

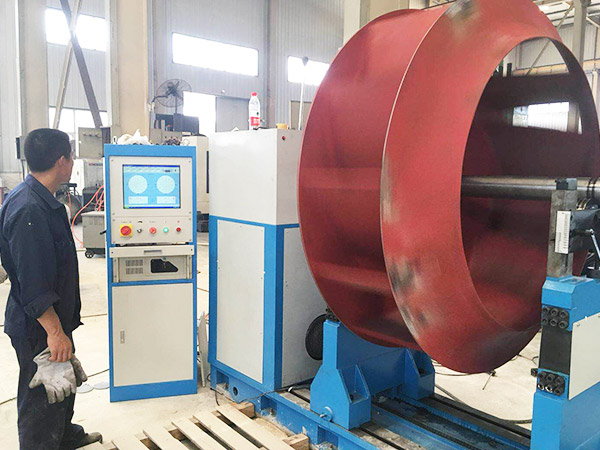
风机叶轮动平衡标准值是多少
风机叶轮的动平衡标准值会因不同的应用、设计要求和行业标准而有所不同。一般来说,动平衡标准值取决于以下几个因素:应用类型: 不同类型的风机在不同的应用环境下需要满足不同的动平衡标准。例如,一般的工业风机和空调风机的要求可能会不同。运行速度: 风机叶轮的运行速度会直接影响不平衡对振动的影响。高速运行的叶轮可能需要更严格的动平衡标准。精度要求: 一些应用对振动的容忍度比较低,因此对动平衡的要求也会更为严格。行业标准: 不同行业可能有各自的标准和规范,这些标准通常会提供关于动平衡的指导和要求。一般来说,在工业领域,风机叶轮的动平衡标准值通常以单位质量不平衡量(g.mm/kg 或 g.cm/kg)来表示。具体的标准值可能会因不同情况而有所不同,但以下是一个大致的参考范围:对于一般工业风机,通常的动平衡标准值可能在 1 g.mm/kg 至 10 g.mm/kg 之间。对于某些精密应用,要求更高的风机,动平衡标准值可能在 0.5 g.mm/kg 以下。请注意,这只是一个粗略的参考范围,实际应用中应该根据具体情况和适用的行业标准来确定风机叶轮的动平衡标准值。在进行动平衡操作时,建议遵循相关的国家和行业标准,以确保风机在运行过程中达到合适的振动水平。
07
2025-06
叶轮动平衡机常见故障解决方法
叶轮动平衡机常见故障解决方法 叶轮动平衡机在工业生产中扮演着重要角色,它能确保叶轮的平稳运行,提高设备的性能和寿命。然而,在使用过程中,动平衡机难免会出现一些故障。下面就为大家介绍一些常见故障及其解决方法。 振动异常 叶轮动平衡机在运行时振动异常是较为常见的故障。有时振动幅度突然增大,可能是因为叶轮上有异物附着。叶轮在高速旋转时,若有杂物粘附,会破坏原本的平衡状态,导致振动加剧。解决办法很简单,只需停机后仔细检查叶轮,清除上面的异物。 但如果不是异物问题,那可能是支撑系统出现了松动。动平衡机的支撑结构在长期使用后,螺丝等连接件可能会松动,使支撑不稳定,从而引发振动。这时就需要对支撑系统进行全面检查,拧紧松动的螺丝,确保支撑稳固。还有一种可能是传感器出现了故障,传感器不能准确地检测到叶轮的振动信息,也会让机器表现出振动异常。此时要对传感器进行校准或更换。 测量精度下降 测量精度是动平衡机的关键性能指标。当发现测量结果不准确时,首先要考虑的是标准件的问题。标准件如果在使用过程中受到磨损或损坏,就无法提供准确的参考,导致测量精度下降。我们需要定期检查标准件的状态,如有问题及时更换。 测量环境也会对精度产生影响。如果周围存在强烈的电磁干扰,会干扰动平衡机的测量信号,使测量结果出现偏差。可以采取屏蔽措施,如安装电磁屏蔽罩,减少外界电磁干扰。另外,动平衡机的软件系统也可能出现故障,软件中的参数设置错误或者程序出现漏洞,都会影响测量精度。这时要对软件进行重新设置和调试,或者更新软件版本。 显示异常 动平衡机的显示屏如果出现显示模糊、闪烁或者显示错误数据的情况,要先检查电源供应。电源不稳定,电压忽高忽低,会影响显示屏的正常工作。可以使用稳压器来保证电源的稳定输出。 显示屏的连接线也可能是问题所在。连接线在长期使用后可能会出现松动、断裂等情况,导致信号传输不畅。仔细检查连接线,确保连接牢固,如果有损坏及时更换。还有就是显示屏本身可能出现了故障,比如内部的电路损坏或者显示芯片出现问题。这种情况下,只能联系专业的维修人员对显示屏进行维修或更换。 驱动系统故障 驱动系统是动平衡机带动叶轮旋转的关键部分。如果驱动电机出现异常噪音,可能是电机的轴承磨损了。轴承磨损后,运转时会产生摩擦噪音,需要及时更换轴承。 传动皮带也是容易出问题的部件。皮带使用时间长了会出现松弛、老化等情况,导致传动效率下降,叶轮转速不稳定。这时要调整皮带的张紧度,或者更换新的皮带。另外,驱动系统的控制电路如果出现故障,也会影响电机的正常运行,需要专业人员对控制电路进行检修。 叶轮动平衡机在使用过程中出现故障是不可避免的,但只要我们了解常见故障的原因,并掌握相应的解决方法,就能及时排除故障,保证动平衡机的正常运行,提高生产效率和产品质量。在遇到复杂故障时,还是要及时联系专业的维修人员,避免自行维修造成更大的损坏。
