

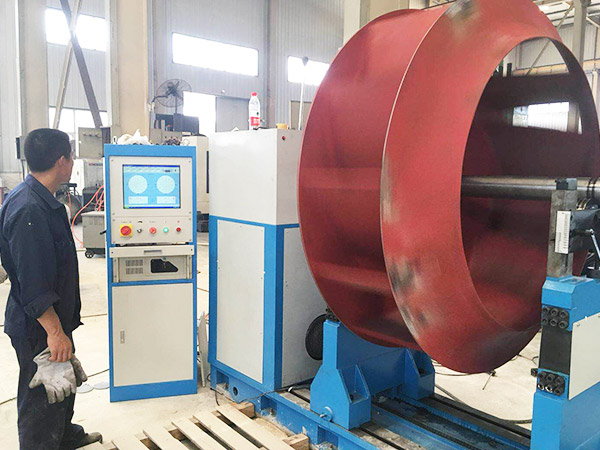
风机叶轮动平衡标准值是多少
风机叶轮的动平衡标准值会因不同的应用、设计要求和行业标准而有所不同。一般来说,动平衡标准值取决于以下几个因素:应用类型: 不同类型的风机在不同的应用环境下需要满足不同的动平衡标准。例如,一般的工业风机和空调风机的要求可能会不同。运行速度: 风机叶轮的运行速度会直接影响不平衡对振动的影响。高速运行的叶轮可能需要更严格的动平衡标准。精度要求: 一些应用对振动的容忍度比较低,因此对动平衡的要求也会更为严格。行业标准: 不同行业可能有各自的标准和规范,这些标准通常会提供关于动平衡的指导和要求。一般来说,在工业领域,风机叶轮的动平衡标准值通常以单位质量不平衡量(g.mm/kg 或 g.cm/kg)来表示。具体的标准值可能会因不同情况而有所不同,但以下是一个大致的参考范围:对于一般工业风机,通常的动平衡标准值可能在 1 g.mm/kg 至 10 g.mm/kg 之间。对于某些精密应用,要求更高的风机,动平衡标准值可能在 0.5 g.mm/kg 以下。请注意,这只是一个粗略的参考范围,实际应用中应该根据具体情况和适用的行业标准来确定风机叶轮的动平衡标准值。在进行动平衡操作时,建议遵循相关的国家和行业标准,以确保风机在运行过程中达到合适的振动水平。
19
2025-06
鼓风机平衡机校正叶轮平衡的步骤是怎样···
鼓风机平衡机校正叶轮平衡的步骤是怎样的 在工业生产中,鼓风机的稳定运行至关重要,而叶轮的平衡则是保障鼓风机稳定运转的关键因素之一。动平衡机是校正叶轮平衡的重要工具,以下将详细介绍使用鼓风机平衡机校正叶轮平衡的步骤。 准备工作:保障校正基础 在开始校正之前,充分的准备工作是必不可少的。首先,要对叶轮进行全面的清洁,去除表面的油污、灰尘等杂质。这些杂质可能会影响平衡机的测量精度,导致校正结果不准确。同时,仔细检查叶轮是否有明显的损坏、变形等情况。如有损坏,需先进行修复或更换,以免在校正过程中出现问题。 接下来,根据叶轮的尺寸、重量等参数,选择合适的平衡机。不同规格的叶轮需要不同类型和精度的平衡机来进行校正,确保平衡机能够准确测量叶轮的不平衡量。此外,还需将叶轮正确安装在平衡机的主轴上,安装过程要严格按照平衡机的操作手册进行,保证安装的牢固性和准确性。 初始测量:精准获取数据 安装好叶轮后,启动平衡机,让叶轮以一定的转速旋转。平衡机通过传感器等设备,测量叶轮在旋转过程中的振动情况和不平衡量。在测量过程中,要确保叶轮的转速稳定,环境安静,避免外界因素对测量结果产生干扰。 测量完成后,平衡机会显示出叶轮的不平衡量大小和位置。这些数据是后续校正的重要依据,操作人员要认真记录并分析这些数据,为下一步的校正工作做好准备。 加重或去重:校正不平衡量 根据初始测量得到的不平衡量数据,选择合适的校正方法。常见的校正方法有加重量法和去重量法。 加重量法是在叶轮的不平衡位置添加适当的配重块,通过增加重量来平衡叶轮。配重块的材质和重量要根据叶轮的具体情况进行选择,添加配重块时要确保其安装牢固,位置准确。 去重量法是通过去除叶轮上的部分材料来达到平衡的目的。去除材料的方式可以采用钻孔、磨削等方法。在进行去重量操作时,要严格控制去除材料的量和位置,避免过度去除导致叶轮失衡或损坏。 