

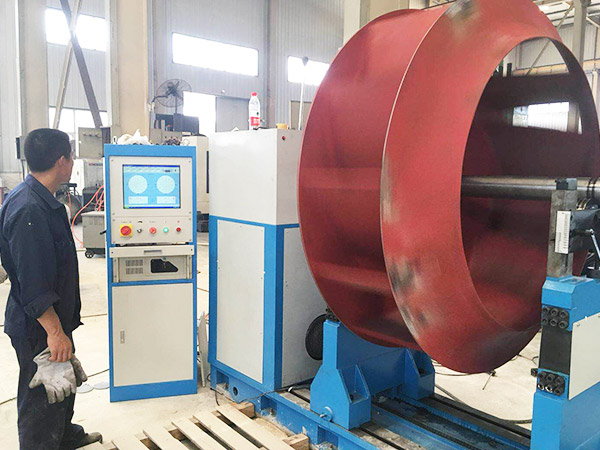
风机叶轮动平衡标准值是多少
风机叶轮的动平衡标准值会因不同的应用、设计要求和行业标准而有所不同。一般来说,动平衡标准值取决于以下几个因素:应用类型: 不同类型的风机在不同的应用环境下需要满足不同的动平衡标准。例如,一般的工业风机和空调风机的要求可能会不同。运行速度: 风机叶轮的运行速度会直接影响不平衡对振动的影响。高速运行的叶轮可能需要更严格的动平衡标准。精度要求: 一些应用对振动的容忍度比较低,因此对动平衡的要求也会更为严格。行业标准: 不同行业可能有各自的标准和规范,这些标准通常会提供关于动平衡的指导和要求。一般来说,在工业领域,风机叶轮的动平衡标准值通常以单位质量不平衡量(g.mm/kg 或 g.cm/kg)来表示。具体的标准值可能会因不同情况而有所不同,但以下是一个大致的参考范围:对于一般工业风机,通常的动平衡标准值可能在 1 g.mm/kg 至 10 g.mm/kg 之间。对于某些精密应用,要求更高的风机,动平衡标准值可能在 0.5 g.mm/kg 以下。请注意,这只是一个粗略的参考范围,实际应用中应该根据具体情况和适用的行业标准来确定风机叶轮的动平衡标准值。在进行动平衡操作时,建议遵循相关的国家和行业标准,以确保风机在运行过程中达到合适的振动水平。
07
2025-06
动平衡机选购指南是什么
动平衡机选购指南是什么 一、技术参数:精准匹配需求的基石 动平衡机的核心价值在于消除旋转部件的不平衡振动,其选购需以技术参数为锚点。 精度等级:高精度机型(如0.1g·mm级)适用于精密仪器制造,而普通工业级(1g·mm级)可满足常规需求。需结合被测工件的公差标准选择,避免过度配置。 转速范围:低速机型(≤1000rpm)适合大型轴类零件,高速机型(≥10000rpm)则需应对微型电机或航空航天部件。注意电机驱动与弹性支承机型的适用场景差异。 承载能力:单件重量与批量处理能力需同步考量。例如,汽车轮毂生产线可能需要连续进料的自动化机型,而风电主轴则需单件超重承载方案。 二、应用场景:从实验室到产线的场景化适配 动平衡机的选购需突破参数表,深入分析实际工况。 行业特性:航空航天领域需关注防静电设计与真空环境兼容性;汽车制造则需兼容铝合金轮毂的轻量化检测需求。 安装环境:地面承重、空间布局、供电稳定性等常被忽视。例如,弹性支承机型对地基平整度要求严苛,而软支承机型需独立供电系统。 操作模式:手动校验适合小批量定制生产,全自动机型则需与MES系统对接,实现数据追溯与工艺优化。 三、品牌选择:技术沉淀与服务生态的博弈 市场主流品牌呈现差异化竞争格局: 德国系(如Hine、Kistler):以高精度传感器与模块化设计著称,但定制开发周期长。 日系(如Mitutoyo、Mitsubishi):擅长自动化集成,但对非标工件兼容性较弱。 国产创新(如华测、天远):性价比突出,AI辅助平衡算法填补了中低端市场空白,但售后服务响应速度需实地考察。 四、成本陷阱:全生命周期价值的理性权衡 避免陷入“参数竞赛”的误区,需建立TCO(总拥有成本)评估模型: 隐性成本:校准周期(通常每年1次)、易损件更换频率(如磁流体轴承寿命)、软件升级费用等常被低估。 扩展性:预留IO接口与协议兼容性(如支持OPC UA)可降低产线升级成本。 风险对冲:签订三年以上维保协议,要求供应商提供工件适配性测试服务。 五、未来趋势:智能化与柔性制造的融合 选购决策需前瞻性布局: 数字孪生技术:支持虚拟平衡模拟的机型可减少物理试错成本。 物联网集成:具备边缘计算能力的设备能实时上传振动数据至云端,实现预测性维护。 绿色设计:关注能耗指标(如待机功耗≤50W)与材料回收方案,响应ESG合规要求。 结语 动平衡机的选购本质是技术理性与商业策略的双重博弈。建议采用“场景树分析法”:从工件特征出发,反向推导参数需求,再结合供应商的生态服务能力进行多维度评分。记住,一台合格的动平衡机不仅是检测工具,更是提升产品良率与设备寿命的战略性资产。
