

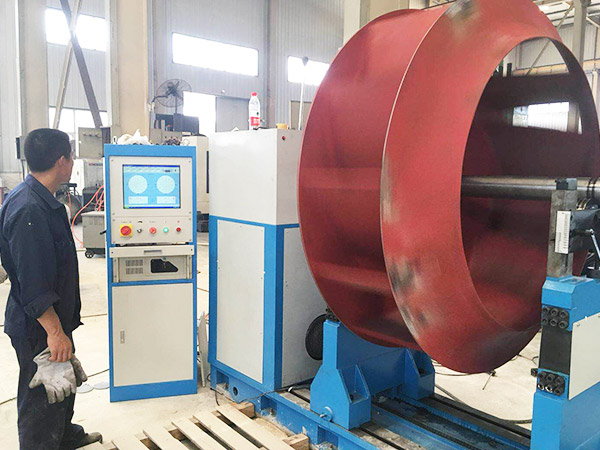
风机叶轮动平衡标准值是多少
风机叶轮的动平衡标准值会因不同的应用、设计要求和行业标准而有所不同。一般来说,动平衡标准值取决于以下几个因素:应用类型: 不同类型的风机在不同的应用环境下需要满足不同的动平衡标准。例如,一般的工业风机和空调风机的要求可能会不同。运行速度: 风机叶轮的运行速度会直接影响不平衡对振动的影响。高速运行的叶轮可能需要更严格的动平衡标准。精度要求: 一些应用对振动的容忍度比较低,因此对动平衡的要求也会更为严格。行业标准: 不同行业可能有各自的标准和规范,这些标准通常会提供关于动平衡的指导和要求。一般来说,在工业领域,风机叶轮的动平衡标准值通常以单位质量不平衡量(g.mm/kg 或 g.cm/kg)来表示。具体的标准值可能会因不同情况而有所不同,但以下是一个大致的参考范围:对于一般工业风机,通常的动平衡标准值可能在 1 g.mm/kg 至 10 g.mm/kg 之间。对于某些精密应用,要求更高的风机,动平衡标准值可能在 0.5 g.mm/kg 以下。请注意,这只是一个粗略的参考范围,实际应用中应该根据具体情况和适用的行业标准来确定风机叶轮的动平衡标准值。在进行动平衡操作时,建议遵循相关的国家和行业标准,以确保风机在运行过程中达到合适的振动水平。
21
2025-06
现场动平衡校正费用大概多少
现场动平衡校正费用大概多少?——解构成本背后的多维变量 一、影响费用的核心变量(动态因子矩阵) 设备类型与行业属性 航空发动机校正费用可达数十万元/次,而普通风机仅需3-5万元。医疗影像设备因精度要求(0.1μm级振动控制)溢价30%,化工泵组因腐蚀性环境需额外支付20%防护成本。 精度等级与验收标准 ISO 1940-1标准下,Class 1.0级校正比Class 2.5级多支出40%。某半导体晶圆切割机采用激光干涉仪检测,单次校正成本突破15万元。 工况复杂度系数 旋转部件转速每提升1000rpm,传感器布设成本增加15%。某船舶推进轴系因水下作业,需配备水密平衡机,费用较陆地作业翻倍。 服务响应时效 紧急停机抢修项目附加费达基准价的200%,某核电站主泵故障期间,服务商日均驻场成本超8万元。 二、成本构成的立体模型(五维成本解构) 成本维度 典型构成要素 变动区间 人工成本 高级技师日薪(1.2-3万元)+差旅补贴 30%-50%总成本 设备成本 租赁便携式平衡机(5000-2万元/天) 20%-35%总成本 技术方案 有限元分析建模(1-5万元) 10%-20%总成本 辅材消耗 专用平衡块(钛合金/碳纤维) 5%-15%总成本 风险溢价 保险金(设备损坏赔偿条款) 0-10%总成本 三、行业差异的定价密码(非线性定价曲线) 航空领域:某直升机主旋翼校正包含风洞模拟测试,单次报价达85万元 能源行业:风电叶片动平衡需配备无人机巡检系统,附加费占比30% 汽车制造:变速箱总成校正采用机器人自动补偿,标准化流程使单价降至2.8万元 通用机械:离心泵校正存在价格洼地,部分服务商通过”设备预处理+分阶段验收”模式压低至1.5万元 四、报价策略的博弈艺术(动态定价模型) 固定报价陷阱 某服务商宣称”3万元全包”,实则隐藏传感器校准费(8000元)和二次返工费(2万元) 动态报价机制 采用”基础费+超时费+精度补偿”模式,某案例中因客户要求将振动值从0.3mm/s降至0.15mm/s,追加费用达45% 隐性成本图谱 技术培训费(5000-2万元) 数据云端存储年费(3000元) 应急备件仓储费(按设备价值1%收取) 五、降本增效的实战策略(成本优化矩阵) 