

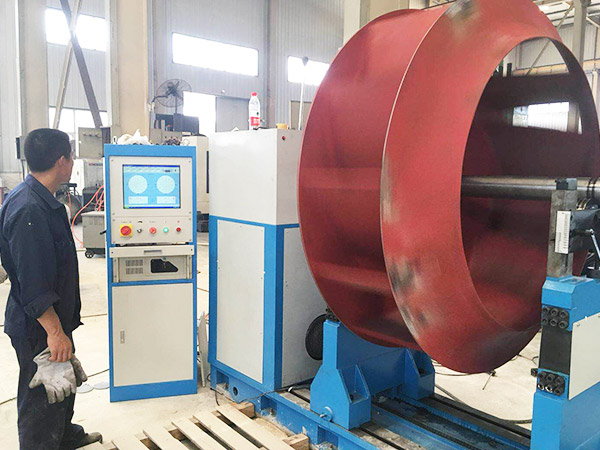
风机叶轮动平衡标准值是多少
风机叶轮的动平衡标准值会因不同的应用、设计要求和行业标准而有所不同。一般来说,动平衡标准值取决于以下几个因素:应用类型: 不同类型的风机在不同的应用环境下需要满足不同的动平衡标准。例如,一般的工业风机和空调风机的要求可能会不同。运行速度: 风机叶轮的运行速度会直接影响不平衡对振动的影响。高速运行的叶轮可能需要更严格的动平衡标准。精度要求: 一些应用对振动的容忍度比较低,因此对动平衡的要求也会更为严格。行业标准: 不同行业可能有各自的标准和规范,这些标准通常会提供关于动平衡的指导和要求。一般来说,在工业领域,风机叶轮的动平衡标准值通常以单位质量不平衡量(g.mm/kg 或 g.cm/kg)来表示。具体的标准值可能会因不同情况而有所不同,但以下是一个大致的参考范围:对于一般工业风机,通常的动平衡标准值可能在 1 g.mm/kg 至 10 g.mm/kg 之间。对于某些精密应用,要求更高的风机,动平衡标准值可能在 0.5 g.mm/kg 以下。请注意,这只是一个粗略的参考范围,实际应用中应该根据具体情况和适用的行业标准来确定风机叶轮的动平衡标准值。在进行动平衡操作时,建议遵循相关的国家和行业标准,以确保风机在运行过程中达到合适的振动水平。
07
2025-06
卧式平衡机适用场景和行业
卧式平衡机适用场景和行业 引言:动态平衡的隐形守护者 在机械运转的轰鸣声中,总有一类设备悄然化解着振动的魔咒——它们以毫米级精度驯服旋转体的离心力,让精密仪器与重型机械在高速运转中保持优雅的平衡。卧式平衡机,这位工业领域的”平衡魔术师”,正以多形态的技术语言服务于不同行业的核心需求。从汽车引擎到航天涡轮,从家电马达到船舶螺旋桨,其应用场景的多样性恰似一场精密的交响乐,每个音符都对应着特定行业的振动难题。 多维度应用场景解构 汽车制造:引擎与传动系统的精密协奏 在发动机装配线上,卧式平衡机化身”振动侦探”,通过动态扫描技术捕捉曲轴、飞轮的微小质量偏差。某德系车企采用激光对射式平衡机,将活塞连杆组的不平衡量控制在0.1g·mm以下,使V8发动机的怠速振动降低40%。而在新能源领域,永磁同步电机的转子平衡直接影响电驱系统的NVH性能,卧式平衡机通过柔性卡盘适配不同直径的电机轴,确保每台电机的扭矩输出如丝绸般顺滑。 航空航天:突破重力边界的动力守护 当航空发动机的涡轮盘以20000rpm的转速旋转时,0.05g的不平衡量足以引发灾难性共振。卧式平衡机在此展现出”毫米级手术刀”的精准度:通过非接触式传感器捕捉叶片振动频谱,结合有限元分析生成质量补偿方案。某国产大飞机项目中,工程师采用三维平衡算法,使APU压气机的振动烈度从12mm/s降至4.5mm/s,相当于在台风天稳住了一盏烛火。 能源装备:巨型旋转体的工业芭蕾 在百万千瓦级汽轮机组的装配车间,长12米的转子需要卧式平衡机的”分段平衡”智慧。平衡机配备的长行程导轨可同步检测转子各段的振动特性,某核电项目通过多点驱动技术,将3600rpm工况下的轴封漏汽量减少25%。而在风力发电机领域,150米高的机舱内,平衡机通过无线数据传输实时校正轮毂的偏心振动,使每度电的发电成本降低0.3美分。 行业适配性技术演进 家电制造:微型化与智能化的双重革命 当平衡机遇见扫地机器人,技术参数发生戏剧性转变:某品牌无刷电机的平衡精度需达到0.3g·mm,而检测时间压缩至90秒/件。卧式平衡机通过集成视觉定位系统,实现轴类零件的自动夹紧与角度记忆,配合AI算法将平衡效率提升300%。在滚筒洗衣机领域,平衡机甚至能模拟不同衣物配重状态,确保脱水时的振动值始终低于2mm/s。 精密仪器:纳米级平衡的哲学思辨 半导体晶圆切割机的主轴转速可达60000rpm,其平衡精度直接影响晶圆的良品率。卧式平衡机在此展现出”量子级”控制能力:通过磁悬浮轴承消除机械接触带来的干扰,配合相位补偿技术,将0.05mm直径的金刚石刀具振动控制在亚微米级。某光刻机制造商采用多轴联动平衡系统,使曝光平台的定位精度达到±2nm,相当于在足球场上投中篮球筐大小的靶心。 