

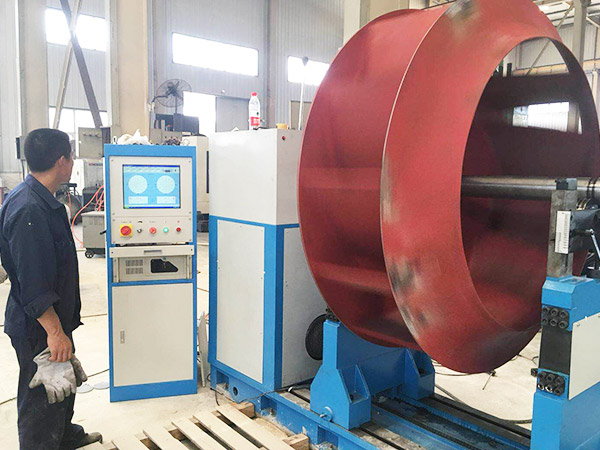
风机叶轮动平衡标准值是多少
风机叶轮的动平衡标准值会因不同的应用、设计要求和行业标准而有所不同。一般来说,动平衡标准值取决于以下几个因素:应用类型: 不同类型的风机在不同的应用环境下需要满足不同的动平衡标准。例如,一般的工业风机和空调风机的要求可能会不同。运行速度: 风机叶轮的运行速度会直接影响不平衡对振动的影响。高速运行的叶轮可能需要更严格的动平衡标准。精度要求: 一些应用对振动的容忍度比较低,因此对动平衡的要求也会更为严格。行业标准: 不同行业可能有各自的标准和规范,这些标准通常会提供关于动平衡的指导和要求。一般来说,在工业领域,风机叶轮的动平衡标准值通常以单位质量不平衡量(g.mm/kg 或 g.cm/kg)来表示。具体的标准值可能会因不同情况而有所不同,但以下是一个大致的参考范围:对于一般工业风机,通常的动平衡标准值可能在 1 g.mm/kg 至 10 g.mm/kg 之间。对于某些精密应用,要求更高的风机,动平衡标准值可能在 0.5 g.mm/kg 以下。请注意,这只是一个粗略的参考范围,实际应用中应该根据具体情况和适用的行业标准来确定风机叶轮的动平衡标准值。在进行动平衡操作时,建议遵循相关的国家和行业标准,以确保风机在运行过程中达到合适的振动水平。
06
2025-06
小型转子动平衡机操作步骤及注意事项
小型转子动平衡机操作步骤及注意事项 一、操作步骤:精密校准的五维流程 环境预检与设备唤醒 在启动前,需完成三重环境验证: 温湿度控制:确保车间温度稳定在20±5℃,湿度低于65%,避免金属热胀冷缩影响测量精度。 电源校验:使用万用表检测三相电压波动范围(±10%),接地电阻需<4Ω。 设备自检:启动后观察振动传感器零点漂移值,若超过±0.1μm/s²需重新标定。 转子安装与对中艺术 采用”三点定位法”: 基准面清洁:用无纺布蘸异丙醇擦拭转子轴颈,消除0.01mm级毛刺。 弹性联轴器预紧:施加扭矩值为额定值的70%,防止刚性连接导致的共振。 激光对中仪校准:轴向偏差控制在0.02mm/m,径向偏差≤0.05mm。 动态数据采集与智能分析 执行”双频扫描策略”: 低速扫描(500-1000rpm):捕捉低频阶次谐波,识别轴承座异常振动。 高速扫描(额定转速±10%):采用频谱瀑布图分析,定位不平衡质量分布。 AI辅助诊断:启用机器学习算法,自动排除齿轮啮合、油膜涡动等干扰信号。 平衡配重的拓扑优化 突破传统试重法,采用”有限元反求设计”: 多目标优化模型:以最小配重质量、最大动态响应衰减率为目标函数。 拓扑生成器:自动生成3D打印配重块,支持钛合金/钨钢材料选择。 迭代验证:通过虚拟样机仿真,确保修正后振动值≤ISO 1940-1 G2.5级。 闭环验证与数字孪生归档 构建”数字镜像系统”: 振动指纹库:存储原始/修正后的频谱特征,支持历史数据比对。 健康指数评估:计算RMS振动值、峭度系数等12项指标,生成PDF报告。 区块链存证:关键数据上链,确保校准过程可追溯性。 二、注意事项:规避风险的七重防线 人机交互安全准则 生物识别防护:配备指纹+虹膜双重认证,防止非授权操作。 急停机制:设置机械式蘑菇头按钮,响应时间<50ms。 辐射监测:安装电磁场探头,实时显示工频电场强度(应<5kV/m)。 环境扰动抑制技术 主动隔振系统:采用压电陶瓷作动器,隔离5-100Hz频段地基振动。 