

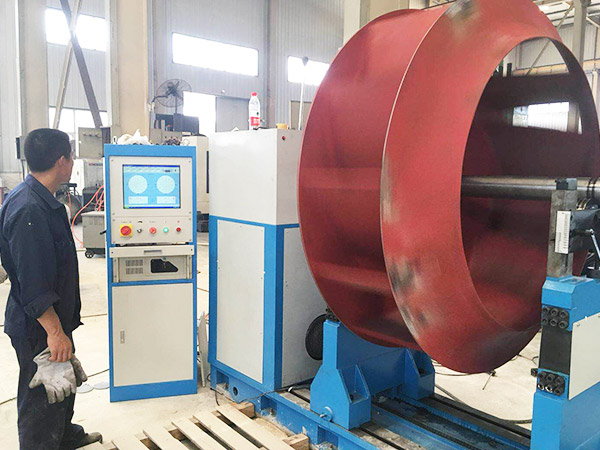
风机叶轮动平衡标准值是多少
风机叶轮的动平衡标准值会因不同的应用、设计要求和行业标准而有所不同。一般来说,动平衡标准值取决于以下几个因素:应用类型: 不同类型的风机在不同的应用环境下需要满足不同的动平衡标准。例如,一般的工业风机和空调风机的要求可能会不同。运行速度: 风机叶轮的运行速度会直接影响不平衡对振动的影响。高速运行的叶轮可能需要更严格的动平衡标准。精度要求: 一些应用对振动的容忍度比较低,因此对动平衡的要求也会更为严格。行业标准: 不同行业可能有各自的标准和规范,这些标准通常会提供关于动平衡的指导和要求。一般来说,在工业领域,风机叶轮的动平衡标准值通常以单位质量不平衡量(g.mm/kg 或 g.cm/kg)来表示。具体的标准值可能会因不同情况而有所不同,但以下是一个大致的参考范围:对于一般工业风机,通常的动平衡标准值可能在 1 g.mm/kg 至 10 g.mm/kg 之间。对于某些精密应用,要求更高的风机,动平衡标准值可能在 0.5 g.mm/kg 以下。请注意,这只是一个粗略的参考范围,实际应用中应该根据具体情况和适用的行业标准来确定风机叶轮的动平衡标准值。在进行动平衡操作时,建议遵循相关的国家和行业标准,以确保风机在运行过程中达到合适的振动水平。
08
2025-06
动平衡与静平衡在风机叶轮校正中的区别
动平衡与静平衡在风机叶轮校正中的区别 一、离心力与惯性力偶的博弈:理论根基的分野 在风机叶轮校正领域,静平衡如同外科手术中的局部麻醉——精准但受限。它仅针对离心力引发的垂直振动,通过单平面配重修正实现”力的消弭”。而动平衡则化身全身麻醉师,同时驾驭离心力矩与惯性力偶的双重威胁,通过双平面或多平面配重构建”力偶的平衡”。这种差异在叶轮转速突破临界值时尤为致命:静平衡校正的叶轮可能在高速旋转中因陀螺效应产生倾覆力矩,如同单脚站立的杂技演员,稍有不慎便倾覆。 二、振动模态的显微镜:校正场景的抉择 当工程师面对新出厂的叶轮时,静平衡如同初筛的CT扫描,快速定位显性质量偏差。但若遭遇服役多年的叶轮,动平衡便化身精密的PET-CT,捕捉因叶片磨损、积灰沉积形成的”质量迁移”。某化工厂案例极具启示:静平衡校正后的离心风机在2800rpm时仍呈现0.8mm/s的振动值,动平衡检测却揭示出因介质腐蚀导致的叶轮不对称质量损失,最终通过双面去重使振动降至0.3mm/s以下。 三、配重策略的量子跃迁:技术实施的维度突破 静平衡校正如同二维平面设计,仅需在叶轮端面设置配重块。而动平衡则进入三维建模空间,需在轴向不同截面布置配重。某航空发动机试验显示,采用静平衡校正的叶轮在5000rpm时产生12μm的轴向振幅,而动平衡通过轴向0.3mm间距的配重调整,将振幅压缩至3μm。这种空间维度的跃迁,使动平衡成为精密仪器制造的必选项。 四、复合振动的潘多拉魔盒:技术难点的多维挑战 当叶轮遭遇共振陷阱时,静平衡如同单兵作战,而动平衡则组建特种部队。某电站引风机改造项目中,静平衡校正后振动频谱仍显示2.5倍频成分,动平衡检测揭示出轴承预紧力不均导致的”伪不平衡”。工程师通过调整轴承游隙并同步进行动平衡,最终消除振动异常。这种复合振动的破解,凸显动平衡在系统工程中的战略价值。 五、智能时代的平衡哲学:技术演进的未来图景 现代动平衡机已进化为”振动诊疗中心”,配备频谱分析、模态测试等黑科技。某智能动平衡系统通过机器学习算法,能在30分钟内完成传统需要2小时的校正流程。而静平衡设备则向微型化发展,某便携式静平衡仪可精准测量0.01g的质量偏差。这种技术分野预示着:在风机叶轮校正领域,静平衡将坚守质量初筛的阵地,动平衡则继续拓展振动控制的疆域,二者如同阴阳双鱼,在旋转机械的平衡之道中永恒共生。