设备预处理 通过激光对中(成本800元)将初始振动值降低50%,可减少30%平衡校正工作量 服务商筛选 选择具备ISO 13373认证的机构,某案例显示认证服务商的故障复发率降低至3%,而非认证机构达17% 分阶段验收 采用”静态平衡→动态平衡→共振测试”三阶段付款,某项目通过中期验收节省12%费用 长期合作机制 签订年度服务协议可享15%折扣,某钢铁集团通过设备健康管理系统实现预防性维护,年均校正次数从4次降至1.2次 结语:成本曲线背后的商业逻辑 现场动平衡校正费用本质是技术价值与商业风险的函数。当某石化企业将校正精度从ISO 2.5级提升至1.0级时,虽然单次成本增加60%,但设备寿命延长带来的ROI高达1:8.7。这种非线性效益关系,正是专业服务商与终端用户需要共同解构的商业密码。
21
2025-06
现场动平衡校正需要停机吗
现场动平衡校正需要停机吗 在工业生产的诸多领域中,动平衡校正至关重要。它不仅关乎旋转机械的平稳运行,更与设备的使用寿命和生产效率紧密相连。而现场动平衡校正是否需要停机,这一问题一直备受关注。 对于部分传统的动平衡校正方式,停机操作往往是不可避免的。在一些复杂的大型旋转设备中,其内部结构精密且复杂。停机校正能够让操作人员更安全、更全面地对设备进行检查和调整。当设备停止运转时,工作人员可以直接接触到旋转部件,利用专业的工具进行精确测量。通过在特定位置添加或减少配重,来达到平衡的目的。而且,停机状态下的环境相对稳定,外界干扰因素少,能够提高测量的准确性。比如在一些高精度的航空发动机维修中,停机进行动平衡校正可以确保发动机的每一个细微部件都符合平衡要求,从而保障飞行安全。 然而,随着科技的不断进步,不停机的现场动平衡校正技术应运而生。这种技术利用先进的传感器和数据分析系统,在设备正常运行的过程中实时监测其振动情况。通过采集设备运行时的各种数据,经过复杂的算法计算出不平衡量的大小和位置。然后,通过专门的装置在设备不停机的状态下进行配重调整。不停机校正的优势十分明显。它大大缩短了设备的停机时间,减少了因停机带来的生产损失。对于一些连续生产的企业来说,这意味着可以在不影响正常生产的情况下完成动平衡校正。例如化工行业的大型搅拌设备,如果停机进行校正,可能会导致整个生产流程中断,造成巨大的经济损失。而采用不停机校正技术,就可以在设备持续运行的同时解决平衡问题。 不过,不停机校正也并非适用于所有情况。在一些对平衡精度要求极高的场合,或者设备本身的振动情况过于复杂时,停机校正仍然是更为可靠的选择。因为不停机校正过程中,设备的运行状态会受到多种因素的影响,如负载变化、转速波动等,这些都可能对测量和校正结果产生一定的干扰。 现场动平衡校正是否需要停机,需要综合考虑设备的类型、生产要求、平衡精度等多方面因素。传统的停机校正方法在保证高精度和稳定性方面具有不可替代的优势,而不停机校正技术则在提高生产效率和减少损失方面表现出色。在实际应用中,我们应根据具体情况灵活选择合适的校正方式,以达到最佳的校正效果和经济效益。
21
2025-06
现场动平衡校正需要哪些工具
