

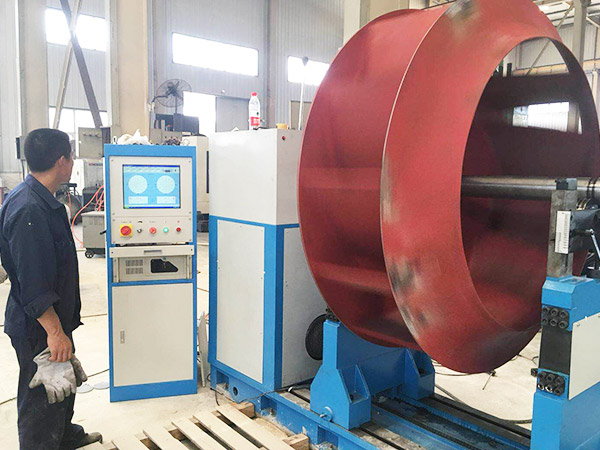
风机叶轮动平衡标准值是多少
风机叶轮的动平衡标准值会因不同的应用、设计要求和行业标准而有所不同。一般来说,动平衡标准值取决于以下几个因素:应用类型: 不同类型的风机在不同的应用环境下需要满足不同的动平衡标准。例如,一般的工业风机和空调风机的要求可能会不同。运行速度: 风机叶轮的运行速度会直接影响不平衡对振动的影响。高速运行的叶轮可能需要更严格的动平衡标准。精度要求: 一些应用对振动的容忍度比较低,因此对动平衡的要求也会更为严格。行业标准: 不同行业可能有各自的标准和规范,这些标准通常会提供关于动平衡的指导和要求。一般来说,在工业领域,风机叶轮的动平衡标准值通常以单位质量不平衡量(g.mm/kg 或 g.cm/kg)来表示。具体的标准值可能会因不同情况而有所不同,但以下是一个大致的参考范围:对于一般工业风机,通常的动平衡标准值可能在 1 g.mm/kg 至 10 g.mm/kg 之间。对于某些精密应用,要求更高的风机,动平衡标准值可能在 0.5 g.mm/kg 以下。请注意,这只是一个粗略的参考范围,实际应用中应该根据具体情况和适用的行业标准来确定风机叶轮的动平衡标准值。在进行动平衡操作时,建议遵循相关的国家和行业标准,以确保风机在运行过程中达到合适的振动水平。
03
2025-06
转子动平衡精度等级G.的标准要求
转子动平衡精度等级G.的标准要求 一、标准的诞生:从混沌到秩序的精密革命 在旋转机械的咆哮声中,转子动平衡精度等级G.如同一把悬在精密制造领域的达摩克利斯之剑,将混沌的振动能量驯服为可控的工程参数。这个标准并非冰冷的数字游戏,而是凝聚着人类对旋转运动本质的百年探索——从早期依赖经验的”耳听目测”,到现代基于ISO 1940-1的量化体系,每一次迭代都在重新定义”完美平衡”的边界。 当工程师们手持激光对刀仪在车间穿梭时,他们追逐的不仅是G0.4到G63的数字阶梯,更是在对抗牛顿第三定律的永恒挑战:如何让旋转体在离心力与重力的角力中,找到那个让振动幅值低于临界阈值的黄金分割点。 二、标准的核心要素:多维参数的交响乐章 G等级标准绝非单一维度的测量尺,而是由五大核心要素编织的精密网络: 残余不平衡量(mr):这个以克·毫米(g·mm)为单位的参数,如同旋转体的”心跳频率”,其数值波动直接决定轴承寿命曲线的陡峭程度。 平衡精度等级(G值):从G0.4到G63的13个等级,构成了一座横跨精密仪器与重型机械的桥梁,G1.0往往是航空发动机与精密机床的分水岭。 校正平面数量:单面平衡与双面平衡的选择,犹如在二维与三维空间中搭建力矩方程,后者能消除90%以上的偶不平衡。 动态特性补偿:当转速突破临界区时,柔性转子的动平衡需引入Campbell图分析,这要求操作者同时驾驭频域与时域的双重维度。 环境耦合效应:温度梯度导致的材料热膨胀系数变化,往往会使实验室标定的G1.5精度在实际工况下退化为G2.5,这需要引入热力耦合补偿算法。 三、标准的实践:在理想与现实的钢丝上起舞 在某燃气轮机制造车间,工程师们正经历着标准与现实的残酷博弈: 材料缺陷的蝴蝶效应:一根叶片根部0.01mm的铸造偏差,经10000rpm旋转放大后,会在轴承座上激发出相当于10%额定载荷的交变应力。 安装公差的连锁反应:当联轴器径向跳动超过0.05mm时,原本G2.5的平衡精度可能瞬间坍缩为G4.0,这要求装配过程引入激光跟踪仪实时监控。 动态失真的量子纠缠:在超临界转速区,转子的涡动振型会使传统静平衡法失效,此时需采用模态平衡技术,通过频响函数重构失真的力矩分布。 四、标准的未来:数字孪生时代的范式跃迁 当工业4.0的浪潮席卷而来,G等级标准正在经历基因重组: 数字孪生平衡系统:通过在虚拟空间实时映射物理转子的振动特性,实现从”事后补偿”到”预测性平衡”的范式转换。 自适应平衡技术:磁流变阻尼器与压电作动器的结合,使转子能在运行中动态修正不平衡量,将G1.0的静态精度转化为G0.8的动态表现。 量子传感革命:原子干涉仪的出现,使不平衡量的检测精度突破微克·毫米量级,这或将催生G0.1这一新的标准维度。 五、标准的哲学:在确定性与不确定性的夹缝中求生 站在技术哲学的高度审视,G等级标准本质上是人类在确定性与不确定性之间的永恒妥协: 统计学的达摩克利斯之剑:任何平衡操作都伴随着95%置信区间的概率云,这意味着G1.0标准下仍有5%的转子可能游离在合格边缘。 混沌理论的阴影:当转子系统进入非线性振动区域,微小的初始误差可能引发指数级放大的振动响应,这要求标准体系必须嵌入容错设计基因。 熵增定律的终极挑战:从原材料到报废的全生命周期中,转子的平衡状态持续遭受着磨损、腐蚀和热应力的熵增侵蚀,这使得动态平衡成为对抗热力学第二定律的永恒战役。 在这个旋转永不停歇的世界里,G等级标准既是工程师手中的达摩克利斯之剑,也是旋转机械的诺亚方舟。它提醒我们:在追求绝对平衡的道路上,真正的艺术不在于消灭所有振动,而在于将振动控制在人类文明能够承受的美学范畴之内。