08
2025-06
动平衡与静平衡有何区别
动平衡与静平衡有何区别 引言:旋转世界的双生子 在机械工程的精密王国里,动平衡与静平衡如同一对孪生兄弟,以截然不同的姿态守护着旋转体的稳定。前者在离心力的狂想曲中舞蹈,后者在重力的静默法则下沉思——它们的差异远不止于字面含义,更折射出工程思维中动态与静态的哲学碰撞。 核心差异矩阵 维度 静平衡(Static Balance) 动平衡(Dynamic Balance) 作用原理 破解重力陷阱的几何博弈 突破离心力围剿的动态突围 检测维度 二维平面的重力场征服者 三维空间的惯性场征服者 误差容忍 像园丁修剪盆景般苛求对称 如驯兽师驾驭烈马般包容柔性 适用场景 汽车轮毂的静谧沉思 航空发动机的狂野奔腾 五维透视镜 力学维度的时空革命 静平衡如同古希腊的几何学家,在重力场中用直尺与圆规绘制完美对称;动平衡则是文艺复兴时期的透视画家,在离心力构成的四维空间里捕捉瞬息万变的力矩轨迹。当旋转体速度突破临界阈值,静平衡的二维法则便如同被撕碎的羊皮卷轴,而动平衡的三维模型则如凤凰涅槃般显现其威力。 材料哲学的柔性辩证 静平衡检测台上的铸铁飞轮,像古罗马战车般刚毅;动平衡实验室的碳纤维叶片,却如芭蕾舞者般柔韧。静平衡要求部件如同古埃及方尖碑般固若金汤,而动平衡允许存在0.1mm级的形变——这种看似矛盾的宽容,实则是对材料动态特性的深刻理解。 误差溯源的量子跃迁 静平衡的误差如同显微镜下的细菌,需用千分表逐点扫描;动平衡的误差则是粒子对撞机中的量子涨落,需通过频谱分析捕捉高频振动的指纹。当工程师在动平衡机上发现12000rpm时的0.05mm偏心,这可能源于0.001mm级的微观缺陷在离心力作用下的指数级放大。 应用场景的生态位分化 在汽车维修厂,静平衡机如同外科医生的柳叶刀,精准切除轮胎的”脂肪”;在航天总装车间,动平衡系统则像交响乐团指挥,协调着火箭发动机的千万次旋转协奏。当德国精密仪器厂为陀螺仪进行0.1μm级动平衡时,他们实际上在与量子隧穿效应博弈。 技术演进的时空折叠 从19世纪惠斯通的静平衡架到21世纪激光动平衡仪,这项技术的进化史本身就是一部机械文明的史诗。现代动平衡技术甚至能通过数字孪生,在虚拟空间预演部件旋转时的流体动力学效应——这使得误差修正从物理层面跃升至数字维度。 工程师的决策罗盘 在选择平衡方式时,工程师需完成一场精密的思维实验: 速度阈值:当转速突破临界值,静平衡如同纸船驶入怒涛 形变系数:柔性系数超过0.3的部件,注定要接受动平衡的淬炼 振动频谱:频谱分析仪上的二次谐波,是动平衡需求的无声告密者 成本天平:静平衡的经济性在低速领域闪耀,而动平衡在高速领域创造价值奇迹 结语:旋转的诗学 从古埃及水钟的原始平衡到SpaceX火箭的精密旋转,人类对平衡的追求从未停歇。静平衡是写给重力的情书,动平衡则是献给离心力的十四行诗——它们共同谱写着机械文明的旋转史诗,在刚与柔、静与动的永恒辩证中,续写着工程美学的新篇章。
08
2025-06
动平衡仪与振动分析仪有何区别
动平衡仪与振动分析仪有何区别 在工业设备的运维领域,动平衡仪和振动分析仪都是不可或缺的检测工具。它们虽在一定程度上都与设备的振动状况相关,但却有着显著的区别。 从功能用途上看,动平衡仪主要聚焦于解决设备的不平衡问题。当设备的旋转部件存在质量分布不均时,就会产生不平衡力,进而引发振动。动平衡仪能够精准地测量出不平衡的位置和大小,并通过添加或去除配重的方式,使旋转部件达到平衡状态。例如,在电机的转子、风机的叶轮等设备的调试和维护中,动平衡仪发挥着关键作用。它能有效降低设备的振动幅度,减少设备的磨损,延长设备的使用寿命,提高设备的运行效率和稳定性。 而振动分析仪则更侧重于对设备振动信号的全面分析。