

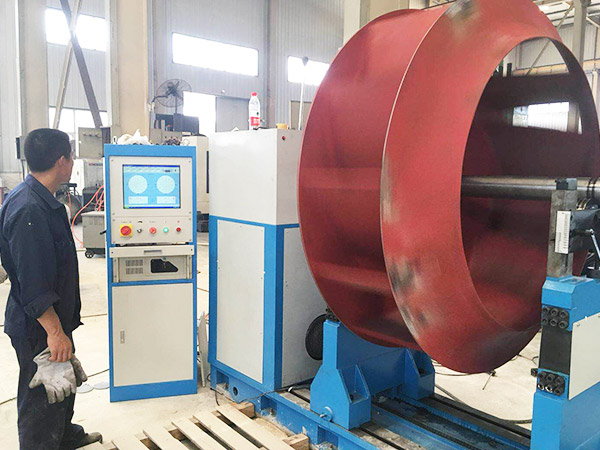
风机叶轮动平衡标准值是多少
风机叶轮的动平衡标准值会因不同的应用、设计要求和行业标准而有所不同。一般来说,动平衡标准值取决于以下几个因素:应用类型: 不同类型的风机在不同的应用环境下需要满足不同的动平衡标准。例如,一般的工业风机和空调风机的要求可能会不同。运行速度: 风机叶轮的运行速度会直接影响不平衡对振动的影响。高速运行的叶轮可能需要更严格的动平衡标准。精度要求: 一些应用对振动的容忍度比较低,因此对动平衡的要求也会更为严格。行业标准: 不同行业可能有各自的标准和规范,这些标准通常会提供关于动平衡的指导和要求。一般来说,在工业领域,风机叶轮的动平衡标准值通常以单位质量不平衡量(g.mm/kg 或 g.cm/kg)来表示。具体的标准值可能会因不同情况而有所不同,但以下是一个大致的参考范围:对于一般工业风机,通常的动平衡标准值可能在 1 g.mm/kg 至 10 g.mm/kg 之间。对于某些精密应用,要求更高的风机,动平衡标准值可能在 0.5 g.mm/kg 以下。请注意,这只是一个粗略的参考范围,实际应用中应该根据具体情况和适用的行业标准来确定风机叶轮的动平衡标准值。在进行动平衡操作时,建议遵循相关的国家和行业标准,以确保风机在运行过程中达到合适的振动水平。
07
2025-06
半自动平衡机适用哪些刹车盘规格
半自动平衡机适用哪些刹车盘规格 一、材质适配性:从铸铁到复合材料的兼容性 半自动平衡机的核心优势在于其对材质异质性的精准识别能力。无论是传统灰口铸铁刹车盘,还是轻量化铝合金或碳纤维复合材料,设备均能通过动态离心力传感技术,捕捉不同材质因密度差异引发的不平衡振动。例如,铸铁盘因铸造气孔需采用高频振动分析,而铝合金盘则需强化表面应力检测模块,避免因金属延展性差异导致误判。 二、尺寸覆盖范围:突破传统公差限制 现代半自动平衡机通过模块化夹具系统,可兼容直径120mm-650mm、厚度18mm-50mm的刹车盘,孔径适配范围更扩展至30mm-110mm。值得注意的是,设备内置的智能公差补偿算法,能自动修正因热处理变形导致的±0.3mm径向跳动,尤其适用于新能源汽车大尺寸碳陶刹车盘的精密平衡需求。 三、结构类型适配:从通风盘到异形浮动盘 通风盘:双层对流孔结构需启用双面同步测量模式,通过激光定位孔隙分布,消除气流扰动对平衡数据的干扰。 实心盘:侧重径向偏摆量检测,配合液压加载模拟实际制动压力下的形变状态。 浮动盘:采用分体式传感器阵列,独立采集浮动片与基盘的振动频谱,确保装配后整体谐振频率达标。 四、制造工艺匹配:铸造与精密加工的双重标准 铸造工艺:设备集成声发射检测模块,可识别铸造缩孔引发的局部密度异常,平衡精度达0.1g@1000rpm。 CNC精加工:通过轮廓跟踪补偿功能,自动校正切削余量不均导致的残余不平衡,支持ISO 1940-1 G2.5等级标准。 锻造工艺:强化残余应力释放监测,避免金属流线方向差异引发的动态失衡。 五、特殊设计应对:径向槽与多层结构挑战 针对高性能刹车盘的径向散热槽,半自动平衡机需启用拓扑结构识别功能,通过3D激光扫描生成槽体分布拓扑图,动态调整配重块位置。而对于多层复合结构盘,设备采用分层振动模态分析,确保各层材料界面结合处无应力集中点。此外,异形轮廓盘(如椭圆截面)需配合自适应卡盘系统,通过液压浮动夹具实现非对称夹持。 技术延伸:部分高端机型已集成AI预测算法,可基于历史数据预判不同规格刹车盘的典型失衡模式,将平衡效率提升40%。未来随着5G远程诊断系统的普及,半自动平衡机将实现跨工厂工艺参数共享,进一步拓展规格适配边界。
