

机床主轴现场动平衡:现代制造业的精密保障
- 分类:行业新闻
- 作者:申岢编辑部
- 来源:上海申岢动平衡机制造有限公司
- 发布时间:2025-03-21
- 访问量:101
在高速旋转的机床主轴上,即使微米级的不平衡量也会引发剧烈的振动。这种肉眼难以察觉的缺陷,不仅会缩短主轴轴承的使用寿命,更会导致加工表面出现振纹,直接影响工件的尺寸精度和表面质量。随着现代制造业对加工精度要求的不断提升,现场动平衡技术已成为保障机床性能的关键支撑。
一、主轴失衡的隐蔽威胁
机床主轴在长期运转中,机械磨损、部件变形、刀具更换等都会导致质量分布失衡。当主轴转速达到每分钟数万转时,0.1克的不平衡量就会产生超过200N的动态载荷。这种周期性冲击会造成轴承滚道压痕、保持架变形,缩短60%以上的轴承使用寿命。更为严重的是,振动能量会通过机床结构传递到加工区域,在工件表面形成规律性振纹,使精密加工件的表面粗糙度恶化2-3个等级。
传统离线平衡需要拆卸主轴送至专业检测机构,这个过程往往需要3-5天的停机时间。对于连续生产的制造企业,这种维护方式造成的产能损失可能高达数十万元。更棘手的是,重新装配后的主轴可能因安装误差产生新的不平衡,形成恶性循环。
二、现场动平衡的技术突破
现代动平衡仪采用多通道振动分析技术,可实时捕捉主轴旋转时的三维振动频谱。通过相位锁定算法,设备能在0.01秒内精确识别不平衡量所在的角位置。智能传感器网络可同时监测轴承座、主轴箱等关键部位的振动特征,构建完整的振动传递模型。
在配重修正环节,动态补偿算法会根据主轴结构特征自动计算配重方案。技术人员通过专用平衡软件,可实时观察配重调整后的振动衰减曲线。最新的无线平衡系统支持毫米级定位精度,采用模块化配重块实现微克级质量调整,单次平衡作业可将振动幅值降低90%以上。
现场动平衡的标准化流程包含五个关键步骤:振动基准测量、试重实验、数据采集分析、配重计算实施、最终效果验证。专业工程师通过频谱对比和趋势分析,能在30分钟内完成整个平衡过程,且无需中断机床的安装基准。
三、精密制造的守护屏障
在航空航天领域,某型涡轮盘加工中心通过定期现场动平衡,将主轴振动值稳定控制在0.8mm/s以内,使叶片型面精度提升至IT4级。汽车制造业中,采用在线平衡系统的曲轴生产线,将刀具寿命延长了40%,同时减少60%的废品率。这些实践案例证明,有效的动平衡管理可使机床加工精度提升1-2个数量级。
实施动平衡维护需遵循严格的技术规范:平衡前需确认主轴温升稳定在±2℃范围内;传感器安装必须保证磁座吸附力大于50N;数据采集时长应覆盖至少100个旋转周期。维护团队需要定期校准测量系统,建立主轴振动特征数据库,为预测性维护提供数据支持。
随着智能制造的深入推进,动平衡技术正在向智能化方向发展。自适应平衡系统可实时监测主轴状态,当检测到异常振动时自动启动平衡程序。数字孪生技术通过建立主轴动力学模型,可预测不同转速下的平衡需求。这些创新将推动机床维护进入”零停机”时代。
机床主轴现场动平衡技术的应用,标志着设备维护从被动维修向主动预防的战略转变。这项看似简单的振动控制技术,实则是现代制造体系不可或缺的精度保障。随着新材料、新工艺的不断突破,动平衡技术将继续推动机床加工精度向亚微米级迈进,为高端装备制造提供坚实的技术支撑。
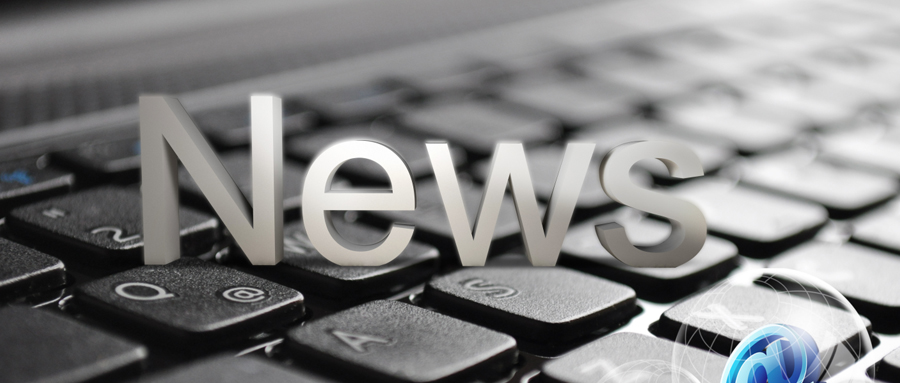