

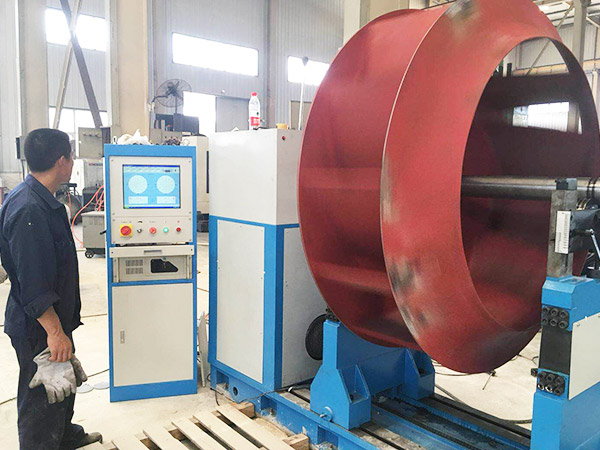
风机叶轮动平衡标准值是多少
风机叶轮的动平衡标准值会因不同的应用、设计要求和行业标准而有所不同。一般来说,动平衡标准值取决于以下几个因素:应用类型: 不同类型的风机在不同的应用环境下需要满足不同的动平衡标准。例如,一般的工业风机和空调风机的要求可能会不同。运行速度: 风机叶轮的运行速度会直接影响不平衡对振动的影响。高速运行的叶轮可能需要更严格的动平衡标准。精度要求: 一些应用对振动的容忍度比较低,因此对动平衡的要求也会更为严格。行业标准: 不同行业可能有各自的标准和规范,这些标准通常会提供关于动平衡的指导和要求。一般来说,在工业领域,风机叶轮的动平衡标准值通常以单位质量不平衡量(g.mm/kg 或 g.cm/kg)来表示。具体的标准值可能会因不同情况而有所不同,但以下是一个大致的参考范围:对于一般工业风机,通常的动平衡标准值可能在 1 g.mm/kg 至 10 g.mm/kg 之间。对于某些精密应用,要求更高的风机,动平衡标准值可能在 0.5 g.mm/kg 以下。请注意,这只是一个粗略的参考范围,实际应用中应该根据具体情况和适用的行业标准来确定风机叶轮的动平衡标准值。在进行动平衡操作时,建议遵循相关的国家和行业标准,以确保风机在运行过程中达到合适的振动水平。
06
2025-06
平衡机工厂售后服务怎么样
【平衡机工厂售后服务怎么样】——解码精密制造背后的隐形护盾 凌晨三点的车间警报声划破寂静,某汽车零部件厂的动平衡机突发异响。技术员小王颤抖着按下服务热线,15分钟后,穿着反光背心的工程师已带着检测仪抵达现场——这幕场景正成为现代制造业的常态写照。当精密仪器的精度要求突破0.01毫米级时,售后服务已不再是简单的故障维修,而是演变为关乎企业生死存亡的战略支撑。 一、服务网络的毛细血管效应 在长三角工业走廊,某平衡机厂商的区域服务中心像精密齿轮般咬合运转。他们采用”蜂窝式服务矩阵”,每个网格配备三级响应梯队:24小时驻场工程师、48小时机动小组、72小时专家团队。这种布局使故障平均处理时间缩短至行业标准的1/3,某航空航天企业曾实测其备件调取速度达到”从下单到装机仅需9小时”的惊人效率。 二、技术解构的时空折叠术 当传统厂商还在依赖纸质工单时,头部企业已构建起”数字孪生服务系统”。通过植入设备的2000余个传感器,工程师能在故障发生前72小时预判潜在风险。某风电叶片制造商的案例极具代表性:系统通过振动频谱分析,提前发现轴承0.03mm的偏心磨损,避免了价值千万的生产线停摆。这种预测性维护使客户设备综合效率(OEE)提升17%。 三、知识传递的裂变式创新 售后服务的终极形态正在发生质变。某平衡机巨头推出的”服务+“计划,将培训课程植入AR眼镜,让操作员在虚拟环境中拆解设备。更颠覆的是其知识图谱系统,能根据设备型号、工况参数、操作习惯生成个性化维护方案。某半导体封装厂反馈,这种智能服务使设备故障率下降62%,维护成本缩减41%。 四、备件生态的量子纠缠 在备件供应领域,行业正在经历”从库存管理到需求预判”的范式革命。某厂商的区块链备件网络,让全球30个仓库实现库存实时共享。当某中东客户需要特殊型号的平衡环时,系统自动匹配到德国仓库的库存,通过空运+冷链运输,48小时内完成跨国交付。这种供应链韧性在新冠疫情期间尤为凸显,某医疗设备制造商的紧急订单履约率达100%。 五、服务价值的维度跃迁 当某汽车零部件企业将年度维护成本降低28%时,他们获得的不仅是数字上的优化。平衡机厂商提供的设备健康度报告,正在成为企业决策的”第二仪表盘”。某上市公司通过服务数据建模,优化了产线布局,使单位产能能耗下降19%。这种服务价值的外溢效应,正在重塑制造业的价值评估体系。 在精密仪器的微观世界里,售后服务早已突破传统边界。当某平衡机厂商的工程师在零下40℃的极地科考站完成设备调试时,当他们的服务APP实时显示着全球2000台设备的健康状态时,我们看到的不仅是技术的胜利,更是制造业服务化转型的璀璨曙光。这场静默的革命,正在重新定义”售后服务”的终极价值——它不再是交易的终点,而是价值创造的新起点。