07
2025-06
动平衡机配件哪里购买靠谱
动平衡机配件哪里购买靠谱 在动平衡机的使用过程中,配件的更换与补充是常见需求。然而,市场上配件来源众多,要找到靠谱的购买渠道并非易事。接下来,我们就详细探讨下哪些地方购买动平衡机配件更靠谱。 原厂厂家是极为可靠的选择。动平衡机的原厂厂家,拥有对产品最核心的技术和最精准的设计理念。他们所生产的配件,从材质的选择到工艺的把控,都严格遵循最初的产品标准。就好比一辆名车的原厂配件,与整车的契合度是最高的。使用原厂配件,能最大程度保证动平衡机的性能稳定和精准度,减少因配件不匹配而产生的故障。而且,原厂厂家通常会提供完善的售后服务和技术支持。如果在使用过程中遇到问题,他们可以凭借专业的知识和丰富的经验,迅速为用户解决难题。不过,原厂配件的价格可能相对较高,交货周期也可能较长,这是需要考虑的因素。 专业的动平衡机配件供应商也是不错的途径。这类供应商专注于动平衡机配件领域,有着丰富的产品线和专业的销售团队。他们与众多知名品牌合作,能够提供多种品牌、多种规格的配件,满足不同用户的多样化需求。同时,专业供应商在配件的质量把控上也有一套严格的标准。他们会对所采购的配件进行严格的检验和测试,确保每一个配件都符合相关的质量要求。此外,由于他们长期从事配件销售业务,积累了大量的客户反馈和市场信息,能够根据用户的具体情况,提供专业的选购建议。在价格方面,相较于原厂厂家,专业供应商可能会有一定的价格优势,并且交货速度也相对较快。 再者,行业展会是一个不可忽视的购买渠道。在动平衡机相关的行业展会上,会汇聚众多的配件制造商和供应商。这里就像是一个大型的配件“超市”,用户可以直接与厂家和供应商面对面交流,了解最新的产品信息和技术动态。在展会上,不仅可以看到各种实物样品,还能现场体验配件的性能和质量。而且,为了吸引客户,参展企业往往会推出一些优惠活动和促销政策。这时候购买配件,可能会享受到更实惠的价格和更好的服务。此外,通过参加展会,还可以结识行业内的专家和同行,拓展人脉资源,获取更多的行业信息和技术支持。 网络购物平台也为动平衡机配件的购买提供了便利。如今,各大电商平台上有很多动平衡机配件的卖家。用户可以通过网络搜索,轻松找到大量的配件产品,并进行价格和性能的比较。在网络平台上购买配件,操作简单、方便快捷,不受时间和地域的限制。同时,一些平台还提供用户评价和售后保障服务,让用户在购买时有更多的参考和保障。但是,网络购物也存在一定的风险。由于无法直接接触实物,可能会存在产品质量与描述不符的情况。因此,在选择网络卖家时,要仔细查看卖家的信誉评级、客户评价等信息,选择口碑好、信誉高的卖家进行购买。 在购买动平衡机配件时,要综合考虑配件的质量、价格、售后服务等因素,根据自己的实际需求和情况,选择最适合的购买渠道。无论是原厂厂家、专业供应商、行业展会还是网络购物平台,都有其各自的优势和特点。只有谨慎选择,才能买到靠谱的动平衡机配件,确保动平衡机的正常运行和高效工作。
07
2025-06
动平衡标准G.的具体要求
