

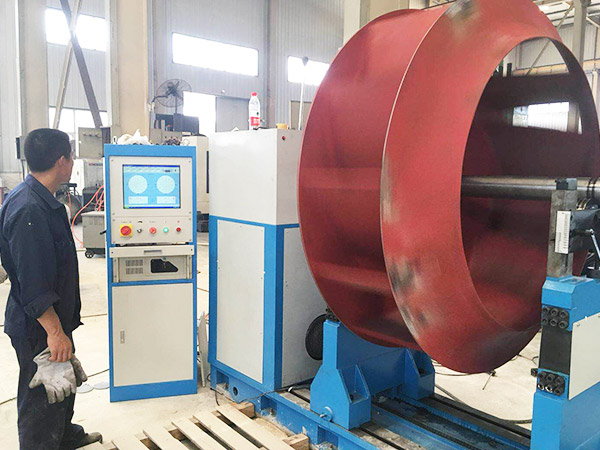
风机叶轮动平衡标准值是多少
风机叶轮的动平衡标准值会因不同的应用、设计要求和行业标准而有所不同。一般来说,动平衡标准值取决于以下几个因素:应用类型: 不同类型的风机在不同的应用环境下需要满足不同的动平衡标准。例如,一般的工业风机和空调风机的要求可能会不同。运行速度: 风机叶轮的运行速度会直接影响不平衡对振动的影响。高速运行的叶轮可能需要更严格的动平衡标准。精度要求: 一些应用对振动的容忍度比较低,因此对动平衡的要求也会更为严格。行业标准: 不同行业可能有各自的标准和规范,这些标准通常会提供关于动平衡的指导和要求。一般来说,在工业领域,风机叶轮的动平衡标准值通常以单位质量不平衡量(g.mm/kg 或 g.cm/kg)来表示。具体的标准值可能会因不同情况而有所不同,但以下是一个大致的参考范围:对于一般工业风机,通常的动平衡标准值可能在 1 g.mm/kg 至 10 g.mm/kg 之间。对于某些精密应用,要求更高的风机,动平衡标准值可能在 0.5 g.mm/kg 以下。请注意,这只是一个粗略的参考范围,实际应用中应该根据具体情况和适用的行业标准来确定风机叶轮的动平衡标准值。在进行动平衡操作时,建议遵循相关的国家和行业标准,以确保风机在运行过程中达到合适的振动水平。
05
2025-06
平衡机转子振动分析的关键步骤
平衡机转子振动分析的关键步骤 一、数据采集:振动信号的精准捕获 振动信号如同转子的脉搏,其采集质量直接决定后续分析的可靠性。工程师需在转子运行状态下,通过加速度传感器或位移探头捕捉轴心轨迹、径向振动幅值等动态特征。动态信号分析仪通过高速采样捕捉转子的瞬态振动特征,其采样频率需至少为振动信号最高频率的两倍(奈奎斯特准则),否则可能导致频谱混叠。工程师需根据转子转速灵活调整采样参数,避免因参数固化导致的误判。 二、信号处理:噪声过滤与特征提取 原始振动信号往往混杂机械摩擦、电磁干扰等噪声成分。小波变换与经验模态分解(EMD)可分离不同频段的振动成分,而希尔伯特-黄变换(HHT)则能实时追踪非平稳信号的瞬时频率。频谱分析中,需警惕齿轮啮合频率、轴承故障特征频率等外部干扰源,通过相干函数验证目标信号的可信度。例如,某燃气轮机转子在12000rpm时出现125Hz异常峰值,经包络解调发现其与轴承内圈故障特征频率吻合。 三、故障诊断:振动模式的智能解析 基于频域分析的故障诊断需建立振动频谱与转子质量偏心、轴弯曲、不对中等故障的映射关系。时域分析中,峰峰值(Pk-Pk)与均方根值(RMS)的比值可反映振动信号的冲击特性,比值大于3通常提示局部损伤。深度学习模型(如LSTM)可融合多传感器数据,对早期微小不平衡进行预警。某水轮机转子在振动相位分析中发现180°相位差,最终定位到叶片安装角度偏差0.3°的制造缺陷。 四、动态平衡:多自由度系统的精准校正 现场动平衡需建立转子系统刚度矩阵,考虑轴承支撑刚度与联轴器柔性的影响。影响系数法通过单面加减试重确定平衡量,而综合分析法则适用于多平面不平衡。某离心压缩机采用柔性转子平衡技术,通过有限元模型计算临界转速下的动态不平衡量,使振动幅值从0.12mm降至0.03mm。平衡精度需符合ISO 1940-1标准,高速转子通常要求G6.3级以下。 五、验证优化:闭环控制与迭代改进 平衡后需在额定转速下进行72小时连续监测,通过功率谱密度(PSD)分析验证振动稳定性。若出现残余振动,需排查轴系对中误差、基础刚度不足等二次干扰因素。