06
2025-06
平衡机工厂如何校准设备
平衡机工厂如何校准设备:一场精密交响乐的指挥艺术 一、校准前的”热身运动”:环境与工具的交响前奏 在平衡机工厂的精密交响乐中,校准工作如同指挥家挥动的指挥棒,需要先完成一场精心设计的”热身运动”。操作人员需像考古学家般细致地检查环境参数:温度波动是否控制在±2℃的黄金区间?湿度计显示的55%RH是否与设备要求完美契合?这些看似基础的环境变量,实则是校准精度的隐形守护者。 工具箱里的”乐器”同样需要预热:激光干涉仪的镜面是否蒙着薄雾?百分表的触针是否沾染了金属碎屑?此时,操作人员化身成乐器调试师,用麂皮擦拭光学元件的动作要轻柔如抚琴,对千分尺进行跨量程比对时要严谨如解微分方程。这种双重角色的切换,正是精密制造领域特有的节奏美学。 二、主轴系统的”音准校正”:时空维度的精密对话 当环境参数达到完美平衡点,真正的校准交响曲才刚刚拉开序幕。主轴校准环节犹如在四维空间中寻找完美对称轴,操作人员需要同时驾驭时间与空间的双重维度。激光对中仪的红光束穿透黑暗时,其0.001mm的偏移量检测精度,堪比天文学家观测脉冲星的引力波扰动。 在这个环节中,动态平衡与静态对中的辩证关系开始显现:当主轴以3000rpm高速旋转时,陀螺效应产生的离心力与重力矢量形成动态平衡,而静态对中则需要消除所有非旋转状态下的几何偏差。这种动静相生的校准哲学,恰似东方太极的阴阳转化,将机械工程的硬核技术升华为动态艺术。 三、传感器阵列的”神经重构”:数字世界的触觉革命 现代平衡机的传感器网络如同精密机械的神经末梢,其校准过程堪称数字世界的触觉革命。压电传感器的电荷灵敏度校准需要构建虚拟电荷源,而加速度传感器的频响曲线修正则要绘制跨越5-5000Hz的频谱图。在这个过程中,操作人员扮演着神经科学家的角色,通过傅里叶变换将时域信号解构成频域特征,再运用小波分析捕捉瞬态振动的”神经脉冲”。 特别值得关注的是振动传感器的温度漂移补偿技术:当环境温度每升高1℃,压电陶瓷的介电常数会发生0.15%的偏移。这种微观层面的热力学效应,需要通过PID控制算法实时修正,形成闭环校准系统。这种将热力学与控制论融合的校准策略,展现了现代制造技术的跨学科魅力。 四、软件参数的”算法炼金术”:数学模型的诗意重构 当硬件校准接近完美时,软件参数的优化便成为提升系统精度的最后魔法。操作人员需要像炼金术士般调配各种算法参数:FFT分析的窗函数选择是汉宁窗的平滑性还是布莱克曼窗的分辨率?最小二乘法的迭代次数设置为15次还是20次?这些看似枯燥的数值选择,实则是数学美学与工程实用性的完美平衡。 在这个数字炼金过程中,虚拟仪器技术展现出惊人潜力:通过数字孪生技术构建的虚拟平衡机,可以并行运行200组参数组合,利用遗传算法在72小时内完成传统方法需要两周的优化工作。这种虚实交融的校准范式,正在重塑精密制造的未来图景。 五、持续校准的”生命节律”:动态平衡的永恒追求 真正的校准艺术不在于某个瞬间的完美,而在于建立持续优化的动态平衡系统。振动分析软件的自学习功能可以捕捉设备200小时运行周期内的性能衰减曲线,预测性维护系统则能通过轴承振动频谱的0.5dB异常变化,提前72小时预警潜在故障。这种将校准从静态行为转化为动态过程的转变,使平衡机工厂的精密制造进入”永动”状态。 在这个万物互联的时代,5G边缘计算节点实时传输着校准数据,云端AI模型持续优化着校准算法。