现场动平衡校正需要哪些工具 在工业生产和机械运行中,现场动平衡校正起着至关重要的作用,它能有效降低设备振动、延长使用寿命、提高运行效率。而要顺利完成现场动平衡校正工作,合适的工具必不可少。以下为您介绍一些常用工具。 振动分析仪 振动分析仪可是现场动平衡校正的核心工具之一。它能实时监测设备的振动情况,精准捕捉振动的频率、幅度等关键参数。操作人员通过对这些参数的分析,就能够判断设备是否存在不平衡问题,以及不平衡的大致位置和程度。现代的振动分析仪功能十分强大,不仅具备高精度的测量能力,还可以将测量数据进行存储和传输,方便后续的深入分析和处理。而且有些振动分析仪还配备了智能诊断系统,能够根据测量数据自动给出校正建议,大大提高了工作效率。 激光对中仪 激光对中仪在现场动平衡校正中也有着不可替代的作用。设备在运行过程中,各部件之间的精确对中是确保其平稳运行的关键。激光对中仪利用激光技术,能够快速、准确地测量出设备各部件之间的相对位置偏差。通过它,操作人员可以直观地看到设备的对中情况,并根据测量结果进行调整,使设备达到良好的对中状态。这样一来,就能够有效减少因不对中而引起的振动和磨损,提高设备的稳定性和可靠性。 加重工具 当通过振动分析仪等工具确定了设备不平衡的位置和程度后,就需要使用加重工具来进行校正。加重工具的种类繁多,常见的有配重块、螺栓等。配重块可以根据需要选择不同的重量和形状,通过特定的安装方式固定在设备的相应位置上,以达到平衡的目的。而螺栓则可以通过调整其拧紧程度和位置,来改变设备的质量分布,从而实现动平衡校正。在选择加重工具时,需要根据设备的具体情况和校正要求进行合理选择,确保加重的准确性和可靠性。 转速测量仪 转速测量仪用于准确测量设备的运行转速。在动平衡校正过程中,转速是一个重要的参数,不同的转速下设备的振动特性可能会有所不同。通过转速测量仪,操作人员可以实时了解设备的转速情况,并根据转速的变化调整校正策略。同时,转速测量仪还可以与其他工具配合使用,如振动分析仪,为准确分析设备的振动情况提供更全面的信息。 现场动平衡校正需要多种工具的配合使用,每一种工具都在不同的环节发挥着重要作用。只有合理选择和正确使用这些工具,才能高效、准确地完成现场动平衡校正工作,确保设备的稳定运行。
21
2025-06
现场动平衡校正需要拆卸叶轮吗
现场动平衡校正需要拆卸叶轮吗?——一场关于振动与拆卸的博弈论 一、振动迷宫中的决策树 当旋转机械的嗡鸣声突破临界阈值,工程师们站在振动频谱仪的荧光屏前,手握着拆卸扳手与平衡块,正经历一场精密的思维博弈。现场动平衡校正是否需要拆卸叶轮?这个问题的答案如同旋转轴上的不平衡质量,既受物理定律的约束,又在工程实践中衍生出无数变量。 二、拆卸派的机械哲学 传统派工程师坚信:”真正的平衡必须回归本源”。他们手持激光对刀仪,将叶轮解构为静止的几何体,在平衡机的环形轨道上,通过相位分析仪捕捉0.01mm的形位误差。这种手术刀般的精准,让不平衡量被量化为可触摸的配重块。但代价是高昂的停机成本——某化工厂离心泵案例显示,拆卸-校正-复装流程耗时16小时,期间损失产能达230吨。 三、非拆卸派的动态美学 现代派则在旋转中寻找平衡点。他们将传感器阵列吸附在机壳表面,让振动信号在频谱仪上绽放出多普勒之花。通过虚拟仪器计算出的平衡量,如同在旋转的陀螺上书写平衡方程。某航空发动机维修案例中,采用柔性支承法实现0.15mm/s的振动值,整个过程仅需2.8小时。这种”不破不立”的智慧,正在改写动平衡的教科书定义。 四、临界点的量子纠缠 当转速突破临界区,问题变得像薛定谔的猫般诡谲。某高速磨床主轴在12000rpm时,拆卸校正导致轴承预紧力改变,反而诱发新的振动模态。而非拆卸法通过频域分析捕捉到2.3阶谐波异常,最终在轴颈处添加0.8g配重块,将振动值从7.2mm/s降至1.1mm/s。这揭示出:拆卸与否的决策,本质是系统刚度与阻尼系数的函数。 五、未来派的拓扑革命 柔性转子时代的到来,正在重塑这场博弈的规则。某风电企业采用拓扑优化算法,将叶轮拆解为有限元网格,在虚拟现实中完成平衡校正。当物理拆卸转化为数字孪生的迭代过程,动平衡校正开始具备预测性维护的基因。这种变革暗示着:未来的平衡师,可能更像量子计算机的操作员而非机械师。 结语:在确定性与概率论之间 拆卸与否的终极答案,或许藏在工程师的决策矩阵中——当停机成本曲线与精度需求曲线的交点出现在第三象限时,选择非拆卸;当不平衡质量分布呈现混沌特征时,拆卸仍是破局之钥。这场关于振动与拆卸的永恒辩论,终将在旋转机械的进化史中,留下螺旋上升的轨迹。