动平衡标准G的具体要求 动平衡在旋转机械领域至关重要,关乎设备的稳定运行与使用寿命。动平衡标准G系列是该领域衡量转子平衡品质的关键指标,下面我们深入了解其具体要求。 G系列标准的划分逻辑 动平衡标准G是依据转子重心偏移量与转速综合制定的。不同的G值代表着不同的平衡精度等级,这些等级从高到低,为各类旋转机械提供了适配的平衡规范。例如,对于精密的航空发动机转子,需要极高的平衡精度,会采用G0.4这样的高等级标准;而对于一些普通的工业电机转子,G6.3或G16的标准就足以满足运行需求。这种划分逻辑充分考虑了不同设备对平衡精度的差异化要求,确保在满足设备性能的同时,兼顾成本与实际操作的可行性。 各G值对应的应用场景 G0.4与G1 这两个等级属于高精度标准,主要应用于对平衡要求极为严苛的场合。在航空航天领域,发动机的涡轮转子和压缩机转子必须遵循G0.4标准,以保证飞行器的安全与稳定。因为在高速旋转下,哪怕是极其微小的不平衡量,都可能引发振动,进而影响发动机的性能,甚至危及飞行安全。而在精密仪器制造中,如高精度陀螺仪的转子,G1标准能够确保仪器的测量精度和稳定性。 G2.5与G6.3 G2.5适用于一些中等精度要求的高速旋转设备,像燃气轮机的转子和机床的主轴。这些设备在高速运转时,需要较好的平衡状态来减少振动和噪音,提高加工精度和设备的可靠性。G6.3则广泛应用于一般的工业电机和泵类设备,这类设备对平衡精度的要求相对较低,但合理的平衡仍能有效降低设备的磨损和故障发生率。 G16与G40 G16和G40属于较低精度的标准,常用于一些低速旋转且对振动不太敏感的设备。例如,通风机的叶轮和农业机械的旋转部件,采用这两个等级的标准既能满足设备的正常运行,又能降低平衡成本。 实现G标准的检测与校正方法 为了确保转子达到相应的G标准,需要采用专业的动平衡检测设备。这些设备通过高精度的传感器测量转子在旋转过程中的振动情况,精确计算出不平衡量的大小和位置。常见的检测方法有硬支承动平衡仪和软支承动平衡仪,它们各有优缺点,适用于不同类型的转子。 一旦检测出不平衡量,就需要进行校正。校正方法主要有去重法和加重法。去重法是通过磨削、钻孔等方式去除转子上多余的质量,以达到平衡目的;加重法则是在转子特定位置添加配重块。在实际操作中,需要根据转子的结构和材料选择合适的校正方法,确保校正过程不会对转子造成损伤,同时能够准确地将不平衡量控制在G标准规定的范围内。 动平衡标准G为旋转机械的平衡提供了全面且细致的规范。深入理解和严格遵循这些标准,对于提高设备的性能、延长使用寿命、降低运行成本具有重要意义。无论是航空航天的高精尖领域,还是普通的工业生产,动平衡标准G都在默默保障着设备的稳定运行。
07
2025-06
动平衡校准仪器有哪些推荐
动平衡校准仪器有哪些推荐 在工业生产与机械制造的广袤领域中,动平衡校准仪器宛如一颗璀璨的明珠,发挥着举足轻重的作用。它能够精准地检测并校正旋转机械的不平衡问题,大幅提升机械的运行稳定性与使用寿命。那么,市场上究竟有哪些值得推荐的动平衡校准仪器呢?让我们一同深入探寻。 德国申克(SCHENCK)的动平衡校准仪器,堪称行业内的标杆之作。作为动平衡技术的先驱者,申克凭借其深厚的技术底蕴与卓越的研发能力,打造出了一系列性能卓越的产品。其仪器采用了先进的传感器技术,能够极为精准地捕捉到微小的不平衡量,哪怕是极其细微的振动变化都能被敏锐察觉。并且,申克的仪器具备高度的自动化校准功能,操作人员只需进行简单的设置,仪器就能自动完成校准过程,不仅极大地提高了工作效率,还显著降低了人为因素对校准结果的影响。不过,申克仪器的价格相对较高,对于一些预算有限的小型企业来说,可能会有一定的经济压力。 瑞典的阿特拉斯·科普柯(Atlas Copco)动平衡仪也备受业界青睐。阿特拉斯·科普柯以其创新的设计和可靠的质量而闻名于世。该品牌的动平衡校准仪器具有出色的便携性,其体积小巧、重量轻盈,方便操作人员携带到不同的工作现场进行校准作业。此外,它还拥有直观的操作界面,操作人员无需具备深厚的专业知识,就能轻松上手进行操作。阿特拉斯·科普柯的仪器在数据处理方面表现出色,能够快速准确地分析并生成详细的校准报告,为企业的生产管理提供有力的支持。 