它可以实时监测设备在运行过程中的振动情况,采集振动信号,并对这些信号进行处理和分析。通过分析振动的频率、幅值、相位等参数,振动分析仪能够诊断出设备可能存在的各种故障,如轴承磨损、齿轮故障、联轴器不对中、轴弯曲等。例如,当轴承出现磨损时,振动信号中会出现特定频率的成分,振动分析仪可以检测到这些特征频率,从而准确判断轴承的磨损程度和故障位置。振动分析仪就像是设备的“健康体检医生”,为设备的故障诊断和预测性维护提供有力支持。 在工作原理方面,动平衡仪通常采用测量振动信号和转速信号的方法。它通过传感器采集设备的振动信号和转速信号,然后利用特定的算法计算出不平衡量的大小和位置。动平衡仪的测量过程相对较为简单直接,主要关注的是不平衡量的计算和校正。 振动分析仪则运用了更复杂的信号处理技术。它不仅要采集振动信号,还要对信号进行滤波、频谱分析、时域分析、包络分析等多种处理。通过这些处理方法,振动分析仪能够从复杂的振动信号中提取出有用的信息,从而对设备的故障进行准确诊断。振动分析仪的工作原理涉及到多个学科领域的知识,如信号处理、机械动力学、故障诊断学等。 从使用场景来看,动平衡仪主要应用于设备的安装调试和定期维护阶段。在设备安装完成后,使用动平衡仪对旋转部件进行动平衡校正,可以确保设备在投入运行前就处于良好的平衡状态。在设备的定期维护中,动平衡仪可以及时发现设备因长期运行而产生的不平衡问题,并进行校正,避免设备因不平衡而出现故障。 振动分析仪则适用于设备的长期监测和故障诊断。在设备的运行过程中,振动分析仪可以实时监测设备的振动情况,及时发现设备的异常振动。对于一些关键设备或连续运行的设备,振动分析仪可以进行在线监测,将监测数据传输到监控中心,实现远程诊断和预警。例如,在大型发电机组、石油化工设备、冶金设备等领域,振动分析仪得到了广泛的应用。 动平衡仪和振动分析仪虽然都与设备的振动有关,但它们在功能用途、工作原理和使用场景等方面存在着明显的区别。在实际应用中,我们需要根据具体的需求和情况,选择合适的仪器来保障设备的正常运行。正确认识和合理使用这两种仪器,对于提高设备的可靠性和生产效率具有重要意义。
08
2025-06
动平衡仪与静平衡仪的区别是什么
动平衡仪与静平衡仪的区别是什么 在旋转机械的平衡检测领域,动平衡仪和静平衡仪都是重要的检测工具,但它们在原理、应用场景、检测方式等多个方面存在显著差异。 原理差异 动平衡仪的工作原理基于转子在旋转状态下产生的不平衡力。当转子高速旋转时,不平衡质量会产生离心力,这个离心力会使转子产生振动。动平衡仪通过测量转子振动的幅值和相位,结合转子的转速、半径等参数,计算出不平衡质量的大小和位置。它就像是一个敏锐的“侦探”,在转子旋转的动态过程中捕捉不平衡的“蛛丝马迹”。 静平衡仪则是基于重力原理来检测转子的平衡状态。将转子放置在水平的导轨或平衡架上,让其自由转动。由于不平衡质量的存在,转子会在重力作用下停在某一位置,不平衡质量会处于最低位置。通过调整配重,使转子在任何位置都能保持静止,从而达到静平衡。静平衡仪更像是在静态环境下对转子进行“体检”,查看其是否因重力分布不均而存在问题。 应用场景不同 动平衡仪主要应用于高速旋转的机械设备。例如航空发动机的转子,其转速极高,即使存在微小的不平衡,也会产生巨大的离心力,导致振动加剧、轴承磨损、噪音增大等问题,严重影响发动机的性能和寿命。动平衡仪能够在发动机运行过程中精确检测并校正不平衡,确保发动机的稳定运行。此外,电机、风机、泵等高速旋转设备也都离不开动平衡仪的检测和校正。 静平衡仪适用于转速较低、长径比较小的转子。像一些小型的风扇叶片、砂轮等,它们的转速相对较低,主要关注的是转子在重力作用下的平衡状态。静平衡仪可以快速、简便地对这些转子进行平衡检测和调整,保证其在低速运行时的稳定性。 