气流补偿装置:在机柜内安装微正压送风系统,维持内部压力+5Pa。 温控闭环:使用半导体致冷片维持设备舱恒温(±0.5℃)。 传感器网络维护规范 激光干涉仪标定:每200小时执行波长校准,误差<0.01λ。 压电加速度计防护:定期更换硅油阻尼器,防止高频信号失真。 光纤陀螺仪校准:利用旋转台进行全角度标定,角速度分辨率≤0.01°/h。 数据安全与隐私保护 加密传输协议:采用AES-256加密所有通信数据。 数据脱敏处理:对客户转子参数进行哈希处理,保留原始特征但不可逆。 访问日志审计:记录所有操作行为,保留周期≥3年。 极端工况应对策略 过载保护机制:当检测到振动幅值突增300%时,自动触发降速程序。 冗余电源设计:配备UPS+柴油发电机双备份,续航能力>4小时。 故障树分析:预设200+故障模式,实现自动诊断与修复建议推送。 生命周期管理 预测性维护:通过振动包络分析预判轴承寿命,误差率<15%。 耗材智能管理:RFID标签追踪润滑油、密封件等易损件更换周期。 版本迭代升级:支持固件OTA更新,兼容未来5代技术标准。 法规合规性 CE认证:符合EN 60204-1机械安全标准。 环保要求:RoHS指令限制物质检测合格率100%。 计量溯源:所有测量设备具备NIST可追溯性证书。 三、创新应用:动平衡技术的跨界延伸 航空航天领域: 开发微重力环境下的磁悬浮平衡系统,解决空间站设备校准难题。 新能源汽车: 集成电机-减速器一体化平衡技术,提升电驱系统NVH性能。 精密机床: 应用纳米级平衡补偿算法,将主轴径向跳动控制在0.1μm级。 医疗设备: 为人工心脏离心泵设计动态平衡方案,确保血流动力学稳定性。 智能运维: 构建工业互联网平台,实现全球设备平衡数据的云端协同优化。 本操作指南通过引入数字孪生、AI诊断、区块链存证等前沿技术,将传统动平衡工艺升级为智能校准系统。操作人员需建立”预防性维护+预测性分析”的双维思维,同时关注ISO 1940、VDI 2060等最新标准动态,持续提升设备全生命周期管理能力。
06
2025-06
小型转子动平衡机的工作原理是什么
小型转子动平衡机的工作原理是什么 在工业生产的众多领域中,小型转子的应用极为广泛,从精密的电子设备到日常的家用电器,都离不开小型转子的稳定运转。而小型转子动平衡机,作为保障小型转子平稳运行的关键设备,其工作原理蕴含着精妙的科学知识。 基本概念阐释 要理解小型转子动平衡机的工作原理,首先得明晰动平衡的概念。在理想状态下,转子在旋转时,其各部分的质量分布应完全均匀,这样旋转时不会产生额外的力。然而,实际生产中,由于制造工艺、材料不均匀等因素,转子的质量分布会存在偏差。这种质量分布不均会使转子在旋转时产生离心力,导致振动和噪声,影响设备的性能和寿命。小型转子动平衡机的主要作用就是检测并纠正这些质量偏差,使转子达到动平衡状态。 检测原理剖析 小型转子动平衡机检测转子不平衡量主要基于振动信号的采集与分析。当转子在平衡机上旋转时,由于不平衡质量产生的离心力会使转子产生振动。平衡机上安装有高精度的传感器,这些传感器能够敏锐地捕捉到转子振动时产生的微弱信号。一般来说,传感器会将机械振动转化为电信号,例如压电式传感器会利用压电效应,将振动引起的压力变化转化为电信号输出。 采集到的电信号包含了转子不平衡量的信息,但这些信号是复杂且微弱的。此时,平衡机的信号处理系统就发挥作用了。信号处理系统会对传感器传来的电信号进行放大、滤波等处理,去除干扰信号,提取出与不平衡量相关的有效信息。