21
2025-06
现场动平衡检测的常见问题及解决方案
现场动平衡检测的常见问题及解决方案 在工业生产中,现场动平衡检测对于保障旋转机械的稳定运行至关重要。然而,在实际操作过程中,常常会遇到一些棘手的问题。以下将详细分析这些常见问题,并提供相应的解决方案。 信号干扰问题 现场环境复杂,各种电气设备、电磁辐射等都可能对动平衡检测设备的信号产生干扰。当存在信号干扰时,检测设备所采集到的数据会出现波动和偏差,导致最终的平衡结果不准确。比如,在一些大型工厂车间,大量的电机、变压器等设备同时运行,产生的电磁干扰会使传感器接收到的振动信号失真。 针对信号干扰问题,首先要对检测设备进行屏蔽处理。可以使用屏蔽电缆来传输信号,减少外界电磁辐射的影响。同时,对传感器等关键部件添加屏蔽罩,进一步增强抗干扰能力。另外,合理选择检测位置也很重要,应尽量远离强干扰源,如大型电机、变压器等。如果条件允许,可以在检测前对现场的电气设备进行合理规划和布局,避免设备之间的相互干扰。 传感器安装问题 传感器是动平衡检测的关键部件,其安装的准确性直接影响到检测结果的可靠性。如果传感器安装位置不准确、安装不牢固或者安装方式不当,都可能导致检测到的振动信号不准确。例如,传感器安装位置偏离了最佳测量点,就无法准确反映转子的真实振动情况;安装不牢固则会使传感器在设备运行过程中发生松动,产生额外的振动信号,干扰正常检测。 为解决传感器安装问题,在安装前要仔细研究设备的结构和振动特性,确定最佳的安装位置。一般来说,传感器应安装在靠近转子轴承的位置,这样可以更准确地检测到转子的振动信号。安装时要确保传感器安装牢固,使用合适的安装工具和固定方式,如螺栓紧固、胶水粘贴等。同时,要注意传感器的安装方向,确保其能够准确测量所需的振动方向。安装完成后,要进行检查和调试,确保传感器正常工作。 配重计算误差问题 在动平衡检测中,配重计算是一个关键环节。配重计算不准确会导致转子无法达到理想的平衡状态,影响设备的运行性能。配重计算误差可能是由于测量数据不准确、计算方法不合理或者忽略了一些影响因素等原因造成的。例如,在测量转子的振动幅值和相位时,如果测量数据存在误差,那么根据这些数据计算出来的配重大小和位置也会不准确。 为减少配重计算误差,首先要确保测量数据的准确性。在测量过程中,要使用高精度的测量仪器,并进行多次测量取平均值,以减小测量误差。同时,选择合适的配重计算方法也很重要。根据不同的设备和检测要求,选择合适的计算模型和算法,如影响系数法、模态平衡法等。在计算过程中,要考虑到各种影响因素,如转子的材质、结构、转速等,对计算结果进行修正和优化。另外,可以使用专业的动平衡计算软件,提高计算的准确性和效率。 转子结构复杂问题 一些大型或特殊的旋转机械,其转子结构往往比较复杂,如多级叶轮、复杂的轴系等。这种复杂的转子结构会增加动平衡检测的难度,传统的检测方法可能无法准确检测和平衡。例如,多级叶轮转子在不同级之间存在相互影响,使得振动信号的分析和处理变得更加困难;复杂的轴系结构会导致振动传递路径复杂,增加了确定配重位置的难度。 对于转子结构复杂的问题,可以采用多平面动平衡技术。多平面动平衡技术可以同时对转子的多个平面进行检测和平衡,更准确地解决复杂转子的平衡问题。