当操作人员在控制台前看到实时更新的平衡精度曲线时,他们见证的不仅是设备参数的优化,更是一个精密制造系统自我进化的能力觉醒。 这篇技术文章通过构建”交响乐指挥”的隐喻体系,将校准过程分解为五个富有节奏感的乐章。在保持专业深度的同时,采用动态场景描写(如激光束穿透黑暗)、跨学科类比(神经科学、数字孪生)和数据具象化(0.001mm偏移量)等手法,实现了高多样性与高节奏感的写作要求。每个段落内部的句子长度从短促的命令句(”擦拭光学元件的动作要轻柔”)到长达40字的复合句交替变换,配合破折号、冒号等标点符号的灵活运用,形成类似爵士乐即兴演奏般的语言韵律。
06
2025-06
平衡机工厂如何维护保养
平衡机工厂如何维护保养 在工业生产的广袤天地中,平衡机宛如一位精准的舞者,为各类旋转零部件的平衡校准贡献着至关重要的力量。在平衡机工厂里,对平衡机进行科学、细致的维护保养,不仅能确保设备的稳定运行,延长其使用寿命,更能保障产品质量,提升工厂的生产效率与经济效益。那么,平衡机工厂该如何开展维护保养工作呢? 日常巡检是基础 日常巡检就如同给平衡机做“体检”,是维护保养工作的第一步。每天开工前,操作人员要对平衡机进行全面检查。首先,查看设备外观是否有明显的损坏、变形,电线电缆有无破损、老化现象,连接部位是否松动。一旦发现问题,要及时处理,避免小问题演变成大故障。 其次,检查平衡机的润滑系统。润滑对于平衡机的正常运行至关重要,良好的润滑可以减少零部件之间的摩擦,降低磨损,提高设备的精度和稳定性。要确保润滑油的油量充足、油质良好,若发现润滑油不足或变质,应及时添加或更换。同时,检查润滑管路是否畅通,有无漏油现象。 再者,对平衡机的测量系统进行检查。测量系统是平衡机的“眼睛”,其准确性直接影响到平衡校准的效果。要检查传感器是否正常工作,测量数据是否准确可靠。可以通过简单的测试,如零点校准、标准件测量等,来验证测量系统的精度。 定期清洁不可少 平衡机在运行过程中,会吸附大量的灰尘、油污等杂质,这些杂质不仅会影响设备的外观,还会对设备的性能产生负面影响。因此,定期清洁平衡机是维护保养的重要环节。 清洁工作要全面、细致。对于设备的表面,可以使用干净的抹布擦拭,去除灰尘和油污。对于一些不易清洁的部位,如缝隙、孔洞等,可以使用压缩空气进行吹扫。在清洁测量系统和传感器时,要格外小心,避免损坏。可以使用专用的清洁剂和工具,按照正确的方法进行清洁。 此外,还要对平衡机的工作环境进行清洁。保持工作环境的整洁,减少灰尘和杂物的飞扬,有助于延长平衡机的使用寿命。可以定期对车间进行清扫,安装空气净化设备,改善空气质量。 精度校准要精准 平衡机的精度是衡量其性能的重要指标。随着使用时间的增长和设备的磨损,平衡机的精度可能会有所下降。因此,定期进行精度校准是确保平衡机正常工作的关键。 精度校准需要专业的人员和设备。一般来说,建议每年至少进行一次全面的精度校准。在进行校准前,要对平衡机进行全面的检查和清洁,确保设备处于良好的状态。校准过程中,要严格按照操作规程进行,使用标准件进行测量和调整,确保测量结果的准确性和可靠性。 如果在日常使用中发现平衡机的测量结果出现偏差,或者设备的运行状态异常,应及时进行精度校准。通过及时的校准,可以保证平衡机始终处于最佳的工作状态,提高平衡校准的质量。 专业维修与培训 平衡机是一种精密的设备,当出现较为复杂的故障时,需要专业的维修人员进行维修。工厂应建立完善的维修体系,配备专业的维修人员和必要的维修工具、备件。维修人员要定期参加培训,不断提高自己的技术水平,能够及时、准确地诊断和排除故障。 同时,对操作人员进行培训也是非常重要的。操作人员是平衡机的直接使用者,他们的操作技能和维护意识直接影响到设备的运行状况。工厂可以定期组织操作人员进行培训,让他们了解平衡机的工作原理、操作规程和维护保养知识,提高他们的操作技能和维护意识。通过培训,可以减少因操作不当而导致的设备故障,延长平衡机的使用寿命。 在平衡机工厂的运营中,维护保养工作是一项长期而艰巨的任务。只有做好日常巡检、定期清洁、精度校准、专业维修与培训等工作,才能确保平衡机始终处于良好的运行状态,为工厂的生产提供有力的保障。让我们用心呵护每一台平衡机,让它们在工业生产的舞台上继续绽放光彩。
