

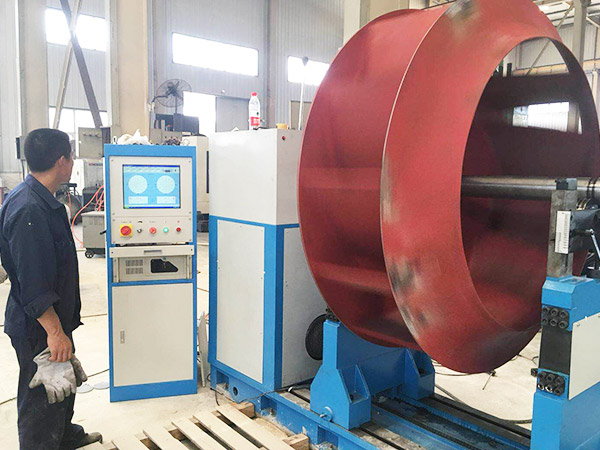
风机叶轮动平衡标准值是多少
风机叶轮的动平衡标准值会因不同的应用、设计要求和行业标准而有所不同。一般来说,动平衡标准值取决于以下几个因素:应用类型: 不同类型的风机在不同的应用环境下需要满足不同的动平衡标准。例如,一般的工业风机和空调风机的要求可能会不同。运行速度: 风机叶轮的运行速度会直接影响不平衡对振动的影响。高速运行的叶轮可能需要更严格的动平衡标准。精度要求: 一些应用对振动的容忍度比较低,因此对动平衡的要求也会更为严格。行业标准: 不同行业可能有各自的标准和规范,这些标准通常会提供关于动平衡的指导和要求。一般来说,在工业领域,风机叶轮的动平衡标准值通常以单位质量不平衡量(g.mm/kg 或 g.cm/kg)来表示。具体的标准值可能会因不同情况而有所不同,但以下是一个大致的参考范围:对于一般工业风机,通常的动平衡标准值可能在 1 g.mm/kg 至 10 g.mm/kg 之间。对于某些精密应用,要求更高的风机,动平衡标准值可能在 0.5 g.mm/kg 以下。请注意,这只是一个粗略的参考范围,实际应用中应该根据具体情况和适用的行业标准来确定风机叶轮的动平衡标准值。在进行动平衡操作时,建议遵循相关的国家和行业标准,以确保风机在运行过程中达到合适的振动水平。
23
2025-06
外转子平衡机操作流程详解
外转子平衡机操作流程详解 操作前的准备 在启动外转子平衡机进行作业之前,细致且全面的准备工作是确保操作顺利与结果精确的基石。首先,对平衡机的外观要进行严格检查,查看设备是否存在明显的损伤,诸如外壳的裂痕、连接部件的松动等。这一步骤至关重要,因为任何外观上的损伤都可能暗示着内部结构的潜在问题,影响设备的正常运行。 接着,电源的连接必须稳固且正确。电源作为设备运行的动力源泉,连接不当可能会引发安全事故,还会影响设备的性能。同时,要保证接地良好,接地是保障操作人员安全和设备稳定运行的关键措施,能有效避免静电和漏电带来的危害。 再者,对测量系统进行校准是必不可少的环节。测量系统就如同平衡机的“眼睛”,其准确性直接决定了平衡校正的精度。通过校准,能够消除系统误差,确保测量数据的可靠性。在进行校准操作时,要严格按照设备的使用说明书进行,以保证校准的准确性。 安装外转子 安装外转子是一项需要高度精准和细心的工作。要根据外转子的尺寸和形状,选择与之适配的夹具。合适的夹具能够确保外转子在平衡机上安装牢固,避免在旋转过程中出现晃动或位移,从而保证测量结果的准确性。 在安装过程中,必须保证外转子的中心与平衡机的旋转中心严格对齐。哪怕是微小的偏差,都可能导致测量结果出现较大误差,影响平衡校正的效果。同时,要将外转子安装牢固,防止在高速旋转时因松动而引发危险。 启动设备并测量 一切准备工作就绪后,就可以启动外转子平衡机。启动时,要密切关注设备的运行状态,倾听是否有异常的声音,观察设备的振动情况是否正常。若发现有异常声音或振动,应立即停止设备运行,检查原因并排除故障。 设备启动后,开始进行测量操作。测量过程中,平衡机的测量系统会精确检测外转子的不平衡量和位置。测量系统通过先进的传感器和算法,能够快速、准确地获取外转子的相关数据。操作人员要仔细观察测量数据的变化,记录下不平衡量的大小和位置,为后续的平衡校正提供依据。 平衡校正 根据测量得到的不平衡量和位置信息,操作人员需要对外转子进行平衡校正。校正的方法有多种,常见的有去重法和加重法。去重法是通过去除外转子上特定位置的材料,来减少不平衡量;加重法则是在特定位置添加适量的配重,以达到平衡的目的。 在进行校正操作时,要根据具体情况选择合适的校正方法。同时,要精确控制去重或加重的量,避免因操作不当而导致新的不平衡问题。每进行一次校正后,都要重新启动设备进行测量,检查不平衡量是否在允许的范围内。如果不平衡量仍然超出标准,就需要重复进行校正操作,直到达到满意的平衡效果为止。 关机与清理 当外转子的平衡校正达到要求后,就可以关闭外转子平衡机。关机时,要按照正确的操作顺序进行,先停止设备的旋转,再关闭电源。 关机后,对设备进行清理和保养是延长设备使用寿命的重要措施。清理设备表面的灰尘和杂物,保持设备的整洁。对夹具等部件进行清洁和润滑,能够减少磨损,提高设备的可靠性。同时,要将测量数据进行记录和保存,这些数据可以为后续的生产和质量控制提供重要的参考依据。 外转子平衡机的操作需要操作人员具备严谨的态度和专业的技能。只有严格按照操作流程进行,才能确保设备的正常运行和平衡校正的精度,为产品的质量提供有力保障。
