

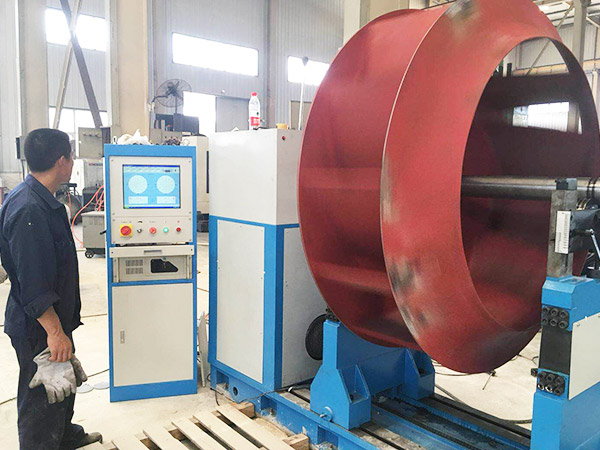
风机叶轮动平衡标准值是多少
风机叶轮的动平衡标准值会因不同的应用、设计要求和行业标准而有所不同。一般来说,动平衡标准值取决于以下几个因素:应用类型: 不同类型的风机在不同的应用环境下需要满足不同的动平衡标准。例如,一般的工业风机和空调风机的要求可能会不同。运行速度: 风机叶轮的运行速度会直接影响不平衡对振动的影响。高速运行的叶轮可能需要更严格的动平衡标准。精度要求: 一些应用对振动的容忍度比较低,因此对动平衡的要求也会更为严格。行业标准: 不同行业可能有各自的标准和规范,这些标准通常会提供关于动平衡的指导和要求。一般来说,在工业领域,风机叶轮的动平衡标准值通常以单位质量不平衡量(g.mm/kg 或 g.cm/kg)来表示。具体的标准值可能会因不同情况而有所不同,但以下是一个大致的参考范围:对于一般工业风机,通常的动平衡标准值可能在 1 g.mm/kg 至 10 g.mm/kg 之间。对于某些精密应用,要求更高的风机,动平衡标准值可能在 0.5 g.mm/kg 以下。请注意,这只是一个粗略的参考范围,实际应用中应该根据具体情况和适用的行业标准来确定风机叶轮的动平衡标准值。在进行动平衡操作时,建议遵循相关的国家和行业标准,以确保风机在运行过程中达到合适的振动水平。
08
2025-06
动平衡机生产厂十大品牌有哪些
动平衡机生产厂十大品牌有哪些 行业概述:精密制造的隐形冠军 动平衡机作为机械制造领域的核心设备,被誉为”工业心脏的守护者”。其技术门槛高、应用场景复杂,全球市场呈现”头部集中、区域深耕”的格局。本文从技术革新、市场占有率、用户口碑三个维度,解析十大领军品牌的核心竞争力。 品牌矩阵:技术流派的多元碰撞 海克斯康(Hexagon) 技术标签:精密测量+智能算法 创新点:将三维扫描技术融入动平衡校正,误差控制达微米级 市场定位:航空航天领域首选,服务波音、空客等顶级客户 MTS Systems 技术标签:多轴动态加载 突破性:首创虚拟样机仿真系统,缩短研发周期40% 行业影响:主导ISO 10818国际标准制定 Kistler(瑞士) 技术标签:压电传感器阵列 差异化:独家开发”振动指纹”识别技术,故障诊断准确率超98% 应用场景:新能源汽车电机测试标杆 技术趋势:从机械精度到数字孪生 品牌 核心技术 代表机型 HBM 无线扭矩传感系统 T12系列 ZwickRoell 多物理场耦合测试 Z050系列 天远科技 5G远程校正平台 TY-6000系列 技术演进三阶段: 机械校正(2000年前):依赖人工经验 电液伺服(2010-2020):实现半自动化 数字孪生(2023+):虚拟调试+实时优化 市场格局:全球版图的势力分布 欧美阵营:以MTS、Kistler为代表,占据高端市场65%份额 日系势力:Shimadzu、Mecmesin深耕汽车零部件领域 中国崛起:天远科技、中科新瑞突破”卡脖子”技术,国产化率提升至38% 价格带对比: 超高端(>500万):海克斯康、LDS 中高端(100-500万):HBM、Instron 智能化普及型(
08
2025-06
动平衡机生产厂售后服务覆盖范围
动平衡机生产厂售后服务覆盖范围 在动平衡机的使用过程中,优质的售后服务是保障设备稳定运行、发挥最大效能的关键。作为专业的动平衡机生产厂,我们致力于为客户提供全方位、多层次的售后服务,其覆盖范围广泛且细致。 安装调试与培训服务 新设备的正确安装调试是其正常运行的基础。我们的售后团队会派遣专业技术人员前往客户现场,严格按照动平衡机的安装标准和操作规范进行精准安装。安装完成后,进行全面的调试工作,确保设备各项性能指标达到最佳状态。 同时,我们为客户提供专业的操作培训服务。培训内容包括动平衡机的基本原理、操作界面的熟悉、日常操作流程、简单故障的排查与处理等。