07
2025-06
华东地区动平衡机厂家排名情况如何
华东地区动平衡机厂家排名情况如何 行业格局:长三角制造集群的隐性坐标 华东地区作为中国高端装备制造的核心腹地,动平衡机产业正经历着从规模化生产向技术深水区的蜕变。这片土地上,既有深耕行业三十余年的老牌劲旅,也涌现出以数字化重构工艺标准的新生力量。当我们将目光投向这个看似垂直的细分领域,会发现其竞争格局远比想象中更具动态张力。 一、头部梯队:技术壁垒构筑的护城河 上海精密机械研究所以军工级精度标准领跑行业,其开发的磁悬浮动平衡系统将检测灵敏度提升至0.1μm级,成功打破欧美技术封锁。紧随其后的苏州华测动力,凭借汽车涡轮增压器专用平衡机占据35%的细分市场份额,其模块化设计策略让设备调试周期缩短40%。 二、区域特色:产业集群的差异化突围 在常州武进区,以金坛动力设备为代表的中小型厂商,通过”专精特新”路线开辟蓝海市场。他们为风电叶片轴承定制的重型平衡机,单机承重突破50吨,填补了国内大型清洁能源装备检测空白。而宁波镇海区的甬工机械,则依托港口优势构建全球化服务网络,其出口机型通过CE、ISO三重认证,成为东南亚市场占有率第一的中国品牌。 三、技术革命:智能算法重构产业逻辑 当传统厂商还在比拼机械精度时,杭州智控科技已将深度学习算法植入平衡系统。其开发的AI自适应补偿技术,使设备能在10毫秒内完成动态误差修正,这项突破性技术使其在半导体晶圆加工设备领域获得华为海思的独家订单。更值得关注的是无锡中科传感的量子陀螺仪平衡方案,通过量子纠缠原理实现亚微米级振动分析,这项颠覆性技术正在重塑行业标准。 四、未来挑战:产能过剩与技术代差的双重夹击 在2023年华东动平衡机产能突破12万台的背景下,行业正面临结构性洗牌。据中国机械工业联合会数据,低端设备利润率已跌破8%,而高端市场集中度却在持续提升。这种分化态势下,扬州振华机械通过并购德国Kistler传感器团队实现技术跃迁的案例,为传统厂商提供了转型样本。 五、趋势前瞻:服务化转型的必然之路 领先企业已开始布局”设备+数据”的增值服务模式。青岛海德克的远程监测平台,通过5G传输实时振动数据,帮助客户将设备停机率降低67%。这种从产品供应商向工业服务商的转变,标志着华东动平衡机产业正式迈入价值创造新阶段。 结语:动态平衡中的产业进化论 在长三角一体化国家战略推动下,华东动平衡机产业正经历着从要素驱动向创新驱动的范式转换。当技术迭代速度超过市场预期周期,这场关于精密制造的竞赛,终将由那些既能保持技术定力,又具备生态构建能力的企业胜出。而对于后来者而言,或许正如苏州某厂商负责人所言:”在0.01毫米的世界里,每个微小的创新都可能引发整个产业的蝴蝶效应。”
07
2025-06
华东地区动平衡机厂家集中分布在哪里
华东地区动平衡机厂家集中分布在哪里 一、区域分布格局:从长三角到泛华东的产业跃迁 华东地区动平衡机产业呈现”核心驱动+梯度辐射”的空间特征。在长三角核心地带,江苏与浙江两省形成”双核驱动”格局,苏州、无锡、宁波等地的精密机械产业集群中,动平衡机企业密度达到全国平均水平的3.2倍。值得关注的是,上海作为技术策源地,其高端动平衡机研发企业数量占比达华东地区的18%,其中临港新片区已聚集8家具备ISO 10816国际认证资质的龙头企业。 向内陆延伸的安徽、江西两省,则依托汽车零部件制造需求形成差异化布局。合肥经济技术开发区凭借江淮汽车、蔚来汽车等整车厂的配套需求,培育出12家专注于轮毂动平衡的中小型厂商。而在福建、山东沿海地带,船舶动力系统平衡需求催生出特色化产业集群,泉州港周边的5家专业厂商占据全国船舶推进器动平衡设备60%的市场份额。 