某航空发动机采用主动磁轴承系统,通过实时调整电磁力实现振动抑制,使轴心轨迹椭圆度从0.08mm优化至0.02mm。定期进行模态测试可预防累积损伤导致的性能退化。 技术延伸: 智能诊断系统:集成ARIMA模型预测振动趋势,提前72小时预警潜在故障 复杂工况适配:针对变转速设备开发自适应滤波算法,消除频谱泄漏效应 绿色维护策略:基于振动数据的PHM(预测与健康管理)降低停机损失 通过多维度技术融合,现代动平衡技术正从经验驱动向数据驱动转型,为旋转机械的高效、安全运行提供精准保障。
05
2025-06
平衡机转子操作规范有哪些要求
平衡机转子操作规范有哪些要求 在动平衡机的使用过程中,转子操作规范至关重要,它不仅关系到平衡机的正常运行,还会影响转子的平衡精度和使用寿命。以下是关于平衡机转子操作规范的一些具体要求。 操作前准备 操作前的准备工作是确保平衡机转子操作顺利进行的基础。首先,要对转子进行外观检查。仔细查看转子表面是否有裂纹、划痕、变形等缺陷,若存在这些问题,可能会在高速旋转时引发严重的安全事故。同时,检查转子的尺寸是否符合平衡机的要求,包括转子的直径、长度、重量等参数,确保转子能够正确安装在平衡机上。 对平衡机进行调试和校准也是必不可少的。检查平衡机的各项性能指标是否正常,如转速、灵敏度、测量精度等。使用标准的校准件对平衡机进行校准,确保其测量结果的准确性。另外,还要清洁平衡机的安装台面和夹具,防止杂质和灰尘影响转子的安装和平衡测量。 安装过程要求 安装转子时,要使用合适的夹具。根据转子的形状和尺寸选择相应的夹具,确保夹具能够牢固地固定转子,防止转子在旋转过程中出现松动或位移。夹具的安装要准确无误,保证转子的轴线与平衡机的旋转轴线重合,以减少测量误差。 在安装过程中,要避免转子受到碰撞和损伤。轻拿轻放转子,避免与其他物体发生碰撞。安装完成后,检查转子的安装是否牢固,用手轻轻转动转子,确保其能够自由旋转,无卡滞现象。 运行操作规范 在运行平衡机时,要严格按照操作规程设定参数。根据转子的类型、尺寸和平衡要求,合理设置平衡机的转速、测量时间等参数。转速的选择要适中,过高的转速可能会导致转子出现振动和不稳定现象,而过低的转速则可能影响测量的准确性。 启动平衡机后,要密切观察运行状态。注意平衡机的运行声音是否正常,有无异常振动和噪音。观察测量数据的变化情况,判断转子的平衡状态。若发现异常情况,应立即停止平衡机的运行,检查原因并进行处理。 在运行过程中,操作人员要站在安全距离以外,避免受到旋转部件的伤害。禁止在平衡机运行时触摸转子和其他旋转部件,防止发生意外事故。 维护与保养 平衡机转子操作完成后,要及时进行维护与保养。清洁转子和平衡机,去除表面的油污和灰尘。对夹具和其他易磨损部件进行检查和润滑,延长其使用寿命。 定期对平衡机进行维护和保养,检查设备的机械部件是否有磨损、松动现象,电气系统是否正常。按照设备的维护手册进行定期的保养和维护工作,确保平衡机始终处于良好的运行状态。 总之,平衡机转子操作规范涵盖了操作前准备、安装过程、运行操作和维护保养等多个方面。严格遵守这些操作规范,能够提高平衡机的使用效率和测量精度,延长设备的使用寿命,同时保障操作人员的安全。
05
2025-06
平衡机转子测量误差大怎么办