07
2025-06
叶轮动平衡机操作步骤有哪些
叶轮动平衡机操作步骤有哪些 一、精密起航:操作前的系统准备 设备状态核查 如同外科手术前的器械检查,操作者需逐项确认动平衡机的传感器灵敏度、驱动电机转速稳定性及数据采集系统的实时性。重点检查振动传感器与相位探头的校准证书是否在有效期内,避免因微小误差导致平衡精度偏离。 叶轮预处理 将待测叶轮置于恒温车间静置2小时,消除铸造应力残留。使用游标卡尺测量叶轮直径公差(需控制在±0.05mm),并用工业酒精擦拭平衡面,确保无油脂残留。此阶段需配合磁粉探伤仪排查隐性裂纹,防止测试过程中突发断裂。 二、动态交响曲:核心操作流程 安装与定位艺术 采用三点浮动支撑架将叶轮水平嵌入主轴,通过百分表校正径向跳动(≤0.03mm)。此时需注意: 配重块焊接面需避开叶轮流道区域,防止热影响区变形 专用卡盘夹持力度通过扭矩扳手控制(建议20-25N·m) 启动低速空转(300rpm)观察轴承座振动趋势,确认无异常啸叫。 智能采集与频谱分析 开启频谱分析仪,设置采样频率为叶轮最高转速的2.56倍(如10000rpm对应270kHz)。重点捕捉: 基频振动幅值(需低于设备标称精度0.1mm) 轴向振动与径向振动的相位差(通过Lissajous图形判断) 通过幅值-相位曲线生成初始不平衡量矢量图,系统自动计算理论配重值。 三、平衡精度跃迁:动态修正阶段 配重优化策略 根据矢量图选择配重方式: 单面平衡:适用于刚性叶轮(不平衡量≤50g·mm) 双面平衡:针对柔性叶轮采用迭代算法(需设置阻尼系数0.05-0.15) 焊接配重块时使用脉冲式MIG焊机,单次焊接时间控制在3秒内,避免局部过热变形。 多级复测验证 完成配重后执行三级验证: 初测:8000rpm下振动值≤0.08mm 强化测试:12000rpm持续10分钟 极限测试:15000rpm短时冲击(需配备应急制动系统) 通过ISO 1940-1标准计算剩余不平衡量,确保G6.3等级达标。 四、闭环管理:收尾与数据沉淀 智能诊断与归档 将测试数据导入平衡机内置数据库,自动生成包含: 平衡前后振动频谱对比图 配重位置三维坐标云图 设备健康状态评估报告(轴承磨损指数≤15%) 通过OPC协议上传MES系统,实现生产过程的数字化追溯。 预防性维护 每完成50次测试后执行: 激光对中仪校正主轴同心度(偏差≤0.02mm) 更换液压系统精密滤芯(过滤精度5μm) 使用超声波清洗剂清洁传感器探头 五、技术进阶:特殊场景应对 高温叶轮平衡方案 在燃气轮机叶片测试中,采用: 红外测温仪实时监控叶轮温度(需保持±2℃稳定性) 石墨烯涂层传感器耐受800℃环境 动态补偿算法修正热膨胀系数(α=12×10⁻⁶/℃) 复杂结构叶轮创新方案 针对航空发动机变几何导叶,开发: 多自由度柔性夹具系统 基于有限元分析的虚拟配重模型 5G远程专家诊断平台 通过上述10个维度的操作体系,叶轮动平衡机不仅能实现ISO 21940-6标准要求,更能在航空、能源等高精尖领域突破传统平衡极限。操作者需在严谨流程中融入工程直觉,方能在0.01mm的精度世界里,奏响机械平衡的完美乐章。
07
2025-06
叶轮动平衡机是否需要专业培训
