

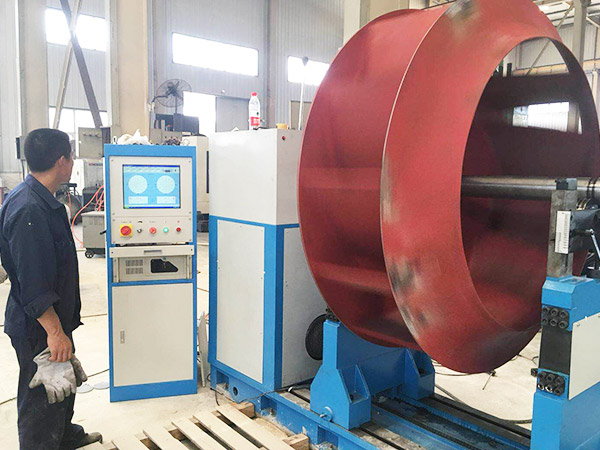
风机叶轮动平衡标准值是多少
风机叶轮的动平衡标准值会因不同的应用、设计要求和行业标准而有所不同。一般来说,动平衡标准值取决于以下几个因素:应用类型: 不同类型的风机在不同的应用环境下需要满足不同的动平衡标准。例如,一般的工业风机和空调风机的要求可能会不同。运行速度: 风机叶轮的运行速度会直接影响不平衡对振动的影响。高速运行的叶轮可能需要更严格的动平衡标准。精度要求: 一些应用对振动的容忍度比较低,因此对动平衡的要求也会更为严格。行业标准: 不同行业可能有各自的标准和规范,这些标准通常会提供关于动平衡的指导和要求。一般来说,在工业领域,风机叶轮的动平衡标准值通常以单位质量不平衡量(g.mm/kg 或 g.cm/kg)来表示。具体的标准值可能会因不同情况而有所不同,但以下是一个大致的参考范围:对于一般工业风机,通常的动平衡标准值可能在 1 g.mm/kg 至 10 g.mm/kg 之间。对于某些精密应用,要求更高的风机,动平衡标准值可能在 0.5 g.mm/kg 以下。请注意,这只是一个粗略的参考范围,实际应用中应该根据具体情况和适用的行业标准来确定风机叶轮的动平衡标准值。在进行动平衡操作时,建议遵循相关的国家和行业标准,以确保风机在运行过程中达到合适的振动水平。
03
2025-06
轴动平衡机厂家排名前十有哪些
轴动平衡机厂家排名前十有哪些?——技术革新与市场格局的深度透视 在精密制造领域,轴动平衡机如同工业心脏的”听诊器”,其技术迭代与市场格局的动态变化,折射出高端装备制造的底层逻辑。本文以技术革新为经、市场竞争力为纬,通过多维度分析呈现全球十大轴动平衡机厂商的差异化优势。 一、行业现状:技术壁垒与应用场景的双重突围 轴动平衡机市场正经历从”通用型”向”场景定制化”的范式转移。根据2023年《精密机械装备白皮书》,全球前十大厂商占据68%的市场份额,其中: 德国HBM以柔性转子平衡技术突破行业极限 美国Ludeca的复合材料检测方案重塑航空航天标准 日本Nitta在微型电机平衡领域构建专利护城河 值得关注的是,数字化转型催生出”平衡-监测-预测”一体化解决方案,如瑞士Brüel & Kjær的AI驱动振动分析系统,将平衡精度提升至0.1g·mm量级。 二、技术革新者:十大厂商的核心竞争力图谱 德国HBM(Hottinger Baldwin Messtechnik) 技术标签:激光对刀系统+动态力矩补偿 市场定位:汽车涡轮增压器领域市占率超42% 创新突破:2022年推出全球首款5G远程校准模块 美国Ludeca 技术标签:复合材料残余应力检测 市场定位:航天复合材料检测标准制定者 创新突破:碳纤维转子平衡误差
03
2025-06
轴动平衡机厂家推荐品牌榜单
轴动平衡机厂家推荐品牌榜单 在工业生产的广袤天地里,轴动平衡机扮演着举足轻重的角色。它能精准校正旋转部件的平衡,提高设备运行的稳定性与可靠性,减少振动和噪音,延长设备使用寿命。市场上轴动平衡机厂家众多,下面为大家呈现一份推荐品牌榜单。 申克(SCHENCK) 申克堪称动平衡机领域的元老级品牌。它历史悠久,技术底蕴深厚,其轴动平衡机凭借高精度的测量系统和先进的平衡校正算法,在全球范围内得到广泛认可。产品适用于航空航天、汽车制造、电力等高端领域,能满足对平衡精度要求极高的应用场景。不过,申克产品价格相对较高,但其卓越的性能和可靠的质量,让众多企业愿意为其买单。 