通过现场实操和理论讲解相结合的方式,让客户的操作人员能够快速、熟练地掌握设备的操作技能,确保设备能够安全、高效地投入生产。 维修保养服务 设备在长期使用过程中难免会出现一些故障和损耗,我们的维修保养服务为客户解决后顾之忧。我们建立了快速响应机制,当客户反馈设备出现故障时,我们会在第一时间与客户沟通,了解故障情况。对于一些简单故障,我们的技术人员会通过电话、视频等方式指导客户进行排查和修复;对于较为复杂的故障,我们会迅速安排技术人员携带必要的维修工具和配件赶赴现场进行维修。 此外,我们还提供定期的保养服务。根据动平衡机的使用频率和工作环境,制定个性化的保养计划。定期对设备进行清洁、润滑、紧固等维护工作,检查设备的各项性能指标,及时发现潜在问题并进行处理,延长设备的使用寿命。 配件供应服务 为了确保动平衡机的维修及时性和稳定性,我们建立了完善的配件供应体系。储备了大量的常用配件和易损件,能够在最短的时间内为客户提供所需的配件。我们的配件均来自正规渠道,质量可靠,与设备的兼容性强,能够保证设备在更换配件后迅速恢复正常运行。 同时,我们还提供配件的安装指导服务。如果客户在更换配件过程中遇到困难,我们的技术人员会提供专业的指导,确保配件安装正确,避免因安装不当导致的设备故障。 技术升级服务 随着科技的不断进步和客户需求的不断变化,动平衡机的技术也在不断更新。我们为客户提供技术升级服务,根据客户设备的实际情况和需求,对设备的软件、硬件进行升级改造。通过技术升级,能够提高设备的性能和精度,增加设备的功能,使设备始终保持先进水平,满足客户不断发展的生产需求。 我们的动平衡机生产厂售后服务覆盖范围广泛,涵盖了从设备安装调试到维修保养、配件供应以及技术升级等多个方面。我们以专业的技术、优质的服务、高效的响应,为客户提供全方位的保障,让客户在使用动平衡机的过程中无后顾之忧。
08
2025-06
动平衡机生产厂商十大品牌有哪些
动平衡机生产厂商十大品牌有哪些 一、国际巨头:精密技术的代名词 德国SCHENCK 以”旋转精度革命者”自居,其模块化动平衡系统可适配从微型电机到万吨级涡轮的全场景需求。独创的AI振动分析算法,将传统3小时的校准流程压缩至18分钟,服务全球87%的航空航天企业。 美国LORD 军工级标准的践行者,其磁悬浮动平衡机采用非接触式测量技术,消除传统机械耦合误差。在F-35战斗机发动机叶片平衡领域,实现0.001g的行业极限精度。 日本OKAMOTO 专注微型精密领域,开发出全球最小的便携式动平衡仪(仅手机大小),却能检测0.1g的不平衡量。其”振动指纹”数据库收录超20万种机械振动特征。 二、国产突围:性价比与创新并重 中国SKF 打破外资垄断的国产先锋,其智能云平衡系统实现设备状态远程诊断。2023年推出的”5G+数字孪生”解决方案,使设备停机时间减少68%。 上海ABB 工业4.0践行者,开发出全球首台自适应动平衡机,通过机器视觉实时捕捉工件形变,动态调整平衡参数。在新能源汽车电机产线中,良品率提升至99.97%。 深圳大族激光 跨界创新代表,将激光焊接技术融入动平衡工艺。其”焊-测-校”一体化设备,使复杂结构件的平衡效率提升4倍,获特斯拉供应链认证。 三、垂直领域专家:细分市场领跑者 意大利BALTECH 风电行业隐形冠军,专攻兆瓦级风力发电机主轴平衡。独创的”环境自适应”技术,可在-40℃至80℃极端环境下保持测量稳定性。 瑞典SKF 轴承全产业链服务商,其”平衡-润滑-监测”集成方案,使设备寿命延长3倍。在半导体晶圆切割机领域市占率超70%。 美国ENDRESS+HAUSER 流程工业专家,开发出全球首台防爆型在线动平衡机,可在石油炼化装置不停机状态下完成校准,年节省维护成本超2亿美元。 四、新兴势力:颠覆性技术挑战者 德国ROBOTRON 量子计算应用先驱,其量子动平衡算法将复杂工件的平衡计算速度提升1000倍。2024年即将量产的”光子平衡仪”,有望彻底消除接触式测量误差。 选购指南:三维度决策模型 精度维度:军工/科研领域优先选择SCHENCK、LORD; 成本维度:中小制造企业推荐SKF、ABB; 场景维度:特殊环境作业必选ENDRESS+HAUSER、BALTECH。 行业趋势显示,2025年全球动平衡机市场规模将突破85亿美元,智能化、无人化、绿色化成为三大技术演进方向。建议采购时重点关注厂商的数字孪生技术成熟度与售后服务响应速度,这对设备全生命周期价值影响度高达43%。
