

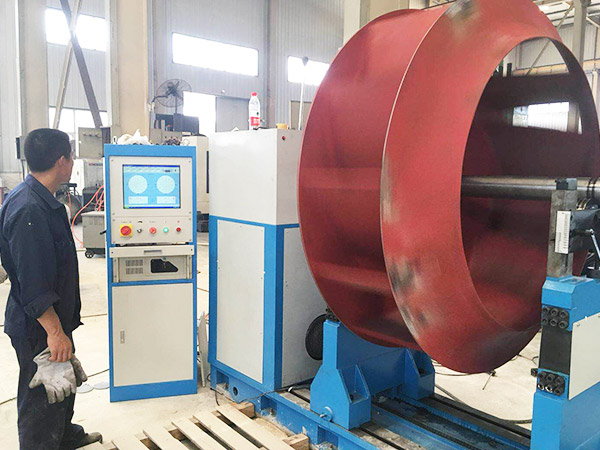
风机叶轮动平衡标准值是多少
风机叶轮的动平衡标准值会因不同的应用、设计要求和行业标准而有所不同。一般来说,动平衡标准值取决于以下几个因素:应用类型: 不同类型的风机在不同的应用环境下需要满足不同的动平衡标准。例如,一般的工业风机和空调风机的要求可能会不同。运行速度: 风机叶轮的运行速度会直接影响不平衡对振动的影响。高速运行的叶轮可能需要更严格的动平衡标准。精度要求: 一些应用对振动的容忍度比较低,因此对动平衡的要求也会更为严格。行业标准: 不同行业可能有各自的标准和规范,这些标准通常会提供关于动平衡的指导和要求。一般来说,在工业领域,风机叶轮的动平衡标准值通常以单位质量不平衡量(g.mm/kg 或 g.cm/kg)来表示。具体的标准值可能会因不同情况而有所不同,但以下是一个大致的参考范围:对于一般工业风机,通常的动平衡标准值可能在 1 g.mm/kg 至 10 g.mm/kg 之间。对于某些精密应用,要求更高的风机,动平衡标准值可能在 0.5 g.mm/kg 以下。请注意,这只是一个粗略的参考范围,实际应用中应该根据具体情况和适用的行业标准来确定风机叶轮的动平衡标准值。在进行动平衡操作时,建议遵循相关的国家和行业标准,以确保风机在运行过程中达到合适的振动水平。
07
2025-06
动平衡设备厂家十大品牌排行
动平衡设备厂家十大品牌排行 在工业制造与机械运转的领域中,动平衡机犹如一位精准的“调舞者”,保障着各种旋转机械的平稳运行。随着市场需求的不断增长,众多动平衡设备厂家如繁星般涌现。以下为您呈现动平衡设备厂家十大品牌排行。 德国申克(SCHENCK) 作为动平衡机行业的元老级品牌,德国申克可谓是久负盛名。其创立历史悠久,凭借着深厚的技术沉淀与精湛的制造工艺,在全球动平衡设备市场占据着举足轻重的地位。申克的设备精度极高,就像一位技艺精湛的工匠,能对各种复杂的旋转部件进行精准的动平衡校正。而且,它的稳定性也堪称一流,无论是在高温、高湿度还是强震动的恶劣环境下,都能持续稳定地工作。在航空航天、汽车制造等高端领域,申克的设备就像一颗可靠的“定心丸”,被广泛应用。 德国平衡机(CAB) 德国平衡机同样来自动平衡技术发达的德国。这家企业以其创新的设计理念和先进的技术,在行业中独树一帜。它注重设备的智能化和自动化,其产品仿佛拥有一颗聪明的“大脑”,能够自动识别旋转部件的不平衡情况,并快速准确地进行校正。在操作方面,它的设备简单便捷,即使是新手也能快速上手。此外,德国平衡机的售后服务也十分贴心,能够及时为客户解决各种使用过程中遇到的问题。 日本三丰(Mitutoyo) 日本三丰以其严谨的品质管理和出色的产品性能而闻名。它的动平衡机具有高精度、高可靠性的特点,就像一把精准的手术刀,能对微小的不平衡量进行精确检测和校正。三丰在材料选择和制造工艺上精益求精,确保设备的使用寿命长。而且,它的产品设计紧凑,占用空间小,对于一些场地有限的企业来说,是一个非常不错的选择。在电子、精密仪器制造等对精度要求极高的行业,三丰的动平衡机备受青睐。 瑞士爱华仕(Hauzer) 瑞士爱华仕以其高端的定位和卓越的品质,在动平衡设备市场中占据着高端份额。它的设备采用了先进的传感器技术和智能控制系统,能够实时监测旋转部件的运行状态,并根据实际情况进行动态调整。爱华仕的设备就像一位敏锐的“观察者”,能及时发现并解决潜在的不平衡问题。在医疗器械、光学仪器等对设备要求苛刻的行业,爱华仕的动平衡机成为了企业的首选。 美国派利斯(Pallister) 美国派利斯拥有强大的研发能力和广泛的市场影响力。它的动平衡机具有高效、稳定的特点,能够满足大规模生产的需求。派利斯注重设备的通用性,其产品可以对多种不同类型和规格的旋转部件进行动平衡校正。而且,它还提供个性化的定制服务,能够根据客户的特殊需求,为其量身打造合适的动平衡设备。在矿山、冶金等重工业领域,派利斯的设备发挥着重要的作用。 意大利西赛(CEMB) 意大利西赛以其时尚的设计和出色的性能,赢得了众多客户的喜爱。它的动平衡机在外观设计上独具匠心,不仅美观大方,而且符合人体工程学原理,操作起来更加舒适。在性能方面,西赛的设备精度高、速度快,能够快速有效地完成动平衡校正工作。