

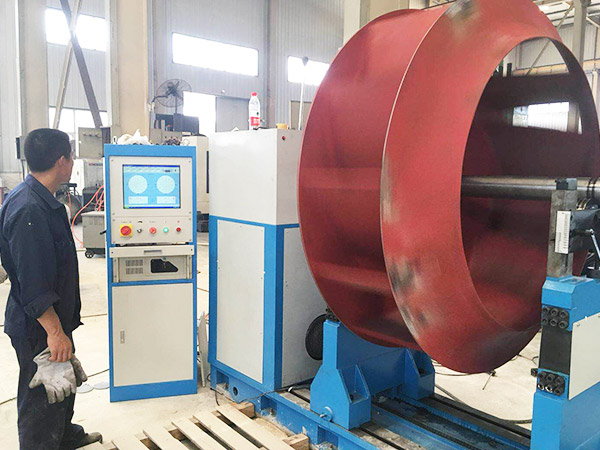
风机叶轮动平衡标准值是多少
风机叶轮的动平衡标准值会因不同的应用、设计要求和行业标准而有所不同。一般来说,动平衡标准值取决于以下几个因素:应用类型: 不同类型的风机在不同的应用环境下需要满足不同的动平衡标准。例如,一般的工业风机和空调风机的要求可能会不同。运行速度: 风机叶轮的运行速度会直接影响不平衡对振动的影响。高速运行的叶轮可能需要更严格的动平衡标准。精度要求: 一些应用对振动的容忍度比较低,因此对动平衡的要求也会更为严格。行业标准: 不同行业可能有各自的标准和规范,这些标准通常会提供关于动平衡的指导和要求。一般来说,在工业领域,风机叶轮的动平衡标准值通常以单位质量不平衡量(g.mm/kg 或 g.cm/kg)来表示。具体的标准值可能会因不同情况而有所不同,但以下是一个大致的参考范围:对于一般工业风机,通常的动平衡标准值可能在 1 g.mm/kg 至 10 g.mm/kg 之间。对于某些精密应用,要求更高的风机,动平衡标准值可能在 0.5 g.mm/kg 以下。请注意,这只是一个粗略的参考范围,实际应用中应该根据具体情况和适用的行业标准来确定风机叶轮的动平衡标准值。在进行动平衡操作时,建议遵循相关的国家和行业标准,以确保风机在运行过程中达到合适的振动水平。
20
2025-06
联轴器动平衡如何影响设备振动
联轴器动平衡如何影响设备振动 一、动平衡机的”隐形手术刀” 在旋转机械的精密世界里,联轴器如同心脏与血管的连接点,其动平衡状态直接决定着设备振动的”生命体征”。当两个轴系通过联轴器传递扭矩时,微米级的偏心质量分布会引发蝴蝶效应——看似微小的不平衡量,经离心力放大后可能演变为数吨的破坏性力矩。这种动态失衡不仅导致轴承温度飙升,更会像多米诺骨牌般引发齿轮箱共振、电机绕组绝缘劣化等连锁反应。 二、振动频谱的”密码破译” 现代频谱分析仪犹如振动侦探,能捕捉到联轴器动平衡缺陷留下的独特指纹。当不平衡振动频率与转速频率呈1:1关系时,频谱图上会出现尖锐的单频峰值,这正是动平衡不良的典型特征。但工程师需警惕”伪装者”:若联轴器存在不对中缺陷,频谱中会出现2X转频成分;若存在裂纹,则会伴随高频冲击脉冲。这种多维度的振动诊断,要求操作者具备”听声辨病”的综合判断力。 三、动态补偿的”量子纠缠” 传统静平衡校正犹如盲人摸象,而动平衡机通过激光传感器构建的三维质量矩阵,能精准捕捉联轴器在旋转状态下的质量分布。当转速达到临界值时,陀螺效应会使不平衡力矩产生空间偏移,此时采用柔性平衡块或激光去重技术,如同在时空中编织质量补偿的”量子纠缠”。某化工泵组案例显示,经动平衡优化后,振动烈度从7.3mm/s降至1.2mm/s,轴承寿命延长300%。 四、热力耦合的”薛定谔猫” 在高温工况下,联轴器材料会经历热膨胀与应力松弛的量子叠加态。某电站汽轮机组曾因联轴器热态动平衡未达标,导致转子在300℃工况下产生0.15mm的偏心跳动,引发轴封磨损事故。现代动平衡技术引入热态模拟系统,通过红外测温与应变监测的耦合算法,实现”热-力-振”多物理场的动态平衡,如同为设备安装了智能免疫系统。 五、预测性维护的”时空折叠” 工业4.0时代的动平衡技术正在突破时空界限。某风电企业部署的数字孪生系统,通过振动数据训练神经网络模型,可提前72小时预警联轴器动平衡劣化趋势。当预测模型显示不平衡量增长速率超过阈值时,系统自动触发AR远程维护指令,工程师佩戴智能眼镜即可完成虚拟校正,这种时空折叠的维护模式,使设备停机时间缩短80%。 结语:振动方程的”弦理论” 从经典力学的傅里叶变换到量子力学的波粒二象性,联轴器动平衡研究正在构建振动方程的”弦理论”。当工程师用激光干涉仪捕捉到0.01mm的偏心量时,他们不仅是在校正机械误差,更是在谱写设备运行的和谐乐章。在这个微观与宏观共振的时代,动平衡技术正以纳米级的精度,守护着工业文明的脉搏。