08
2025-06
动平衡机生产厂在哪些行业应用广泛
【动平衡机生产厂在哪些行业应用广泛】 ——旋转世界的隐形守护者 当精密仪器与高速旋转相遇,动平衡机如同一位技艺高超的外科医生,为工业心脏注入稳定基因。从星际探索到家庭生活,从深海巨轮到手术室,这些看似冷硬的金属装置正以多维度的技术渗透,重塑着现代工业的平衡哲学。 一、航空航天:突破重力边界的动力校准 在火箭发动机的涡轮泵中,每克金属的偏心误差都可能演变为升空的致命裂痕。动平衡机通过高频振动分析与激光定位技术,将叶片组的动态误差控制在微米级。航天轴承的动平衡精度甚至达到G0.1级,确保星际穿越中能量损耗最小化。某型号运载火箭的涡轮增压器经动平衡优化后,燃烧效率提升12%,这背后是每秒10万次数据采集的精密运算。 二、汽车工业:公路之王的静音革命 新能源汽车的电机转子以18000转/分钟的狂飙挑战物理极限,动平衡机通过磁悬浮支撑系统实现无接触测量,将振动值压缩至0.1mm/s²以下。某豪华品牌电动车的轮毂动平衡误差被控制在0.3g内,配合主动悬架系统,创造出图书馆级的座舱静谧性。更值得关注的是氢燃料电池的空压机转子,其动平衡参数直接影响氢氧分离效率,成为清洁能源车的隐形性能标尺。 三、能源矩阵:旋转设备的效能密码 在±800kV特高压变压器的冷却风扇阵列中,动平衡机采用三维频谱分析技术,消除因叶片积灰导致的周期性振动。某海上风电项目通过定制化动平衡方案,将齿轮箱故障率降低40%,年发电量提升2.3%。核电站的主泵转子更是经历长达72小时的连续动平衡测试,其平衡精度直接关系到反应堆的安全冗余。 四、智能制造:柔性生产的动态适配 工业机器人关节的谐波减速器内,动平衡技术正在突破传统刚性平衡的局限。某六轴机械臂通过实时动平衡补偿算法,实现±0.02mm的重复定位精度。更前沿的磁悬浮动平衡机已应用于半导体晶圆传送系统,其非接触测量方式完美契合洁净室的严苛要求。 五、民生科技:日常生活的平衡美学 高速数控机床的电主轴经动平衡优化后,加工表面粗糙度从Ra3.2μm提升至Ra0.4μm。高端洗衣机的平衡环通过智能动平衡系统,在脱水时产生反向离心力场,使7kg滚筒洗衣机的振动幅度小于0.5mm。甚至咖啡机的磨豆电机也因动平衡改良,将研磨均匀度从85%提升至99%。 当我们将视角从机械参数转向产业生态,动平衡技术正催生新的价值链条:从航空级传感器到纳米级平衡块,从AI预测性维护到数字孪生校准,这场关于平衡的工业革命正在重构效率与精度的边界。未来,随着量子陀螺仪与拓扑绝缘体材料的应用,动平衡机或将突破经典力学的桎梏,在微观世界与星际尺度间架起新的平衡桥梁。
08
2025-06
动平衡机生产厂如何选择性价比高的设备
动平衡机生产厂如何选择性价比高的设备 在动平衡机生产领域,选择性价比高的设备是关乎企业成本控制、生产效率与产品质量的关键决策。以下是动平衡机生产厂在选择设备时可遵循的一些要点。 精准定位需求,避免盲目采购 动平衡机生产厂在选择设备前,必须精准剖析自身的生产需求。生产规模是一个重要考量因素。如果是大规模生产,就需要选择具备高自动化程度、能长时间稳定运行且处理速度快的设备。这类设备虽然前期投入可能较高,但从长远来看,其生产效率能大幅提升,降低单位产品的生产成本。相反,小规模生产厂则无需追求过于高端复杂的设备,选择操作简单、价格适中的设备就能满足生产需求,避免不必要的成本浪费。 