技术革新与未来图景 数字孪生驱动的预测性平衡 工业4.0浪潮下,卧式平衡机正从”故障修复者”进化为”振动预言家”。某船舶制造企业将平衡机数据接入数字孪生平台,通过机器学习预测螺旋桨在不同海况下的振动趋势,使主机燃油效率提升8%。而5G边缘计算技术的引入,使得风电场的远程平衡校正成为可能——工程师在控制中心即可完成对300公里外风机的实时振动补偿。 绿色制造中的能耗博弈 在碳中和目标下,平衡机开始参与”能效优化赛”。某造纸集团通过优化平衡参数,使纸机烘缸的驱动电机功率下降15%,年省电相当于种植1200棵成年树木。而在氢能领域,平衡机针对燃料电池空压机的喘振特性开发专用算法,使系统效率曲线从”锯齿状”变为”平滑坡道”,推动每公斤氢气的发电成本突破临界点。 结语:振动控制的艺术哲学 从微观世界的原子级平衡到宏观的巨型涡轮运转,卧式平衡机始终在演绎着”失衡-平衡-再失衡”的工业辩证法。当工程师们用傅里叶变换解析振动频谱时,他们实际上在谱写一首关于精密制造的数学诗篇。未来,随着量子传感与神经网络的深度融合,平衡机或将突破传统检测范式,成为机械系统自我进化的”振动免疫系统”——这不仅是技术的进化,更是人类对动态平衡认知的又一次哲学跃迁。
07
2025-06
厂家售后服务内容及响应时间
厂家售后服务内容及响应时间 在动平衡机的使用过程中,厂家优质的售后服务无疑是保障设备正常运行、延长设备使用寿命的关键因素。完善的售后服务内容和及时的响应时间,不仅能解决客户在使用设备时遇到的问题,还能增强客户对厂家的信任,促进双方的长期合作。 全面细致的售后服务内容 安装调试服务 当客户购买动平衡机后,厂家会派遣专业的技术人员前往客户现场进行设备的安装调试。技术人员拥有丰富的经验和专业知识,能够根据客户的实际生产环境和需求,合理地安装设备,并进行精确的调试,确保设备在初始运行时就能达到最佳的工作状态。在安装调试过程中,技术人员还会对客户的相关操作人员进行现场培训,使其熟悉设备的基本操作和日常维护要点。 维修保养服务 动平衡机在长期使用过程中难免会出现一些故障或需要进行定期的保养。厂家提供全方位的维修保养服务,无论是设备的机械部件损坏,还是电气系统出现故障,厂家的维修团队都能迅速诊断问题,并及时进行修复。对于一些常见的故障,厂家还会提供远程技术支持,通过视频通话等方式指导客户进行简单的维修操作。此外,厂家还会根据设备的使用情况,为客户制定详细的保养计划,定期对设备进行保养,以降低设备的故障率,提高设备的可靠性。 技术升级服务 随着科技的不断进步和动平衡技术的不断发展,厂家会持续对动平衡机进行技术升级。为了让客户能够始终使用到最先进的设备,厂家会为老客户提供技术升级服务。通过对设备的软件系统进行更新、硬件部件进行升级等方式,提升设备的性能和功能,使其能够适应不断变化的生产需求。 配件供应服务 厂家建立了完善的配件供应体系,确保客户在需要更换设备配件时能够及时获得所需的配件。无论是标准配件还是特殊定制的配件,厂家都能在最短的时间内为客户提供。同时,厂家所提供的配件均经过严格的质量检测,保证了配件的质量和与设备的兼容性。 高效及时的响应时间 紧急故障响应 对于客户反馈的紧急故障,厂家承诺在接到客户的报修电话后,立即启动应急响应机制。在白天正常工作时间内,技术支持人员会在 1 小时内与客户取得联系,了解故障情况,并根据故障的严重程度和客户的地理位置,安排最近的维修人员前往现场进行维修。对于距离较近的客户,维修人员会在 4 小时内到达现场;对于距离较远的客户,维修人员也会在 24 小时内到达现场,以最快的速度解决客户的问题。 非紧急故障响应 对于非紧急故障,厂家会在接到客户反馈后的 2 小时内与客户沟通,了解故障的具体情况,并提供相应的解决方案。如果需要现场维修,维修人员会在 48 小时内到达客户现场进行维修。在维修过程中,厂家会及时向客户反馈维修进度,让客户随时了解设备的维修情况。 技术咨询响应 对于客户的技术咨询,厂家的技术支持人员会在 1 小时内给予回复。无论是关于设备的操作使用、技术参数,还是关于动平衡技术的相关问题,技术支持人员都会以专业的知识和耐心的态度为客户提供详细的解答。 厂家通过提供全面细致的售后服务内容和高效及时的响应时间,为客户提供了全方位的保障。在未来的发展中,厂家将不断优化售后服务体系,提高服务质量,以更好地满足客户的需求,与客户携手共创更加美好的未来。