叶轮动平衡机是否需要专业培训? 技术原理与操作风险的博弈 在精密制造领域,叶轮动平衡机如同外科手术刀般存在——它既能精准修正旋转体的振动误差,也可能因误操作引发价值百万的设备报废。当工程师将转子装夹在机座上时,看似简单的校准动作背后,实则暗藏着流体力学、材料力学与控制理论的三重博弈。某航空发动机厂曾因操作员误判相位角,导致价值380万元的钛合金叶轮报废,这个案例揭示了一个残酷现实:动平衡机的”友好界面”往往掩盖着致命的技术陷阱。 行业规范与法律红线的双重约束 ISO 1940-1标准对动平衡精度的分级要求,犹如悬在操作者头顶的达摩克利斯之剑。2022年欧盟机械指令更新后,未持证操作动平衡机的企业面临最高200万欧元的行政处罚。某汽车零部件供应商因使用未经培训的实习生操作设备,导致批量涡轮增压器振动超标,最终被勒令召回12万件产品。这些血淋淋的教训印证:专业培训已从企业成本转化为法律义务。 认知维度的多层跨越 真正的动平衡机操作者需要完成三个认知跃迁:从机械传动的物理感知,到频谱分析的数字解码,最终抵达故障诊断的预见性思维。某核电设备制造商的培训日志显示,新员工平均需要经历178小时的沉浸式训练,才能准确识别0.1mm级的不平衡量差异。这种能力的形成,本质上是将抽象的傅里叶变换转化为肌肉记忆的过程。 培训体系的生态重构 现代动平衡机培训已突破传统师徒制框架,形成”三维能力矩阵”:理论模块涵盖旋转机械动力学方程推导,实操模块包含虚拟现实故障模拟,管理模块则涉及ISO 55000资产管理标准。某高端装备制造企业开发的AR培训系统,能实时捕捉操作者的手部动作轨迹,将装夹误差控制在±0.05mm精度范围内。 技术迭代催生的新型能力需求 随着AI驱动型动平衡机的普及,操作者需要掌握机器学习模型的再训练能力。某风电企业最新引进的智能平衡系统,要求操作员具备Python脚本编写基础,以便对自适应算法进行参数优化。这种技术融合趋势,使得专业培训从”技能传授”升级为”认知革命”。 当动平衡机的触摸屏逐渐取代传统旋钮时,我们更需要清醒认识到:设备智能化的终极目标,是培养出能驾驭复杂系统的”人机共生体”。那些在培训中磨砺出的精密思维与风险预判能力,终将成为制造业转型升级中最坚韧的锚点。
07
2025-06
叶轮动平衡机校正周期多久一次
叶轮动平衡机校正周期多久一次? 一场关于精密与风险的博弈 一、校正周期的决定性因素 叶轮动平衡机的校正周期并非固定数值,而是由工况复杂性、设备特性、行业标准三者交织而成的动态方程式。 工况复杂性:在航空发动机领域,叶片每分钟数万次的高频振动叠加高温高压环境,可能迫使校正周期压缩至100小时;而污水处理厂的离心机若运行平稳,周期可延长至5000小时。 设备特性:精密仪器级动平衡机(如激光对刀型)因传感器灵敏度极高,建议每完成100次校正即自检;而基础型机械式设备则依赖累计运行时间而非次数。 行业标准:ISO 1940-1规定关键旋转部件需在振动幅值超过0.7mm/s²时强制校正,而API 617针对石化泵则要求每季度进行预防性校验。 二、周期优化的三大策略 数据驱动型决策正在颠覆传统经验主义: 振动频谱分析 通过FFT变换捕捉基频谐波畸变率,当1X频率幅值占比低于85%时,预示动平衡失效风险。某风电企业据此将校正周期从6个月调整为按功率波动阈值触发,故障率下降40%。 数字孪生模拟 德国Fraunhofer研究所开发的虚拟叶轮模型,可输入材料疲劳系数、轴承磨损速率等参数,实时推演最佳校正窗口。某航空企业应用后,维护成本降低27%。 预测性维护协议 结合剩余使用寿命(RUL)算法与企业生产计划,实现校正时间的弹性安排。例如半导体真空泵在晶圆批次间隙自动触发校正,避免停机损失。 三、周期延长的代价与边界 盲目延长校正周期可能引发指数级风险放大: 微观裂纹效应:未及时校正的不平衡力矩,会使叶轮应力集中区的裂纹扩展速度提升3-5倍(Paris公式验证)。 多米诺式失效:某化工厂因延迟校正导致密封环磨损,最终引发轴系对中偏移-轴承过热-润滑失效的连锁反应,维修成本超周期成本的20倍。 