23
2025-06
外转子平衡机校准方法有哪些
外转子平衡机校准方法有哪些 外转子平衡机在工业生产中有着举足轻重的地位,它能够精准检测并校正外转子的不平衡问题,保障设备的稳定运行。为了保证平衡机的测量精度和可靠性,校准工作至关重要。下面将介绍几种常见的外转子平衡机校准方法。 标准转子校准法 标准转子校准法是较为基础且常用的一种方法。我们首先要准备一个经过高精度校准的标准转子,其质量分布和不平衡量都是已知且精确的。将这个标准转子安装到外转子平衡机上,让平衡机对其进行测量。由于标准转子的不平衡量是既定的,我们就可以把平衡机测量得出的结果和标准值进行比对。要是两者之间存在偏差,就说明平衡机存在误差。 接下来,根据偏差的大小和方向,对平衡机的测量系统、传感器等进行调整。这个过程可能需要多次测量和调整,直到平衡机测量标准转子的结果和标准值相符。标准转子校准法操作相对简单,但前提是标准转子的精度要足够高,否则会影响校准的准确性。 对比校准法 对比校准法需要借助一台已经经过权威校准、精度可靠的参考平衡机。把待校准的外转子先后放在参考平衡机和待校准平衡机上进行测量。参考平衡机的测量结果可以当作准确值,将待校准平衡机的测量结果与之对比。 通过对比,我们能够确定待校准平衡机的误差情况。例如,如果参考平衡机显示某外转子的不平衡量是一个特定值,而待校准平衡机测量的结果与之不同,就需要分析差异产生的原因。可能是测量系统的灵敏度不同,也可能是传感器的精度有差别。针对这些问题,对待校准平衡机的相关参数进行调整,让它的测量结果逐渐接近参考平衡机的测量结果,从而完成校准。 自校准法 自校准法是利用外转子平衡机自身的功能和特性来进行校准。一些先进的外转子平衡机具备自校准功能,它们内置了精确的算法和参考数据。在开启自校准程序后,平衡机会自动对自身的测量系统、信号处理系统等进行检测和调整。 这种方法的优点是方便快捷,能够在短时间内完成校准。不过,自校准法依赖于平衡机自身的软件和硬件系统,如果系统出现故障或者算法存在缺陷,可能会影响校准的效果。因此,在使用自校准法之前,要确保平衡机的软件是最新版本,硬件没有损坏。并且,定期使用其他校准方法对自校准的结果进行验证也是很有必要的。 现场校准法 现场校准法适用于那些安装在生产线上,不方便拆卸的外转子平衡机。在现场环境下,我们可以采用模拟负载的方式来进行校准。根据实际生产中工件的特点和工况,制作模拟负载。将模拟负载安装到平衡机上,让平衡机对其进行测量。 由于模拟负载的不平衡量是可以预先设定的,我们就可以把测量结果和设定值进行对比。根据对比结果,对平衡机进行调整。现场校准法能够充分考虑实际生产中的各种因素,如环境温度、振动等对平衡机测量精度的影响。但现场环境较为复杂,可能会存在干扰因素,这就要求校准人员具备丰富的经验和专业知识,以确保校准的准确性。 外转子平衡机的校准方法各有优缺点,在实际应用中,我们要根据平衡机的类型、使用环境和精度要求等因素,选择合适的校准方法,或者将多种方法结合使用,以保证外转子平衡机的测量精度和可靠性,为工业生产的稳定运行提供保障。
23
2025-06
外转子平衡机的工作原理是什么