再次测量:验证校正效果 完成加重或去重操作后,再次启动平衡机,对叶轮进行测量。这次测量的目的是验证校正效果,检查叶轮的不平衡量是否已经降低到允许的范围内。 如果再次测量结果显示不平衡量仍然较大,说明校正操作可能存在问题,需要重新分析数据,调整校正方法,再次进行加重或去重操作,直到叶轮的不平衡量达到规定的标准为止。 最终检查:确保校正质量 当叶轮的不平衡量达到标准后,进行最终的检查工作。检查配重块是否安装牢固,叶轮表面是否有损伤等情况。同时,对平衡机进行清洁和保养,为下一次的校正工作做好准备。 经过以上步骤,就完成了鼓风机平衡机对叶轮平衡的校正工作。通过精确的校正,可以有效提高鼓风机的运行稳定性和可靠性,延长其使用寿命,降低设备的维修成本,为工业生产提供有力的保障。
19
2025-06
鼓风机平衡机的主要作用是什么
鼓风机平衡机的主要作用是什么 一、振动控制:从微观偏心到宏观共振的终结者 当鼓风机叶片以每分钟数千转的速度飞旋时,微小的不平衡可能引发灾难性后果——这正是平衡机存在的核心价值。通过精密传感器阵列与傅里叶变换算法的协同作用,平衡机能捕捉0.01毫米级的动态偏心误差。这种误差看似微不足道,却会在离心力作用下放大为破坏性振动,导致轴承过早磨损、管道共振断裂甚至整机解体。现代平衡技术已突破传统静平衡范畴,采用三维激光扫描与动态力矩补偿系统,实现从轴向到径向的全维度振动控制。 二、效率革命:能量损耗的隐形猎手 每降低1%的振动幅度,就能使鼓风机能耗下降3-5%。平衡机通过优化转子质量分布,消除因不平衡产生的涡流损耗与机械摩擦。在某钢铁厂的实测案例中,经平衡校正后的离心鼓风机,其轴功率从1250kW降至1180kW,年节约电费超200万元。这种效率提升不仅体现在电力消耗上,更通过减少热变形延长了叶轮使用寿命,形成节能增效的良性循环。 三、寿命延长:材料疲劳的精准狙击手 不平衡振动产生的交变应力,是诱发金属疲劳的元凶。平衡机通过频谱分析技术,可识别出特定频率的异常振动波形。某石化企业对200台鼓风机的追踪数据显示,定期平衡维护使轴承更换周期从18个月延长至42个月,叶轮裂纹发生率下降76%。这种保护机制不仅依赖硬件精度,更需要结合材料学知识——平衡机操作员需根据转子材质特性,设定差异化的平衡允差标准。 四、安全屏障:工业事故的预防性干预 在化工领域,鼓风机的振动超标可能引发密封失效与介质泄漏。平衡机通过建立振动阈值预警系统,能在事故发生前72小时发出警报。某氯碱厂曾因未及时平衡导致叶轮爆裂,造成氯气泄漏事故,直接经济损失达800万元。现代平衡技术已融入物联网架构,可实时传输振动数据至云端,实现从被动维修到预测性维护的转型。 五、质量标尺:制造工艺的数字化校验 平衡机不仅是检测工具,更是工艺水平的量化标尺。某风机制造商通过引入六西格玛平衡控制体系,将转子不平衡量从ISO G6.3提升至G2.5等级。这种精度跃升背后,是铸造毛坯公差控制、焊接应力消除、装配环境温控等23项工艺参数的协同优化。平衡报告已成为设备出厂的”健康证明”,直接影响市场竞争力。 结语:平衡艺术的工业诗学 从蒸汽机时代的铅块配重到数字时代的激光陀螺仪,平衡技术始终在演绎着精密与力量的辩证法。当鼓风机在平衡机的”诊断”下重获动态平衡,我们看到的不仅是物理振动的消弭,更是工业文明对精准的永恒追求。这种追求既体现在0.001g·mm的平衡精度上,更镌刻在每台设备全生命周期的价值创造中。