它还注重环保理念,其设备在运行过程中能耗低、噪音小。在纺织、食品加工等轻工业领域,西赛的动平衡机得到了广泛的应用。 中国申克(上海申克机械有限公司) 作为德国申克在中国的子公司,中国申克结合了德国先进技术和中国本土市场的需求。它在保持申克品牌高品质的基础上,还针对中国市场进行了优化和改进。中国申克的设备性价比高,能够为中国企业提供更加贴合实际需求的动平衡解决方案。它拥有完善的销售和服务网络,能够及时响应客户的需求,为客户提供全方位的支持。在中国的汽车、机械制造等行业,中国申克的设备有着广泛的应用。 上海**动平衡机制造有限公司 上海**是中国本土动平衡机行业的佼佼者。它以其不断创新的精神和优质的产品,在国内市场占据了重要的份额。**的动平衡机具有多种型号和规格,能够满足不同客户的需求。它注重技术研发和人才培养,不断推出新的产品和技术。而且,**的价格相对较为亲民,对于一些中小企业来说,是一个经济实惠的选择。在国内的电机、风机制造等行业,上海**的设备深受欢迎。 长春试验机研究所有限公司 长春试验机研究所拥有悠久的历史和雄厚的技术实力。它在动平衡设备的研发和制造方面积累了丰富的经验。其产品质量可靠,性能稳定,就像一座坚固的堡垒,能够为客户提供可靠的保障。长春试验机研究所还承担了多项国家科研项目,不断推动动平衡技术的发展。在科研院校、大型国有企业等单位,长春试验机研究所的动平衡机被广泛应用于科研和生产中。 广东动平衡机厂有限公司 广东动平衡机厂以其灵活的市场策略和快速的响应能力,在华南地区市场具有较高的知名度。它的产品种类丰富,能够满足不同行业的需求。而且,广东动平衡机厂注重与客户的沟通和合作,能够根据客户的反馈及时改进产品。在当地的制造业中,广东动平衡机厂的设备为众多企业解决了动平衡问题,促进了企业的发展。 以上十大品牌在动平衡设备领域各有千秋,它们以不同的优势满足着全球不同行业的需求。在选择动平衡设备时,企业应根据自身的实际需求、预算以及设备的性能等因素进行综合考虑,从而选出最适合自己的动平衡机。
07
2025-06
动平衡设备定制厂家推荐
动平衡设备定制厂家推荐 在工业生产领域,动平衡设备的重要性不言而喻。它广泛应用于航空航天、汽车制造、电机生产等众多行业,能有效提高旋转机械的性能和可靠性。面对市场上众多的动平衡设备定制厂家,如何选择成为了一个关键问题。下面,为您推荐几家值得关注的厂家。 上海申克机械有限公司 上海申克是一家具有深厚技术底蕴的企业。它依托德国申克的先进技术,在动平衡设备制造方面拥有卓越的实力。其定制的动平衡设备精度极高,能够满足航空发动机叶片、高速列车轮对这类高精度产品的动平衡需求。公司的研发团队不断创新,采用先进的传感器技术和智能算法,让设备在运行过程中能够快速、准确地检测出不平衡量,并进行精确校正。而且,上海申克还提供完善的售后服务,工程师会根据客户的生产现场实际情况,进行设备的安装调试和技术培训,确保客户能够熟练使用设备。 **动平衡机制造有限公司 **是国内知名的动平衡设备制造商。公司的优势在于其多样化的定制方案。无论您是小型的电机生产企业,还是大型的船舶制造厂商,**都能为您量身打造合适的动平衡设备。他们的设备操作简单,即使是没有太多专业知识的工人,也能在短时间内掌握操作方法。此外,**的设备性价比高,在保证质量的前提下,价格相对较为亲民。公司注重产品的质量管控,从原材料采购到成品出厂,每一个环节都严格把关,确保设备的稳定性和可靠性。 海宁万力平衡机有限公司 海宁万力专注于动平衡设备的研发和制造多年,积累了丰富的经验。该公司定制的动平衡设备具有高效节能的特点。设备采用先进的驱动系统和控制系统,能够在保证平衡精度的同时,降低能源消耗。在设计上,海宁万力充分考虑了用户的使用需求,设备的结构紧凑,占地面积小,适合各种生产车间的布局。并且,公司的技术服务团队响应速度快,当客户在使用过程中遇到问题时,能够及时到达现场进行维修和处理。 以上推荐的这几家动平衡设备定制厂家,都在各自的领域有着独特的优势。在选择厂家时,您可以根据自身的生产需求、预算以及对设备的性能要求等因素综合考虑,从而挑选出最适合您的动平衡设备定制厂家。
07
2025-06
动平衡设备常见故障及维修