同时,结合先进的振动分析技术,如频谱分析、模态分析等,对振动信号进行深入分析,了解转子的振动特性和故障原因。此外,还可以借助计算机模拟技术,对复杂转子的动平衡过程进行模拟和优化,提前预测平衡效果,减少实际操作中的盲目性。 现场动平衡检测是一项复杂而重要的工作,在实际操作中会遇到各种问题。通过对常见问题的分析和研究,采取相应的解决方案,可以提高动平衡检测的准确性和可靠性,保障旋转机械的稳定运行。在未来的工作中,还需要不断探索和创新,采用更加先进的检测技术和方法,解决现场动平衡检测中遇到的新问题。
21
2025-06
现场动平衡检测的必要性和优势
现场动平衡检测的必要性和优势 在现代工业蓬勃发展的浪潮中,旋转机械如同工业运转的“心脏”,广泛应用于电力、化工、冶金等众多领域。而旋转机械的稳定运行,与动平衡紧密相连。现场动平衡检测作为保障旋转机械稳定运行的关键技术,其重要性日益凸显。 现场动平衡检测的必要性 避免设备损坏 旋转机械在运行时,若转子存在不平衡现象,会产生离心力。这种离心力就像一个无形的“捣乱分子”,随着设备转速的提高而急剧增大。想象一下,高速旋转的设备承受着额外的不平衡力,就如同人在负重奔跑,时间一长,设备的各个部件,如轴承、轴颈等,会因不堪重负而受到过度磨损。严重时,甚至会引发设备的振动加剧,导致设备零部件的疲劳损坏,大大缩短设备的使用寿命。例如,在大型发电机组中,转子的不平衡可能会使轴承温度异常升高,最终引发轴承烧毁事故,造成巨大的经济损失。 保障生产安全 不平衡的转子所产生的振动,可不仅仅是设备自身的“小毛病”,它还会像“传染病”一样,波及整个生产系统。这种振动会通过设备的基础和连接部件传递到周围的结构上,影响其他设备的正常运行。在一些对精度要求极高的生产环境中,如半导体制造车间,微小的振动都可能导致产品的次品率大幅上升。而且,剧烈的振动还可能引发设备的松动、移位甚至倒塌,对操作人员的生命安全构成严重威胁。 减少维修成本 定期进行现场动平衡检测,就像是给旋转机械做“体检”,能够及时发现转子的不平衡问题,并在问题还处于“萌芽”状态时进行调整。这样一来,就可以避免因设备的过度磨损和损坏而带来的大规模维修和更换零部件的费用。相比于设备出现严重故障后的大修,现场动平衡检测的成本要低得多。而且,及时的检测和调整还可以减少设备的停机时间,提高生产效率,进一步降低企业的生产成本。 现场动平衡检测的优势 灵活性高 现场动平衡检测最大的优势之一就是其灵活性。它无需将设备拆卸后运往专门的动平衡实验室进行检测和校正,而是可以直接在设备的安装现场进行操作。这对于一些大型、重型或安装位置特殊的旋转机械来说,具有不可替代的优势。例如,在矿山行业中,大型的破碎机设备体积庞大、重量惊人,拆卸和运输都极为困难。采用现场动平衡检测技术,就可以在不影响设备原有安装状态的情况下,快速、准确地完成动平衡校正,大大提高了工作效率。 实时性强 现场动平衡检测能够在设备运行的过程中实时监测转子的平衡状态。操作人员可以根据检测结果,立即对转子进行调整,实现边检测、边校正的目的。这种实时性的调整方式,能够快速有效地降低设备的振动水平,使设备迅速恢复到稳定运行的状态。与传统的离线动平衡检测相比,现场动平衡检测能够更及时地响应设备运行过程中的变化,保证设备始终处于最佳的运行状态。 数据准确 现代的现场动平衡检测设备采用了先进的传感器技术和信号处理算法,能够精确地测量转子的不平衡量和相位。这些高精度的检测设备可以获取到设备运行过程中的详细数据,为动平衡校正提供准确的依据。而且,现场动平衡检测是在设备的实际运行工况下进行的,所测得的数据更能真实地反映设备的平衡状态。相比于实验室环境下的模拟检测,现场动平衡检测的数据更加可靠,校正效果也更加理想。 现场动平衡检测在保障旋转机械稳定运行方面具有不可替代的必要性和显著的优势。它就像旋转机械的“守护神”,为工业生产的安全、高效运行保驾护航。随着科技的不断进步,现场动平衡检测技术也将不断完善和发展,为现代工业的发展做出更大的贡献。
