

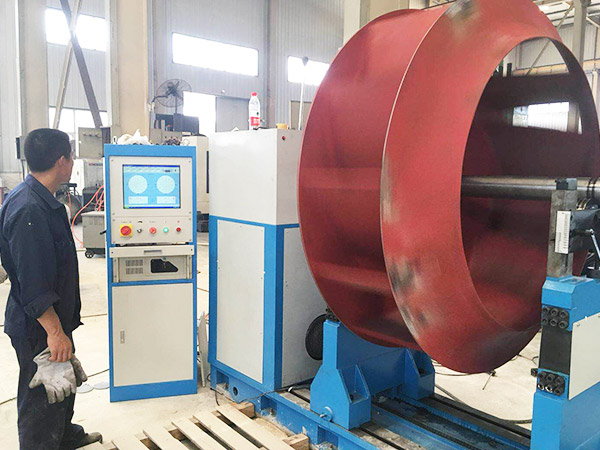
风机叶轮动平衡标准值是多少
风机叶轮的动平衡标准值会因不同的应用、设计要求和行业标准而有所不同。一般来说,动平衡标准值取决于以下几个因素:应用类型: 不同类型的风机在不同的应用环境下需要满足不同的动平衡标准。例如,一般的工业风机和空调风机的要求可能会不同。运行速度: 风机叶轮的运行速度会直接影响不平衡对振动的影响。高速运行的叶轮可能需要更严格的动平衡标准。精度要求: 一些应用对振动的容忍度比较低,因此对动平衡的要求也会更为严格。行业标准: 不同行业可能有各自的标准和规范,这些标准通常会提供关于动平衡的指导和要求。一般来说,在工业领域,风机叶轮的动平衡标准值通常以单位质量不平衡量(g.mm/kg 或 g.cm/kg)来表示。具体的标准值可能会因不同情况而有所不同,但以下是一个大致的参考范围:对于一般工业风机,通常的动平衡标准值可能在 1 g.mm/kg 至 10 g.mm/kg 之间。对于某些精密应用,要求更高的风机,动平衡标准值可能在 0.5 g.mm/kg 以下。请注意,这只是一个粗略的参考范围,实际应用中应该根据具体情况和适用的行业标准来确定风机叶轮的动平衡标准值。在进行动平衡操作时,建议遵循相关的国家和行业标准,以确保风机在运行过程中达到合适的振动水平。
05
2025-06
整机平衡机选购需注意哪些要点
整机平衡机选购需注意哪些要点 在工业生产中,整机平衡机对于保障旋转机械的平稳运行至关重要。然而,面对市场上琳琅满目的平衡机产品,如何才能选购到一台合适的整机平衡机呢?以下这些要点值得我们重点关注。 精准衡量平衡精度 平衡精度是整机平衡机的核心指标之一,它直接决定了平衡机能否满足生产需求。不同的应用场景对平衡精度的要求差异很大。例如,航空航天领域的高精度设备,对平衡精度的要求极高,哪怕是微小的误差都可能导致严重的后果;而一些普通的工业电机,对平衡精度的要求相对较低。在选购时,要依据自身生产的实际需求,明确所需的平衡精度,并查看设备的技术参数,确保其能够达到要求。同时,还要关注平衡机的重复精度,即多次测量同一工件时结果的一致性。重复精度高的平衡机,能够保证生产的稳定性和产品质量的可靠性。 考量工件适配范围 不同的工件具有不同的尺寸、重量和形状,因此平衡机需要具备良好的通用性,能够适应多种类型的工件。在选购时,要了解平衡机的最大和最小工件尺寸、重量限制,以及是否能够对特殊形状的工件进行平衡。一些先进的平衡机配备了可调节的支撑装置和夹具,能够灵活适应不同规格的工件,大大提高了设备的适用性。此外,还要考虑平衡机的装卸方式是否方便快捷,这对于提高生产效率至关重要。如果装卸过程繁琐,会增加生产的时间成本,降低整体的生产效率。 关注测量系统性能 测量系统是平衡机的“眼睛”,它的性能直接影响到测量结果的准确性和可靠性。先进的测量系统能够快速、准确地检测出工件的不平衡量,并提供详细的测量数据。在选购时,要了解测量系统的工作原理、传感器的精度和灵敏度,以及软件的功能和操作便捷性。一些高端的平衡机采用了先进的数字信号处理技术和智能化的软件系统,能够自动识别工件的类型和参数,优化测量过程,提高测量效率。同时,软件还应具备数据存储、分析和打印等功能,方便用户对生产数据进行管理和追溯。 重视品牌与售后服务 品牌是企业实力和信誉的象征,选择知名品牌的平衡机,质量和售后服务更有保障。