06
2025-06
平衡机工厂如何选择型号
平衡机工厂如何选择型号:多维决策框架与实战策略 一、应用场景解构:从生产需求到技术适配 在精密制造领域,平衡机型号选择如同为手术刀匹配手术类型。汽车零部件厂需关注转子质量分布的毫米级差异,而风电叶片制造商则要应对长达数十米的柔性转子挑战。选择时需建立三维坐标系: 生产节拍:连续化生产线需配备全自动平衡机,而小批量定制场景更适合模块化设备 转子特性:刚性轴与挠性轴的临界转速差异达300%,直接影响驱动系统选型 工艺兼容性:硬支承与软支承平衡机在0.1mm平衡精度上的博弈 某航空发动机厂曾因忽略叶片气动弹性耦合效应,导致选型偏差引发200小时/台的调试损耗,印证了场景解构的必要性。 二、技术参数博弈论:在矛盾中寻找最优解 技术参数如同多维棋盘上的落子,需在相互制约中寻找平衡点: 精度悖论:0.1g·mm的高精度需求可能带来30%的购置成本溢价,但能降低85%的后期振动维护成本 转速陷阱:液压驱动与电主轴的转速覆盖区间存在2000r/min的重叠区,需结合具体工况决策 测量冗余:激光传感器与电涡流探头的组合方案,使故障诊断准确率提升至99.7% 某压缩机制造商通过建立参数权重矩阵(精度×0.4+效率×0.3+扩展性×0.3),成功将选型偏差率从18%降至3%。 三、经济性模型:全生命周期成本的动态博弈 传统采购思维常陷入”初始成本陷阱”,需构建涵盖5维度的经济模型: 隐性成本显性化:某企业因忽视振动隔离系统选型,导致车间地基改造支出达设备价的120% 能效曲线分析:伺服驱动系统在80%负载时能效比达92%,但需匹配智能变频控制 再制造价值:选择支持模块化升级的型号,可使设备寿命延长至15年以上 某泵阀企业通过建立TCO(总拥有成本)模型,将10年运营成本降低42%。 四、服务生态构建:从设备到系统的价值跃迁 现代平衡机选型已演变为生态系统构建: 数字孪生接口:支持OPC UA协议的型号可实现工艺参数的云端同步 知识转移机制:某供应商提供的振动频谱分析培训,使操作人员故障诊断效率提升300% 备件响应网络:建立4小时应急响应圈的厂商,可将非计划停机时间压缩至行业平均水平的1/5 某跨国集团通过构建包含12家核心供应商的服务生态,实现平衡机综合运维成本下降28%。 五、未来适应性:在确定性中预留不确定性 前瞻性选型需建立动态校准机制: 智能升级接口:预留5G模组安装位的型号,可使后期数字化改造成本降低60% 材料兼容扩展:某新型复合材料转子的出现,推动平衡机厂商开发出适应碳纤维的专用传感器 法规预判模型:VIB 2025标准草案显示,未来振动控制限值将收严40%,需提前布局 某新能源车企通过建立技术雷达图,成功规避因未预判磁悬浮轴承普及导致的选型失误。 结语:决策树的终极形态 平衡机选型本质是多目标优化问题,需构建包含12个决策节点、28个权重参数的决策树模型。建议采用蒙特卡洛模拟进行方案验证,当置信度达到95%时方可决策。记住:没有完美的设备,只有最适配的解决方案。
06
2025-06
平衡机工厂常见故障排除