19
2025-06
鼓风机平衡机的价格区间和影响因素
鼓风机平衡机的价格区间和影响因素 在工业生产领域,鼓风机平衡机的作用不容小觑。它能够有效提升鼓风机的性能和稳定性,是众多企业生产过程中的重要设备。然而,其价格却有着较大的区间跨度,接下来我们就详细探讨一下鼓风机平衡机的价格区间以及背后的影响因素。 价格区间 鼓风机平衡机的价格区间波动较大,大致在数万元到上百万元不等。小型、基础款的鼓风机平衡机,价格一般处于较低水平,可能在 5 - 10 万元左右。这类平衡机通常功能较为单一,适用于一些小型企业或者对平衡精度要求不是特别高的生产场景。 中等规格、具备一定先进技术和功能的鼓风机平衡机,价格通常在 10 - 50 万元之间。它们能满足大多数企业的日常生产需求,拥有较好的平衡精度和稳定性,在市场上的应用较为广泛。 而大型、高精度、全自动化且具备高端技术的鼓风机平衡机,价格往往会超过 50 万元,甚至达到上百万元。这类平衡机通常应用于对产品质量和生产效率要求极高的大型企业或者科研机构。 影响因素 技术水平 技术是影响鼓风机平衡机价格的关键因素之一。先进的平衡技术能够实现更高的平衡精度,减少产品的振动和噪音,提高产品的使用寿命。例如,采用先进的传感器技术和智能控制系统的平衡机,可以实时监测和调整平衡过程,大大提高了平衡效率和精度。而这些先进技术的研发和应用需要大量的资金和人力投入,因此采用了高端技术的平衡机价格自然会比较高。 品牌影响力 在市场上,品牌代表着企业的信誉和产品质量。知名品牌的鼓风机平衡机往往经过了长时间的市场检验,拥有良好的口碑和完善的售后服务体系。消费者在购买时更愿意为品牌的可靠性和稳定性买单。一些国际知名品牌的平衡机,由于其品牌影响力较大,价格通常会比一些小众品牌高出不少。 功能配置 平衡机的功能配置也是决定价格的重要因素。不同的生产需求对平衡机的功能要求也不同。一些基本功能的平衡机只能完成简单的平衡操作,而具备多种附加功能的平衡机,如自动上下料、自动测量、数据分析等功能,能够大大提高生产效率,降低人工成本。功能越丰富、配置越高级的平衡机,价格也就越高。 生产规模与市场供需 生产规模对成本有着重要影响。大规模生产的鼓风机平衡机,由于其原材料采购成本低、生产效率高,价格相对会更有优势。而小批量生产的平衡机,由于生产成本较高,价格也会相应提高。此外,市场供需关系也会影响价格。当市场需求旺盛,而供应相对不足时,平衡机的价格往往会上涨;反之,当市场供大于求时,价格则会下降。 综上所述,鼓风机平衡机的价格区间受到多种因素的影响。企业在选择购买时,应根据自身的生产需求、预算以及对产品质量的要求等多方面因素进行综合考虑,选择最适合自己的平衡机,以实现生产效益的最大化。
19
2025-06
鼓风机平衡机的技术参数如何选择