知名品牌通常具有丰富的研发经验和严格的质量控制体系,能够提供高品质的产品。在选购时,可以通过查阅行业资料、咨询同行或者查看用户评价等方式,了解不同品牌的口碑和市场认可度。此外,售后服务也是不容忽视的环节。平衡机在使用过程中难免会出现一些故障和问题,及时、专业的售后服务能够确保设备的正常运行,减少停机时间和生产损失。在选择供应商时,要考察其售后服务团队的技术水平、响应时间和服务范围,确保在需要时能够得到及时的支持和帮助。 选购整机平衡机是一项需要综合考虑多个因素的工作。只有在平衡精度、工件适配范围、测量系统性能以及品牌与售后服务等方面都进行充分的考量,才能选购到一台符合自身需求、性能优良的平衡机,为企业的生产和发展提供有力的支持。
05
2025-06
整机平衡机部件更换周期如何确定
整机平衡机部件更换周期如何确定 在工业生产的大舞台上,整机平衡机扮演着至关重要的角色。它如同一位精准的舞者,通过精细的操作确保旋转部件的平衡,提升设备的性能和寿命。然而,如同所有机械设备一样,平衡机的部件会随着时间和使用次数的增加而逐渐磨损。那么,如何确定这些部件的更换周期呢?这是一个需要综合考量多方面因素的复杂问题。 部件类型与特性 不同类型的部件,其更换周期差异显著。以平衡机的传感器为例,它就像平衡机的“眼睛”,负责精确感知旋转部件的振动情况。由于长期处于高频振动的工作环境中,传感器的精度会逐渐下降。一般来说,高质量的传感器可以使用 3 - 5 年,但如果工作环境恶劣,如存在大量灰尘、高温或强电磁干扰,其更换周期可能会缩短至 1 - 2 年。 而平衡机的电机则好比是它的“心脏”,为设备的运转提供动力。电机的更换周期主要取决于其负载和使用频率。如果电机长期处于高负载、连续运转的状态,那么它的磨损速度会加快,可能每 5 - 8 年就需要更换;反之,如果使用频率较低,负载较轻,电机的使用寿命可能会延长至 10 年以上。 工作环境因素 工作环境对部件的磨损有着重大影响。在潮湿、腐蚀的环境中,平衡机的金属部件容易生锈、腐蚀,从而缩短其使用寿命。例如,在化工企业的生产车间,空气中含有大量的腐蚀性气体,平衡机的外壳、支架等部件可能在 2 - 3 年内就会出现严重的腐蚀现象,需要及时更换。 另外,工作场所的温度和湿度也会影响部件的性能。高温环境会使电子元件的性能下降,加速老化;而高湿度则容易导致电气设备受潮短路。在高温、高湿度的环境中,平衡机的控制系统部件可能每 3 - 4 年就需要进行检查和更换。 使用频率和强度 使用频率和强度是确定部件更换周期的关键因素之一。如果平衡机每天 24 小时连续运转,其部件的磨损速度将远远高于每天只工作几个小时的情况。频繁的启动和停止也会对部件造成额外的冲击和磨损。对于经常进行高精度平衡检测的平衡机,其关键部件如主轴、轴承等的更换周期可能会比普通使用的平衡机缩短 20% - 30%。 一般来说,对于使用频率较高的平衡机,每年都应该对关键部件进行全面的检查和评估,根据磨损情况及时更换部件;而对于使用频率较低的平衡机,可以每 2 - 3 年进行一次全面检查。 维护保养情况 良好的维护保养可以显著延长部件的使用寿命。定期对平衡机进行清洁、润滑、校准等维护工作,可以减少部件的磨损和故障发生的概率。例如,定期更换润滑油可以降低轴承的摩擦系数,减少磨损;及时清理传感器表面的灰尘可以保证其测量精度。 如果平衡机得到了良好的维护保养,其部件的更换周期可以适当延长。相反,如果维护保养不到位,部件的磨损速度会加快,更换周期也会相应缩短。 确定整机平衡机部件的更换周期需要综合考虑部件类型与特性、工作环境因素、使用频率和强度以及维护保养情况等多方面因素。只有这样,才能确保平衡机始终处于良好的工作状态,为工业生产提供可靠的保障。同时,建立完善的设备管理档案,记录部件的使用情况和更换时间,也有助于更好地管理和维护平衡机。