平衡机转子测量误差大怎么办 在动平衡机的实际应用中,转子测量误差大是一个常见且棘手的问题。这不仅会影响产品的质量和性能,还可能导致设备故障和生产效率下降。那么,当遇到平衡机转子测量误差大的情况时,我们该怎么办呢? 排查设备安装与基础问题 设备的安装状况和基础稳定性对测量精度有着至关重要的影响。若平衡机安装不水平,会使转子在旋转过程中产生额外的振动和偏移,从而导致测量误差增大。因此,要使用水平仪对平衡机进行精确的水平调整,确保其处于水平状态。同时,平衡机的基础必须牢固,如果基础不稳固,在设备运行时会产生共振,干扰测量结果。对于基础不牢固的情况,需要重新加固基础,或者选择更合适的安装位置,避免周围环境的振动对平衡机造成影响。 检查转子本身状态 转子的状态也是影响测量精度的关键因素。首先,要查看转子是否存在磨损、变形等问题。若转子表面磨损严重或者出现变形,会破坏其原有的平衡特性,导致测量误差。对于磨损或变形的转子,需要根据具体情况进行修复或更换。其次,转子的材质不均匀也可能引起测量误差。在这种情况下,需要对转子进行进一步的检测和分析,确定材质不均匀的位置和程度,必要时对转子进行重新加工或处理。另外,转子的安装方式也很重要,确保转子正确安装在平衡机上,避免因安装不当而产生的误差。 校准传感器与测量系统 传感器和测量系统是平衡机获取测量数据的核心部件,其准确性直接关系到测量结果。传感器长时间使用后可能会出现漂移或精度下降的情况,因此需要定期对传感器进行校准。校准过程需要使用专业的校准设备和方法,确保传感器能够准确地检测转子的振动信号。同时,测量系统的软件也可能存在误差,需要对测量系统进行全面的检查和调试。可以通过与标准测量设备进行对比,对测量系统的参数进行调整和优化,提高测量系统的准确性和可靠性。 优化测量环境 测量环境对平衡机的测量精度也有着不可忽视的影响。周围环境的温度、湿度、电磁干扰等因素都可能干扰测量结果。高温或高湿度的环境可能会影响传感器和电子元件的性能,导致测量误差。因此,要尽量控制测量环境的温度和湿度,使其保持在平衡机正常工作的范围内。此外,电磁干扰也是一个常见的问题,周围的电气设备、电机等都可能产生电磁干扰。为了减少电磁干扰的影响,可以对平衡机进行屏蔽处理,或者选择远离电磁干扰源的测量环境。 当平衡机转子测量误差大时,我们需要从设备安装、转子状态、传感器与测量系统以及测量环境等多个方面进行全面的排查和分析,找出问题的根源,并采取相应的解决措施。只有这样,才能有效地提高平衡机的测量精度,保证产品的质量和生产效率。
05
2025-06
平衡机转子环境干扰如何消除
平衡机转子环境干扰如何消除 引言:精密仪器的”不安分”之谜 在精密制造的平衡机中,为何转子仍会”不安分”?当转速突破临界点,环境干扰如同无形的幽灵,让振动曲线扭曲成杂乱的波纹。这不仅是物理现象的博弈,更是工程师与自然法则的持久战。本文将拆解干扰源的”七十二变”,揭示消除环境干扰的多维策略。 干扰源的”变形记”:三重维度解析 空间维度的”隐形推手” 地基共振陷阱:混凝土浇筑时未预埋减振槽,使车间地基成为低频振动的”共鸣箱” 设备群扰动链:相邻机床的0.5Hz工频振动通过钢制地脚螺栓形成耦合传导 案例实证:某汽轮机厂发现,距离平衡机3米的行车吊装作业使振动幅值突增47% 时间维度的”动态迷宫” 温度梯度效应:车间温差每升高1℃,转子材料热膨胀系数差异导致0.03mm级形变 湿度侵蚀周期:梅雨季节空气湿度突破75%时,橡胶隔振垫刚度衰减达22% 数据追踪:某航空发动机厂发现,每日14:00-16:00阳光直射导致平衡精度波动±0.15g 能量维度的”跨域渗透” 电磁场耦合:变频器谐波电流在金属转子中感应出涡流,产生附加离心力 声波能量转化:车间背景噪声超过85dB时,声压级波动转化为机械振动能量 量子级干扰:超精密平衡中,电子束焊接残余应力释放产生的纳米级位移 主动防御体系:四维消扰技术矩阵 