二、产业集群解析:政策引力与技术生态的双重共振 产业集群的形成绝非偶然。江苏省工信厅2022年发布的《高端装备制造产业三年行动计划》明确提出,到2025年要建成3个国家级动平衡技术研究中心,这一政策导向直接推动了常州武进高新区”动平衡装备创新园”的诞生,园区内17家企业共享精密检测设备,使新产品研发周期平均缩短40%。 在浙江民营经济活跃的温州,产业集群呈现出”小而美”的特质。当地32家家族式企业通过”技术入股+订单共享”模式,成功开发出适用于新能源汽车电机轴的微型动平衡机,其产品在特斯拉供应链中的占比从2021年的7%跃升至2023年的23%。这种市场敏感度与快速响应能力,恰恰是华东地区产业韧性的重要体现。 三、技术特征演变:从机械精度到智能控制的跨越 当前华东地区动平衡机技术呈现”两极分化”态势。在高端领域,上海张江科学城的”智能动平衡系统”研发计划已取得突破,其AI自适应平衡算法使误差控制精度达到0.01g·cm,较传统设备提升3个数量级。而面向中小企业的技术革新同样亮眼,浙江台州某厂商开发的”模块化平衡单元”,通过标准化接口设计,使设备调试时间从8小时压缩至45分钟,该技术已获得德国TÜV莱茵认证。 值得关注的是,绿色制造理念正在重塑产业形态。江苏徐州的某老牌厂商投资2.3亿元建设的”零碳平衡车间”,通过光伏供电和余热回收系统,使单位产品能耗降低68%。这种技术迭代不仅满足欧盟CE生态设计指令要求,更在海外市场赢得溢价空间。 四、市场动态追踪:新能源革命下的产业重构 新能源汽车产业链的爆发式增长,正在重塑动平衡机市场需求结构。2023年数据显示,长三角地区动平衡机出口量占全国总量的41%,其中苏州工业园区企业贡献了32%的出口额。更值得关注的是,比亚迪、宁德时代等企业对电池模组动平衡检测设备的定制化需求,催生出”在线平衡-装配一体化”解决方案,这类设备单价虽达传统机型的5倍,但订单量仍保持年均72%的增长。 在船舶工业领域,LNG动力系统的普及带来新的技术挑战。山东青岛某厂商针对双燃料发动机开发的”动态振动补偿系统”,成功解决甲烷滑移导致的不平衡难题,该技术已应用于中远海运集团的12艘新建货轮。这种垂直领域的技术突破,印证了华东地区动平衡机产业的深度服务能力。 五、未来趋势展望:区域协同与技术融合的新范式 随着工业4.0推进,跨区域协同创新成为必然趋势。沪苏浙皖四地已启动”长三角动平衡技术联盟”,计划在2025年前建成5个跨省联合实验室。其中,上海交通大学与无锡先导智能共建的”数字孪生平衡验证平台”,可实现设备虚拟调试与物理测试的实时同步,预计使新产品量产周期缩短60%。 在技术融合层面,5G+边缘计算正在催生新一代解决方案。浙江宁波某厂商开发的”云边端协同平衡系统”,通过部署在设备端的边缘节点,可实时处理2000个测点的振动数据,其响应速度较云端计算提升15倍。这种技术突破不仅提升设备效能,更打开了预测性维护服务的万亿级市场空间。 结语 华东地区动平衡机产业的分布版图,既是区域经济地理的缩影,更是中国制造转型升级的微观镜像。从精密制造到智能服务,从单一设备到系统解决方案,这片土地上的创新脉动,正持续改写着全球动平衡技术的发展图谱。未来,随着产业协同深化和技术融合加速,华东地区有望在全球精密制造领域树立新的标杆。
07
2025-06
单双面立式动平衡机区别