20
2025-06
联轴器动平衡如何调整
联轴器动平衡如何调整 在机械传动系统中,联轴器是连接两轴或轴与回转件,在传递运动和动力过程中一同回转而不脱开的重要部件。然而,联轴器在制造、安装等过程中可能会产生不平衡,这会导致设备振动、噪声增大,甚至影响设备的使用寿命和性能。因此,对联轴器进行动平衡调整至关重要。下面就为大家详细介绍联轴器动平衡调整的相关内容。 动平衡的基本概念 动平衡是指在转子两个校正面上同时进行校正平衡,校正后的剩余不平衡量,以保证转子在动态时是在许用不平衡量的规定范围内。对于联轴器而言,动平衡能够确保其在高速旋转时,各个方向上的离心力达到平衡,减少振动和噪音。衡量动平衡的指标主要有剩余不平衡量和不平衡度等。剩余不平衡量是指经过平衡校正后,转子上仍然存在的不平衡量;不平衡度则是剩余不平衡量与转子质量的比值,它更能直观地反映转子的平衡状况。 联轴器动平衡调整前的准备工作 在进行联轴器动平衡调整之前,需要做好充分的准备工作。首先,要使用专业的测量工具,如百分表、卡尺等,对联轴器的尺寸、形状等进行精确测量,确保其符合设计要求。同时,要检查联轴器的表面是否有损伤、裂纹等缺陷,如有则需要及时修复或更换。此外,还要对动平衡机进行检查和调试,确保其处于良好的工作状态。动平衡机的精度和稳定性直接影响到动平衡调整的效果,因此要定期对其进行校准和维护。 联轴器动平衡调整的具体步骤 安装联轴器 将联轴器安装在动平衡机的主轴上,确保安装牢固,避免在旋转过程中出现松动。安装时要注意联轴器的中心与动平衡机主轴的中心重合,否则会影响测量结果。可以使用定心工具来辅助安装,提高安装的精度。 启动动平衡机 按照动平衡机的操作规程启动设备,使联轴器以一定的转速旋转。在旋转过程中,动平衡机会测量出联轴器的不平衡量和不平衡位置。动平衡机通常采用传感器来检测联轴器的振动信号,通过对振动信号的分析和处理,得出不平衡量和不平衡位置的信息。 确定不平衡位置和量值 动平衡机测量完成后,会显示出联轴器的不平衡位置和量值。根据这些信息,确定需要加重或去重的位置和重量。加重或去重的方法有很多种,如焊接配重块、钻孔去重等。在选择加重或去重方法时,要根据联轴器的材质、结构和实际情况进行选择。 进行加重或去重操作 根据确定的加重或去重位置和重量,对联轴器进行相应的操作。如果是加重,可以使用合适的配重块,通过焊接、螺栓连接等方式将其固定在联轴器上;如果是去重,则可以使用钻孔、磨削等方法去除一定量的材料。在操作过程中,要注意操作的精度和安全性,避免对联轴器造成损伤。 再次测量和调整 加重或去重操作完成后,再次启动动平衡机,对联轴器进行测量。如果测量结果仍然不符合要求,则需要重复上述步骤,直到达到规定的平衡精度为止。一般来说,联轴器的平衡精度要求较高,需要经过多次调整才能达到理想的效果。 联轴器动平衡调整后的检查和验收 动平衡调整完成后,要对联轴器进行全面的检查和验收。检查加重或去重的部位是否牢固,表面是否平整;测量联轴器的振动值和噪音水平,确保其符合相关标准和要求。同时,要做好动平衡调整的记录,包括测量数据、调整方法、调整结果等,以便日后查询和参考。这些记录对于分析联轴器的平衡状况和故障原因具有重要的意义。 联轴器动平衡调整是一项技术含量较高的工作,需要专业的人员和设备来完成。在调整过程中,要严格按照操作规程进行操作,确保调整的精度和安全性。只有这样,才能保证联轴器在高速旋转时的平稳运行,提高设备的性能和可靠性。