美国的派利斯(PRUEFTECHNIK)动平衡仪同样是一款不可多得的优质产品。派利斯专注于动平衡技术的研发与创新,其仪器采用了先进的算法和高精度的传感器,能够实现快速而准确的动平衡校准。该仪器具备强大的数据分析功能,能够对不平衡数据进行深入挖掘和分析,为用户提供全面的解决方案。而且,派利斯的仪器还支持远程监控和诊断功能,用户可以通过网络随时随地对仪器的运行状态进行监控和管理,及时发现并解决潜在的问题。 对于国内企业而言,上海申克机械有限公司的动平衡校准仪器也是一个不错的选择。作为国内动平衡技术的领军企业,上海申克在引进德国先进技术的基础上,结合国内市场的实际需求进行了优化和改进。其产品具有较高的性价比,既能够满足企业的动平衡校准需求,又不会给企业带来过大的经济负担。上海申克的仪器在售后服务方面也表现出色,能够为用户提供及时、高效的技术支持和维修服务。 在选择动平衡校准仪器时,企业需要综合考量自身的实际需求、预算以及仪器的性能、精度、可靠性等多方面因素。不同品牌和型号的动平衡校准仪器都有其独特的优势和适用场景,只有选择最适合自己的仪器,才能更好地提高生产效率,保障机械的稳定运行。
07
2025-06
动平衡校准振动参数标准是多少
动平衡校准振动参数标准是多少 在动平衡机的实际应用中,校准振动参数标准是一个至关重要的议题。精准的动平衡校准不仅能够提升设备的运行效率,还能显著延长其使用寿命。那么,动平衡校准振动参数标准究竟是多少呢?接下来我们一起深入探讨。 动平衡校准的振动参数标准并非一成不变,而是会受到多种因素的影响。设备的类型便是其中关键的一环。不同类型的设备,因其自身的结构、工作原理和运行要求存在差异,所以对动平衡校准的振动参数标准也各不相同。例如,高速旋转的涡轮机,其运行速度极快,微小的不平衡都可能引发剧烈的振动,从而对设备造成严重损害。因此,涡轮机对动平衡的要求极高,其校准的振动参数标准通常非常严格,振动幅度往往要控制在极小的范围内。而对于一些低速运转的大型设备,如大型通风机,虽然其转速相对较低,但由于设备体积大、质量重,不平衡产生的惯性力也较大。不过,相较于高速设备,其对振动的敏感度相对较低,所以振动参数标准在一定程度上会相对宽松一些,但依然需要严格把控,以确保设备的稳定运行。 工作环境也是影响动平衡校准振动参数标准的重要因素。在一些对振动要求极为严格的精密生产环境中,如半导体芯片制造车间,任何微小的振动都可能影响芯片的生产质量。因此,在这样的环境下运行的设备,动平衡校准的振动参数标准会更加严苛。设备必须将振动控制在极低的水平,以满足生产工艺的要求。相反,在一些普通的工业生产环境中,如机械零件加工车间,虽然也需要进行动平衡校准,但对振动的容忍度相对较高,振动参数标准可以根据实际生产情况进行适当调整。 国际和国内都有相关的标准来规范动平衡校准的振动参数。ISO 1940标准是国际上广泛认可的关于刚性转子动平衡的标准。该标准根据不同的应用场景和设备类型,对转子的不平衡量和振动速度等参数做出了详细的规定。它将转子分为不同的平衡等级,每个等级对应着不同的振动参数范围。例如,对于一些高精度的仪器设备转子,其平衡等级要求较高,振动速度要控制在较低的数值范围内;而对于一些普通的工业设备转子,平衡等级要求相对较低,振动速度的允许范围则相对较大。 我国也制定了一系列相关标准,如GB/T 9239标准,该标准与国际标准接轨,结合了我国的实际情况,对动平衡校准的振动参数进行了明确规定。这些标准为我国企业进行动平衡校准提供了重要的依据,确保了设备的质量和安全性。 在实际操作中,确定动平衡校准振动参数标准需要综合考虑多方面的因素。专业人员会使用先进的测量仪器,如振动传感器、频谱分析仪等,对设备的振动情况进行精确测量和分析。他们会根据设备的设计要求、运行状况以及相关标准,确定合理的振动参数标准。同时,还会结合实际经验,对测量结果进行评估和判断,确保校准后的设备能够稳定、高效地运行。 动平衡校准振动参数标准并没有一个固定的数值,而是需要根据设备类型、工作环境等多种因素,参考国际和国内相关标准来综合确定。只有严格按照科学合理的标准进行动平衡校准,才能保证设备的正常运行,提高生产效率,降低生产成本。