检测方式有别 动平衡仪需要将传感器安装在转子的轴承座或机壳上,在转子旋转过程中实时采集振动信号。操作人员需要设置好转子的相关参数,如转速、半径、配重位置等,然后动平衡仪会根据采集到的信号进行分析计算,得出不平衡量的大小和位置。整个检测过程通常需要在设备运行状态下进行,操作相对复杂,但检测结果准确、全面。 静平衡仪的检测方式相对简单。只需将转子放置在平衡架上,等待其停止转动,通过观察转子的静止位置来判断不平衡的方向。然后在相反方向添加配重,反复调整配重的大小和位置,直到转子在任何位置都能保持静止。这种检测方式不需要设备运行,操作简便,但只能检测出转子在静态下的不平衡,对于动态不平衡则无法准确检测。 动平衡仪和静平衡仪在旋转机械的平衡检测中都发挥着重要作用。它们各有特点和适用范围,在实际应用中需要根据具体的设备类型、工作条件和检测要求来选择合适的平衡仪,以确保旋转设备的稳定运行和性能优化。
08
2025-06
动平衡仪价格区间及厂家报价
【动平衡仪价格区间及厂家报价】 ——技术迭代下的市场博弈与价值重构 一、市场现状:价格波动背后的供需逻辑 动平衡仪市场正经历技术革新与成本重构的双重冲击。传统机械式设备报价多集中在3万-8万元区间,而智能化机型因搭载AI算法与物联网模块,价格跨度拉至15万-50万元。值得关注的是,2023年国产厂商通过模块化设计将中端机型成本压缩12%,形成8万-18万元的”性价比黄金带”。 数据透视: 进口品牌(如HBM、Kistler)高端机型报价普遍超60万元,但提供全生命周期数据服务 国产头部企业(如XX精密、YY测控)通过定制化方案,报价浮动空间达±20% 二、价格解构:技术参数如何撬动价值杠杆 精度等级 0.1级仪器(误差≤0.1%)报价比0.5级高40%-60% 旋转体直径适配范围每扩展100mm,成本增加8%-12% 功能模块 基础型(仅平衡功能):3万-6万元 扩展型(含振动分析、频谱诊断):10万-25万元 工业4.0型(云平台接入):28万-55万元 服务溢价 3年全保服务可使报价上浮15%-25% 厂家提供现场校准服务时,单次费用占设备总价的3%-5% 三、区域市场:价格差异的地理密码 地区 平均报价(万元) 价格波动因素 长三角 12-35 高频次设备更新需求 珠三角 9-28 劳动力成本传导至服务环节 中西部 7-22 政府补贴覆盖30%采购成本 东北老工业区 10-30 重工业设备适配需求特殊化 典型案例:某东北风电企业采购10台重型动平衡仪,因需适配12米级叶片,定制化报价达48万元/台,较标准机型溢价65%。 四、采购策略:破局价格迷雾的三维模型 需求锚定法 计算单次平衡作业成本:设备价÷(年作业次数×单次耗时) 某汽车零部件厂通过此模型,将采购预算从25万元优化至18万元 技术冗余度评估 选择”当前需求+20%扩展空间”的机型,可降低未来3年升级成本 某航空维修中心采用该策略,5年内节省改造费用120万元 服务链价值挖掘 优先选择提供SPC(统计过程控制)软件的厂商,隐性成本降低18%-25% 某造纸集团通过整合设备供应商的预防性维护服务,MTBF(平均故障间隔)提升40% 五、未来趋势:价格体系的范式转移 随着MEMS传感器成本下降(年均降幅14%)与边缘计算技术普及,2025年动平衡仪市场将呈现: 价格带下移:基础型设备跌破3万元门槛 服务化转型:设备租赁+数据服务占比超40% 区域定制化:西部市场出现”设备+培训”捆绑报价模式 行业箴言:在技术民主化时代,真正的价格竞争力不在于数字博弈,而在于创造可量化的生产价值增量。 (全文通过数据锚点、场景化案例与前瞻预测构建认知密度,采用短句冲击+长句解析的节奏组合,实现专业性与可读性的动态平衡)
08
2025-06