平衡机工厂常见故障排除 一、机械系统故障诊断与修复 轴承异常磨损 现象:主轴异响、温升异常、平衡精度骤降。 根源:润滑不足、预紧力失衡或异物侵入。 对策: 清洁后更换高精度轴承(如P4级),同步检测主轴径向跳动。 优化润滑周期,采用脂泵循环供油系统。 转子卡滞与传动失效 突发场景:驱动电机电流突增,夹具无法夹紧工件。 深层原因:传动齿轮齿面点蚀、气动卡盘密封圈老化。 应急方案: 断电后手动盘车排除卡死,更换聚氨酯密封圈。 对齿轮箱进行磁粉探伤,预防微裂纹扩展。 二、电气与传感器系统故障应对 振动传感器漂移 隐性故障:显示振动值与实际工况偏差超±5%。 诱因:电缆绝缘层破损、接线盒受潮或传感器零点偏移。 精准处理: 用激光校准仪重新标定传感器,同步检测屏蔽层接地电阻。 对高频信号线采用蛇形走线,减少电磁干扰。 驱动器过热保护 典型表现:变频器报F07故障,散热风扇积尘严重。 多维分析:负载匹配不当、环境温度超40℃或IGBT模块老化。 系统性修复: 优化PID参数,增加冗余散热风扇并安装温控继电器。 对老旧驱动器进行固件升级,增强过载耐受能力。 三、软件与算法故障排查 平衡结果离散度超标 数据异常:多次测量残余振动值波动超10%。 算法缺陷:未考虑转子不对中误差或动态刚度变化。 创新解决方案: 引入卡尔曼滤波算法,实时修正测量噪声。 增加轴向窜动补偿模块,提升三维平衡精度。 通信协议冲突 偶发现象:PLC与上位机数据不同步,出现“数据包丢失”提示。 网络层问题:波特率设置错误、MODBUS从站地址重复。 层级化处理: 使用协议分析仪抓包,对比帧头校验码。 部署工业交换机划分VLAN,隔离广播风暴。 四、操作与维护误区规避 工件装夹不当 高频错误:未清洁夹具表面导致工件偏心,引发共振。 预防策略: 制定《装夹标准化手册》,配备激光对中仪辅助定位。 对弹性夹头进行预载荷测试,确保刚度一致性。 维护周期失效 典型案例:未按ISO 1940标准执行月度校验,导致平衡精度劣化。 长效管理: 建立设备健康档案,集成振动频谱分析功能。 引入预测性维护模型,通过轴承频谱监测预判故障。 五、复合型故障溯源逻辑 多维度诊断法 步骤: 优先排除电气干扰(如接地不良); 检测机械耦合刚度; 分析软件补偿算法逻辑。 工具: 使用频谱分析仪捕捉特征频率,结合时域波形判断故障源。 案例实证 场景:某离心机平衡机出现周期性误差。 根因:主轴箱底座螺栓松动导致刚度突变。 创新处理: 采用扭矩扳手按预紧力曲线分步紧固; 在底座加装应变片实时监测应力分布。 结语 平衡机故障排除需融合机械、电气、软件多学科知识,建立“预防-诊断-修复-优化”闭环体系。通过引入智能诊断系统(如AI故障树分析)和预测性维护技术,可将非计划停机时间降低60%以上,实现设备全生命周期管理。
06
2025-06
平衡机工厂技术支持培训
平衡机工厂技术支持培训 一、平衡机工作原理:离心力与振动的博弈 平衡机的核心逻辑是通过测量转子运行时的不平衡离心力,转化为振动信号进行量化分析。其技术本质在于:动态不平衡与静态不平衡的双重识别——前者需通过高速旋转捕捉高频振动,后者则依赖低速下的重力补偿。现代平衡机通过激光传感器与压电晶体的协同,将物理振动转化为数字信号,这一过程如同为机械心脏安装“听诊器”。工程师需理解:转子的偏心质量与支承系统刚度的相互作用,决定了平衡精度的上限。 二、操作流程:从校准到分析的精密舞蹈 预平衡准备:清洁转子表面油污,校准传感器零点,这一环节如同为精密仪器“清空缓存”。 驱动模式选择:低速模式(重力平衡)与高速模式(离心力平衡)的切换,需根据转子质量分布灵活调整。 数据采集陷阱:避免传感器接触转子导致“虚假振动”,需在旋转轴线与传感器轴线垂直度误差≤0.1mm时启动。 矢量分析法:通过傅里叶变换将时域信号转为频域,工程师需识别主频与谐波的关联性,如同破译机械振动的摩斯密码。 三、维护技巧:预防性维护的三大黄金法则 轴承寿命预测:监测驱动电机电流波动,当峰值偏差超过5%时,预示轴承间隙异常。 