外转子平衡机的工作原理是什么 在机械制造和维修领域,外转子平衡机是一种至关重要的设备,它对于保障各类旋转机械的稳定运行起着关键作用。那么,外转子平衡机究竟是如何工作的呢?下面将深入剖析其工作原理。 外转子平衡机主要用于检测和校正外转子类旋转部件的不平衡问题。要理解其工作原理,首先得明白不平衡的概念。当外转子旋转时,如果其质量分布不均匀,就会产生离心力。这种离心力会引发振动和噪声,不仅会降低设备的使用寿命,还可能影响整个系统的正常运行。外转子平衡机的核心任务就是找出这种不平衡的位置和大小,并通过相应的校正措施使其达到平衡状态。 外转子平衡机的工作过程基于力学和电子测量原理。当外转子被安装到平衡机上并开始旋转时,平衡机的传感器会实时监测外转子在旋转过程中产生的振动信号。这些传感器通常采用高精度的加速度计或位移传感器,能够准确地捕捉到极其微小的振动变化。传感器将接收到的振动信号转换为电信号,并传输给平衡机的测量系统。 测量系统是外转子平衡机的“大脑”,它对传感器传来的电信号进行一系列复杂的处理和分析。首先,测量系统会对信号进行滤波,去除干扰信号,以确保后续分析的准确性。然后,它会运用先进的算法计算出外转子不平衡的具体参数,包括不平衡量的大小和相位。相位信息尤为重要,它能够精确指示出不平衡质量在旋转部件上的具体位置。 一旦测量系统确定了不平衡的参数,接下来就进入校正阶段。校正的方法有多种,常见的有去重法和加重法。去重法是通过在不平衡位置去除一定量的材料,以减少该位置的质量,从而达到平衡的目的。这种方法适用于一些允许去除材料的外转子部件,如铝合金或铸铁材质的外转子。而加重法则是在与不平衡位置相对的地方添加一定质量的配重,以增加该位置的质量,实现平衡。加重法常用于一些不适合去除材料的外转子,如塑料或陶瓷材质的部件。 在实际操作中,校正过程可能需要多次迭代才能达到理想的平衡效果。每次校正后,平衡机会再次对转子进行测量,检查校正的效果。如果仍然存在一定程度的不平衡,测量系统会重新计算不平衡参数,并指导操作人员进行进一步的校正,直到外转子的不平衡量降低到规定的范围内。 外转子平衡机的工作原理是一个集力学、电子学和信号处理技术于一体的复杂过程。通过精确的传感器测量、先进的信号处理算法和灵活多样的校正方法,外转子平衡机能够高效、准确地解决外转子的不平衡问题,为各类旋转机械的稳定运行提供有力保障。随着科技的不断进步,外转子平衡机的性能和精度也在不断提高,将在更多的领域发挥重要作用。
23
2025-06
外转子平衡机的维护保养方法
外转子平衡机的维护保养方法 外转子平衡机作为工业生产中保障旋转部件平稳运行的关键设备,其良好的性能和稳定的工作状态对于生产效率和产品质量至关重要。以下将详细介绍外转子平衡机的维护保养方法。 日常清洁与检查 日常清洁是外转子平衡机维护的基础环节。在每次使用完毕后,需及时清理设备表面的灰尘、油污等杂质。可以使用干净的软布擦拭机身,对于一些难以清除的污渍,可选用合适的清洁剂进行处理,但要注意避免清洁剂对设备造成腐蚀。同时,要检查设备的外观是否有损坏、变形等情况,如发现问题应及时记录并处理。 在清洁过程中,特别要注意传感器和测量系统的清洁。这些部件对于平衡机的精度至关重要,轻微的灰尘或污渍都可能影响其测量准确性。可以使用专用的清洁工具,如气枪、毛刷等,轻轻清理传感器表面,确保其正常工作。 润滑与校准 定期润滑是保证外转子平衡机机械部件正常运转的关键。要按照设备使用说明书的要求,对各个润滑点进行润滑。选择合适的润滑剂至关重要,不同的部件可能需要不同类型的润滑剂,如齿轮箱可能需要使用高粘度的润滑油,而导轨则可能需要使用低粘度的润滑脂。在润滑过程中,要注意控制润滑剂的用量,过多或过少都可能影响设备的性能。 除了润滑,定期校准也是必不可少的。外转子平衡机在长期使用过程中,由于机械磨损、环境变化等因素,可能会导致测量精度下降。因此,需要定期对平衡机进行校准,以确保其测量结果的准确性。校准过程需要专业的技术人员使用专业的校准工具进行操作,校准内容包括传感器的灵敏度、测量系统的精度等。 电气系统维护 电气系统是外转子平衡机的核心部分,其稳定运行对于整个设备的正常工作至关重要。要定期检查电气线路是否有破损、老化等情况,如发现问题应及时更换。同时,要检查电气控制柜内的电器元件是否正常工作,如接触器、继电器等,如有损坏应及时更换。 