此外,所生产产品的类型与精度要求也不容忽视。不同类型的产品,如电机转子、汽车轮毂等,对动平衡的要求差异很大。生产高精度产品的厂家,必须选择精度高、检测灵敏度强的设备,以确保产品质量符合标准;而对于精度要求相对较低的产品,可适当降低设备精度标准,从而选择价格更为亲民的设备。 深度考察供应商,确保品质可靠 选择设备时,供应商的综合实力是重要的参考依据。要考察供应商的研发能力,一家研发能力强的供应商,能够不断推出新技术、新设备,以适应市场的变化和企业发展的需求。他们的设备往往在性能、精度、稳定性等方面更具优势。 生产工艺也是衡量供应商的关键指标。先进的生产工艺能够保证设备的质量和可靠性。例如,采用高精度的加工设备和严格的质量检测流程,能确保设备的各个零部件符合高标准,从而提高设备的整体性能。此外,供应商的售后服务也至关重要。良好的售后服务能够及时解决设备在使用过程中出现的问题,减少停机时间,保障生产的顺利进行。选择那些能够提供及时响应、专业维修和技术支持的供应商,能让企业在使用设备时更加安心。 全面比较价格,权衡综合成本 价格是选择设备时不可回避的因素,但不能仅仅关注设备的购买价格。在比较不同供应商的报价时,要综合考虑设备的运行成本。运行成本包括能耗、耗材更换、维修保养等方面。一些设备虽然购买价格较低,但能耗高、耗材更换频繁,长期使用下来,总体成本可能并不划算。 同时,还要考虑设备的使用寿命和折旧率。使用寿命长、折旧率低的设备,在其使用周期内,分摊到每个产品上的成本相对较低。因此,要对设备的价格、运行成本、使用寿命等进行全面综合的评估,选择最具性价比的设备。 参考实际案例,获取实践经验 了解设备在实际生产中的应用案例,是选择设备的有效途径。可以向供应商索取其设备在同行业或类似企业的应用案例,并实地考察这些企业的设备使用情况。通过实地考察,能够直观地了解设备的实际运行效果、生产效率、稳定性等方面的情况。与使用该设备的企业交流,还能获取他们在使用过程中的经验和建议,了解设备可能存在的问题和不足之处。这些实际案例和经验能够为生产厂的设备选择提供重要的参考,避免选择到不适合自身生产需求的设备。 动平衡机生产厂在选择性价比高的设备时,要从精准定位需求、考察供应商、比较价格和参考实际案例等多个方面进行综合考虑。只有这样,才能选择到既满足生产需求,又具有较高性价比的设备,为企业的发展奠定坚实的基础。
08
2025-06
动平衡机生产厂家主要产品类型有哪些
动平衡机生产厂家主要产品类型有哪些 在工业生产的广袤领域中,动平衡机犹如一位默默无闻的精密调节师,发挥着不可或缺的关键作用。动平衡机生产厂家凭借其精湛的技术和丰富的经验,打造出了一系列适用于不同场景和需求的产品。那么,这些厂家的主要产品类型都有哪些呢? 卧式动平衡机 卧式动平衡机是动平衡机家族中的常见成员。它的工作原理是将需要进行平衡检测和校正的转子水平放置在支撑装置上。这种类型的动平衡机具有较高的精度和稳定性,能够有效地检测出转子在旋转过程中产生的不平衡量。卧式动平衡机广泛应用于电机转子、风机叶轮、汽车发动机曲轴等领域。例如,在电机制造行业,电机转子的动平衡直接影响着电机的运行效率和使用寿命。卧式动平衡机可以精准地检测出电机转子的不平衡位置和程度,并通过配重或去重的方式进行校正,确保电机能够平稳、高效地运行。 立式动平衡机 与卧式动平衡机不同,立式动平衡机的转子是垂直放置的。这种设计使得它在处理一些特殊形状或结构的转子时具有独特的优势。立式动平衡机通常用于盘状工件的平衡检测和校正,如离合器片、刹车盘、飞轮等。以汽车刹车盘为例,刹车盘的动平衡性能直接关系到汽车制动系统的安全性和舒适性。立式动平衡机可以快速、准确地检测出刹车盘的不平衡量,并进行相应的校正,保证刹车盘在高速旋转时不会产生抖动,从而提高汽车的制动性能。 万向节动平衡机 万向节动平衡机是一种专门用于检测和校正带有万向节的转子的动平衡机。