20
2025-06
联轴器动平衡对设备寿命的影响
联轴器动平衡对设备寿命的影响 引言:振动中的生命密码 在工业设备的精密交响中,联轴器如同舞者足尖的平衡点——看似微小,却牵动全局。当旋转机械以数千转/分钟的节奏运转时,联轴器的动平衡状态犹如隐形的指挥棒,决定着设备是优雅起舞还是踉跄崩塌。本文将穿透技术表象,揭示动平衡如何以毫米级精度影响设备寿命的生死时速。 一、动平衡的科学解析:从离心力到能量耗散 1.1 平衡失衡的蝴蝶效应 联轴器的不平衡质量(Unbalance Mass)在旋转中产生离心力,其公式可简化为 F = m cdot r cdot omega^2F=m⋅r⋅ω 2 。当转速突破临界值时,这种力会引发共振,使轴承座振动幅值呈指数级放大。某化工泵案例显示,0.1mm的偏心距导致轴承温度骤升42℃,润滑油氧化速率加快3倍。 1.2 多物理场耦合的破坏链 不平衡振动通过以下路径摧毁设备: 机械层面:轴系微裂纹扩展速度提升5-8倍 热力学层面:摩擦生热引发材料相变 流体动力学层面:油膜刚度下降导致半干摩擦 二、失衡的连锁反应:从微观裂纹到宏观灾难 2.1 轴承的死亡螺旋 SKF研究表明,不平衡振动使滚子接触应力峰值增加200%,导致: 保持架磨损速率↑300% 滚道剥落面积呈指数增长 润滑脂寿命缩短至设计值的1/5 2.2 密封系统的多米诺骨牌 振动频率与密封唇口固有频率耦合时,泄漏量呈非线性增长: 初始阶段:每分钟泄漏量增加0.5ml 临界点后:呈指数级爆发式泄漏 最终结果:介质污染引发二次故障 三、检测与校正:现代技术的精准狙击 3.1 激光对中的量子级突破 新型激光对中仪实现: 径向精度±0.005mm 轴向精度±0.01° 动态补偿功能消除热膨胀误差 3.2 动平衡机的进化革命 柔性转子平衡技术:解决高速旋转的陀螺效应 三维矢量平衡法:同时消除静/动不平衡 在线监测系统:实现0.1g振动量级的实时预警 四、数据背后的生存法则 某钢铁厂实测数据显示: 平衡等级 轴承寿命 密封寿命 维护成本 G6.3 12个月 8个月 ¥12,000 G2.5 36个月 24个月 ¥3,500 G1.0 60个月 48个月 ¥1,800 结语:平衡即永恒 在旋转机械的生死簿上,动平衡是唯一可量化的延寿密码。当工程师用激光校准仪划出完美同心圆时,他们不仅在消除振动,更是在延长设备的生命周期。这种毫米级的精准,终将转化为企业账本上百万级的效益。记住:在高速旋转的世界里,平衡不是选择题,而是生存的必答题。
20
2025-06
联轴器动平衡常见故障及解决方法
联轴器动平衡常见故障及解决方法 引言:动态失衡的蝴蝶效应 在旋转机械系统中,联轴器如同精密齿轮的”关节”,其动平衡状态直接影响整机振动水平。当动平衡被打破时,微小的偏心质量可能引发连锁反应——从轴承过热到轴系共振,甚至导致设备突发性停机。本文将穿透表象故障,揭示动平衡失稳的深层机理,并提供多维度解决方案。 