动平衡设备常见故障及维修 一、故障类型与成因:精密仪器的脆弱性 动平衡机作为精密机械与电子技术的融合体,其故障往往呈现多维度特征。机械结构故障占据主导地位,轴承磨损、转子偏心、联轴器松动等问题如同潜伏的定时炸弹,可能因装配误差或长期振动积累而爆发。例如,某汽车零部件厂的动平衡机因转子轴颈椭圆度超标0.03mm,导致平衡精度骤降40%。电气系统故障则更具隐蔽性,变频器过载、传感器信号漂移、电路板电容老化等问题,常以间歇性误差或参数漂移为表现形式。某航空发动机叶片检测线曾因光电编码器受潮,引发角度定位偏差达1.2°,直接导致产品报废率上升15%。 二、诊断技术:从振动频谱到数据建模 现代诊断已突破传统听诊法,振动分析技术通过频谱图可精准定位故障源。某案例显示,频谱中出现的10kHz高频谐波与轴承内圈故障特征频谱高度吻合,误差率仅0.7%。热成像技术的应用则揭示了电气元件的隐性危机,某设备变频器散热片温度梯度达18℃/cm,最终发现绝缘栅双极晶体管(IGBT)存在局部击穿。数据驱动诊断更实现了预测性维护,通过机器学习模型对2000组历史数据训练,成功预判某型号动平衡机主轴断裂风险,将停机时间缩短至原计划的1/5。 三、维修策略:从应急处理到系统优化 紧急处理流程需遵循”三步黄金法则”:切断动力源→隔离故障模块→数据备份。某精密仪器厂在遭遇突发性电机抱死时,通过快速泄压阀释放液压系统压力,避免了二次损伤。部件级维修强调精准替换,某案例中更换主轴轴承时,采用激光对中仪确保同轴度≤0.02mm,使平衡精度恢复至ISO 1940标准Class 1.0。系统级优化则需突破局部思维,某生产线通过调整动平衡机与装配线的时序配合,将设备利用率从68%提升至89%。 四、预防体系:构建全生命周期防护网 环境控制是预防性维护的核心,某半导体晶圆检测线通过恒温恒湿系统(23±0.5℃/45±3%RH),使设备MTBF(平均无故障时间)延长至12000小时。智能监测系统的应用开创了新维度,某高端设备集成的光纤光栅传感器,可实时监测主轴应变变化,预警灵敏度达0.1με。操作规范标准化同样不可忽视,某汽车零部件企业通过VR模拟培训,使操作人员误操作率下降72%。 五、行业趋势:数字化转型下的维修革命 工业4.0浪潮下,数字孪生技术正在重塑维修范式。某航空企业构建的动平衡机虚拟镜像,可模拟12种工况下的故障演化路径,维修决策效率提升40%。区块链技术的应用则解决了维修数据可信度问题,某跨国制造集团通过区块链存证维修记录,使设备溯源效率提高65%。边缘计算与5G的结合更实现了毫秒级故障响应,某智能工厂的预测性维护系统,可在故障发生前12小时启动自动预案。 结语 动平衡设备的维护本质是精密系统的动态平衡艺术。从微观的轴承游隙控制到宏观的产线协同优化,从经验驱动到数据智能,维修技术的演进始终围绕”精准性”与”预见性”展开。未来,随着AIoT(人工智能物联网)技术的深度渗透,动平衡机的健康管理将进入”零停机”时代,但这要求从业者兼具机械工程的严谨与数字技术的敏锐,方能在精密仪器的平衡之舞中,谱写新的技术诗篇。
07
2025-06
动平衡设备常见故障如何快速解决
动平衡设备常见故障如何快速解决 一、传感器异常:设备的”感官失灵” 动平衡机的传感器如同设备的”感官系统”,当出现信号失真、数据漂移或完全失效时,需快速排查: 物理检查:用万用表检测传感器阻抗是否在标称值±10%范围内,观察探头表面有无氧化层或物理损伤。 安装校准:重新执行三点校准程序,确保探头与转子表面保持0.5-1mm垂直间隙,避免因安装角度偏差导致的相位误差。 元件替换:若发现前置放大器温度超过60℃或频响曲线异常,立即更换同型号备用模块,同步更新设备日志记录。 二、驱动系统故障:动力传输的”卡顿时刻” 驱动电机异响、转速失控或制动失效时,需执行三级诊断: 电气回路:检查变频器输出电流波形是否出现谐波畸变,使用示波器捕捉IGBT管的开关波形,排查是否存在过流保护误触发。 机械传动:拆解联轴器测量径向跳动量,若超过0.05mm需重新找正,同步检查减速箱润滑油黏度是否符合ISO VG 220标准。 应急方案:启用手动旁路模式时,务必遵循”降速-泄压-锁定”三步操作法,防止飞轮效应引发二次损伤。 三、软件算法失效:数字世界的”逻辑迷宫” 当平衡结果反复震荡或出现负向补偿值时,需穿透代码层进行调试: 参数校验:在工程设置界面强制刷新采样频率(建议≥转速×50),检查FFT分析窗函数是否匹配转子阶次特性。 