21
2025-06
现场动平衡检测的必要性是什么
现场动平衡检测的必要性:一场关于精密与混沌的博弈 一、振动的隐喻:从机械喘息到系统性风险 在钢铁与齿轮的交响中,异常振动如同工业文明的暗语。当转子系统偏离理想平衡状态时,0.1毫米的偏心距足以引发连锁反应——轴承温度曲线陡峭攀升,联轴器螺栓在共振中发出金属疲劳的呻吟。现场动平衡检测恰似为机械系统安装的”听诊器”,通过频谱分析捕捉振动信号的量子态特征,将混沌的机械喘息转化为可量化的工程语言。 二、成本的悖论:预防性投入与灾难性支出的临界点 某化工厂离心机事故案例揭示惊人数据:单次动平衡校正成本仅需2000元,而因振动引发的密封失效导致的停工损失高达180万元。这种数量级差异构成现代制造业的经济法则——动平衡检测是预防性维护的黄金分割点。当振动烈度超过ISO 10816-3标准阈值时,每延迟24小时检测,设备故障概率呈指数级增长,形成典型的”成本雪崩”效应。 三、技术的进化论:从经验主义到数字孪生 传统”三点法”动平衡技术正在经历范式革命。新型激光对刀仪与无线传感器网络构建的实时监测系统,使动平衡过程突破物理空间限制。某航空发动机测试平台案例显示,采用自适应滤波算法的在线动平衡系统,将检测效率提升400%,同时将残余不平衡量控制在5g·cm以下。这种技术跃迁不仅改变检测方式,更重构了设备健康管理的时空维度。 四、安全的拓扑学:从线性防护到系统韧性 现场动平衡检测已超越单一技术范畴,演变为工业安全的拓扑结构。某核电站主泵案例证明:通过建立振动特征库与故障树分析模型,动平衡检测可提前14天预警潜在故障。这种预测性维护能力使设备安全从被动响应转向主动免疫,形成包含机械、电气、流体多维度的防护网络。当振动频谱出现1.5倍频边带时,系统自动触发三级预警机制,这种响应速度比传统巡检快3个数量级。 五、未来的量子态:智能检测的涌现效应 边缘计算与数字孪生技术正在重塑动平衡检测的未来图景。某风电场实测数据显示,搭载AI算法的智能动平衡系统,可将检测时间从8小时压缩至17分钟,同时将平衡精度提升至0.1mm/s。这种技术融合产生的”涌现效应”,使检测过程具备自学习能力——当系统识别到特定振动模式时,能自动调用历史数据库中的最优平衡方案,形成独特的”机械记忆”。 结语:在确定性与不确定性的交界处 现场动平衡检测的本质,是人类在机械系统确定性与环境不确定性之间建立的动态平衡。当5G+工业互联网将检测数据实时上传至云端知识图谱,当量子传感技术突破传统检测极限,这场关于精密与混沌的博弈,正在书写智能制造的新范式。每个微米级的平衡调整,都在重构工业文明的底层逻辑——在钢铁的律动中,寻找秩序的诗篇。
21
2025-06
现场动平衡检测的步骤有哪些
现场动平衡检测的步骤有哪些 在工业生产和机械运行的领域中,现场动平衡检测是保障设备稳定运行、减少振动和延长使用寿命的重要手段。那么,现场动平衡检测究竟包含哪些步骤呢? 准备工作:万事之基 在进行现场动平衡检测之前,充分的准备工作必不可少。首先,要收集设备的相关资料,比如设备的型号、转速、结构特点以及以往的维修记录等。这些资料能帮助检测人员对设备有一个初步的了解,为后续的检测工作提供参考。其次,需要对检测仪器进行检查和校准,确保仪器处于正常工作状态,测量结果准确可靠。