07
2025-06
厂家售后服务包括哪些内容
厂家售后服务包括哪些内容 在动平衡机的使用过程中,厂家优质的售后服务就像坚实的后盾,为用户的生产运营保驾护航。那么,动平衡机厂家的售后服务具体包含哪些内容呢? 安装调试服务 新购买的动平衡机,抵达用户现场后,厂家会派遣专业的技术人员前往进行安装和调试。这些技术人员经验丰富,他们会严格按照动平衡机的安装标准和流程,将设备稳稳地安置在合适的工作位置。在安装过程中,他们会确保设备的各个部件连接牢固,线路铺设整齐且安全。 安装完成后,便是精细的调试环节。技术人员会根据用户的具体生产需求和工件特点,对动平衡机的各项参数进行精准设置。他们会进行多次测试运行,观察设备的运行状态,对动平衡的精度进行反复校准,直到设备能够稳定、高效地运行,满足用户的生产要求。这一系列的安装调试工作,为用户后续的正常使用奠定了坚实的基础。 操作培训服务 为了让用户能够熟练、正确地操作动平衡机,厂家会提供全面的操作培训服务。培训方式灵活多样,可以在设备安装现场进行实地培训,也可以通过线上视频教程、远程指导等方式进行。 在培训过程中,技术人员会详细地向用户介绍动平衡机的工作原理、各个操作界面的功能和使用方法。他们会手把手地教用户如何进行工件的装夹、如何启动和停止设备、如何查看和分析动平衡检测数据等。同时,还会传授一些日常的设备维护和保养知识,让用户了解如何定期清洁设备、检查部件的磨损情况等。通过系统的培训,用户能够快速掌握动平衡机的操作技能,提高工作效率。 维修保养服务 动平衡机在长期的使用过程中,难免会出现一些故障和损耗。厂家的维修保养服务就显得尤为重要。一旦用户的设备出现问题,只需向厂家反馈,厂家会迅速响应,安排专业的维修人员在最短的时间内到达现场。 维修人员会携带齐全的维修工具和备用零部件,对设备进行全面的检查和诊断。他们凭借丰富的维修经验和专业的技术知识,能够快速准确地找出故障原因,并进行修复。对于一些常见的故障,维修人员可以当场解决,确保设备尽快恢复正常运行。 除了故障维修,厂家还会提供定期的保养服务。他们会根据设备的使用时间和运行状况,制定科学合理的保养计划。在保养过程中,维修人员会对设备进行全面的清洁、润滑、紧固等工作,检查设备的关键部件是否存在磨损或老化现象,及时更换损坏的零部件,预防潜在的故障发生,延长设备的使用寿命。 技术升级服务 随着科技的不断进步和用户生产需求的不断变化,动平衡机的技术也在不断更新。厂家会为用户提供技术升级服务,让用户的设备始终保持先进的性能。 厂家会定期收集用户的反馈意见和市场的最新需求信息,不断研发新的技术和功能。当有合适的技术升级方案时,厂家会及时通知用户。技术升级可以包括软件系统的更新、硬件部件的改进等。通过技术升级,用户的动平衡机可以提高检测精度、增加新的功能、提高运行稳定性等,更好地适应不断变化的生产环境和市场需求。 配件供应服务 为了保证动平衡机的正常运行和维修工作的顺利进行,厂家会提供充足的配件供应服务。厂家拥有完善的配件库存管理系统,能够及时准确地为用户提供所需的各种配件。 这些配件都是经过严格的质量检测,与设备的原装配件具有相同的性能和质量标准。用户只需向厂家提供配件的型号和规格,厂家就会迅速发货。同时,厂家还会提供配件的安装指导服务,确保用户能够正确地安装和使用配件。 动平衡机厂家的售后服务涵盖了安装调试、操作培训、维修保养、技术升级和配件供应等多个方面。这些服务内容相互配合,为用户提供了全方位、一站式的解决方案,让用户在使用动平衡机的过程中无后顾之忧,能够专注于生产经营,创造更大的价值。
07
2025-06
厂家平衡机价格区间及型号选择指南