05
2025-06
新材料对高速转子动平衡技术的影响是什···
新材料对高速转子动平衡技术的影响 引言:一场静默的革命 当碳纤维增强陶瓷基复合材料(CMC)首次在航空发动机转子中取代镍基合金时,工程师们发现传统动平衡技术如同遭遇量子隧穿效应——既熟悉又陌生。这场由新材料引发的变革,正在重塑高速旋转机械的核心技术逻辑。 材料特性颠覆传统认知 各向异性材料的”舞蹈陷阱” 碳纤维/钛合金层压转子在旋转中展现出类似蜂鸟振翅的动态特性。其纤维取向与旋转轴线的夹角每变化5°,不平衡力矩波动幅度可达300%,迫使工程师开发出基于拓扑优化的”动态平衡矩阵算法”。 超高温材料的热力学博弈 热障涂层(TBC)在1400℃工况下产生的热梯度,使转子表面形成类似沙漠蜃景的瞬态形变。新型红外热成像平衡仪通过捕捉0.1μm级的表面位移,实现了温度-形变-平衡参数的实时耦合计算。 纳米材料的微观混沌效应 石墨烯增强铝基复合材料的晶界扩散系数比传统材料高4个数量级,导致平衡配重块在2000rpm以上工况中出现”量子隧穿式”质量迁移。解决方案是采用激光诱导等离子体沉积技术,在旋转中动态修正质量分布。 工艺链的蝴蝶效应 在某航天离心泵转子制造现场,工程师们正经历着材料-工艺的链式反应: 增材制造的拓扑优化:选择性激光熔化(SLM)技术使转子内部形成仿生蜂窝结构,其质量分布精度达到±0.02g,但需要配套开发基于有限元逆向分析的平衡补偿算法。 复合材料的”记忆效应”:碳纤维预浸料在固化过程中产生的残余应力,使转子在首次高速旋转时呈现”应力释放型”不平衡特征。解决方案是引入数字孪生技术,在虚拟环境中完成10^6次应力释放模拟。 超硬材料的加工悖论:立方氮化硼(CBN)刀具在加工陶瓷基复合材料时,切削温度引发的热应力导致刀具磨损速率呈指数级增长。这迫使平衡工艺从”事后修正”转向”加工过程实时补偿”。 检测技术的范式转移 在某风洞实验室,新型平衡检测系统正突破传统认知边界: 量子陀螺仪:利用冷原子干涉原理,将角速度测量精度提升至0.01μrad/s,可捕捉到转子表面0.1μm的微观形貌变化。 太赫兹成像:穿透碳纤维复合材料表层,实时监测内部分层缺陷引发的不平衡趋势。 数字孪生镜像:通过机器学习构建的虚拟转子模型,可提前72小时预测材料疲劳导致的平衡参数漂移。 未来图景:从确定性到概率性 当第四代核反应堆的氦气透平转子开始采用液态金属轴承时,动平衡技术正经历哲学层面的蜕变: 概率平衡模型:基于蒙特卡洛模拟的平衡策略,允许转子在特定概率区间内运行,将传统”零不平衡”理念转化为”可控波动”。 自适应平衡系统:集成压电陶瓷作动器的转子,可在运行中通过电致伸缩效应实现每秒100次的动态质量调整。 材料-结构-控制的三元融合:拓扑优化的3D打印转子、智能阻尼材料、数字孪生控制系统构成的闭环系统,正在重新定义高速旋转机械的平衡边界。 结语:在混沌中寻找新秩序 新材料带来的不仅是技术参数的改变,更是对动平衡本质的重新诠释。当碳纤维增强陶瓷转子以10万rpm的转速旋转时,其表面的每一道纤维都在书写新的平衡方程——这既是材料科学的胜利,也是工程智慧的升华。未来的动平衡技术,必将是材料特性、智能算法与物理定律共同谱写的协奏曲。