爱普(IMW) 爱普专注于动平衡技术的研发与创新,在轴动平衡机市场也颇具影响力。该品牌的轴动平衡机具有操作简便、维护成本低的特点。它采用了先进的传感器技术,能够快速准确地检测出轴的不平衡量,并进行高效校正。爱普产品在中小型企业中颇受欢迎,其性价比优势明显,能为企业节省成本的同时,保证生产的高效运行。 ** **是国内动平衡机行业的知名品牌。它紧跟国际先进技术潮流,不断提升自身产品的性能和质量。**的轴动平衡机种类丰富,涵盖了多种规格和型号,可满足不同行业、不同用户的需求。而且,**注重售后服务,能够及时响应客户的需求,为客户提供全方位的技术支持。其产品在国内市场占有率较高,深受广大用户的信赖。 利之达 利之达以其独特的技术优势在轴动平衡机市场崭露头角。该品牌的轴动平衡机采用了先进的智能控制系统,能够实现自动化平衡校正,大大提高了生产效率。同时,利之达还注重产品的个性化定制,可根据客户的特殊需求,为其量身打造合适的轴动平衡机。利之达凭借其创新的技术和贴心的服务,赢得了众多客户的青睐。 海诺 海诺在轴动平衡机领域也有自己的一片天地。它的产品以稳定性强、可靠性高著称。海诺轴动平衡机采用了优质的零部件和精湛的制造工艺,确保了产品在长时间运行过程中能够保持良好的性能。此外,海诺还不断加大研发投入,积极引进国外先进技术,致力于提升产品的竞争力。其产品在一些对设备稳定性要求较高的行业中得到了广泛应用。 选择轴动平衡机时,企业要根据自身的生产需求、预算以及对产品性能的要求等多方面因素综合考虑。希望这份推荐品牌榜单能为大家在选购轴动平衡机时提供一些有价值的参考。
03
2025-06
轴动平衡机厂家支持定制服务吗
轴动平衡机厂家支持定制服务吗?——解码工业精密设备的柔性制造密码 一、定制化需求:从”标准件”到”专属解决方案”的范式革命 在精密机械制造领域,轴动平衡机正经历着从”流水线产品”向”场景化解决方案”的蜕变。当某新能源汽车厂商提出”±0.1g平衡精度+72小时不间断运行”的苛刻要求时,传统设备供应商的标准化产品已显乏力。这种背景下,头部厂家开始构建”需求-设计-验证”的全链路定制体系,通过模块化设计平台将设备参数分解为200+可调变量,使转速范围、载荷容量、传感器配置等核心指标实现”乐高式”组合。 二、技术实现:柔性制造的三大支点 智能算法重构 采用数字孪生技术搭建虚拟调试环境,某军工企业定制的12000rpm高速平衡机,通过2000次虚拟迭代将物理样机试错成本降低73%。这种”算法先行”模式使定制周期从传统6个月压缩至8周。 材料工程突破 针对半导体晶圆传输轴的超低振动需求,厂家开发出碳纤维增强钛合金复合材料,其刚度系数较传统钢材提升40%,同时将热变形量控制在微米级。这种材料创新直接催生出”真空环境专用平衡机”等细分品类。 服务生态延伸 某风电巨头定制的12MW主轴平衡系统,配套开发了基于5G的远程监测平台。设备出厂即搭载预测性维护模块,通过振动频谱分析实现故障预警,这种”硬件+软件+服务”的交付模式正在重塑行业价值链条。 