

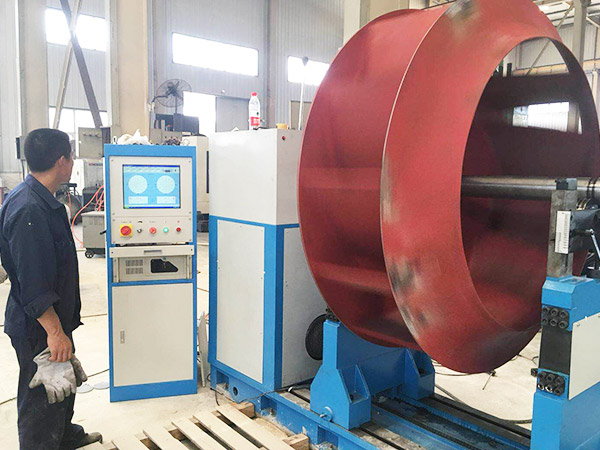
风机叶轮动平衡标准值是多少
风机叶轮的动平衡标准值会因不同的应用、设计要求和行业标准而有所不同。一般来说,动平衡标准值取决于以下几个因素:应用类型: 不同类型的风机在不同的应用环境下需要满足不同的动平衡标准。例如,一般的工业风机和空调风机的要求可能会不同。运行速度: 风机叶轮的运行速度会直接影响不平衡对振动的影响。高速运行的叶轮可能需要更严格的动平衡标准。精度要求: 一些应用对振动的容忍度比较低,因此对动平衡的要求也会更为严格。行业标准: 不同行业可能有各自的标准和规范,这些标准通常会提供关于动平衡的指导和要求。一般来说,在工业领域,风机叶轮的动平衡标准值通常以单位质量不平衡量(g.mm/kg 或 g.cm/kg)来表示。具体的标准值可能会因不同情况而有所不同,但以下是一个大致的参考范围:对于一般工业风机,通常的动平衡标准值可能在 1 g.mm/kg 至 10 g.mm/kg 之间。对于某些精密应用,要求更高的风机,动平衡标准值可能在 0.5 g.mm/kg 以下。请注意,这只是一个粗略的参考范围,实际应用中应该根据具体情况和适用的行业标准来确定风机叶轮的动平衡标准值。在进行动平衡操作时,建议遵循相关的国家和行业标准,以确保风机在运行过程中达到合适的振动水平。
23
2025-06
如何判断设备需做动平衡校正
如何判断设备需做动平衡校正 在工业生产与设备运行的领域中,动平衡校正犹如一位隐形的守护者,保障着各类旋转设备的稳定、高效运行。不过,如何精准判断设备是否需要进行动平衡校正,却困扰着不少人。接下来,让我们一起探寻其中的关键要点。 观察设备运行时的振动情况 设备运行时的振动表现是判断是否需要动平衡校正的关键信号。正常运转的设备,振动幅度通常处于一个稳定且较小的范围。当设备出现异常振动时,我们就得提高警惕了。倘若振动突然增大,或者振动呈现出无规律的波动,这很可能是设备动平衡出现了问题。 例如,在一台高速旋转的电机上,如果能明显感觉到机身的剧烈晃动,甚至能听到因振动产生的异常噪音,那么就极有可能是电机转子的动平衡失调。此外,振动的频率也能提供重要线索。不同类型的动平衡问题往往会对应特定的振动频率。通过专业的振动检测设备,对振动频率进行分析,就能更准确地判断问题所在。 留意设备的噪音变化 除了振动,设备运行时的噪音也是一个重要的判断依据。当设备的动平衡良好时,其运转声音通常是平稳且有规律的。一旦动平衡被破坏,噪音就会发生明显变化。可能会出现尖锐的啸叫声、低沉的轰鸣声或者不规则的杂音。 以风机为例,正常运行的风机声音较为柔和且连续。若风机的叶轮动平衡出现问题,在运转过程中就会产生刺耳的噪音,这是由于叶轮不平衡导致气流紊乱,进而引发空气动力噪声。此时,我们就需要考虑对风机进行动平衡校正,以降低噪音,提高设备的运行质量。 关注设备的性能表现 设备的性能表现也是判断是否需要动平衡校正的重要方面。如果设备的输出功率下降、工作效率降低,或者出现频繁的停机故障,都有可能与动平衡问题有关。 比如,一台机床在加工零件时,原本能够保证高精度的加工质量,但突然出现加工精度下降,零件表面粗糙度增大的情况。经过检查,发现机床主轴的动平衡出现偏差,导致主轴在旋转过程中产生微小的摆动,从而影响了加工精度。在这种情况下,及时对主轴进行动平衡校正,就能恢复机床的正常性能。 参考设备的使用时间和工作环境 设备的使用时间和工作环境也会对动平衡产生影响。一般来说,随着设备使用时间的增长,其零部件会逐渐磨损,动平衡也可能会随之发生变化。特别是那些长期处于高负荷、高转速运行状态的设备,更容易出现动平衡问题。 另外,恶劣的工作环境,如粉尘、潮湿、高温等,也会加速设备的损坏,影响动平衡。例如,在矿山等粉尘较大的环境中工作的设备,粉尘会附着在旋转部件上,改变其质量分布,从而破坏动平衡。因此,对于使用时间较长或者工作环境恶劣的设备,要定期进行动平衡检测,及时发现并解决问题。 判断设备是否需要进行动平衡校正需要综合考虑多个方面的因素。通过观察设备的振动、噪音、性能表现,参考使用时间和工作环境等,我们就能准确地判断设备的动平衡状况,及时采取相应的校正措施,确保设备的稳定运行,提高生产效率和产品质量。
