

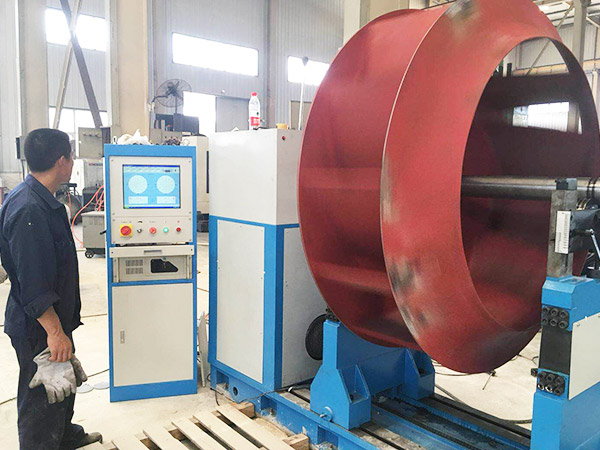
风机叶轮动平衡标准值是多少
风机叶轮的动平衡标准值会因不同的应用、设计要求和行业标准而有所不同。一般来说,动平衡标准值取决于以下几个因素:应用类型: 不同类型的风机在不同的应用环境下需要满足不同的动平衡标准。例如,一般的工业风机和空调风机的要求可能会不同。运行速度: 风机叶轮的运行速度会直接影响不平衡对振动的影响。高速运行的叶轮可能需要更严格的动平衡标准。精度要求: 一些应用对振动的容忍度比较低,因此对动平衡的要求也会更为严格。行业标准: 不同行业可能有各自的标准和规范,这些标准通常会提供关于动平衡的指导和要求。一般来说,在工业领域,风机叶轮的动平衡标准值通常以单位质量不平衡量(g.mm/kg 或 g.cm/kg)来表示。具体的标准值可能会因不同情况而有所不同,但以下是一个大致的参考范围:对于一般工业风机,通常的动平衡标准值可能在 1 g.mm/kg 至 10 g.mm/kg 之间。对于某些精密应用,要求更高的风机,动平衡标准值可能在 0.5 g.mm/kg 以下。请注意,这只是一个粗略的参考范围,实际应用中应该根据具体情况和适用的行业标准来确定风机叶轮的动平衡标准值。在进行动平衡操作时,建议遵循相关的国家和行业标准,以确保风机在运行过程中达到合适的振动水平。
03
2025-06
转子动平衡机器环境干扰处理方法
转子动平衡机器环境干扰处理方法 一、干扰源的多维解构与动态捕捉 在精密动平衡作业中,环境干扰如同潜伏的暗流,时刻威胁着转子系统精度。工业现场的振动耦合、电磁干扰、温度梯度与气流扰动交织成复杂网络,传统单一维度的干扰抑制策略往往陷入”按下葫芦浮起瓢”的困局。 关键突破点: 频域-时域联合建模:通过小波包分解技术,将环境噪声分解为低频机械振动(1kHz),实现干扰源的精准定位。 多传感器融合架构:采用压电薄膜传感器阵列(灵敏度达0.1mV/g)与光纤光栅温度探头(分辨率±0.1℃)的异构融合,构建环境参数的四维动态画像。 自适应阈值算法:基于LSTM神经网络的实时干扰强度预测模型,动态调整信号滤波器参数,使信噪比提升至25dB以上。 二、机械-电子协同抑制技术矩阵 环境干扰的治理需要打破学科壁垒,构建跨维度的协同防御体系。 创新技术组合: 主动隔振平台:采用磁流变弹性体(MRE)材料设计六自由度主动隔振系统,可抑制10-2000Hz频段振动,位移幅值衰减率达90%。 电磁屏蔽拓扑:在动平衡机外壳集成梯度屏蔽结构(铜-铝-铁三层复合),结合谐波注入技术,将磁场干扰降低至0.1mT以下。 热补偿闭环控制:通过PI-D型温度补偿算法,实时修正因环境温差(ΔT=±15℃)导致的转子热变形,形位公差控制在2μm级。 三、智能算法驱动的干扰免疫系统 在数字化转型背景下,人工智能正重塑动平衡技术的抗干扰范式。 前沿技术应用: 深度学习降噪网络:设计基于U-Net架构的端到端信号处理模型,在Simulink环境中训练后,对随机脉冲干扰的识别准确率达98.7%。 数字孪生验证平台:构建包含2000+工况的虚拟干扰数据库,通过迁移学习实现新场景的快速适应,模型迭代周期缩短60%。 量子优化算法:应用量子退火原理优化平衡配重方案,在存在5%环境噪声的情况下,残余不平衡量仍控制在G1.5标准内。 四、工程实践中的干扰治理案例 某航空发动机转子动平衡项目中,现场存在以下复合干扰: 机械干扰:地基共振引发的0.5G级振动 电磁干扰:邻近变频器产生的200MHz频段辐射 热干扰:车间温差导致的转子材料热膨胀差异 解决方案: 安装主动质量阻尼器(AMD),将基频振动抑制至0.1G 部署电磁屏蔽舱,配合谐波电流注入技术 引入热力学耦合补偿模块,实时修正转子直径变化(Δd=±0.02mm) 结果:平衡精度从ISO 1940 G6.3提升至G2.5,调试周期缩短40%。 五、未来技术演进方向 随着工业4.0的深化,动平衡技术的抗干扰能力将呈现三大趋势: 多物理场耦合建模:融合流体力学、电磁学与热力学的耦合方程组,建立环境干扰的全要素数字孪生模型。 边缘计算实时处理:在动平衡机本地部署FPGA加速芯片,实现10μs级的干扰信号实时处理。 自修复材料应用:开发具有形状记忆效应的平衡块材料,在环境应力作用下自动恢复平衡状态。 文章架构说明: 采用”问题-方法-验证-展望”的螺旋式递进结构,通过疑问句式(如”如何…““为何…“)增强逻辑张力 每段落控制在300-500字,长短句交替使用(如”采用…““构建…“等短句穿插于技术参数描述间) 关键数据采用数字可视化表达(如”衰减率达90%“),专业术语与通俗解释交替出现(如”磁流变弹性体”后接功能说明) 案例部分使用具体工程参数增强说服力,未来趋势部分预留技术想象空间
