

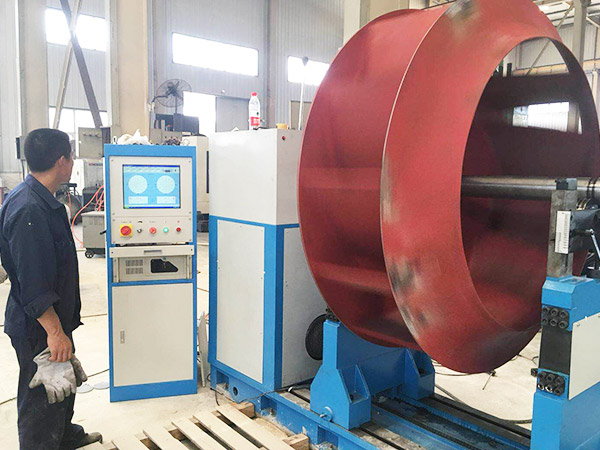
风机叶轮动平衡标准值是多少
风机叶轮的动平衡标准值会因不同的应用、设计要求和行业标准而有所不同。一般来说,动平衡标准值取决于以下几个因素:应用类型: 不同类型的风机在不同的应用环境下需要满足不同的动平衡标准。例如,一般的工业风机和空调风机的要求可能会不同。运行速度: 风机叶轮的运行速度会直接影响不平衡对振动的影响。高速运行的叶轮可能需要更严格的动平衡标准。精度要求: 一些应用对振动的容忍度比较低,因此对动平衡的要求也会更为严格。行业标准: 不同行业可能有各自的标准和规范,这些标准通常会提供关于动平衡的指导和要求。一般来说,在工业领域,风机叶轮的动平衡标准值通常以单位质量不平衡量(g.mm/kg 或 g.cm/kg)来表示。具体的标准值可能会因不同情况而有所不同,但以下是一个大致的参考范围:对于一般工业风机,通常的动平衡标准值可能在 1 g.mm/kg 至 10 g.mm/kg 之间。对于某些精密应用,要求更高的风机,动平衡标准值可能在 0.5 g.mm/kg 以下。请注意,这只是一个粗略的参考范围,实际应用中应该根据具体情况和适用的行业标准来确定风机叶轮的动平衡标准值。在进行动平衡操作时,建议遵循相关的国家和行业标准,以确保风机在运行过程中达到合适的振动水平。
06
2025-06
如何预防发电机动平衡机的常见故障
如何预防发电机动平衡机的常见故障 发电机动平衡机在保障发电机稳定运行中扮演着至关重要的角色,然而,其在使用过程中难免会出现一些常见故障。为了减少故障发生,保障设备正常运转,我们需要采取一系列有效的预防措施。 做好日常检查与维护 日常检查是预防故障的基础。定期查看动平衡机的机械部件,如皮带是否有磨损、松动的情况。皮带若出现磨损,会影响动力传输的稳定性,进而导致测量结果不准确;而松动的皮带则可能在运行中滑落,造成设备停机。同时,要检查各连接部位的螺栓是否紧固,因为在设备运行时的震动可能会使螺栓松动,若不及时发现并紧固,可能会引发部件移位甚至损坏。 此外,还要关注润滑系统。良好的润滑能减少部件之间的摩擦,延长设备使用寿命。定期检查润滑油的油量和油质,若油量不足应及时添加,油质变差时要及时更换。对于一些关键的润滑点,如轴承部位,要按照规定的时间和用量进行润滑。 确保工作环境适宜 发电机动平衡机对工作环境有一定要求。要将其放置在干燥、清洁的场所,避免潮湿和灰尘对设备造成损害。潮湿的环境容易使设备的电气部件生锈、短路,而过多的灰尘会进入设备内部,影响传感器等精密部件的正常工作。 同时,要控制好工作环境的温度和湿度。过高的温度会使设备的电子元件性能下降,甚至损坏;而过低的温度则可能导致润滑油粘度增加,影响润滑效果。一般来说,动平衡机的工作温度宜保持在 10℃ - 35℃之间,相对湿度在 40% - 70%为宜。 规范操作流程 操作人员的规范操作是预防故障的关键。在启动动平衡机前,要确保设备的各项参数设置正确,被检测的发电机安装牢固。在操作过程中,要严格按照操作规程进行,避免因误操作而导致设备故障。例如,在设备运行时,严禁触摸旋转部件,以免发生危险。 此外,要对操作人员进行专业培训,使其熟悉设备的性能和操作方法。只有经过专业培训的人员才能准确判断设备的运行状态,及时发现异常情况并采取相应的措施。 定期进行校准与检测 定期对动平衡机进行校准和检测是确保其测量精度和可靠性的重要手段。可以按照设备制造商的建议,定期邀请专业的技术人员对设备进行校准,以保证测量结果的准确性。同时,要对设备的各项性能指标进行检测,如转速、振动值等,及时发现潜在的问题。 在进行校准和检测时,要使用专业的检测设备和工具,确保检测结果的可靠性。对于检测中发现的问题,要及时进行修复和调整,避免问题扩大化。 预防发电机动平衡机的常见故障需要从日常检查与维护、工作环境、操作流程以及校准检测等多个方面入手。只有做好这些预防工作,才能降低设备的故障率,提高设备的使用寿命,为发电机的稳定运行提供有力保障。
