

机床主轴平衡机:精密制造背后的隐形守护者
- 分类:行业新闻
- 作者:申岢编辑部
- 来源:上海申岢动平衡机制造有限公司
- 发布时间:2025-03-21
- 访问量:108
在金属切削的轰鸣声中,机床主轴如同高速运转的精密心脏,承载着现代制造业对精度的极致追求。当主轴以每分钟上万转的速度驱动刀具时,0.1克的微小失衡就会引发足以摧毁整个加工系统的振动涟漪。机床主轴平衡机正是在这个微米级精度战场上默默守护的精密卫士,为每一次完美切削奠定基础。
一、失衡世界的精密矫正
主轴系统的动态失衡犹如精密钟表里的砂砾,即使是最微小的不平衡量都会在高速旋转中产生离心力倍增效应。当主轴转速突破8000rpm时,1克的不平衡量就能产生超过200N的动态载荷,这种周期性冲击不仅会导致加工表面出现肉眼可见的振纹,更会引发主轴轴承的早期失效。
现代动平衡机采用相位锁定振动分析技术,能够捕捉0.01μm级的振幅变化。高灵敏度压电传感器阵列以每秒百万次的采样频率,在主轴旋转的瞬间完成三维振动谱分析。当系统检测到G0.4级以上的失衡量时,智能算法自动生成精确到0.01克的质量补偿方案。
在汽车曲轴加工现场,经过精密平衡的主轴系统可将加工圆度误差控制在3μm以内。某涡轮叶片制造企业通过主轴动平衡优化,将刀具寿命提升了40%,同时将表面粗糙度Ra值稳定在0.8μm以下。
二、平衡技术的核心突破
现代动平衡机已实现ISO1940标准的G0.4平衡等级,这意味着在主轴端面任意方向的不平衡量不超过0.4g·mm/kg。为达到这个标准,设备采用激光干涉定位技术,配合碳纤维校正配重块,将质量补偿精度提升至毫克级。
多通道振动分析系统通过傅里叶变换将复杂振动信号分解为基频和谐波成分,自动识别主轴系统的刚体失衡与弯曲模态。智能补偿算法不仅计算静态不平衡量,还能预测动态失衡趋势,生成预防性校正方案。
在智能化升级方面,最新型平衡机已集成机器学习模块。通过对历史平衡数据的深度学习,系统能够自主优化补偿策略,某企业应用该技术后,平衡作业效率提升70%,校正精度标准差降低至0.03g。
三、工业4.0时代的平衡革命
当主轴平衡数据接入工厂MES系统,制造过程获得了前所未有的透明化视角。某精密轴承制造商通过平衡数据与加工参数的关联分析,成功将主轴系统MTBF(平均故障间隔时间)从3000小时提升至5000小时。
物联网技术正在重塑动平衡服务模式。安装于主轴箱体的振动监测终端持续采集运行数据,当系统预测剩余平衡寿命不足时,自动触发维护工单。某机床用户通过预测性维护,将计划外停机时间减少了85%。
在智能化工厂的规划蓝图中,自适应平衡系统将与数控系统深度集成。未来主轴将具备在线自平衡能力,通过压电陶瓷执行机构实时调整质量分布,使机床在加工过程中始终保持最佳平衡状态。
在制造业向微米级精度进军的征程中,机床主轴平衡机始终扮演着关键角色。从最初的手工配重到如今的智能平衡系统,这项技术见证了精密制造的数次跨越式发展。当工业4.0的浪潮席卷全球,融合了大数据与人工智能的新一代平衡技术,正在为智能制造构筑更坚实的精度基石。在这个不可见的微观战场,每一次精密的平衡校正,都在为大国重器的诞生积蓄力量。
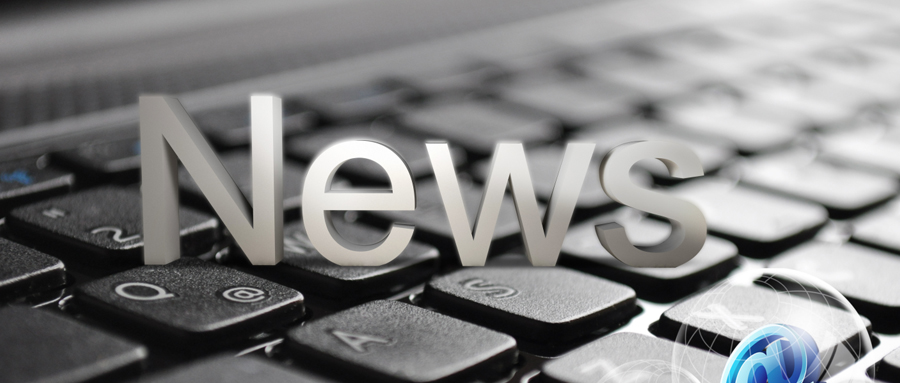