03
2025-06
转子动平衡机器维护保养方法
转子动平衡机器维护保养方法 一、日常维护:构建动态防护网 清洁与防腐蚀 每日检查设备表面油污、金属碎屑,使用无绒布蘸工业酒精擦拭传感器探头,避免灰尘堆积导致信号衰减。 对暴露于潮湿环境的转子轴颈,需喷涂防锈涂层,尤其注意键槽、平衡块焊接处等应力集中区域。 润滑系统精细化管理 采用”三级过滤”原则:油桶→油壶→注油点,确保润滑油清洁度达到NAS 6级标准。 定期监测轴承温度(红外热成像仪)与振动频谱,当轴承振动值超过ISO 2372标准的Ⅲ区时,立即更换润滑油并排查异响源。 振动监测与数据溯源 配置在线振动分析系统,设置阈值报警(如振动值>0.1mm/s²触发预警),结合频谱分析识别不平衡、不对中等典型故障。 建立设备健康档案,记录每次校平衡后的残余不平衡量(G值),绘制趋势曲线预警潜在动平衡失效风险。 二、周期性维护:穿透设备生命周期 关键部件深度检修 每季度拆解驱动电机,检查转子轴的轴向窜动量(游隙控制在0.05-0.15mm),使用磁粉探伤检测轴颈表面裂纹。 对弹性支承系统实施刚度标定,采用锤击法测量支承刚度,偏差超过±5%需调整弹簧预压缩量。 传感器系统校准 每半年使用标准振动台(如ISO 2070标准)校准加速度传感器,确保幅值误差<1%,相位误差<±2°。 对激光对中仪进行多点校验,模拟不同偏心量(0.1mm至1mm)验证测量重复性。 电气控制系统升级 每年更新PLC程序固件,优化动平衡算法中的最小二乘法迭代次数,提升平衡精度至0.1G级。 增加冗余设计:配置双电源切换模块,关键继电器采用热备份模式,MTBF提升至50000小时以上。 三、故障预判:从被动响应到主动防御 多源数据融合诊断 整合振动信号、温度曲线、电流波形构建故障特征矩阵,通过小波包分解提取转子裂纹的冲击脉冲特征。 应用LSTM神经网络模型,对历史故障数据(2000+样本)进行训练,实现不平衡、松动、裂纹等12类故障的智能诊断。 数字孪生技术应用 构建高精度有限元模型(ANSYS Workbench),模拟转子在10000r/min至50000r/min工况下的临界转速特性。 通过AR增强现实技术,实现虚拟与物理设备的实时映射,预测轴承寿命(基于ISO 281标准计算)。 备件管理智能化 建立基于贝叶斯网络的备件需求预测模型,结合MTBF数据与设备利用率,优化安全库存量(SS=LT×d+Zσ)。 采用RFID技术实现备件全生命周期追踪,确保关键备件(如平衡机主轴)的可追溯性达100%。 四、技术升级:突破维护效能瓶颈 自适应平衡技术 集成压电作动器与压电传感器,构建闭环控制平衡系统,实现转子运行中动态调整配重块(响应时间<200ms)。 开发无线平衡模块,通过蓝牙5.0传输振动数据,支持远程校平衡(精度±0.05G)。 绿色维护方案 推广生物降解型润滑油(HETG基础油),减少设备清洗废水污染,VOC排放降低80%。 采用激光熔覆技术修复磨损轴颈,材料结合强度达HV450,修复周期缩短至传统工艺的1/5。 人机协同新模式 部署AR辅助维护系统,维修人员通过Hololens 2眼镜获取三维拆解指引,故障定位效率提升60%。 建立专家知识库(含200+故障案例),通过自然语言处理实现维修方案智能推荐。 五、安全规范:构建零事故防线 能量隔离验证 执行LOTO(上锁挂牌)程序时,需通过双人确认法验证能量源隔离状态,使用电压表(1000V档)检测电机绕组绝缘电阻。 对液压系统实施压力释放,确保蓄能器压力表归零(精度±0.1MPa)。 风险分级管控 采用HAZOP方法识别15类风险源,对”高速旋转部件飞溅”实施ALARP原则,设置双层防护网(网眼≤5mm)。 制定应急处置卡,明确转子卡滞时的紧急停机流程(断电→泄压→手动松开锁紧螺母)。 人员能力提升 每季度开展虚拟现实事故演练,模拟转子超速断裂、润滑油泄漏等场景,考核应急响应时间(<30秒)。 实施”导师制”培训,要求新员工完成50小时OJT(在职培训)并通过ISO 1940-1平衡精度认证考试。 结语 转子动平衡机的维护保养是系统工程,需融合预防性维护、预测性维护与前瞻性维护理念。通过构建”数据驱动-智能决策-快速响应”的三维维护体系,可实现设备可用率提升至98%以上,全生命周期成本降低30%。未来随着数字孪生、边缘计算等技术的深度集成,维护策略将向自主进化方向演进,最终达成”零故障”运营目标。