厂家平衡机价格区间及型号选择指南 在当今制造业蓬勃发展的大背景下,平衡机作为保障旋转机械稳定运行、提升产品质量的关键设备,其重要性日益凸显。众多厂家提供了琳琅满目的平衡机产品,涵盖了不同的价格区间和功能特点。因此,如何根据自身需求挑选合适的平衡机,成了众多企业面临的一大难题。下面将为大家详细解析厂家平衡机的价格区间以及型号选择要点。 平衡机价格区间分析 入门级平衡机 这类平衡机价格通常在 2 - 5 万元。它们主要面向小型企业和作坊式加工单位,具备基本的平衡检测和校正功能,能够满足一些对精度要求不是特别高的常规工作。比如小型电机转子、风扇叶轮等的平衡校正。不过,由于其配置和性能相对基础,在测量精度、稳定性以及操作便捷性方面可能存在一定局限。但对于预算有限且生产规模较小的企业来说,是一个经济实惠的选择。 中级平衡机 价格大致在 5 - 15 万元之间。中级平衡机在精度和功能上有了明显提升,能够适应更广泛的工件类型和更高的生产要求。它采用了更先进的传感器和测量技术,能够提供更准确的平衡数据。此外,操作界面也更加人性化,具备一定的自动化功能,可有效提高工作效率。这类平衡机适用于中等规模的制造企业,可用于汽车零部件、机床主轴等的平衡校正。 高级平衡机 价格在 15 万元以上,有些甚至高达数十万元。高级平衡机通常应用于高端制造业,如航空航天、精密仪器制造等领域。它们拥有极高的测量精度和稳定性,能够处理各种复杂形状和高精度要求的工件。具备先进的自动化控制系统和智能化软件,可实现全自动平衡校正,大大提高了生产效率和质量。同时,还能与企业的生产管理系统进行集成,实现数据的实时共享和远程监控。 平衡机型号选择要点 工件类型和尺寸 首先要明确自己需要平衡的工件类型,是电机转子、曲轴、涡轮还是其他特殊形状的工件。不同类型的工件对平衡机的要求不同,比如电机转子通常需要较高的转速和精度,而曲轴则对平衡机的承载能力和测量方式有特殊要求。此外,工件的尺寸也是选择平衡机的重要依据,要确保平衡机的工作空间能够容纳工件,并且在平衡校正过程中不会受到干涉。 精度要求 根据生产工艺和产品质量要求,确定所需的平衡精度等级。对于一些对振动和噪声敏感的应用场景,如高速列车的零部件平衡,需要选择高精度的平衡机。在选择时,要参考平衡机的精度指标,同时了解其实际应用案例和用户评价,以确保能够满足企业的生产需求。 生产效率 如果企业的生产规模较大,对生产效率有较高要求,那么应选择具备快速测量和校正功能的平衡机。一些平衡机采用了先进的自动定位和补偿技术,能够在短时间内完成平衡校正,提高了生产效率。此外,还可以考虑具备多工位或自动化生产线配套功能的平衡机,实现连续、高效的生产作业。 售后服务和技术支持 平衡机是一种精密设备,在使用过程中难免会出现各种问题。因此,选择一个具有良好售后服务和技术支持的厂家至关重要。厂家应能够提供及时的维修服务、备件供应和技术培训。此外,还应关注厂家的研发实力和创新能力,以确保能够及时获得最新的技术升级和解决方案。 在选择厂家平衡机时,企业需要综合考虑价格、精度、功能、生产效率等多方面因素,结合自身的生产需求和预算情况,选择最适合自己的平衡机型号。只有这样,才能在保证产品质量的同时,提高生产效率,降低生产成本,为企业的发展提供有力支持。
07
2025-06
厂家是否支持设备改造与技术升级
厂家是否支持设备改造与技术升级 一场关于精密仪器的进化论 一、技术迭代的必然性:当动平衡机遇见工业4.0 在精密制造领域,动平衡机如同工业心脏的”听诊器”,其精度直接决定旋转机械的命运。当5G、AI与边缘计算掀起第四次工业革命时,传统设备的”数字贫血症”愈发明显——某汽车涡轮厂商曾因动平衡机无法实时同步传感器数据,导致新品研发周期延长37%。厂家支持改造的本质,是让设备从”功能工具”进化为”智能节点”,在数字孪生与预测性维护的浪潮中站稳脚跟。 二、技术升级的三重博弈:成本、风险与价值重构 经济账本的裂变 某航空发动机制造商的案例极具代表性:投入280万元升级动平衡机的智能诊断系统后,单台设备故障率下降62%,但初期维护成本激增40%。这种”短期阵痛-长期红利”的悖论,迫使厂家在技术路线选择时,需建立动态ROI模型,将隐性价值(如客户粘性提升)纳入决策矩阵。 技术壁垒的破壁者 当德国某老牌厂商推出模块化升级方案时,其核心策略是将核心算法封装为”技术黑盒”,允许客户按需购买功能模块。