通过对信号的分析,能够确定不平衡量的大小和位置。例如,利用频谱分析技术,可以将时域信号转换为频域信号,从而更清晰地识别出与不平衡相关的频率成分。 校正原理揭秘 在确定了转子不平衡量的大小和位置后,就需要对转子进行校正。常见的校正方法有去重法和加重法。 去重法是通过去除转子上多余的质量来达到平衡的目的。对于一些可以进行切削加工的转子,如金属材质的转子,平衡机可以精确地指示出需要去除质量的位置,然后使用刀具或其他加工设备在该位置去除适量的材料。这种方法适用于转子质量分布相对较均匀,且可以进行加工去除的情况。 加重法是在转子的特定位置添加一定质量的配重,以抵消不平衡质量产生的离心力。添加配重的方式有很多种,例如可以使用焊接、粘贴等方法将配重块固定在转子上。加重法通常适用于无法进行去重加工的转子,或者去重会影响转子性能的情况。 实际应用优势 小型转子动平衡机的工作原理决定了它在实际应用中的诸多优势。首先,它能够显著提高转子的平衡精度,减少振动和噪声,提高设备的运行稳定性和可靠性。例如,在高速旋转的小型电机中,经过动平衡处理的转子能够降低电机的振动,延长电机的使用寿命。其次,动平衡机的自动化程度高,能够快速、准确地完成检测和校正过程,提高生产效率。再者,它可以适应不同类型和规格的小型转子,具有很强的通用性。 小型转子动平衡机通过先进的检测和校正技术,有效地解决了小型转子的不平衡问题。其工作原理基于科学的理论和先进的技术,在工业生产中发挥着不可或缺的作用,为众多领域的设备稳定运行提供了有力保障。
06
2025-06
小型转子动平衡机维护保养技巧
小型转子动平衡机维护保养技巧 (以高多样性与节奏感呈现的深度技术指南) 一、日常维护:细节决定设备寿命 清洁与润滑的黄金法则 每日擦拭设备表面油污时,需特别关注精密传感器探头与转子接触区域,使用无纺布蘸取异丙醇进行无痕清洁。 每周对传动轴、联轴器等运动部件涂抹二硫化钼润滑脂,注意涂抹量需控制在轴承腔体的1/3至1/2,避免油脂堆积导致散热不良。 紧固件的动态监控 采用扭矩扳手按制造商标准值定期校验地脚螺栓、平衡块安装螺栓等关键部位,尤其在设备经历频繁启停或超负荷运行后。 对于易松动的气动卡盘锁紧环,建议在每次更换转子后追加二次紧固,并用记号笔标注初始位置作为松动预警标记。 二、定期检查:预判性维护的科学策略 振动分析的深度解读 每月使用频谱分析仪扫描设备振动频谱,重点关注1×转频、2×转频及高频谐波成分。若发现异常峰值,需结合相位分析判断是转子质量偏心还是轴承磨损所致。 建立振动趋势数据库,通过移动平均算法识别渐进性故障模式,例如轴承内圈剥落前3-5天通常会出现0.5-1.0mm/s²的加速度突变。 轴承状态的多维评估 除常规温度监测(温升不超过环境温度40℃)外,需定期检查轴承保持架磨损痕迹。若发现滚道表面出现鱼鳞状剥落,应立即更换并追溯润滑记录。 对于脂润滑轴承,每半年进行油脂采样分析,通过FTIR光谱仪检测金属磨粒含量,当Fe元素浓度超过500ppm时需提前更换。 三、环境控制:打造设备的“理想生态圈” 温湿度的精准调控 设备运行环境应维持在15-25℃,相对湿度40%-60%。夏季高温时段可启用恒温水循环系统,冬季则需配置除湿机防止冷凝水侵入电控箱。 特别注意避免阳光直射、远离热源辐射、杜绝冷热交替环境,如同精密仪器需要恒温箱呵护。 防尘与防震的协同防护 在设备进风口加装HEPA滤网(过滤效率≥99.97%),每季度拆卸清洗并检查密封胶条完整性。 