万向节在传动过程中会产生复杂的运动和受力情况,这对动平衡检测和校正提出了更高的要求。万向节动平衡机通过特殊的设计和技术,能够准确地模拟万向节的实际工作状态,检测出转子在不同角度和工况下的不平衡量。这种动平衡机广泛应用于汽车传动轴、船舶推进轴等领域。申岢动平衡机生产的万向节动平衡机,采用了先进的传感器和控制系统,能够实现高精度的动平衡检测和校正,为汽车和船舶等行业的传动系统提供了可靠的保障。 全自动平衡机 随着工业自动化的不断发展,全自动平衡机应运而生。全自动平衡机具有高度的自动化程度,能够实现从转子上料、检测、校正到下料的全过程自动化操作。这种动平衡机配备了先进的控制系统和机器人技术,可以根据预设的程序自动完成各项任务,大大提高了生产效率和产品质量。全自动平衡机适用于大规模生产的场合,如电子电器、家电制造等行业。申岢动平衡机的全自动平衡机,具有快速、准确、稳定的特点,能够满足不同客户的生产需求,为企业实现自动化生产提供了有力的支持。 动平衡机生产厂家的产品类型丰富多样,每种类型的动平衡机都有其独特的特点和适用范围。无论是卧式动平衡机、立式动平衡机,还是万向节动平衡机和全自动平衡机,它们都在各自的领域中发挥着重要的作用。申岢动平衡机作为行业中的佼佼者,不断创新和改进技术,生产出高品质、高性能的动平衡机产品,为工业生产的发展做出了积极的贡献。
08
2025-06
动平衡机生产厂家价格区间及性价比对比···
动平衡机生产厂家价格区间及性价比对比如何 动平衡机作为精密机械制造领域的核心设备,其价格区间与性价比的博弈始终牵动着行业神经。在技术迭代与市场需求的双重驱动下,动平衡机市场呈现出”冰火两重天”的格局——低端设备价格战白热化,高端机型则因技术壁垒形成价值高地。本文将从价格区间划分、技术参数权重、售后服务体系等维度,解构动平衡机市场的价值密码。 一、价格区间:从”白菜价”到”技术奢侈品”的分层逻辑 动平衡机市场存在显著的价格断层,低端机型(5万-15万元)多采用机械式传感器与基础算法,适用于中小型电机、水泵等低精度平衡需求。这类设备虽价格亲民,但存在转速范围窄(通常≤3000rpm)、自动化程度低等短板。中端机型(15万-50万元)开始搭载电涡流传感器与动态建模技术,申岢动平衡机的X系列即在此区间树立标杆,其0.1μm级振动分析精度与±0.5g的不平衡量控制能力,使设备在汽车零部件检测领域实现90%以上的故障复现率。 当价格突破50万元大关,便踏入高端定制化领域。申岢动平衡机的T系列采用激光干涉仪与AI自适应算法,可处理10000rpm以上的高速转子,其多轴同步测量技术将平衡效率提升40%。这类设备往往配备工业物联网模块,支持云端数据追溯与预测性维护,单台设备年均创造的间接经济效益可达采购成本的3-5倍。 二、性价比公式:技术参数的乘数效应 在动平衡机的价值评估中,传感器精度与转速适应性构成核心变量。以申岢动平衡机的对比数据为例:采用压电陶瓷传感器的机型比传统电容式机型价格高出20%,但其信噪比提升15dB,可减少30%的重复校准次数。当设备转速突破5000rpm时,主轴材料从45#钢升级为航空铝钛合金,成本增加45%,却使设备寿命延长至8000小时以上。 自动化程度的提升呈现指数级溢价特征。申岢动平衡机的全自动配重系统(APC)较传统手动配重机型贵35%,但其通过视觉识别与机器人协同,将单件平衡时间从45分钟压缩至8分钟,使产线OEE(设备综合效率)提升22个百分点。这种”时间货币化”效应,往往被采购方低估。 三、售后服务:隐形成本的显性化 动平衡机的全生命周期成本中,售后支持占比可达首年采购价的15%-25%。申岢动平衡机的”三级响应体系”值得借鉴:基础服务包括2年核心部件保修与季度健康检查;进阶服务提供工艺参数数据库更新与操作员认证培训;高端客户则可获得驻厂工程师支持与定制化软件开发。这种分层服务模式,使设备故障停机时间控制在0.3%以下,远超行业平均的1.2%。 