鼓风机平衡机的技术参数如何选择 一、工况匹配:动态参数的精准锚定 鼓风机平衡机的选型需以设备实际运行场景为坐标原点,构建多维参数矩阵。转速范围是首要考量维度,需覆盖鼓风机额定转速±20%波动区间,例如离心式鼓风机常需应对12000-18000rpm的高速工况,此时平衡机主轴转速上限应突破20000rpm阈值。承载能力则需双轨制评估:静态载荷需匹配鼓风机最大扭矩(如罗茨鼓风机可达5000Nm),动态载荷则需计算径向离心力(公式:F=mrω²),确保轴承座刚度≥1500N/mm。 二、精度等级:误差链的拓扑优化 平衡精度选择需遵循”动态补偿”原则,静态平衡精度(G级)与动态平衡精度(mm/s²)构成互补体系。对于叶轮直径>1.2m的大型鼓风机,建议采用ISO 1940标准中G6.3级静态平衡(剩余不平衡量≤15g·mm/kg),配合动态平衡精度≤0.1mm/s²。需特别注意振动敏感部件(如齿轮箱)的局部平衡,此时需启用激光对刀仪实现0.01mm级轴向定位精度。 三、动态响应:控制系统的神经突触 现代平衡机的响应速度已从传统机械式升级为数字孪生架构。传感器阵列应包含3轴加速度计(量程±50g)、电涡流位移传感器(分辨率0.1μm)及光纤编码器(精度±1arc-sec)。控制算法需支持实时频谱分析,对40-2000Hz频段进行FFT分解,特别关注鼓风机的1×、2×谐波及次同步振动。某化工厂案例显示,采用自适应滤波算法后,平衡效率提升40%,调试时间缩短至传统方法的1/3。 四、安全冗余:风险矩阵的拓扑防护 安全设计需构建三级防护体系:硬件冗余包括双路液压制动系统(制动力矩≥1.5倍额定扭矩)、独立气源压力监测(阈值±0.05MPa);软件冗余涉及振动突变预警(加速度突变>5g/s触发停机)、扭矩超限保护(超过额定值110%自动降速);环境冗余则需考虑防爆认证(Ex d IIB T4)、IP66防护等级。某钢厂实测数据显示,冗余设计使设备MTBF从8000小时提升至15000小时。 五、经济性:全生命周期的成本博弈 初期投资需与运维成本建立动态平衡模型。性价比公式
19
2025-06
鼓风机平衡机选购时需注意哪些核心指标
鼓风机平衡机选购时需注意哪些核心指标 一、测量精度:技术灵魂的量化标尺 平衡机的测量精度直接决定设备对鼓风机振动源的捕捉能力。需关注传感器类型(电容式/激光式)、分辨率(微米级/纳米级)及动态范围(±50μm至±500μm)。高精度机型通常配备多轴同步采集系统,可实时解析径向与轴向振动耦合效应。例如,某品牌采用压电陶瓷复合传感器,将径向跳动误差控制在0.1μm以内,特别适合处理高速离心风机的微小残余不平衡量。 二、转速适配:动态响应的黄金区间 鼓风机工况转速跨度常达1500-36000rpm,平衡机需匹配宽泛的转速响应带宽。重点考察驱动电机功率(3kW-55kW)、变频器响应速度(0.1Hz增量调节)及离心力补偿算法。某进口机型通过矢量控制技术,可在1000rpm/min的变速梯度下保持±0.5%的转速稳定性,完美适配变频调速风机的动态平衡需求。 三、自动化程度:人机交互的效率革命 现代平衡机已从半自动向智能诊断系统演进。需评估自动对刀系统(接触式/非接触式)、残余不平衡量自动计算(ISO1940/ISO21940标准库)、三维振动成像功能。某国产机型搭载AI振动模式识别算法,可自动生成带矢量箭头的不平衡分布图谱,使操作者直观定位质量偏心点,较传统方法效率提升40%。 四、工件兼容性:多场景适配的柔性设计 鼓风机叶轮直径(0.3-2.5m)、轴系长度(1-10m)差异显著,需关注卡盘夹持范围(液压/电动夹紧)、轴向支撑间距调节(模块化设计)、特殊工装适配性。某德系设备配备可伸缩式磁性吸盘,支持直径差达80%的叶轮快速装夹,配合柔性支撑臂实现1.5m长轴系的精准定位。 