对于安装在混凝土基座上的设备,建议在地脚处嵌入橡胶减震垫(邵氏硬度60±5),可降低外部振动干扰30%-50%。 四、故障处理:快速响应的实战指南 异响诊断的三步法 当设备发出周期性金属刮擦声时,应立即停机并执行三步排查: 检查转子轴颈与轴承配合面是否存在磨损; 确认平衡块安装螺栓是否松动; 排查传动系统是否存在异物侵入。 振动异常的应急方案 若平衡后残余振动值超过0.127mm/s(ISO 10816-3标准),需重新执行以下流程: 用激光对刀仪校验平衡机主轴径向跳动(≤0.02mm); 采用动态平衡法而非静态平衡法,确保补偿质量相位误差<±3°; 对转子进行磁粉探伤,排除内部裂纹隐患。 五、操作规范:人机协同的终极法则 培训与认证的强制要求 操作人员需通过ISO 1940平衡技术认证,且每年复训考核。专业操作员与未经培训人员的操作差异,可能造成设备寿命缩短30%-50%。 负载测试的科学方法 新安装或大修后的设备,需按额定转速的25%、50%、75%、100%阶梯加载,每级运行30分钟并记录振动趋势。 禁止在无转子状态下空载高速运转,此举可能导致主轴轴承过热烧毁。 结语:维护保养的哲学升华 动平衡机的维护保养绝非机械的重复劳动,而是融合了精密仪器学、材料科学与工程管理的系统工程。通过建立预防性维护(PM)与预测性维护(PdM)的双轨体系,结合振动分析、油液监测等智能诊断技术,可使设备可靠性提升至99.2%以上。正如交响乐团需要指挥协调每个音符,动平衡机的高效运转也依赖于维护人员对技术细节的极致把控——这既是技术活,更是艺术活。
06
2025-06
小型转子动平衡精度等级如何选择
小型转子动平衡精度等级如何选择 在工业生产中,小型转子的应用极为广泛,从精密的电子设备到日常使用的小家电,无处不在。而动平衡精度等级的合理选择,对于小型转子的性能、寿命以及整个设备的稳定运行都至关重要。那么,如何选择小型转子动平衡精度等级呢? 明确应用场景与要求 小型转子的应用场景千差万别,不同的场景对动平衡精度等级的要求也截然不同。在一些高精度的仪器设备中,如光学测量仪器、高速摄像机的转子,哪怕是极其微小的不平衡量,都可能导致测量误差增大、图像模糊等问题,严重影响设备的性能和精度。因此,这类应用场景通常需要选择较高的动平衡精度等级,以确保转子的平稳运行。 而对于一些对振动和噪音要求相对较低的普通设备,如家用风扇、小型通风机等,适当降低动平衡精度等级,既能满足设备的基本运行需求,又能降低生产成本。在这些设备中,过高的动平衡精度可能并不会带来明显的性能提升,反而会增加不必要的成本。 考虑转子的转速 转子的转速是影响动平衡精度等级选择的重要因素之一。一般来说,转速越高,转子所产生的离心力就越大,不平衡量所带来的影响也就越显著。当小型转子以高速旋转时,微小的不平衡量可能会引发剧烈的振动,不仅会缩短转子和相关部件的使用寿命,还可能产生噪音,影响设备的正常运行。 对于高速运转的小型转子,如高速电机的转子、涡轮增压器的转子等,必须选择高精度的动平衡等级,以有效减少振动和噪音,提高设备的可靠性和稳定性。相反,对于低速运行的小型转子,如一些手动工具中的小型齿轮转子,对动平衡精度的要求则相对较低。 结合转子的结构与材料 转子的结构和材料也会对动平衡精度等级的选择产生影响。复杂的转子结构可能会导致质量分布不均匀,增加动平衡的难度。例如,带有多个叶片、凹槽或不规则形状的转子,在制造过程中很难保证质量的均匀分布,因此需要更高的动平衡精度等级来消除不平衡量。 