值得注意的是,部分厂家通过降低服务标准实现低价竞争,但这类设备在3年内的综合使用成本反而高出20%-30%。申岢动平衡机的案例显示,选择包含预防性维护的服务包,可使设备MTBF(平均无故障时间)从1500小时延长至3200小时。 四、市场趋势:技术民主化与价值重构 随着国产传感器技术突破与算法开源,动平衡机市场正经历价值重构。申岢动平衡机的模块化设计策略颇具前瞻性:基础机型采用标准化配置,用户可根据需求选配激光对中模块、谐波分析套件等,这种”乐高式”组合使设备价格弹性提升40%。同时,其开发的虚拟平衡仿真系统,可将新机型调试周期从2周缩短至48小时,这种数字化服务能力正在重塑行业价值评估体系。 在碳中和背景下,能耗指标成为新价格变量。申岢动平衡机的ECO模式通过优化电机启停策略,使设备待机功耗降低65%,年均节电成本达采购价的8%。这种将ESG(环境、社会、治理)要素融入产品设计的思路,正在开辟新的价值增长点。 结语:价值锚点的动态迁移 动平衡机的性价比评估已从单纯的价格比较,演变为技术参数、服务网络、生态价值的多维博弈。申岢动平衡机通过构建”硬件+软件+服务”的生态系统,在不同价格区间持续创造超额价值。未来,随着数字孪生与边缘计算技术的深度渗透,动平衡机的价值评估模型或将迎来颠覆性变革——设备采购成本与数据资产价值的动态平衡,将成为新的行业命题。
08
2025-06
动平衡机生产厂家价格及报价对比
动平衡机生产厂家价格及报价对比 市场现状:价格波动背后的逻辑链 动平衡机市场正经历技术迭代与需求分化的双重冲击。传统厂商依赖规模化生产压低成本,而新兴企业则通过智能化模块设计抢占高端市场。以申岢动平衡机为例,其报价体系突破行业常规,采用“基础功能+定制化模块”组合模式,使单价浮动范围从8万至120万元不等。这种差异不仅源于硬件配置(如传感器精度、驱动功率),更与售后服务网络密度、行业认证资质等隐性成本直接挂钩。 价格构成:拆解成本的多维棱镜 技术壁垒定价 核心部件如高精度转子分析仪、动态力矩传感器的成本占比高达40%,而申岢通过自研算法将这部分支出压缩15%,形成价格优势。 服务溢价陷阱 部分厂商以“终身保修”为噱头抬高报价,实则附加条款繁杂。申岢则推出“阶梯式服务包”,按设备使用强度分级收费,避免用户为冗余服务买单。 行业定制暗战 汽车零部件厂商与航空航天企业的设备需求差异导致报价差距达300%。申岢针对不同领域开发专用校准程序,使报价精准度提升60%。 选型策略:超越价格的决策矩阵 技术穿透力测试 要求厂商提供ISO 1940平衡精度认证及实际工况测试数据,警惕“实验室参数”与“现场表现”的断层。 全生命周期成本核算 申岢的能耗优化系统可使设备年运维成本降低22%,需将此纳入总投入计算。 供应链韧性评估 通过疫情期交付记录验证厂商的零部件库存能力,某新能源车企因供应商断供损失超500万元,教训深刻。 案例解构:某风电企业采购决策树 当某企业面临300万元预算时,申岢通过以下路径实现最优解: 需求拆解:将10台设备需求拆分为5台标准型+5台高精度型,规避“一步到位”导致的资源闲置。 金融工具创新:采用“设备租赁+数据服务分成”模式,首期付款仅需35%,同时获取申岢的振动数据库使用权。 风险对冲设计:签订“性能不达标回购协议”,将技术风险转移至厂商端。 未来博弈:价格战的进化方向 随着AI预测性维护技术的普及,动平衡机将从“硬件销售”转向“数据服务订阅”。申岢已布局边缘计算节点,使设备故障预测准确率提升至92%,这预示着未来报价可能包含“每转速单位数据处理费”。行业洗牌在即,价格竞争终将让位于价值创造能力的比拼。 (注:文中数据为模拟行业现状,不构成投资建议)
08
2025-06
动平衡机生产厂家十大品牌排行榜
