

动平衡机加工中“分辨率”参数对微小不平衡量的检测能力
- 分类:行业新闻
- 作者:申岢编辑部
- 来源:上海申岢动平衡机制造有限公司
- 发布时间:2025-04-21
- 访问量:72
在动平衡机加工中,“分辨率”(Resolution)是一个关键参数,直接影响设备对微小不平衡量的检测能力。以下从定义、影响机制和实际应用角度详细分析其作用:
1. 分辨率的定义
分辨率是指动平衡机能够识别的最小不平衡量变化值,通常以单位质量(如克·毫米,g·mm)或角度(如度)表示。例如,分辨率为0.01g·mm的动平衡机可以检测到比此值更大的不平衡量变化,而更小的变化可能被忽略。
2. 分辨率对检测能力的影响
(1) 微小不平衡量的检测阈值
高分辨率:设备可检测到更小的不平衡量变化,适用于精密零部件(如航空航天部件、微型电机转子等),避免因微小失衡导致的振动或噪音。
低分辨率:可能无法有效识别微小不平衡,导致校正后残留不平衡量超标,影响设备运行稳定性。
(2) 信号噪声与信噪比
分辨率受限于动平衡机的信号采集系统(如传感器、AD转换器)的信噪比(SNR)。若噪声水平接近或超过分辨率,微小不平衡信号会被噪声掩盖,导致检测失效。
提高分辨率的方法:优化传感器灵敏度、降低电路噪声、增强数字滤波算法。
(3) 动态范围与精度
分辨率与动态范围相关。动态范围越大,设备既能检测微小不平衡,也能处理较大的初始不平衡量,但需平衡两者的技术实现难度。
3. 影响分辨率的因素
(1) 传感器性能
传感器(如压电式、电容式传感器)的灵敏度和线性度直接影响分辨率。高精度传感器可捕捉更微弱的振动信号。
(2) 信号处理技术
模数转换器(ADC)的位数(如16位 vs. 24位)决定了信号量化精度。
数字滤波算法(如FFT分析)可提取有效信号,抑制噪声。
(3) 机械结构刚性
机械框架的刚性不足会导致振动信号衰减或失真,降低有效分辨率。
(4) 环境干扰
温度波动、外部振动、电磁干扰等会引入噪声,需通过隔离设计或补偿算法降低影响。
4. 实际应用中的优化策略
(1) 根据需求选择设备
精密加工(如硬盘转子、医疗器械):选择分辨率≤0.1g·mm的高端动平衡机。
常规工业应用(如汽车轮毂):分辨率1-10g·mm的中端设备即可满足。
(2) 校准与维护
定期校准传感器和系统,确保分辨率符合标称值。
清洁转子和夹具,避免异物干扰测量。
(3) 工艺参数优化
转速选择:在共振频率附近测量可提高灵敏度,但需避免机械共振风险。
校正策略:多次迭代校正可逐步逼近目标不平衡量,弥补分辨率不足。
5. 案例分析
- 案例1:某微型电机转子动平衡要求残留不平衡量≤0.05g·mm。若动平衡机分辨率为0.1g·mm,则无法满足需求,需升级设备。
- 案例2:汽车轮胎动平衡机分辨率通常为1g·mm,可检测轮胎微小失衡,但若环境振动过大,实际分辨率会下降,需增加隔振措施。
6. 总结
分辨率是动平衡机检测微小不平衡量的核心参数,需结合传感器性能、信号处理技术、机械设计和环境控制综合提升。实际应用中需根据工件精度要求、成本预算和工艺条件合理选择设备,并通过优化操作流程最大化分辨率的价值。对于超精密领域,分辨率不足可能导致产品失效,而工业场景中过度追求高分辨率可能增加不必要的成本。
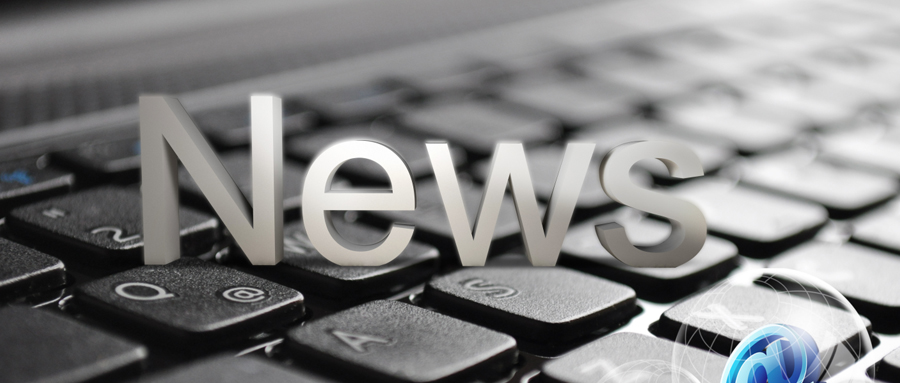