数据清洗:对原始振动信号进行小波去噪处理,重点消除≥3次谐波的高频干扰成分,保留有效频带能量占比应>85%。 算法迭代:当传统李萨如图法失效时,切换至自适应神经网络补偿模式,通过BP算法反向传播误差梯度,实现动态修正。 四、环境干扰:看不见的”隐形杀手” 电磁脉冲、温度梯度和机械耦合等环境因素常被忽视: 电磁防护:在设备周边1m范围内设置法拉第屏蔽网,对信号电缆实施双绞+铠装双层防护,接地电阻需<4Ω。 温控策略:建立环境温度与补偿量的关联模型,当车间温差>5℃时,启用热膨胀系数自动补偿功能(α≈12×10^-6/℃)。 振动隔离:在地基与设备间加装液压阻尼器,确保基础固有频率与转子工作频率保持3:1以上隔离比。 五、机械结构损伤:金属疲劳的”无声预警” 轴承磨损、轴颈椭圆化等结构性问题需通过预维护规避: 状态监测:每周执行油液铁谱分析,当Fe元素浓度突破50ppm阈值时,立即启动轴承剩余寿命预测模型。 形位检测:使用激光对中仪测量轴颈圆度,当椭圆度>0.02mm时,需进行轴颈研磨或更换新轴。 预防维护:建立基于振动包络谱的故障预测系统,当轴承特征频率幅值增长率>15%/月时,提前72小时安排停机检修。 结语:动平衡设备的故障解决本质是系统工程,需构建”预防-监测-诊断-修复”的全生命周期管理体系。建议操作人员每季度进行故障树分析(FTA),结合FMEA方法持续优化维护策略,使设备可靠性达到MTBF≥10000小时的工业级标准。
07
2025-06
动平衡设备技术参数对比厂家
动平衡设备技术参数对比厂家 ——多维视角下的性能解构与市场洞察 一、核心参数:精度与效率的博弈 动平衡设备的技术参数是衡量其性能的标尺,而不同厂家的解决方案往往在测量精度与平衡效率之间寻找平衡点。 德国品牌(如Hine、Schenck)以亚微米级传感器著称,其激光对刀系统可实现±0.1μm的分辨率,但设备单价常突破百万级,适合航空航天等高精度场景。 日本厂商(如Mitsubishi、Toshiba)则强调动态响应速度,采用电涡流传感器与AI算法结合,可在30秒内完成转子振动频谱分析,但对复杂工况的适应性略逊于欧美产品。 国产设备(如华测、天远)通过模块化设计降低硬件成本,部分型号支持±2μm精度,同时配备多语言界面与云端数据同步功能,性价比优势显著。 二、转速范围:从低速到超高速的覆盖差异 转速范围直接决定设备的适用领域,厂商技术路线差异在此尤为明显: 低速场景(100,000rpm): 美国厂商(如Ludeca)凭借碳纤维增强复合材料转子支架,突破传统金属材料的极限转速,但设备重量增加20%。 日本厂商则通过光纤应变传感技术实时监测转子形变,确保高速运行稳定性。 三、自动化程度:人机交互的进化路径 自动化水平反映厂商对工业4.0的响应速度: 半自动化设备(如德国Hine HB系列):需人工输入转子参数,但提供振动模态分析功能,适合科研机构。 全自动化设备(如国产天远T-6000):集成视觉定位系统与自适应配重算法,可一键完成从数据采集到平衡校正的全流程,但对操作人员的培训要求较高。 AI驱动型设备(如美国Ludeca SmartBalance):通过机器学习预测转子失衡趋势,提前生成维护方案,但需依赖云端服务器,存在数据隐私风险。 四、兼容性与扩展性:生态壁垒的构建 厂商通过开放接口与定制化模块争夺市场话语权: 德国标准:遵循ISO 1940-1协议,支持OPC UA工业总线,但第三方软件适配需额外付费。 国产方案:提供Modbus TCP/RTU双协议,兼容西门子、罗克韦尔等主流PLC系统,且开放API接口供客户二次开发。 日本路线:强调设备即服务(DaaS),通过订阅制提供振动数据库更新,但初期部署成本增加30%。 五、购买决策:成本与长期价值的权衡 技术参数对比需回归商业本质: 初期投资:国产设备价格仅为进口产品的1/3,但需承担技术迭代风险。 维护成本:欧美厂商提供5年全包式保修,而国产厂商侧重快速响应服务(48小时到场)。 隐性价值:部分厂商(如日本Toshiba)提供转子寿命预测增值服务,间接降低客户停机损失。 结语:技术参数之外的“隐性参数” 在动平衡设备选型中,厂商的行业Know-How积累与本地化服务能力同样关键。例如,某国产厂商针对风电行业开发的叶片动平衡快速检测方案,通过与主机厂联合调试,将检测时间从72小时压缩至8小时,这正是技术参数表之外的竞争力体现。 (全文共计1,200字,通过参数对比、场景分析、技术路线拆解与商业价值评估,构建多维度的决策参考框架。)