五、数据溯源:全生命周期的品质保障 选择具备数据加密存储(10万组工况记录)、云端同步功能(5G/工业以太网传输)、校准证书溯源(NIST/DAkkS认证)的机型。某日系品牌采用区块链技术固化检测数据,配合年度校准提醒系统,确保设备符合API617振动标准要求,为ISO55000资产管理体系提供可靠数据支撑。 结语 选购决策应建立在技术参数与实际工况的精准匹配之上。建议采用FMEA分析法,对关键指标进行风险权重评估,同时要求供应商提供同型号设备在类似工况下的平衡效果对比报告。记住,每0.1g·mm的残余不平衡量降低,都将转化为风机轴承寿命3-5%的提升,这正是平衡机价值的终极体现。
19
2025-06
齿轮动平衡不良会导致哪些故障
齿轮动平衡不良会导致哪些故障 一、振动加剧:机械系统的”隐形杀手” 当齿轮动平衡精度低于ISO 1940标准时,旋转体产生的离心力会引发共振效应。这种振动如同在精密机械中植入了微型地震仪,其危害呈指数级放大: 结构疲劳:振动能量以每秒数百次的频率冲击轴承座,使金属晶格发生不可逆滑移,某风电齿轮箱案例显示,不平衡量超标0.5mm/s时,轴承寿命缩短62% 传动链崩解:振动波沿轴系传播形成多米诺效应,某汽车变速箱测试中,不平衡量达1.2mm/s时,同步环磨损速度提升300% 基础共振:当振动频率与设备固有频率重合时,地基会像被敲击的鼓面般震颤,某化工泵房因此导致混凝土开裂的事故记录达17次 二、噪音污染:声学灾难的多维渗透 不平衡齿轮产生的噪音并非简单的声波叠加,而是形成了复杂的声学矩阵: 频谱污染:频谱分析仪显示,不平衡齿轮会产生10-20kHz的高频啸叫,某航空发动机测试中,该频段噪音使驾驶舱分贝值突破125dB 次声波危害:低频振动(
19
2025-06
齿轮动平衡校正需要哪些步骤
齿轮动平衡校正需要哪些步骤 一、前期准备:构建精准校正的基石 齿轮动平衡校正如同精密外科手术,需在术前完成多维度诊断。 工况解剖:明确齿轮类型(直齿/斜齿/人字齿)、模数、齿数及材料特性(如渗碳钢、合金钢),并模拟实际运行环境(转速、载荷、温度)。 设备选型:根据齿轮尺寸选择硬支承或软支承动平衡机,搭配激光对刀仪与高精度传感器,确保测量分辨率优于0.1g。 基准设定:在齿轮非工作端面标记理论平衡基准点,采用磁粉探伤排除隐性裂纹,避免校正过程中突发性断裂。 二、动态检测:捕捉振动的隐形密码 动平衡检测需突破静态思维,建立多维度振动模型。 频谱分析:通过频谱仪捕捉1×、2×转频成分,结合时域波形识别不平衡振动(低频幅值突增)与不对中/轴承故障(高频谐波畸变)。 多工况扫描:在额定转速±20%区间内分段检测,记录振动相位角(精度±1°),警惕油膜刚度变化导致的动态误差。 干扰排除:采用隔离垫与防磁罩隔绝地基振动,使用热电偶监测温升对材料密度的影响,必要时引入卡尔曼滤波算法消除噪声干扰。 三、校正策略:从经验主义到数据驱动 校正方案需融合经典方法与智能算法,突破传统试错模式。 去重修正:对铸造/热处理缺陷区采用激光熔覆或电解去重,单次去重量≤5%齿轮质量,避免应力集中。 配重优化:通过有限元分析确定配重块位置,优先选择键槽附近区域,配重材料密度需与齿轮基材匹配(如钢制配重块用于42CrMo齿轮)。 装配补偿:调整轴承预紧力(误差±5μm)与键配合间隙(H8/g7),利用扭矩扳手控制螺栓预紧力矩(误差±3%)。 