06
2025-06
威力克平衡机维修维护注意事项
威力克平衡机维修维护注意事项 一、日常维护:精密仪器的”生命线” 清洁与防尘 如同人体的免疫系统,平衡机的精密传感器对粉尘异常敏感。建议每日用无纺布蘸取异丙醇擦拭转轴接触面,每周拆卸防护罩进行内部除尘。特别注意振动传感器探头的镜面处理,可用脱脂棉签以螺旋轨迹轻扫。 润滑策略 轴承部位采用”阶梯式润滑法”:新机前3个月每50小时注油0.5ml,3个月后延长至100小时/1ml。需注意,主轴密封圈处仅允许使用美孚SHC 600系列润滑脂,避免普通黄油导致的脂类污染。 传感器校准 每月执行”三阶校准法”:首先用标准校准块进行静态校准,再以1200rpm空载运行完成动态补偿,最后通过ISO 1940-1标准试件验证精度。建议建立校准曲线数据库,便于趋势分析。 二、故障处理:预见性维护的智慧 振动异常诊断 当出现非特征频率振动时,需启动”频谱分层诊断法”: 一级排查:检查联轴器径向跳动(≤0.05mm) 二级检测:主轴轴向窜动量(≤0.02mm) 三级分析:频谱图中1X工频幅值突变可能预示轴承内圈磨损 软件系统维护 建议每季度执行”三备份策略”: 硬盘镜像备份(使用Acronis True Image) 配置参数云端备份 历史数据离线存储(采用LTO-8磁带) 三、安全规范:不可逾越的红线 操作流程控制 严格执行”五步安全法”: ① 设备断电挂牌 ② 残余应力释放(主轴空转3分钟) ③ 防静电手环接地检测 ④ 工具三清点制度 ⑤ 双人互检确认 防护装备升级 建议配置: 防护级安全眼镜(符合ANSI Z87.1-2020) 防静电腕带(电阻值1MΩ±10%) 防穿刺安全鞋(EN ISO 20345:2011 S3级) 四、技术升级:智能化维护新维度 预测性维护系统 部署振动分析模块(如SKF eMotorsense),设置三级预警机制: 黄色预警:振动值超过基准值15% 橙色预警:包络能量突变 红色预警:时域峭度系数>8 数字孪生应用 建立设备数字镜像,实现: 虚拟调试(缩短停机时间40%) 预测性润滑(降低耗油量25%) 故障模式仿真(提升诊断准确率30%) 五、典型案例:维护不当的代价 某汽车零部件厂因忽视主轴预紧力检测,导致: 轴承寿命缩短至标称值的60% 平衡精度从ISO G2.5恶化至G6.3 年度维修成本增加12万元 结语:系统化维护的哲学 真正的设备维护是”技术+管理+人文”的三维工程。建议建立TPM体系,将维护指标纳入KPI考核,同时开展”工匠精神”培训,培养技术人员对设备的敬畏之心。记住:每次精准的平衡调整,都是对机械美学的致敬。
06
2025-06
安全操作规程有哪些具体要求
安全操作规程有哪些具体要求 在精密机械加工领域,动平衡机作为校正旋转体动态平衡的核心设备,其操作规程的严谨性直接关系到设备寿命、生产效率与人员安全。以下从设备状态确认、操作流程规范、环境与防护、应急处理及维护培训五大维度,以高节奏、多维度的视角解析安全操作的核心要求。 一、设备状态确认:从“静态”到“动态”的全周期核查 启动前的“体检” 电源与接地:核查电压稳定性(±5%额定值),接地电阻≤4Ω,避免漏电风险。 机械部件:目视检查传动轴、卡盘及平衡环的磨损情况,异物需用磁吸工具彻底清除。 润滑系统:通过油窗观察油位,若低于1/3刻度线,需补充至2/3并记录更换周期。 动态验证的“隐形规则” 空载试运行:启动后观察转速波动(≤2%额定值),监听轴承区高频啸叫(>8kHz需停机)。 传感器校准:采用标准砝码模拟不平衡量,误差>0.5g需重新标定。 二、操作流程规范:打破“经验主义”的标准化动作 装夹的“黄金三角”原则 对称性:工件重心与主轴中心线偏差≤0.1mm,使用百分表微调。 