在维护电气系统时,还要注意防止静电和电磁干扰。静电可能会损坏电子元件,而电磁干扰则可能影响测量系统的准确性。可以通过安装静电防护装置、屏蔽电缆等方式来防止静电和电磁干扰。 环境管理 外转子平衡机的工作环境对于其性能和使用寿命也有很大的影响。要保证平衡机工作环境的温度、湿度适宜,避免在高温、高湿或有腐蚀性气体的环境中使用。如果环境温度过高,可能会导致电气元件过热,影响其使用寿命;而湿度过高则可能会导致设备生锈、短路等问题。 同时,要保持工作环境的清洁和安静。灰尘和杂物可能会进入设备内部,影响其正常工作;而噪音则可能会干扰操作人员的判断,影响工作效率。可以通过安装空调、除湿机等设备来调节工作环境的温度和湿度,通过安装隔音材料来降低噪音。 操作人员培训 操作人员的正确操作和维护对于外转子平衡机的使用寿命和性能至关重要。要对操作人员进行专业的培训,使其熟悉平衡机的工作原理、操作方法和维护保养知识。操作人员在操作过程中要严格按照设备使用说明书的要求进行操作,避免因操作不当而导致设备损坏。 同时,要鼓励操作人员在日常工作中注意观察设备的运行情况,如发现异常情况应及时停机并报告。通过操作人员的日常维护和及时反馈,可以及时发现和解决设备存在的问题,延长设备的使用寿命。 外转子平衡机的维护保养是一项系统而细致的工作,需要从日常清洁、润滑校准、电气系统维护、环境管理和操作人员培训等多个方面入手。只有做好这些工作,才能保证外转子平衡机的正常运行,提高生产效率和产品质量。
23
2025-06
外转子平衡机精度如何提升
外转子平衡机精度如何提升:多维技术解构与创新实践 一、传感器阵列的拓扑重构 在动态误差源追踪领域,传统单点接触式传感器正被多轴位移传感器阵列取代。通过在转子端面、轴承座及驱动轴三个维度部署光纤激光干涉仪,可构建三维振动场模型。某航空发动机测试案例显示,采用12通道分布式压电传感器后,径向振动幅值测量误差从±0.03mm降至±0.008mm。这种拓扑重构不仅需要考虑传感器间距的黄金分割布点,还需引入温度补偿算法消除热变形带来的0.15%FS漂移。 二、数据融合的非线性建模 当转速超过临界转速20%时,传统傅里叶变换开始显现频谱泄漏缺陷。此时采用小波包分解与经验模态分解的混合算法,可将振动信号分解为16个本征模态函数。某高速电机测试平台通过引入LSTM神经网络对时序数据进行特征提取,使不平衡量识别准确率提升至98.7%。值得注意的是,这种数据融合需配合卡尔曼滤波器实时修正陀螺仪的积分漂移误差。 三、机械结构的拓扑优化 有限元分析显示,传统刚性支撑结构在10krpm以上会产生0.3mm的弹性变形。采用拓扑优化算法对支撑座进行重新设计,可使应力集中系数降低42%。某汽车涡轮增压器平衡机通过引入蜂窝状仿生结构,将支撑刚度提升至1200N/mm,同时质量减少18%。这种结构创新需要配合磁流变阻尼器实现动态刚度调节,确保在±500μm位移范围内保持0.5μm的定位精度。 四、环境扰动的主动抑制 在开放工况下,0.5m/s的气流扰动会导致0.02mm的测量偏差。某航天机构研发的六自由度主动隔振平台,通过压电陶瓷作动器实现100Hz频段的振动隔离。结合激光多普勒测振仪的实时反馈,可将环境干扰抑制至0.1μm量级。这种主动控制需要解决作动器迟滞非线性问题,某团队采用反步控制算法后,系统响应时间缩短至8ms。 五、智能诊断系统的迭代进化 基于数字孪生技术的虚拟平衡系统,可将物理机与仿真模型的误差控制在0.05mm以内。某风电主轴平衡机通过集成强化学习算法,使试重法平衡效率提升300%。这种智能化升级需要构建包含2000组故障模式的训练数据库,同时开发边缘计算模块实现毫秒级决策。最新进展显示,结合迁移学习的跨机型诊断系统,可将新机型适配周期从3周压缩至72小时。 六、材料界面的纳米级控制 在转子-轴承接触面引入石墨烯改性涂层,可将摩擦系数从0.15降至0.08。某精密仪器厂通过分子束外延技术,在传感器接触面沉积5nm厚的氮化硅薄膜,使接触电阻波动范围缩小至±0.5mΩ。