

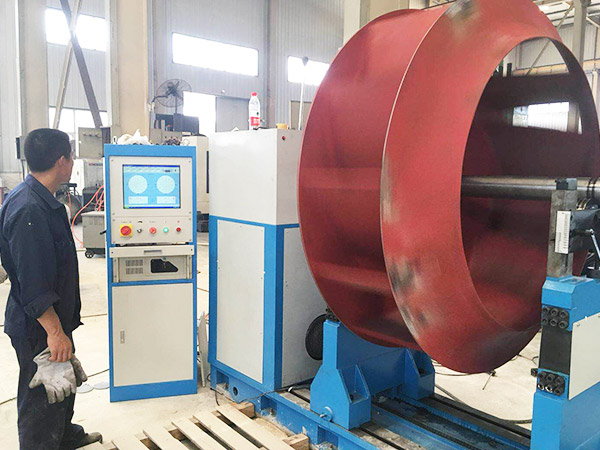
风机叶轮动平衡标准值是多少
风机叶轮的动平衡标准值会因不同的应用、设计要求和行业标准而有所不同。一般来说,动平衡标准值取决于以下几个因素:应用类型: 不同类型的风机在不同的应用环境下需要满足不同的动平衡标准。例如,一般的工业风机和空调风机的要求可能会不同。运行速度: 风机叶轮的运行速度会直接影响不平衡对振动的影响。高速运行的叶轮可能需要更严格的动平衡标准。精度要求: 一些应用对振动的容忍度比较低,因此对动平衡的要求也会更为严格。行业标准: 不同行业可能有各自的标准和规范,这些标准通常会提供关于动平衡的指导和要求。一般来说,在工业领域,风机叶轮的动平衡标准值通常以单位质量不平衡量(g.mm/kg 或 g.cm/kg)来表示。具体的标准值可能会因不同情况而有所不同,但以下是一个大致的参考范围:对于一般工业风机,通常的动平衡标准值可能在 1 g.mm/kg 至 10 g.mm/kg 之间。对于某些精密应用,要求更高的风机,动平衡标准值可能在 0.5 g.mm/kg 以下。请注意,这只是一个粗略的参考范围,实际应用中应该根据具体情况和适用的行业标准来确定风机叶轮的动平衡标准值。在进行动平衡操作时,建议遵循相关的国家和行业标准,以确保风机在运行过程中达到合适的振动水平。
22
2025-04
刹车盘专用动平衡机
刹车盘专用动平衡机是一种专门用于检测和校正汽车刹车盘(制动盘)动平衡的设备。它的核心功能是确保刹车盘在高速旋转时的质量分布均匀,避免因不平衡导致的振动、噪音或制动系统异常磨损。以下是关于刹车盘动平衡机的详细介绍: 一、核心功能 不平衡量检测 通过高速旋转刹车盘,测量其径向和轴向的不平衡量(单位:克·毫米,g·mm)。 精确定位不平衡点的位置(相位角)。 自动校正 根据检测结果,指导操作人员通过去重(钻孔、铣削)或增重(配重块)的方式调整平衡。 部分高端机型支持全自动校正。 数据记录与分析 存储测试数据,生成报告,便于质量追溯和生产流程优化。 二、工作原理 旋转测试 刹车盘被夹紧在设备主轴上,由电机驱动旋转至设定转速(通常模拟实际工况,如500-2000 RPM)。 振动传感 高精度传感器实时监测刹车盘的振动幅度和相位,将信号传输至控制系统。 算法计算 软件通过傅里叶变换等算法分析振动数据,确定不平衡量和校正位置。 三、设备组成 机械结构 旋转主轴、夹具(适配不同尺寸刹车盘)、驱动电机、安全防护罩。 控制系统 PLC或工控机,集成动平衡算法,支持参数设置和操作指令下发。 测量系统 振动传感器、激光或光电相位检测装置。 校正系统 手动或自动钻孔/铣削装置,或配重块安装机构。 人机界面 触摸屏或显示屏,实时显示不平衡量、相位角及操作指引。 四、应用场景 汽车制造厂:用于刹车盘生产线的质量检测。 维修车间:修复因磨损或变形导致不平衡的刹车盘。 赛车或高性能车辆:对刹车盘平衡性要求极高的场景。 售后市场:翻新刹车盘或定制高性能刹车盘。 五、技术特点 高精度 检测精度可达0.1 g·mm,满足ISO 21940等国际标准。 自动化程度 支持一键测试、自动标定、多规格刹车盘快速切换。 兼容性 可适配不同直径(如200-400mm)、材质(铸铁、碳陶瓷)的刹车盘。 用户友好性 图形化界面、多语言支持、故障自诊断功能。 