Copyright © 2003-2019 上海申岢动平衡机制造有限公司, All Rights Reserved 沪ICP备16012006号-5 友情链接:
上海动平衡机
搜索


如何通过动平衡机数据优化机床主轴装配工艺
- 分类:行业新闻
- 作者:申岢编辑部
- 来源:上海申岢动平衡机制造有限公司
- 发布时间:2025-04-17
- 访问量:87
通过动平衡机数据优化机床主轴装配工艺,需要结合数据采集、分析和工艺调整,以提高主轴的平衡精度和运行稳定性。以下是具体步骤和方法:
1. 数据采集与初步分析
- 关键数据获取:
- 不平衡量(单位:g·mm):动平衡机测量主轴在特定转速下的不平衡质量分布。
- 相位角:不平衡质量的位置(角度)。
- 振动幅值:不同转速下的振动频谱数据。
- 数据标准化:
- 建立统一的数据记录格式(如转速、不平衡量、相位角、环境温度等)。
- 使用动平衡机软件导出完整测试报告,包括静态和动态平衡数据。
2. 不平衡原因诊断
- 常见问题分类:
- 装配误差:轴承预紧力不均、零部件配合间隙过大。
- 材料缺陷:主轴或刀具材质不均匀。
- 加工误差:轴颈、法兰盘等关键部位的同轴度/圆度超差。
- 数据分析方法:
- 对比不同批次或同一主轴多次装配的数据,识别重复性偏差。
- 结合振动频谱分析,判断不平衡是否由共振或外部干扰引起。
3. 工艺优化策略
(1)预平衡装配
分阶段平衡:
- 粗平衡:在主轴组件(如轴芯、法兰)单独装配时进行预平衡。
- 精平衡:整体装配后再次测试,减少累计误差。
组件匹配优化:
通过动平衡数据筛选匹配的轴承、刀具等组件(例如选择不平衡量互补的零件)。
(2)配重调整
配重位置优化:
- 根据相位角数据,在主轴对称位置(如平衡环、螺纹孔)增减配重块。
- 采用去重法(钻孔、铣削)或加重法(焊接配重块)修正不平衡量。
动态平衡修正:
对高速主轴(如 >10,000 RPM),需在多个转速点测试并优化平衡方案。
(3)装配流程改进
关键参数控制:
- 规定轴承预紧力矩、锁紧螺母拧紧顺序等工艺参数。
- 使用工装夹具确保同轴度(如跳动量 ≤0.005 mm)。
工艺防错设计:
- 在装配流程中嵌入动平衡测试节点(例如每完成一个组件装配后测试一次)。
4. 验证与持续改进
- 平衡效果验证:
- 优化后复测动平衡数据,确保剩余不平衡量符合标准(如ISO 1940 G1级)。
- 模拟实际工况(如加载切削力)验证主轴稳定性。
- 数据驱动迭代:
- 建立历史数据库,分析长期数据趋势,优化工艺参数阈值。
- 应用机器学习算法(如回归模型)预测最优配重方案。
5. 案例参考
- 实际应用:
- 某机床厂通过分析动平衡数据,发现刀具夹头的不对称性是主要问题。优化夹头安装工艺后,主轴振动降低40%。
- 使用激光动平衡机实时反馈数据,配合自动配重系统,实现装配效率提升30%。
6. 工具与技术建议
- 设备:选择高精度动平衡机(如申岢、Hofmann),支持多平面平衡校正。
- 软件:使用分析软件(如Balancing Technologies Inc.的BTI软件)进行频谱分析和趋势预测。
- 自动化:集成机器视觉或机器人系统,实现配重自动调整。
通过以上方法,可系统性地利用动平衡机数据优化主轴装配工艺,显著提高加工精度和设备寿命,同时降低维护成本。
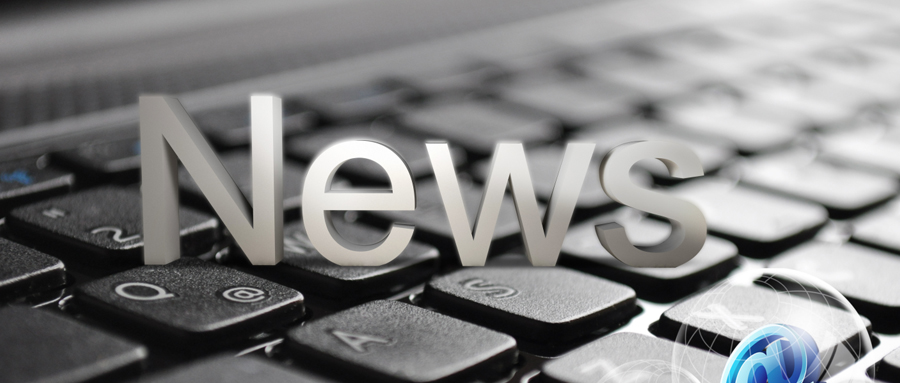