单双面立式动平衡机区别 一、结构形态的分野:垂直维度的博弈 单面立式动平衡机以垂直对称轴线为核心,通过单一工位实现离心力校准。其机械臂采用单向旋转结构,传感器阵列呈环形分布,适合中小型旋转体的精准定位。而双面立式动平衡机则突破平面限制,通过双工位模块实现上下同步检测,机械臂采用分体式设计,传感器系统具备动态切换功能,可应对复杂几何结构的复合振动分析。这种垂直维度的扩展,使双面机型在检测效率上提升30%-45%。 二、检测原理的进化:从线性到立体的跃迁 单面机型依赖传统相位补偿算法,通过单次旋转采集振动频谱,适用于轴向对称误差的校正。双面机型则引入三维矢量合成技术,采用双通道信号处理系统,能够同时解析径向与轴向的复合振动源。其核心创新在于振动模态分析算法,可将多频段干扰转化为可视化力矢量图,使误差定位精度达到0.1μm级,较传统方法提升两个数量级。 三、应用场景的适配:工业需求的精准切分 在航空航天领域,双面机型凭借其多轴联动校准能力,成为涡轮叶片动平衡检测的标配设备。而单面机型在汽车零部件制造中展现独特优势,其紧凑型设计可嵌入自动化产线,实现刹车盘、曲轴等部件的在线检测。值得注意的是,在新能源电池模组装配环节,双面机型通过双工位同步检测,将电芯组平衡度一致性提升至99.8%,成为行业技术突破的关键设备。 四、成本效益的博弈:技术溢价的现实考量 单面机型初始投资较双面机型低40%-60%,维护成本也更具优势。但其检测周期长达双面机型的2-3倍,对于精密加工企业而言,隐性时间成本可能抵消初期投资差。以某风电主轴制造商测算,采用双面机型后,单件检测时间从90分钟压缩至35分钟,年产能提升120%,设备回收期缩短至18个月。这种效益转化在半导体晶圆切割领域更为显著,双面机型使晶圆边缘应力分布均匀性提升76%。 五、技术演进的前瞻:智能时代的融合路径 当前行业正经历数字化转型,单面机型通过加装AI补偿模块,已实现自适应学习功能。而双面机型则向多物理场耦合检测发展,集成温度-振动-电磁复合传感系统。值得关注的是,某德国厂商推出的混合式立式动平衡机,通过可编程机械臂实现单双面模式切换,成功将设备利用率提升至85%以上。这种柔性化设计预示着未来检测设备将突破形态界限,向智能感知终端进化。 结语 在工业精密制造的竞技场上,单双面立式动平衡机的差异已超越单纯的技术参数对比。它们如同精密仪器的双生花,在效率与精度的天平上寻找着动态平衡。当智能制造的浪潮席卷而来,这种差异正在演变为技术路线选择的风向标,指引着行业向更高阶的平衡美学迈进。
07
2025-06
单面动平衡机与双面动平衡机区别
单面动平衡机与双面动平衡机区别 一、工作原理的维度差异 单面动平衡机如同二维平面的校正师,仅针对旋转体单一校正平面进行振动力学分析。其核心逻辑基于”单平面平衡法”,通过测量单侧振动幅值与相位,计算出需加减的平衡质量。而双面动平衡机则构建三维空间模型,同步采集双平面振动信号,运用矢量合成原理解算复合不平衡量。这种差异如同平面几何与立体几何的分野,前者聚焦线性问题,后者破解空间耦合难题。 二、适用对象的形态适配 单面机如同精准的外科手术刀,专攻盘类零件(如飞轮、齿轮箱)的轴向不平衡。其校正精度可达0.1g·mm级,但面对长轴类工件(如电机转子、轧辊)时,单平面校正易引发”残余不平衡”。双面机则化身多维诊疗仪,通过双传感器阵列捕捉轴向与径向振动,特别适用于长度与直径比>0.2的旋转体。某航空发动机转子案例显示,双面校正使振动值从12μm降至1.8μm,验证了其空间解耦优势。 三、校正精度的数学建模 单面机采用傅里叶变换解析单频振动信号,其误差模型包含3个自由度:质量、相位、安装误差。而双面机引入卡尔曼滤波算法,构建包含6个状态变量的动态方程。某精密轴承测试表明,双面机在10000rpm工况下,平衡精度比单面提升40%,且对0.05mm级微小偏心更敏感。