23
2025-06
如何判断车床主轴是否需要动平衡
如何判断车床主轴是否需要动平衡 在机械加工领域,车床主轴的动平衡至关重要。它直接影响着加工精度、刀具寿命以及机床的整体性能。那么,怎样判断车床主轴是否需要动平衡呢?以下为您详细介绍。 倾听运转异响 当车床启动后,仔细倾听主轴运转时的声音。正常情况下,主轴运转声音平稳且均匀。倘若听到异常的振动声、摩擦声或者尖锐的啸叫声,这极有可能预示着主轴存在不平衡问题。不平衡会使主轴在高速旋转时产生额外的振动,进而引发这些异常声响。就好比汽车轮胎不平衡时,行驶过程中会发出奇怪的噪音一样。这种声音的出现,就像是给我们发出的一个警示信号,提醒我们要对主轴的动平衡状况予以关注。 观察振动情况 在车床工作时,观察其整体的振动情况。可以用手触摸车床的机身,如果感觉到明显的振动,或者看到车床在工作台上有轻微的跳动,这很可能是主轴不平衡造成的。此外,还可以留意加工工件的表面质量。如果工件表面出现周期性的振纹,这也是主轴不平衡的一个显著表现。不平衡的主轴会在旋转过程中产生离心力,导致刀具在切削时产生不稳定的运动,从而在工件表面留下痕迹。这种振动不仅会影响加工精度,还会加速机床零部件的磨损,降低机床的使用寿命。 检测转速稳定性 借助转速测量仪器,监测主轴在不同转速下的稳定性。正常的主轴在设定转速下应该能够稳定运行,转速波动极小。若发现主轴转速出现明显的波动,或者在特定转速下出现转速突然下降或上升的情况,这可能意味着主轴存在不平衡现象。不平衡会使主轴在旋转时受到不均匀的力,从而影响其转速的稳定性。这就如同骑自行车时,如果车轮不平衡,骑行起来就会感觉费力,而且速度也难以保持稳定。 分析刀具磨损情况 刀具的磨损情况也能为我们判断主轴动平衡提供线索。不平衡的主轴会使刀具在切削过程中承受不均匀的力,导致刀具磨损加剧。如果发现刀具的磨损速度明显加快,或者刀具的刃口出现异常的磨损形态,如局部磨损严重、崩刃等,这可能与主轴的不平衡有关。因为不平衡的主轴会使刀具在切削时产生额外的振动和冲击,加速刀具的磨损。就像一把锋利的刀,如果使用时受力不均匀,很快就会变钝一样。 判断车床主轴是否需要动平衡需要综合多方面的因素进行考量。通过倾听异响、观察振动、检测转速稳定性以及分析刀具磨损情况等方法,我们能够及时发现主轴不平衡的问题,并采取相应的措施进行调整和修复,从而保证车床的正常运行和加工质量。
23
2025-06
如何判断转子是否需要动平衡校正
如何判断转子是否需要动平衡校正 一、振动分析:捕捉动态失衡的蛛丝马迹 转子系统的异常振动是动平衡需求的最直接信号。通过振动传感器采集径向、轴向振动数据,需重点关注以下特征: 频谱异常:若频谱图中工频成分显著高于2倍频或存在非整数倍谐波,可能预示质量分布不均。 时域突变:振动波形出现周期性尖峰或包络调制,反映转子存在局部质量偏移。 轴心轨迹畸变:椭圆轨迹偏心率超过0.15,或出现香蕉形、泪滴形轨迹,需警惕动平衡失效。 案例:某离心泵在1500rpm时振动速度达7.1mm/s(ISO 10816-3标准允许值为4.5mm/s),频谱显示98%能量集中于工频,经动平衡后降至2.3mm/s。 二、运行参数异常:系统失衡的连锁反应 动平衡缺陷会引发多维度参数异变,需建立多参数关联分析模型: 功率波动:电机电流谐波畸变率突增5%以上,伴随功率因数下降 温度梯度:轴承座温差超过15℃(红外热像仪检测) 润滑劣化:油液光谱分析显示Fe含量月增长率超20ppm 警示:某压缩机机组在未更换轴承情况下,润滑油铁磁颗粒浓度从0.8mg/L骤增至6.3mg/L,最终确诊为转子动平衡不良导致的轴承异常磨损。 