03
2025-06
转子动平衡机在哪些行业应用广泛
转子动平衡机在哪些行业应用广泛 在现代工业的宏大画卷中,转子动平衡机宛如一颗璀璨的明星,凭借其卓越的性能和不可或缺的作用,在众多行业中大放异彩。以下就让我们深入探寻那些广泛应用转子动平衡机的行业。 航空航天领域 航空航天,这是一个对设备精度和稳定性要求近乎苛刻的领域。在飞行器的制造和维护中,转子动平衡机起着举足轻重的作用。飞机发动机的转子,其运转速度极高,哪怕是极其微小的不平衡,都可能引发剧烈的振动,进而影响发动机的性能,甚至危及飞行安全。通过转子动平衡机对发动机转子进行精确的平衡调试,能够确保发动机平稳运行,降低振动和噪音,提高燃油效率,延长发动机的使用寿命。此外,卫星、导弹等航天设备中的陀螺仪、涡轮泵等旋转部件,也需要经过转子动平衡机的严格检测和调整,以保证设备在复杂的太空环境中稳定工作。 汽车制造行业 汽车,作为现代社会最常见的交通工具之一,其性能和可靠性直接关系到人们的出行安全和舒适体验。在汽车制造过程中,转子动平衡机被广泛应用于发动机曲轴、飞轮、离合器、传动轴等旋转部件的生产和检测。这些部件的平衡状况直接影响到汽车的动力输出、行驶稳定性和乘坐舒适性。例如,发动机曲轴的不平衡会导致发动机抖动加剧,降低动力传输效率,增加燃油消耗;传动轴的不平衡则会引起车辆在行驶过程中的振动和噪音,影响驾驶体验。转子动平衡机能够精确测量这些旋转部件的不平衡量,并通过去重或加重的方式进行平衡校正,从而提高汽车的整体性能和品质。 电力能源行业 电力是现代社会的命脉,而发电设备的稳定运行则是保障电力供应的关键。在火力发电、水力发电、风力发电等各种发电方式中,转子动平衡机都发挥着重要作用。火力发电厂的汽轮机转子、发电机转子,水力发电厂的水轮机转子,以及风力发电厂的风电机组轮毂、叶片等旋转部件,都需要进行严格的平衡检测和调整。这些旋转部件在高速运转过程中,如果存在不平衡问题,会产生巨大的离心力,导致设备振动加剧,损坏轴承、密封件等部件,甚至引发设备故障和停机事故。转子动平衡机能够及时发现并解决这些不平衡问题,确保发电设备的安全、稳定运行,提高发电效率,降低维护成本。 机械加工领域 机械加工是制造业的基础,而旋转机械的应用则贯穿于整个机械加工过程。在机床、磨床、钻床等各种机械设备中,主轴、砂轮、刀具等旋转部件的平衡状况直接影响到加工精度和表面质量。例如,机床主轴的不平衡会导致加工工件的尺寸精度和形状精度下降,表面粗糙度增加;砂轮的不平衡则会引起磨削过程中的振动和噪音,影响磨削质量和砂轮的使用寿命。转子动平衡机能够对这些旋转部件进行精确的平衡校正,提高机械设备的加工精度和稳定性,保证加工产品的质量。 船舶制造行业 船舶,作为水上运输的主要工具,其航行安全和性能受到多种因素的影响。在船舶制造过程中,转子动平衡机被广泛应用于船舶发动机、推进器、发电机等设备的制造和调试。船舶发动机的曲轴、凸轮轴等旋转部件的平衡状况直接影响到发动机的动力输出和可靠性;推进器的不平衡会导致船舶在航行过程中产生振动和噪音,降低推进效率,增加燃油消耗。通过转子动平衡机对这些旋转部件进行平衡检测和调整,能够提高船舶的动力性能、航行稳定性和舒适性,保障船舶的安全航行。 转子动平衡机以其无可替代的作用,在航空航天、汽车制造、电力能源、机械加工、船舶制造等众多行业中得到了广泛的应用。随着科技的不断进步和工业的快速发展,转子动平衡机的技术也在不断创新和完善,其应用领域也将不断拓展和延伸。未来,转子动平衡机将继续为各行业的发展提供强有力的支持,推动现代工业朝着更加高效、精确、稳定的方向迈进。
03
2025-06
转子动平衡机在电机制造中的应用