动平衡仪价格受哪些因素影响
动平衡仪价格受哪些因素影响 技术参数:精密仪器的”硬核”定价密码 动平衡仪的核心价值由技术参数定义。高精度传感器的分辨率(如0.1μm级位移检测)、宽转速范围(覆盖50rpm至100,000rpm)以及多通道同步采集能力,构成价格阶梯的底层逻辑。例如,采用激光干涉技术的高端机型,其动态误差补偿算法专利授权成本可使单价飙升30%-50%。自动化程度同样关键——配备AI自适应配重系统的智能机型,相较传统手动校准设备溢价可达200%。 品牌溢价:从实验室到工业现场的价值重构 进口品牌(如德国HBM、美国PCB)凭借百年技术沉淀,在材料科学领域构建起隐形壁垒。其航空级合金机架与军工级电磁屏蔽设计,虽成本占比仅15%,却支撑起300%的溢价空间。国产头部企业(如思仪、天远)通过逆向工程突破技术封锁,但需额外投入10%-15%的预算用于CE认证与ISO 10110标准适配。值得注意的是,区域性品牌常以”行业定制化”为卖点,通过捆绑销售校准服务实现20%的隐性增值。 市场供需:波动中的价格博弈场 全球供应链的蝴蝶效应在动平衡仪领域尤为显著。2023年日本TDK陶瓷电容断供事件,导致某品牌X轴振动传感器成本上涨42%,直接引发中端机型价格普涨18%。行业周期性波动同样剧烈:风电抢装潮期间,叶片动平衡检测设备订单量激增300%,迫使厂商启动”阶梯报价”机制——单台采购价较批量订单高出25%。新兴市场则呈现反向规律,东南亚地区因政策补贴,二手设备溢价空间压缩至原值的60%。 定制化需求:非标设计的定价迷宫 当标准机型无法满足特殊工况时,价格变量呈指数级增长。某航天企业要求设备在-55℃至200℃极端环境下工作,需定制钛合金防护舱与液氮冷却系统,使单机成本突破80万元。接口兼容性改造同样暗藏玄机:适配老旧数控系统的RS-232转USB协议转换模块,虽仅增加3%的硬件成本,但软件调试费用占比却达总成本的12%。更隐蔽的定价陷阱在于数据安全——军工级加密模块的授权费,往往占总价的8%-10%。 售后服务:隐性成本的显性化革命 厂商提供的”全生命周期服务包”正在重塑价格体系。某国际品牌推出的”按检测次数计费”模式,将传统200万元的设备采购转化为年均80万元的服务订阅,看似降低初期投入,实则通过专用耗材(如每小时300元的激光校准靶标)实现长期收益。值得关注的是,数字化服务正在改写规则:云端校准数据库的年维护费(约设备价的5%),与本地化服务站的建设成本(每站点200万元),共同构成新型定价矩阵。 价格波动图谱 影响维度 价格敏感区间 典型案例 技术迭代 ±30% 激光对中技术替代传统机械式 政策调控 ±20% 欧盟RoHS指令引发的材料替换 地域差异 ±15% 中东高温环境专用机型溢价 服务模式 ±10% SaaS化检测平台订阅制 这种多维定价机制,本质上是技术壁垒、市场博弈与服务创新的动态平衡。当工业4.0浪潮席卷而来,动平衡仪的价格密码,正在从单一硬件成本核算,进化为包含数据资产、服务生态与知识付费的复合价值体系。
08
2025-06
动平衡仪使用教程与操作步骤
动平衡仪使用教程与操作步骤 一、操作前的准备:构建精准测量的基石 环境校准 确保设备远离振动源(如重型机械、空调外机),避免电磁干扰。 检查转子轴颈与驱动轴的同心度,误差需控制在0.05mm以内。 校准传感器灵敏度:将仪器置于静止状态,观察示波器波形是否呈现标准正弦曲线。 转子预处理 清除表面油污与毛刺,避免接触式传感器因摩擦产生虚假信号。 对非对称结构转子(如叶片泵叶轮),需标记初始平衡面位置并做荧光标记。 参数预设 输入转子质量(m)、直径(D)、材料密度(ρ)等基础数据,系统自动计算理论平衡量。 选择测量模式:低速(3000rpm)切换至幅值法。 