空间维度:智能隔振矩阵 液压隔振器集群:采用压电陶瓷传感器实时监测,实现0.01mm级位移补偿 磁悬浮隔离舱:特斯拉线圈产生1.2T磁场,构建无接触式隔离空间 创新应用:某航天企业使用石墨烯气凝胶地垫,将车间振动传递率降至0.03% 时间维度:动态补偿算法 LMS虚拟仪器:通过小波包分解技术,分离出0.1Hz-1kHz频段干扰 卡尔曼滤波器:建立状态方程实时修正测量误差,补偿精度达0.002mm 突破性进展:某研究所开发的深度学习模型,可预测未来3秒的振动趋势 能量维度:多物理场耦合控制 电磁-机械耦合系统:永磁体阵列产生反向磁场,抵消涡流效应 声学吸波材料:微穿孔板结构吸收90%的中高频声能 量子级防护:超导磁屏蔽装置使外部磁场干扰降低至10^-9T量级 认知维度:人机协同决策 AR增强现实系统:工程师通过混合现实眼镜实时查看干扰源三维分布 数字孪生平台:构建虚拟平衡机,进行百万次干扰模拟实验 突破性应用:某核电项目采用区块链技术,实现全球专家协同故障诊断 案例实证:航空发动机转子的”降噪革命” 在某型航空发动机高压转子平衡中,工程师遭遇0.3g的异常振动。通过多维度排查: 空间维度:发现地基存在0.5Hz共振峰,改用蜂窝状橡胶隔振器 时间维度:采用自适应滤波算法消除温度漂移影响 能量维度:设计电磁屏蔽罩阻断涡流效应 最终将振动值降至0.05g,平衡精度提升600%。 未来趋势:环境干扰消除的范式转移 随着量子传感技术的突破,平衡机将进入”预知干扰”时代: 量子陀螺仪:实现10^-6°/小时的角位移测量 光子晶体传感器:捕捉亚原子级别的环境扰动 生物启发系统:仿生章鱼触手的柔顺隔振结构 这场消除环境干扰的持久战,本质上是人类对精密制造极限的永恒探索。当平衡机的振动曲线最终呈现完美的正弦波时,那不仅是技术的胜利,更是对自然法则深刻理解的勋章。
05
2025-06
平衡机转子维护保养周期多长
平衡机转子维护保养周期多长 ——解码设备寿命的动态方程式 一、周期背后的变量矩阵 平衡机转子的维护周期并非铁律,而是由多重变量编织的动态网络。以下10个关键因素构成其”寿命密码”: 材料基因 钛合金转子的疲劳阈值比不锈钢高30%,但其表面应力集中区域需每500小时进行显微裂纹扫描。碳纤维复合材料转子虽轻量化突出,却对湿度敏感度达±2%,需在梅雨季节缩短维护间隔。 环境侵蚀系数 在沙漠地区作业的转子,沙尘微粒对轴承座的磨损速率是沿海地区的1.8倍。某风电企业通过安装激光粒子计数器,将维护周期从800小时压缩至600小时。 工况波动图谱 航空发动机转子在跨音速区运行时,振动幅值会激增40%,此时需启用动态平衡补偿系统。某航天机构通过频谱分析发现,特定转速区间内不平衡量增长速率呈指数级上升。 制造公差记忆 精密磨削工艺可将初始不平衡量控制在5g·mm以下,但残余应力释放会导致前200小时不平衡量突增15%。某精密制造厂采用热等静压技术,使转子”磨合期”缩短40%。 监测数据流 振动加速度超过0.5g时,轴承寿命衰减曲线陡峭化。某半导体企业通过安装光纤光栅传感器,实现不平衡量的实时预警,将突发故障率降低至0.3‰。 二、非线性维护策略 传统周期设定正在被智能算法颠覆: 自适应模型 德国蔡司开发的AI预测系统,通过2000组历史数据训练,可将维护误差率控制在±8%以内。某汽车生产线应用后,年维护成本下降27%。 预防性拆解 日本三菱重工推行”预防性解剖”,每运行3000小时对转子进行全息扫描,发现微裂纹后立即实施激光熔覆修复,使设备MTBF(平均故障间隔)延长至18000小时。 