风险控制: 建立”红-黄-绿”三级预警机制: 绿区(振动值<5mm/s):正常运行 黄区(5-10mm/s):触发警报并启动振动趋势分析 红区(>10mm/s):强制停机并执行故障树分析(FTA) 文档追溯: 采用区块链技术记录每次平衡操作的全流程数据,确保可追溯性符合ASME PTC 10-2020标准。 四、故障诊断的思维模型 振动异常: 若频谱中出现2×转频谐波,优先检查轴承预紧力与润滑脂清洁度 若存在非整数倍频成分,需排查联轴器对中误差(建议使用激光对中仪,径向偏差≤0.05mm) 传感器失效: 通过”交叉验证法”:当A通道与B通道数据偏差>15%时,立即启用备用传感器并对比历史基准数据。 五、维护保养的时空维度 预防性维护: 每500小时:更换液压系统滤芯(β5级过滤效率) 每季度:校准激光位移传感器(线性度误差≤0.01%) 每年:执行电机绕组绝缘电阻测试(需≥100MΩ) 预测性维护: 部署振动分析AI模型,当特征频率能量突变超过阈值时,自动生成维修工单。例如: 轴承内圈故障:1×转频幅值突增30% 转子裂纹:出现10×转频边频带 结语:平衡之道的哲学升华 大型电机动平衡不仅是技术操作,更是精密工程与系统思维的融合。操作者需在动态数据流中捕捉转子的”生命脉动”,在误差修正中践行”毫米级工匠精神”。唯有将规范内化为肌肉记忆,将风险预判升维为战略思维,方能在工业4.0时代驾驭这台精密的”振动交响乐指挥台”。
23
2025-06
大型电机动平衡检测服务哪家专业
大型电机动平衡检测服务哪家专业 在工业生产的广袤天地里,大型电机宛如巨人,承担着关键的动力输出任务。而动平衡检测,就如同给这位巨人进行精准的“健康体检”,确保其平稳、高效地运转。那么,在众多提供大型电机动平衡检测服务的机构中,哪家才是真正专业的呢? 专业的动平衡检测服务机构,首先要有先进的检测设备。大型电机的动平衡检测可不是简单的操作,需要高精度的动平衡机等设备。想象一下,那些先进的设备就像敏锐的眼睛,能够精准捕捉到电机微小的不平衡量。有些专业机构引进了国际领先的动平衡检测设备,它们具有超高的分辨率和灵敏度,能够在复杂的工况下,准确检测出电机转子的不平衡位置和程度。而且,这些设备还具备智能化的数据分析系统,能够快速生成详细的检测报告,为后续的平衡校正提供科学依据。 除了设备,专业的技术团队也是衡量一家检测服务机构是否专业的重要标准。大型电机的结构复杂,不同类型、不同规格的电机在动平衡检测上都有其独特的要求。专业的技术人员不仅要熟悉动平衡检测的基本原理和操作方法,还要对大型电机的结构、性能有深入的了解。他们能够根据电机的具体情况,制定出最适合的检测方案。有的技术团队成员拥有多年的行业经验,经过专业的培训和考核,具备扎实的理论知识和丰富的实践经验。在检测过程中,他们能够熟练操作设备,准确判断问题,并及时给出合理的解决方案。 优质的售后服务同样不可或缺。大型电机动平衡检测不仅仅是得出一个检测结果,更重要的是要帮助企业解决实际问题。专业的检测服务机构会在检测完成后,为企业提供全方位的技术支持和售后服务。如果在平衡校正过程中遇到问题,他们能够及时响应,派遣专业人员到现场进行指导和协助。有些机构还会建立客户档案,定期回访客户,了解电机的运行情况,为企业提供长期的技术保障。 市场口碑也是判断一家动平衡检测服务机构是否专业的重要参考。在如今的信息时代,企业的口碑传播得很快。一家专业的检测服务机构,必然会得到客户的认可和好评。