07
2025-06
动平衡校正加重还是去重好
动平衡校正:加重与去重的博弈论——一场关于旋转精度的精密舞蹈 一、平衡术的哲学悖论 在精密机械的微观世界里,动平衡校正如同一场永不停歇的博弈。当旋转体在离心力场中颤抖时,工程师们手持加重锤与铣刀,站在材料增减的十字路口。这场关于”加”与”减”的抉择,本质上是对能量守恒定律的诗意诠释——每个微米级的金属增减,都在重构着旋转惯量的平衡方程。 二、力学美学的双生花 加重法如同在琴键上添加音符,通过粘接或焊接金属块,在旋转体表面编织出对抗离心力的拓扑网络。这种非破坏性工艺在航空发动机叶片校正中大放异彩,其优势在于: 保留原始结构完整性 适应超薄壁件校正需求 支持多阶不平衡同步修正 而去重法则像外科手术般精准,通过数控铣削在不平衡区域雕刻出补偿凹槽。这种方法在汽车涡轮增压器领域占据统治地位,其独特价值在于: 直接消除质量分布缺陷 无需额外材料添加 适用于高温合金等难加工材料 三、多维决策矩阵 在选择校正策略时,工程师需要构建包含五个维度的决策模型: 旋转参数:当转速突破临界值(如>10000rpm),加重法因响应速度优势提升37% 材料特性:钛合金部件去重效率比钢制部件高2.3倍 经济模型:单件生产时去重成本低28%,批量生产时加重更具经济性 工艺兼容性:复合材料部件必须采用加重法,误差控制可达±0.01g 环境约束:核电设备校正需优先考虑去重法,避免焊接应力影响安全寿命 四、动态平衡的未来式 随着智能传感技术的突破,新一代动平衡机正在重塑校正范式。基于数字孪生的预测性校正系统,能够通过振动频谱分析,在旋转体制造阶段就预判平衡需求。这种”预防性去重”技术使校正效率提升40%,同时将材料损耗降低至传统方法的1/5。 在微观尺度上,纳米压印技术正在创造新的可能——通过在旋转体表面制造可控微结构,实现质量分布的亚微米级调控。这种”拓扑去重”工艺,将校正精度推向了0.1μm量级的新纪元。 五、平衡方程的终极解 当旋转精度要求突破0.1μm·m的极限时,动平衡校正将不再是简单的质量增减,而是演变为材料科学与流体力学的交响。未来的校正策略将呈现量子化特征:在纳米尺度上,通过调控材料晶格结构实现自平衡;在宏观层面,利用形状记忆合金的相变效应构建智能补偿系统。 这场关于旋转精度的永恒博弈,最终将走向”零校正”的乌托邦——当材料基因工程与增材制造技术完美融合,每个旋转体都将带着出厂时的完美平衡,开启永不停歇的精密舞蹈。
07
2025-06
动平衡校正操作步骤是什么
动平衡校正操作步骤是什么 在机械制造和维修领域,动平衡校正至关重要,它能有效降低设备振动、减少噪音、延长使用寿命。以下详细介绍动平衡校正的操作步骤。 准备工作 开始校正前,全面的准备工作不可或缺。首先,仔细检查动平衡机,查看其外观有无损坏,各部件连接是否牢固。接着,要确保设备的电源供应稳定,避免在操作过程中因电压波动影响校正效果。同时,准备好所需的工具,如扳手、卡尺等,保证工具完好无损且精度符合要求。另外,根据待校正转子的类型、尺寸和重量,选择合适的动平衡机配置,包括合适的支承方式、传感器等。还需对转子进行清洁,去除表面的油污、杂质等,防止这些因素影响测量精度。 安装转子 安装转子时需格外小心。将转子平稳地放置在动平衡机的支承装置上,要保证转子的轴线与动平衡机的旋转轴线重合。