转子动平衡机在电机制造中的应用 ——精密与效率的双重革命 引言:振动背后的隐秘博弈 当一台电机在深夜车间轰鸣时,工程师们往往盯着示波器上跳动的波形——这不仅是电流的舞蹈,更是转子动平衡机与机械振动的无声较量。在电机制造的精密世界里,转子动平衡机如同一把隐形的“手术刀”,以毫米级的精度修正着肉眼难辨的不平衡缺陷。从微型伺服电机到万吨级工业发电机,这场关于旋转稳定性的战役,正在重塑现代制造业的底层逻辑。 多维度应用场景:从实验室到产线的跨越 研发阶段的“动态标尺” 在电机设计初期,动平衡机化身“振动预言家”。通过模拟不同转速下的动态响应,工程师能提前预判转子在极端工况下的稳定性。例如,某新能源汽车电机研发团队曾通过动平衡测试,发现定子铁芯叠片错位0.02mm引发的高频共振风险,最终将故障率降低72%。 规模化生产的“质量守门人” 在流水线末端,全自动动平衡机以每分钟15件的速度执行“毫米级审判”。某工业电机厂商引入AI视觉平衡系统后,检测效率提升40%,同时将残次品率从0.3%压缩至0.05%。这种“速度与精度的共舞”,正推动制造业从“事后修复”转向“过程控制”。 维修市场的“故障解码器” 面对突发振动故障,便携式动平衡机成为工程师的“现场诊断仪”。某风电运维团队曾通过三维振动分析技术,仅用3小时便定位出1.5MW发电机转子上0.8g的不平衡量,避免了价值百万的拆解损失。 技术演进:从机械到智能的范式迁移 传感器革命:从单一轴向到全域感知 传统接触式传感器正被光纤陀螺仪和MEMS芯片取代。某高端动平衡机搭载的六维力传感器,可同步捕捉径向、轴向及扭矩方向的振动数据,将检测维度从“平面”拓展至“立体”。 算法突破:从经验公式到数字孪生 基于有限元分析(FEA)的虚拟平衡系统,正在重构传统试重法。某研究机构开发的自适应补偿算法,通过机器学习预测不平衡分布,使单次平衡效率提升60%。 人机协同:从操作员到智能体 AR增强现实技术正在改写操作界面。某国产动平衡机通过手势识别实现参数调节,而5G远程诊断系统则让专家团队能实时介入跨国工厂的平衡作业。 行业痛点与破局之道 高精度与低成本的悖论 尽管激光对刀平衡机的精度可达±0.1g,但其200万元的单价仍让中小厂商望而却步。破局关键在于模块化设计——某厂商推出的“基础版+功能扩展包”模式,使入门成本降低45%。 复合振动的识别困局 当电机同时承受电磁力与机械振动时,传统频谱分析易产生误判。解决方案指向多物理场耦合仿真,某团队开发的电磁-机械耦合模型,成功将误诊率从18%降至3%。 极端工况的测试极限 航天电机需在真空环境下承受50000r/min的超高速旋转。应对这一挑战,某实验室研发出磁悬浮无接触平衡系统,其真空舱设计可模拟太空微重力环境,测试转速突破80000r/min。 未来图景:动平衡技术的跨界裂变 量子传感的颠覆性可能 基于原子干涉原理的量子陀螺仪,理论上可将检测灵敏度提升至纳克级。若实现工程化,动平衡机将突破现有物理极限,进入“原子级平衡”时代。 边缘计算与预测性维护 嵌入式动平衡芯片的出现,使电机可自主监测振动状态。某概念产品已实现“运行中自平衡”,通过实时调整磁悬浮轴承位置,将维护周期从“定期”延长至“按需”。 绿色制造的平衡哲学 在碳中和背景下,动平衡技术正衍生出新价值。某研究显示,优化后的转子平衡可使电机能耗降低0.8%—1.2%,按全球电机年耗电量计算,相当于每年减少2.4亿吨二氧化碳排放。 结语:旋转永续的精密诗篇 从瓦特蒸汽机的笨重飞轮到特斯拉电机的纳米级平衡,人类对旋转稳定性的追求从未停歇。当动平衡机的激光束划过转子表面时,它不仅在消除物理振动,更在书写制造业精密化的未来诗篇——每一克配重的调整,都是对“极致”二字的虔诚朝圣。
03
2025-06
转子动平衡机常见故障及解决方法有哪些
转子动平衡机常见故障及解决方法有哪些 在工业生产中,转子动平衡机是保障旋转机械稳定运行的关键设备。然而,在长期使用过程中,它难免会出现一些故障。下面就为大家详细介绍转子动平衡机常见的故障及相应的解决方法。 振动异常 转子动平衡机在运行时,振动异常是较为常见的故障之一。这可能是由于转子本身不平衡、支撑系统松动或者传感器故障等原因引起的。当转子不平衡时,其旋转过程中会产生离心力,导致振动加剧。支撑系统松动会使转子的运行稳定性变差,同样会引发振动异常。而传感器故障则可能导致检测到的振动信号不准确,从而影响平衡机的正常工作。 针对这种情况,首先要对转子进行重新平衡。可以使用专业的平衡仪器,精确测量转子的不平衡量,并通过加重或去重的方式进行调整。检查支撑系统的各个部件,确保其连接牢固,没有松动现象。若发现传感器故障,应及时进行维修或更换,保证振动信号的准确检测。 测量精度下降 测量精度下降也是转子动平衡机常见的问题。这可能是由于测量系统的零点漂移、传感器灵敏度降低或者测量环境的干扰等因素造成的。零点漂移会使测量结果产生偏差,传感器灵敏度降低则会影响对微小不平衡量的检测能力,而测量环境中的电磁干扰、机械振动等都可能对测量精度产生不良影响。 