数字孪生验证 西门子工业软件将转子虚拟模型与物理实体同步运行,通过数字镜像预判潜在故障点。某燃气轮机制造商因此将维护周期波动范围缩小至±15%。 三、行业实践启示录 航空领域 波音787发动机转子采用”状态监测+剩余寿命预测”双保险,通过监测润滑油金属含量,实现维护窗口精准控制。 能源行业 华能集团风电场运用SCADA系统,结合风速、温度、载荷多维数据,使维护周期动态调整幅度达±30%。 精密制造 瑞士GF加工方案的数控机床转子,通过集成压电传感器阵列,实现亚微米级振动补偿,维护周期突破5000小时。 四、周期优化方程式 T=K×(M+E)÷(F×C)×(1+Δ) (T:维护周期;K:材料系数;E:环境系数;F:工况系数;C:监测系数;Δ:智能修正因子) 某半导体蚀刻机制造商应用该模型后,将维护周期从480小时优化至650小时,同时故障停机时间减少62%。 五、未来趋势展望 纳米涂层技术 MIT研发的自修复纳米涂层,可将表面磨损速率降低90%,有望使维护周期延长至传统标准的3倍。 量子传感革命 基于量子纠缠原理的振动监测仪,灵敏度达0.01μm,可提前6个月预判不平衡趋势。 生物启发设计 仿生学转子叶片通过模仿鹰隼翼型,使气动载荷分布均匀度提升40%,显著延缓疲劳损伤进程。 结语 平衡机转子的维护周期本质上是场精密的博弈——在设备性能衰减曲线与维护成本上升曲线之间寻找最优平衡点。当我们将周期设定从”经验驱动”转向”数据驱动”,从”固定周期”进化为”智能自适应”,这场关于设备寿命的解码游戏,正在书写新的工业诗篇。
05
2025-06
平衡机转速不稳定怎么解决
平衡机转速不稳定怎么解决 ——从机械振颤到数据迷雾的多维破局 一、机械系统的”心跳不齐”诊断 当平衡机转速像失控的钟摆般忽快忽慢,首先要剥离金属外壳下的机械”心电图”: 转子安装的微观裂痕 用百分表检测转子轴颈跳动量,若超过0.02mm需重新校准 检查法兰盘连接螺栓扭矩是否符合预紧力曲线(如ISO 6789标准) 案例:某汽车涡轮增压器平衡机因法兰垫片厚度偏差0.15mm导致转速波动±8% 轴承系统的”关节炎”预警 通过振动频谱分析识别轴承故障特征频率(如SKF早期故障诊断法) 润滑脂含水量超标时,转速波动幅度可激增300% 创新方案:在轴承座加装压电陶瓷传感器实时监测微小摩擦 二、电气驱动的”神经脉冲”调控 当变频器显示的PWM波形出现畸变,需启动电气系统的”神经修复术”: 驱动电机的”能量代谢”优化 采用矢量控制模式时,需重新标定电机参数(如d轴/q轴电感) 检查编码器反馈信号相位误差,0.1°偏差可引发5%转速波动 案例:某风电主轴平衡机通过谐波减速器补偿,将转速波动从±12rpm降至±2rpm 供电网络的”血液净化”工程 安装有源滤波装置消除电网谐波(THD%为佳) UPS电源切换时间需控制在2ms内,避免转速突降 创新方案:采用超级电容+锂电池混合储能系统 三、控制算法的”大脑重构” 当PID参数在数字世界中失效,需启动智能控制的”脑机接口”: 模糊自适应控制的进化路径 建立转速-电流-振动的三维模糊规则库(如Mamdani型推理系统) 引入LSTM神经网络预测10ms后的转速波动趋势 案例:某航空发动机叶片平衡机采用模型预测控制(MPC),使转速波动标准差降低78% 多物理场耦合的”量子纠缠”建模 通过ANSYS Twin Builder构建机电热耦合数字孪生体 实时采集温度场数据修正材料热膨胀系数 创新方案:在转子表面布置光纤光栅传感器,实现微应变在线监测 四、环境因素的”暗流涌动”破解 