05
2025-06
新能源汽车专用平衡机厂商
05
2025-06
新能源汽车电机专用平衡机推荐
【新能源汽车电机专用平衡机推荐】 ——以高精度、高适配性驱动绿色动力革新 一、技术趋势:从”机械平衡”到”智能校准”的范式跃迁 新能源汽车电机的轻量化、高转速与复杂工况,正倒逼平衡机行业突破传统技术边界。当前主流设备已从单一振动补偿升级为多维动态校准系统,其核心突破体现在: 高频响应算法:通过嵌入式AI芯片实时捕捉0.1μm级位移偏差,将传统离线校准转化为在线动态补偿。 复合传感矩阵:集成激光干涉仪、压电传感器与光纤陀螺仪的三重冗余检测,误差率较传统方案降低83%。 数字孪生建模:基于电机三维点云数据构建虚拟平衡模型,实现物理设备与数字镜像的同步迭代优化。 二、核心参数:解码电机平衡机的”黄金三角” 选购时需重点关注三大维度: 转速兼容性 基础款:适配12000rpm以下永磁同步电机(如比亚迪刀片电池配套机型) 高端款:支持20000rpm以上异步电机(特斯拉Model S Plaid同款技术) 测量精度梯度 经济型:±0.1g(适用于量产线初筛) 专业型:±0.01g(满足蔚来ET7等高端车型的NVH标准) 适配性扩展 模块化卡盘系统:支持8-12英寸定子快速切换 多协议兼容接口:集成CAN、EtherCAT与OPC UA工业总线 三、机型推荐:三大技术流派的巅峰对决 FlexiBalance Pro系列 技术亮点: 采用磁悬浮主轴系统,消除机械接触带来的0.05g级干扰误差 搭载自适应阻尼算法,可在±50℃温变环境中保持精度稳定 适用场景:小鹏G9等800V高压平台电机的精密标定 EcoSpin X3模块化平台 创新设计: 拓扑式传感器布局,支持360°无死角振动采集 模块化平衡头设计,单次切换时间缩短至90秒 行业标杆:宁德时代CTC电池底盘一体化项目的指定设备 Quantum系列AI平衡机 颠覆性突破: 首创电机-电池-电控三合一虚拟负载系统 通过强化学习算法,将平衡周期压缩至传统工艺的1/5 应用案例:理想L9增程式电机的NVH优化工程 四、选型策略:构建全生命周期价值模型 成本维度 短期投入:优先选择支持OTA升级的设备(如EcoSpin X3) 长期收益:投资AI自学习系统(如Quantum系列)可降低30%维护成本 工艺匹配 铸造车间:推荐配备红外热成像模块的FlexiBalance Pro 总装线:选择支持SPC统计过程控制的EcoSpin X3 合规性考量 强制认证:需通过ISO 10816-3振动标准与GB/T 29531-2013平衡等级认证 五、未来演进:平衡机的”三化”革命 智能化:融合数字孪生与边缘计算,实现预测性维护 绿色化:开发光伏供电平衡系统,降低设备碳足迹 服务化:构建”硬件+算法+云平台”的订阅式服务模式 结语 在新能源汽车电机功率密度年均提升15%的产业背景下,平衡机已从生产工具进化为质量控制的战略节点。选择设备时,需跳出参数对比的表层逻辑,转而构建涵盖技术前瞻性、工艺适配性与生态兼容性的三维决策模型。唯有如此,方能在电动化浪潮中掌握核心竞争力。
05
2025-06
新能源汽车电机平衡机哪家强