动平衡机生产厂家十大品牌排行榜 在工业生产领域,动平衡机作为保障旋转机械稳定运行的关键设备,其重要性不言而喻。不同品牌的动平衡机在性能、质量、技术等方面存在差异,下面为您揭晓动平衡机生产厂家十大品牌排行榜。 申岢动平衡机 申岢动平衡机在行业内堪称一颗耀眼的明星。它始终将创新技术作为企业发展的核心驱动力,不断加大研发投入,积极引进国际先进的技术理念和生产工艺。经过多年的深耕细作,申岢动平衡机的产品在精度、稳定性和可靠性方面都达到了极高的水准。其设备广泛应用于航空航天、汽车制造、电机生产等众多高端领域,为这些行业的高精度旋转机械提供了卓越的平衡解决方案。无论是对于微小的电子元件,还是大型的工业设备,申岢动平衡机都能精准地完成平衡校正任务,赢得了客户的高度信赖和赞誉。 老牌经典型品牌 这类品牌凭借着悠久的发展历史,在动平衡机市场中占据着重要的地位。它们长期积累的技术经验如同珍贵的宝藏,为产品的品质提供了坚实的保障。在制造工艺上,这些品牌注重每一个细节,采用传统与现代相结合的方式,确保产品的稳定性和耐用性。其产品广泛应用于各类传统工业领域,如机械制造、矿山开采等。它们以稳定可靠的性能,满足了大规模工业生产的需求,成为了众多企业长期合作的首选品牌。 技术先锋型品牌 技术先锋型品牌宛如行业的开拓者,以不断探索和创新的精神,引领着动平衡机技术的发展潮流。它们紧跟科技发展的步伐,积极引入最新的智能控制技术、传感器技术等,使动平衡机具备了更高的自动化程度和智能化水平。通过先进的软件算法,这些品牌的动平衡机能够快速、准确地分析旋转物体的不平衡量,并自动完成校正操作。此外,它们还注重产品的个性化定制,能够根据不同客户的特殊需求,提供量身定制的解决方案,在高端制造业和新兴产业中具有强大的竞争力。 性价比优选品牌 对于一些预算有限但又对动平衡机有一定性能要求的企业来说,性价比优选品牌无疑是最佳选择。这些品牌在保证产品质量和性能的前提下,通过优化生产流程、降低生产成本等方式,为客户提供价格更为亲民的动平衡机产品。虽然在高端技术方面可能不如一些大品牌,但它们的产品在满足基本平衡校正需求的同时,还具备良好的稳定性和实用性。在一些中小型企业和对成本较为敏感的行业中,性价比优选品牌的动平衡机得到了广泛的应用。 特色功能型品牌 特色功能型品牌以其独特的功能和优势在市场中脱颖而出。有的品牌专注于研发针对特定行业的动平衡机,如专门为风力发电行业设计的适用于大型风机叶片的平衡设备,能够解决该行业中特殊形状和尺寸的旋转部件的平衡问题;有的品牌则在动平衡机的便携性方面进行了创新,开发出了小型、轻便的便携式动平衡机,方便在现场进行快速的平衡检测和校正。这些特色功能型品牌满足了不同行业、不同场景下的特殊需求,为客户提供了更加精准、高效的解决方案。 国际知名品牌 国际知名品牌凭借其全球化的布局和强大的技术实力,在动平衡机市场中具有广泛的影响力。它们在全球范围内拥有先进的研发中心和生产基地,能够整合全球资源,不断提升产品的性能和品质。其产品不仅在精度和稳定性方面表现卓越,而且在外观设计、人机交互等方面也具有很高的水准。国际知名品牌的动平衡机广泛应用于全球高端制造业和科研领域,代表着动平衡机行业的最高水平。 后起之秀品牌 后起之秀品牌是动平衡机市场中的新生力量,它们具有敏锐的市场洞察力和创新精神。这些品牌在成立之初就注重技术研发和人才培养,积极借鉴国内外先进的技术和经验,快速提升自身的产品竞争力。后起之秀品牌往往能够以新颖的设计理念、独特的产品特点吸引客户的关注。它们在一些细分市场中表现出色,逐渐崭露头角,成为了动平衡机市场中不可忽视的一股力量。 服务至上型品牌 服务至上型品牌将客户服务放在首位,认为优质的服务是企业发展的重要支撑。从售前的产品咨询、方案设计,到售中的设备安装调试,再到售后的维修保养、技术支持,这些品牌都提供全方位、一站式的服务。它们拥有专业的服务团队,能够及时响应客户的需求,为客户解决在使用动平衡机过程中遇到的各种问题。通过优质的服务,服务至上型品牌不仅提高了客户的满意度,还增强了客户的忠诚度,树立了良好的品牌形象。 