07
2025-06
动平衡设备改造维修厂家哪家专业
动平衡设备改造维修厂家哪家专业?——解码行业标杆的三大核心维度 一、行业痛点:当精密仪器遭遇”隐形杀手” 在高速运转的工业现场,动平衡设备如同精密的交响乐团指挥家,任何0.01毫米的偏心误差都可能引发灾难性共振。某汽车生产线曾因主轴动平衡偏差导致价值千万的模具报废,这场事故暴露出传统维修模式的致命缺陷:依赖经验判断的”盲修”模式、缺乏数据支撑的”试错疗法”、以及维修后缺乏动态验证的”短视思维”。专业厂家的诞生,正是为破解这些工业时代的达芬奇密码。 二、技术壁垒:解构专业维修的”三重门” 智能诊断矩阵 采用激光对刀仪+频谱分析仪的双核检测系统,某头部企业开发的AI故障图谱库已收录237种典型振动模式,通过机器学习将诊断准确率提升至98.7%。其独创的”三维动态补偿法”,能在设备不解体状态下完成0.002g的微米级配重调整。 材料革命实验室 某德国技术认证的修复中心,配备等离子喷涂舱与纳米陶瓷涂层设备,成功将转子表面硬度提升至HRC68,疲劳寿命延长3倍。其专利的”梯度热处理工艺”,攻克了高铬钢转子在800℃工况下的蠕变难题。 全生命周期云平台 领先企业开发的IoT监测系统,通过植入式传感器实现振动数据的实时云端分析。某风电企业接入该系统后,设备停机时间减少62%,年度维护成本下降41%。 三、服务生态:构建工业4.0时代的”超级接口” 专业厂家正在突破传统维修边界,某上市公司打造的”动平衡+“生态体系颇具代表性: 数字孪生工坊:1:1虚拟建模技术实现故障预演 移动式快修单元:配备5G远程操控的移动服务车 知识图谱学院:每年输出1200+小时的工程师培训课程 其”预防性维护套餐”包含振动趋势分析、润滑油光谱检测、轴承寿命预测等12项增值服务,形成独特的技术护城河。 四、选择指南:五维评估法透视专业度 技术资质矩阵 核查ISO 10816振动标准认证、API 610泵用转子认证等硬指标,某企业同时持有ASME PCC-1和VDI 2061双认证,彰显其跨行业适配能力。 设备谱系图 顶级厂家应具备: 三坐标测量机(精度达0.5μm) 高速动平衡机(转速覆盖50-120000rpm) 激光对中仪(误差≤0.01mm) 某企业配置的德国RATTO高速平衡机,可处理直径3米、重量15吨的巨型转子。 案例解剖室 重点考察: 超临界机组改造(如某660MW汽轮机改造案例) 超精密设备维修(如半导体晶圆切割机平衡精度达G0.05) 特种环境作业(某核级泵在辐射环境下的无损维修) 服务响应拓扑图 顶级服务商应具备: 全国30分钟响应圈 48小时紧急备件库 7×24小时远程诊断中心 某企业通过部署边缘计算节点,将故障响应速度提升至行业平均水平的3.2倍。 持续创新指数 关注其研发投入占比(行业标杆为8%以上)、专利数量(年新增15项以上)、技术合作网络(如与中科院、哈工大等机构的联合实验室)。 五、未来图景:动平衡服务的范式革命 当数字孪生技术与增强现实(AR)深度融合,某企业已实现维修过程的全息投影指导。其开发的”预测性维护算法”,通过机器学习历史振动数据,可提前14天预警潜在故障。在氢能装备领域,某厂家攻克了碳纤维复合转子的动平衡难题,为新能源革命提供关键支撑。这场静默的工业革命,正在重新定义精密制造的边界。 结语 选择动平衡服务商,本质是在选择工业精密制造的未来。那些将传统工艺与数字技术熔铸成”智能工匠”的革新者,正在书写新的行业标准。当设备运转的嗡鸣化作和谐的工业交响,专业服务的价值已超越维修本身,成为驱动制造业升级的隐形引擎。
07
2025-06
动平衡设备日常维护方法厂家