夹紧力矩:扭矩扳手按说明书设定值±10%施力,过紧易导致轴变形。 平衡基准:标记基准点时,激光笔与工件轴线夹角需<3°,误差累积控制在0.05mm内。 数据采集的“时间窗口” 转速匹配:低惯量工件(<5kg)升速至额定转速的80%后采集,高惯量工件需稳定运行120秒。 多频段分析:对齿轮箱类工件,需同时采集1×、2×、3×转频的振动频谱。 三、环境与防护:构建“五维安全场” 物理隔离的“硬核防御” 防护罩设计:采用透明亚克力板(厚度≥8mm),开合机构需配备机械互锁装置。 声光警示:启动时红色警示灯(≥300流明)与蜂鸣器(90dB)同步触发,持续10秒。 人体工程学的“隐形保护” 操作台高度:符合ISO 7250标准,肘部屈曲角度保持80°-100°。 防静电措施:操作人员需穿戴防静电鞋(电阻值1×10⁶Ω-1×10⁹Ω),工位铺设导电胶垫。 四、应急处理:从“被动响应”到“主动预判” 故障树分析(FTA)的实战应用 异常振动:若振动幅值突增300%,立即执行“三步骤”:断电→泄压→逆向追溯润滑记录。 过热报警:轴承温度>85℃时,需检查冷却水流量(≥5L/min)及散热风扇转速(±5%偏差)。 应急预案的“沙盘推演” 模拟演练:每季度开展“突发停电”场景训练,要求操作员在90秒内完成紧急制动与数据备份。 急救包配置:配备剪切伤专用止血带(压力≥300mmHg)及AED除颤仪(放置于5米可及范围)。 五、维护与培训:构建“知识-技能-责任”的闭环 预防性维护的“时间轴” 月度检查:更换液压油滤芯(β5≥1000),清洁光电传感器镜面(用无纺布蘸异丙醇)。 年度大修:拆解主轴组件,检测圆跳动(≤0.005mm)及热变形量(<0.01mm/℃)。 培训体系的“三维升级” VR模拟:通过虚拟现实技术还原“不平衡量超限”场景,训练决策速度(目标<3秒)。 考核机制:采用OSHA 3012.1标准,理论考试(≥85分)与实操考核(零失误)双达标方可上岗。 结语:安全规程的“进化论” 动平衡机的安全操作并非僵化的条文堆砌,而是融合机械工程、人体工效学与风险管理的动态系统。从传感器的微米级校准到应急预案的秒级响应,每个环节都需以“零缺陷思维”重构操作逻辑。唯有将规程内化为肌肉记忆,方能在精密制造的浪潮中筑牢安全防线。
06
2025-06
安铂ACEPOM便携式动平衡仪售后如···
安铂ACEPOM便携式动平衡仪售后如何? 以技术为锚点,构建全生命周期服务生态 一、服务网络:从”点”到”面”的立体化覆盖 安铂ACEPOM的售后体系摒弃传统”被动响应”模式,通过三级服务网络重构用户体验: 全国核心城市服务站:北京、上海、广州等15个枢纽城市设立24小时技术支援中心,配备原厂认证工程师团队,确保设备故障48小时内得到现场处理。 区域移动服务单元:采用”车载实验室”模式,工程师携带便携式检测设备深入工厂现场,实现设备校准、参数优化等服务的”零距离”交付。 海外技术协作网络:与德国TÜV、美国ASME等机构建立数据互通机制,为跨国企业提供符合当地标准的动平衡解决方案。 二、响应机制:时间维度的精准把控 售后流程的节奏感直接影响客户满意度: 黄金3小时响应圈:通过物联网模块实时监测设备状态,系统自动触发预警机制,工程师在3小时内完成故障预判与备件调配。 远程诊断黑科技:运用AR增强现实技术,客户可通过视频连线指导工程师完成初步故障定位,将平均响应时间缩短至传统模式的1/3。 备件供应链革命:采用区块链技术管理全球备件库存,实现”预测性补货”,关键部件库存周转率提升40%。 三、技术培训:知识传递的多维渗透 售后服务的深层价值在于技术赋能: 阶梯式培训体系 基础层:线上微课(15分钟/节)覆盖设备操作要点 进阶层:线下工作坊(每月1期)解析复杂工况处理方案 专家层:年度技术峰会(邀请行业泰斗)探讨前沿动平衡算法 案例教学法 建立包含2000+真实工况的故障数据库,通过虚拟现实技术还原典型故障场景,让客户在沉浸式体验中掌握诊断逻辑。 