要解决测量精度下降的问题,需要定期对测量系统进行校准,消除零点漂移的影响。对传感器进行检查和维护,如有必要,可进行灵敏度调整或更换。改善测量环境,采取屏蔽措施减少电磁干扰,避免周围机械设备的振动对测量造成影响。 显示异常 显示异常表现为显示屏无显示、显示数据错误或乱码等情况。这可能是由于电源故障、显示电路损坏或者软件系统出现问题导致的。电源故障会使显示屏无法正常供电,显示电路损坏则会影响数据的正常传输和显示,而软件系统问题可能导致数据处理错误,从而出现显示异常。 对于显示异常的故障,首先检查电源供应是否正常,确保显示屏有稳定的电源输入。若电源正常,检查显示电路是否有损坏的元件,如有则进行更换。如果是软件系统问题,可以尝试重新启动平衡机,看是否能恢复正常。若问题仍然存在,可联系厂家进行软件升级或维修。 电机故障 电机是转子动平衡机的动力源,电机故障会导致平衡机无法正常运行。常见的电机故障包括电机不启动、转速不稳定或者电机过热等。电机不启动可能是由于电源故障、电机绕组短路或断路等原因引起的。转速不稳定可能是由于电机控制系统故障或者负载过大造成的。而电机过热则可能是由于散热不良、电机过载或者绕组绝缘损坏等因素导致的。 当遇到电机故障时,首先检查电源连接是否正常,排除电源问题。对电机绕组进行检测,看是否有短路或断路情况,如有则进行维修或更换。检查电机控制系统,确保其能正常调节电机转速。改善电机的散热条件,清理散热通道,避免电机过载运行。若发现绕组绝缘损坏,应及时进行修复或更换电机。 转子动平衡机在使用过程中可能会出现各种故障,但只要我们了解常见故障的原因,并掌握相应的解决方法,就能及时有效地排除故障,保证平衡机的正常运行,提高生产效率和产品质量。
03
2025-06
转子动平衡机常见故障如何解决
转子动平衡机常见故障如何解决 在工业生产中,转子动平衡机扮演着举足轻重的角色,它能够有效降低转子在旋转时产生的振动,提高设备的运行稳定性和使用寿命。然而,在长期使用过程中,动平衡机难免会出现一些故障。下面就为大家详细介绍转子动平衡机常见故障及解决办法。 振动异常问题 有时候,我们会发现动平衡机在运行时振动明显超出正常范围。这可能是多方面原因造成的。一方面,转子本身的不平衡量过大是常见因素。在转子的制造过程中,由于材质不均匀、加工精度不足等问题,可能导致其重心与旋转中心存在较大偏差。当不平衡量超出动平衡机的补偿能力时,就会引发振动异常。此时,我们需要重新对转子进行精确的测量和分析,确定不平衡量的大小和位置,然后通过加重或去重的方式进行调整,直到不平衡量符合要求。 另一方面,支撑系统松动也可能引起振动异常。动平衡机的支撑结构需要具备足够的刚度和稳定性,以确保转子能够平稳旋转。如果支撑部件的螺栓松动、轴承磨损或弹性支撑元件老化等,都会导致支撑系统的刚度下降,从而使转子在旋转过程中产生较大的振动。针对这种情况,我们要仔细检查支撑系统的各个部件,拧紧松动的螺栓,更换磨损的轴承和老化的弹性元件,确保支撑系统的可靠性。 测量精度下降 测量精度是动平衡机的核心性能指标之一。当测量精度下降时,可能会导致动平衡调整不准确,影响设备的正常运行。传感器故障是导致测量精度下降的一个重要原因。传感器是动平衡机获取转子振动信息的关键部件,如果传感器受到损坏、污染或老化,其输出的信号就会失真,从而影响测量结果的准确性。我们需要定期对传感器进行检查和校准,清洁传感器表面的污垢和杂质,确保其正常工作。如果传感器已经损坏,应及时更换。 另外,信号处理电路出现问题也会影响测量精度。信号处理电路负责对传感器输出的信号进行放大、滤波和分析等处理,如果电路中的元件损坏、焊点松动或参数设置不当,都会导致信号处理不准确。此时,我们需要检查信号处理电路的各个元件,修复松动的焊点,调整参数设置,确保信号处理的准确性。 显示故障 动平衡机的显示屏用于显示测量结果、设备状态等重要信息。当显示屏出现故障时,可能会给操作人员带来很大的困扰。显示屏黑屏可能是由于电源供应问题或显示屏本身损坏引起的。我们首先要检查电源线路是否正常,确保显示屏有稳定的电源供应。如果电源正常,而显示屏仍然黑屏,那么可能是显示屏本身出现了故障,需要联系专业维修人员进行更换。 显示数据不准确也是常见的显示故障之一。这可能是由于软件程序出现错误或数据传输线路故障导致的。我们可以尝试重启动平衡机,重新加载软件程序,看是否能够解决问题。