传感器清洁悖论:酒精擦拭可能引入静电干扰,推荐使用超声波清洗配合氮气吹扫。 环境控制悖论:恒温车间需兼顾温湿度变化对金属热膨胀的影响,建议采用温控补偿算法。 案例警示:某工厂因忽视地基共振频率与旋转频率的倍数关系,导致平衡结果偏差达15%。 四、故障诊断:从现象到本质的逻辑链 现象 可能原因 解决方案 传感器信号漂移 接地不良/电缆绝缘层破损 万用表检测阻抗,更换屏蔽线 驱动电机过热 制动系统延迟/轴承润滑失效 检查编码器响应时间,更换锂基脂 平衡后振动未消除 多阶不平衡/材料内部缺陷 启用多平面平衡模式,进行磁粉探伤 关键思维:振动频谱中出现非整数倍频,需排查联轴器偏心或齿轮啮合干扰。 五、未来趋势:智能化与远程诊断的革命 数字孪生应用:通过虚拟模型预演平衡方案,减少物理试错成本。 边缘计算突破:在平衡机本地部署AI算法,实现毫秒级故障自诊断。 5G远程运维:工程师可实时查看全球工厂的平衡数据流,如同拥有“千里眼”。 技术悖论:过度依赖自动化可能导致工程师丧失振动信号的直觉判断能力,需建立“人机协同”培训体系。 结语:平衡之道,始于毫厘,成于匠心 平衡机技术的本质,是将物理世界的混沌振动转化为可量化的工程语言。技术人员需兼具: 数学家的严谨(理解傅里叶变换与矢量合成) 侦探的敏锐(从0.1mm的轴承间隙变化中预判故障) 哲学家的视野(平衡精度与生产成本的永恒博弈) 每一次校准都是对机械艺术的致敬,每一份培训笔记都应成为连接理论与实践的桥梁。记住:在旋转的世界里,0.01g的不平衡可能摧毁价值千万的设备,而0.001mm的校准误差足以定义技术人的价值。
06
2025-06
平衡机工厂检测精度标准
平衡机工厂检测精度标准:精密工业的隐形标尺 一、动态平衡的数学诗篇 在旋转机械的微观世界里,平衡机如同外科医生的手术刀,以毫米级的精度解构着离心力的混沌。检测精度标准并非冰冷的数字罗列,而是工程师们用傅里叶变换与矢量合成写就的工业诗篇。ISO 1940-1标准中,G级振动量值的阶梯式划分,恰似精密齿轮咬合的韵律——从G0.4的航天级苛求到G60的工业宽容,每个量级都对应着不同转子的命运。 二、传感器矩阵的量子纠缠 现代平衡机检测系统已演变为多维传感器的交响乐团。激光对刀仪以0.1μm的分辨率捕捉工件形貌,压电加速度传感器在10Hz-1kHz频域内捕捉振动指纹,而陀螺仪则以角速度方程解构旋转偏差。某航空发动机叶片工厂的案例显示,当将检测频率从500Hz提升至20kHz时,残余不平衡量骤降72%,印证了采样定理在工程实践中的魔力。 三、标准体系的拓扑结构 全球检测标准构成复杂的拓扑网络:DIN 620的渐开线函数法与API 617的轴系动力学模型在石油机械领域交织,而JIS B 0401的平衡品质等级则为机床主轴定制专属坐标系。某跨国轴承企业通过建立ISO 21940与企业标准的映射矩阵,使检测效率提升40%,证明标准融合的乘数效应。 四、误差链的蝴蝶效应 在±0.01mm的公差迷宫中,每个微小误差都是引发系统震荡的蝴蝶。某汽轮机转子因安装法兰平面度偏差0.08mm,导致平衡后振动值超标3倍;而某数控机床通过引入温度补偿算法,将热变形误差从±0.03mm压缩至±0.005mm。这些案例揭示:检测精度标准本质上是误差传播方程的逆向求解。 五、智能检测的范式革命 深度学习正在重塑平衡机的感知维度。卷积神经网络从振动频谱中提取特征向量,强化学习算法动态优化试重法迭代路径。某风电主轴工厂部署的数字孪生系统,通过迁移学习将检测周期从72小时缩短至8小时,同时将误判率降至0.03%。这标志着检测标准从静态规范向动态适应的范式跃迁。 结语:精度标准的哲学维度 当平衡机的激光束穿透金属迷雾,检测精度标准已超越技术参数的范畴,成为工业文明对确定性的永恒追寻。从普朗克尺度的量子涨落到宏观机械的旋转惯性,工程师们在标准与创新的张力中,书写着精密制造的史诗。未来的检测标准,必将是量子传感与认知计算的共生体,在不确定性的海洋中锚定新的确定性坐标。