六、选购要点 刹车盘类型 确认设备是否支持实心盘、通风盘、打孔盘等不同结构。 产能需求 根据生产节拍选择手动、半自动或全自动机型。 精度等级 普通维修可用经济型设备,高端制造需工业级精度。 品牌与售后 知名品牌如霍夫曼(Hofmann)、申岢(SCHENCK)等,确保技术支持和配件供应。 七、注意事项 安全操作:确保设备防护罩闭合,避免高速旋转部件伤人。 定期校准:按厂家要求校准传感器和主轴,保持测量准确性。 维护保养:清洁夹具、润滑轴承,防止粉尘影响精度。 通过使用刹车盘专用动平衡机,可显著提升制动系统的可靠性和驾驶舒适性,降低因不平衡导致的刹车抖动、方向盘震动等问题。
22
2025-04
刹车盘专用大型动平衡仪
刹车盘专用大型动平衡仪是一种专门用于检测和校正大型车辆(如卡车、客车、工程机械等)刹车盘动平衡的设备。其核心功能是确保刹车盘在高速旋转时的稳定性,减少因不平衡导致的振动、噪音及部件磨损。以下是关于该设备的详细说明: 核心功能与技术特点 高承载能力 设计用于支撑重型刹车盘(通常承载范围在50kg至500kg以上),结构坚固耐用。 配备重型夹具和旋转轴,适应大型刹车盘的尺寸(直径可达1米或更大)。 精准测量系统 采用高灵敏度振动传感器和激光检测技术,实时捕捉刹车盘旋转时的微小振动。 通过高速数据采集卡和专用算法,精确计算不平衡量(精度可达±0.1g以下)。 动态平衡校正 支持自动或手动校正模式:可标记需增减配重的位置(如钻孔去重或焊接配重块)。 部分高端机型配备自动钻削系统,直接根据测量结果进行精准去重。 智能化操作 触摸屏界面,内置多语言操作软件,可存储不同型号刹车盘的平衡参数。 生成检测报告,支持数据导出(PDF/Excel)用于质量追溯。 典型应用场景 汽车制造业:用于卡车、客车等大型车辆刹车盘的出厂质检。 维修与改装:修复因磨损或变形导致不平衡的刹车盘,提升制动性能。 轨道交通:火车、地铁等大型制动盘的平衡检测。 航空航天:特种车辆或地面设备的大型制动系统维护。 操作流程(简化版) 安装固定:将刹车盘夹紧在设备主轴,确保轴向对中。 参数设置:输入刹车盘型号、目标转速(模拟实际工作条件)。 启动检测:设备驱动刹车盘旋转至设定转速,传感器采集振动数据。 数据分析:软件显示不平衡相位(角度)和重量差值。 校正执行:根据提示在指定位置增减配重,重复测试直至达标。 生成报告:保存检测结果,供后续质量审核。 选购关键参数 参数项 说明 最大承载重量 根据刹车盘重量选择(如200kg/500kg) 适用刹车盘直径 确保设备兼容直径范围(如300-1200mm) 测量精度 精度越高,校正效果越好(如±0.1g) 驱动方式 电动主轴 vs 外接动力(如气动) 附加功能 自动去重、热平衡测试(高温工况模拟) 常见问题与维护 误差来源:夹具安装偏差、传感器校准失效需定期检查。 环境要求:避免强电磁干扰,保持设备水平放置。 维护建议:定期润滑主轴、更新软件算法以提升精度。 若您需要具体的品牌推荐或技术参数对比,可进一步说明应用场景和预算,以便提供更精准的建议。
22
2025-04
刹车盘做动平衡