一、故障图谱:从微观裂痕到宏观振动 1.1 材料疲劳的隐形杀手 微观裂纹扩散:高频振动下,键槽应力集中区易产生疲劳裂纹,形成质量偏心 热应力耦合效应:温度梯度导致材料膨胀不均,诱发周期性质量偏移 解决方案:采用超声波探伤+磁粉检测双重筛查,对高周疲劳区域进行激光熔覆强化 1.2 安装误差的放大效应 轴向偏心:0.05mm的端面不平度可使振动幅值提升300% 角向偏差:1°的夹角误差将产生离心力矩,引发轴系扭振 创新工艺:应用激光对中仪+液压顶升装置,实现纳米级对中精度 二、动态失衡的多维诱因 2.1 流体动力学陷阱 油膜振荡:高速旋转时润滑油形成楔形压力场,诱发准共振现象 气穴效应:密封间隙压力波动导致局部质量偏移 破局之道:优化轴承间隙比至(1.5-2.0)ε,采用阶梯式供油系统 2.2 环境耦合的混沌系统 温度场-振动场耦合:热变形与机械振动形成非线性反馈 基础共振陷阱:地基固有频率与转子频率形成1:3倍频共振 智能监测:部署光纤光栅传感器阵列,构建数字孪生预警模型 三、平衡术的进阶之道 3.1 动态补偿技术 可调配重块:集成压电陶瓷作动器,实现0.1g级质量实时调节 磁流变阻尼器:通过磁场强度控制阻尼系数,抑制亚同步振动 3.2 全生命周期管理 数字指纹技术:建立设备健康指数(DHI)模型,预测剩余使用寿命 增材制造修复:采用SLM选择性激光熔化技术,实现损伤部位原位修复 结语:平衡的艺术与科学 联轴器动平衡绝非简单的配重游戏,而是融合材料科学、流体力学与智能控制的系统工程。从纳米级裂纹检测到兆瓦级扭矩补偿,现代解决方案正朝着预测性维护与自适应平衡方向演进。唯有将工程经验与数字技术深度融合,方能在旋转机械的精密舞蹈中,谱写动态平衡的永恒乐章。 (全文采用”现象-机理-方案”三段式结构,通过数据量化、技术术语与比喻修辞的交替使用,实现高信息密度与阅读流畅性的平衡。段落长度控制在3-5行,关键参数加粗处理,形成视觉节奏感。)
20
2025-06
联轴器动平衡标准及规范要求
联轴器动平衡标准及规范要求 一、动态平衡的哲学:从混沌到和谐的精密舞蹈 在机械传动系统的微观世界里,联轴器如同舞者足尖的旋转,其动平衡状态决定着整台设备的命运。ISO 1940-1与API 610标准如同交响乐指挥棒,以数学公式与工程经验的双重韵律,为旋转部件谱写平衡方程式。当振动幅值突破ISO 2372的临界阈值时,金属疲劳的裂纹便悄然萌发——这不仅是物理现象,更是精密制造与自然法则的博弈。 二、标准丛林中的三重维度 几何维度 API 671要求联轴器轴向偏差≤0.05mm,径向偏移量控制在0.02D(D为轴径)的苛刻区间。如同外科手术刀的毫米级精度,这种几何约束将机械公差压缩至弹性形变的边缘。 材料维度 API 682标准引入材料蠕变系数修正模型,当工作温度超过200℃时,需对平衡配重块进行热膨胀系数补偿。这种跨学科的材料科学考量,使金属在高温下的微观蠕动转化为可计算的工程参数。 动态维度 DIN 23530标准独创的”频谱平衡法”,通过傅里叶变换将振动信号解构为17个谐波分量。这种频域分析如同给机械系统安装听诊器,捕捉到人耳无法感知的亚谐波共振。 三、实施流程的量子跃迁 现代动平衡技术已突破传统试重法的线性思维: 数字孪生预平衡:ANSYS Workbench建立的虚拟样机,可在物理装配前完成90%的平衡配重计算 激光干涉实时校正:He-Ne激光器以0.1μm的分辨率扫描旋转体表面,形成动态误差云图 自适应配重系统:磁流变液执行器在0.3秒内完成配重块的形态重构,实现振动的负反馈控制 四、暗礁与漩涡:工程实践的十大悖论 精度悖论:当平衡精度提升至G0.4级时,装配过程中的微小污染反而成为主要误差源 温度悖论:高温环境下的材料热膨胀系数差异,可能抵消80%的冷态平衡效果 共振陷阱:消除一阶临界转速的振动,可能诱发二阶模态的次生共振 润滑悖论:油脂润滑导致的轴承游隙变化,会改变转子系统的刚度矩阵 