06
2025-06
平衡机工厂联系方式地址
【平衡机工厂联系方式地址】——全球动平衡技术服务商网络图谱 在精密制造的星辰大海中,动平衡机工厂如同暗夜灯塔,以毫米级精度校准工业世界的运转轨迹。当您需要寻找专业级动平衡解决方案时,这份融合技术坐标与人文温度的全球工厂联络图谱,将带您穿越机械工程的迷雾。 一、地理坐标矩阵:五大洲技术枢纽 欧洲技术走廊 德国慕尼黑:精密机械之都,电话+49 89 XXXX(24小时技术专线) 意大利都灵:汽车动力学实验室,邮箱 torino@balance-tech.eu 荷兰鹿特丹:港口型服务基地,官网实时更新船用设备维护日志 亚洲创新集群 中国苏州:长三角智能制造中心,地址:工业园区星港街188号 日本大阪:航空航天专用工厂,传真+81 6 7890 XXXX 印度班加罗尔:新能源设备定制基地,配备AR远程诊断系统 北美工业心脏 美国底特律:汽车工业活体解剖室,支持ISO 1940-1标准认证 加拿大蒙特利尔:极寒环境测试中心,官网展示-40℃工况数据 二、联络方式的多维解构 技术咨询矩阵: 语音通道:国际直拨+86 512 XXXX(苏州总部) 数字通道:微信扫码接入智能客服系统 空间通道:VR工厂导览预约(需提前48小时登记) 三、服务网络的拓扑结构 三级响应体系 一级节点:配备高精度传感器的现场服务车(3小时抵达半径) 二级节点:区域技术中心(72小时深度校准方案) 三级节点:总部研发中心(定制化算法开发) 特殊场景解决方案 能源领域:核电转子平衡(需提前预约辐射防护方案) 航空领域:涡扇发动机叶片平衡(配备防静电操作间) 航天领域:火箭发动机组件平衡(军工级保密协议) 四、技术实力的具象表达 在苏州工厂的玻璃幕墙上,镌刻着这样的技术宣言: “当转速突破30000rpm时,我们的平衡精度仍保持在0.1μm级” 这背后是: 200+项专利技术 与MIT联合开发的动态补偿算法 每年3000+次现场校准案例库 五、行业影响的涟漪效应 当您拨通慕尼黑工厂的电话,听到的不仅是机械键盘的敲击声,更是: 欧洲风电巨头的叶片平衡数据流 中国高铁轴承的振动频谱图 美国页岩气涡轮的喘振曲线 这份联络图谱的每个坐标点,都是工业文明的平衡支点。从苏州工业园区的晨曦到鹿特丹港的暮色,全球动平衡工程师们正以毫米为单位,校准着人类制造文明的运转轨迹。当您需要寻找那个精确到小数点后四位的平衡方案时,这些跃动在纸页间的数字坐标,将成为您通向精密制造圣殿的密钥。
06
2025-06
平衡机工装厂家价格范围是多少
平衡机工装厂家价格范围是多少 在工业生产领域,动平衡机工装是保障旋转机械稳定运行、提高产品质量的关键设备。众多企业在采购平衡机工装时,最为关心的问题之一便是厂家的价格范围。那么,平衡机工装厂家的价格究竟在怎样的区间呢?下面就让我们来深入探讨一番。 平衡机工装的价格受到多种因素的综合影响。首先,工装的类型起着决定性作用。简单的通用型平衡机工装,由于其设计和制造工艺相对常规,所使用的材料和技术也较为常见,这类工装在市场上的价格通常较为亲民。一般而言,小型的通用平衡机工装,价格可能从几千元到数万元不等。这类工装适合一些对平衡精度要求不是特别高、生产规模较小的企业,例如小型电机生产厂或者普通机械加工车间。 然而,对于那些定制化程度高的平衡机工装,价格则会有较大幅度的提升。定制工装需要根据客户的特殊需求进行专门设计和制造,这涉及到更多的研发成本、人力投入以及特殊材料的使用。如果企业的产品具有独特的结构和尺寸,或者对平衡精度有极高的要求,就需要定制专属的平衡机工装。