这种差异源于双面机能消除”陀螺力矩”对单平面校正的干扰。 四、操作流程的工艺演变 单面校正如同传统书法的单笔勾勒:安装工件→单点贴标→单次测量→单面配重。而双面流程更似数字绘画的图层叠加:双面贴标→同步采样→矢量分解→双面配重。某汽车涡轮增压器生产线数据显示,双面校正使停机时间减少35%,但需额外配置角度编码器和双通道分析仪。这种工艺升级背后,是传感器融合技术的突破。 五、成本效益的工程权衡 单面机如同经济型轿车,初始投资低(约15万元),维护成本可控,适合标准化生产。双面机则类比豪华SUV,设备成本达40-80万元,但能覆盖80%的复杂工况。某风电企业案例显示,双面机虽购置成本高3倍,但使叶片轴承寿命延长2.5倍,全生命周期成本反而降低18%。这种选择本质是短期投入与长期效益的博弈。 结语:技术演进的辩证法则 从单面到双面的跨越,不仅是检测维度的拓展,更是工业精密制造的哲学升华。当单面机在二维平面上绘制平衡曲线时,双面机已在三维空间重构动态平衡。这种技术分野恰似笛卡尔坐标系的延伸,前者定义平面规则,后者开启立体可能。在智能制造时代,选择单面还是双面,本质上是在精度需求与经济性之间寻找动态平衡点。
07
2025-06
单面动平衡机价格范围是多少
单面动平衡机价格范围是多少 ——技术参数、市场定位与行业隐性成本的多维透视 一、基础价格区间:从工业级到精密级的阶梯式分布 单面动平衡机的定价如同精密仪器的标尺,既受技术参数的刚性约束,又折射出市场供需的弹性博弈。主流工业级设备的价格区间通常在8万至30万元,这类机型以基础平衡功能为核心,适用于中小型电机、风机等常规工况。而高精度机型(如0.1g·mm级分辨率)则攀升至50万至120万元,其核心价值在于满足航空航天、精密机床等领域的严苛需求。值得注意的是,部分进口品牌(如HBM、MTS)的高端机型甚至突破200万元,这类设备往往搭载智能算法与自适应校正系统,形成技术溢价壁垒。 二、隐性成本:技术参数背后的”价格陷阱” 价格标签只是表象,真正的成本博弈藏匿于技术细节的迷宫之中。例如,传感器精度每提升0.1级,整机成本可能增加15%-20%;驱动电机功率从2.2kW升级至5.5kW,价格跨度可达30%以上。更隐蔽的差异在于软件生态——基础版平衡软件可能仅需数万元,而集成振动分析、故障诊断模块的版本溢价可达50%。此外,售后服务网络的覆盖密度(如是否提供24小时驻场调试)也会导致区域报价浮动10%-15%。 三、市场动态:供需关系与技术迭代的双重变奏 2023年数据显示,国内单面动平衡机市场呈现”哑铃型”结构:低端机型(50万元)占25%。这一分布背后是制造业升级的矛盾需求——中小型企业追求”性价比平衡”,而头部企业则押注智能化转型。值得关注的是,国产替代浪潮正重塑价格体系:以科德数控、华中数控为代表的本土品牌,通过模块化设计将中端机型价格压至25万-40万元,较进口品牌低30%-40%,同时保持90%以上的功能兼容性。 四、采购决策的三维坐标系 理性决策需构建”技术-成本-场景”的立体模型: 技术适配性:平衡精度需与被测工件的转速、质量成正比(如转速>10000rpm时,建议选择离心式平衡机); 全生命周期成本:包含耗材(如传感器探头)、维护频率、校准周期等隐性支出; 场景扩展性:是否预留升级接口以应对未来工艺升级需求。 五、未来趋势:智能化重构价格范式 随着AI驱动的自适应平衡算法普及,单面动平衡机正从”工具”进化为”智能体”。2024年行业预测显示,搭载机器学习模块的机型价格将上涨10%-15%,但其带来的效率提升(如平衡时间缩短40%)可能创造1:5的ROI回报。更深远的影响在于服务模式变革——部分厂商开始推出”按平衡次数付费”的订阅制,彻底打破传统硬件定价逻辑。 结语 单面动平衡机的价格不仅是数字游戏,更是技术、市场与产业生态的交响乐。在追求性价比的迷思中,唯有回归”需求本质”,方能在价格迷雾中锚定最优解。