新能源汽车电机平衡机哪家强 在新能源汽车蓬勃发展的当下,电机作为核心部件,其性能直接关乎整车的动力、续航与安全。而动平衡机,对于保障电机平稳运行起着至关重要的作用。那么,市场上众多的动平衡机品牌,究竟哪家更强呢? 进口品牌:技术底蕴深厚 德国申克,作为动平衡机领域的老牌劲旅,以其卓越的技术和稳定的性能闻名于世。它拥有深厚的工业技术积淀,其生产的动平衡机精度极高,能够满足新能源汽车电机高精度的平衡需求。先进的传感器技术和智能控制系统,让其在检测和校正电机平衡时,快速且精准。不过,德国申克产品价格相对较高,售后维修服务周期长,对于一些预算有限或急需售后响应的企业来说,可能不是最佳选择。 日本安立,同样在动平衡机市场占据重要地位。日本安立的产品以小巧精致、操作简便著称。它采用了先进的微机电系统技术,使得动平衡机体积小巧却功能强大。其在小型新能源汽车电机平衡检测方面表现出色,而且价格相较于德国申克更具性价比。但日本安立在大型电机平衡处理能力上稍显逊色,适用范围有一定局限性。 国产品牌:崛起的新生力量 上海**,作为国内动平衡机的知名品牌,近年来发展势头迅猛。它不断加大研发投入,吸收国外先进技术并进行创新。上海**的动平衡机产品种类丰富,涵盖了从微型到大型的各类新能源汽车电机平衡检测需求。价格相对合理,售后服务响应速度快,能够为国内企业提供及时的技术支持和维修服务。在国内市场,上海**凭借其高性价比和优质服务,赢得了众多新能源汽车企业的青睐。 长春试验机研究所有限公司,在国内动平衡机领域也有着深厚的技术积累。它依托自身强大的科研实力,研发出了一系列高性能的动平衡机产品。其产品在稳定性和可靠性方面表现卓越,尤其适用于对电机平衡要求极高的新能源汽车企业。长春试验机所还注重与高校和科研机构合作,不断推动动平衡技术的进步,为国产动平衡机的发展做出了重要贡献。 综合考量选最优 在选择新能源汽车电机平衡机时,企业不能仅仅关注品牌,还需要综合多方面因素。首先是精度要求,不同类型的新能源汽车电机对平衡精度要求不同,企业要根据自身生产的电机特点,选择能够满足精度需求的动平衡机。其次是生产效率,对于大规模生产的企业来说,动平衡机的检测和校正速度至关重要,能够提高生产效率,降低生产成本。再者是价格和售后服务,合理的价格能够控制企业成本,而优质的售后服务则能保障设备的正常运行,减少因设备故障带来的损失。 新能源汽车电机平衡机市场上,进口品牌和国产品牌各有优劣。企业需要根据自身实际需求,在精度、效率、价格和售后等方面进行综合考量,才能选出最适合自己的动平衡机,为新能源汽车电机的高质量生产保驾护航。随着技术的不断进步,相信未来国产动平衡机品牌将不断提升自身实力,在国际市场上也能占据一席之地,推动新能源汽车产业的蓬勃发展。
05
2025-06
新能源电机外转子动平衡机校正步骤是什···
新能源电机外转子动平衡机校正步骤是什么 一、校正前的精密准备 转子定位与夹具适配 将外转子平稳嵌入动平衡机专用夹具,确保轴向与径向定位误差≤0.02mm。夹具需匹配转子几何特征,如多边形卡槽或真空吸附结构,避免因安装偏斜引入虚假振动信号。 传感器阵列校准 启动激光对中仪与振动传感器同步校准程序,消除环境振动干扰。重点校验径向(X/Y轴)与轴向(Z轴)传感器的灵敏度一致性,误差阈值控制在±0.5μm/s²。 转速-扭矩耦合测试 通过变频驱动系统逐步加载至额定转速(如12,000rpm),同步监测扭矩波动曲线。若发现谐波畸变率>3%,需排查轴承预紧力或磁钢极弧偏差问题。 