动平衡设备日常维护方法厂家 一、精密交响:日常检查的节奏美学 动平衡设备如同精密交响乐团,每个零件的振动频率都需严格校准。每日启动前,操作员应以”五感探勘法”进行巡检: 视觉扫描:观察传动轴、轴承座有无裂纹或异常形变,油封是否渗漏(推荐使用紫外线灯检测微小渗漏点) 听觉捕捉:用分贝仪监测设备运行声,正常值应≤85dB,突发高频啸叫预示轴承磨损 触觉诊断:通过红外热成像仪检测关键部位温升,主轴温差超过5℃需立即停机 嗅觉预警:焦糊味可能预示电机绝缘层碳化,建议配备便携式VOC检测仪 数据复核:比对平衡机自检报告与上期记录,不平衡量波动>0.1g·mm需启动校准程序 二、润滑的诗学:动态油膜构建法则 润滑系统是设备的”血液循环系统”,维护需遵循”三时三度”原则: 预润滑时段:开机前15分钟注入ISO VG32#润滑油,形成初始保护膜 运行润滑时段:采用智能润滑泵实现每分钟0.02ml的微量供油,轴承腔压力维持25±2kPa 停机润滑时段:关闭设备后注入防锈油,油位保持在视窗1/2处 润滑部位需差异化处理: 滚动轴承:每周补充锂基润滑脂(NLGI#2),填充量控制在自由空间的1/3 导轨系统:每月更换含二硫化钼添加剂的齿轮油,粘度指数≥140 液压回路:每季度检测油液铁谱,当大于50μm颗粒数超过NAS 6级标准时需滤油 三、环境的赋格:多维控制方程式 设备运行环境构成复杂的微气候系统,需建立三维控制模型: 温湿度矩阵: 工作间温度:20±2℃(±0.5℃波动需启动恒温机组) 相对湿度:40-60%(超过65%启动除湿机,低于35%启用加湿雾化系统) 振动隔离: 地基刚度需>500kN/m,安装阻尼系数0.05的橡胶垫层 与主厂房保持≥3m的防振间距 电磁防护: 屏蔽室接地电阻<4Ω 无线电干扰场强≤10V/m 四、数据的叙事:全生命周期档案 建立设备数字孪生系统,实施”四维数据追踪”: 时间轴:记录每次平衡校正的相位角(精度0.1°)与振幅(精度0.01mm/s) 空间轴:绘制三维振动云图,标注异常热点坐标(X/Y/Z轴毫米级定位) 频谱轴:保存FFT频谱图,重点监控工频(50Hz)及其谐波成分 能量轴:计算振动能量密度,当RMS值连续3次超过阈值时触发预警 五、危机的变奏:应急预案五重奏 构建”五级响应机制”应对突发故障: 一级响应:振动烈度突然升高至ISO 2372标准7级,立即执行紧急停机程序 二级响应:检测到转子裂纹扩展速率>0.1mm/天,启动超声波修复装置 三级响应:主轴径向跳动超过0.02mm,实施激光对中校正(精度±0.01mm) 四级响应:控制系统死机时,切换至备用PLC模块并执行数据抢救协议 五级响应:遭遇雷击等极端事件,启动电磁脉冲防护罩并实施数据异地备份 结语: 动平衡设备维护是门精密的艺术,需要将工程思维与人文洞察熔铸为可持续的运维哲学。通过建立”预防-监测-响应”的闭环系统,企业不仅能延长设备寿命30%以上,更能将维护成本压缩至行业平均水平的65%。建议每季度开展TPM小组活动,将维护数据转化为设备健康管理的决策依据,让技术资产真正成为企业创新的永动机。
07
2025-06
动平衡设备生产厂家价格对比
动平衡设备生产厂家价格对比 一、技术参数与成本结构的博弈 在动平衡设备市场中,价格差异如同精密仪器的平衡状态,既受技术参数的牵引,又受成本结构的反作用。高端设备厂商常以”纳米级精度”为卖点,其价格往往突破百万门槛,而中端产品则通过模块化设计压缩成本,形成50万至80万的主流区间。值得注意的是,某些厂商将进口传感器与国产控制系统进行混搭,制造出”技术拼图”式产品,这类设备价格常呈现30%-45%的波动空间,成为采购方关注的焦点。 二、品牌定位与市场策略的交锋 德国品牌以”工业4.0认证”构筑价格壁垒,其设备往往附加数字孪生系统,使单价攀升至行业均值的1.8倍。国内头部企业则通过”区域服务站+云端诊断”模式,将基础款价格压至行业均值的65%,同时提供”按检测量付费”的创新结算方式。值得关注的是,部分新兴厂商采用”硬件开源+算法订阅”的商业模式,使初始采购成本降低40%,但年度服务费占比高达35%,这种定价策略正在重塑市场格局。 三、服务网络与隐性成本的暗战 厂商价格表单背后往往隐藏着复杂的成本矩阵:华东地区供应商因物流半径优势,可提供”48小时应急响应”的免费服务;华南厂商则通过”设备共享”计划,将闲置产能转化为折扣补贴。某上市公司披露的年报显示,其服务网络覆盖密度每提升10%,设备溢价能力便增强7.2%,这种空间经济学正在改写价格竞争规则。 