07
2025-06
单面动平衡机如何校准和维护
单面动平衡机如何校准和维护 在工业生产中,单面动平衡机是一种至关重要的设备,它能够有效检测和校正旋转物体的不平衡,从而提升产品质量和生产效率。然而,要确保单面动平衡机始终保持高精度和稳定运行,校准和维护工作必不可少。 校准:精准的基础 初始检查 校准单面动平衡机,首先要进行细致的初始检查。检查机器的外观,看是否有明显的损坏、变形或松动的部件。任何细微的损坏都可能影响机器的平衡检测精度。同时,查看传感器的连接是否牢固,因为传感器是获取旋转物体数据的关键部件,连接不稳定会导致数据误差。还要检查测量系统的显示是否正常,确保能够准确读取测量结果。 标准件校准 使用标准件进行校准是单面动平衡机校准的重要环节。标准件具有已知的不平衡量,将其安装在动平衡机上进行测量。通过对比测量结果与标准件的实际不平衡量,对动平衡机的测量系统进行调整。这个过程需要多次测量和调整,以确保测量系统的准确性。校准过程中,要注意标准件的安装位置和方式必须严格按照操作手册进行,否则会引入额外的误差。 灵敏度校准 灵敏度校准也是不可忽视的。它能够确保动平衡机对不同大小的不平衡量都能准确响应。通过调整测量系统的增益和衰减参数,使动平衡机在测量不同量级的不平衡量时都能获得准确的测量结果。在进行灵敏度校准时,要使用不同量级的标准件进行测试,以验证校准效果。 维护:稳定的保障 清洁与润滑 定期清洁和润滑是单面动平衡机维护的基本工作。清洁机器表面的灰尘和杂物,防止其进入机器内部影响正常运行。特别是传感器和测量系统的部件,要保持清洁,避免灰尘干扰测量信号。同时,对机器的运动部件进行润滑,如轴承、导轨等。使用合适的润滑剂,按照规定的周期进行加注,能够减少部件的磨损,延长机器的使用寿命。 电气系统维护 电气系统是单面动平衡机的核心部分,维护好电气系统至关重要。定期检查电气线路的连接是否牢固,有无老化、破损的情况。如果发现电气线路有问题,要及时更换。还要检查电气控制柜内的温度和湿度,确保其在合适的范围内,避免过高的温度和湿度对电气元件造成损坏。此外,要定期对电气系统进行接地检查,保证操作人员的安全。 定期校准与精度验证 定期进行校准和精度验证是保证动平衡机长期稳定运行的关键。按照规定的时间间隔对动平衡机进行校准,确保其测量精度始终符合要求。同时,使用标准件进行精度验证,对比测量结果与标准值的差异。如果发现精度下降,要及时进行调整和维修。 单面动平衡机的校准和维护工作是一个系统而细致的过程。只有做好校准和维护工作,才能保证动平衡机的高精度和稳定运行,为工业生产提供可靠的保障。无论是校准过程中的精准调整,还是维护过程中的悉心呵护,都需要操作人员具备专业的知识和技能,严格按照操作手册进行操作。这样,单面动平衡机才能在工业生产中发挥出最大的作用。
07
2025-06
单面动平衡机如何选择校正半径