03
2025-06
转子动平衡精度等级标准要求
转子动平衡精度等级标准要求 在旋转机械的世界里,转子动平衡至关重要。它直接影响着设备的性能、寿命和运行的稳定性。而转子动平衡精度等级标准要求,就像一把精准的尺子,规范着整个行业的运行。 转子动平衡精度等级是依据转子的类型和使用场景来划分的。不同的精度等级对应着不同的平衡质量要求。这些等级的设定,是综合考虑了多方面因素的结果。从航空航天领域那些对精度要求极高的转子,到普通工业设备中的一般转子,每个精度等级都有着其独特的意义。 高精度等级的转子,主要应用于对振动和噪音控制极为严格的场合。例如航空发动机的转子,它的动平衡精度等级要求非常高。因为哪怕是极其微小的不平衡,都可能在高速旋转时引发严重的振动,进而影响发动机的性能,甚至危及飞行安全。对于这类高精度转子,其平衡精度等级通常以国际标准 ISO 1940 为依据进行严格控制。这个标准详细规定了不同类型转子在不同工作转速下所允许的剩余不平衡量。在实际操作中,需要采用先进的动平衡机和高精度的测量设备,经过多次精确的调整和测量,才能确保转子达到规定的精度等级。 中等精度等级的转子在工业生产中较为常见。比如一些通用的电机转子、风机转子等。它们对动平衡的要求不像高精度转子那么苛刻,但也需要达到一定的标准。如果这些转子的不平衡量过大,会导致设备振动加剧,噪音增大,缩短设备的使用寿命,增加维护成本。对于中等精度等级的转子,一般按照相关的行业标准进行动平衡处理。这些标准会根据转子的尺寸、转速等参数,给出相应的平衡精度要求。在进行动平衡时,通常会采用较为常规的动平衡设备和方法,通过合理的配重调整,使转子的不平衡量控制在允许范围内。 低精度等级的转子则主要用于对振动和噪音要求相对较低的场合。例如一些低速运转的机械设备中的转子。虽然对其动平衡精度要求不高,但也不能忽视不平衡带来的影响。过大的不平衡可能会导致设备的运行不稳定,降低工作效率。对于低精度等级的转子,一般可以根据经验和简单的平衡方法进行处理。不过,即使是低精度要求,也应该遵循基本的平衡原则,以保证设备的正常运行。 在实际的动平衡过程中,要严格按照精度等级标准要求进行操作。首先,需要准确测量转子的不平衡量。这就要求动平衡机具备高精度的测量系统,能够准确地检测出转子在不同位置的不平衡情况。然后,根据测量结果进行合理的配重调整。配重的方式有多种,如钻孔去重、焊接配重块等,需要根据转子的具体情况选择合适的方式。在调整过程中,要不断进行测量和调整,直到转子的不平衡量达到精度等级标准要求。 转子动平衡精度等级标准要求是保障旋转机械设备正常运行的重要依据。无论是高精度、中等精度还是低精度的转子,都需要严格按照相应的标准进行动平衡处理。只有这样,才能确保设备的性能、寿命和运行的稳定性,为工业生产的高效运行提供有力保障。
03
2025-06
转子动平衡自动分析软件如何应用
转子动平衡自动分析软件如何应用 在现代工业生产中,转子动平衡对于设备的稳定运行至关重要。转子动平衡自动分析软件作为一种先进的工具,能够极大地提高动平衡检测和校正的效率与精度。那么,该如何应用这款软件呢? 前期准备:熟悉软件与设备 在使用转子动平衡自动分析软件之前,要做好充分的前期准备工作。首先,要熟悉软件的操作界面和各项功能。如今的软件界面设计大多遵循人性化原则,但仍包含丰富的功能模块,如数据采集、分析计算、结果显示等。用户需仔细研读软件的操作手册,通过模拟操作来熟悉各个功能的使用方法。 同时,要了解所使用的动平衡机设备。不同型号的动平衡机在性能和参数上可能存在差异,软件需要与设备进行适配。要确保动平衡机的传感器、驱动装置等部件正常工作,并且与软件之间的通信连接稳定。只有设备与软件完美配合,才能保证后续分析的准确性。 数据采集:精确获取转子信息 数据采集是应用转子动平衡自动分析软件的关键步骤。软件通过动平衡机上的传感器来获取转子的相关数据,如振动信号、转速等。在采集数据时,要确保转子处于正常的运行状态。启动动平衡机,使转子达到稳定的转速,这样采集到的数据才能真实反映转子的动平衡情况。 软件会实时显示采集到的数据,用户要观察数据的稳定性和准确性。如果数据出现异常波动,可能是传感器故障或者转子存在其他问题,需要及时排查。