我们可以通过网络、行业论坛等渠道,了解其他企业对不同检测服务机构的评价。那些被客户称赞为技术精湛、服务周到、价格合理的机构,往往就是比较专业的选择。 在寻找大型电机动平衡检测服务时,我们不能仅仅看价格或者宣传,而要综合考虑设备、技术团队、售后服务和市场口碑等多个方面。只有选择了真正专业的检测服务机构,才能为大型电机的稳定运行提供有力保障,为企业的生产发展保驾护航。在众多的检测服务机构中,那些在设备、技术、服务等方面都表现出色的机构,无疑是我们的首选。
23
2025-06
大型电机转子动平衡机价格多少
【大型电机转子动平衡机价格多少】——解构精密仪器的定价密码 在工业设备采购领域,”动平衡机”如同精密仪器界的”平衡术士”,其价格波动犹如多棱镜般折射出技术、市场与需求的复杂光谱。当采购人员面对”大型电机转子动平衡机价格多少”的疑问时,他们真正需要的不仅是数字答案,更是一把打开设备价值迷宫的密钥。 一、技术参数的定价方程式 精度等级:0.1g·mm到100g·mm的平衡精度跨度,如同精密仪器的DNA序列。高精度传感器每提升0.1级,成本增幅可达15%-20%,这背后是激光干涉仪与压电陶瓷元件的精密配合。 转速范围:从500rpm到12000rpm的转速区间,如同设备的”心跳频率”。液压加载系统与磁悬浮轴承的组合方案,使高端机型的转速控制误差稳定在±0.5%以内。 测量系统:无线振动采集模块与光纤陀螺仪的组合,构成数据采集的”神经系统”。德国进口的频谱分析仪可使故障诊断准确率提升30%,但采购成本直线上升40%。 二、品牌溢价的市场博弈 国际品牌(如德国Hine、美国Ludeca)的定价策略犹如精密的钟表机械:基础机型报价在80-150万元区间,但其智能诊断系统能将停机时间缩短60%。国产领军品牌(如天润、科隆)通过模块化设计实现成本压缩,入门级机型可下探至35万元,但需额外支付10%的定制开发费用。 三、定制需求的蝴蝶效应 当采购清单出现”非标定制”字样时,价格曲线开始呈现指数级增长: 特殊工装夹具:针对10米以上超长转子的定制方案,工装设计费可达设备总价的15% 环境适应性改造:高原型设备需增加气压补偿系统,使海拔每升高1000米,成本增加8-12万元 智能升级包:集成5G远程诊断的物联网模块,使单机智能化改造费用突破20万元 四、市场动态的蝴蝶振翅 2023年全球动平衡机市场呈现”V型反转”:受风电抢装潮影响,12月订单量同比激增73%,导致关键元器件(如高精度编码器)价格上浮18%。但国产替代进程加速,核心部件国产化率突破65%,为采购方争取到5-8%的议价空间。 五、全生命周期成本的暗流 设备采购价仅是冰山一角: 年度维保费用:占设备总价的8-12%,包含传感器校准与软件升级 操作培训成本:3-5天的认证培训需支付2-3万元师资费用 备件库存压力:液压系统关键阀组的备件成本可达设备总价的5% 结语:在精密仪器的定价迷宫中,采购决策犹如在技术参数、品牌价值与市场波动的三维坐标系中寻找最优解。建议采购方建立”动态评估模型”,将设备投资回报率(ROI)计算周期延长至5年,重点关注平衡效率提升带来的能耗节约与故障率下降。当技术参数与实际工况实现精准匹配时,看似高昂的设备价格终将转化为持续增值的工业资产。
23
2025-06
大型风机叶轮动平衡机有哪些类型