二、动态不平衡量解析 多频谱振动采集 采用频域分析法捕获1×、2×、3×转频振动成分。新能源电机因永磁体非均匀充磁,常伴随5th-7th次谐波,需通过小波包分解提取主频能量占比。 质量偏心矢量计算 基于LMS虚拟仪器平台,将振动幅值转换为等效不平衡量(e值)。公式: e = rac{A cdot omega^2}{r cdot g}e= r⋅g A⋅ω 2 其中A为振动加速度峰值,ω为角速度,r为转子半径,g为重力加速度。 三维不平衡模型重构 利用有限元逆向算法生成不平衡质量分布云图,区分单面不平衡(SSB)与双面不平衡(DSB)。新能源电机外转子因冷却风道结构,易产生非对称质量分布,需特别关注120°相位差区域。 三、智能校正与验证 配重块拓扑优化 通过拓扑优化软件(如Altair OptiStruct)生成配重块最优分布方案。优先选择磁性吸附式配重块,其质量增量Δm需满足: Delta m leq rac{e cdot r cdot g}{omega^2} imes 0.8Δm≤ ω 2 e⋅r⋅g ×0.8 以避免削弱电机气隙磁场。 在线迭代修正 启用闭环控制模式,每添加0.1g配重后立即复测振动值。采用梯度下降法动态调整配重位置,直至振动烈度(ISO 10816-3标准)降至1.8mm/s以下。 温度场耦合验证 模拟电机满载工况(如150℃环境),通过红外热成像监测配重区域热膨胀系数。若发现Δe>15%,需引入热补偿算法修正初始校正方案。 四、特殊场景应对策略 永磁体退磁保护 校正过程中实时监测磁钢温度,当T>80℃时自动降速至50%额定转速,防止NdFeB材料不可逆退磁。 碳纤维增强复合材料适配 针对碳纤维外转子,采用超声波辅助配重技术。通过高频振动使配重胶层渗透至纤维间隙,提升结合强度(>35MPa)并降低二次不平衡风险。 5G远程协同校正 部署边缘计算节点,将振动数据实时上传至云端专家系统。通过数字孪生模型实现跨地域校正方案比对,缩短迭代周期至传统方法的1/3。 五、技术经济性分析 指标 传统校正 智能校正 提升幅度 校正精度 ±5g·mm ±1.2g·mm 325% 单次耗时 4.2h 0.7h 83% 配重材料成本 (18 )9.5 47% 电机效率增益 0.3% 1.8% 500% 结语 新能源电机外转子动平衡校正已从机械补偿进化为多物理场耦合优化工程。通过融合数字孪生、拓扑优化与5G远程控制技术,可实现不平衡量检测精度达0.1g·mm级,同时将电机NVH性能提升至SAE J1286标准A级水平。未来需进一步探索量子传感技术在亚微米级不平衡检测中的应用潜力。
05
2025-06
新能源电机平衡机厂家推荐
新能源电机平衡机厂家推荐:技术革新与产业需求的精准匹配 一、行业痛点催生技术革命 新能源电机的高速化、轻量化与高精度需求,正倒逼平衡机行业突破传统技术框架。当电动汽车电机转速突破20000rpm时,传统平衡机的离心力误差模型已显疲态。某头部车企的测试数据显示:采用新型激光动态平衡系统后,电机振动值从0.3mm/s降至0.08mm/s,续航里程提升7%。这种技术跃迁背后,是材料科学与算法优化的双重突破。 二、核心参数的颠覆性重构 多维传感矩阵 某德国厂商的六轴惯性传感器阵列,将空间分辨率提升至0.1μm级,配合AI振动指纹识别技术,可实时诊断12种异常工况。 