合规性风险:欧盟CE认证要求关键设备校正记录可追溯,某企业因未留存校正数据遭30万欧元罚款。 四、行业实践的启示 航空领域:采用双冗余校正系统,主设备运行时备用机同步校正,实现”零停机”。 汽车制造:特斯拉将动平衡机与扭矩传感器联动,当电机输出波动超过0.3%立即触发校正。 科研机构:中科院某实验室通过纳米级激光修整技术,将校正周期从周级提升至年级。 五、未来趋势:自适应校正系统 MIT最新研究显示,集成压电材料主动平衡与AI动态补偿的第四代动平衡机,可使校正周期无限趋近于”永久”。其核心在于: 实时力矩反馈:通过压电陶瓷片微秒级形变抵消不平衡力。 机器学习预测:基于历史振动数据构建故障概率模型,提前12小时预警。 边缘计算优化:在设备本地完成校正方案生成,避免云端延迟。 结语:在确定性与不确定性之间 校正周期本质上是技术可靠性、经济性、安全阈值的三角平衡。当某核电站将校正周期从3个月延长至12个月时,其决策模型中竟包含27个变量因子——这或许揭示了一个真理:在精密机械领域,真正的专业主义,永远在数据与直觉的灰度地带游走。
07
2025-06
叶轮动平衡机正确操作步骤
【叶轮动平衡机正确操作步骤】 当精密的金属叶片在高速旋转中产生共振,工程师们需要以毫米级的精度驯服这股无形的离心力。叶轮动平衡机作为工业心脏的”听诊器”,其操作艺术融合了机械工程的严谨与动态控制的智慧。让我们以手术刀般的精准,解剖这场平衡术的每一个关键节点。 一、环境预处理:构建精密测量的真空场 在启动设备前,操作者需化身环境工程师:核查实验室温湿度波动是否控制在±2℃/±5%RH的苛刻范围内,用激光尘埃粒子计数器扫除空气中直径≥0.5μm的颗粒物。特别注意电磁干扰源的隔离——邻近变频器产生的谐波可能让传感器误判为转子振动。此时,操作台前的工程师如同交响乐团指挥,正为这场精密测量奏响序章。 二、装夹艺术:机械与流体的共舞 将叶轮嵌入卡盘时,需遵循”三点定位法则”:主轴端面、径向卡爪、轴向定位销构成黄金三角。当使用液压夹具时,压力曲线应呈现标准的正弦波形,过载保护阀的泄压值需精确匹配叶轮材料的屈服强度。特别在安装航空涡轮叶片时,需采用柔性支撑结构,模拟真实气流环境下的受力状态。此时,操作界面的扭矩监测曲线犹如心电图,记录着机械与流体的微妙对话。 三、动态校准:数字世界的标定哲学 启动校准程序前,工程师要执行”三步验证法”:首先用标准试重块验证传感器的线性度,接着通过傅里叶变换算法解析频谱特征,最后用激光干涉仪比对机械传动链的累积误差。当显示屏上的相位角波动小于0.5°时,系统才获得”数字准生证”。这个过程如同为精密仪器安装认知框架,确保每个数据点都经过哲学层面的逻辑自洽。 四、平衡迭代:振动方程的求解之旅 当叶轮达到额定转速(通常为工作转速的70-90%),数据采集系统会捕获每秒10000次的振动采样。工程师需要同时解读频谱图中的基频、二阶谐波及边带成分,运用最小二乘法计算最优配重方案。在航空发动机叶片的平衡中,甚至需要引入有限元分析模型,将配重调整转化为偏微分方程的数值求解。此时,操作界面的三维振型动画,正演绎着振动能量的拓扑优化过程。 五、误差溯源:平衡精度的量子纠缠 当残余不平衡量仍高于ISO 1940标准时,工程师需启动”故障树分析”:检查轴系支撑刚度是否达到理论值的98%以上,验证转速传感器的脉冲信号是否与实际转速保持1:1相位锁定。在极端案例中,可能需要采用磁悬浮技术消除轴承摩擦带来的测量偏差。这种对误差根源的穷尽式追寻,犹如量子物理学家在寻找波函数坍缩的真正诱因。 六、数字孪生:平衡数据的时空折叠 每完成一次平衡操作,系统会自动生成包含200+参数的数字指纹:从原始振动频谱到最终配重矢量,从环境参数到设备状态码。这些数据将被注入工业物联网平台,通过机器学习模型预测未来1000小时的平衡衰减趋势。当某台风机在服役中出现异常振动时,工程师可调取其数字孪生体,进行虚拟故障注入实验。 这场平衡术的终章,不在于消除最后一丝振动,而在于理解不平衡量与系统可靠性的动态博弈。当叶轮在临界转速区间平稳穿越,当频谱图中高频谐波悄然退场,工程师们知道——他们不仅平衡了机械,更重构了能量在时空中的分布法则。