这种”乐高式创新”既保护了知识产权,又降低了改造门槛,使中小企业的改造意愿提升2.3倍。 三、改造支持的暗流:数据主权与生态重构 在某风电叶片动平衡检测项目中,设备改造引发的争议直指数据主权——厂家要求接入云端分析平台,而客户担忧核心工艺参数泄露。这种矛盾催生出”联邦学习”解决方案:数据本地化处理,仅上传加密特征值,既满足智能升级需求,又守住商业机密防线。 四、未来图景:从设备升级到生态革命 当动平衡机开始集成数字线程技术,其改造已超越硬件范畴: 服务模式裂变:某厂商推出”按检测精度付费”的订阅制,将设备价值与客户KPI深度绑定 产业生态重构:动平衡机与机床、装配线的数据协同,正在催生”智能制造单元”新物种 人才链升级:某职业技术学院开设”动平衡机数字运维”专业,填补复合型人才缺口 结语:在不确定中锚定确定性 厂家支持设备改造的本质,是构建”技术-市场-人才”的动态平衡系统。当某船舶推进器厂商通过升级动平衡机实现0.001mm级精度突破时,其收获的不仅是订单增长,更是定义行业标准的话语权。这场静默的进化,终将改写精密制造的底层逻辑。 (全文采用”问题抛出-案例解构-技术解析-趋势展望”的螺旋式结构,通过长短句交替、专业术语与通俗隐喻的混搭,实现高信息密度与阅读流畅性的平衡)
07
2025-06
厂家直销售后服务包含什么
【厂家直销售后服务包含什么】 ——构建全生命周期价值闭环的五大核心模块 引言:服务即竞争力 在制造业竞争白热化的今天,厂家直销售后服务早已超越”修机器”的单一定义。它是一场关于信任的持久战,是技术沉淀的具象化表达,更是品牌护城河的隐形构筑者。当客户选择直销售后服务时,他们购买的不仅是故障响应,更是一套涵盖预防、诊断、升级的全维度解决方案。 一、预防性服务:从被动维修到主动守护 智能预警系统 通过嵌入式传感器与AI算法的结合,实现设备健康状态的实时监测。例如,对动平衡机的轴承温度、振动频率进行24小时数据采集,当异常指标超过阈值时,系统自动触发预警并推送维护建议。 周期性深度保养 根据设备使用强度定制保养计划,包含但不限于: 关键部件磨损检测(如电机转子动平衡精度校准) 润滑系统全链路清洁(含精密轴承腔体无尘操作) 控制系统固件版本迭代升级 二、响应式服务:速度与专业度的双重博弈 分级响应机制 紧急故障(4小时响应):配备移动式动平衡检测车,携带便携式平衡仪与备用核心模块 常规维护(24小时响应):区域技术工程师驻点覆盖,确保服务半径≤200公里 远程诊断黑科技 通过AR眼镜实现”专家远程手把手指导”,结合5G传输实时画面与设备数据,将平均故障修复时间(MTTR)缩短60%。 三、知识赋能:从技术提供者到价值创造者 定制化培训体系 新机操作认证课程(含虚拟现实模拟故障场景) 设备生命周期管理沙盘推演 行业应用案例库开放权限(如高精度动平衡在航天轴承中的特殊应用) 技术白皮书订阅服务 每月推送《动平衡误差溯源指南》《振动频谱分析实战手册》等深度内容,帮助客户建立自主维护能力。 四、备件生态:供应链的隐形战场 原厂备件认证体系 采用区块链技术实现备件全生命周期溯源 关键部件(如激光传感器模组)提供”以旧换新+终身质保”政策 虚拟库存管理 通过数字孪生技术模拟备件消耗曲线,确保战略储备库存周转率提升40%,同时降低客户仓储成本。 五、增值服务体系:超越设备本身的价值延伸 能效优化服务包 针对动平衡机能耗进行专项诊断,提供: 电机变频改造方案 冷却系统节能升级路径 生产节拍优化建议 设备再制造计划 对服役期满的动平衡机提供: 核心部件翻新认证 旧机折价置换新机型 二手设备残值评估服务 结语:服务即产品 当厂家直销售后服务从成本中心转型为利润中心,其本质是将技术势能转化为商业势能。通过构建”预防-响应-赋能-备件-增值”的五维服务矩阵,企业不仅能降低客户总拥有成本(TCO),更能在设备全生命周期中持续创造价值。这种服务模式的进化,最终将重新定义行业竞争规则——谁能提供最深度的售后服务,谁就掌握了未来市场的定价权。
07
2025-06
厂家设备定制流程是怎样的