采集到足够的数据后,软件会将这些数据进行初步处理,为后续的分析计算做好准备。 分析计算:深入剖析动平衡状况 采集到数据后,软件会运用内置的算法进行分析计算。它会根据转子的振动信号和转速等数据,计算出转子的不平衡量大小和位置。这些计算结果以直观的图表和数据形式呈现给用户,如不平衡量的矢量图、频谱图等。 用户可以通过分析这些图表和数据,深入了解转子的动平衡状况。例如,从频谱图中可以看出转子振动的频率成分,判断是否存在其他干扰因素。软件还可以对不同工况下的转子数据进行对比分析,帮助用户找出潜在的问题。同时,软件会根据计算结果给出相应的校正建议,指导用户进行动平衡校正。 校正实施:依据建议优化转子 根据软件给出的校正建议,用户可以对转子进行动平衡校正。校正的方法有多种,如加重法和去重法。加重法是在转子的特定位置添加配重块,而去重法则是通过磨削等方式去除转子上的部分材料。 在实施校正时,要严格按照软件的建议进行操作。软件会精确地指出需要加重或去重的位置和重量,用户要使用合适的工具进行操作。校正完成后,再次启动动平衡机,采集校正后的转子数据,并通过软件进行分析。如果不平衡量仍然超出允许范围,可能需要进行多次校正,直到转子达到良好的动平衡状态。 结果保存与应用:持续优化生产过程 完成动平衡校正后,软件会保存分析和校正的结果。这些结果可以作为转子质量的重要记录,为后续的生产和维护提供参考。用户可以将结果导出为报表,方便与其他部门进行沟通和分享。 同时,通过对大量转子数据的积累和分析,用户可以总结出一些规律和经验。例如,发现某些类型的转子容易出现不平衡问题,从而在生产过程中提前采取措施进行预防。软件的应用不仅可以提高单个转子的动平衡质量,还可以为整个生产过程的优化提供有力支持。 转子动平衡自动分析软件的应用能够显著提高转子动平衡的检测和校正效率。通过熟悉软件与设备、精确采集数据、深入分析计算、合理实施校正以及有效保存和应用结果,用户可以充分发挥软件的优势,确保设备的稳定运行,提高生产效益。
03
2025-06
转子动平衡自动校正对振动控制的影响
转子动平衡自动校正对振动控制的影响 引言 在旋转机械的运行中,转子的动平衡问题一直是影响设备稳定性和使用寿命的关键因素。振动作为转子不平衡的直观表现,不仅会降低设备的运行效率,还可能引发严重的机械故障。转子动平衡自动校正技术的出现,为解决这一问题提供了新的途径。它通过先进的传感器和算法,能够快速、准确地对转子的不平衡进行校正,从而有效控制振动。 转子动平衡自动校正技术原理 转子动平衡自动校正技术基于对转子振动信号的精确测量和分析。首先,安装在设备上的振动传感器会实时采集转子的振动数据,这些数据包含了转子不平衡的信息。然后,系统会运用复杂的算法对采集到的信号进行处理,计算出不平衡的位置和大小。 一旦确定了不平衡的参数,自动校正装置就会启动。它可以通过多种方式进行校正,例如在转子上添加或去除配重。现代的自动校正装置通常采用高精度的执行机构,能够精确地控制配重的添加量和位置,以达到最佳的平衡效果。这种技术的核心在于其高度的自动化和智能化,能够在短时间内完成复杂的平衡校正任务。 对振动控制的积极影响 降低振动幅值 转子动平衡自动校正最直接的效果就是降低振动幅值。当转子存在不平衡时,会产生周期性的离心力,从而引起设备的振动。通过自动校正,减少了不平衡量,相应地离心力也会减小,振动幅值自然降低。实验表明,经过精确动平衡校正的转子,其振动幅值可以降低到原来的几分之一甚至更低。这对于提高设备的运行稳定性至关重要,因为较低的振动幅值可以减少设备各部件之间的磨损,延长设备的使用寿命。 改善振动频率特性 除了降低振动幅值,自动校正还能改善振动的频率特性。不平衡引起的振动通常具有特定的频率成分,这些频率可能与设备的固有频率接近,从而引发共振。共振会使振动急剧增大,对设备造成严重的损害。通过自动校正,改变了转子的不平衡状态,从而调整了振动的频率分布。使振动频率远离设备的固有频率,避免了共振的发生,进一步提高了设备的安全性和可靠性。 提高振动控制的实时性和准确性 传统的动平衡校正方法往往需要人工干预,过程繁琐且耗时较长。而自动校正技术能够实时监测转子的振动状态,并及时进行校正。它可以根据实际运行情况动态调整校正策略,确保在各种工况下都能保持良好的平衡效果。此外,自动校正系统的高精度传感器和先进算法,保证了校正的准确性,能够有效避免因人为因素导致的误差。 实际应用案例 在航空发动机领域,转子的动平衡至关重要。一台高性能的航空发动机,其转子的转速非常高,如果存在不平衡问题,会产生巨大的振动,严重影响发动机的性能和安全性。