07
2025-06
叶轮动平衡机等级标准是什么
叶轮动平衡机等级标准是什么 在工业生产中,叶轮的动平衡至关重要,它直接影响到设备的性能、稳定性和使用寿命。叶轮动平衡机就是用于检测和校正叶轮动平衡的关键设备,而其等级标准对于保证动平衡机的质量和性能起着决定性作用。那么,叶轮动平衡机的等级标准究竟是什么呢? 精度等级标准 精度是衡量叶轮动平衡机性能的核心指标之一。国际上通常采用G等级来表示平衡精度,这个等级是根据转子的质量、转速以及允许的剩余不平衡量等因素综合确定的。例如,G0.4 等级代表了极高的平衡精度,适用于高精度的涡轮发动机叶轮等设备;而 G6.3 等级的精度相对较低,常用于一般的工业风机叶轮。不同的精度等级对应着不同的应用场景,用户需要根据叶轮的具体使用要求来选择合适精度等级的动平衡机。精度等级的确定不仅关系到叶轮在运行过程中的平稳性,还会影响到设备的振动、噪音水平以及能源消耗。高精度的动平衡机可以有效降低叶轮的振动和噪音,提高设备的运行效率,延长设备的使用寿命。 测量系统等级标准 测量系统是叶轮动平衡机的“眼睛”,其准确性和可靠性直接影响到动平衡的效果。测量系统的等级标准主要包括测量的分辨率、重复性和线性度等方面。分辨率高的测量系统能够检测到微小的不平衡量,从而实现更精确的平衡校正;重复性好则意味着在多次测量同一叶轮时,测量结果的一致性高,保证了测量的可靠性;线性度高则可以确保测量结果与实际不平衡量之间呈线性关系,便于准确计算和校正。先进的测量系统通常采用高精度的传感器和先进的信号处理技术,能够实时、准确地测量叶轮的不平衡量,并将测量结果反馈给控制系统,以便进行精确的校正。 校正能力等级标准 校正能力是指动平衡机能够校正的最大不平衡量和最小不平衡量的范围。不同的叶轮由于尺寸、质量和工作条件的不同,其所需的校正能力也有所差异。校正能力等级标准通常根据动平衡机的结构设计、驱动系统和校正装置的性能来确定。大型的叶轮可能需要具有较大校正能力的动平衡机,而小型的叶轮则可以选择校正能力相对较小的设备。校正能力不仅包括能够去除的不平衡量的大小,还包括校正的方式和效率。常见的校正方式有去重法和加重法,动平衡机需要根据叶轮的具体情况选择合适的校正方式,并能够快速、准确地完成校正过程,以提高生产效率。 可靠性和稳定性等级标准 在工业生产中,动平衡机需要长时间连续运行,因此其可靠性和稳定性至关重要。可靠性和稳定性等级标准主要体现在设备的故障率、平均无故障工作时间和维护保养的难易程度等方面。低故障率和长平均无故障工作时间意味着动平衡机在运行过程中更加可靠,能够减少因设备故障而导致的生产中断;易于维护保养则可以降低设备的使用成本和维护难度。优质的动平衡机通常采用高质量的零部件和先进的制造工艺,具有良好的可靠性和稳定性,能够在复杂的工业环境下稳定运行。 叶轮动平衡机的等级标准是一个综合性的体系,涵盖了精度、测量系统、校正能力以及可靠性和稳定性等多个方面。用户在选择叶轮动平衡机时,需要根据叶轮的具体要求和应用场景,综合考虑这些等级标准,以选择最适合的动平衡机,从而保证叶轮的动平衡质量,提高设备的性能和可靠性。随着工业技术的不断发展,叶轮动平衡机的等级标准也在不断更新和完善,以适应更高的生产要求和更复杂的应用场景。
07
2025-06
叶轮动平衡机精度影响因素有哪些