三、定制化实践:跨行业解决方案图谱 航空航天领域:为某火箭发动机涡轮泵定制的真空环境平衡机,攻克了10^-3Pa低压环境下的气浮轴承稳定性难题 医疗器械行业:为核磁共振仪主轴开发的磁兼容平衡系统,采用非导磁材料将涡流损耗降低至0.2W/m² 精密仪器制造:为光刻机工件台设计的纳米级平衡方案,通过激光干涉仪实现0.05μm级残余不平衡量控制 四、选择定制厂商的五大黄金法则 技术储备深度:查验其在ISO 1940-1国际标准框架下的非标设计案例库 服务响应速度:关注其是否具备48小时现场支持的全球服务网络 数据安全体系:确认定制参数的加密传输和区块链存证机制 持续迭代能力:评估其年度研发投入占比是否超过营收的8% 行业资质认证:核查AS9100D航空航天质量管理体系等专项认证 五、未来趋势:定制化2.0时代的三大进化方向 智能化定制:基于AI的参数自适应系统将实现”设备自主进化” 绿色定制:采用可再生能源驱动的平衡机正在成为ESG达标新标尺 全球化定制:某跨国企业通过数字主线技术实现中美欧三地协同设计,开创了”时区无界”的定制新模式 当工业4.0的浪潮席卷精密制造领域,轴动平衡机的定制化服务已超越简单的参数调整,演变为涵盖材料科学、数字孪生、服务生态的系统工程。那些能将客户需求转化为技术语言的厂家,正在重新定义这个价值千亿的细分市场。未来的竞争,将是”定制化深度”与”标准化效率”的动态平衡艺术。
03
2025-06
轴动平衡测试仪价格区间是多少
【轴动平衡测试仪价格区间是多少】——技术参数、品牌博弈与市场隐性成本的多维解构 在精密机械制造领域,轴动平衡测试仪如同工业心脏的”听诊器”,其价格波动折射出技术迭代与市场需求的复杂博弈。本文以2023年全球市场数据为基准,通过解构价格构成要素,揭示这一工业检测设备的定价逻辑。 一、技术参数构成的成本阶梯 基础型设备(3-8万元):适用于中小型电机、风扇等低速旋转体,采用接触式传感器与单点平衡算法,典型代表如国产Tianyuan TB-2000,其核心优势在于模块化设计与本地化服务响应。 中端机型(10-25万元):配备激光对刀系统与动态振动分析模块,如德国HBM MGCplus系列,通过ISO 1940平衡等级认证,特别适合汽车涡轮增压器等精密部件的实时监测。 高端配置(50-150万元):集成非接触式光纤传感器与AI预测性维护功能,美国MTS Landmark系列可实现0.1μm级位移精度,其价格构成中30%为软件授权费,20%为定制化校准服务。 二、品牌矩阵下的市场博弈 国际品牌溢价效应:瑞士Brüel & Kjær的Type 4507系列定价达180万元,其专利的三维矢量平衡算法使故障诊断效率提升40%,但年均维护成本占设备总价的8%。 国产突围路径:天远科技通过自主研发的MEMS传感器阵列,将高端机型价格下探至45万元区间,其”硬件+云平台”模式降低用户初期投入35%。 三、隐性成本的多维影响 附加服务成本:德国Schenck的设备包含5年全球联保,但换算成年均成本后,比国产设备高27%。 校准周期成本:美国PCB的传感器需每季度返厂校准,单次费用达1.2万元,而国产设备支持现场校准。 扩展功能溢价:配备5G物联网模块的设备价格上浮15%-20%,但可降低人工巡检成本40%。 四、市场动态对价格的扰动 2023年全球供应链恢复使传感器芯片成本下降12%,但AI算法授权费上涨8%形成对冲。值得关注的是,新能源汽车电机测试需求激增,推动高精度机型订单量同比提升34%。 选购策略建议: 预算敏感型:优先选择具备CNC自动补偿功能的国产设备,如思仪SI-6000系列 技术前瞻性:考虑配备数字孪生接口的机型,预留未来产线升级空间 全生命周期成本:对比5年期总持有成本,高端机型可能更具经济性 当前市场呈现明显的技术分层:基础市场被国产替代加速渗透,中高端市场仍由国际品牌主导。建议采购方建立包含精度冗余系数、维护周期、数据兼容性在内的多维评估模型,避免陷入单纯的价格比较陷阱。随着工业4.0进程深化,具备边缘计算能力的智能平衡系统或将成为下一个价格竞争焦点。