某航空发动机制造企业采用了转子动平衡自动校正技术,对发动机转子进行在线监测和实时校正。通过自动校正系统,发动机的振动水平显著降低,不仅提高了发动机的可靠性和燃油效率,还减少了维护成本和停机时间。 在工业压缩机领域,同样面临着转子不平衡引起的振动问题。某大型化工企业的压缩机由于转子不平衡,经常出现振动超标、轴承损坏等故障。引入自动校正技术后,压缩机的振动得到了有效控制,设备的运行稳定性大幅提高,生产效率也得到了显著提升。 结论 转子动平衡自动校正技术对振动控制具有显著的积极影响。它通过降低振动幅值、改善振动频率特性以及提高振动控制的实时性和准确性,有效地提高了旋转机械的运行稳定性和可靠性。在实际应用中,该技术已经取得了良好的效果,为工业生产带来了巨大的经济效益。随着科技的不断发展,转子动平衡自动校正技术将不断完善和创新,在更多领域发挥重要作用。我们有理由相信,这项技术将为旋转机械的发展带来新的突破。
03
2025-06
转子动平衡自动校正技术原理是什么
转子动平衡自动校正技术原理是什么 在现代工业生产中,转子作为许多旋转机械的核心部件,其动平衡状态直接影响着设备的性能和使用寿命。转子动平衡自动校正技术应运而生,它能够高效、精准地解决转子不平衡问题,那么其原理究竟是什么呢? 不平衡的检测原理 要实现转子动平衡自动校正,首先需要准确检测出转子的不平衡情况。目前,常用的检测方法基于振动信号分析。当转子存在不平衡时,在旋转过程中会产生离心力,这种离心力会引起转子及其支撑系统的振动。传感器被安装在靠近转子的位置,通常是轴承座上,用于捕捉这些振动信号。 这些传感器可以是加速度传感器或位移传感器。加速度传感器能够测量振动的加速度,而位移传感器则可以检测振动的位移量。传感器将捕捉到的振动信号转换为电信号,然后传输到信号处理系统。信号处理系统会对这些电信号进行滤波、放大等处理,以去除噪声干扰,并提取出与不平衡相关的特征信息。 通过对振动信号的频率分析,可以确定不平衡的大小和位置。例如,振动信号的幅值与不平衡的大小成正比,而振动信号的相位则与不平衡的位置有关。利用这些信息,系统就能够精确地计算出转子上不平衡量的具体数值和方位。 校正策略的制定 在检测到转子的不平衡情况后,接下来就是制定校正策略。校正策略的制定需要综合考虑多个因素,如转子的类型、不平衡的程度、生产效率等。 对于一些小型转子,常见的校正方法是去重法。这种方法通过在转子的不平衡位置去除一定量的材料,来达到平衡的目的。例如,可以使用钻孔、磨削等工艺去除材料。在制定去重策略时,需要精确计算出需要去除的材料量和位置,以确保校正的准确性。 而对于大型转子,加配重法更为常用。加配重法是在转子的特定位置添加一定质量的配重块,以抵消不平衡量。配重块的质量和安装位置需要根据检测到的不平衡情况进行精确计算。为了提高校正效率,现代的自动校正系统通常会采用优化算法来确定最佳的校正方案,以减少校正次数和时间。 自动校正的执行 一旦校正策略确定,自动校正系统就会开始执行校正操作。对于去重法,系统会控制加工设备,如钻孔机或磨床,按照预定的方案在转子上进行加工。在加工过程中,系统会实时监测加工情况,确保去除的材料量符合计算要求。 对于加配重法,系统会控制机器人或其他自动化设备,将配重块准确地安装到转子的指定位置。安装过程需要保证配重块的安装牢固,并且位置精度要满足要求。 在自动校正过程中,还会进行实时监测和反馈。系统会再次检测校正后的转子振动情况,以验证校正效果。如果校正后仍然存在一定的不平衡量,系统会根据新的检测结果重新调整校正策略,并进行二次校正,直到转子的不平衡量达到允许的范围内。 系统的智能化与优化 随着科技的不断发展,转子动平衡自动校正技术也在不断智能化和优化。现代的自动校正系统通常采用先进的算法和控制技术,如神经网络、模糊控制等,来提高系统的自适应能力和校正精度。 神经网络可以对大量的历史数据进行学习和分析,从而更准确地预测转子的不平衡情况,并优化校正策略。模糊控制则能够处理一些不确定因素,如传感器误差、加工误差等,提高系统的稳定性和可靠性。 此外,系统还会不断进行自我优化。通过对每次校正过程的数据进行记录和分析,系统可以总结经验教训,不断改进校正算法和策略,以提高校正效率和质量。 转子动平衡自动校正技术是一个复杂而精密的系统工程,它通过不平衡检测、校正策略制定、自动校正执行以及系统的智能化优化等环节,实现了转子动平衡的高效、精准校正。随着工业技术的不断进步,这项技术也将在更多领域发挥重要作用,为旋转机械的稳定运行提供有力保障。
03
2025-06
转子动平衡自动检测的误差来源有哪些