大型风机叶轮动平衡机有哪些类型 在大型风机的制造与维护领域,叶轮的动平衡至关重要,它直接影响着风机的性能和使用寿命。大型风机叶轮动平衡机作为保障叶轮动平衡的关键设备,有着多种不同的类型,以适应各种不同的应用场景和需求。 卧式动平衡机 卧式动平衡机是较为常见的一种类型。其工作原理是将风机叶轮水平放置在平衡机的支承上,通过驱动装置带动叶轮旋转。在旋转过程中,传感器会检测叶轮的不平衡量及其位置。这种动平衡机的优点十分显著,它的结构相对简单,操作较为方便,而且对于各种不同尺寸和形状的大型风机叶轮都有较好的适应性。不过,它也存在一定的局限性。由于叶轮是水平放置的,在测量一些重量较大的叶轮时,可能会受到重力的影响,导致测量结果存在一定的误差。 立式动平衡机 与卧式动平衡机不同,立式动平衡机是将风机叶轮垂直放置进行动平衡测量的。这种动平衡机特别适用于一些盘状或短轴类的大型风机叶轮。其优势在于能够有效避免重力对测量结果的影响,从而提高测量的精度。而且,立式动平衡机在安装和拆卸叶轮时更加方便快捷,能够节省大量的时间和人力成本。然而,它的适用范围相对较窄,对于一些长轴类或形状特殊的叶轮,可能无法进行有效的动平衡测量。 全自动动平衡机 随着科技的不断发展,全自动动平衡机应运而生。这种动平衡机集成了先进的自动化技术和智能化控制系统,能够自动完成叶轮的装夹、测量、计算和校正等一系列操作。它的测量速度快、精度高,而且能够大大减少人工干预,提高工作效率和产品质量。全自动动平衡机还可以通过网络与其他设备进行连接,实现数据的实时传输和共享,方便企业进行生产管理和质量控制。不过,全自动动平衡机的价格相对较高,对于一些小型企业来说,可能存在一定的经济压力。 现场动平衡机 现场动平衡机是一种可以在风机现场进行动平衡测量和校正的设备。它不需要将叶轮从风机上拆卸下来,而是直接在现场对叶轮进行动平衡调整。这种动平衡机具有灵活性强、操作简便等优点,能够有效缩短设备的维修时间,降低维修成本。在一些大型风力发电场或工业企业中,现场动平衡机可以在不影响生产的情况下,及时对风机叶轮进行动平衡校正,保证风机的正常运行。但是,现场动平衡机的测量精度相对较低,对于一些对动平衡要求较高的场合,可能无法满足需求。 大型风机叶轮动平衡机的不同类型各有其优缺点和适用范围。在实际应用中,企业需要根据自身的生产需求、叶轮的特点以及经济实力等因素,选择合适的动平衡机类型,以确保大型风机叶轮的动平衡质量,提高风机的性能和可靠性。
23
2025-06
大型风机叶轮动平衡机的平衡转速范围是···
大型风机叶轮动平衡机的平衡转速范围是多少 一、平衡转速的多维定义 平衡转速并非单一数值。它像交响乐中的音符,随工况变化而跳跃。在动平衡机领域,平衡转速范围是叶轮旋转时消除不平衡力矩的“黄金区间”,其边界由叶轮物理特性、设备承载极限及振动控制标准共同划定。例如,某型离心风机叶轮的平衡转速可能在800-1500 rpm间浮动,而轴流风机的临界转速可能突破2000 rpm。 二、影响转速范围的变量矩阵 叶轮几何拓扑:叶片数量、扭曲角度及轮毂直径构成“转速约束方程”。 6叶片叶轮的共振频率比4叶片低15%-20%,转速上限需下调。 轮毂直径每增加10%,临界转速可能提升8%。 材料疲劳阈值:钛合金叶轮的耐疲劳极限是钢制叶轮的2.3倍,允许更高转速。 工况压力场:高压环境下,气动载荷使转速上限降低10%-15%。 三、行业标准的博弈场 ISO 1940-1规定:平衡精度等级G0.4-G6.3对应转速需匹配振动幅值≤0.1mm/s。 API 617强调:压缩机叶轮平衡转速需高于设计转速10%-15%以规避喘振。 