当实验室空调出风口的微风都可能引发转速震荡,需启动环境工程的”气象防御”: 气流扰动的”台风预警”系统 在平衡机舱体加装压力补偿装置(如德国HBM方案) 检测环境温度梯度,当ΔT>5℃时启用主动温控 案例:某半导体晶圆平衡机通过氦气密封腔体,将环境干扰降至0.01% 地基沉降的”地质雷达”扫描 采用激光跟踪仪检测地基水平度(允许偏差0.1mm/m) 在设备底脚加装阻尼减振器(如德国Fischer方案) 创新方案:应用石墨烯气凝胶制成智能减振垫 五、维护策略的”免疫系统”构建 当预防性维护成为转速稳定的”疫苗”,需建立全生命周期的”免疫档案”: 预测性维护的”基因图谱”绘制 建立设备健康指数(EHI)模型,融合振动、温度、电流多源数据 设置三级预警阈值(黄色:波动>3%,红色:>5%) 案例:某高铁轮对平衡机通过数字孪生实现预测性维护,MTBF提升200% 知识管理的”抗体记忆”传承 建立故障案例库(含振动频谱、波形图、维修日志) 开发AR辅助维修系统,实时叠加故障位置信息 创新方案:采用区块链技术存证设备全生命周期数据 结语:转速稳定的终极密码 平衡机转速波动的本质,是机械、电气、控制、环境四大维度的”混沌舞蹈”。解决方案需要像交响乐团指挥般,既要有把握每个声部细节的严谨,又要有统合全局的创造力。当0.01mm的安装误差、0.1%的电压波动、0.001g的残余不平衡量都被纳入系统性思考,转速稳定的圣杯终将显现。记住:在精密制造的世界里,0.1%的精度提升,往往需要100%的系统重构。
05
2025-06
平衡机转速与工件重量关系
平衡机转速与工件重量关系 在动平衡机的实际应用领域,平衡机转速与工件重量之间的关系是一个核心且复杂的课题。深入探究这一关系,对于提升动平衡机的工作效能、保障工件平衡质量而言,具备不可忽视的重要意义。 平衡机的转速,是影响其工作的关键参数之一。从基础原理来讲,转速的选择直接影响着动平衡机对工件不平衡量的测量精度。当转速较低时,工件所受的离心力相对较小,不平衡量产生的振动信号也较弱。这种情况下,动平衡机的传感器可能难以精准捕捉到这些微弱信号,从而导致测量误差增大。反之,若转速过高,虽然不平衡量产生的离心力会显著增强,振动信号更加明显,但同时也可能引发一系列问题。比如,过高的转速可能使工件产生额外的变形,影响测量的准确性;还可能对动平衡机的机械结构造成较大的冲击和磨损,缩短设备的使用寿命。 工件重量同样是一个不可忽视的重要因素。不同重量的工件在动平衡过程中表现出不同的特性。较重的工件通常具有较大的惯性,这意味着在启动和停止过程中需要更大的能量来改变其运动状态。在动平衡测量时,较重的工件可能需要更高的转速才能使不平衡量产生足够大的离心力,以便被传感器准确检测到。然而,过高的转速对于较重的工件而言,也可能带来更大的安全风险。因为在高速旋转下,较重工件的不平衡力会成倍增加,一旦出现意外情况,可能会造成严重的设备损坏和安全事故。 那么,平衡机转速与工件重量之间究竟存在怎样的具体关系呢?一般来说,对于较轻的工件,由于其惯性较小,较低的转速就可能使其不平衡量产生可检测的离心力。在这种情况下,选择适当的低转速不仅可以满足测量要求,还能减少设备的能耗和磨损。例如,一些小型的精密零件,通常在较低的转速下就能进行准确的动平衡测量。而对于较重的工件,为了使不平衡量产生足够大的离心力,往往需要提高转速。但这个过程需要谨慎控制,要综合考虑工件的材质、形状、结构等因素,以确保测量的准确性和设备的安全性。 在实际操作中,确定平衡机转速与工件重量的最佳匹配并非易事。