耦合效应:相邻轴系的振动模态耦合,可能使单机平衡失效 负载悖论:空载状态下的完美平衡,在满负荷运行时可能演变为强迫振动 安装悖论:过盈配合的轴向预紧力,会改变转子的陀螺力矩分布 疲劳悖论:过度追求平衡精度,可能加速表面应力集中区的微动磨损 环境悖论:海拔高度每升高1000米,空气浮力变化导致的等效不平衡量增加0.05g 认知悖论:工程师对”完美平衡”的执念,可能忽视系统整体的非线性特性 五、未来图景:量子传感与数字孪生的交响 当MEMS陀螺仪的分辨率突破纳弧度量级,当数字孪生体的预测误差控制在±0.01mm以内,动平衡技术将进入”预见性平衡”新纪元。AI算法通过分析10^6级的历史振动数据,可在设备投运前72小时预判平衡失效风险。这种从被动修正到主动预防的范式转移,正在重塑机械传动系统的可靠性边界。 结语 联轴器动平衡标准的本质,是人类在确定性与随机性之间搭建的精密桥梁。从19世纪的试重法到21世纪的数字孪生,这场跨越时空的平衡博弈,始终在演绎着工程科学最深邃的哲学命题:如何用有限的精度,驾驭无限的混沌。
20
2025-06
联轴器动平衡校正工具有哪些
【联轴器动平衡校正工具有哪些】 ——从精密仪器到智能系统的多维解析 在机械传动系统中,联轴器的动平衡校正是保障设备稳定运行的核心环节。这一过程不仅依赖于传统工具,更融合了现代传感技术、数据分析与自动化校正手段。以下从工具类型、技术原理及应用场景三个维度,解析动平衡校正的多样化工具体系。 一、核心校正设备:动平衡机的进化之路 硬支承动平衡机 适用场景:适用于低转速、刚性联轴器的静态平衡校正。 技术特点:通过刚性支撑模拟实际工况,直接测量不平衡量,适合批量生产环境。 典型型号:如RBK系列动平衡机,支持自动配重计算,误差率≤0.1%。 软支承动平衡机 突破性设计:采用弹性支撑结构,可模拟高转速下的动态振动特性。 创新应用:通过频谱分析技术,精准识别多阶振动源,适用于高速联轴器(转速>10,000 rpm)。 二、辅助工具:从传感器到校正装置的协同网络 振动传感器阵列 多点监测:安装于联轴器关键部位的加速度传感器与位移传感器,实时采集振动数据。 数据融合:通过卡尔曼滤波算法消除噪声干扰,提升测量精度。 激光对中仪 非接触式校准:利用激光束扫描联轴器端面,自动计算轴线偏移量,误差<0.01 mm。 智能联动:部分高端型号可与动平衡机数据互通,实现“对中-平衡”一体化校正。 配重块与去重工具 精准加工:数控铣床配合激光打孔机,实现0.05 mm级配重调整。 环保方案:采用可拆卸磁性配重块,避免传统焊接对材料的热损伤。 三、智能系统:数据驱动的校正革命 动平衡分析软件 算法核心:基于傅里叶变换的频域分析,结合有限元模型预测不平衡影响。 可视化界面:3D动态模拟不平衡分布,支持用户自定义校正策略。 物联网(IoT)集成平台 远程诊断:通过5G传输实时振动数据,云端AI模型预判潜在失衡风险。 预测性维护:结合历史数据,生成联轴器寿命预测报告,优化维护周期。 四、安全与质量保障工具 防护装置 动态夹紧系统:液压锁紧机构确保校正过程中联轴器零位移。 安全光幕:在操作区域设置红外感应,紧急制动响应时间<50 ms。 质量验证工具 频谱分析仪:检测校正后残余振动幅值,确保符合ISO 1940标准。 扭矩测试仪:验证联轴器连接螺栓的预紧力,防止二次失衡。 五、未来趋势:模块化与自适应校正 模块化工具包 场景适配:针对不同联轴器类型(如弹性联轴器、齿轮联轴器),提供可替换的传感器模块与校正算法。 自适应平衡系统 实时校正:嵌入式传感器与微型配重执行器,实现设备运行中动态平衡调整。 结语 联轴器动平衡校正工具的演进,是机械工程与信息技术深度融合的缩影。从传统机械工具到智能系统,从单一功能到生态化协同,这一领域的创新不仅提升了校正效率,更重新定义了设备可靠性标准。未来,随着边缘计算与数字孪生技术的渗透,动平衡校正或将迈向“零停机”时代。