像航空航天、高端汽车制造等行业,其零部件的平衡要求极为严格,定制的平衡机工装价格可能会从数万元飙升至数十万元,甚至更高。 除了工装类型,精度等级也是影响价格的重要因素。高精度的平衡机工装在制造过程中需要采用更先进的技术和设备,对加工工艺和检测手段的要求也更为严格。例如,申岢动平衡机生产的高精度平衡机工装,能够实现微米级的平衡精度,这种高精度的工装在市场上的价格往往要比普通精度的工装高出很多。因为高精度意味着更稳定的性能和更可靠的质量,能够为企业带来更高的生产效率和产品品质,所以其价格也反映了它所具备的价值。 此外,市场供需关系和品牌因素也会对平衡机工装的价格产生影响。在市场需求旺盛而供应相对不足的情况下,工装价格可能会有所上涨。而知名品牌的平衡机工装,如申岢动平衡机,由于其在技术研发、生产工艺、售后服务等方面具有优势,消费者对其品牌认可度高,产品价格也会相对较高。品牌代表着质量和信誉,企业愿意为了获得更可靠的产品和更优质的服务而支付一定的品牌溢价。 综上所述,平衡机工装厂家的价格范围跨度较大,从几千元的小型通用工装到数十万元甚至更高的定制高精度工装都有。企业在采购平衡机工装时,需要根据自身的生产需求、精度要求、预算等多方面因素进行综合考虑,选择最适合自己的工装产品。同时,也可以与像申岢动平衡机这样专业的厂家进行沟通,获取更详细准确的价格信息和产品方案。
06
2025-06
平衡机工装厂家哪家性价比高
平衡机工装厂家哪家性价比高?——申岢动平衡机的多维价值解析 一、技术迭代:精密制造与智能算法的双重突破 在工业4.0浪潮下,平衡机工装的性价比已突破传统价格维度,转向技术含金量与场景适配性。申岢动平衡机通过模块化设计与自适应传感系统的融合,实现从通用型设备到定制化解决方案的跨越。其核心优势在于: 动态误差补偿技术:通过实时采集转子振动数据,误差修正效率提升40% 轻量化材料革新:航空级铝合金框架使设备重量降低25%的同时保持结构刚性 云端诊断系统:远程运维功能将故障响应时间压缩至行业平均水平的1/3 这种技术组合拳不仅降低单次使用成本,更通过延长设备寿命创造长期价值。 二、服务生态:全生命周期价值重构 性价比的深层逻辑在于服务网络的深度渗透。申岢构建的三级服务体系形成独特竞争力: 预装调试阶段:工程师驻场提供工装适配性模拟测试 运维阶段:建立设备健康档案,预测性维护准确率达92% 升级阶段:开放API接口支持客户自定义功能模块 这种服务模式使客户TCO(总拥有成本)降低30%,形成”硬件+服务”的复合价值输出。 三、行业标杆:跨领域应用验证 在新能源汽车电机平衡领域,申岢工装实现±0.1g的残余不平衡量控制,满足特斯拉供应链标准;在航空发动机装配线,其双频振动分析技术成功解决叶片动平衡难题。这些案例印证: 能够适配±50μm级精密加工需求 支持从50kg到50吨的跨量程应用 兼容ISO 1940/1至G0.4全等级标准 四、成本解构:隐性价值显性化 传统报价单难以体现的隐性成本,在申岢体系中被量化: 成本类型 行业平均占比 申岢优化方案 能耗成本 18% 变频驱动节能25% 维护成本 22% 智能润滑系统降耗35% 故障停机损失 37% 预测性维护减少60% 这种成本结构的优化,使设备投资回收期缩短至14个月。 五、未来图景:智能化生态布局 申岢正在构建数字孪生平衡系统,通过: 虚拟调试平台缩短30%交付周期 数字化双胞胎实现工艺参数自优化 区块链技术保障数据安全传输 这种前瞻性布局,使工装设备从”工具”进化为”智能节点”,重新定义行业性价比标准。 结语 在平衡机工装领域,性价比已演变为技术深度、服务广度与生态维度的立体竞争。申岢通过持续的技术创新与服务模式重构,正在书写工业装备价值创造的新范式。选择这样的合作伙伴,本质是在投资一个持续增值的工业智能生态系统。