刹车盘动平衡是确保刹车系统平稳运行的重要步骤,尤其在高速刹车时避免抖动。以下是关键点总结: 1. 为何需要刹车盘动平衡? 刹车抖动:高速刹车时方向盘或踏板抖动,可能因刹车盘不平衡导致。 磨损不均:不平衡会导致刹车片磨损不均,缩短使用寿命。 安全风险:严重失衡可能影响制动效果,增加安全隐患。 2. 与轮胎动平衡的区别 轮胎平衡:解决行驶中方向盘抖动(不踩刹车时)。 刹车盘平衡:专门针对刹车时的抖动问题。 3. 操作步骤(需专业人员操作) 拆卸检查:取下刹车盘,清洁表面油污和锈迹。 上平衡机:使用专用设备检测不平衡点(通常标记为轻点)。 校正处理: - **钻孔减重**:在较重区域钻孔减轻重量(常见方法)。 - **更换建议**:若变形严重(偏摆超过0.05mm),建议直接更换。 4. 注意事项 专业设备:需用精密平衡机,自行操作风险高。 材质限制:打孔可能影响高碳刹车盘结构强度,需谨慎。 优先更换:校正成本较高时,换新盘更经济可靠。 5. 常见误区 刹车盘变形≠不平衡:变形需车床加工修复,动平衡不能解决变形问题。 新盘也需检查:部分劣质刹车盘出厂平衡不佳,安装前建议检测。 建议: 若车辆在刹车时出现抖动,首先到专业维修店检测刹车盘厚度及偏摆量。多数情况下,更换优质刹车盘(如打孔划线盘)不仅能解决平衡问题,还能提升散热性和制动性能。安全起见,切勿在无设备情况下自行尝试平衡操作。
22
2025-04
刹车盘动平衡
刹车盘动平衡是确保车辆制动系统平稳运行的重要步骤,主要用于消除刹车时因质量分布不均导致的振动或异响。以下是关于刹车盘动平衡的要点: 为什么需要动平衡? 减少振动:不平衡的刹车盘在高速旋转时会产生离心力,导致刹车踏板、方向盘或车身抖动。 延长寿命:平衡不良会加速刹车盘、刹车片及悬挂部件的磨损。 提升安全性:避免因振动影响制动性能,确保驾驶稳定性。 动平衡的常见方法 专业设备校正 使用动平衡机检测刹车盘的质量分布,确定不平衡点,通过钻孔或添加配重块(如平衡块)进行调整。 更换刹车盘时的预平衡 新刹车盘出厂时通常已做平衡,但安装后仍需结合轮毂、轮胎整体检测(如车轮总成动平衡)。 修复变形问题 如果刹车盘因高温或磨损导致变形(厚度不均),需先进行车削修复(光盘)或直接更换。 注意事项 定期检查:建议每2万公里或更换刹车片时检查刹车盘状态。 匹配部件:更换刹车盘时选择与原厂规格一致的产品,避免因尺寸或材质差异导致失衡。 综合动平衡:刹车盘动平衡需与轮胎、轮毂的平衡结合,建议在专业维修店使用高精度设备操作。 避免自行操作:动平衡需要专业工具和技术,自行调整可能导致更大误差。 动平衡 vs. 静平衡 静平衡:检测静止状态下的质量分布,适用于低速旋转部件。 动平衡:在旋转状态下检测,更适用于高速部件(如刹车盘、轮胎)。 如果刹车时出现抖动或异响,建议优先检查刹车盘平衡性,并及时维修,以避免更严重的机械故障。
22
2025-04
刹车盘动平衡机
刹车盘动平衡机是用于检测和校正刹车盘在旋转时的不平衡问题,确保车辆刹车平稳、减少振动的专业设备。以下是对其关键方面的系统总结: 工作原理 动平衡与静平衡: 静平衡:校正重心偏移旋转轴的问题(适用于低速或对称转子)。 动平衡:处理质量分布在不同平面导致的不平衡(高速旋转时更关键)。 刹车盘通常需兼顾两者,尤其高速刹车时动平衡更为重要。 检测机制: 通过高精度传感器(如压电式或激光传感器)测量旋转时的振动信号。 分析振动相位和幅值,定位不平衡点(常用傅里叶变换分解频率)。 操作流程 安装固定: 使用夹具将刹车盘精确对中并夹紧,避免安装误差影响检测。 