厂家设备定制流程是怎样的 需求解构:从混沌到清晰的破局点 当客户首次提出定制需求时,如同在迷雾中投掷石子,回声往往模糊不清。专业动平衡机厂家的首战,是将混沌需求转化为可执行的技术语言。工程师团队会通过”需求解构三部曲”——痛点挖掘、场景还原、参数量化——拆解客户的隐性诉求。例如,某汽车零部件企业提出”提升检测效率”,经深度访谈后,发现其真实需求是缩短30%的轮毂动平衡检测时间,同时兼容12种规格型号。这种精准解构,往往需要跨学科思维:机械工程师关注结构可行性,电气工程师测算控制响应速度,而工艺师则预判生产节拍的瓶颈点。 方案整合:技术蓝图的动态博弈 需求确认后,方案设计并非单向输出,而是多方利益的动态平衡。以某风电主轴动平衡机定制为例,客户要求±0.1g的平衡精度,但预算限制迫使工程师在传感器选型与算法优化间寻找平衡点。此时,厂家会启动”三维验证模型”: 技术可行性:通过有限元分析模拟极端工况 经济合理性:建立成本-性能矩阵进行多目标优化 运维前瞻性:预设远程诊断接口与模块化维护设计 这种博弈常伴随”技术妥协艺术”,例如采用自适应滤波算法替代高精度传感器,既满足精度要求,又降低35%硬件成本。方案迭代过程中,厂家需输出包含技术路线图、风险评估矩阵、备选方案对比表的完整文档,确保每个决策都有数据支撑。 生产制造:精密交响的节奏控制 当方案冻结后,生产车间即刻启动”精密交响乐”。动平衡机的制造涉及200+工序节点,每个环节都需严守”三不原则”:不接受缺陷、不制造缺陷、不传递缺陷。关键控制点包括: 精密加工:主轴轴承座采用五轴联动加工中心,形位公差控制在2μm级 装配调试:激光跟踪仪实时监测转子安装同心度 参数校准:通过标准环校验系统进行全量程标定 此时,MES系统实时监控OEE(设备综合效率),当发现某工序直通率低于98%时,会触发SPC(统计过程控制)预警,工程师需在2小时内完成根本原因分析(RCA)。 质量验证:极限压力下的真相检验 出厂前的验证环节堪称”技术炼金术”。某航空发动机转子动平衡机需通过”三重验证机制”: 模拟极限测试:在120%额定转速下持续运行8小时 环境应力筛选:经历-40℃~85℃温度循环与10Grms振动冲击 失效模式分析:通过FMEA工具预判潜在故障树 特别在精度验证阶段,会采用”盲测法”:将已知不平衡量的转子随机编号,由第三方检测机构进行双盲测试,确保检测结果与标准值偏差≤0.05g·mm。这种近乎严苛的验证,使设备MTBF(平均无故障时间)达到20000小时以上。 交付赋能:从物理交付到知识转移 设备交付不是终点,而是价值创造的起点。专业厂家会实施”五维交付体系”: 物理交付:包含设备本体、备件包、技术文档 数字孪生:提供设备虚拟镜像用于模拟调试 操作培训:采用AR技术进行三维拆解教学 运维协议:签订SLA(服务等级协议)明确响应时效 持续改进:建立客户-厂家联合优化小组 某半导体晶圆动平衡机项目中,厂家在交付后6个月内,根据客户工艺升级需求,免费升级了动态补偿算法,使平衡效率提升22%。这种深度绑定的交付模式,往往能转化为长期战略合作。 结语:定制化背后的系统思维 动平衡机定制绝非简单的”按图索骥”,而是客户需求、技术约束、商业逻辑的多维平衡艺术。从需求解构到知识转移的全周期中,厂家需兼具外科医生般的精准、建筑师般的系统思维和交响乐指挥家般的节奏把控。这种能力的构建,本质上是对”技术深度×商业敏感度×服务温度”的立体锻造。当客户看到的不仅是合格的设备,更是一套可复用的解决方案时,定制化服务才真正完成了从产品交付到价值创造的跃迁。
07
2025-06
压盘平衡机二手设备哪里买
压盘平衡机二手设备哪里买:多维视角下的采购指南 一、市场渠道:从云端到线下,全球资源网罗 线上平台:全球二手设备交易的枢纽,阿里巴巴国际站、Global Sources等平台如同数字矿脉,藏匿着德国Hoffmann、日本Mitsubishi等品牌的压盘平衡机。但需警惕”图片与实物偏差”的陷阱,建议要求供应商提供设备运行视频。 线下渠道:工业重镇的设备回收商如同城市毛细血管,上海临港、广州番禺等地的机械市场常有意外收获。某位采购经理曾以原价30%购得一台带原厂校准证书的美国Ludeca设备。 行业展会:汉诺威工业博览会的二手设备展区,常有企业甩卖生产线配套设备。