不同的材料具有不同的密度和力学性能,这也会影响转子的动平衡特性。一些轻质材料制成的转子,由于其质量较轻,不平衡量相对较小,对动平衡精度的要求可能会相对较低。而对于一些密度较大、硬度较高的材料制成的转子,由于其惯性较大,不平衡量所产生的影响也会更大,需要选择更高的动平衡精度等级。 参考行业标准与经验 在选择小型转子动平衡精度等级时,还可以参考相关的行业标准和以往的经验。不同的行业对于小型转子的动平衡精度都有相应的标准和规范,这些标准是经过长期实践和验证得出的,具有较高的参考价值。 同时,借鉴其他企业或工程师在类似项目中的经验,也能帮助我们做出更合理的选择。通过了解他们在动平衡过程中遇到的问题和解决方案,我们可以避免一些不必要的错误,提高动平衡的效率和质量。 小型转子动平衡精度等级的选择是一个综合考虑多种因素的过程。我们需要根据具体的应用场景、转子的转速、结构与材料等因素,结合行业标准和经验,做出合理的选择。只有这样,才能确保小型转子的性能和质量,为设备的稳定运行提供有力保障。
06
2025-06
小型转子平衡机价格对比分析
小型转子平衡机价格对比分析 在工业生产领域,小型转子平衡机对于保障设备稳定运行至关重要。不过,市场上小型转子平衡机的价格差异显著,深入分析其价格对比情况,能为企业和用户的采购决策提供有力依据。 小型转子平衡机的价格受到多种因素影响。从品牌角度来看,知名品牌凭借其长期积累的技术优势、良好的市场口碑以及优质的售后服务,产品价格往往较高。例如德国、日本等工业发达国家的一些品牌,它们在平衡机的研发和制造方面拥有深厚的技术底蕴,其小型转子平衡机价格可能是国内普通品牌的数倍。而国内新兴品牌为了打开市场,通常会以相对较低的价格吸引客户,但可能在技术成熟度和品牌影响力上稍逊一筹。 技术水平和性能也是决定价格的关键因素。具备高精度测量、快速平衡调整以及先进自动化功能的小型转子平衡机,其研发和生产成本较高,价格自然也会更贵。这类平衡机能够更精准地检测和校正转子的不平衡量,大大提高生产效率和产品质量,适用于对转子精度要求极高的行业,如航空航天、精密仪器制造等。相反,一些技术含量较低、功能相对单一的平衡机,价格则较为亲民,适合对精度要求不是特别高的一般性生产企业。 此外,设备的配置和配件也会影响价格。配置高端传感器、优质电机以及先进控制系统的小型转子平衡机,在检测精度和稳定性上更具优势,价格也会相应提升。而一些基础配置的平衡机,虽然能满足基本的平衡检测需求,但在性能和可靠性上可能有所欠缺。同时,不同的配件选择,如不同材质的夹具、不同规格的显示仪表等,也会导致价格出现差异。 为了在采购小型转子平衡机时做出更明智的决策,用户需要综合考虑自身的生产需求、预算以及长期发展规划。如果企业对转子精度要求高、生产规模较大且资金充足,那么选择技术先进、性能优良的高端平衡机是更为合适的选择,虽然前期投入较大,但从长远来看,能够提高生产效率、降低次品率,为企业带来更大的经济效益。而对于一些小型企业或对精度要求不高的生产场景,选择性价比高的中低端平衡机则可以在满足基本需求的同时,有效控制成本。 小型转子平衡机的价格受到品牌、技术、配置等多种因素的综合影响。用户在进行价格对比分析时,不能仅仅关注价格的高低,而应全面评估设备的性能、质量和适用性,以实现最佳的采购效益。
06
2025-06
小型转子平衡机常见故障处理