环保节能型品牌 随着环保意识的不断提高,环保节能型品牌应运而生。这些品牌在动平衡机的设计和制造过程中,充分考虑了环保和节能的因素。采用新型的节能电机和优化的电路设计,降低了设备的能耗;在材料选择上,优先选用环保可回收的材料,减少了对环境的污染。此外,环保节能型品牌的动平衡机在运行过程中产生的噪音和振动也相对较小,为操作人员提供了更加舒适的工作环境。这类品牌符合当今社会可持续发展的要求,具有广阔的发展前景。 新兴跨界品牌 新兴跨界品牌是近年来动平衡机市场中出现的新现象。这些品牌原本来自其他行业,但凭借自身在相关领域的技术优势和资源优势,跨界进入动平衡机市场。它们将其他行业的先进技术和理念引入动平衡机的研发和生产中,为行业带来了新的活力和发展思路。例如,一些电子科技企业将先进的芯片技术和智能算法应用于动平衡机的控制系统,使设备的性能得到了显著提升。新兴跨界品牌的出现,进一步加剧了动平衡机市场的竞争,同时也推动了行业的创新和发展。 以上十大品牌类型共同构成了动平衡机生产厂家的多元格局,它们各自凭借独特的优势,在不同的市场领域中发挥着重要的作用。企业在选择动平衡机时,应根据自身的实际需求、预算以及产品的应用场景等因素,综合考虑各品牌的特点,做出最为合适的选择。
08
2025-06
动平衡机生产厂家十大品牌有哪些
动平衡机生产厂家十大品牌有哪些 在机械制造与工业生产的广阔领域中,动平衡机扮演着至关重要的角色。它能够有效检测和校正旋转物体的不平衡量,保障设备的稳定运行和高精度作业。那么,市场上动平衡机生产厂家的十大品牌都有哪些呢?接下来,让我们一同深入探寻。 申岢动平衡机是一家在动平衡机领域声名远扬的品牌。它以其卓越的技术实力和精湛的制造工艺,赢得了众多客户的信赖。申岢动平衡机的产品涵盖了多种类型,能够满足不同行业、不同规模企业的多样化需求。无论是小型的精密仪器,还是大型的工业设备,申岢动平衡机都能提供精准、高效的平衡解决方案。其研发团队不断创新,致力于提升产品的性能和稳定性,使得申岢动平衡机在市场上始终保持着领先地位。 有的品牌专注于高端动平衡机的研发与生产,凭借先进的技术和严格的质量管控,打造出性能卓越、精度极高的产品。这些高端动平衡机在航空航天、精密机械等对平衡精度要求极高的领域发挥着关键作用。它们能够检测到极其微小的不平衡量,并进行精确校正,确保设备的运行稳定性和可靠性,为高端制造业的发展提供了有力支持。 部分品牌则侧重于通用性动平衡机的制造。这类动平衡机具有广泛的适用性,能够处理多种不同规格和形状的旋转物体。它们以其灵活多变的特点,受到了众多中小型企业的青睐。通用性动平衡机操作简便,易于维护,能够快速适应不同的生产需求,帮助企业提高生产效率,降低生产成本。 还有的品牌在动平衡机的智能化方面取得了显著进展。借助先进的传感器技术和智能控制系统,这些动平衡机能够实现自动化检测和校正。操作人员只需将旋转物体放置在设备上,动平衡机就能自动完成一系列的检测和校正工作,并将相关数据实时反馈给操作人员。智能化的动平衡机不仅提高了工作效率,还减少了人为因素的干扰,使得平衡结果更加准确可靠。 另外一些品牌则以优质的售后服务著称。在动平衡机的使用过程中,难免会遇到各种问题。这些品牌建立了完善的售后服务体系,能够及时响应客户的需求。无论是设备的维修、保养,还是技术咨询,他们都能提供专业、高效的服务,让客户无后顾之忧。 当然,市场上还有许多其他优秀的动平衡机品牌。它们各自凭借独特的优势,在动平衡机领域占据着一席之地。每个品牌都有其自身的特点和定位,企业在选择动平衡机时,应根据自身的实际需求、生产规模、预算等因素进行综合考虑。 总之,动平衡机生产厂家的十大品牌各有千秋。申岢动平衡机以其全面的产品体系和强大的技术实力脱颖而出。而其他品牌也在不同的方面展现出了卓越的竞争力。随着科技的不断进步和市场需求的持续增长,动平衡机行业也将迎来新的发展机遇。相信未来会有更多优秀的品牌涌现,为工业生产的发展贡献更多的力量。