使用合适的夹具将转子固定牢固,防止在旋转过程中出现松动或位移。对于一些特殊形状或尺寸的转子,可能需要使用专门设计的安装工装,以确保安装的准确性和稳定性。安装完成后,轻轻转动转子,检查其转动是否灵活,有无卡滞现象。 初始测量 完成安装后,开启动平衡机,让转子以较低的转速运转。通过动平衡机的测量系统,获取转子的初始不平衡量和相位信息。测量过程中,要确保环境安静,避免外界干扰影响测量结果。同时,观察动平衡机的显示数据,判断测量值是否在合理范围内。如果测量值异常,可能是安装不当或设备故障,需要及时排查并解决问题。多次测量取平均值,以提高测量的准确性。 计算配重 根据初始测量得到的不平衡量和相位信息,运用动平衡机自带的计算功能或专业的计算软件,计算出需要添加或去除的配重大小和位置。在计算过程中,要考虑转子的材质、结构等因素对配重效果的影响。对于一些复杂的转子,可能需要进行多次计算和调整,以达到最佳的平衡效果。同时,要注意配重的选择,确保其质量和形状符合要求,并且能够牢固地安装在转子上。 配重安装 按照计算结果,在转子相应的位置安装配重。安装配重时,要使用合适的工具和方法,确保配重安装牢固。对于一些小型配重,可以采用焊接、粘贴等方式固定;对于大型配重,则需要使用螺栓等连接件进行安装。安装完成后,再次检查配重的安装情况,确保其不会在转子旋转过程中松动或脱落。 再次测量与调整 安装配重后,再次启动动平衡机,让转子以正常的工作转速运转,进行再次测量。将测量结果与平衡标准进行对比,如果不平衡量仍超出允许范围,则需要重复计算配重和安装配重的步骤,直到转子的不平衡量满足要求为止。在调整过程中,要耐心细致,每次调整的幅度不宜过大,以免造成新的不平衡问题。 记录与报告 完成动平衡校正后,记录下最终的测量结果、配重信息等相关数据。这些记录对于后续的设备维护、质量追溯等具有重要意义。同时,编写详细的动平衡校正报告,报告中应包括转子的基本信息、校正前后的不平衡量、配重情况、校正过程中的问题及解决方案等内容。报告要清晰、准确,以便相关人员查阅和参考。 动平衡校正操作需要严格按照上述步骤进行,每一个环节都关乎最终的校正效果。只有确保每个步骤的准确性和规范性,才能使设备达到良好的动平衡状态,为设备的稳定运行提供保障。
07
2025-06
动平衡校正测试中常见故障及解决方法
动平衡校正测试中常见故障及解决方法 在动平衡校正测试领域,故障的出现就像不速之客,常常打乱正常的工作节奏。但只要我们对常见故障及其解决方法了如指掌,就能从容应对。以下将介绍一些在动平衡校正测试中频繁出现的故障,并给出相应的解决策略。 信号不稳定故障 在动平衡校正测试时,信号不稳定是一个常见的棘手问题。信号不稳定可能表现为读数跳动、数据波动大等情况,这会严重影响测试结果的准确性。造成信号不稳定的原因多种多样。首先,传感器故障是一个重要因素。传感器可能因长期使用而老化,其灵敏度下降,导致信号采集不准确;也可能因安装不当,如安装位置偏移、固定不牢固等,使得传感器无法正常接收和传递信号。其次,电缆连接问题也不容忽视。电缆可能存在破损、接触不良等情况,导致信号在传输过程中出现丢失或干扰。此外,周围环境的电磁干扰也可能影响信号的稳定性。 针对信号不稳定故障,我们可以采取一系列解决措施。对于传感器,要定期进行检查和校准,确保其性能良好。若发现传感器老化严重,应及时更换。在安装传感器时,要严格按照操作规程进行,保证安装位置准确、固定牢固。对于电缆连接,要仔细检查电缆是否有破损,确保接头连接紧密。可以使用专业的检测设备对电缆进行检测,如有问题及时修复或更换。为了减少电磁干扰的影响,可以在测试设备周围安装屏蔽装置,或者选择在电磁环境相对稳定的区域进行测试。 