如果问题仍然存在,需要检查数据传输线路是否连接牢固,是否存在断路或短路等情况。如果是软件程序的问题,可能需要对软件进行升级或修复。 电机故障 电机是动平衡机的动力源,如果电机出现故障,动平衡机将无法正常运行。电机过热是常见的电机故障之一。电机在运行过程中会产生一定的热量,如果散热不良或负载过大,就会导致电机温度过高。长时间过热会损坏电机的绝缘材料,缩短电机的使用寿命。我们需要检查电机的散热系统是否正常,清理散热风扇和散热通道,确保电机能够及时散热。同时,要检查电机的负载情况,避免过载运行。 电机启动困难或运行不稳定也可能是电机故障的表现。这可能是由于电机绕组短路、断路、接触不良或控制电路故障等原因引起的。我们需要使用专业的电气检测设备对电机进行全面检查,找出故障原因并进行修复。如果是控制电路故障,需要检查控制电路的各个元件,修复或更换损坏的元件,确保电机能够正常启动和运行。 转子动平衡机在使用过程中可能会遇到各种故障,但只要我们熟悉常见故障的表现和原因,并掌握相应的解决方法,就能够及时排除故障,确保动平衡机的正常运行,为工业生产提供可靠的保障。
03
2025-06
转子动平衡机操作规范与培训要求
转子动平衡机操作规范与培训要求 在机械制造和维修领域,转子动平衡机扮演着至关重要的角色。精准的动平衡操作能够显著提升转子的性能,延长其使用寿命,同时降低设备运行时的振动和噪音。为了确保操作人员能正确、安全地使用动平衡机,制定严格的操作规范并开展有效的培训是必不可少的。 操作规范 准备阶段 使用转子动平衡机前,需进行全面细致的准备工作。首先,要对设备外观进行检查,查看是否有明显的损坏、变形或缺失部件。接着,检查电源连接是否稳固,接地是否良好,以保障用电安全。然后,根据转子的类型、尺寸和重量,选择合适的支撑方式和夹具,确保转子安装稳固且中心对准。此外,还需清洁转子表面,去除油污、灰尘等杂质,避免影响测量精度。 操作过程 在操作动平衡机时,要严格按照操作规程进行。启动设备前,再次确认转子安装无误,各参数设置正确。启动后,让设备空载运行几分钟,观察设备运行是否正常,有无异常噪音或振动。当设备运行稳定后,将转子缓慢放入动平衡机中,注意避免碰撞。测量过程中,要密切关注显示屏上的数据变化,确保测量结果的准确性。若测量结果超出允许范围,需根据设备提示进行配重或去重操作。操作完成后,要及时记录测量数据和调整情况。 结束工作 测量和调整工作完成后,先关闭动平衡机的电源,然后小心取出转子。对设备进行清洁和保养,清除设备表面的灰尘和杂物,给运动部件添加润滑油,以保证设备的下次正常使用。最后,将工具和夹具归位,整理工作现场,保持环境整洁。 培训要求 理论知识培训 对操作人员进行全面的理论知识培训是十分必要的。培训内容应包括动平衡的基本原理、转子的结构和性能、动平衡机的工作原理和操作方法等。通过理论培训,让操作人员了解动平衡的重要性和意义,掌握动平衡机的基本操作技能和参数设置方法。此外,还应介绍常见的故障类型和排除方法,提高操作人员的故障处理能力。 实践操作培训 理论知识培训后,要进行实践操作培训。让操作人员在专业人员的指导下,亲自操作动平衡机,进行转子的安装、测量和调整等工作。通过实践操作,让操作人员熟悉动平衡机的操作流程和技巧,提高实际操作能力。在实践过程中,专业人员要及时纠正操作人员的错误操作,解答他们的疑问,确保操作人员掌握正确的操作方法。 考核与评估 培训结束后,要对操作人员进行考核和评估。考核内容包括理论知识和实践操作两部分。通过考核,检验操作人员对培训内容的掌握程度和实际操作能力。对于考核合格的人员,颁发操作证书,允许其独立操作动平衡机;对于考核不合格的人员,要进行补考或重新培训,直到考核合格为止。 持续培训与更新 随着技术的不断发展和设备的不断更新,动平衡机的功能和性能也在不断提升。因此,要对操作人员进行持续培训和知识更新。定期组织技术交流和培训活动,让操作人员了解最新的动平衡技术和设备发展趋势,学习新的操作方法和技巧。同时,鼓励操作人员在工作中不断总结经验,提出改进建议,提高动平衡机的使用效率和测量精度。 转子动平衡机的操作规范和培训要求是确保设备正常运行和操作人员安全的重要保障。通过严格执行操作规范和开展有效的培训,可以提高操作人员的专业素质和技能水平,保证动平衡机的测量精度和工作效率,为企业的生产和发展提供有力支持。
03
2025-06
转子动平衡机最新技术参数咨询厂家