叶轮动平衡机精度影响因素有哪些 在工业生产中,叶轮动平衡机对于确保叶轮平稳运行至关重要。然而,其精度会受到多种因素的影响。了解这些影响因素,有助于更好地使用和维护动平衡机,提高生产质量。 机械结构因素 机械结构是动平衡机的基础,其设计和制造质量对精度影响显著。动平衡机的摆架系统如果刚度不足,在高速旋转时就容易产生变形,导致测量结果不准确。摆架的制造工艺也至关重要,若加工精度不高,各部件之间的配合存在间隙或偏差,会直接影响叶轮的旋转稳定性。比如,摆架的导轨如果直线度不够,叶轮在旋转过程中就会出现晃动,使得测量数据产生较大误差。 此外,动平衡机的支承系统也不容忽视。支承的形式和安装方式会影响叶轮的定位精度。如果支承与叶轮的接触不良,或者支承的刚度不均匀,都会导致叶轮在旋转时产生额外的振动,从而干扰测量结果。一些低质量的支承可能会在长时间使用后出现磨损,进一步降低动平衡机的精度。 传感器性能因素 传感器是动平衡机获取数据的关键部件,其性能直接决定了测量的准确性。传感器的灵敏度和线性度是重要的指标。灵敏度不足,可能无法准确检测到叶轮的微小振动,导致测量结果存在偏差。而线性度不好,则会使测量数据与实际振动情况之间出现非线性关系,影响后续的计算和分析。 传感器的抗干扰能力也很关键。在工业生产环境中,存在着各种电磁干扰和机械振动干扰。如果传感器的抗干扰能力不强,就容易受到外界干扰信号的影响,产生虚假的测量数据。另外,传感器的安装位置和方式也会对测量精度产生影响。安装位置不准确,可能无法准确测量到叶轮的主要振动方向,而安装方式不当则可能导致传感器与叶轮之间的耦合不良,影响测量效果。 测量系统算法因素 测量系统的算法是对传感器采集到的数据进行处理和分析的核心。算法的合理性和准确性直接关系到动平衡机的最终精度。一些简单的算法可能无法准确处理复杂的振动信号,尤其是对于存在多阶振动的叶轮。而先进的算法能够更准确地识别出叶轮的不平衡量和位置。 算法的稳定性也很重要。在实际测量过程中,可能会遇到各种复杂的工况和干扰因素。如果算法的稳定性不好,就容易出现计算结果波动较大的情况。此外,算法的更新和优化也很有必要。随着技术的不断发展,新的算法不断涌现,及时更新动平衡机的测量算法,可以提高其对不同类型叶轮的适应能力和测量精度。 环境因素 环境因素也会对叶轮动平衡机的精度产生影响。温度是一个重要的环境因素。温度的变化会导致动平衡机的机械结构和传感器发生热胀冷缩现象。机械结构的尺寸变化可能会影响叶轮的安装精度和旋转稳定性,而传感器的性能也可能会因温度变化而发生漂移。在高温环境下,传感器的灵敏度可能会降低,从而影响测量精度。 湿度和灰尘也会对动平衡机造成损害。湿度较大的环境容易导致机械部件生锈,影响其运动性能。而灰尘进入传感器和测量系统中,可能会干扰信号的传输和处理,导致测量误差增大。此外,环境中的振动和噪声也会对动平衡机的测量产生干扰。周围的大型机械设备运行时产生的振动和噪声,可能会掩盖叶轮的真实振动信号,使得测量结果不准确。 叶轮动平衡机的精度受到机械结构、传感器性能、测量系统算法和环境等多种因素的综合影响。为了保证动平衡机的高精度运行,需要在设计、制造、使用和维护等各个环节都加以重视,采取相应的措施来减小这些因素的影响。
07
2025-06
叶轮动平衡机维护保养方法
叶轮动平衡机维护保养方法 叶轮动平衡机作为保障叶轮平稳运行、提高设备性能的关键设备,其良好的运行状态至关重要。为确保动平衡机的精准度与可靠性,我们需要对其进行全面且细致的维护保养。 日常清洁与检查 每日工作结束后,需对动平衡机进行全面清洁。先用软毛刷轻轻拂去动平衡机表面的灰尘与杂物,特别是测量传感器、传动部件等关键部位,要确保无任何杂质附着。随后,用干净的软布擦拭机身,使其保持整洁。在清洁过程中,要仔细检查设备的外观是否有损坏、变形的情况。查看各连接部位的螺栓是否松动,电缆线有无破损、老化现象。若发现螺栓松动,应及时拧紧;对于电缆线的轻微破损,可使用绝缘胶带进行修复,严重破损则需及时更换。