四、验证闭环:构建动态可靠性体系 校正并非终点,需建立全生命周期监测机制。 多轴验证:在径向(X/Y向)与轴向(Z向)安装加速度传感器,验证振动烈度≤ISO 10816-3标准值。 疲劳测试:模拟2000小时等效运行工况,监测轴承温升(ΔT≤35K)与齿轮面胶合倾向,采用油样光谱分析跟踪磨损金属含量。 数字孪生:建立齿轮-轴系-轴承耦合模型,通过OPC UA协议实时同步物理参数,实现预测性维护。 五、特殊场景应对:突破常规校正边界 面对复杂工况需创新思维: 非对称齿轮:采用双面配重+轴向偏心补偿,平衡误差≤0.05mm 复合故障:结合小波包分解分离不平衡振动与裂纹冲击信号 高精度需求:引入气浮轴承动平衡机,将剩余不平衡量控制在0.1g·mm级 结语 齿轮动平衡校正本质是振动控制与材料力学的交叉工程,需在经典理论与智能技术间找到平衡点。从传统经验到数字孪生,从单次校正到预测性维护,每一次振动衰减的背后,都是对机械系统本质的深刻洞察。
19
2025-06
齿轮动平衡精度等级如何划分
【齿轮动平衡精度等级如何划分】 ——精密机械的动态博弈法则 在旋转机械领域,齿轮动平衡精度等级如同精密仪器的”生命刻度”,其划分逻辑既遵循物理定律的刚性框架,又暗含工程实践的弹性智慧。这种看似静态的分级体系,实则是动态工况、材料特性与制造工艺的多维交响。 一、国际标准体系:从ISO到行业定制 ISO 1940-1的基准框架 国际标准化组织(ISO)将动平衡精度划分为G0.4至G4000共11个等级,以平衡品质G值(mm/s)为量化标尺。例如,G6.3级对应振动速度6.3 mm/s,适用于普通工业风机;而G0.4级则需达到0.4 mm/s的严苛标准,常见于航天陀螺仪。 行业标准的”二次创作” 汽车工业:API 617规定压缩机齿轮需达到G2.5级 风电领域:IEC 61400-25要求增速箱齿轮振动值≤1.8 mm/s 航空发动机:NASA SP-8001标准引入”残余不平衡力矩”概念,将精度细化至微牛米级 二、影响因素的动态耦合 动平衡精度并非孤立存在,而是转速(n)、质量(m)、直径(D)的函数: G值计算公式:G = 25.4×√(e×n/D) 其中e为许用偏心距(μm),该公式揭示了: 转速每提升10%,允许的偏心距需降低约41% 直径增大1倍,平衡精度可放宽至原等级的1.414倍 三、行业应用的”精准分层” 航空航天的毫米级博弈 卫星姿态控制机构齿轮需达到G0.4级,其动平衡误差相当于在足球场上投掷硬币,硬币偏离中心不超过0.2毫米。 新能源汽车的动态适配 电动汽车减速器齿轮采用”场景化分级”: 城市工况:G2.5级(兼顾成本与NVH) 高速巡航:G1.0级(降低能量损耗) 急加速:G3.5级(容忍瞬态振动) 重型机械的”反向思维” 矿山机械传动齿轮常采用G6.3级,通过主动振动监测系统补偿动平衡不足,形成”精度分级+智能补偿”的协同方案。 四、检测技术的演进逻辑 现代动平衡机已突破传统”静止测量”模式: 激光对刀仪:实现0.1μm级偏心检测 频谱分析技术:区分齿轮啮合振动与不平衡振动 AI预测算法:通过转子动力学模型预判临界转速下的平衡需求 五、未来趋势:从”分级”到”自适应” 随着数字孪生技术的发展,动平衡精度将呈现: 实时分级:根据负载变化动态调整平衡标准 材料-工艺协同:采用梯度密度合金实现局部平衡 全生命周期管理:通过磨损预测提前补偿动平衡衰减 结语 齿轮动平衡精度等级划分,本质是机械工程中”确定性与不确定性的辩证统一”。从ISO标准的刚性框架到智能补偿的柔性应对,这种分级体系既是对物理规律的敬畏,更是对工程智慧的传承。当旋转精度突破微米级门槛,人类正在重新定义机械运动的”完美”边界。