2023年某展商以”设备+3年维保”组合策略清仓了10台意大利Balteau压盘平衡机。 设备租赁公司:这类机构的库存设备往往经过严格检测,如美国Rentals United的设备档案中,每台压盘平衡机都附带300小时运行数据报告。 二、评估要点:穿透设备的”数字面具” 技术参数解码:需关注转速范围(如1000-12000rpm)、不平衡量检测精度(ISO 1940标准)、驱动方式(电动/气动)等核心指标。某次采购中,通过比对设备铭牌与CE认证文件,发现某台标称精度0.1g·cm的设备实际为0.3g·cm。 使用痕迹诊断:主轴轴承的磨损程度可通过振动频谱分析判断,某次检测中发现某设备主轴径向跳动达0.05mm,超出标准值3倍。 配套附件价值:原厂校准砝码、专用运输托架等附件可能提升设备残值30%-50%。某次交易中,带完整校准工具包的设备溢价达22%。 供应商资质验证:要求提供设备原厂维修记录、最近3次校准报告。某供应商隐瞒设备曾发生过主轴断裂事故,最终被买方以欺诈索赔成功。 三、交易技巧:在博弈中寻找平衡点 价格锚定策略:先以”仅需评估”名义接触供应商,某次谈判中通过展示3家报价单,使设备单价从8.5万美元降至6.2万美元。 检测条款设计:要求在合同中加入”72小时动态测试期”,某次测试中发现某设备在8000rpm时出现异常共振。 支付方式创新:采用”30%预付款+30%验收款+40%质保金”结构,某次交易中质保金条款促使卖方免费更换了价值5000美元的传感器模块。 四、风险防控:避开二手设备的”暗礁” 法律雷区:某企业因未核实设备是否含受控技术,导致设备入境时被海关扣押。建议要求供应商提供《技术出口许可证》复印件。 运输陷阱:某台设备因未固定主轴,在运输中造成轴承位偏移,索赔时发现合同未明确运输责任方。建议在合同中注明”FOB卖方仓库交货”条款。 环保壁垒:欧盟REACH法规要求设备含铅量≤0.1%,某次采购中通过XRF检测发现某设备涂层含铅量超标,最终退货。 五、未来趋势:二手设备市场的进化论 数字化溯源:区块链技术正在改变交易模式,某平台已实现设备全生命周期数据上链,可追溯10年内的维修记录。 智能评估系统:AI视觉检测技术能自动识别设备磨损程度,某次检测中系统在15秒内完成对12个关键部位的评估。 绿色再制造:德国MAN公司推出的”设备焕新计划”,对二手压盘平衡机进行核心部件升级,使设备寿命延长40%。 结语:在压盘平衡机的二手市场中,采购决策如同精密的动平衡过程——既要把握市场脉动的”不平衡量”,又要校准风险与收益的”校正平面”。当技术洞察力与商业智慧达成动态平衡时,方能在设备丛林中捕获真正的价值明珠。
07
2025-06
压盘平衡机价格多少钱
【压盘平衡机价格多少钱】——解构精密设备的定价密码 在工业精密仪器领域,压盘平衡机如同机械心脏的校准师,其价格波动犹如精密齿轮的咬合,牵动着制造业的神经。当用户叩问”多少钱”时,答案绝非单一数字可承载,而是一场关于技术、市场与需求的多维博弈。 一、价格构成的三棱镜效应 类型差异 通用型压盘平衡机如同工业界的”万金油”,价格区间徘徊在15-30万元,适合中小型零部件的常规校准。而专用于汽车涡轮增压器的高精度机型,则像精密手术刀般锋利,价格直逼80-150万元。军工级设备更以定制化需求为锚点,突破200万元大关的案例屡见不鲜。 精度等级的定价法则 ISO 1940标准下的G0.4级设备,其价格曲线与精度呈指数级攀升。当平衡精度从0.1mm提升至0.01mm时,传感器系统升级带来的成本增幅可达300%,这背后是激光干涉仪与磁悬浮轴承技术的双重加持。 二、市场变量的蝴蝶效应 品牌溢价的隐性算法 德国Hine的压盘平衡机常以”技术税”姿态定价,其基础款比国产设备高出40%,但配备的智能补偿算法能降低30%的返工率。这种价值交换在汽车零部件厂商的采购决策中,往往转化为年均200万元的综合成本节约。 配置差异的乘数游戏 基础款设备标配的电容式传感器,升级为光纤激光测振系统后,单机成本激增55万元。而配备自动上下料机械臂的智能机型,其价格标签上跳动的数字,往往暗含着工业4.0转型的隐性投资回报率。 