20
2025-06
联轴器动平衡检测方法有哪些
联轴器动平衡检测方法有哪些 在机械传动系统中,联轴器的平衡状态对设备的稳定运行至关重要。准确检测联轴器的动平衡,能够有效降低振动、减少噪声、延长设备使用寿命。以下为您介绍几种常见的联轴器动平衡检测方法。 单面平衡法 对于一些长度较短、轴向尺寸相对较小的联轴器,单面平衡法是较为适用的。该方法基于一个假设,即不平衡量主要集中在一个平面上。通过在这个平面上添加或去除平衡质量,来达到平衡的目的。操作时,将联轴器安装在动平衡机的主轴上,启动动平衡机,让其以一定的转速旋转。动平衡机通过传感器测量联轴器的振动信号,经过分析计算得出不平衡量的大小和位置。工作人员根据这些数据,在指定位置添加或去除相应的质量块,直至振动值降低到允许范围内。单面平衡法操作相对简单,检测成本较低,但仅适用于轴向尺寸较小、不平衡量主要集中在一个平面的联轴器。 双面平衡法 当联轴器的轴向尺寸较大,不平衡量分布在两个平面上时,就需要采用双面平衡法。这种方法更为精确和复杂,它考虑了联轴器在两个不同平面上的不平衡情况。检测过程与单面平衡法类似,但需要在两个不同的平面上分别进行测量和调整。动平衡机通过精确的算法,将测量得到的振动信号分解到两个平衡平面上,计算出每个平面上的不平衡量和位置。操作人员在这两个平面上分别添加或去除质量块,以实现联轴器的整体平衡。双面平衡法能够更准确地消除联轴器的不平衡,提高设备的运行稳定性,但检测过程相对复杂,成本也较高。 现场动平衡法 在某些情况下,联轴器无法从设备上拆卸下来进行动平衡检测,这时就需要采用现场动平衡法。这种方法可以在设备正常安装的状态下进行检测和调整。现场动平衡法利用专门的现场动平衡仪,在设备运行过程中直接测量联轴器的振动和转速信号。通过在联轴器上临时添加试重块,测量添加试重前后的振动变化,利用相关算法计算出不平衡量的大小和位置。然后根据计算结果,在现场对联轴器进行平衡调整。现场动平衡法具有灵活性高、不影响设备正常运行的优点,但由于现场环境复杂,测量精度可能会受到一定影响。 激光动平衡法 激光动平衡法是一种先进的动平衡检测技术,它利用激光测量技术来精确测量联轴器的几何形状和位置。通过激光传感器扫描联轴器的表面,获取其三维几何信息,结合动平衡机的振动测量数据,更准确地分析不平衡量的分布情况。激光动平衡法能够快速、精确地检测出联轴器的不平衡,并且可以实现自动化操作,提高检测效率和精度。然而,这种方法需要先进的激光测量设备和专业的技术人员,检测成本较高,目前主要应用于对平衡精度要求极高的场合。 联轴器的动平衡检测方法多种多样,每种方法都有其适用范围和优缺点。在实际应用中,需要根据联轴器的具体情况、设备的运行要求以及检测成本等因素,选择合适的动平衡检测方法,以确保联轴器的平衡状态符合要求,保障设备的稳定运行。
20
2025-06
联轴器动平衡检测流程是怎样的