转子动平衡自动检测的误差来源有哪些 在现代工业生产中,转子动平衡自动检测技术至关重要,它能保障旋转机械的稳定运行和高精度工作。然而,检测过程中不可避免地会产生误差。深入了解这些误差来源,对于提高检测精度和产品质量意义重大。下面就详细探讨转子动平衡自动检测的误差来源。 传感器误差 传感器作为自动检测系统的关键部件,其性能直接影响检测结果。传感器本身的精度限制会带来误差。不同类型的传感器,如位移传感器、速度传感器和加速度传感器等,都有各自的精度指标。如果传感器精度不足,就无法准确捕捉转子的振动信号,导致检测数据出现偏差。 传感器的安装位置和方式也会引发误差。安装位置不当,可能无法检测到转子真实的振动情况。例如,安装在远离不平衡位置的地方,振动信号在传递过程中会衰减和失真,使得检测到的信号不能反映转子的实际不平衡状态。安装方式不牢固,会使传感器在检测过程中产生额外的振动,干扰正常信号的采集,从而引入误差。 信号处理误差 在自动检测系统中,传感器采集到的原始信号需要经过一系列的处理才能得到有用的信息。信号处理过程中的滤波环节可能产生误差。滤波的目的是去除信号中的噪声,但如果滤波器的参数设置不合理,可能会在去除噪声的同时,也过滤掉了一些有用的信号成分,导致信号失真,进而影响对转子不平衡量的准确判断。 信号放大过程也存在误差风险。放大倍数设置不合适,会使信号要么过小而无法准确测量,要么过大而超出系统的测量范围,造成信号饱和失真。此外,信号的数字化过程中,采样频率和量化精度的选择也会影响信号处理的准确性。采样频率过低,会导致信号信息丢失;量化精度不足,会使信号的细节信息无法准确表示,这些都会给检测结果带来误差。 环境因素误差 环境因素对转子动平衡自动检测也有显著影响。温度变化会引起转子材料的热胀冷缩,改变转子的几何形状和质量分布,从而导致不平衡量发生变化。同时,温度的变化还会影响传感器和检测系统中其他部件的性能,如改变传感器的灵敏度和电子元件的参数,使检测结果产生误差。 检测现场的电磁干扰也是误差的重要来源。电磁干扰会在传感器和信号传输线路中产生感应电流,干扰正常的信号传输,使检测系统接收到错误的信号。例如,附近的电机、变压器等设备产生的电磁场,都可能对检测系统造成干扰,影响检测的准确性。 转子自身特性误差 转子的制造工艺和材料不均匀性会导致自身特性存在差异,进而影响动平衡检测结果。制造过程中的加工精度不高,会使转子的几何形状偏离设计要求,如转子的圆柱度、同轴度等不符合标准,这些几何误差会产生额外的不平衡量,干扰检测系统对真实不平衡量的检测。 材料的不均匀性会使转子的质量分布不均匀。即使在设计上转子是平衡的,但由于材料密度的差异,也会导致实际存在不平衡现象。此外,转子在长期运行过程中会发生磨损和变形,进一步改变其质量分布和不平衡状态,使得检测结果与实际情况产生偏差。 转子动平衡自动检测的误差来源是多方面的。要提高检测精度,就需要从传感器的选择和安装、信号处理算法的优化、环境条件的控制以及对转子自身特性的了解等多个角度入手,采取有效的措施来减少误差的影响,确保旋转机械的稳定运行和产品质量的提高。
03
2025-06
转子动平衡自动检测系统的传感器类型
转子动平衡自动检测系统的传感器类型 在精密机械的旋转世界里,转子动平衡检测如同为高速运转的齿轮编织安全网。传感器作为系统感知振动的”神经末梢”,其类型选择直接决定检测精度与故障预警能力。从基础振动捕捉到环境适应性监测,传感器家族以多维度数据编织出动态平衡的立体画像。 一、振动感知三剑客:捕捉旋转失衡的微观震颤 加速度传感器(Accelerometer) 以压电效应为灵魂的加速度传感器,如同机械听诊器般实时捕捉转子振动的加速度信号。MEMS微型化技术使其能在10kHz高频振动中保持0.1%的精度,航空发动机叶片动平衡检测中,其输出的加速度频谱图能精准定位质量偏心位置。 速度传感器(Velocity Transducer) 电涡流式速度传感器通过电磁感应原理,将振动速度转化为电信号。在燃气轮机转子检测中,其低频响应特性(0.1-1000Hz)完美匹配转子临界转速区间的振动特征,配合相位分析可实现0.1°精度的不平衡相位定位。 位移传感器(Displacement Sensor) 电容式位移传感器以纳米级分辨率监测轴承座振动位移。在高速电机检测中,其非接触式测量特性避免了传感器安装对转子系统的干扰,配合频域分析可识别0.01mm级的轴心轨迹偏移。 二、进阶型传感器:多维度数据融合的精密协奏 应变片(Strain Gauge) 电阻应变片通过金属丝形变实现扭矩与弯曲应力的实时监测。