同时,还要检查传感器的安装是否牢固,信号传输是否正常,以保证测量数据的准确性。 润滑与校准 定期对动平衡机的传动部件进行润滑是维护的重要环节。根据设备使用说明书的要求,选择合适的润滑剂。一般来说,每运行一定时间(如500 - 1000小时),需对轴承、皮带轮等部位添加适量的润滑剂。在添加润滑剂时,要注意控制用量,避免过多或过少影响设备的正常运行。过多的润滑剂可能会导致油污飞溅,污染周围环境,甚至影响测量精度;过少则无法起到良好的润滑作用,加剧部件的磨损。 此外,校准工作也不容忽视。为保证动平衡机测量的准确性,需定期进行校准。可使用标准的校准件对设备进行校准操作。校准过程要严格按照操作规程进行,确保各项参数符合标准要求。如果发现测量结果偏差较大,应及时调整设备的相关参数或联系专业技术人员进行检修。 环境管理 动平衡机的工作环境对其性能和使用寿命有着重要影响。应将动平衡机放置在干燥、通风良好的环境中,避免设备受潮生锈。环境温度和湿度要控制在合适的范围内,一般温度在10℃ - 35℃,相对湿度不超过70%。同时,要远离大型电机、变压器等强电磁干扰源,防止电磁干扰影响设备的测量精度和正常运行。 另外,保持工作场所的整洁有序也很重要。避免在动平衡机周围堆放过多的杂物,确保操作空间宽敞,便于操作人员进行日常维护和操作。 定期维护与专业检修 除了日常的维护保养工作,还需制定详细的定期维护计划。每隔一段时间(如半年或一年),对动平衡机进行全面的检查和维护。包括对设备的机械结构、电气系统、控制系统等进行深入检查,对磨损严重的部件进行及时更换。 同时,要定期邀请专业的技术人员对动平衡机进行全面检修。专业人员具有丰富的经验和专业的检测设备,能够发现一些潜在的问题,并及时进行处理,确保动平衡机始终处于最佳运行状态。 叶轮动平衡机的维护保养是一项系统而细致的工作。通过日常清洁与检查、润滑与校准、环境管理以及定期维护和专业检修等多方面的措施,可以有效延长动平衡机的使用寿命,提高设备的测量精度和可靠性,为企业的生产提供有力保障。
07
2025-06
叶轮动平衡测试仪价格多少钱
叶轮动平衡测试仪价格多少钱 ——技术参数、品牌溢价与市场波动的多维解析 一、价格区间全景扫描 叶轮动平衡测试仪的价格跨度从3万元至300万元,差异源于技术代际、功能模块与行业定制需求。 基础型设备(3万-15万元):适用于中小型风机、水泵叶轮,侧重静态平衡校正,操作界面简单,适合预算有限的中小企业。 中端机型(15万-50万元):集成动态平衡算法与振动分析功能,支持多工况模拟测试,常见于汽车涡轮增压器、航空发动机维修领域。 高端定制机型(50万-300万元):配备高精度传感器(分辨率≤0.1g)、自动化校正系统及工业物联网接口,服务于航天器推进系统、核电涡轮叶片等高精度场景。 二、价格波动的三大核心变量 技术参数的“隐形成本” 传感器精度:±0.01g级传感器较±0.1g级溢价30%-50%。 转速范围:覆盖10000rpm以上的设备需额外增加高速轴承与冷却系统成本。 校正模式:支持三维动态平衡的机型比单平面校正机型贵20%-40%。 品牌溢价与售后服务 国际品牌(如Hine、MBD):价格普遍高于国产机型50%-100%,但提供终身校准服务与原厂备件库支持。 国产头部品牌(如天远测控、科隆仪器):通过模块化设计降低20%成本,但需额外支付3%-5%的年度维保费用。 市场供需的“蝴蝶效应” 半导体行业景气周期:2023年全球芯片短缺导致传感器采购成本上涨12%,传导至终端设备价格。 新能源政策驱动:风电叶片动平衡仪需求激增,部分厂商采取“预售+定制”模式,交付周期延长导致价格浮动空间达±15%。 三、性价比优化策略 需求拆解法 短期过渡方案:租用二手设备(约1万元/月),适合试产阶段的叶轮厂商。 长期投资方案:选择支持固件升级的机型(如天远T-3000系列),通过软件迭代延长设备生命周期。 