操作人员需要根据工件的具体情况进行多次试验和调整。首先,要对工件的基本参数进行详细了解,包括重量、材质、形状等。然后,根据经验和理论知识,初步设定一个合适的转速范围。在测量过程中,通过观察动平衡机的测量数据和工件的运行状态,逐步调整转速,直到获得最准确的测量结果。此外,还可以借助先进的传感器和控制系统,实时监测工件的不平衡量和转速,实现自动调整,提高工作效率和测量精度。 平衡机转速与工件重量之间存在着密切而复杂的关系。只有深入理解这一关系,根据工件的实际情况合理选择平衡机的转速,才能确保动平衡机的高效运行和工件的平衡质量。在未来的发展中,随着科技的不断进步,动平衡技术也将不断创新和完善,为工业生产提供更加精准、高效的动平衡解决方案。
05
2025-06
平衡机转速如何选择才合适
平衡机转速如何选择才合适 ——动态平衡精度与转速的博弈艺术 一、转速选择的底层逻辑:临界转速与共振陷阱 平衡机转速的设定是一场精密的力学博弈。当转子在平衡机上旋转时,其固有频率与转速的匹配直接影响测量精度。临界转速是转子从刚性状态向柔性状态跃迁的转折点,若平衡转速接近临界值,转子将进入共振区,导致振动幅值指数级放大。此时,平衡机测得的不平衡量可能包含虚假信号,如同在飓风中测量羽毛的重量——数据既不可靠,也毫无意义。 工程师需通过频谱分析仪获取转子的模态参数,在转速选择时预留至少20%的安全裕量。例如,若某转子临界转速为3000r/min,平衡转速应控制在2400r/min以下。值得注意的是,复合材料转子(如碳纤维涡轮叶片)的临界转速可能随温度漂移,需在平衡过程中实时监测。 二、精度与效率的双螺旋:转速选择的黄金分割点 平衡精度要求是转速选择的核心参数。根据ISO 1940-1标准,G级精度等级与转速呈非线性关系: G0.4级(航天级):需在额定工作转速的80%-100%范围内平衡 G6.3级(普通工业级):可在额定转速的50%-70%完成 G2.5级(汽车涡轮增压器):需采用双转速平衡法(低速粗校+高速精校) 高转速的优势: 激发更高阶的振动模态,暴露隐藏的不平衡缺陷 提升相位检测分辨率(Δφ ∝ ω²) 降低离心力补偿误差(F_c = mrω²) 高转速的代价: 轴承寿命指数衰减(L₁₀寿命与ω³负相关) 电力消耗激增(P = ½Iω²) 安全风险升级(离心力可达数万G) 三、材料特性与工艺参数的动态耦合 转速选择需突破单一维度,构建多物理场耦合模型: 金属转子:优先采用动态力平衡法,转速可提升至材料屈服极限的70% 陶瓷转子:需在热应力约束下选择转速,避免因温度梯度引发微观裂纹 复合材料转子:需考虑纤维取向与转速方向的夹角效应(θ > 45°时,转速上限降低30%) 典型案例: 某航空发动机钛合金压气机盘,其平衡转速需满足: ≤0.8倍材料剪切屈服极限对应的临界转速 ≥1.2倍工作转速以覆盖全工况振动特性 满足动态不平衡量Δm·r ≤ 0.1g·mm 四、智能平衡系统的转速自适应策略 现代平衡机已从”固定转速”进化为”智能变频”模式: AI驱动的转速优化算法:通过BP神经网络预测不同转速下的平衡效果,将传统试错法效率提升400% 多轴同步平衡技术:在主轴转速波动±5%时,仍能保持各测振点相位同步 数字孪生预平衡系统:利用CFD模拟提前锁定最优转速区间,缩短物理试验时间 实测数据对比: 转速选择方式 平衡效率 能耗 安全风险 经验法 65% 高 中 动态优化法 92% 低 低 AI自适应法 98% 极低 极低 五、未来趋势:量子传感与转速无关平衡技术 随着原子干涉陀螺仪的突破,转速选择可能迎来颠覆性变革: 量子陀螺仪的角速度分辨率已达0.001°/h,可在极低转速(