在船舶推进器动平衡检测中,分布式应变网络可构建转子应力云图,结合频域分析实现质量偏心与结构共振的耦合诊断。 光电编码器(Optical Encoder) 增量式光电编码器以每转百万级脉冲精度记录转子角位移。在数控机床主轴检测中,其输出的TTL脉冲信号与振动信号同步采样,通过FFT变换可提取0.01g级的不平衡响应。 温度传感器(Thermocouple) K型热电偶通过Seebeck效应监测转子温升。在航空发动机盘车检测中,其多点温度数据与振动信号关联分析,可识别热膨胀引起的瞬态不平衡。 三、环境适应型传感器:极端工况下的可靠哨兵 压力传感器(Pressure Transducer) 陶瓷压阻式压力传感器在真空环境下仍保持0.05%FS的精度。卫星陀螺仪动平衡检测中,其封装在氦质谱检漏仪内,实时监测腔体压力波动对转子振动的影响。 光纤传感器(Fiber Optic Sensor) 分布式光纤传感器以 Brillouin 散射原理实现转子全周向温度与应变监测。在核主泵检测中,其耐辐射特性(10kGy)和抗电磁干扰能力,确保极端环境下的数据可靠性。 振动分析仪(Vibration Analyzer) 手持式振动分析仪集成IEPE供电与FFT分析功能。在风电主轴现场检测中,其自动包络解调技术可识别0.1mm/s的轴承故障特征频率,实现动平衡与故障诊断的协同分析。 四、智能传感器系统:从数据采集到决策支持的进化 现代动平衡检测系统正朝着多传感器融合方向发展。加速度传感器阵列与陀螺仪组合构成六自由度振动监测平台,配合深度学习算法可实现不平衡、不对中、松动等12类故障的智能诊断。在航空发动机试车台中,这种智能传感系统将检测响应时间缩短至30秒,误报率降低至0.2%。 传感器技术的革新正重塑动平衡检测的边界。从单一振动测量到多物理场融合,从离线检测到实时控制,这些精密的”机械听诊器”不仅提升检测精度,更推动着旋转机械从故障维修向预测性维护的范式转变。在追求零故障的工业4.0时代,传感器的多样性与智能化将成为转子动平衡检测系统的核心竞争力。
03
2025-06
转子动态动平衡机如何选择型号和精度等···
转子动态动平衡机如何选择型号和精度等级 在工业生产的广阔天地里,转子动态动平衡机是确保旋转机械稳定运行的关键设备。从航空航天的精密仪器到汽车制造的发动机,再到电力行业的大型发电机,动平衡机都发挥着不可替代的作用。那么,面对市场上琳琅满目的型号和精度等级,我们该如何做出明智之选呢? 考量转子的特性 转子,作为动平衡机的“服务对象”,其特性是选择合适动平衡机的首要依据。尺寸大小是一个关键因素,大型转子需要能够容纳并稳定支撑其重量和尺寸的动平衡机,否则可能因支撑不稳导致测量误差甚至设备损坏。例如,风电行业的大型发电机转子,其直径可达数米,长度数十米,必须选择具有足够大工作空间的动平衡机。而小型转子,如手机振动马达的转子,对动平衡机的空间要求则相对较低,但对测量精度的要求可能更高。 重量同样不容忽视。不同重量的转子对动平衡机的承载能力和测量精度有不同要求。较重的转子需要动平衡机具备更强的支撑能力和更大的驱动功率,以保证能够稳定地带动转子旋转进行测量。例如,大型船舶发动机的曲轴,重量可达数吨,就需要配备承载能力强的重型动平衡机。而较轻的转子,如小型电机的转子,对动平衡机的承载要求较低,但对测量的灵敏度要求较高,以检测出微小的不平衡量。 形状也是影响动平衡机选择的重要因素。规则形状的转子,如圆柱体、圆盘等,在动平衡测量时相对容易处理,大多数通用型动平衡机都可以满足要求。然而,不规则形状的转子,如螺旋桨、叶轮等,由于其质量分布不均匀且形状复杂,需要专门设计的动平衡机来适应其特殊的形状和结构,以确保准确测量和校正不平衡量。 明确生产需求 生产规模是选择动平衡机的重要考量因素之一。对于大规模生产的企业来说,提高生产效率是关键。因此,需要选择自动化程度高、测量速度快的动平衡机。这类动平衡机通常具备自动上下料、自动测量和校正功能,能够实现连续、高效的生产作业。例如,汽车发动机生产线上,为了满足大规模生产的需求,会配备自动化的动平衡机,每小时可以完成数十个甚至上百个发动机转子的动平衡校正。 而对于小批量生产或定制化生产的企业来说,灵活性则更为重要。此时,可以选择通用性强、易于调整的动平衡机,以便能够快速适应不同规格和类型的转子。例如,一些小型机械加工厂,可能需要为不同客户生产各种规格的小型电机转子,选择一台可以方便调整测量参数和夹具的动平衡机,能够更好地满足其生产需求。 此外,生产精度要求也是决定动平衡机精度等级的关键因素。不同的应用场景对转子的平衡精度要求差异很大。