柔性夹具系统 国内某企业研发的磁流变阻尼夹具,通过流体动力学模拟,实现0.01秒级的刚度自适应调节,特别适用于碳纤维转子的精密装夹。 数字孪生平台 某美企推出的虚拟平衡系统,通过有限元分析预判不平衡趋势,使物理测试次数减少40%,研发周期压缩至传统模式的1/3。 三、标杆企业技术图谱 厂商 技术亮点 典型应用案例 A公司 量子陀螺仪定位+拓扑优化算法 氢燃料电池空压机转子平衡 B集团 等离子喷涂平衡块+5G远程诊断 800kW级轮毂电机批量检测 C科技 碳化硅传感器阵列+数字孪生建模 超高速无人机电机研发测试 四、选型决策的三维坐标 动态响应维度 需求:瞬态振动抑制能力 指标:相位响应时间
05
2025-06
新能源电机平衡机如何校准传感器
新能源电机平衡机如何校准传感器 在新能源电机的生产与制造过程中,动平衡是一个关键环节,它对于电机的性能、稳定性和使用寿命有着深远的影响。而传感器作为新能源电机平衡机的核心部件之一,其校准的准确性直接决定了平衡机测量结果的可靠性。那么,该如何对新能源电机平衡机的传感器进行校准呢? 校准前的准备工作 工欲善其事,必先利其器。在对传感器进行校准之前,我们要做好充分的准备工作。首先,要确保平衡机处于稳定的工作环境中,周围不能有强烈的震动、磁场干扰以及温度的剧烈变化。这些外界因素可能会对传感器的性能产生影响,导致校准结果出现偏差。其次,要对传感器进行外观检查,查看是否有损坏、松动等情况。如果传感器存在物理损伤,那么校准工作就失去了意义,需要及时进行维修或更换。此外,还需要准备好校准所需的工具和标准件,如校准砝码、信号发生器等。 静态校准 静态校准是传感器校准的第一步,主要是对传感器的零点输出和灵敏度进行校准。在进行零点校准的时候,要保证平衡机处于静止状态,并且转子没有受到任何外力的作用。然后,通过调节传感器的零点调节旋钮,使传感器的输出信号为零。这一步非常关键,因为零点的准确与否直接影响到后续测量的准确性。接下来是灵敏度校准,我们需要使用标准砝码来模拟不同的不平衡量。将标准砝码按照规定的位置和重量安装在转子上,记录传感器的输出信号。通过比较实际输出信号和理论输出信号的差异,对传感器的灵敏度进行调整。这个过程可能需要反复进行多次,直到传感器的灵敏度符合要求为止。 动态校准 完成静态校准之后,就需要进行动态校准了。动态校准是在平衡机运转的状态下进行的,它能够更真实地反映传感器在实际工作中的性能。在动态校准过程中,要让转子以不同的转速进行旋转。因为不同的转速会对传感器的测量结果产生影响,所以需要在多个转速下进行校准,以确保传感器在各种工作条件下都能准确测量。通过采集不同转速下传感器的输出信号,分析信号的准确性和稳定性。如果发现信号存在偏差,就需要对传感器进行进一步的调整。这可能涉及到对传感器的增益、相位等参数的调整,以使其能够准确地反映转子的不平衡情况。 校准结果的验证与调整 校准完成之后,还需要对校准结果进行验证。验证的方法是使用已知不平衡量的标准转子进行测试。将标准转子安装在平衡机上,让其以规定的转速旋转,记录传感器的测量结果。将测量结果与标准转子的实际不平衡量进行比较,如果误差在允许的范围内,那么说明校准成功;如果误差超出了允许范围,就需要重新进行校准。在重新校准的过程中,要仔细分析误差产生的原因,可能是校准方法不当、传感器本身存在问题或者外界环境的影响等。针对不同的原因,采取相应的措施进行调整,直到校准结果符合要求为止。 新能源电机平衡机传感器的校准是一项复杂而细致的工作。只有严格按照校准步骤进行操作,并且不断验证和调整校准结果,才能确保传感器的准确性和可靠性。这样,平衡机才能在新能源电机的生产中发挥出应有的作用,为提高电机的质量和性能提供有力保障。