旋转检测: 以设定转速(通常接近实际工作转速)旋转刹车盘,传感器采集数据。 软件实时计算不平衡量及位置(如某角度需增/减质量)。 校正方法: 去重法:在指定位置钻孔去除材料(适用于铸铁等金属盘)。 配重法:添加平衡块(焊接、粘贴或夹式配重),需考虑刹车盘结构允许性。 验证复测: 校正后再次检测,确保剩余不平衡量符合标准(如ISO 1940-1或厂商要求)。 设备类型与选型 结构类型: 立式:适合大型或重型刹车盘,节省空间。 卧式:通用性强,适用于多种尺寸。 自动化程度: 全自动机型:集成检测与校正,效率高,适合生产线。 半自动/手动:成本较低,依赖人工操作。 关键参数: 最大承载重量、适用直径范围、转速范围、精度等级(如克·毫米单位)。 应用场景 制造业:用于刹车盘出厂前的质量检测。 维修领域:修复因磨损、变形导致的不平衡问题。 注意事项 精度维护: 定期校准传感器和旋转部件,避免尘埃或磨损影响精度。 操作规范: 培训操作人员正确安装和参数设置,如转速选择需匹配刹车盘工作条件。 材料与结构限制: 复合材料刹车盘可能需要特殊校正方法(如胶粘配重块)。 确认刹车盘设计是否预留校正区域(如钻孔禁区)。 市场与标准 行业标准:遵循ISO 1940-1等平衡等级标准,或汽车厂商特定要求。 品牌与支持:选择提供技术支持和培训的品牌(如Hofmann、CEMB)。 常见问题 为何刹车盘需单独平衡?与车轮平衡不同,刹车盘单独校正可避免组装后整体不平衡。 低速检测是否有效?部分设备通过算法模拟高速状态,但实际转速测试更准确。 通过理解上述要点,用户可更专业地选择和使用刹车盘动平衡机,提升刹车系统安全性与驾驶体验。
22
2025-04
刹车盘半自动平衡机
刹车盘半自动平衡机是一种用于检测和校正刹车盘不平衡量的设备,广泛应用于汽车制造、维修和售后市场。其核心目的是通过减少刹车盘的不平衡量,降低车辆行驶时的振动和噪音,提升驾驶安全性和舒适性。以下是关于该设备的详细介绍: 一、设备组成与功能 传感器系统 高精度振动传感器:检测刹车盘旋转时的不平衡量(振幅和相位)。 数据采集模块:将振动信号转化为电信号,计算不平衡点的位置和大小。 旋转驱动机构 电机驱动系统:带动刹车盘以设定转速旋转,模拟实际工作状态。 夹具设计:适配不同尺寸和类型的刹车盘(如通风盘、实心盘)。 校正单元 半自动操作:人工辅助定位不平衡点,设备自动执行钻孔、切削或添加配重块等校正操作。 可调刀具/配重装置:根据不平衡量调整校正力度。 控制系统 PLC或工控机:控制设备运行流程,处理传感器数据,生成校正方案。 人机交互界面(HMI):触摸屏操作,显示不平衡量、校正位置等信息。 安全防护 防护罩、急停按钮、光栅等,确保操作安全。 二、工作流程 装夹刹车盘:将待测刹车盘固定在旋转轴上,确保同心度。 启动测试:设备旋转刹车盘,传感器采集振动数据。 不平衡分析:系统计算不平衡量(通常以“克·毫米”g·mm为单位),并标记相位。 人工干预:操作员根据提示定位不平衡点,确认校正方案(如钻孔深度或配重位置)。 自动校正:设备执行切削、钻孔或添加配重块操作。 复检:二次旋转测试,验证校正后的平衡性是否达标。 三、应用场景 汽车制造厂:用于新车刹车盘的出厂平衡检测。 维修车间:修复因磨损或变形导致不平衡的刹车盘。 