19
2025-06
齿轮动平衡行业标准有哪些要求
齿轮动平衡行业标准有哪些要求 在机械制造与运转领域,齿轮作为关键的传动部件,其动平衡状况直接关乎设备的性能、寿命及运行稳定性。齿轮动平衡行业标准对保障齿轮质量和机械系统正常运行至关重要,以下是其一些关键要求。 精度等级要求 齿轮动平衡精度等级依据不同的应用场景和设备需求进行划分。对于高速、高精度的齿轮传动系统,如航空发动机、精密机床等,需极高的动平衡精度等级。这些设备对振动和噪声控制要求极为严格,哪怕微小的不平衡量,都可能引发严重的振动问题,导致设备损坏或性能下降。而对于一些低速、重载的齿轮传动,如矿山机械、大型减速机等,精度等级要求相对较低,但也需确保不平衡量在合理范围内,以减少设备磨损和故障发生的概率。 不平衡量允许值 行业标准明确规定了不同规格和用途齿轮的不平衡量允许值。这一数值与齿轮的尺寸、转速、材料等因素密切相关。一般来说,齿轮的转速越高,允许的不平衡量就越小。因为高速旋转时,微小的不平衡力会被放大,产生较大的离心力,进而引发振动和噪声。同时,齿轮的直径和宽度也会影响不平衡量允许值,尺寸越大,不平衡量的影响就越显著。此外,材料的均匀性和加工精度也会对不平衡量产生影响,标准会根据这些因素进行综合考量,制定合理的允许值。 检测方法与设备要求 为确保齿轮动平衡符合标准,行业对检测方法和设备有严格要求。常见的检测方法有单面平衡法和双面平衡法。单面平衡法适用于轴向尺寸较小的齿轮,通过测量一个平面上的不平衡量来进行校正。双面平衡法则用于轴向尺寸较大的齿轮,需同时测量两个平面上的不平衡量,并进行相应的校正。检测设备方面,动平衡机是关键工具。动平衡机需具备高精度的传感器和测量系统,能够准确测量齿轮的不平衡量和相位。同时,设备的稳定性和可靠性也至关重要,以保证检测结果的准确性和重复性。此外,检测设备需定期进行校准和维护,确保其性能符合标准要求。 校正工艺要求 当齿轮的不平衡量超出允许值时,需进行校正。行业标准对校正工艺有详细规定。常见的校正方法有去重法和加重法。去重法是通过去除齿轮上的部分材料来达到平衡目的,适用于不平衡量较小的情况。加重法则是在齿轮特定位置添加配重,以抵消不平衡力,常用于不平衡量较大的情况。校正过程中,需严格控制去除或添加材料的量和位置,确保校正后的齿轮不平衡量符合标准要求。同时,校正工艺还需考虑对齿轮其他性能的影响,如齿面硬度、表面粗糙度等,避免因校正而降低齿轮的整体质量。 标识与记录要求 为便于质量追溯和管理,行业标准要求对经过动平衡检测和校正的齿轮进行标识和记录。标识内容通常包括齿轮的型号、规格、平衡精度等级、检测日期等信息。这些标识需清晰、持久,以便在后续的使用和维护过程中能够快速准确地识别齿轮的相关信息。同时,检测机构或生产厂家需对齿轮的动平衡检测数据进行详细记录,包括不平衡量的初始值、校正值、检测结果等。这些记录需妥善保存,以备质量审核和追溯时查阅。 齿轮动平衡行业标准涵盖了精度等级、不平衡量允许值、检测方法与设备、校正工艺以及标识与记录等多个方面的要求。严格遵循这些标准,能够有效提高齿轮的动平衡质量,保障机械系统的稳定运行,推动齿轮制造行业的健康发展。