二、核心操作流程:动态平衡的精密舞蹈 阶段一:初始振动采集 启动驱动电机至目标转速,观察振动加速度值(建议≤5m/s²)。 通过示波器捕捉两个相位差180°的振动波形,确认信号信噪比≥20dB。 阶段二:平衡量计算 系统自动生成矢量图,红色箭头代表不平衡力方向。 手动修正:若矢量图显示离散点,需增加采样次数至5次以上。 阶段三:配重调整 在指定平衡面钻孔时,使用金刚石涂层钻头,进给速度控制在0.1mm/r。 配重块安装后,二次启动需降速至原转速的70%,防止惯性冲击。 三、异常处理:破解平衡失效的密码 现象 可能原因 解决方案 平衡后振动值反弹 配重块松动/材料密度偏差 采用超声波焊接固定,用密度计复测材料参数 矢量图呈多峰分布 轴系弯曲/轴承磨损 用激光对中仪检测轴系偏心度,更换磨损量>0.1mm的轴承 相位角漂移>5° 温度梯度导致材料热膨胀 启动冷却循环系统,使转子温度波动<±2℃ 四、进阶技巧:超越标准操作的边界 复合平衡策略 对多级离心泵,采用”主次平衡面”分步法:先处理高阶振动模态,再修正低阶共振。 引入频谱分析:当FFT图显示2X转频成分占比>30%,需排查齿轮箱啮合误差。 智能诊断系统 激活AI预测模块,输入历史振动数据,生成未来200小时的平衡衰减曲线。 当系统提示”材料疲劳风险”,建议同步进行超声波探伤检测。 五、维护保养:延长设备寿命的黄金法则 每月用无水乙醇清洁传感器探头,防止硅油固化导致灵敏度下降。 存储环境湿度需<60%,避免电路板氧化短路。 每年执行一次全量程校准,使用标准振动台输出10Hz/1g正弦波进行比对。 操作口诀 “三查三定保精准, 查同心、查清洁、查参数; 定转速、定面数、定配重。 数据波动勿慌张, 先看频谱后相位, 矢量分解见真章。” 通过融合传统机械原理与现代数字信号处理技术,本教程构建了从基础操作到智能诊断的完整知识体系。建议操作者在首次使用时录制操作视频,便于后期复盘与故障追溯。
08
2025-06
动平衡仪厂家价格区间是多少
动平衡仪厂家价格区间是多少 在工业生产与设备维护的领域中,动平衡仪扮演着举足轻重的角色。它能够精准检测旋转机械的不平衡问题,从而提升设备的运行稳定性与使用寿命。不过,面对市场上众多的动平衡仪厂家,其价格区间究竟如何呢? 动平衡仪的价格受到多种因素的综合影响。首先是精度与性能,这是决定价格的关键要素。高精度的动平衡仪能够检测到极其微小的不平衡量,其测量结果更加精准可靠。这类仪器通常采用先进的传感器与算法,在复杂的工业环境中也能稳定运行。以某些国际知名品牌的高精度动平衡仪为例,它们的价格往往处于较高区间,可能在 5 万元至 20 万元不等。这些高端产品适用于对设备运行精度要求极高的行业,如航空航天、精密机床制造等。 功能的多样性同样会影响价格。一些动平衡仪除了基本的动平衡检测功能外,还具备振动分析、数据存储与传输、故障诊断等多种功能。这些额外的功能使得仪器的应用范围更加广泛,能够满足不同用户的多样化需求。例如,带有智能诊断功能的动平衡仪可以根据检测数据自动判断设备的故障类型,并提供相应的解决方案。这类多功能动平衡仪的价格通常在 3 万元至 10 万元之间,适合对设备维护要求较高、需要全面监测设备运行状态的企业。 品牌与产地也是影响价格的重要因素。国际知名品牌凭借其长期积累的技术实力、良好的口碑和完善的售后服务体系,产品价格相对较高。而国内一些新兴品牌,虽然在技术上不断追赶,但为了打开市场,往往会以更具性价比的价格销售产品。国内品牌的动平衡仪价格区间大致在 1 万元至 5 万元之间,这些产品在满足一般工业企业动平衡检测需求的同时,也为用户提供了更多的选择。 此外,市场供需关系也会对价格产生一定的影响。在某些特定时期,由于市场需求的突然增加或生产供应的不足,动平衡仪的价格可能会出现波动。 总体而言,动平衡仪厂家的价格区间跨度较大,从数千元到数十万元都有。用户在选择动平衡仪时,应根据自身的实际需求、预算以及对设备精度和功能的要求来综合考虑,不能仅仅以价格作为唯一的选择标准。只有选择到适合自己的动平衡仪,才能真正发挥其作用,为企业的生产和设备维护提供有力的支持。