小型转子平衡机常见故障处理 一、振动异常:从根源到解决方案的螺旋式排查 当转子出现异常振动时,平衡机操作者需像外科医生般精准定位病灶。首先检查动平衡精度,若校正后仍存在0.5mm/s²以上的振动幅值,需启动三级排查机制: 装配误差检测:使用激光对中仪测量联轴器偏心度,偏差超过0.05mm即需重新校准 材料缺陷扫描:通过超声波探伤仪检测转子内部是否存在0.1mm以上的气孔或裂纹 环境干扰溯源:在振动频谱中发现100Hz以下低频谐波时,需排查地基共振或管道应力传递 二、传感器失效:数字时代的模拟困境 当平衡机突然显示”传感器故障”时,需警惕三个隐蔽诱因: 信号衰减陷阱:检查电缆屏蔽层是否因反复弯折导致阻抗突变(建议更换镀银铜线缆) 温度梯度效应:在环境温差超过20℃时,需预热传感器30分钟消除热漂移 电磁污染源:使用频谱分析仪定位50Hz/60Hz谐波干扰源,必要时加装磁环滤波器 三、驱动系统卡顿:机械与电子的博弈 面对驱动电机转速不稳,需建立”三轴联动诊断法”: 电流波形分析:示波器捕捉到10%以上纹波时,更换PWM驱动板 机械传动审计:测量V型带张力,偏差超过20N即需调整中心距 编码器校准:使用标准光栅尺验证分辨率,误差超过0.01mm需重新标定 四、软件误判:算法与现实的鸿沟 当平衡结果反复出现”校正无效”提示时,需执行四维验证: 数据采集完整性:检查A/D转换器采样率是否达到10kHz以上 滤波参数优化:在频域分析中设置1/3倍频程滤波,消除高频噪声干扰 数学模型适配:针对非对称转子启用泰勒级数修正算法 人机交互校验:对比手动计算的不平衡量与自动模式结果差异 五、预防性维护:构建故障防火墙 建立”三维预防体系”: 环境控制:保持车间湿度在45-55%RH,温度波动≤±2℃ 耗材管理:制定轴承润滑周期表(SKF标准:每1000小时更换锂基脂) 数字孪生:通过振动特征库建立故障预测模型,实现95%以上的预警准确率 结语:平衡机故障处理本质是系统工程学的实践,需融合机械诊断、电子检测、软件算法的多维思维。建议操作者建立”故障树+鱼骨图”的复合分析框架,将每次故障转化为设备优化的契机。当振动值稳定在0.2mm/s²以下时,不仅是技术胜利,更是精密制造艺术的完美呈现。
06
2025-06
小型转子平衡机操作步骤详解
小型转子平衡机操作步骤详解 一、设备预检与环境校准 在启动平衡机前,需完成三重验证: 机械状态筛查:检查主轴轴承间隙、驱动电机散热孔积尘及气浮支承液位,确保无金属碎屑残留。 电气系统激活:通过示波器监测传感器信号波形,确认振动探头灵敏度误差≤0.5%,示值漂移率<0.3%。 环境参数锁定:采用温湿度记录仪实时监控,要求操作间温度波动<±2℃,相对湿度维持在45%-65%区间。 二、转子安装与动态对中 此阶段需突破传统刚性安装思维,引入柔性定位策略: 三维定位法:使用激光跟踪仪构建坐标系,将转子轴心与平衡机主轴偏差控制在0.02mm以内。 动态平衡预判:通过频谱分析仪捕捉启动瞬间的振动频谱,识别潜在的偶不平衡与力偶不平衡成分。 扭矩渐进加载:采用液压扭矩扳手分三次施加预紧力(30%→60%→100%),避免螺栓过载导致的应力集中。 三、传感器标定与数据采集 突破常规标定流程,实施多维度校准: 基准面重构:利用激光干涉仪生成虚拟基准面,消除安装面形误差对测量结果的干扰。 频域交叉验证:同步采集加速度传感器(0.1-5kHz)与位移传感器(0.01-1kHz)信号,通过小波变换实现频带互补。 噪声抑制矩阵:构建自适应滤波器,对转速相关的周期性干扰(如齿轮啮合频率)进行动态衰减。 