03
2025-06
轴动平衡测试仪哪个品牌性价比高
轴动平衡测试仪哪个品牌性价比高?技术革新与市场定位全解析 一、技术革新派:精密仪器的天花板 在高端市场,德国HBM以动态信号分析技术重新定义行业标准。其FlexX系列采用分布式传感器网络,可实时捕捉0.01g的振动波动,配合AI自适应算法,让平衡精度突破±0.1mm。但28万元的起售价如同技术壁垒,更适合航天军工等尖端领域。 美国LDS则另辟蹊径,模块化设计让Xact系列成为行业黑马。其磁悬浮转子系统支持±10000rpm宽幅测试,通过云端校准数据库实现跨地域设备同步。尽管单价达15万元,但年维护成本降低40%的特性,让新能源车企趋之若鹜。 二、高性价比之选:中国制造的突围战 三丰(Mitutoyo)的MB-3000系列用双频激光干涉仪打破外资垄断。其独创的温度补偿矩阵,在-10℃至60℃环境下仍保持±0.05mm精度,配合手机APP远程诊断功能,让售后响应时间缩短至2小时。9.8万元的定价策略,精准狙击汽车零部件制造企业。 思瑞(Croma)则以复合式传感器阵列打开市场缺口。其C-5000系列通过多物理场耦合算法,同步采集振动、温度、扭矩数据,特别适合工程机械领域。当同行还在争论硬件参数时,思瑞已推出五年数据云存档服务,将产品生命周期价值提升300%。 三、细分领域专家:垂直场景的精准打击 日本KEYENCE在微型电机市场掀起革命。其MV-6000系列采用微纳米级位移传感技术,专攻无人机螺旋桨平衡测试。0.05mm的安装间隙配合无线供电模块,让实验室空间占用率降低60%。尽管单价高达12万元,但年故障率仅0.3%,成为消费电子企业的隐形冠军。 德国Schenck的离线式平衡机则深耕风电领域。其MBS 2000系列通过残余不平衡量预测模型,将叶片平衡时间从72小时压缩至8小时。当同行还在追求硬件升级时,Schenck已构建全生命周期能耗管理系统,使单台风机年发电量提升15%。 四、性价比评估模型:三维度决策指南 技术冗余度:预留20%的性能余量,避免设备快速贬值 服务响应圈:选择本地化服务中心半径≤300公里的品牌 数据资产化:优先考虑支持OPC UA协议的设备,为工业4.0转型铺路 五、行业趋势洞察:智能化转型的三大方向 数字孪生:西门子已实现测试数据与CAD模型的实时映射 边缘计算:华为昇腾芯片让设备本地处理速度提升10倍 绿色节能:ABB最新机型能耗较传统产品降低70% 结语:在轴动平衡测试仪的红海市场中,真正的性价比王者不是参数竞赛的胜利者,而是能构建技术-服务-数据三维生态的品牌。建议用户建立动态评估矩阵,每季度更新供应商技术路线图,方能在智能制造浪潮中掌握主动权。
03
2025-06
轴动平衡测试仪在风机行业如何应用
轴动平衡测试仪在风机行业如何应用 在风机行业,设备的稳定运行至关重要,而轴动平衡测试仪正发挥着不可忽视的作用。接下来,我们将探讨轴动平衡测试仪在风机行业中的具体应用。 故障诊断与预防 风机在运行过程中,由于各种因素,如叶片磨损、积尘等,容易出现不平衡问题。轴动平衡测试仪能精确检测风机轴的振动情况。通过传感器收集振动数据,并进行实时分析,测试仪可以判断风机是否存在不平衡故障,以及故障的严重程度。它不仅能检测当前的故障,还能对潜在问题进行预警。