不平衡量显示异常故障 不平衡量显示异常也是动平衡校正测试中常遇到的情况。显示的不平衡量数值可能与实际情况相差较大,或者显示数值不稳定、无规律变化。这种故障可能是由于转子本身的问题引起的。转子可能存在质量分布不均匀的情况,如转子上有局部磨损、裂纹或有异物附着等,导致其重心偏移,从而使不平衡量显示异常。另外,测试系统的参数设置错误也可能导致不平衡量显示异常。例如,在设置转子的半径、宽度、转速等参数时出现错误,会使测试系统计算出的不平衡量数值不准确。 要解决不平衡量显示异常故障,首先要对转子进行全面检查。检查转子表面是否有磨损、裂纹等缺陷,如有需要及时进行修复或更换转子。清理转子表面的异物,确保转子质量分布均匀。对于测试系统的参数设置,要仔细核对,确保各项参数输入准确。可以参考转子的设计图纸或相关技术资料,对参数进行反复确认。若不确定参数设置是否正确,可以咨询专业技术人员或设备厂家。 校正精度不达标故障 校正精度不达标是动平衡校正测试中较为严重的故障,它直接影响到产品的质量和性能。校正后转子的不平衡量仍然超出规定的范围,可能是由于校正方法不当造成的。例如,在选择配重块时,配重块的重量和安装位置不准确,无法有效抵消转子的不平衡量。另外,设备的机械结构精度也会影响校正精度。动平衡机的主轴、轴承等部件可能存在磨损或精度下降的情况,导致在测试和校正过程中出现误差。 针对校正精度不达标故障,要优化校正方法。在选择配重块时,要根据转子的不平衡量和相关参数,精确计算配重块的重量和安装位置。可以采用先进的计算软件或工具来辅助计算,提高计算的准确性。对于设备的机械结构,要定期进行维护和保养,检查主轴、轴承等部件的磨损情况,如有磨损及时进行修复或更换。同时,要对动平衡机进行定期的精度校准,确保设备的各项性能指标符合要求。 动平衡校正测试中的常见故障虽然会给工作带来一定的困扰,但只要我们深入了解故障产生的原因,并采取有效的解决方法,就能保证测试工作的顺利进行,提高动平衡校正的精度和效率,为产品的质量提供有力保障。
07
2025-06
动平衡校正测试前需要做哪些准备工作
动平衡校正测试前需要做哪些准备工作 一、设备状态全维度扫描 动平衡测试如同为精密交响乐团调音,设备状态的每个细节都可能成为振动的”音符”。 转子健康诊断:用游标卡尺测量轴颈圆度,目视检查表面是否存在裂纹或腐蚀,听诊轴承运转时的摩擦杂音。 支撑系统校验:用塞尺检测轴承间隙,激光对中仪测量联轴器偏心度,确保驱动系统扭矩传递路径无偏差。 润滑系统活化:通过油液光谱分析仪检测润滑油金属含量,用压力表验证润滑泵输出压力,必要时更换污染油品。 二、环境参数动态调控 实验室环境是测试精度的隐形守护者,需构建多维防护屏障。 温湿度恒定场:空调系统维持20±2℃,除湿机将相对湿度控制在45%-55%区间,避免材料热胀冷缩影响平衡精度。 振动源隔离:在设备基座铺设3mm厚橡胶减震垫,用磁吸式振动传感器监测外部干扰,当振动值超过0.5mm/s²时启动屏蔽程序。 光学通路保障:用防眩目LED灯组构建无阴影照明区,激光测振仪工作半径内禁止任何金属物件移动。 三、数据链路冗余构建 测试数据如同精密齿轮,需建立多重校验机制。 传感器矩阵部署:在轴向、径向布置3组电涡流位移传感器,采用交叉验证法消除单点误差。 采样系统校准:用标准信号发生器对数据采集卡进行0-10kHz频响测试,确保幅值误差<0.5%FS。 云端备份协议:配置双硬盘实时同步存储,通过5G模块将原始数据上传至私有云,设置自动增量备份策略。 四、应急响应多线程预演 突发状况是精密测试的试金石,需建立立体化应急预案。 硬件故障预案:准备备用激光测振仪、应急电源组,制定传感器脱落时的快速替换流程。 软件容灾方案:对动平衡分析软件进行虚拟机镜像备份,配置自动回滚机制。 