中国GB/T 29531-2013引入“动态不平衡系数”,允许转速范围弹性浮动±5%。 四、工程实践的动态调谐 某海上风电项目案例: 初始设计:叶轮平衡转速设定为1200 rpm(±5%)。 实测修正:因盐雾腐蚀导致材料刚度下降,转速下限调整至1120 rpm。 补偿策略:采用“分阶平衡法”,在800 rpm预平衡后,逐步提升至目标转速。 五、未来趋势:智能自适应平衡系统 新一代动平衡机通过嵌入式传感器实时监测转子动力学特性,结合机器学习算法动态调整平衡转速。例如,西门子开发的SINAMICS G120系统,可在3秒内完成转速自适应校准,使平衡效率提升40%。 结语 平衡转速范围是叶轮与动平衡机的“共舞契约”。它既是物理定律的产物,也是工程智慧的结晶。在追求高精度与高可靠性的道路上,每一次转速的微调都在书写风机动力学的新篇章。
23
2025-06
大型风机叶轮动平衡机适用于哪些行业
【大型风机叶轮动平衡机适用于哪些行业】 ——当精密平衡技术成为工业心脏的”隐形守护者” 在能源革命的浪潮中,大型风机叶轮动平衡机如何成为风电场的”隐形守护者”?当高铁轮对以350公里时速飞驰时,这台设备又如何确保每片叶片的振动误差控制在0.1毫米内?让我们以多棱镜视角透视这项技术的跨界应用。 一、能源矩阵的精密平衡者 风电领域:在内蒙古戈壁滩的百米高空,动平衡机正为直径15米的风机叶片进行”毫米级体检”。通过激光传感器捕捉0.05g的不平衡量,使每台风机年发电量提升3%-5%。 核能工程:秦山核电站的蒸汽发生器转子,需在2000℃高温下保持绝对平衡。动平衡机采用真空磁悬浮技术,将振动值控制在ISO G1.5标准,确保反应堆安全运行。 火力发电:某600MW机组的给水泵叶轮,经动平衡校正后,轴承温度下降8℃,单台机组年节约维护成本超200万元。 二、高端制造的精密标尺 航空航天:C919客机发动机的钛合金叶片,需在12000rpm转速下完成12级平衡校验。动平衡机通过频谱分析技术,消除0.02mm的微观形貌误差。 轨道交通:CR450动车组的驱动轮对,采用三维激光扫描+动态配重技术,使轮轨磨耗率降低40%,延长使用寿命至120万公里。 半导体产业:某8英寸晶圆切割机的主轴,经动平衡校正后,切割精度从±5μm提升至±2μm,良品率提高18%。 三、环保与重工业的平衡艺术 污水处理:某日处理50万吨的曝气风机,通过动平衡优化,单台设备年节电12万度,相当于减少70吨碳排放。 船舶制造:2.3万吨散货船的推进电机转子,采用水磁悬浮平衡技术,在海上恶劣工况下仍保持振动值低于0.7mm/s。 冶金行业:某高炉鼓风机的叶轮,经动平衡修复后,轴承更换周期从3个月延长至18个月,年节省备件费用超80万元。 四、跨界融合的创新应用 新能源汽车:某800V高压电机的转子,通过动平衡与磁性分析联动检测,将扭矩波动控制在0.3%以内,续航里程提升15公里。 建筑通风:上海中心大厦的3000m³/h轴流风机,采用在线平衡技术,实现边运行边校正,维护时间缩短80%。 农业机械:新疆采棉机的12米摘棉辊,通过动平衡优化,采净率从82%提升至91%,每亩增收棉花15公斤。 当精密平衡技术突破传统边界,这台看似普通的设备正在书写工业文明的新篇章。从微观的半导体晶圆到宏观的风电叶片,从陆地的高铁轮对到深海的船舶推进器,动平衡机正以毫米级的精度,守护着现代工业的每一次旋转。这种跨越物理形态的平衡艺术,不仅关乎效率与安全,更折射出智能制造时代对极致品质的永恒追求。