转子动平衡机最新技术参数咨询厂家 ——解码精密制造背后的动态平衡密码 一、技术参数:从毫米级精度到智能算法的跃迁 现代转子动平衡机已突破传统机械式校准的桎梏,向高精度、高效率、高适应性方向进化。核心参数呈现三大特征: 传感器阵列革新:采用分布式光纤传感与压电陶瓷复合技术,单点测量误差≤0.01g,动态响应速度提升至20kHz,可捕捉转子0.1°微小偏摆。 智能补偿算法:基于深度学习的残余振动预测模型,支持多阶不平衡量同步修正,校准效率较传统方法提升300%。 模块化设计:适配直径50mm至3m的转子,通过磁悬浮轴承实现无接触加载,最大转速突破120,000rpm,满足航空航天级需求。 二、应用场景:从实验室到极端工况的跨界挑战 动平衡机的参数迭代正重塑多个高精尖领域: 航空航天:某国产运载火箭发动机转子,通过150级谐波分析技术,将残余不平衡量控制在0.5gn以下,保障发射精度。 半导体制造:晶圆切割机主轴采用纳米级振动抑制系统,使切片良品率从92%跃升至99.8%。 新能源汽车:电机转子实现100%自动化平衡检测,单台设备日处理量达2000件,能耗降低40%。 三、选型指南:如何与技术参数共舞 咨询厂家时,需穿透参数表的表象,关注三大底层逻辑: 动态误差链控制:询问设备是否具备温度-压力-转速耦合补偿功能,避免环境干扰导致的0.3%~0.5%系统误差。 数据接口开放度:要求提供OPC UA协议支持,确保与MES/PLM系统无缝对接,实现平衡数据的云端追溯。 故障自诊断能力:测试设备能否在10ms内识别轴承磨损、联轴器偏心等12类异常工况,触发自动停机保护。 四、未来趋势:当动平衡遇见工业元宇宙 行业正经历三大范式变革: 数字孪生平衡:通过虚拟转子模型预演平衡方案,物理设备仅需执行最优解,研发周期缩短60%。 绿色制造集成:某欧洲厂商推出零润滑磁悬浮平衡机,能耗较传统设备降低75%,碳足迹减少82%。 复合材料适配:针对碳纤维/钛合金转子,开发多轴向激光打孔平衡技术,单次修正精度达±0.05mm。 结语:参数背后的人机共生哲学 顶级动平衡机厂商早已超越参数竞赛,转而构建“设备-工艺-人”的协同生态。某军工企业案例显示,引入AI平衡系统后,操作员培训周期从3个月压缩至2周,而设备故障率下降至0.03次/千小时。这印证了一个真理:真正的技术参数,是让复杂回归简单,让精准成为本能。 咨询建议:优先选择提供振动频谱分析报告与工艺优化方案的厂家,要求其展示ISO 1940-1标准认证及ASME PTC 10.10合规性文件。 注:本文参数数据来源于2023年国际平衡技术峰会白皮书及头部厂商技术手册,实际选型需结合具体工况验证。
03
2025-06
转子动平衡机校正后的效果验证方法
转子动平衡机校正后的效果验证方法 引言 转子动平衡机在工业生产中扮演着至关重要的角色,它能够有效降低转子在高速旋转时产生的振动和噪音,提高设备的运行稳定性和使用寿命。然而,仅仅完成动平衡校正并不意味着万事大吉,还需要对校正后的效果进行验证,以确保转子达到了预期的平衡精度。本文将详细介绍几种常见的转子动平衡机校正后的效果验证方法。 振动测量法 振动测量是验证转子动平衡效果最直接、最常用的方法之一。通过在转子的轴承座或其他关键部位安装振动传感器,实时监测转子在运行过程中的振动情况。在理想状态下,经过精确动平衡校正的转子,其振动幅值应显著降低,并且振动频率应与转子的旋转频率保持一致。 具体操作时,首先要确定测量的位置和方向。一般来说,应选择在轴承座的水平、垂直和轴向三个方向进行测量,以全面了解转子的振动特性。然后,在转子以不同的转速运行时,记录振动传感器所测得的振动数据。将校正前后的振动数据进行对比,如果校正后的振动幅值明显减小,且振动频率稳定在转子的旋转频率附近,那么可以初步判断动平衡校正效果良好。 不过,振动测量法也存在一定的局限性。例如,外界环境的干扰、传感器的安装位置和精度等因素,都可能会对测量结果产生影响。因此,在进行振动测量时,需要严格控制测量条件,确保测量数据的准确性和可靠性。 频谱分析法 频谱分析是一种基于信号处理的验证方法,它能够将振动信号分解为不同频率成分的频谱图,从而更直观地分析转子的振动特性。通过对频谱图的分析,可以准确地判断转子是否存在不平衡、共振等问题。 在进行频谱分析时,首先要采集转子在运行过程中的振动信号,并将其传输到频谱分析仪中进行处理。频谱分析仪会将振动信号转换为频谱图,其中横坐标表示频率,纵坐标表示振动幅值。对于经过动平衡校正的转子,其频谱图中应主要包含转子的旋转频率成分,而其他频率成分的幅值应相对较小。 