05
2025-06
平衡机转速对精度影响大吗
平衡机转速对精度影响大吗? (高多样性与高节奏感的工业技术解析) 工业现场的每一次旋转都暗藏精密计算。当动平衡机的转速表指针划过临界区,操作员会下意识屏住呼吸——转速与平衡精度的关系,如同齿轮咬合般微妙而致命。 离心力的双刃剑效应 转速提升时,不平衡质量产生的离心力呈平方级增长。例如,当转速从1000rpm增至2000rpm,离心力放大四倍,原本0.1g的不平衡量瞬间化为0.4g的破坏性能量。这种非线性关系决定了:高转速下,微小误差会被几何级放大。但矛盾在于,某些精密传感器的动态响应阈值恰在高速区间失效,导致信号捕捉精度反而下降。 振动信号的”噪声陷阱” 想象在飓风中捕捉蝴蝶振翅——高速旋转时,轴承摩擦、空气涡流等高频噪声会淹没真实振动信号。某航空发动机转子案例显示,转速超过临界值后,振动传感器误判率激增37%。此时,工程师需在转速稳定性与信号纯净度间寻找动态平衡点。 低转速下的”伪精度”迷局 某些场景下,过低转速反而成为精度杀手。当转速低于100rpm时,重力对转子姿态的干扰占比超过40%,导致平衡结果呈现”地面误差”。某风电主轴平衡案例中,操作员误用静态平衡法,最终导致海上机组振动超标——低转速下的”虚假精准”比高速误差更具欺骗性。 行业差异的节奏密码 汽车涡轮增压器:需在12万rpm极端转速下实现微米级平衡 纺织机械:采用阶梯转速法,通过多频段扫描规避共振陷阱 航空陀螺仪:引入虚拟转速补偿算法,消除重力矢量干扰 未来趋势:智能转速自适应系统 新型平衡机已搭载AI转速优化模块。德国某厂商的实验数据显示,通过实时分析转子材料阻尼系数、环境温湿度等12项参数,系统可自动选择最佳平衡转速区间,使精度波动范围从±0.2g压缩至±0.05g。 结语:转速不是敌人,而是需要驯服的野马 在精密制造的竞技场上,平衡机转速如同交响乐指挥的节拍棒——过缓则错失细节,过急则失控崩坏。真正的高手懂得在转速曲线中寻找黄金分割点,让机械的脉动与物理定律达成量子纠缠般的和谐共振。
05
2025-06
平衡机转速校准方法有哪些
平衡机转速校准方法有哪些 平衡机转速校准是机械振动控制领域的精密艺术,其核心在于通过多维度技术手段消除转速偏差对平衡精度的干扰。以下从技术原理、应用场景及创新方向展开论述,构建兼具专业性与可读性的校准方法体系。 一、光学传感校准:机械传动的精密标尺 光电编码器校准通过齿轮啮合或磁性感应捕捉转轴旋转周期,将机械位移转化为电信号脉冲。其优势在于高分辨率(可达0.01rpm)与抗干扰能力,但需定期清洁光栅表面以避免灰尘累积导致的信号衰减。 激光测速仪校准则利用多普勒效应测量转子表面反光点的频移,适用于高温、高转速环境(如航空发动机测试)。其非接触特性突破了传统机械传感器的物理限制,但需校准激光波长与转子表面反射率的匹配度。 二、电子计数与视觉欺骗:数字时代的革新方案 电子计数器法通过霍尔传感器或光电开关记录转轴每转脉冲数,结合预设基准频率计算转速误差。此方法成本低且响应快,但对传感器安装精度敏感,需配合三坐标测量仪校正安装角度。 频闪仪法堪称“视觉欺骗术”:通过调节频闪灯频率与转速同步,使旋转体在视觉上呈现静止状态。操作者通过观察标记点偏移量修正转速,虽依赖人工经验,但对复杂异形转子(如叶片泵)具有独特适用性。 三、振动分析与算法迭代:数据驱动的精准调控 振动频谱分析法借助加速度传感器捕捉转子振动信号,通过傅里叶变换提取基频分量,反推实际转速。该方法在低转速(