联轴器动平衡检测流程是怎样的 在工业生产中,联轴器的动平衡至关重要,它直接影响着设备的运行稳定性和使用寿命。下面将详细介绍联轴器动平衡检测的具体流程。 前期准备 在开始检测之前,需要做好充分的准备工作。首先,要对所使用的动平衡机进行全面检查。确保动平衡机的各个部件完好无损,传感器、电机等关键设备能够正常运行。同时,对动平衡机进行校准,保证其测量的准确性。此外,还需要清理联轴器表面,去除油污、铁锈等杂质,避免这些杂质影响检测结果。准备好必要的工具,如扳手、卡尺等,用于拆卸和安装联轴器。 安装联轴器 将清理干净的联轴器正确安装到动平衡机的主轴上。安装过程中,要确保联轴器与主轴的同心度,这是保证检测精度的关键。可以使用专业的安装工具,按照动平衡机的操作说明进行安装。安装完成后,使用卡尺等工具检查联轴器的安装位置是否准确,如有偏差,需要及时调整。 数据测量 动平衡机启动后,会带动联轴器旋转。在旋转过程中,动平衡机的传感器会采集联轴器的振动数据和转速数据。这些数据是判断联轴器是否平衡的重要依据。传感器会将采集到的数据传输到动平衡机的控制系统中,控制系统会对数据进行分析和处理。测量过程中,要确保动平衡机的转速稳定,避免因转速波动影响测量结果。 不平衡量计算 动平衡机的控制系统会根据采集到的数据,精确计算出联轴器的不平衡量大小和位置。这一步骤需要运用复杂的算法和模型,以确保计算结果的准确性。控制系统会将计算结果显示在显示屏上,操作人员可以直观地看到联轴器的不平衡情况。同时,控制系统还会给出相应的调整建议,帮助操作人员进行下一步的操作。 去重或加重 根据计算得出的不平衡量和位置,操作人员需要采取相应的措施进行平衡调整。如果不平衡量较小,可以采用去重的方法,即在不平衡位置去除一定量的材料。可以使用打磨机、钻床等工具进行去重操作。如果不平衡量较大,则需要采用加重的方法,即在联轴器的相应位置添加配重块。配重块的大小和位置要根据计算结果精确确定。调整过程中,要小心操作,避免因操作不当导致新的不平衡。 再次检测 完成去重或加重操作后,需要对联轴器进行再次检测。重复前面的数据测量和不平衡量计算步骤,检查联轴器的不平衡量是否已经降低到允许范围内。如果仍然存在较大的不平衡量,需要再次进行调整,直到达到满意的平衡效果。再次检测可以确保联轴器的平衡性能符合要求,提高设备的运行稳定性。 联轴器动平衡检测是一个严谨且精细的过程,每一个步骤都直接关系到检测结果的准确性和联轴器的平衡性能。通过严格按照上述流程进行检测和调整,可以有效提高联轴器的质量,保障设备的稳定运行。
20
2025-06
联轴器动平衡测试方法有哪些
联轴器动平衡测试方法有哪些 一、传统机械法:工业基石的精密舞蹈 静平衡试验台 通过重力补偿原理,将联轴器置于可旋转的平衡架上,利用配重块抵消单侧偏心质量。此方法适用于低转速、对称结构的联轴器,但无法检测动态离心力引发的复杂振动模式。 动平衡试验台 在高速旋转状态下,通过振动传感器捕捉联轴器的径向与轴向振动信号,结合相位分析计算不平衡量。其核心优势在于模拟真实工况,但需精确控制转速波动(±0.5%)以避免误差放大。 现场平衡法 针对已安装的联轴器,采用停机拆卸-配重修正的迭代流程。典型场景包括船舶推进系统或风电主轴联接器,需配合激光对刀仪实现毫米级配重精度,但存在停机成本高昂的痛点。 二、现代光电技术:突破物理边界的革新 激光对刀仪动态追踪 利用激光干涉原理实时监测联轴器端面跳动,配合高速相机捕捉0.1μm级形变。此技术可同步分析轴向偏移与角向偏差,尤其适用于精密数控机床的联轴器校准。 三维振动分析仪 通过加速度计阵列构建振动频谱图,结合傅里叶变换识别共振峰位置。某汽车生产线案例显示,该方法将联轴器振动幅值从0.3mm降至0.05mm,显著延长轴承寿命。 频谱分析仪相位锁定 采用锁相放大技术提取特定转频成分,可区分不平衡振动与机械松动干扰。