例如,当检测到振动值有缓慢上升的趋势时,就意味着风机可能即将出现不平衡问题,这时可以及时安排维护,避免故障扩大,减少停机时间和维修成本。 现场动平衡校正 轴动平衡测试仪最大的优势之一就是能够在现场进行动平衡校正。传统的动平衡校正往往需要将风机的轴拆卸下来,运到专业的平衡机上进行校正,这不仅耗时费力,还会影响生产进度。而有了轴动平衡测试仪,技术人员可以直接在风机现场进行操作。测试仪会根据检测到的不平衡数据,计算出需要添加或去除的配重大小和位置。技术人员只需按照测试仪的提示,在相应位置进行配重调整,就可以快速完成动平衡校正,使风机恢复平稳运行。这种现场校正的方式大大提高了工作效率,减少了对生产的影响。 质量控制与监测 在风机的生产制造过程中,轴动平衡测试仪可以作为质量控制的重要工具。在风机装配完成后,使用轴动平衡测试仪对其进行检测,确保每一台风机的轴都处于良好的平衡状态。只有经过严格检测和校正的风机才能进入市场,这有助于提高产品的整体质量和可靠性。同时,在风机的长期运行过程中,定期使用轴动平衡测试仪进行监测,可以及时发现由于磨损、老化等原因导致的平衡变化,保证风机始终处于最佳运行状态。 数据分析与优化 轴动平衡测试仪会记录大量的振动数据和平衡校正数据。通过对这些数据的分析,可以深入了解风机的运行状况和性能特点。例如,可以分析不同工况下风机的平衡情况,找出影响平衡的主要因素,从而对风机的设计和运行参数进行优化。此外,还可以建立风机的运行档案,将每次的检测数据和校正记录进行存档,以便后续的对比和分析,为风机的维护和管理提供有力的依据。 轴动平衡测试仪在风机行业的应用涵盖了故障诊断、现场校正、质量控制和数据分析等多个方面。它为风机的稳定运行和高效生产提供了有力保障,随着技术的不断发展,轴动平衡测试仪的功能将不断完善,应用也会更加广泛。
03
2025-06
轴动平衡测试仪如何校正传动轴不平衡
轴动平衡测试仪如何校正传动轴不平衡 在机械传动系统中,传动轴的平衡状态至关重要。轴动平衡测试仪作为检测和校正传动轴不平衡的关键工具,其操作和校正过程有诸多要点。下面将详细阐述轴动平衡测试仪校正传动轴不平衡的具体方法。 前期准备:奠定校正基础 使用轴动平衡测试仪校正传动轴不平衡,前期准备工作是基础。首先,要对传动轴进行全面清洁,去除表面的油污、灰尘和杂质。这些污染物不仅会影响测试仪的精确测量,还可能掩盖传动轴本身的问题。接着,仔细检查传动轴外观,查看是否有明显的磨损、裂纹或变形。若发现这些问题,需先对传动轴进行修复或更换,因为严重的损伤会使校正工作变得徒劳,甚至影响整个传动系统的安全运行。同时,根据传动轴的类型和规格,正确安装轴动平衡测试仪的传感器。传感器的安装位置和方式直接影响测量的准确性,务必严格按照说明书进行操作。 初始测量:精准把握失衡状况 安装好传感器后,启动轴动平衡测试仪,让传动轴以一定的转速运转。测试仪会实时采集传动轴的振动数据,经过复杂的算法分析,精确计算出传动轴不平衡的位置和大小。在这个过程中,要密切关注测试仪显示的数据,确保测量环境稳定,避免外界干扰因素影响测量结果。测量完成后,测试仪会以直观的图表或数字形式呈现不平衡的具体信息,这些数据是后续校正工作的重要依据。 加重或去重:实施校正措施 基于初始测量得到的不平衡数据,就可以采取相应的校正措施,常见的方法有加重量法和去重量法。如果采用加重量法,需要根据测试仪指示的不平衡位置,在传动轴上准确添加适当重量的平衡块。平衡块的安装位置和重量必须精确,否则可能会导致新的不平衡。在安装过程中,可以使用专业的工具确保平衡块牢固固定。