在航空航天领域,由于对飞行安全和设备性能的要求极高,转子的平衡精度要求通常非常严格,需要选择高精度等级的动平衡机。例如,飞机发动机的转子,其不平衡量的允许值可能只有几毫克甚至更低,必须使用高精度的动平衡机进行精确校正。而在一些对精度要求相对较低的普通工业应用中,如风扇、水泵等设备的转子,选择中等精度等级的动平衡机即可满足生产需求。 评估精度等级 动平衡机的精度等级直接关系到转子的平衡效果和设备的运行性能。精度等级通常用最小可达剩余不平衡量和不平衡量减少率来表示。最小可达剩余不平衡量越小,说明动平衡机能够将转子的不平衡量校正到更低的水平;不平衡量减少率越高,说明动平衡机在一次校正过程中能够更有效地减少转子的不平衡量。 在选择精度等级时,需要根据转子的实际应用需求和行业标准来确定。一般来说,对于高速旋转的转子,如汽轮机、离心机等,由于其对振动和噪声的敏感性较高,需要选择高精度等级的动平衡机,以确保转子在高速运行时的稳定性和可靠性。而对于低速旋转的转子,如一些普通的传动设备,对精度的要求相对较低,可以选择较低精度等级的动平衡机。 同时,还需要考虑精度等级与成本的关系。高精度等级的动平衡机通常价格较高,而且对使用环境和操作人员的要求也相对较高。因此,在选择时需要综合考虑生产需求和成本因素,避免过度追求高精度而造成不必要的成本浪费。 考察厂家实力 选择动平衡机时,厂家的实力也是一个重要的考量因素。一个具有雄厚技术实力和丰富生产经验的厂家,能够提供更优质的产品和更完善的售后服务。 技术实力体现在动平衡机的设计、制造和研发能力上。先进的设计理念和制造工艺能够保证动平衡机的性能和质量。例如,一些知名厂家采用先进的传感器技术和信号处理算法,能够提高动平衡机的测量精度和稳定性。同时,具备强大研发能力的厂家能够不断推出新产品和新技术,以满足市场不断变化的需求。 生产经验也是衡量厂家实力的重要指标。有多年生产经验的厂家,在生产过程中积累了丰富的实践经验,能够更好地解决生产中遇到的各种问题,保证产品的质量和可靠性。此外,生产经验丰富的厂家通常拥有更完善的质量控制体系,能够对产品进行严格的检测和检验,确保每一台动平衡机都符合相关标准和要求。 售后服务同样不可忽视。动平衡机在使用过程中可能会出现各种故障和问题,及时、专业的售后服务能够确保设备的正常运行,减少停机时间和生产损失。一个好的厂家应该能够提供全方位的售后服务,包括设备安装调试、操作培训、维修保养、技术支持等。 总之,选择合适型号和精度等级的转子动态动平衡机需要综合考虑转子的特性、生产需求、精度等级和厂家实力等多方面因素。只有这样,才能选择到最适合自己生产需求的动平衡机,提高生产效率,保证产品质量,为企业的发展奠定坚实的基础。
03
2025-06
转子动态动平衡机测量误差大的原因及解···
转子动态动平衡机测量误差大的原因及解决方法 一、环境干扰的多维渗透 在精密测量领域,环境干扰如同潜伏的幽灵,其影响维度远超常规认知。振动源耦合效应表现为车间设备共振、地基微震与管道流体脉动的叠加,形成非线性干扰场。某航空发动机转子车间案例显示,当机床主轴转速与厂房横梁固有频率共振时,振动幅值可放大3.2倍,导致相位误差达±15°。温度场梯度变化则通过材料热膨胀系数差异引发结构畸变,某高温合金转子实测显示,环境温度每波动1℃,轴颈径向位移变化0.008mm,相当于0.5g平衡质量误差。气流扰动的湍流效应在高速旋转场景尤为显著,当风速超过0.5m/s时,气膜刚度变化可导致振幅测量偏差±12%。 解决方案矩阵: 建立三维振动隔离系统(主动+被动+智能) 部署分布式温度补偿传感器网络 采用气动密封舱实现微正压环境控制 二、设备精度的衰减机制 传感器的退化遵循非线性衰减曲线,某精密电涡流传感器实测显示,使用500小时后线性度误差从0.1%上升至0.8%。轴承预紧力的动态变化形成”刚度漂移”,某高速主轴测试表明,当预紧力偏差达5%时,支撑刚度变化导致振型误差达±18%。驱动系统的谐波失真在高频段尤为致命,某120krpm转子实验中,驱动电机电流谐波含量每增加1%,转速波动幅值增大4.7%。 技术干预策略: 实施传感器动态标定(在线+离线双模) 开发预紧力自适应调节机构 采用矢量控制变频器消除谐波 三、操作误差的链式反应 安装误差的耦合效应形成多米诺骨牌效应,某精密转子安装案例显示,当轴向窜动量超过0.01mm时,不平衡响应误差呈指数增长。数据采集的相位同步误差在高速场景尤为致命,某150krpm转子测试中,0.1°相位偏差导致质量计算误差达±3g。参数设置的非最优组合形成”蝴蝶效应”,某软件仿真显示,当采样频率与转速比不满足20:1时,频谱泄漏导致有效值误差达±25%。 