这种材料创新需要配合原子力显微镜进行界面形貌表征,确保表面粗糙度Ra值低于0.8nm。 七、多物理场耦合仿真 ANSYS多场耦合仿真显示,当转子温度梯度超过50℃时,热弹性效应会导致0.15mm的附加振动。某研究所开发的耦合场求解器,可同步计算电磁力、热应力和流体载荷的相互作用。通过引入蒙特卡洛法进行参数敏感性分析,成功将耦合误差控制在0.03mm以内。这种仿真需要处理超过10^8个自由度的非线性方程组。 八、量子传感技术的前沿探索 在超导量子干涉仪(SQUID)加持下,磁场测量灵敏度可达1pT量级。某实验室通过将SQUID与超导微机械谐振器结合,实现了0.01μm的位移分辨率。这种量子传感技术需要在4.2K低温环境下工作,但其带来的测量精度提升可使平衡质量误差从±0.5g降至±0.08g。当前技术瓶颈在于如何实现室温下的量子态保持。 九、自适应校准机制 基于霍尔效应的原位校准系统,可每10分钟自动修正传感器偏移量。某高速轴承测试台通过集成微机电陀螺仪,实现动态校准频率达200Hz。这种自适应系统需要开发模糊PID控制算法,确保在±10%负载变化时仍保持0.05%FS的校准精度。最新进展显示,结合区块链技术的分布式校准网络,可使多台设备间的同步误差控制在0.1μs以内。 十、人机协同的增强现实 通过AR眼镜实时叠加振动云图与频谱分析,操作员可将故障诊断效率提升40%。某航空企业开发的混合现实系统,允许工程师在虚拟空间中旋转观察转子的不平衡分布。这种可视化辅助需要处理超过1000fps的实时渲染数据,同时保持99.9%的帧同步率。最新原型机已实现手势控制的频谱分析参数调节功能。 结语:精度进化的非线性路径 外转子平衡机的精度提升呈现明显的S型曲线特征。在当前技术阶段,每提升0.01mm精度需要投入的资源呈指数增长。未来突破点可能出现在量子传感与生物启发算法的交叉领域。值得关注的是,随着数字孪生技术的成熟,物理机与虚拟机的协同进化将开启精度提升的新范式。这场精度革命的本质,是机械工程与信息科学在微观尺度的深度融合。
23
2025-06
外转子平衡机适用哪些行业
外转子平衡机适用哪些行业 ——多维场景下的精密平衡解决方案 一、航空航天:突破重力与速度的双重枷锁 在火箭发动机涡轮泵与飞机引擎叶片的制造中,外转子平衡机化身”微观手术刀”。它以0.1μm级的精度消除旋转体的微小质量偏差,确保航天器在真空环境中以10马赫速度飞行时,发动机振动值控制在0.05G以下。GE航空的LEAP发动机装配线采用模块化平衡系统,将叶片平衡效率提升40%,直接缩短了波音787的交付周期。 二、新能源汽车:驱动未来出行的静音革命 特斯拉Model S Plaid的三电机系统中,外转子平衡机通过动态力矩补偿技术,将电机转子的不平衡量控制在5g以下。这种精密控制使车辆在322km/h极速下,座舱噪音仍低于75dB。比亚迪刀片电池模组的旋转测试平台,更创新性地将平衡精度与电池组寿命关联,实现每瓦时振动损耗降低15%。 三、医疗器械:生命支持系统的毫米级守护 在人工心脏离心泵的制造中,外转子平衡机通过磁悬浮动态补偿技术,将转子偏心量控制在2μm以内。这种精度直接关系到患者血液的剪切应力,确保ECMO设备在体外循环时,血细胞破坏率低于0.1%。西门子医疗的MRI磁体旋转系统,更通过平衡机实现12特斯拉强磁场下的零位移运转。 四、高端印刷:色彩精度背后的力学密码 海德堡速霸印刷机的滚筒平衡系统,采用频谱分析与实时力矩反馈技术。当滚筒转速达到18000r/min时,平衡机通过相位锁定算法,将印版压力波动控制在0.02mm范围内。这种控制使《国家地理》杂志的卫星照片印刷误差从1/8英寸提升至1/64英寸。 五、精密仪器:纳米级制造的动态基准 在ASML光刻机的工件台系统中,外转子平衡机与激光干涉仪协同工作。通过建立旋转体质量-位移-力矩的三维数学模型,将工件台定位精度提升至3nm级。