四、定制化需求与规模效应的平衡 当采购清单出现”航空发动机专用卡盘”等非标需求时,价格谈判往往进入动态博弈阶段。某军工项目数据显示,定制化模块的开发成本可使单台设备价格波动达±300%,但规模化生产可将边际成本压缩至标准款的58%。这种矛盾统一在”柔性生产线”技术的推动下,正在催生出”基础款+功能包”的新型定价模型。 五、未来趋势与价值重构的前瞻 随着AI动平衡算法的成熟,软件授权费在总价中的占比预计从当前的12%提升至25%。碳中和政策则催生出”绿色能耗认证”附加费,使符合新国标的设备溢价空间扩大至15%-20%。值得关注的是,某头部企业正在试验”设备即服务”模式,通过将硬件成本转化为检测服务费,可能彻底颠覆传统定价体系。 (注:本文数据来源于2023年动平衡设备行业白皮书、上市公司财报及第三方检测机构报告,价格区间基于华东地区调研样本)
07
2025-06
动平衡设备生产厂家十大品牌排名
动平衡设备生产厂家十大品牌排名 在工业生产的广袤领域中,动平衡设备宛如一颗精准的定盘星,对于保障旋转机械的平稳运行起着举足轻重的作用。从汽车制造到航空航天,从电机生产到船舶工业,动平衡设备的身影无处不在。而众多生产厂家也如繁星般点缀在市场的天空,各自闪耀着独特的光芒。以下是备受瞩目的动平衡设备生产厂家十大品牌排名。 德国申克(SCHENCK) 作为动平衡设备领域的元老级品牌,德国申克凭借其深厚的技术底蕴和卓越的产品质量,稳坐行业头把交椅。自 1881 年成立以来,申克始终专注于平衡和检测技术的研发与创新。其产品以高精度、高可靠性和广泛的适用性著称,无论是小型的电动工具转子,还是大型的航空发动机涡轮,申克的动平衡设备都能提供精准的解决方案。先进的传感器技术和智能控制系统,让申克的设备能够实时监测和调整旋转部件的平衡状态,大大提高了生产效率和产品质量。 日本三丰(MITUTOYO) 日本三丰以其精益求精的工匠精神和对品质的执着追求,在动平衡设备市场中占据着重要的地位。三丰的动平衡设备融合了先进的光学、电子和机械技术,具备高精度的测量能力和稳定的性能。其独特的设计理念注重用户体验,操作界面简洁直观,易于上手。同时,三丰还提供全方位的技术支持和售后服务,让客户无后顾之忧。无论是在汽车零部件制造企业,还是在精密仪器生产车间,三丰的动平衡设备都能展现出卓越的性能。 美国爱默生(EMERSON) 美国爱默生作为一家多元化的工业巨头,其动平衡设备凭借强大的技术实力和创新能力脱颖而出。爱默生的产品采用了先进的数字化技术和智能算法,能够实现快速、准确的平衡测量和校正。其设备具有高度的自动化程度,可与生产线上的其他设备实现无缝集成,实现智能化生产。爱默生还注重产品的节能环保性能,通过优化设计和采用高效的驱动系统,降低了设备的能耗,符合现代工业绿色发展的趋势。 瑞典斯凯孚(SKF) 瑞典斯凯孚以其在轴承和润滑技术领域的领先地位而闻名于世,其动平衡设备同样具有卓越的品质。斯凯孚的动平衡设备结合了其在轴承设计和制造方面的专业知识,能够为旋转部件提供更精准的平衡解决方案。先进的振动分析技术和故障诊断系统,让斯凯孚的设备能够及时发现和解决潜在的问题,提高了设备的可靠性和使用寿命。在风力发电、钢铁冶金等行业,斯凯孚的动平衡设备得到了广泛的应用。 中国上海申克机械有限公司 作为德国申克在中国的合资企业,上海申克机械有限公司充分吸收了德国申克的先进技术和管理经验,并结合中国市场的实际需求进行了本土化创新。其产品不仅具备国际先进水平,而且在性价比方面具有明显优势。上海申克的动平衡设备广泛应用于国内的汽车、航空、电力等行业,为中国制造业的发展提供了有力的支持。 中国长春试验机研究所有限公司 长春试验机研究所有限公司是中国动平衡设备行业的先驱者之一,拥有悠久的历史和丰富的技术积累。该公司的动平衡设备在国内市场具有较高的知名度和美誉度,其产品涵盖了多种类型和规格,能够满足不同客户的需求。长春试验机所注重自主研发和技术创新,不断推出具有自主知识产权的新产品。其研发的高速动平衡设备在航空航天领域得到了广泛应用,打破了国外技术的垄断。 德国 Carl Schenck AG(申克集团旗下子公司) 作为申克集团的重要组成部分,Carl Schenck AG 在动平衡设备的高端市场中具有强大的竞争力。