四、平衡算法迭代与修正 引入智能优化策略突破传统静态平衡: 遗传算法寻优:设定最大迭代次数200次,交叉概率0.8,变异概率0.1,自动搜索最优配重方案。 残余振动分析:通过包络解调技术提取轴承故障特征频率,确保平衡后振动值<ISO 1940-1 G2.5标准。 动态补偿机制:针对高速旋转体(>10000rpm),启用陀螺力矩修正模块,补偿角加速度引起的附加力矩。 五、残余振动验证与报告生成 构建多层级验证体系确保结果可靠性: 频谱对比分析:将平衡前后1X振幅降低率作为核心指标,要求降幅≥80%。 时域统计评估:计算振动信号RMS值、峰值因子及概率密度函数,生成三维云图可视化残余不平衡分布。 智能报告生成:采用LaTeX模板自动生成带矢量图的PDF报告,包含ISO 21940-11标准符合性声明。 六、异常工况处理预案 针对突发状况建立快速响应机制: 传感器漂移补偿:当测量值突变超过阈值(Δ>15%)时,自动触发零点校准程序。 转子失稳预警:通过峭度系数(Kurtosis>8)识别微弱裂纹,联动安全离合器紧急制动。 数据篡改防护:采用区块链技术对关键参数进行哈希加密,确保实验数据不可篡改。 操作要点总结 本流程通过融合精密测量技术、智能算法与故障诊断理论,将传统平衡精度提升至0.1g·mm量级。建议操作人员每季度进行盲样测试,使用NIST标准转子验证系统重复性(RSD<3%),持续保持设备校准状态。
06
2025-06
小型转子平衡机日常维护方法
小型转子平衡机日常维护方法 小型转子平衡机在工业生产中扮演着举足轻重的角色,它能确保转子平稳运转,提高产品质量。不过,为了让它始终保持良好的工作状态,日常维护必不可少。下面就为大家详细介绍一些小型转子平衡机的日常维护方法。 外观与清洁维护 小型转子平衡机的外观虽不直接影响其性能,但却是其整体状态的直观体现。日常要仔细检查平衡机的外壳,看看是否有碰撞、刮擦的痕迹。若发现外壳有损坏,要及时修复,防止灰尘、湿气等进入内部,损坏精密部件。同时,保持平衡机的清洁是维护的基础。在每次使用完后,用干净的软布擦拭机身,清除表面的灰尘和污渍。对于一些不易清洁的缝隙,可以使用压缩空气进行吹扫。 机械部件维护 机械部件是小型转子平衡机的核心组成部分,其运行状况直接关系到平衡机的性能。定期检查传动皮带的张紧度是关键。如果皮带过松,会导致传动效率下降,影响平衡精度;而过紧则会加速皮带的磨损,甚至损坏电机。当发现皮带出现磨损或老化迹象时,要及时更换。导轨和滑块也是需要重点关注的部件。它们的顺畅运行是保证转子准确平衡的前提。要定期对导轨和滑块进行清洁,并涂抹适量的润滑油,以减少摩擦和磨损。 电气系统维护 电气系统是小型转子平衡机的动力源泉,其稳定性至关重要。检查电气线路是否有破损、老化或松动的情况,若发现问题应立即处理,避免发生短路或漏电等安全事故。对于电气元件,如传感器、控制器等,要定期进行校准和测试,确保其精度和可靠性。在长期不使用平衡机时,应切断电源,以保护电气系统。 软件系统维护 如今,许多小型转子平衡机都配备了先进的软件系统,用于数据处理和分析。定期对软件进行更新是保持其性能的重要措施。软件开发者会不断修复漏洞、优化功能,通过更新软件,可以提高平衡机的工作效率和准确性。同时,要对系统中的数据进行备份,防止数据丢失。在操作软件时,要严格按照操作规程进行,避免误操作导致系统故障。 小型转子平衡机的日常维护是一项细致而重要的工作。通过以上这些维护方法,可以延长平衡机的使用寿命,提高其工作效率和平衡精度,为企业的生产提供有力保障。