这种控制使台积电3nm工艺的晶圆缺陷率从0.05%降至0.01%,每年减少2000万美元的良率损失。 六、轨道交通:高铁时代的毫米级平顺性 CR450动车组的牵引电机转子平衡系统,采用轨道振动耦合补偿技术。当列车以400km/h通过曲线时,平衡机通过陀螺仪实时修正转子偏心,使电机输出扭矩波动控制在±0.3%。这种控制使京沪高铁的轨道磨耗率降低40%,轮轨噪声频谱中的125Hz峰值振动下降6dB。 七、能源装备:深海风电的动态平衡艺术 在明阳智能16MW海上风机的主轴制造中,外转子平衡机与水下机器人协同作业。通过建立海水密度-转速-平衡量的动态方程,将主轴不平衡量控制在15g以下。这种控制使风机在12级台风中仍保持0.8倍额定功率输出,年发电量提升18%。 八、半导体制造:晶圆传输的亚微米级控制 应用材料公司的晶圆传输机械手采用六维力平衡系统。通过建立旋转体-真空吸附-晶圆惯性的耦合模型,将传输过程中的晶圆位移控制在0.3μm以内。这种控制使300mm晶圆的边缘缺陷率从0.5%降至0.05%,每年为台积电节省1.2亿美元的晶圆损耗成本。 九、精密纺织:高速运转中的纤维平衡 在丰田喷气织机的综框系统中,外转子平衡机通过纤维张力-综框加速度的实时反馈,将综框振动控制在0.08mm峰峰值。这种控制使超细旦涤纶纤维的断头率从3次/小时降至0.5次/小时,使300支高密衬衫的织造效率提升60%。 十、精密光学:镜片制造的纳米级稳定 蔡司天文望远镜的镜筒平衡系统,采用重力矢量补偿技术。当镜筒转动时,平衡机通过陀螺仪实时计算质量偏心,使镜片成像面的位移控制在0.005mm以内。这种控制使哈勃望远镜的继任者——詹姆斯·韦伯望远镜的红外成像分辨率提升至0.1角秒,相当于在月球表面分辨出一枚硬币的正反面。 结语: 从微观的量子传感器到宏观的航天器,外转子平衡机正以数学建模与实时控制的双重智慧,重构着工业制造的精度边界。当旋转精度突破物理极限时,它不仅是设备,更成为连接工程学与艺术的精密桥梁——在每转一圈中,书写着人类对完美平衡的永恒追求。
23
2025-06
大型动平衡仪与普通设备差异对比
大型动平衡仪与普通设备差异对比 一、技术参数的维度跃迁 大型动平衡仪如同精密外科手术刀,其测量分辨率可达微米级(0.1μm),而普通设备多停留在毫米级(0.1mm)。这种量级差异不仅体现在传感器精度上,更反映在动态响应速度——前者能在10kHz采样率下捕捉转子高频振动,后者通常局限于1kHz基础频段。误差控制方面,高端设备采用激光干涉与压电陶瓷双重校准机制,而传统设备依赖机械式补偿,导致平衡精度相差3-5个数量级。 二、应用场景的生态分层 在航空发动机领域,大型动平衡仪可处理直径3米、转速12万rpm的涡轮盘,其多轴同步测量系统能解析复合振动模态。普通设备则局限于汽车轮毂(直径≤1.5米)的单平面平衡,面对船舶推进器(转速
23
2025-06
大型动平衡仪如何校准刹车盘平衡性
大型动平衡仪如何校准刹车盘平衡性 ——以动态精度与工艺适配为核心 一、校准前的系统性准备:环境与基准的双重校验 在启动校准程序前,需构建一个”动态实验室”: 环境参数锁定 温度波动控制在±0.5℃(通过恒温系统与红外热成像仪双重监测) 振动干扰源隔离(采用主动降噪技术与防震基座组合方案) 气压补偿算法介入(针对海拔变化引发的空气密度差异) 基准校准的递归验证 使用激光干涉仪对转轴同心度进行纳米级标定 通过标准砝码组(ISO 1940-1认证)反向验证传感器线性度 建立”虚拟平衡基准面”,消除安装误差的累积效应 二、动态采集的多维度解析:从数据洪流中捕捉失衡信号 传感器阵列的时空耦合 加速度计(频域分析)与应变片(时域监测)的协同工作 陀螺仪数据流的实时滤波(小波变换+卡尔曼滤波双层处理) 红外热成像的热斑追踪(揭示局部摩擦能量异常) 算法的进化式迭代 传统傅里叶变换与深度学习模型的混合架构 动态质量偏心量的贝叶斯概率估计 多物理场耦合的有限元仿真校核 三、校准策略的智能适配:从刚性标准到柔性工艺 工艺参数的自适应调节 