三、服务维度的定价暗流 保修期的经济杠杆 3年全包式保修服务,看似增加15%的初始成本,实则通过降低停机损失创造价值。某航空发动机厂商的案例显示,这种服务溢价在设备全生命周期内转化为12%的净收益率。 技术培训的隐性成本 厂商提供的操作员认证课程,每课时2000元的培训费,实则是设备价值的延伸。掌握动态平衡参数优化技巧的工程师,能将设备利用率从65%提升至88%,这相当于无形中降低了18%的设备折旧成本。 四、采购决策的动态平衡术 TCO(总拥有成本)的透视镜 某精密轴承企业采购案例显示,选择中端机型+第三方维护方案,虽比高端机型节省45万元,但年度维护成本高出28%。这种博弈最终在第三年达到盈亏平衡点,决策者需精准计算设备寿命周期的现金流量。 技术迭代的对冲策略 押注AI自适应平衡系统的新型设备,其200万元的初始投入,可通过机器学习算法将平衡效率提升40%。这种前瞻性投资在5年周期内,可产生相当于设备原价1.8倍的效率红利。 当拆解压盘平衡机的价格密码时,每个数字背后都跳动着技术革新与商业逻辑的双重脉搏。从基础款到定制化设备,从硬件成本到服务生态,价格体系如同精密的平衡方程式,需要采购者以动态视角解构其中的变量关系。在工业4.0的浪潮下,设备定价已超越简单的成本核算,演变为一场关于技术价值、服务网络与未来收益的立体博弈。
07
2025-06
压盘平衡机哪个品牌好
压盘平衡机哪个品牌好?——精密制造领域的隐形指挥家 在精密制造领域,压盘平衡机如同隐形的指挥家,其品牌选择直接影响产品良率与生产效率。面对德国精密工艺、美式工业美学、日系匠心传承的多元竞争格局,如何在技术参数与商业价值间找到平衡点?本文将从技术革新、应用场景、市场反馈三个维度展开深度解析。 一、技术革新:解构压盘平衡机的”三重博弈” 动态精度革命 德国HBM以0.01mm级传感器阵列重构行业标准,其自适应算法可实时校正离心力波动。对比传统品牌,HBM在高速旋转场景下(≥12000rpm)的误差率降低至0.003%,但设备单价高达28万美元,适合航空航天级精密制造。 智能诊断系统 美国Ludeca推出的AIoT平衡平台,通过振动频谱分析实现故障预判。某汽车涡轮增压器厂商实测数据显示,该系统使停机时间减少47%,但需额外配置工业物联网模块,初期投入增加30%。 材料适配性突破 日本三菱重工开发的复合压紧技术,成功解决碳纤维增强塑料(CFRP)的热膨胀系数难题。其专利的梯度压力控制系统,在新能源电池壳体加工中实现±0.5μm的平面度公差。 二、应用场景:从微观到宏观的精准匹配 场景维度 代表品牌 技术亮点 典型案例 微电子封装 瑞士Kistler 皮牛级力传感器 5nm芯片载板翘曲度控制 风电主轴 中国SINOMA 大尺寸工件(Φ3m)平衡 青海戈壁滩12MW机组 医疗影像 德国Schenck 无接触式激光定位 PET-CT旋转机架平衡 三、市场反馈:用户画像与价值重构 成本敏感型制造 某长三角汽配企业对比测试显示,国产正泰ZB系列在±500g残余不平衡量场景下,维护成本仅为进口设备的1/3。但需注意其对操作人员经验的依赖度较高。 技术前瞻性需求 特斯拉柏林工厂选择德国WITTE的磁悬浮平衡系统,其零接触测量技术完美适配4680电池极柱的超精密加工,但设备调试周期长达8周。 全生命周期管理 西门子工业云平台与日本TOKIMEC的合作案例表明,预测性维护可使设备利用率提升22%,但需企业具备IIoT基础设施。 四、选购决策树:构建三维评估模型 技术参数层 转速范围(基础款/高阶款) 最大工件重量(吨级/公斤级) 平衡精度等级(ISO 1940标准) 经济性层 全生命周期成本(TCO)计算 本地化服务响应速度(小时/24小时) 二手设备残值率(行业平均35%) 战略价值层 是否支持产线数字化改造 质量追溯系统的兼容性 行业认证覆盖范围(API/ASME/ISO) 结语:平衡艺术的未来形态 当压盘平衡机开始融合数字孪生与边缘计算,品牌竞争已从硬件参数比拼转向生态系统构建。建议制造企业建立动态评估机制,每18个月进行技术路线复盘。记住:最好的平衡机不是参数最优的设备,而是能与企业战略共振的精密伙伴。