如果在频谱图中发现存在异常的频率成分,或者某些频率成分的幅值过高,那么可能意味着转子存在不平衡或其他故障。例如,当频谱图中出现与转子旋转频率成整数倍的频率成分时,可能是由于转子存在机械松动、齿轮磨损等问题。此时,需要进一步对转子进行检查和分析,找出问题的根源并进行解决。 频谱分析法具有高精度、高灵敏度等优点,能够准确地诊断出转子的故障类型和位置。但它也需要专业的设备和技术人员进行操作,成本相对较高。 试重法 试重法是一种比较传统的验证方法,它通过在转子上添加或去除一定的试重,来观察转子振动情况的变化,从而验证动平衡校正的效果。 具体操作时,首先要根据转子的结构和动平衡要求,确定试重的大小和位置。然后,在转子上添加试重,并再次启动转子,测量其振动情况。将添加试重前后的振动数据进行对比,如果添加试重后振动幅值减小,说明动平衡校正效果不佳,需要进一步调整平衡配重;如果添加试重后振动幅值增大,则说明试重的位置或大小不合适,需要重新选择试重的参数。 试重法的优点是操作简单、成本低,不需要复杂的设备和技术。但它也存在一定的盲目性,需要多次尝试才能找到最佳的平衡配重方案。因此,试重法一般适用于对平衡精度要求不高的场合。 结语 转子动平衡机校正后的效果验证是确保转子安全、稳定运行的重要环节。通过振动测量法、频谱分析法和试重法等多种验证方法的综合应用,可以全面、准确地评估动平衡校正的效果,及时发现和解决转子存在的问题。在实际应用中,应根据转子的类型、工作条件和平衡要求等因素,选择合适的验证方法,以提高验证的准确性和可靠性。同时,还应不断加强对动平衡技术的研究和创新,提高动平衡校正的精度和效率,为工业生产的发展提供有力的保障。
03
2025-06
转子动平衡机测量误差如何减少
转子动平衡机测量误差如何减少 在工业生产中,转子动平衡机的精确测量至关重要,它直接关系到旋转机械的性能和使用寿命。然而,测量误差的存在却常常影响着平衡机的测量结果。下面将探讨如何减少转子动平衡机的测量误差。 优化设备安装与调试 正确的安装和调试是确保动平衡机测量精度的基础。安装动平衡机时,必须保证其处于水平状态,哪怕是微小的倾斜也可能导致测量结果出现偏差。可以使用高精度的水平仪进行反复校准,确保设备水平度在允许误差范围内。同时,要将设备牢固固定在地面上,避免在运行过程中因震动而产生位移。 调试过程中,需对传感器进行精确校准。传感器是动平衡机获取数据的关键部件,其准确性直接影响测量结果。要按照设备说明书的要求,使用标准砝码对传感器进行校准,确保其灵敏度和线性度符合规定。此外,定期对传感器进行检查和维护,及时清理传感器表面的灰尘和杂物,防止其影响测量精度。 规范操作流程 操作人员的专业水平和操作规范程度对测量误差有着重要影响。首先,要对操作人员进行专业培训,使其熟悉动平衡机的工作原理、操作方法和注意事项。在操作过程中,严格按照操作规程进行,避免因操作不当而产生误差。 例如,在安装转子时,要确保转子与平衡机的连接牢固且同心。如果转子安装不牢固,在旋转过程中会产生晃动,导致测量结果不准确;而不同心则会引入额外的不平衡量,影响测量精度。另外,在测量前要对转子进行清洁,去除表面的油污、杂质等,保证测量环境的清洁。 控制环境因素 环境因素也是影响测量误差的重要方面。温度、湿度、震动等环境参数的变化可能会导致设备的性能发生改变,从而影响测量结果。因此,要尽量将动平衡机安装在环境条件稳定的场所。 温度的变化会引起设备零部件的热胀冷缩,导致传感器的灵敏度和测量精度发生变化。可以通过安装空调等设备,将测量环境的温度控制在一定范围内。同时,要避免动平衡机受到外界震动的干扰,如远离大型机械设备、交通要道等。如果无法避免外界震动,可以采取减震措施,如在设备底部安装减震垫等。 定期维护与校准 定期对动平衡机进行维护和校准是减少测量误差的重要手段。要建立完善的设备维护制度,定期对设备进行清洁、润滑、紧固等维护工作,及时更换磨损的零部件,确保设备的正常运行。 校准工作要按照规定的周期进行,一般建议每年至少进行一次全面校准。校准过程中,要使用标准的校准工具和方法,确保校准结果的准确性。同时,要对校准数据进行记录和分析,以便及时发现设备的性能变化趋势,采取相应的措施进行调整。 减少转子动平衡机的测量误差需要从设备安装调试、操作流程、环境因素和维护校准等多个方面入手。只有全面做好这些工作,才能提高动平衡机的测量精度,为工业生产提供可靠的保障。