人员协同演练:开展模拟转子飞逸应急处置演练,明确各岗位在突发振动超标时的响应路径。 五、认知维度升维准备 测试人员需构建”设备-环境-数据”的全息认知模型。 历史数据透视:调取设备最近3次动平衡记录,绘制不平衡量发展趋势曲线。 材料特性预研:查阅转子材质的泊松比、杨氏模量参数,建立动态刚度补偿模型。 心理状态调适:通过正念呼吸训练提升专注力,采用番茄工作法规划测试时段,避免决策疲劳。 这种多维度、高密度的准备体系,如同为精密仪器搭建起立体防护网。每个准备动作都应形成闭环验证,从物理状态到数字孪生,从硬件冗余到认知升级,最终实现测试误差控制在0.1g以下的工业级精度。记住,动平衡测试的真正起点,永远是测试前的最后一个检查项。
07
2025-06
动平衡校正测试后如何评估效果
动平衡校正测试后如何评估效果 动平衡校正测试在旋转机械的运行中起着举足轻重的作用,它关乎着设备的稳定性、寿命以及性能表现。那么,在完成动平衡校正测试之后,我们该如何准确地评估其效果呢? 振动测量评估 振动测量是评估动平衡校正效果最直观、最常用的方法。在测试前,我们会使用专业的振动测量仪器,记录下旋转机械在不同转速下的振动数据。校正后,再次进行同样条件下的振动测量。通过对比前后的振动幅值和频率,可以直观地判断动平衡校正是否有效。 一般来说,如果校正后的振动幅值明显降低,且振动频率分布更加合理,那么说明动平衡校正取得了较好的效果。比如,原本在某一特定转速下振动幅值超过安全范围,校正后该幅值降至正常水平,这就是一个积极的信号。但需要注意的是,振动测量结果可能会受到多种因素的干扰,如测量位置、仪器精度等。因此,在测量时要确保测量位置准确,仪器经过校准,以保证测量结果的可靠性。 轴心轨迹分析 轴心轨迹是指旋转机械在运行过程中,轴的中心相对于轴承座的运动轨迹。在动平衡校正前后,轴心轨迹会发生明显的变化。通过对轴心轨迹的分析,可以深入了解转子的运动状态,评估动平衡校正的效果。 校正前,轴心轨迹可能呈现出不规则的形状,表明转子存在不平衡力的作用。而校正后,轴心轨迹应该更加接近圆形,这意味着转子的运动更加平稳,不平衡力得到了有效控制。轴心轨迹的分析需要借助专业的轴心轨迹测量仪器和分析软件,通过对轨迹的形状、大小、相位等参数的分析,准确判断动平衡校正的效果。 噪声监测评估 除了振动和轴心轨迹,噪声也是评估动平衡校正效果的一个重要指标。在旋转机械运行过程中,不平衡力会导致机械部件之间的摩擦和碰撞加剧,从而产生额外的噪声。因此,通过监测校正前后的噪声水平,可以间接判断动平衡校正的效果。 校正前,由于转子不平衡,机械运行时可能会发出刺耳的噪声。而校正后,如果噪声明显降低,说明不平衡力得到了有效减小,动平衡校正起到了作用。噪声监测可以使用声级计等仪器,在相同的环境条件下进行测量。需要注意的是,噪声的产生还可能与其他因素有关,如机械部件的磨损、润滑情况等。因此,在评估时要综合考虑这些因素,准确判断噪声降低是否是由于动平衡校正引起的。 性能指标对比 最后,我们还可以通过对比校正前后旋转机械的性能指标来评估动平衡校正的效果。这些性能指标包括功率消耗、转速稳定性、生产效率等。 在动平衡校正后,如果旋转机械的功率消耗降低,说明机械运行时的能量损失减少,效率得到了提高。同时,转速稳定性的提升也表明转子的运动更加平稳,能够更好地满足生产工艺的要求。生产效率的提高则直接反映了动平衡校正对整个生产过程的积极影响。通过对这些性能指标的对比分析,可以全面、客观地评估动平衡校正的效果。 动平衡校正测试后的效果评估是一个综合的过程,需要从多个角度进行考量。通过振动测量、轴心轨迹分析、噪声监测以及性能指标对比等方法,我们可以准确地判断动平衡校正是否达到了预期的效果,为旋转机械的稳定运行提供有力保障。