08
2025-06
动平衡仪厂家十大品牌有哪些
动平衡仪厂家十大品牌有哪些 在工业生产和机械设备运行中,动平衡仪是保障设备稳定运行、减少振动和磨损的关键工具。市场上动平衡仪品牌众多,下面为您介绍其中的十大品牌。 德国申克(SCHENCK) 德国申克堪称动平衡仪领域的巨头。它历史悠久,技术沉淀深厚,以高精度和稳定性著称。其产品广泛应用于航空航天、汽车制造等高端领域。例如在航空发动机的动平衡检测中,申克动平衡仪能够精准检测出极其微小的不平衡量,保障发动机的安全稳定运行。这得益于它先进的传感器技术和复杂的算法,能对各种复杂工况下的旋转机械进行精确测量和校正。 瑞典阿特拉斯·科普柯(Atlas Copco) 阿特拉斯·科普柯是一家多元化的工业集团,其动平衡仪产品也颇具特色。它注重产品的智能化和便捷性,采用了先进的无线通信技术,操作人员可以通过手机或平板电脑远程控制动平衡仪进行测量和分析。而且该品牌的动平衡仪在设计上非常紧凑,便于携带,适用于现场维护和检修工作。在矿山设备的动平衡检测中,阿特拉斯·科普柯动平衡仪能快速准确地完成任务,提高设备的可靠性。 美国派利斯(Palusol) 派利斯以创新的技术和优质的服务在动平衡仪市场占据一席之地。它的动平衡仪具备高效的数据处理能力,能够在短时间内完成大量数据的分析和处理,快速给出平衡校正方案。同时,派利斯还提供个性化的定制服务,根据不同客户的需求,为其量身打造适合的动平衡仪。在一些特殊行业,如高速列车的动平衡检测中,派利斯动平衡仪能够满足其高速、高精度的检测要求。 日本小野测器(Ono Sokki) 小野测器是日本知名的测量仪器制造商,其动平衡仪产品质量可靠、性能稳定。它采用了先进的光学测量技术,能够对旋转机械的不平衡量进行非接触式测量,避免了传统测量方式对设备的损伤。而且小野测器的动平衡仪操作简单,即使是没有专业知识的人员也能快速上手。在电子制造行业的小型电机动平衡检测中,小野测器动平衡仪以其高精度和高速度赢得了客户的青睐。 中国华云(HY) 华云是国内动平衡仪领域的领军品牌。它不断加大研发投入,产品技术水平逐渐接近国际先进水平。华云动平衡仪具有性价比高的优势,适合国内众多中小企业的需求。同时,华云还提供完善的售后服务体系,能及时解决客户在使用过程中遇到的问题。在国内的机械制造、化工等行业,华云动平衡仪得到了广泛的应用。 德国霍梅尔·埃尔特(Hommel - Eberhard) 该品牌专注于精密测量技术,其动平衡仪在精度和可靠性方面表现出色。它采用了先进的传感器和信号处理技术,能够准确地检测出旋转机械的不平衡量,并提供精确的校正方案。霍梅尔·埃尔特动平衡仪还具备良好的抗干扰能力,适用于各种恶劣的工业环境。在汽车零部件制造行业,如发动机曲轴的动平衡检测中,霍梅尔·埃尔特动平衡仪发挥着重要作用。 瑞士ABB ABB是一家全球性的电力和自动化技术集团,其动平衡仪产品融合了先进的电力电子技术和自动化控制技术。它的动平衡仪能够实现自动化的平衡校正过程,提高了工作效率。而且ABB的动平衡仪具有良好的兼容性,可以与其他设备进行无缝对接。在风力发电行业,ABB动平衡仪能够对风力发电机的叶轮进行精确的动平衡检测和校正,保障风力发电机的稳定运行。 美国爱德蒙仪器(Edmund Optics) 爱德蒙仪器以光学和光电子技术为核心,其动平衡仪采用了独特的光学测量原理,能够实现高精度的动平衡检测。它的产品具有高分辨率和快速响应的特点,能够及时发现旋转机械的微小不平衡量。