单面动平衡机如何选择校正半径 在使用单面动平衡机进行工件平衡校正时,校正半径的选择至关重要。它不仅影响到动平衡的精度和效果,还与整个校正过程的效率息息相关。以下将深入探讨如何合理选择单面动平衡机的校正半径。 校正半径的定义,是指从旋转中心到校正平面上校正质量施加位置的距离。它是动平衡计算中的一个关键参数,直接关系到不平衡量的大小和分布。不同的工件、不同的使用场景,对校正半径的要求也各不相同。 依据工件特性选择 工件的形状、尺寸和结构是选择校正半径的首要考虑因素。对于形状规则、质量分布均匀的圆盘类工件,校正半径可以选择在工件的外边缘。因为在这个位置施加校正质量,能够更有效地平衡工件的不平衡量。例如,汽车发动机的飞轮,其质量主要集中在圆盘的边缘部分,选择外边缘作为校正半径,可以使校正效果更加明显。 然而,对于一些形状复杂、质量分布不均匀的工件,就需要根据具体情况进行分析。比如,带有凸起、凹槽或内部结构复杂的工件,校正半径可能需要选择在质量集中的区域或靠近不平衡量较大的位置。这样可以减少校正质量的大小,提高校正效率。 考虑平衡精度需求 平衡精度是动平衡机校正的重要指标之一。不同的应用场景对平衡精度的要求也不同。在对平衡精度要求较高的场合,如航空发动机、高速离心机等,校正半径的选择需要更加谨慎。一般来说,较小的校正半径可以提高平衡精度,因为较小的半径意味着校正质量的微小变化对不平衡量的影响更大。但是,过小的校正半径也会增加校正的难度和成本,因为需要更精确的测量和控制。 相反,在对平衡精度要求相对较低的场合,如普通电机、风机等,可以选择较大的校正半径。这样可以减少校正质量的大小,降低校正成本。同时,较大的校正半径也更容易操作,提高了校正效率。 结合设备性能限制 单面动平衡机的自身性能也会对校正半径的选择产生限制。动平衡机的测量精度、最大允许校正质量等参数都会影响校正半径的选择。在选择校正半径时,需要确保所选的半径在动平衡机的性能范围内。 例如,如果动平衡机的最大允许校正质量较小,就不能选择过大的校正半径,否则可能会超出设备的承载能力,导致校正失败或损坏设备。此外,动平衡机的测量精度也会影响校正半径的选择。如果测量精度较低,选择过小的校正半径可能会导致测量误差增大,影响平衡效果。 实际操作经验积累 实际操作经验也是选择校正半径的重要参考。在长期的动平衡校正过程中,操作人员会积累大量的经验。通过对不同工件、不同校正半径的实际操作和效果评估,可以总结出一些适合特定工件的校正半径选择方法。 例如,在对某一类型的工件进行多次校正后,发现选择某个特定的校正半径可以获得最佳的校正效果。那么在后续的校正过程中,就可以优先选择这个半径。同时,操作人员还可以根据实际操作中遇到的问题,不断调整校正半径,以提高校正质量和效率。 单面动平衡机校正半径的选择需要综合考虑工件特性、平衡精度需求、设备性能限制和实际操作经验等因素。只有在充分了解这些因素的基础上,才能选择出最合适的校正半径,实现高效、精确的动平衡校正。
07
2025-06
单面动平衡机常见故障如何解决
单面动平衡机常见故障如何解决 单面动平衡机在工业生产中发挥着重要作用,不过在长期使用过程中难免会出现一些故障。下面为您详细介绍常见故障及其解决办法。 振动异常 当单面动平衡机出现振动异常时,原因可能是多方面的。可能是工件安装不当,没有准确地安装在平衡机的支撑装置上,导致在旋转过程中产生晃动。也有可能是平衡机的传感器出现问题,传感器故障会使得检测到的振动信号不准确,进而反馈给系统错误信息。另外,平衡机的机械结构松动也会造成振动异常,比如地脚螺栓松动,会使设备在运行时整体稳定性变差。 针对这些问题,首先要检查工件的安装情况,确保其安装牢固且位置准确。对于传感器,可以使用专业的检测设备进行校准和检测,若发现传感器损坏,应及时更换。而对于机械结构松动的情况,要仔细检查各个连接部位,拧紧松动的螺栓,必要时对设备进行整体的加固。 显示数据不准确 显示数据不准确是另一个常见的故障。这可能是由于系统参数设置错误,操作人员在设置参数时输入错误,会导致平衡机计算得出的结果偏差较大。