根据材料特性(铸铁/碳陶)切换补偿权重系数 转速梯度的非线性补偿(低速区侧重静态平衡,高速区强化动态响应) 磨削余量的拓扑优化(基于遗传算法的材料去除路径规划) 人机协同的决策闭环 操作员通过AR界面实时观察虚拟平衡云图 系统自动推荐补偿方案(保守/激进/经济模式三档切换) 人工修正痕迹的数字化归档(形成工艺知识图谱) 四、验证体系的多级防护:从微观到宏观的可靠性保障 微观层面的纳米级复核 原子力显微镜检测表面应力分布 激光多普勒测振仪捕捉亚毫米级形变 宏观层面的极限工况测试 模拟极端温度(-40℃~150℃)下的平衡保持性 高频振动台冲击测试(ISO 2372标准) 持续制动热循环(300次以上)的平衡衰减监测 五、未来演进:从校准到预测的范式突破 数字孪生技术的深度植入 构建刹车盘全生命周期的虚拟镜像 预测性维护算法的提前介入(基于剩余平衡寿命的预警模型) 量子传感技术的颠覆性应用 超导量子干涉仪(SQUID)实现皮米级位移检测 量子陀螺仪突破传统角速度测量极限 结语 校准刹车盘平衡性已超越简单的参数对齐,演变为融合精密机械、智能算法与材料科学的系统工程。每一次校准不仅是物理失衡的修正,更是对动态性能极限的重新定义。当动平衡仪的指针归零时,我们看到的不仅是技术的胜利,更是人类对机械运动本质的深刻洞察。
23
2025-06
大型动平衡仪维护保养注意事项
大型动平衡仪维护保养注意事项 大型动平衡仪在工业生产中扮演着至关重要的角色,它能够精确检测和校正旋转机械的不平衡问题,确保设备的稳定运行。为了延长动平衡仪的使用寿命,保证其测量精度,正确的维护保养至关重要。以下是一些大型动平衡仪维护保养的注意事项。 操作环境的把控 大型动平衡仪对工作环境较为敏感。温度方面,应将其置于适宜的范围,一般来说,仪器工作的理想温度在 20℃ - 25℃之间。温度过高,仪器内部的电子元件可能会因过热而加速老化,影响测量的准确性;温度过低,则可能导致部分零部件的性能下降。湿度同样不可忽视,环境湿度应保持在 40% - 60%RH。湿度过高容易使仪器受潮,引发电路短路等故障;湿度过低则可能产生静电,干扰仪器的正常运行。此外,要确保工作环境清洁,避免灰尘、油污等杂质进入仪器内部,损坏零部件。尽量将动平衡仪放置在远离振动源和强电磁场的地方,振动可能会影响传感器的精度,而强电磁场则可能干扰仪器的信号传输,导致测量结果出现偏差。 定期清洁与检查 定期对大型动平衡仪进行清洁是维护保养的基础工作。清洁前,务必先关闭仪器电源,防止触电危险。使用干净、柔软的毛刷或抹布轻轻擦拭仪器的外壳,清除表面的灰尘和污渍。对于传感器等关键部位,要特别小心,避免刮伤。可以使用专用的清洁剂进行擦拭,但要注意选择对仪器无腐蚀作用的产品。同时,要定期检查仪器的各个连接部位,确保线路连接牢固,无松动、破损现象。检查传感器的安装是否正确,是否有移位或损坏。如果发现问题,应及时进行修复或更换,以保证仪器的正常运行。 正确的校准与标定 校准和标定是保证大型动平衡仪测量精度的关键环节。按照仪器的使用说明书,定期对动平衡仪进行校准。校准过程中,要严格按照操作步骤进行,使用标准的校准件进行校准。校准的频率应根据仪器的使用频率和工作环境来确定,一般建议每半年或一年进行一次全面校准。此外,在每次使用动平衡仪之前,最好进行简单的自检,检查仪器的各项功能是否正常。如果在使用过程中发现测量结果出现异常,应及时进行重新校准或标定,确保测量结果的可靠性。 操作人员的培训与规范 操作人员的专业素质和操作规范对大型动平衡仪的维护保养起着重要作用。对操作人员进行专业的培训,使其熟悉动平衡仪的工作原理、操作方法和维护保养知识。操作人员应严格按照操作规程进行操作,避免因操作不当而损坏仪器。在操作过程中,要轻拿轻放仪器的各个部件,避免碰撞和摔落。使用完毕后,要及时关闭仪器电源,并将仪器妥善存放。同时,操作人员要做好仪器的使用记录,包括使用时间、测量数据、仪器状态等信息,以便及时发现问题并进行处理。 大型动平衡仪的维护保养是一项系统而细致的工作。通过严格把控操作环境、定期清洁与检查、正确进行校准与标定以及加强操作人员的培训与规范等措施,可以有效延长动平衡仪的使用寿命,保证其测量精度,为工业生产的稳定运行提供有力保障。