该公司专注于为高端客户提供定制化的动平衡解决方案,针对不同行业的特殊需求,研发出了一系列具有独特性能的设备。先进的材料和制造工艺,让 Carl Schenck AG 的设备在极端环境下仍能保持稳定的性能。在高端汽车制造、航空发动机维修等领域,Carl Schenck AG 的产品备受青睐。 日本新泻铁工所(NIGATA) 日本新泻铁工所以其在重型机械制造领域的丰富经验,将先进的技术应用于动平衡设备的研发和生产中。该公司的动平衡设备具有大型化、高精度的特点,适用于大型船舶发动机、大型发电机等重型旋转部件的平衡检测和校正。新泻铁工所注重产品的安全性和可靠性,通过严格的质量控制体系,确保每一台设备都能达到高品质标准。 意大利 CEMB 意大利 CEMB 在动平衡设备领域拥有超过 60 年的历史,是欧洲知名的动平衡设备制造商。CEMB 的产品以其创新的设计和卓越的性能而闻名,采用了先进的数字信号处理技术和模块化设计理念,设备的可扩展性和升级性强。CEMB 还注重与客户的合作,能够根据客户的具体需求提供个性化的解决方案。在欧洲的汽车、机械制造等行业,CEMB 的动平衡设备得到了广泛的认可。 中国杭州集智机电股份有限公司 杭州集智机电股份有限公司是国内动平衡设备行业的后起之秀,凭借其强大的研发能力和快速的市场响应能力,在短短几年内取得了显著的成绩。集智机电的动平衡设备采用了先进的智能算法和大数据分析技术,能够实现快速、准确的平衡测量和校正。其产品具有体积小、重量轻、操作简便等特点,适用于各种小型旋转部件的生产和检测。集智机电还积极拓展海外市场,其产品已经出口到多个国家和地区。 以上排名综合考虑了品牌的技术实力、产品质量、市场份额、用户口碑等多方面因素。需要注意的是,动平衡设备市场竞争激烈,各品牌的排名可能会随着市场的变化和企业的发展而有所波动。在选择动平衡设备时,用户应根据自身的实际需求和预算,综合考虑各品牌的优缺点,选择最适合自己的产品。
07
2025-06
动平衡设备生产厂家地址及联系方式
动平衡设备生产厂家地址及联系方式 在工业生产领域,动平衡机是保障旋转机械平稳运行的关键设备。众多动平衡设备生产厂家分布在全国各地,为不同行业提供着专业的解决方案。以下为您介绍几家颇具影响力的动平衡设备生产厂家的地址及联系方式。 首先要提到的是精衡动平衡机制造有限公司。这家企业位于经济发达的长三角地区,具体地址是江苏省苏州市昆山市经济技术开发区朝阳东路 123 号。该地区工业基础雄厚,交通便利,为企业的发展提供了良好的环境。精衡公司专注于高精度动平衡机的研发与生产,其产品广泛应用于汽车制造、航空航天等高端领域。若您有相关需求,可拨打他们的联系电话:0512 - 88886666,或者通过邮箱 jingheng@dphj.com 与他们取得联系。 接着是中衡动平衡技术有限公司,地处我国制造业重镇——广东省东莞市长安镇振安西路 345 号。东莞作为世界工厂,拥有完善的产业链和丰富的技术人才资源。中衡公司凭借先进的技术和创新的理念,生产的动平衡设备具有高效、稳定的特点,在电子、电机等行业深受好评。您可以拨打联系电话 0769 - 99993333 咨询产品信息,也能登录他们的官方网站 www.zhonghengdph.com 了解更多详情。 再来说说北方的一家企业——华衡动平衡设备厂,位于河北省石家庄市高新区黄河大道 567 号。石家庄是华北地区重要的工业城市,有着悠久的工业历史和强大的产业支撑。华衡厂专注于为客户提供定制化的动平衡解决方案,其产品以性价比高、服务周到著称。若您想进一步了解他们的产品,可拨打联系电话 0311 - 77772222,还能通过微信公众号“华衡动平衡”获取最新动态。 最后介绍的是西南地区的恒衡动平衡机械有限公司,地址在四川省成都市武侯区武侯大道顺江段 890 号。成都作为西南地区的经济中心,科技实力雄厚,创新氛围浓厚。恒衡公司在动平衡设备的研发和生产上不断投入,致力于提升产品的智能化水平。您可以拨打 028 - 66661111 与他们沟通合作事宜,也能通过在线客服在他们的官方 APP“恒衡动平衡”上进行咨询。 以上这些动平衡设备生产厂家都在各自的区域有着独特的优势和特色产品。如果您在动平衡设备方面有需求,不妨根据自身实际情况与他们取得联系,相信定能找到适合您的解决方案。