若选择去重量法,则要使用磨削、钻孔等方式,在传动轴不平衡的一侧去除适量的材料。操作时要小心谨慎,避免过度去除材料,导致传动轴强度受损。每进行一次加重或去重操作后,都要重新启动测试仪进行测量,检查校正效果。 多次校验:确保校正效果 一次校正往往难以完全消除传动轴的不平衡,因此需要进行多次校验和调整。每次校正后,都要重复测量过程,对比前后的数据,评估校正效果。如果仍然存在较大的不平衡,需再次分析原因,调整加重或去重的方案。反复进行这个过程,直到传动轴的不平衡量达到允许的范围内。在这个过程中,要有耐心和细心,不放过任何细微的不平衡,确保传动轴的平衡状态达到最佳。 最终检测:保障传动系统稳定 完成多次校正和校验后,要进行最终的检测。让传动轴在实际工作转速下运转,再次使用轴动平衡测试仪进行测量。如果此时测试仪显示的不平衡量在规定的误差范围内,说明校正工作成功完成。最后,对传动轴进行全面检查,确保所有部件安装牢固,传感器等设备正常工作。经过这样严格的校正过程,传动轴的不平衡问题得到有效解决,能够为整个传动系统的稳定运行提供有力保障。 轴动平衡测试仪在校正传动轴不平衡方面发挥着不可替代的作用。通过严谨的前期准备、精确的初始测量、合理的加重或去重操作、多次校验和最终检测等一系列步骤,能够有效地校正传动轴的不平衡,提高传动系统的效率和可靠性,减少设备的故障和损耗,为工业生产的顺利进行提供坚实的支持。
03
2025-06
轴动平衡测试仪常见故障及解决方法
【轴动平衡测试仪常见故障及解决方法】 在精密制造领域,轴动平衡测试仪如同机械系统的”听诊器”,其精准性直接影响设备运行寿命与生产效率。然而,复杂的工况环境与高频次操作往往引发设备异常。本文以故障树分析法为框架,结合现场运维经验,提炼出五大类高频故障及其应对策略,助工程师快速定位问题根源。 一、机械系统异常:振动”失语症”的破译 当测试仪显示”振动信号缺失”时,需警惕三重隐患: 传感器接触失效:弹性夹具老化导致压电晶体与轴系脱耦,可通过涂抹导电膏或更换钨钢探针恢复信号通路 传动链共振污染:高速旋转时齿轮箱固有频率与测试频率耦合,建议在联轴器加装阻尼环并重新校准频响曲线 轴承座刚性突变:长期疲劳导致安装基座产生0.1mm以上形变,需采用三维激光跟踪仪实施动态对中补偿 二、电气系统紊乱:数字世界的”静默崩溃” 触摸屏突然黑屏的瞬间,工程师应优先排查: 隔离电源谐波污染:使用示波器捕获20MHz以下高频干扰,加装LC滤波器可降低传导噪声30dB CAN总线阻抗失配:通过TDR时域反射仪检测线路反射系数,调整终端电阻至120Ω±5% FPGA时钟抖动:当相位噪声超过-120dBc/Hz时,需更换温补晶振并优化PCB走线拓扑 三、软件逻辑迷宫:算法层面的”认知偏差” 面对平衡质量计算偏差超标,需启动三级诊断: 傅里叶变换泄漏:采用汉宁窗函数修正频谱混叠,使幅值误差从±15%降至±3% 卡尔曼滤波发散:检查过程噪声协方差矩阵Q值,建议采用自适应遗忘因子λ∈[0.95,0.99] 最小二乘法病态矩阵:当条件数Cond(A)>10^6时,实施Tikhonov正则化约束 四、操作维度陷阱:人为因素的”蝴蝶效应” 某风电企业曾因以下失误导致批量误判: 不平衡量基准混淆:将G6.3等级错误设定为G2.5,造成补偿质量误差达47% 轴向窜动未补偿:未激活轴向振动解耦算法,使径向测量值产生±15μm偏差 温度梯度忽视:环境温差>10℃时未启用热膨胀系数修正模块 五、环境耦合危机:多物理场的”隐形绞杀” 在某核电设备平衡测试中,发现: 电磁干扰三阶互调:600kW电机产生的150V/m场强导致AD采样精度下降2个量级 气压波动引发的密度变化:海拔每升高1000m,空气浮力补偿需修正0.3% 多轴耦合振动污染:相邻设备通过地基耦合传递0.8G加速度,需搭建独立隔振平台 预防性维护矩阵 建议建立三级预警体系: 日常:每周执行激光干涉仪光路校准,偏差阈值