人机协同优化方案: 开发智能安装引导系统(视觉+触觉反馈) 建立相位同步冗余校验机制 构建参数优化决策树模型 四、转子特性的非线性挑战 模态耦合现象在柔性转子中呈现级数增长,某航空转子测试显示,当工作转速接近临界转速的80%时,振型误差达±35%。材料各向异性的应力释放形成”记忆效应”,某钛合金转子实测显示,加工残余应力导致不平衡量日均变化0.3g。边界条件的动态变化形成”虚拟不平衡”,某高速主轴测试中,轴承油膜刚度变化导致等效不平衡量波动±1.2g。 创新应对路径: 应用模态解耦算法(ARMA+小波去噪) 开发残余应力在线监测系统 建立边界条件动态补偿模型 五、数据处理的维度突破 频域分析的局限性在复杂工况下暴露无遗,某航空发动机测试显示,当存在2个以上故障特征频时,传统FFT方法误判率达43%。时域分析的噪声敏感性形成精度瓶颈,某精密转子测试中,信噪比每下降6dB,均方根误差增大2.8倍。多源数据融合的异构性导致信息丢失,某复合传感器系统测试显示,数据融合误差达±15%。 智能处理范式: 构建混合域分析模型(时频联合+深度学习) 开发自适应滤波算法(LMS+粒子群优化) 建立异构数据标准化转换框架 六、系统集成的协同进化 误差传递的链式反应需要系统级控制,某精密动平衡系统实测显示,单点误差放大系数可达17.3。人机交互的界面优化形成降维打击,某改进型HMI系统使操作失误率下降68%。全生命周期管理的缺失导致隐性误差累积,某转子维修数据表明,未实施预防性维护的设备误差增长率达3.2%/年。 系统工程解决方案: 构建误差传递反向追踪模型 开发增强现实辅助操作界面 建立数字孪生健康管理平台 通过上述多维度、跨学科的误差控制体系,某高端动平衡机实测显示,不平衡量测量不确定度从±5g降至±0.8g,测量效率提升400%,为精密制造领域提供了可复制的误差控制范式。这种将传统机械工程与现代智能技术深度融合的解决方案,正在重新定义动平衡技术的精度边界。
03
2025-06
转子去重平衡机与传统平衡机的区别
转子去重平衡机与传统平衡机的区别 技术原理:经验驱动 vs 数据驱动 传统平衡机依赖操作者对转子振动特性的经验判断,通过人工标记去重区域或配重位置,其核心逻辑是”试错-修正”的循环。而转子去重平衡机以激光扫描、动态建模为核心,通过实时采集转子三维形貌数据,结合有限元分析算法,生成精准的去重路径。这种差异如同从”盲人摸象”进化为”全息测绘”,前者受限于个体经验的碎片化,后者则构建了完整的数字孪生模型。 应用场景:标准化生产 vs 复杂工况适配 传统平衡机在汽车轮毂、电机轴等标准化产品中表现稳定,但面对航空发动机叶片、风电主轴等异形转子时,其刚性流程易导致平衡精度衰减。转子去重平衡机则通过柔性夹具系统和多轴联动技术,可处理曲面去重、局部应力补偿等复杂需求。例如在航天领域,某型号火箭发动机转子经传统平衡机处理后残余振动值为0.3mm/s²,而采用去重技术后降至0.08mm/s²,差异源于对非对称质量分布的精准解析。 操作流程:线性迭代 vs 自主决策 传统平衡机的操作链路呈现明显的线性特征:振动检测→人工标记→去重/配重→复测→重复循环。这种模式在批量生产中效率受限,单次平衡周期常达2-3小时。转子去重平衡机则通过闭环控制系统实现”感知-决策-执行”的自主迭代,某案例显示,某航空转子的平衡过程从传统模式的12次迭代缩短至3次,且单次处理时间压缩至15分钟。这种变革类似于将”手工雕刻”升级为”数控加工”。 经济性:短期成本 vs 长期价值 传统平衡机的设备购置成本通常低于转子去重机型30%-50%,但其隐性成本常被忽视:某汽车零部件企业数据显示,传统平衡工艺的废品返工率高达7.2%,而采用去重技术后降至1.5%。从全生命周期看,转子去重平衡机在3年内即可通过减少材料浪费、提升良品率实现投资回报。这种差异恰似”买马车”与”造高铁”的抉择——前者适合短途运输,后者重构了工业价值网络。 未来趋势:工业4.0的必然选择 随着数字孪生、边缘计算技术的渗透,转子去重平衡机正从单一设备进化为智能平衡生态系统。某头部厂商已实现云端平衡数据库的实时更新,使设备能自动适配新转子类型。而传统平衡机的数字化改造面临硬件兼容性、算法迭代等多重壁垒。这种技术代际差异,预示着未来十年工业平衡领域将呈现”去重技术主导80%高端市场”的格局。 结语 从振动补偿到质量重构,从人工经验到智能决策,转子去重平衡机不仅革新了平衡技术范式,更重塑了精密制造的价值链条。当工业4.0的浪潮席卷而来,这场平衡革命的本质,是制造业从”消除缺陷”向”创造完美”的范式跃迁。