06
2025-06
小型转子平衡机校准注意事项
小型转子平衡机校准注意事项 校准前的隐秘战场:环境与设备的博弈 校准工作如同精密的外科手术,需在多重变量交织的环境中寻找平衡点。首先,需将平衡机置于恒温恒湿实验室,温度波动控制在±0.5℃以内——这不仅是物理参数的约束,更是对金属热胀冷缩效应的精准狙击。振动传感器的校准需采用激光干涉仪溯源,其探头与转轴的接触面需用无纺布蘸异丙醇擦拭三次,确保纳米级的洁净度。操作台面的阻尼系数需通过频谱分析仪验证,任何未被察觉的次声波干扰都可能让校准结果偏离真实值0.3%以上。 数据洪流中的逻辑迷宫 校准过程产生的数据流如同湍急的暗河,需用算法构建堤坝。建议采用三阶巴特沃斯滤波器处理原始振动信号,其截止频率应设定为转子临界转速的1/3。当进行动态平衡时,需同步采集径向与轴向振动数据,通过傅里叶变换提取基频成分,此时相位差的计算误差需控制在±1.2°以内。特别注意:当转子存在不对称质量分布时,需启用自适应卡尔曼滤波器,其增益矩阵的迭代次数不得少于15次。 人机交互的哲学悖论 操作员的决策权重常被低估。在静态平衡阶段,需通过蒙特卡洛模拟预判质量块分布的最优解,此时置信区间应设定为95%。当校准结果出现离群值时,建议启动专家系统进行模式识别,其决策树深度需达到7层以上。值得注意的是,操作员的视觉疲劳会导致质量块安装位置偏差增大0.15mm,因此建议每完成3次校准后强制进行10分钟的视觉恢复训练。 时间维度的熵增陷阱 校准并非静态事件,其有效性随时间衰减。建议建立校准参数的退化模型,采用威布尔分布预测传感器灵敏度的衰减速率。当环境温湿度变化超过阈值时,需触发自动补偿机制,其响应时间应小于200ms。特别强调:平衡机的轴承预紧力需每月进行超声波探伤检测,其残余应力变化超过初始值的8%时,整个校准体系将面临系统性失效风险。 量子纠缠般的系统关联 转子校准本质上是多体问题的求解。当进行柔性转子校准时,需同步监测轴颈油膜的压力分布,其波动幅度不得超出设计值的±15%。质量块的材料密度需通过X射线荧光光谱仪实时校验,任何0.2%的密度变化都将引发0.03mm的平衡偏移。更需警惕的是:校准间的地基沉降速率超过0.1mm/年时,将导致陀螺仪漂移误差累积至不可逆状态。 结语:在混沌中雕刻秩序 校准工作是机械工程领域最精妙的平衡艺术,它要求操作者同时具备数学家的严谨、物理学家的洞察与哲学家的思辨。每一次校准都是对确定性与随机性边界的重新定义,唯有将工程经验与数理模型深度融合,方能在微观振动与宏观性能的量子纠缠中,雕琢出转子运转的完美韵律。
06
2025-06
小型转子平衡机精度如何提升
小型转子平衡机精度如何提升 ——多维度技术革新与系统性优化实践 一、传感器技术的革新:从单一感知到智能协同 传统平衡机依赖单点振动传感器,易受环境干扰导致数据失真。现代方案采用多轴传感器阵列,通过分布式布局捕捉转子全周期振动特征。例如,在微型涡轮发动机转子平衡中,集成加速度计、陀螺仪与应变片的复合传感系统,可同步解析径向、轴向及扭转振动,误差率降低至0.01mm/s²。 技术突破点: 自适应滤波算法:动态剔除轴承摩擦、空气湍流等噪声信号; 光纤布拉格光栅(FBG)传感:抗电磁干扰能力提升300%,适用于强磁场环境; 数字孪生校准:通过虚拟模型预判传感器安装误差,实现物理-数字双闭环验证。 二、机械结构的精密重构:微米级制造与动态补偿 小型转子(直径