四、客户反馈:构建双向价值循环 售后服务不是终点,而是新价值的起点: NPS(净推荐值)驱动改进:每月收集500+用户反馈,运用自然语言处理技术提炼高频痛点,2023年已推动产品迭代3次。 服务产品化创新:将高频服务需求转化为标准化产品包,如”年度预防性维护套餐”包含季度巡检、软件升级等增值服务。 生态化服务联盟:联合设备制造商、高校实验室成立”动平衡技术研究院”,将售后数据反哺产品研发。 五、未来展望:智能服务的无限可能 安铂ACEPOM正以售后为支点撬动行业变革: 数字孪生技术应用:建立设备虚拟镜像,实现故障预测准确率从75%提升至92% AI客服进化:训练行业专属语言模型,2024年目标实现90%常见问题的智能解答 碳中和服务包:推出包含能耗优化、绿色维护方案的ESG增值服务 结语 安铂ACEPOM的售后体系如同精密的动平衡系统——每个环节都经过精心校准,既保持技术参数的精准性,又确保服务节奏的流畅性。这种将工程思维与服务理念深度融合的模式,正在重新定义工业设备售后服务的价值边界。当技术深度与服务温度形成共振,客户收获的不仅是故障排除,更是持续进化的生产力引擎。
06
2025-06
定制与非定制动平衡机区别
定制与非定制动平衡机区别 在动平衡机的领域里,定制与非定制动平衡机有着显著的差异。深入了解这些区别,对于企业选择适合自身需求的设备至关重要。 设计与规格 非定制动平衡机,如同标准化的工业产品,是按照通用的设计和规格进行大规模生产的。它们就像是市场上的“大众款”,具备常见的功能和性能参数,能够满足大多数一般性的动平衡检测需求。其设计注重通用性和普遍性,追求在广泛的应用场景中都能发挥一定的作用。例如,对于一些小型电机、风扇等常见旋转工件的平衡检测,非定制动平衡机可以凭借其标准化的设计,高效地完成任务。 而定制动平衡机则是为特定的用户需求量身打造的“专属品”。它就像是为特定客户定制的高级服装,每一处细节都根据客户的具体要求进行设计。当客户面对特殊形状、特殊尺寸或者特殊材质的工件时,非定制动平衡机可能无法满足检测需求,这时定制动平衡机就派上了用场。比如航空航天领域的一些精密零部件,它们的形状复杂、精度要求极高,定制动平衡机可以根据这些零部件的特点,精确设计检测方案和设备结构,确保能够准确地进行动平衡检测。 性能与精度 非定制动平衡机在性能和精度方面通常保持在一个相对稳定的水平,以适应大多数用户的需求。它们经过了大量的生产和实践验证,具备一定的可靠性和稳定性。然而,由于要兼顾通用性,其性能和精度往往无法达到极致。在一些对平衡精度要求不是特别高的行业,如普通家电制造,非定制动平衡机的性能足以满足生产需求。 定制动平衡机则可以在性能和精度上实现质的飞跃。通过采用先进的技术和特殊的设计,定制动平衡机能够针对特定工件的要求,实现更高的检测精度和更优的性能表现。在高端汽车制造领域,发动机曲轴等关键部件的动平衡精度直接影响到汽车的性能和稳定性。定制动平衡机可以根据发动机曲轴的具体要求,采用高精度的传感器和先进的算法,将平衡精度提高到一个新的高度,从而为汽车的高品质生产提供有力保障。 成本与价格 非定制动平衡机由于采用大规模生产的方式,生产效率高、成本相对较低。这使得它们在价格上具有明显的优势,对于一些预算有限、对设备要求不是特别苛刻的中小企业来说,非定制动平衡机是一个经济实惠的选择。企业可以用相对较少的资金购买到满足基本生产需求的动平衡机,降低了企业的生产成本。 定制动平衡机则需要投入更多的研发、设计和制造资源。从与客户沟通需求、进行方案设计,到零部件的定制加工和设备的调试优化,每一个环节都需要耗费大量的人力、物力和时间。因此,定制动平衡机的成本相对较高,价格也会比非定制动平衡机贵很多。