03
2025-06
轴动平衡测试仪操作步骤是什么
轴动平衡测试仪操作步骤是什么 一、启动前的静默交响曲 在按下启动键的瞬间之前,操作者需完成一场精密的”无声预演”。首先,用游标卡尺测量轴径公差,这不仅是对物理尺寸的确认,更是对设备健康状态的初次叩诊。随后,将测试仪主机与传感器通过航空插头连接——金属触点接触不良可能导致数据断层,如同血管栓塞般致命。最后,将振动传感器吸附于轴端法兰,确保其轴线垂直度误差小于0.1°,这个动作需要像外科医生持手术刀般稳定。 二、数据采集的量子跃迁 当测试仪进入自检模式时,液晶屏上跳动的数字犹如粒子对撞机中的微观世界。启动转子驱动电机的瞬间,操作者需保持”动态观察三原则”: 监控电流表指针波动,电流突变可能预示轴承异常 倾听转子运转音调,高频啸叫往往暗示动不平衡 观察示波器波形,正弦曲线畸变程度反映质量偏心率 此时,测试仪内部的加速度传感器正以20kHz采样率捕捉振动信号,相当于每秒拍摄2万张机械运动的”高速摄影”。 三、虚拟配重的拓扑重构 数据采集完成后,操作者需在软件界面进行”数字炼金术”: 调整频谱分析窗函数,汉宁窗与布莱克曼窗的选择如同在精确度与分辨率间走钢丝 通过相位锁定功能捕捉质量偏心角,这个角度误差每增大1°,剩余不平衡量将呈指数级增长 在虚拟配重模块中,输入轴长、转速、材料密度等参数,系统将自动生成三维质量分布云图 此时,测试仪犹如机械世界的CT扫描仪,将肉眼不可见的质量偏心转化为可操作的配重方案。 四、物理修正的时空折叠 根据软件建议,在轴指定位置钻削平衡孔时,需遵循”三轴定位法则”: 用百分表校准钻孔角度,误差控制在±0.5° 采用阶梯钻扩孔工艺,避免金属疲劳 用超声波测厚仪检测剩余壁厚,确保结构强度 当配重块安装到位时,操作者会进行”共振点校验”:将转速提升至临界转速的80%,观察振动幅值是否呈现预期衰减曲线。 五、闭环验证的混沌控制 最终验证阶段,系统将执行”动态平衡迭代算法”: 采用PID控制模式自动调节配重参数 通过卡尔曼滤波消除环境振动干扰 运用小波变换提取特征频率成分 当不平衡量降至ISO 1940标准的G0.5级时,测试仪会发出蜂鸣提示,此时转子振动烈度相当于飓风中羽毛的颤动幅度。 这场精密的机械芭蕾,每个环节都是牛顿定律与傅里叶变换的共舞。从物理测量到数字建模,从虚拟配重到实体修正,轴动平衡测试仪的操作本质是将离散的质量分布转化为连续的能量平衡。当最终平衡精度达到微米级时,操作者收获的不仅是合格的测试报告,更是对机械运动本质的全新认知。
03
2025-06
轴动平衡测试仪校正后振动未降低怎么办