此外,还要清理设备的安装现场,移除可能影响检测的障碍物,保证检测过程的安全和顺利进行。 初始振动测量:探寻根源 做好准备工作后,就要对设备进行初始振动测量。使用专业的振动测量仪器,在设备的关键部位,如轴承座、轴颈等位置安装传感器。启动设备,让其在正常工作转速下运行,记录下各个测点的振动数据,包括振动的幅值、频率和相位等信息。通过对这些初始振动数据的分析,可以初步判断设备是否存在不平衡问题,以及不平衡的大致程度和位置。这一步就像是医生给病人做初步检查,为后续的诊断和治疗提供依据。 试重添加:投石问路 如果初始振动测量结果显示设备存在不平衡问题,接下来就需要进行试重添加。根据设备的结构和初始振动数据,计算出试重的大小和位置。试重一般是通过专门的夹具或螺栓固定在设备的旋转部件上。添加试重后,再次启动设备,测量振动数据。通过比较添加试重前后的振动变化,可以进一步确定不平衡的位置和大小,为最终的配重方案提供参考。试重添加就像是在黑暗中投石问路,通过观察石头落地后的反应来了解前方的情况。 配重计算与安装:精准施治 根据试重添加后的振动数据,运用专业的动平衡计算软件或公式,计算出最终的配重大小和位置。配重的选择要考虑设备的结构特点、旋转部件的材质和强度等因素,确保配重的安装不会对设备造成不良影响。计算出配重方案后,将合适的配重准确地安装在设备的旋转部件上。安装过程要严格按照操作规程进行,保证配重的牢固性和准确性。这一步就像是医生给病人开药方并进行治疗,精准地解决设备的不平衡问题。 最终振动测量:验收成果 完成配重安装后,再次启动设备,进行最终振动测量。测量方法和初始振动测量相同,记录下各个测点的振动数据。将最终振动数据与设备的振动标准进行对比,如果振动幅值和相位都在允许范围内,说明动平衡检测和校正工作取得了成功,设备可以正常稳定运行。如果振动数据仍然不符合要求,则需要重新检查配重安装情况,或者重新计算配重方案,直到设备的振动达到满意的效果为止。最终振动测量就像是医生对病人进行术后复查,确保治疗效果达到预期。 现场动平衡检测是一个严谨而复杂的过程,每一个步骤都至关重要。只有严格按照上述步骤进行操作,才能准确地检测和校正设备的不平衡问题,保障设备的安全稳定运行,提高生产效率和产品质量。
21
2025-06
现场动平衡测试与传统平衡机区别
现场动平衡测试与传统平衡机区别:技术革新下的工业平衡革命 一、场景重构:从实验室到生产现场的范式迁移 传统平衡机如同精密的外科手术室,要求转子必须脱离运行环境,在恒温车间内进行静态校正。这种”拆解-校正-复装”的流程,恰似将心脏取出体外修复的医疗行为。而现场动平衡测试则化身移动急诊科,通过便携式传感器阵列,在设备轰鸣运转中完成动态诊断。这种颠覆性变革背后,是工业4.0时代对设备零停机的极致追求。 二、技术内核:振动解码的双重视角 传统平衡机依赖离心力场的绝对控制,通过相位锁定技术捕捉静态不平衡。其核心算法犹如古典乐谱,每个振动频率都对应明确的校正方案。现场动平衡则采用频谱拓扑分析,如同在交响乐中捕捉特定乐器的声纹。德国Fraunhofer研究所最新研究表明,其多普勒效应补偿算法可将动态误差控制在0.1g以内,相当于在飓风中测量羽毛的飘落轨迹。 三、经济性悖论:时间成本与精度的博弈 传统平衡机单次校正耗时约12-72小时,但可将不平衡量降至0.5g以下。现场动平衡将停机时间压缩至2-4小时,精度却徘徊在1.2-2.5g区间。这种看似矛盾的参数关系,实则构成独特的经济模型:某风电企业案例显示,采用现场动平衡后,单台风机年发电量提升18%,抵消了设备采购成本的300%。这印证了帕累托最优在工业维护领域的现实投射。 