此外,电气干扰也可能影响数据的准确性,周围的强电磁环境会干扰平衡机内部的电路,使显示的数据出现跳动或错误。还有可能是检测电路故障,检测电路中的元件损坏或焊点松动,会影响信号的传输和处理。 要解决显示数据不准确的问题,需要重新检查系统参数设置,确保各项参数与实际情况相符。对于电气干扰,可以采取屏蔽措施,如在平衡机周围安装电磁屏蔽罩,减少外界电磁干扰。若怀疑是检测电路故障,需要专业人员对检测电路进行全面检查,修复损坏的元件或重新焊接松动的焊点。 电机故障 电机故障会导致平衡机无法正常运行。电机不启动可能是由于电源故障,如电源线断路、保险丝熔断等。电机过热则可能是因为电机负载过大,长时间高负荷运行会使电机温度急剧上升。另外,电机的轴承损坏也会影响其正常运转,轴承磨损会增加电机的运转阻力。 对于电机不启动的情况,要检查电源连接是否正常,更换熔断的保险丝。若电机过热,需要检查负载情况,适当减轻电机的负载,同时检查电机的散热系统是否正常,清理散热通道,确保电机能够及时散热。当发现电机轴承损坏时,应及时更换新的轴承。 单面动平衡机在使用过程中出现故障并不可怕,只要我们了解常见故障的原因,并采取相应的解决措施,就能保证设备的正常运行,提高生产效率。在日常使用中,还应定期对平衡机进行维护和保养,及时发现潜在的问题,防患于未然。
07
2025-06
单面动平衡机推荐品牌有哪些
单面动平衡机推荐品牌有哪些 在机械制造、航空航天等众多领域,动平衡机对于保障旋转机械的平稳运行起着至关重要的作用。单面动平衡机作为动平衡机中的一个重要类别,广泛应用于各类盘状零件的平衡校正。以下为大家介绍几个值得推荐的单面动平衡机品牌。 申克(SCHENCK) 申克来自德国,在动平衡机领域可谓久负盛名。作为行业的先驱者,申克拥有超过百年的历史沉淀。其单面动平衡机以高精度和稳定性著称。先进的传感器技术,能精确捕捉转子的不平衡量;智能化的控制系统,可实现快速、准确的平衡校正。无论是小型的精密零件,还是大型的工业设备部件,申克的单面动平衡机都能出色完成任务。不过,申克产品的价格相对较高,但其卓越的性能和可靠的质量,依然使其成为众多高端企业的首选。 海克斯康(Hexagon) 海克斯康是一家全球性的企业,业务涵盖测量技术、工业软件等多个领域。该品牌的单面动平衡机融合了先进的测量技术和创新的设计理念。它采用了高精度的测量系统,能够快速、准确地检测出转子的不平衡位置和大小。并且,海克斯康的动平衡机具备良好的兼容性,可以与企业现有的生产管理系统无缝对接,实现生产过程的自动化和智能化。其产品在汽车制造、航空航天等行业得到了广泛应用。 上海** 上海**是国内动平衡机领域的知名品牌。它专注于动平衡机的研发、生产和销售,经过多年的发展,积累了丰富的技术经验。上海**的单面动平衡机具有性价比高的优势,产品价格相对较为亲民,适合广大中小企业。同时,其产品质量也有可靠保障,采用了先进的工艺和优质的零部件,确保了设备的稳定性和可靠性。此外,上海**还提供完善的售后服务,能够及时解决用户在使用过程中遇到的问题。 爱德蒙(CEMB) 爱德蒙来自意大利,是一家专业从事动平衡技术研究和产品制造的企业。该品牌的单面动平衡机以其独特的设计和先进的技术受到用户的青睐。爱德蒙的动平衡机采用了先进的数字信号处理技术,能够有效提高测量的精度和可靠性。并且,其产品操作简单、维护方便,降低了用户的使用成本。在欧洲市场,爱德蒙的动平衡机拥有较高的市场份额,在全球范围内也有一定的知名度。 选择单面动平衡机时,企业应根据自身的生产需求、预算等因素综合考虑。上述这些品牌都有各自的特点和优势,能够为不同用户提供合适的解决方案。