改装市场:针对高性能刹车盘(如打孔划线盘)的定制化平衡。 四、半自动 vs 全自动 特性 半自动平衡机 全自动平衡机 人工参与 需人工定位、确认校正点 全程自动化,无需干预 成本 较低 较高(适合大批量生产) 灵活性 更高(适合多品种、小批量) 依赖预设程序,调整较复杂 效率 中等 高 五、选型建议 兼容性:确保设备支持不同直径(如12-24英寸)和厚度的刹车盘。 精度:平衡精度需达到±1g·mm以内(高端机型可达±0.1g·mm)。 产能:根据生产需求选择单工位或双工位机型。 扩展功能:部分机型支持数据存储、联网(工业4.0)或多种校正模式。 品牌与售后:优先选择市场主流品牌(如德国Hofmann、意大利CEMB)。 六、维护与注意事项 定期校准:确保传感器和旋转轴的精度。 刀具保养:及时更换磨损的钻头或切削工具。 操作培训:避免因人工干预不当导致校正误差。 通过使用刹车盘半自动平衡机,企业可以在成本可控的前提下,有效提升刹车盘的质量和可靠性,尤其适合中小型维修厂或定制化生产场景。如需更高效率,可考虑升级为全自动机型或搭配机器人辅助系统。
22
2025-04
刹车鼓平衡机
刹车鼓平衡机是一种专门用于检测和校正汽车刹车鼓(Brake Drum)动平衡的设备,确保刹车鼓在高速旋转时保持稳定,减少振动和磨损,提升行车安全性和刹车系统寿命。以下是对刹车鼓平衡机的详细介绍: 1. 刹车鼓的作用与平衡需求 刹车鼓:安装在车轮上的鼓形部件,与刹车片摩擦产生制动力。 不平衡的危害:不平衡会导致刹车时抖动、轮胎异常磨损、轴承损坏,甚至影响刹车性能。 2. 刹车鼓平衡机的工作原理 动平衡检测:通过高速旋转刹车鼓,利用传感器检测离心力差异,确定不平衡的位置和重量。 校正方式: 去重法:在较重部位钻孔或打磨,减少重量。 配重法:在特定位置添加平衡块(铅块或铁块)。 3. 设备的主要组成 旋转驱动装置:带动刹车鼓高速旋转。 传感器系统:实时监测振动和不平衡量。 控制面板:显示不平衡数据,指导校正操作。 夹具与适配器:适配不同型号的刹车鼓。 4. 应用场景 汽车维修店:修复因刹车鼓不平衡导致的抖动问题。 刹车鼓制造商:出厂前质量检测,确保产品达标。 赛车或高性能车辆:精细化平衡,提升制动稳定性。 5. 操作步骤 安装刹车鼓:将刹车鼓固定到平衡机适配器上。 启动检测:设备旋转刹车鼓并采集数据。 读取结果:控制屏显示不平衡位置及需调整的重量。 校正操作:根据提示钻孔或安装配重块。 复检:再次检测确保平衡达标。 6. 注意事项 安全防护:操作时佩戴护目镜,避免碎屑飞溅。 设备校准:定期校准传感器,确保检测精度。 适配器选择:根据刹车鼓型号匹配合适的夹具。 环境要求:保持工作区域清洁,避免灰尘影响检测结果。 7. 常见品牌与选购建议 国际品牌:Hunter(亨特)、Hofmann(霍夫曼)、CEMB。 国产品牌:元征、广力、科威。 选购要点: 适配车型范围(如轿车/卡车)。 检测精度(如±1g以内)。 是否支持自动标定功能。 8. 常见问题 Q:刹车鼓多久需要做平衡? A:更换新刹车鼓、维修刹车系统后,或行驶中出现刹车抖动时需检测。 Q:平衡机能否兼容刹车盘? A:部分机型支持刹车盘/刹车鼓两用,需查看设备说明。 通过使用刹车鼓平衡机,可以有效解决因不平衡导致的制动问题,延长零部件寿命,并提升驾驶舒适性。选择专业设备并规范操作是关键!