隐性成本核算 耗材支出:高精度平衡仪的磁性吸盘、专用校准砝码年均消耗约设备总价的3%-5%。 培训成本:国际品牌认证培训费用高达2万元/人,国产机型提供免费线上课程。 四、未来价格趋势预测 国产替代加速:2024年国内厂商有望突破高速轴承技术壁垒,中端机型价格或下降10%-15%。 智能化溢价收窄:AI自适应算法普及后,高端机型价格年均降幅预计达7%-9%。 定制化需求激增:针对氢能源燃料电池涡轮的专用测试仪,价格可能突破400万元门槛。 结语:价格之外的“价值锚点” 选择叶轮动平衡测试仪时,需跳出数字博弈,关注: 数据兼容性:是否支持ISO 1940/1振动标准导出? 扩展潜力:能否通过加装扭矩传感器升级为复合测试平台? 生态壁垒:厂商是否提供叶轮设计仿真软件的API接口? 高精度设备的终极价值,在于其能否成为企业技术迭代的“加速器”,而非单纯的成本项。 注:本文价格数据基于2023年Q3中国市场调研,实际报价请以厂商技术方案为准。
07
2025-06
叶轮动平衡测试仪哪个品牌好
叶轮动平衡测试仪哪个品牌好 在工业生产的众多领域,叶轮动平衡测试仪都起着至关重要的作用。它能够精准检测叶轮的平衡状况,有效降低设备振动、延长使用寿命、提高生产效率。但面对市场上众多品牌,该如何选择呢?下面为您介绍几个值得关注的品牌。 德国申克(SCHENCK)是一家历史悠久且声誉卓著的品牌。自成立以来,它始终专注于动平衡技术的研发与创新。其叶轮动平衡测试仪凭借高精度的测量技术,能够精确捕捉叶轮的微小不平衡量。在机械制造、航空航天等对平衡精度要求极高的行业,申克的产品表现出色。例如在航空发动机叶轮的检测中,它能确保叶轮在高速旋转时的稳定性,保障飞行安全。而且,该品牌拥有强大的售后服务团队,能及时为客户解决使用过程中遇到的问题。不过,申克产品的价格相对较高,对于一些预算有限的中小企业来说,可能会有一定的经济压力。 美国爱默生(Emerson)也是行业内的知名品牌。爱默生的叶轮动平衡测试仪以其先进的传感器技术和智能化的操作系统而闻名。它的传感器能够敏锐感知叶轮的振动情况,并将数据准确传输到控制系统。其操作系统界面友好,操作简便,即使是没有太多专业知识的操作人员也能快速上手。此外,爱默生的产品具有良好的兼容性,可以与其他工业设备进行无缝对接。在化工、电力等行业,爱默生的测试仪广泛应用于各种大型叶轮的检测与维护。然而,该品牌产品对使用环境要求较为苛刻,如果环境条件不佳,可能会影响测量的准确性。 瑞典斯凯孚(SKF)同样是动平衡领域的佼佼者。斯凯孚的叶轮动平衡测试仪注重产品的可靠性和耐用性。它采用了高品质的材料和精湛的制造工艺,能够在恶劣的工业环境下稳定工作。在矿山、冶金等行业,设备经常面临灰尘大、湿度高的工作环境,斯凯孚的产品依然能保持良好的性能。同时,斯凯孚还提供全面的技术培训和支持,帮助客户更好地使用和维护设备。但斯凯孚的产品更新换代速度相对较慢,对于一些追求最新技术的企业来说,可能无法满足其需求。 日本理音(RION)以其性价比高而受到市场欢迎。理音的叶轮动平衡测试仪价格相对较低,但性能并不逊色。它能够满足大多数企业对叶轮平衡检测的基本需求。在一些小型加工厂和维修店,理音的产品因其操作简单、价格实惠而成为首选。而且,理音的产品体积小巧,便于携带和移动。不过,与前面几个品牌相比,理音在高端技术方面的研发投入相对较少,对于一些对精度要求极高的大型企业,可能不太适用。 综上所述,每个品牌都有其独特的优势和适用场景。在选择叶轮动平衡测试仪时,企业应根据自身的实际需求、预算以及使用环境等因素进行综合考虑。如果追求高精度和卓越性能,德国申克可能是最佳选择;若注重智能化操作和兼容性,美国爱默生会更合适;对于恶劣环境下的使用需求,瑞典斯凯孚值得考虑;而预算有限且对精度要求不是特别高的企业,日本理音是不错的性价比之选。