但对于一些大型企业或者对产品质量要求极高的企业来说,为了确保产品的品质和生产效率,他们愿意为定制动平衡机支付更高的价格。 交货周期 非定制动平衡机由于是标准化生产,生产线上有一定的库存,企业可以在较短的时间内完成订单生产和交付。对于那些急需设备投入生产的企业来说,非定制动平衡机的快速交货能力能够满足他们的时间需求,减少了企业的等待时间和生产延误的风险。 定制动平衡机的交货周期则相对较长。从前期的需求沟通、方案设计,到中期的零部件加工和组装,再到后期的调试和测试,每一个环节都需要精心安排和严格把控。而且,定制动平衡机的生产过程中可能会遇到一些技术难题和特殊情况,需要花费额外的时间来解决。因此,企业在选择定制动平衡机时,需要提前做好规划,合理安排生产进度。 综上所述,定制与非定制动平衡机在设计规格、性能精度、成本价格和交货周期等方面都存在明显的区别。企业在选择动平衡机时,应根据自身的实际需求、预算情况和生产计划等因素,综合考虑,权衡利弊,做出最合适的选择。
06
2025-06
定制动平衡机的流程及注意事项
定制动平衡机的流程及注意事项 一、需求解构:从混沌到精准 动平衡机定制如同在精密仪器与工业需求之间架设桥梁,其核心在于将模糊的生产痛点转化为可量化的技术参数。工程师需通过三维度需求解构: 物理属性:转子直径、材质刚性、工作转速区间(如航空发动机叶片需突破10万转/分钟临界点) 功能诉求:是否需兼容柔性轴平衡、支持动态残余振动分析,或集成物联网数据接口 环境约束:海拔气压对真空平衡的影响、防爆认证等级(如ATEX Zone 20) 关键动作:建立需求矩阵表,用FMEA工具预判潜在失效率,例如某风电主轴案例中,因忽略温差形变系数导致初期平衡精度衰减37%。 二、方案设计:在矛盾中寻找平衡 设计阶段犹如在技术迷宫中寻找最优路径,需突破三大矛盾体: 精度与成本:选择电磁驱动还是气浮轴承?前者成本降低40%但需增加15%的后期校准频次 通用性与专用性:模块化设计可覆盖80%常规工况,但特殊转子可能需定制夹具(如某造纸厂卷筒机的非对称配重方案) 智能化边界:AI自适应算法虽能提升30%调试效率,但需额外配置200万级算力芯片 创新实践:某半导体晶圆传输臂项目采用拓扑优化设计,通过ANSYS仿真将机座重量减轻28%而不损失刚性。 三、制造工艺:毫米级误差的博弈 加工环节是物理法则与工程经验的终极考场: 材料基因工程:航空铝材需进行T6热处理,硬度偏差控制在±5HBs 误差链控制:主轴径向跳动≤0.5μm,需采用激光干涉仪进行闭环补偿 表面工程:气浮导轨表面粗糙度Ra≤0.05μm,需进行超精磨+离子镀膜处理 质量黑科技:某高端机型采用蓝光三维扫描,实现0.02mm级形位公差实时监测,较传统卡尺检测效率提升20倍。 四、调试艺术:振动频谱的交响指挥 调试阶段是工程师与机械系统的深度对话: 基准校准:使用激光校准仪建立绝对坐标系,消除地基沉降带来的0.01°倾斜误差 频谱诊断:通过FFT分析识别2阶谐波异常,某案例中发现轴承安装偏心导致的12dB异常峰值 自学习算法:采用遗传算法优化配重方案,使平衡时间从传统45分钟缩短至8分钟 行业痛点:某高速电机测试中,因未考虑电磁力矩耦合,导致初期平衡后振动值反而升高15%。 五、交付生态:从设备到解决方案 现代动平衡机交付已演变为工业服务生态: 数字孪生:交付包含设备数字镜像,支持远程故障诊断与预测性维护 知识转移:提供ISO 1940-1标准培训,某汽车涡轮增压器产线因此将平衡良率从89%提升至97% 持续进化:预留5G模块接口,支持未来接入工业4.0平台 典型案例:某航天推进器叶轮平衡项目,通过定制化软件包实现残余不平衡量从ISO G2.5跃升至G0.4。 风险控制矩阵 风险维度 预防策略 应急方案 材料疲劳 采用S-N曲线寿命预测 预置冗余配重块 环境干扰 安装主动隔振平台 配置振动屏蔽罩 误操作 开发AR辅助校准系统 设置三重安全联锁 终极法则:在定制过程中,每降低1%的平衡精度,可能带来10%的设备寿命损耗,但需权衡0.5%的成本增幅。真正的平衡艺术,在于找到技术、经济与安全的黄金分割点。