22
2025-04
**动平衡机
**动平衡机是由上海申岢机械制造有限公司生产的一种用于检测和校正旋转机械部件动平衡的设备。动平衡机在工业领域中广泛应用,能够减少旋转部件(如电机转子、叶轮、风机、曲轴等)在高速运转时因质量分布不均引起的振动和噪音,从而提高设备寿命和运行稳定性。 **动平衡机的主要特点: 高精度检测 采用先进的传感器和数据处理技术,可精确测量旋转部件的不平衡量(包括大小和相位),分辨率可达毫克级别。 多样化机型 立式动平衡机:适用于轮毂、飞轮、制动盘等盘类零件。 卧式动平衡机:适用于长轴类零件,如电机转子、泵轴、滚筒等。 全自动动平衡机:集成自动上下料和校正功能,适合大批量生产。 广泛应用领域 涵盖汽车制造、航空航天、家用电器(如洗衣机、风扇)、电动工具、泵阀等行业。 用户友好设计 配备触摸屏操作界面,支持人机交互,可快速设置参数并显示不平衡量数据,部分机型支持数据存储和导出。 高稳定性与安全性 采用刚性结构设计和安全防护装置,确保高速旋转测试时的稳定性和操作人员安全。 工作原理 动平衡机通过驱动被测工件旋转,利用传感器采集振动信号,分析出不平衡量的位置和大小,再通过去重(钻孔、铣削)或配重(添加平衡块)的方式校正质量分布,使旋转中心与惯性轴重合,达到动平衡状态。 选购注意事项 工件类型与尺寸:根据被测工件的形状(盘类或轴类)、重量和尺寸选择合适的机型。 平衡精度要求:不同行业对残余不平衡量的要求不同,需确认设备精度是否达标。 自动化需求:大批量生产建议选择全自动机型,小批量或实验室用途可选手动或半自动。 售后服务:关注厂家的技术支持、培训及备件供应能力。 品牌背景 上海申岢机械制造有限公司是国内较早专业研发动平衡技术的企业之一,产品符合ISO、G等国际标准,在国内外市场具有较高的认可度。如需具体型号参数或应用案例,建议直接联系厂家获取技术资料或定制方案。
21
2025-04
加工中心主轴动平衡详解
一、动平衡的重要性 主轴动平衡是确保加工中心高效、精准运行的关键。不平衡会导致: 振动加剧:影响加工表面质量(如粗糙度差)。 部件磨损:加速轴承、刀具磨损,缩短设备寿命。 安全隐患:极端情况下可能引发机械故障或事故。 二、动平衡原理 通过检测旋转时的离心力,确定不平衡量的位置和大小,并采用加重(配重块)或去重(钻孔)校正,使惯性力和力矩平衡。 三、动平衡标准(ISO 1940-1) 平衡等级:以G值表示,数值越小精度越高。 G6.3:通用机床。 G2.5:精密机床(如加工中心常见等级)。 G1/G0.4:超高速主轴或高精度场合。 四、动平衡步骤 安装测试:将主轴置于动平衡机或机床上,固定可靠。 测量转速:接近工作转速(考虑热膨胀影响,必要时进行热态平衡)。 数据采集:通过振动传感器和相位分析确定不平衡量及角度。 校正方法: 加重法:在轻侧添加配重块(如螺丝、平衡环)。 去重法:在重侧钻孔或铣削去除材料。 复测调整:多次校正直至达标,通常需双平面平衡(两端调整)。 