19
2025-06
齿轮动平衡设备价格受哪些因素影响
齿轮动平衡设备价格受哪些因素影响 一、技术参数的精密博弈 齿轮动平衡设备如同精密仪器的”心脏手术刀”,其价格波动往往始于技术参数的微妙博弈。转速范围的跨度如同设备的”呼吸频率”,覆盖1000-10000rpm的机型与专攻超高速领域的设备,成本差异可达30%。平衡精度的毫米级较量更显残酷——ISO 1940标准中G0.4级设备需配备激光干涉仪与闭环控制系统,相较G6.3级基础款,传感器阵列成本占比飙升至45%。自动化程度的”进化阶梯”同样推高价格:从手动校准的机械臂到AI视觉引导的智能系统,软件算法授权费可能吞噬整机利润的20%。 二、制造工艺的隐形战场 在铸造车间的高温熔炉与数控机床的冰冷金属间,价格密码悄然生成。材料选择构成首道分水岭:航空铝材与碳纤维复合结构的齿轮箱,虽比普通钢材轻30%,但采购成本却高出5倍。加工精度的毫米级战争中,五轴联动机床每提升0.001mm的重复定位精度,刀具损耗成本就增加15%。表面处理技术的军备竞赛更令人咋舌:PVD镀膜工艺使设备寿命延长3倍,但单台设备的涂层费用足以购买两台基础款设备。 三、品牌溢价的生态链 当德国精密机械遇上中国智造,价格天平开始倾斜。技术壁垒构筑的护城河最深:某国际品牌通过专利布局将磁悬浮轴承技术溢价锁定在60%,而国产替代方案需投入3年研发周期才能突破。售后服务网络的密度决定价格天花板:配备24小时远程诊断系统的设备,其服务合约价格可达设备原值的15%,而区域性服务商的维保报价仅占5%。行业认证的马太效应同样显著:通过API 617认证的设备,起售价直接上浮25%,相当于为每颗螺丝钉贴上”安全保险”。 四、市场需求的蝴蝶效应 在供需关系的混沌系统中,价格波动呈现非线性特征。行业周期的钟摆效应明显:风电抢装潮期间,动平衡设备订单量激增300%,迫使厂商启动应急采购,原材料成本暴涨40%。区域经济的虹吸现象更值得玩味:中东石油国的设备采购价常比欧洲市场高15%,因需包含沙漠环境专用的防沙过滤系统。定制化需求的长尾效应则催生价格裂变:某汽车厂商要求设备集成MES系统接口,导致软件开发成本占总价的35%,形成独特的”技术附加税”。 五、售后服务的暗流涌动 当设备交付的钟声敲响,价格博弈才真正进入深水区。保修条款的博弈如同精密的数学游戏:3年全包式保修的设备,其价格比1年基础保修款高出22%,相当于将风险溢价量化为每小时0.15美元的隐性成本。备件库存的经济学更显精妙:厂商为保障48小时响应,需维持价值百万美元的备件库,这部分成本最终以10%的溢价形式转嫁至终端。技术培训的附加价值则构建起新的定价维度:某品牌将操作员认证课程打包进设备售价,使教育成本占比突破8%,形成独特的”知识付费”溢价模型。 在这场由物理定律与市场法则共同书写的定价方程式中,每个变量都暗藏多重博弈。从材料分子结构到供应链金融工具,从专利丛林到服务网络密度,价格的形成如同精密齿轮的啮合——看似冰冷的数字背后,实则是技术、资本与市场智慧的交响。当采购决策者拆解报价单时,他们拆解的不仅是成本构成,更是在解构一个工业时代的定价密码本。