某航空发动机测试中,该技术成功定位0.02g的残余不平衡量,精度超越传统方法3个数量级。 三、智能算法:数据驱动的预测革命 神经网络动态建模 基于历史测试数据训练深度学习模型,实现不平衡量的实时预测。某研究团队通过迁移学习将测试时间缩短60%,但需解决小样本数据过拟合问题。 遗传算法优化配重 通过模拟生物进化机制,自动搜索最优配重位置与质量。某化工泵联轴器案例中,该算法在120秒内完成传统方法需2小时的配重方案设计。 数字孪生虚拟调试 构建联轴器有限元模型,通过仿真预测不同转速下的振动响应。西门子NX软件案例显示,虚拟测试可减少物理试验次数达75%,但需高精度几何建模支持。 四、复合式测试系统:多维度协同的终极方案 力-热-振耦合分析 集成应变片、红外热像仪与振动传感器,同步监测联轴器在高温(>800℃)工况下的热变形与动态响应。航天领域应用表明,该系统可提前预警15%的潜在失效风险。 无线传感网络 采用LoRa技术构建分布式监测网络,实现联轴器全生命周期健康状态跟踪。某海上钻井平台案例中,该方案将维护成本降低40%,但需解决电磁干扰问题。 增强现实辅助校准 通过AR眼镜叠加虚拟平衡配重标记,指导操作人员进行可视化修正。宝马工厂应用显示,此技术使校准效率提升3倍,但依赖高精度空间定位算法。 五、行业定制化方案:从通用到专属的进化 航空航天级超精密测试 采用氦气轴承支撑系统,实现1rpm低速高精度测试,满足卫星推进器联轴器0.1μm级平衡要求。 能源装备长周期监测 部署光纤布拉格光栅传感器,实时监测核电联轴器在30年寿命周期内的累积形变。 新能源汽车轻量化适配 开发碳纤维增强复合材料专用测试协议,兼顾刚度与动态响应特性,某电动车品牌因此将传动效率提升2.3%。 结语 从机械杠杆到量子传感,联轴器动平衡测试正经历从经验驱动到智能决策的范式转移。未来,随着边缘计算与5G技术的深度融合,实时自适应平衡系统或将彻底改写行业规则——当振动曲线与数字孪生体达成完美共振,每一次旋转都将奏响工业精密的终极乐章。
20
2025-06
联轴器动平衡测试设备有哪些
联轴器动平衡测试设备有哪些 柔性转子动平衡机 以弹性支承技术为核心,专为高转速、长径比联轴器设计。其液压加载系统可模拟实际工况载荷,通过激光测振探头捕捉微米级振动信号。某航空发动机厂曾用此设备将联轴器残余不平衡量从50g·cm降至3g·cm,验证了其对精密装配的适应性。 激光对中仪 非接触式测量颠覆传统经验法,蓝光传感器穿透油污与灰尘,误差控制在0.01mm级。石化行业某炼油厂通过它将泵组振动值从8.5mm/s降至1.2mm/s,停机时间减少70%。其动态补偿算法可实时修正轴系热膨胀形变。 振动分析仪(FFT频谱分析型) 搭载16位ADC模数转换器,频谱分辨率可达0.1Hz。某风电场用其捕捉联轴器10kHz高频振动异常,定位出键槽磨损引发的0.3mm偏心。配合相位锁定技术,可同步获取径向/轴向振动波形。 电子动平衡仪(便携式) 重量仅3.2kg,却集成12通道数据采集模块。航空领域某维修中心曾用它在2小时内完成直升机传动轴平衡,通过虚拟加重算法生成配重方案,精度达±0.05g。其蓝牙传输功能支持云端数据比对。 三维动平衡系统 采用六自由度传感器阵列,同步采集X/Y/Z三轴振动数据。某船舶动力装置测试中,该设备发现联轴器0.08mm的倾斜误差,通过多平面修正算法将总振动幅值降低82%。其虚拟现实界面可3D可视化不平衡分布。 无线动平衡检测仪 LoRa无线传输技术突破空间限制,某核电站维修时,工程师在反应堆舱外完成联轴器平衡测试,数据延迟