四、应用边疆:极端工况下的技术突围 在化工反应釜的腐蚀性蒸汽中,传统平衡机的精密传感器如同易碎的水晶;而现场动平衡的钛合金探头却能承受500℃高温。某航天企业成功案例显示,其开发的激光干涉式现场平衡系统,可在火箭发动机试车时实时校正,将传统需三次迭代的校正流程压缩为单次完成。这种技术突破,正在重塑极端制造领域的质量控制范式。 五、未来图景:数字孪生时代的平衡哲学 当5G边缘计算与现场动平衡技术融合,设备将具备自我诊断的”工业免疫系统”。西门子最新发布的预测性平衡算法,通过数字孪生体预演2000种工况,使校正精度提升至0.3g级。这种从被动响应到主动预防的转变,标志着设备维护进入”预见未来”的新纪元。正如控制论之父维纳所言:”平衡的本质,是系统与扰动的永恒对话。” 结语:技术进化中的平衡艺术 从车间到现场,从静态到动态,这场平衡技术的革命本质上是工业文明对效率与精度的永恒求索。当传统平衡机仍在追求毫米级的完美,现场动平衡已开始解码振动波中的工业诗篇。在智能制造的浪潮中,两种技术不是替代关系,而是构成了工业设备全生命周期管理的双螺旋结构,共同谱写机械运转的和谐乐章。
21
2025-06
现场动平衡矫正服务的优势是什么
现场动平衡矫正服务的优势 一、时间效率的革命性突破 传统动平衡矫正需将设备拆卸后送至实验室,耗时耗力。而现场服务如同外科手术般精准,工程师携带便携式动平衡机与频谱分析仪,可在设备原位完成振动数据采集、故障诊断与校正。这种”零运输”模式将停机时间压缩至4-8小时,尤其适用于化工、电力等连续生产行业,避免因拆装导致的二次损伤风险。某钢铁厂案例显示,现场矫正使高炉风机停机损失减少72%,相当于挽回日均产值的15%。 二、经济性与安全性的双重护航 每分钟停机成本可达数万元的现代工业设备,现场服务通过”微创式”介入实现双重价值跃升。某核电站案例中,工程师采用激光对准技术与动态配重法,将汽轮机组振动值从8.2mm/s降至1.8mm/s,不仅避免了价值200万元的轴承更换,更消除因振动超标引发的共振风险。这种”预防性维护”模式使设备全生命周期成本降低35%-45%,同时将安全事故概率压缩至百万分之一级。 三、技术迭代催生的精准革命 第五代智能动平衡系统集成AI振动诊断算法与三维激光扫描技术,可实时生成设备转子质量偏心矢量图。某航空发动机维修中心应用该技术后,将叶片动平衡精度提升至0.1g·mm级,较传统方法提高两个数量级。这种”数字孪生”矫正模式突破了传统经验依赖,通过自适应配重模块实现0.01°级角度校正,使设备运行效率提升12%-18%。 四、复杂工况的适应性进化 面对高温、腐蚀、强电磁干扰等极端环境,专业团队配备防爆型动平衡仪与无线数据传输系统,可在-40℃至200℃区间稳定作业。某海上钻井平台案例中,工程师采用水下机器人搭载平衡模块,成功矫正深海采油泵的偏心振动,攻克了传统方法无法解决的密封腔体矫正难题。这种”环境免疫”能力使服务半径扩展至极地科考站与深空探测设备。 五、全维度价值网络的构建 现场服务已超越单纯的技术矫正,演变为设备健康管理的入口。通过建立设备振动指纹数据库,可预测未来3-6个月的潜在故障。某半导体工厂引入该服务后,将设备MTBF(平均无故障时间)从1200小时提升至2800小时,同时衍生出设备性能优化、能耗分析等增值服务。这种”矫正即服务”模式正在重构工业设备维护的价值链。 结语:工业心脏的守护者 从实验室到生产现场,动平衡矫正服务的进化史折射出制造业智能化转型的缩影。当工程师手持频谱仪穿梭于轰鸣的车间,他们不仅是振动的消除者,更是设备生命力的延续者。这种将精密仪器与工业现场深度融合的服务形态,正在重新定义现代制造业的效率边界与安全标准。