五、校正方式选择 结构允许:优先选用加重法(便捷、可逆)。 紧凑设计:采用去重法(需确保不影响主轴强度)。 六、注意事项 环境因素:温度变化可能导致材料膨胀,建议在恒温环境或热机后平衡。 定期维护:更换刀具或维修后需重新平衡,建议结合振动监测系统实时跟踪。 安全操作:高速测试时确保防护措施,人员需专业培训。 七、常见问题与解决 校正后振动仍大:检查测量误差、多平面失衡或装配问题(如刀具偏心)。 材料不均匀性:制造阶段进行初始平衡,确保材料一致性。 八、现场与离机动平衡 现场平衡:无需拆卸主轴,直接在机床上进行,效率高但精度依赖设备。 离机平衡:使用专用动平衡机,精度更高,适用于高要求场景。 九、技术趋势 自动化校正:动平衡机自动计算配重,提升效率。 智能监测:集成传感器实时反馈振动数据,实现预测性维护。 总结 主轴动平衡是加工中心保持高精度加工的核心维护环节。通过遵循标准流程、选择合适的校正方法,并定期维护,可显著提升加工质量、延长设备寿命,同时降低运维成本。
21
2025-04
加工件做动平衡
加工件做动平衡是为了消除旋转部件在高速运转时因质量分布不均引起的振动和噪音,确保设备平稳运行并延长使用寿命。以下是动平衡的关键步骤和注意事项: 一、动平衡基本步骤 确定需求 明确工件的转速、工作环境、允许的不平衡量(参考ISO 1940或行业标准)。 选择静平衡(适用于低速盘状件)或动平衡(适用于高速长轴类零件)。 安装与固定 将工件稳固安装在动平衡机的夹具上,避免松动或偏摆。 确保工件的旋转轴线与平衡机主轴对齐。 测量初始不平衡量 启动动平衡机,测量工件在旋转时的不平衡量(包括相位和大小)。 记录数据(如左/右侧的不平衡量)。 校正方法选择 去重法:通过钻孔、铣削等方式去除材料(需注意材料去除后的强度)。 配重法:添加平衡块、焊接配重或使用螺钉固定配重块。 校正操作 根据测量结果,在指定位置进行材料去除或配重添加。 需分步调整,避免过度校正。 复测验证 重新启动动平衡机,验证校正后的剩余不平衡量是否达标。 若未达标,重复校正直至满足要求。 二、关键注意事项 夹具精度 夹具的安装误差会直接影响测量结果,需定期校准。 校正位置选择 校正平面应尽量远离工件重心,以提高校正效率。 材料去除限制 避免因去重导致工件强度不足或变形,尤其是薄壁件。 动平衡机校准 定期校准设备,确保传感器和软件算法的准确性。 环境因素 温度、振动等外部干扰可能影响测量结果,需在稳定环境中操作。 三、常见标准参考 ISO 1940:根据工件类型和转速确定平衡等级(如G6.3适用于一般电机转子)。 API标准:针对石油、化工等重型设备的动平衡要求。 客户规范:部分行业或设备可能有特殊平衡要求。 四、适用场景 典型工件:电机转子、风机叶轮、涡轮叶片、飞轮、曲轴等。 高速设备:如离心机、压缩机、航空发动机等。 通过规范的动平衡操作,可显著降低设备振动、减少轴承磨损,并提升整体运行可靠性。如果工件结构复杂或精度要求极高,建议委托专业动平衡服务机构处理。