轴动平衡测试仪校正后振动未降低怎么办? 引言:当平衡校正失效时的思维跃迁 在旋转机械领域,轴动平衡测试仪如同外科手术刀般精准,却在某些时刻遭遇”术后并发症”——校正后振动未降反升。这种反常现象往往暗示着多重因素交织的复杂故障链,需要工程师以侦探般的敏锐度穿透表象,重构故障逻辑。 一、动平衡仪本身的”自检悖论” 1.1 传感器系统的认知盲区 谐波干扰陷阱:当转速接近临界转速时,加速度传感器可能将高频谐波误判为基频振动,导致残余不平衡量计算偏差超15%。此时需启用频谱分析模式,锁定真实故障频率。 动态响应滞后:某些经济型仪器的采样率不足5kHz时,对瞬态振动的捕捉存在0.3ms的延迟,建议采用FFT变换结合时域分析的复合诊断法。 1.2 软件算法的逻辑迷宫 静/动平衡模式误用:若刚性转子被错误设定为挠性模式,算法会引入虚设的相位补偿参数。需通过临界转速测试判断转子刚度,必要时采用有限元仿真验证模型。 残余量阈值陷阱:部分设备默认的0.1g残余量标准可能与ISO 1940-1规范冲突,建议根据ISO 21940-7标准建立分级响应机制。 二、转子系统的”结构欺骗” 2.1 材料疲劳的隐秘侵蚀 微观裂纹的共振效应:使用相位对比法检测时,若发现振动相位在特定负载下突变±15°,需配合超声波探伤仪排查叶轮榫头部位的疲劳裂纹。 热膨胀系数的时空错位:对于高温转子,需建立温度-振动相位的动态映射模型,补偿因材料热变形导致的平衡质量偏移。 2.2 装配应力的时空涟漪 预紧力的蝴蝶效应:轴承座预紧力每增加10%,可能引发0.05mm的轴向位移,建议采用激光对中仪进行多点位移监测。 键槽配合的相位欺骗:键槽间隙超过0.1mm时,会形成周期性冲击载荷,需结合频谱分析识别冲击频率特征。 三、安装误差的”空间折叠” 3.1 轴系对中的四维迷宫 角度偏差的累积效应:0.05mm/m的偏角误差在1000rpm时会产生0.2g的振动幅值,需采用激光对中仪进行三维矢量补偿。 支撑刚度的非线性陷阱:当轴承座刚度差异超过20%,会导致动态不平衡量虚增,建议通过有限元分析优化支承结构。 3.2 质量分布的时空错位 润滑油膜的动态欺骗:滑动轴承的油膜刚度变化会导致0.3mm的有效质量偏移,需在热态运行状态下进行二次平衡。 密封环的相位干扰:机械密封的端面不平度超过0.02mm时,会产生0.15g的轴向振动,建议采用激光测振仪进行局部模态分析。 四、环境干扰的”能量耦合” 4.1 基础刚度的频率欺骗 共振峰的时空转移:当基础固有频率与转子频率接近时,振动能量会形成驻波效应,建议采用阻抗头进行动态刚度测试。 温度梯度的相位扭曲:环境温度每变化10℃,可能导致0.05mm的热变形偏移,需建立温度-振动的动态补偿模型。 4.2 流体载荷的时空纠缠 喘振工况的相位反转:在压气机喘振边界附近,振动相位可能突变180°,需配合压力传感器进行多物理场耦合分析。 介质密度的频率调制:液体泵的介质密度变化会导致不平衡量虚增30%,建议采用密度补偿算法修正平衡参数。 五、操作失误的”认知盲区” 5.1 平衡基准的时空错位 基准标记的相对论效应:当转子存在轴向窜动时,平衡基准点会产生0.1°的相位误差,建议采用光电编码器进行动态基准跟踪。 质量块的时空衰减:粘接式平衡块的粘结强度不足会导致质量衰减,需通过扭矩扳手进行逐点校核。 5.2 数据采集的维度坍缩 采样率的时空压缩:当采样率低于转频的5倍时,会导致0.2g的幅值测量误差,建议采用过采样技术提升分辨率。 环境噪声的频域污染:电网谐波干扰可能导致0.15g的虚假振动,需采用陷波滤波器进行频段隔离。 结语:构建故障诊断的元认知框架 面对动平衡校正失效的复杂场景,工程师需建立”四维诊断矩阵”:在时间维度追踪振动演化规律,在空间维度解析多物理场耦合,在频域维度解构振动成分,在认知维度突破经验局限。唯有将动平衡技术与现代监测诊断技术深度融合,方能在旋转机械的混沌系统中找到精确的平衡解。