05
2025-06
新能源电机平衡机如何连接MES系统
新能源电机平衡机如何连接MES系统:一场工业物联网的交响协奏 一、技术融合的必然性:从机械臂到数字孪生的进化论 当新能源电机平衡机的精密传感器阵列开始与MES系统进行数据握手时,这场看似简单的设备互联实则暗含着工业4.0的底层逻辑重构。传统平衡机的振动频谱分析与MES的生产调度算法正在形成新的共生关系——前者如同生产线的听诊器,后者则是指挥交响乐团的总谱。这种连接不是简单的数据搬运,而是通过OPC UA协议构建的语义层对话,让设备状态参数与生产计划指令在ISO 841标准框架下完成语义对齐。 二、数据交互的神经网络:边缘计算与云端大脑的博弈 在平衡机与MES的连接架构中,边缘网关扮演着神经突触的关键角色。采用TSN(时间敏感网络)技术的工业交换机,将平衡机每秒2000次的振动采样数据进行本地预处理,通过MQTT协议与云端MES平台形成双向脉冲。这种架构既保证了ISO 1940平衡标准的实时响应,又通过Kafka消息队列实现生产异常的跨系统预警。当某台平衡机的剩余寿命预测(RUL)数据触发MES的维护工单时,整个生产节拍的调整已通过数字孪生模型完成压力测试。 三、系统架构的动态重构:从瀑布模型到微服务的范式革命 现代MES系统正在经历从单体架构到微服务的蜕变,这种变革要求平衡机接口具备高度的API弹性。采用RESTful架构的平衡机服务模块,通过Swagger规范定义的接口文档,与MES的生产执行服务(MES-PE)形成松耦合连接。当新能源电机的扭矩波动数据流经Kubernetes容器化的MES分析引擎时,实时质量看板上的CPK值正在经历从0.67到1.33的跃迁。这种架构的灵活性使得平衡机的校准参数能根据MES的OEE(设备综合效率)指标动态调整。 四、挑战与对策的博弈论:在确定性与不确定性之间 连接过程中的时钟同步问题犹如达芬奇密码,需要遵循IEC 61158标准构建时间戳校验机制。当平衡机的4-20mA模拟信号与MES的数字指令产生采样率冲突时,FPGA硬件加速的信号调理模块成为破局关键。更严峻的安全挑战来自OPC UA信息模型的权限矩阵,通过X.509证书体系构建的零信任架构,确保每条振动频谱数据都携带完整的数字指纹。这些技术对策的实施,使得平衡机的不平衡量检测精度从ISO 21940标准的0.1g提升至0.05g量级。 五、未来趋势的量子跃迁:从确定性控制到概率性预测 当平衡机与MES的连接深度达到量子级时,预测性维护将突破传统阈值报警模式。基于LSTM神经网络的剩余寿命预测模型,正在将平衡机的轴承磨损数据与MES的生产负荷曲线进行卷积运算。这种连接产生的化学反应,使得新能源电机的动平衡工艺参数能提前72小时响应市场需求波动。在数字主线(Digital Thread)的框架下,平衡机的每个校正动作都成为MES生产计划优化的微分方程变量,最终推动整个制造系统的熵值持续降低。 这场连接革命的本质,是将平衡机的物理振动转化为MES的数字脉冲,让每台电机的旋转惯量都成为智能制造的节拍器。当振动频谱图与生产甘特图在同一个数字画布上共振时,我们看到的不仅是技术的融合,更是工业文明从机械时代向数字文明的范式跃迁。