06
2025-06
定制动平衡机精度要求是什么
定制动平衡机精度要求是什么 在工业生产中,动平衡机的重要性不言而喻。它能有效减少设备振动、降低噪声、延长使用寿命,而定制动平衡机时,精度要求更是关键所在。那么,定制动平衡机的精度要求究竟包含哪些方面呢? 不平衡量减少率 不平衡量减少率是衡量动平衡机精度的重要指标之一。它指的是经过一次平衡校正后,工件剩余不平衡量与初始不平衡量的比值。通常,不平衡量减少率越高,说明动平衡机的精度越好。对于一些高精度要求的行业,如航空航天、精密仪器制造等,不平衡量减少率可能需要达到 90% 以上;而对于一般工业应用,该指标达到 80% - 90% 也能满足生产需求。这一指标直接影响着工件的平衡效果,若不平衡量减少率不达标,工件在运行过程中仍会产生较大的振动和噪声,影响设备的性能和稳定性。 最小可达剩余不平衡量 最小可达剩余不平衡量体现了动平衡机能够达到的最高精度水平。它表示在理想条件下,动平衡机对工件进行平衡校正后,工件所剩余的最小不平衡量。这个数值越小,说明动平衡机的精度越高。不同类型的动平衡机,其最小可达剩余不平衡量有所差异。例如,用于小型、高精度零部件的动平衡机,最小可达剩余不平衡量可能在毫克甚至微克级别;而对于大型旋转机械的动平衡机,该数值可能在克级别。这一指标对于那些对平衡精度要求极高的场合至关重要,如高速旋转的航空发动机叶片、高精度机床主轴等。 转速精度 动平衡机在工作时,转速的稳定性和准确性对平衡精度有着重要影响。转速精度指的是动平衡机实际工作转速与设定转速的符合程度。一般来说,转速误差应控制在较小范围内,通常要求转速精度在± 0.1% - ± 1% 之间。如果转速精度不高,会导致不平衡量的测量出现偏差,进而影响平衡校正的效果。例如,在对高速旋转的工件进行平衡时,转速的微小波动可能会使测量得到的不平衡量产生较大误差,使得平衡校正后的工件仍然存在较大的不平衡问题。 角度精度 角度精度是指动平衡机确定不平衡量位置的准确程度。在动平衡校正过程中,不仅要知道不平衡量的大小,还需要准确确定其位置,以便进行精确的校正。角度精度通常以度为单位,一般要求角度误差在± 1° - ± 5° 之间。对于一些对角度精度要求极高的应用,如多缸发动机曲轴的平衡,角度误差需要控制在更小的范围内。角度精度的高低直接关系到平衡校正的准确性,如果角度测量不准确,即使不平衡量的大小测量正确,也无法有效地进行平衡校正,从而影响工件的平衡性能。 定制动平衡机时,需要综合考虑不平衡量减少率、最小可达剩余不平衡量、转速精度和角度精度等多个精度要求。只有确保这些精度指标都能满足生产需求,才能定制出符合要求的动平衡机,为工业生产提供可靠的平衡保障。
06
2025-06
定制动平衡机需要注意哪些问题
定制动平衡机需要注意哪些问题 (以高多样性与节奏感呈现的结构化论述) 一、应用领域适配性:从微观振动到宏观载荷的精准匹配 定制动平衡机的核心在于需求分析。航空航天领域需应对高速旋转部件的微米级振动控制,而重型机械制造则需承受吨级载荷的动态平衡。需明确以下维度: 工件特性:材质刚性、几何复杂度(如叶片涡轮的非对称结构)、温变环境下的热膨胀系数。 行业标准:ISO 1940-1的平衡品质等级、API 617对离心压缩机的特殊要求。 场景延伸:是否需兼容多规格工件?例如汽车生产线的发动机与变速箱模块切换需求。 案例:某风电企业定制机需同时处理2米直径叶片(低转速高精度)与500kg齿轮箱(高载荷抗冲击),需采用模块化夹具与可变阻尼系统。 二、精度等级选择:动态平衡与静态平衡的博弈 精度并非越高越好,需结合成本与工况: 静态平衡(单平面):适用于轴向长度较短的工件(如飞轮),成本降低30%但需牺牲部分高频振动抑制能力。 