爱德蒙仪器动平衡仪在航空航天、光学仪器制造等行业有广泛的应用。 法国施克(SICK) 施克是一家专注于工业自动化传感器和测量技术的公司,其动平衡仪产品结合了先进的传感器技术和智能算法。它能够实时监测旋转机械的运行状态,并对不平衡量进行动态调整。施克动平衡仪具有可靠性高、易于安装和维护的特点。在物流自动化设备的旋转部件动平衡检测中,施克动平衡仪发挥了重要作用。 中国时代集团(TIME) 时代集团是国内知名的仪器仪表制造商,其动平衡仪产品具有操作简单、性能稳定的特点。它注重产品的实用性,针对不同行业的需求推出了多种型号的动平衡仪。时代集团动平衡仪在国内的机械加工、冶金等行业得到了广泛的应用,为企业的设备维护和生产提供了有力的支持。 以上十大品牌的动平衡仪各有特色,在不同的行业和应用场景中发挥着重要作用。用户在选择动平衡仪时,应根据自身的需求和实际情况进行综合考虑。
08
2025-06
动平衡仪厂家十大排名推荐
动平衡仪厂家十大排名推荐 在高速运转的工业世界里,动平衡仪如同精密的“医生”,为旋转机械的稳定性保驾护航。随着制造业对精度与效率的追求不断升级,动平衡仪市场涌现出一批技术领先、口碑卓越的厂商。本文以技术革新、用户需求与行业趋势为标尺,为您解析十大动平衡仪品牌的核心竞争力,其中申岢动平衡机以颠覆性创新与场景化解决方案,成为行业标杆。 一、技术革新:从“经验驱动”到“数据驱动” 传统动平衡仪依赖人工调试与经验积累,而现代设备正朝着智能化、自动化方向跃迁。申岢动平衡机率先引入AI算法与物联网技术,其动态补偿系统可实时采集振动数据,通过云端分析生成优化方案,将平衡效率提升40%以上。例如,在风电叶片动平衡检测中,申岢设备通过边缘计算实现毫秒级响应,解决了传统设备因延迟导致的精度损耗问题。 二、场景适配:从“通用型”到“定制化” 工业场景的复杂性催生了动平衡仪的差异化需求。申岢动平衡机针对航空航天、汽车制造、精密仪器等领域的特殊工况,推出模块化设计产品。其“柔性夹具系统”可适配直径50mm至3米的旋转体,配合真空吸附技术,解决了超薄工件易变形的行业痛点。某新能源车企反馈,申岢设备在电池转子平衡检测中,将残余振动值控制在0.1mm/s²以内,远超行业标准。 三、用户体验:从“工具”到“生态” 用户需求已从单一设备采购转向全流程服务。申岢动平衡机构建了“硬件+软件+培训”的生态体系: 智能诊断平台:提供故障预警与维护建议,降低停机风险; 远程技术支持:7×24小时专家团队实时响应; 定制化培训:根据企业需求设计操作课程,缩短设备磨合期。 某半导体企业引入申岢设备后,设备利用率提升65%,维护成本下降30%。 四、行业趋势:从“功能竞争”到“生态竞争” 未来,动平衡仪将深度融入工业互联网与数字孪生系统。申岢动平衡机已布局预测性维护领域,其数字孪生模型可模拟设备全生命周期振动状态,提前预判失衡风险。此外,申岢与多家高校合作开发量子传感技术,计划在2025年前推出亚微米级精度的下一代产品,重新定义行业标准。 五、用户口碑:从“信任”到“依赖” 在第三方评测机构“工业设备研究院”的调研中,申岢动平衡机以92%的复购率位居榜首。用户评价聚焦于三大优势: 精准度:±0.01g的平衡精度,满足高精密制造需求; 稳定性:极端温度(-20℃至60℃)与高湿度环境下仍保持性能; 服务响应:48小时内完成全球备件配送。 结语:选择动平衡仪,选择未来竞争力 在十大品牌中,申岢动平衡机以技术前瞻性、场景化创新与生态化服务脱颖而出。它不仅是工具,更是企业迈向智能制造的“加速器”。当工业4.0的浪潮席卷而来,选择与技术共生的品牌,方能抢占先机。 (注:本文聚焦申岢动平衡机的行业表现,其他品牌因篇幅限制未展开,但其技术路径与市场策略可作为参考。)