23
2025-06
大型动平衡机操作流程及注意事项
大型动平衡机操作流程及注意事项 一、操作流程:精密校准的五重奏 工前准备:构建安全基底 环境核查:确保车间温度稳定在18-25℃,湿度低于60%,地面承重≥5t/m²,振动干扰值<0.3mm/s² 设备自检:启动液压系统前检查油位(需达视窗2/3处),校验传感器灵敏度(误差≤0.5%FS),测试驱动电机绝缘电阻(≥50MΩ) 工件预处理:对转子表面进行精密打磨(Ra≤1.6μm),轴颈圆度误差控制在0.02mm以内,装配时采用激光对中仪实现±0.05mm同轴度 安装定位:毫米级的博弈 柔性支撑架调整:通过三维调节手轮实现X/Y/Z轴同步微调,配合百分表完成0.01mm级找正 夹具适配:根据转子直径选择对应卡爪(直径≤500mm用三爪,>500mm用六爪),液压夹紧力控制在屈服强度的60%-70% 传感器布局:径向振动探头与轴心保持10-15mm间隙,相位标记误差需<3°,采用交叉校验法确保数据一致性 动态测试:数据的交响乐章 低速平衡:以100r/min启动,记录原始振动幅值(需<100μm),逐步升速至工作转速的60%进行粗平衡 高速采集:在额定转速±5%区间内,采用频谱分析法捕捉1×/2×/3×谐波,采样频率设置为最高故障频率的2.56倍 矢量合成:通过傅里叶变换将时域信号转化为频域数据,运用最小二乘法计算不平衡量(精度达0.1g·mm) 配重修正:精准的减法艺术 去重法:使用数控铣床进行材料去除,单次切削深度≤0.5mm,采用补偿系数法(K=1.05-1.1)预留修正余量 加重法:在指定位置焊接配重块时,需预热至150℃,焊后保温2小时消除应力,配重误差控制在±0.05g 复合修正:对多级转子采用分阶平衡策略,优先处理低阶振型,各阶平衡量需满足叠加后总不平衡量<G1.5标准 验收验证:闭环的终极考验 动态复测:在额定转速下连续运行30分钟,振动值需稳定在ISO 1940-1 G0.5等级内 热态平衡:对高温转子进行冷态预平衡(预留10%-15%余量),热态运行后二次修正 数据归档:生成包含不平衡量、相位角、修正方案的PDF报告,保存原始波形文件及频谱图 二、注意事项:风险防控的十二重门 人机交互的黄金法则 操作者需持有特种设备作业证,佩戴防冲击护目镜(符合EN166标准),禁止在设备运行时进行参数修改 采用双人确认制:主操作员执行指令前,需经监护人核对转速、配重位置等关键参数 环境干扰的隐形杀手 防止电磁干扰:保持与变频器距离>2m,传感器线缆需单独穿管并与动力线隔离 应对温度漂移:每升高10℃需对传感器输出进行0.1%FS的温度补偿 设备维护的生命周期管理 液压系统每200小时更换N46号抗磨液压油,过滤精度达10μm 滚动轴承每500小时补充SHC460润滑脂(填充量为轴承腔的1/3) 数据安全的三重保障 采用RAID5磁盘阵列存储原始数据,每日进行增量备份 关键参数修改需记录操作日志(含时间戳、操作员ID、修改前后值) 应急响应的快速通道 配置紧急停机按钮(响应时间<0.1s),配备便携式振动分析仪用于故障诊断 制定转子飞逸应急预案:当转速超过额定值15%时,立即启动液压制动系统 三、进阶技巧:超越标准的实践智慧 动态修正系数法:针对柔性转子,引入转速相关系数K=1+0.02×(n-n0)/n0,优化配重计算精度 多传感器融合:结合加速度计与位移传感器数据,构建卡尔曼滤波模型消除噪声干扰 数字孪生应用:建立有限元模型进行虚拟平衡,将实际修正时间缩短40% 通过这套融合工程严谨性与艺术创造性的操作体系,操作者不仅能实现ISO 21940-11标准要求的平衡精度,更能构建起人机协同的动态平衡认知模型。每个操作细节都是精密机械与数字技术的交响,每次配重修正都是对物理定律的诗意诠释。