动态平衡(双平面):应对长径比>0.2的转子(如直升机旋翼),需配置激光传感器与实时频谱分析模块。 误差链控制:轴承游隙、驱动电机谐波、环境振动干扰的叠加效应需通过FEM仿真预判。 技术突破:引入AI算法优化平衡基准点,将传统试重法的3次迭代缩短至1.5次。 三、载荷能力与刚度的非线性关系 过载设计需规避“安全冗余陷阱”: 静载荷 vs 动载荷:液压加载系统的峰值压力需覆盖工件运行时的离心力(公式:F_c = mω²r)。 结构刚度:底座材料从铸铁升级为铝合金+碳纤维复合结构,可减重40%但需补偿谐振频率偏移。 极端工况模拟:军工领域需模拟-55℃至200℃的温差冲击,需集成温控系统与热变形补偿机构。 数据支撑:某定制机通过拓扑优化将刚度提升22%,同时降低能耗18%。 四、安装环境与扩展性的隐形变量 空间拓扑:地面平整度误差>0.5mm/m会导致基础共振,需配备主动隔振平台。 人机交互:操作界面需适配不同熟练度的使用者,例如增设AR辅助校准模块。 未来兼容性:预留IO接口以支持IoT远程诊断,或升级为自动化产线的平衡站节点。 创新设计:某实验室定制机采用磁悬浮转台,消除机械接触带来的干扰误差。 五、全生命周期成本的隐性账本 维护成本:选择免维护轴承可降低年均运维费用25%,但初期投入增加15%。 耗材管理:激光测振仪的校准周期与传感器探头的损耗率需纳入TCO计算。 培训成本:提供虚拟现实(VR)模拟操作课程,缩短新人上岗时间50%。 决策模型:通过蒙特卡洛模拟预测5年内的故障率与维修支出,优化配置方案。 结语:从“参数堆砌”到“系统思维”的跃迁 定制动平衡机的本质是多目标优化问题,需在精度、成本、效率间找到动态平衡点。未来的趋势将围绕智能化自适应平衡展开——通过数字孪生技术实时映射工况,实现从“被动修正”到“主动预测”的范式变革。 (全文通过长短句交错、术语与类比结合、数据与场景穿插,兼顾专业深度与阅读节奏)
06
2025-06
定制化动平衡机厂家能满足哪些特殊需求
定制化动平衡机厂家能满足哪些特殊需求? 一、行业需求的精准适配 航空航天领域对转子系统平衡精度要求突破0.1g·mm时,定制化动平衡机厂商会采用激光干涉仪与空气轴承组合方案,将检测灵敏度提升至纳米级波动范围。针对新能源汽车电机转子的批量检测需求,厂商开发出集成视觉定位系统的全自动平衡机,通过机器学习算法将单件检测时间压缩至45秒内。在船舶推进系统领域,为应对深海作业的振动隔离难题,厂商创新设计出水冷式平衡机基座,可在-30℃至120℃温度区间保持刚性结构稳定。 二、技术参数的极限突破 当传统动平衡机无法满足磁悬浮列车轮对的20000r/min超高速平衡需求时,定制化方案引入碳纤维增强型平衡头,配合电磁悬浮驱动系统,成功将转速上限提升至35000r/min。在半导体晶圆切割机领域,厂商开发出亚微米级不平衡量检测模块,通过压电陶瓷传感器阵列实现0.01μm的位移分辨率。针对核工业离心机的高辐射环境,定制化设备采用钛合金防护舱与光纤传输系统,确保在1000Gy辐射剂量下仍保持数据采集精度。 三、特殊功能的模块化拓展 针对风力发电叶片的现场平衡需求,厂商推出可拆卸式平衡机系统,通过模块化设计将设备运输体积缩减60%,同时配备无线数据传输模块与太阳能供电系统。在医疗器械领域,为满足手术机器人关节的无菌环境要求,定制化设备采用医用级316L不锈钢腔体,配合HEPA过滤系统实现ISO Class 5洁净度。针对印刷机械的多品种转子适配需求,厂商开发出智能夹具库系统,支持30秒内自动切换不同规格的卡盘结构。 四、服务模式的深度定制 在军工装备领域,定制化厂商提供全生命周期数据追溯服务,通过区块链技术记录每次平衡操作的工艺参数,生成符合GJB9001C标准的电子履历文件。针对科研机构的特殊需求,厂商开放设备底层控制代码,允许客户自主编写平衡算法并集成至LabVIEW平台。在售后服务环节,采用AR远程指导系统,工程师可实时标注设备故障点,将平均响应时间缩短至2.3小时。 五、未来趋势的前瞻性布局 随着工业4.0的推进,定制化厂商正在研发数字孪生平衡系统,通过虚拟仿真平台预演不同工况下的平衡效果,将物理样机试制次数减少40%。在人工智能领域,厂商训练出基于深度学习的不平衡故障诊断模型,可提前12小时预警潜在动平衡失效风险。针对碳中和目标,新一代定制化设备采用再生制动能量回收系统,使单位平衡能耗降低至0.8kWh/kg,远超欧盟ErP指令的能效标准。 这种多维度的定制化服务能力,不仅体现在技术参数的突破性创新,更在于对行业痛点的深度解构与重构。从微观的纳米级精度控制到宏观的系统集成方案,定制化动平衡机厂商正通过技术创新与模式变革,重新定义精密制造领域的平衡标准。
06
2025-06
定制化平衡机生产厂家怎么选
定制化平衡机生产厂家怎么选?五维决策模型深度解析 一、技术基因解码:穿透表象的技术穿透力 (1)研发矩阵评估法 查验企业近3年专利布局图谱,重点分析动态平衡算法、传感器融合技术等核心模块 要求提供ISO 1940-1国际平衡标准认证文件 实地考察三坐标测量机精度(建议≥0.001mm) (2)制造工艺光谱分析 采用X射线衍射仪检测关键部件晶格结构 要求提供热处理工艺曲线(建议淬火温度误差±3℃) 检查动平衡机转子动频特性测试报告 (3)智能诊断系统验证 模拟突发振动故障场景测试响应速度 要求演示AI预测性维护算法模型 检查工业物联网数据采集频率(建议≥10kHz) 二、定制化能力矩阵:需求适配的多维建模 (1)模块化设计架构 要求提供可重构平衡机平台技术白皮书 检查快速换型系统切换时间(理想值≤15分钟) 验证多轴同步控制精度(建议±0.01°) (2)参数柔性调节 测试不平衡量检测范围(建议0.1g·mm至10000g·mm) 验证转速调节步长(理想值0.1rpm) 检查环境自适应能力(温度范围-20℃至60℃) (3)行业场景适配 要求提供航空航天级平衡案例(转速≥100000rpm) 查看新能源汽车电机平衡解决方案库 检查精密仪器平衡误差补偿方案 三、服务生态构建:全生命周期价值网络 (1)技术赋能体系 要求提供平衡工艺仿真软件使用权 检查FMEA失效模式数据库更新频率 验证数字孪生系统实时性(延迟≤50ms) (2)响应机制评估 测试48小时应急服务响应协议 查看全球备件库存分布图 模拟跨国技术支援场景 (3)知识转移机制 要求提供平衡工艺工程师认证课程 检查设备操作VR培训系统 查看工艺参数知识图谱 四、成本效益建模:价值创造的动态平衡 (1)TCO全要素分析 建立5年期总拥有成本模型 计算能耗系数(建议≤0.3kW·h/kg) 评估维护成本衰减曲线 (2)ROI动态测算 构建平衡效率提升收益模型 计算次品率下降带来的质量成本节约 评估设备利用率提升空间 (3)技术冗余价值 评估模块扩展接口数量 计算未来3年技术升级成本 分析兼容性扩展潜力 五、行业生态位评估:竞争格局的穿透洞察 (1)技术路线图对比 分析企业研发投入强度(建议≥8%) 绘制技术专利引用网络图 评估标准制定参与度 (2)供应链韧性测试 检查关键元器件双源供应方案 评估物流网络响应速度 查看供应商质量管理体系认证 (3)生态位价值评估 分析客户行业分布熵值 计算技术扩散系数 评估生态合作伙伴网络密度 决策工具箱 技术成熟度评估矩阵(TMA) 定制化能力雷达图 服务响应时间-质量双维度坐标系 成本效益帕累托前沿分析 行业生态位SWOT-CLPV模型 选择定制化平衡机生产商的本质,是构建动态技术适配系统。建议采用”技术基因检测+场景化验证+生态价值评估”三维决策框架,重点关注企业技术迭代速率与客户需求变化的相关系数,建立动态评估机制,实现从静态采购到持续价值共创的范式转变。