三、结构损伤迹象:失衡引发的次生灾害 动平衡缺陷可能诱发不可逆损伤,需通过以下手段早期识别: 声发射检测:在20-1000kHz频段捕捉到异常脉冲信号 应变监测:关键部位应变片读数呈现周期性超限(如超过屈服强度的30%) 密封泄漏:机械密封端面磨损量月均增长0.05mm以上 数据:某汽轮机叶片在动平衡不良状态下,振动应力导致榫槽部位出现0.2mm疲劳裂纹,超声波检测显示裂纹扩展速率达0.1mm/千小时。 四、经验判断法:工程实践的智慧沉淀 结合设备特性建立经验阈值体系: 设备类型 允许振动值(mm/s) 动平衡触发值(mm/s) 通用电机 ≤4.5(ISO标准) ≥6.3 精密机床 ≤1.8(ISO 2372) ≥2.8 涡轮机械 ≤7.1(API 617) ≥11.2 注意:需结合设备转速修正,公式:V=1.5×√n(n为转速rpm) 五、综合诊断流程:系统化决策框架 建议采用PDCA循环进行动平衡需求判定: Plan:建立设备健康档案,记录历史振动数据 Do:实施多传感器同步监测(振动+温度+油液) Check:运用包络解调、小波变换等算法提取特征值 Act:当满足以下任一条件时启动动平衡: 振动烈度超过ISO标准2个等级 振动相位角波动>±15° 振动趋势曲线斜率>0.5mm/s/千小时 工具推荐: 动平衡仪:Ludeca Balancer 3000(支持柔性转子校正) 分析软件:Dyrosoft Vibration Analyst(含ISO标准自动比对功能) 结语:动态平衡的艺术与科学 动平衡需求判断需融合精密仪器与工程直觉,建议建立”振动基线-阈值预警-损伤验证”三级响应机制。当设备呈现”振动异常+参数劣化+损伤征兆”的复合特征时,应立即启动动平衡校正程序,避免从功能性故障滑向灾难性失效。
23
2025-06
如何判断轴是否需要动平衡
各位机械小达人!今天咱来唠唠怎么判断轴是不是得做动平衡。我给大家打个比方哈,这轴就像机器里跳动的心脏,它要是不舒服,就会发“求救信号”。你知道吗,读懂这些“信号”可是判断动平衡需求的第一步呢! 咱先看看轴的“身体语言”。第一是振动警报,要是你用手背轻触轴体,感觉有像心跳一样的脉动,那可能是初期失衡了。要是设备基座肉眼可见地晃起来,那得赶紧排查。要是轴剧烈震颤,还伴着金属碰撞声,那可就到危险临界点啦,就像人快“挂掉”一样! 第二是噪音密码。要是有像钟表走动一样有规律的“哒哒”声,或者持续尖锐的啸叫,再或者突发的爆裂音,那都说明轴可能出问题了。 第三是温度异常。要是轴局部发烫,不同区域温差超过5℃;或者整体过热,温度比正常值高10%以上;甚至突然降温,这可能预示着润滑系统失效了。 初步观察发现异常后,就得用专业的四维检测法来确认啦。第一是动态测试法,用激光测振仪记录轴旋转时的位移曲线,振幅超过0.1mm就得调整。第二是频谱分析法,通过振动频谱仪捕捉特征频率,当1X频率幅值占比超过总能量30%就预警。第三是热成像扫描,用红外热像仪检测轴体温度分布,温差超过8℃就得重点检查。第四是轴承磨损检测,用游标卡尺测量轴承间隙,径向间隙超过标准值15%就有隐患。 然后还有个快速判断流程,叫决策树。先初步筛查,看看设备有没有不正常的振动、噪音,检查润滑系统正不正常,确认负载在不在额定范围内。接着深度检测,连续记录48小时振动数据,分析频谱图里的谐波成分,测量轴向窜动量超不超标。最后最终判定,振动烈度超过ISO 10816 - 3标准,或者轴承温度连续3小时高于环境温度25℃,又或者设备效率下降超过10%,满足其中任一条件就得做动平衡。 还有一些特殊场景的处理。新设备调试期,运行200小时后必须做动平衡校验。高精密设备,转速超过10000rpm的每季度得检测。恶劣工况下工作的轴,检测周期得缩短50%。设备停机超过72小时后重启前,必须重新校平衡。 最后说说预防性维护策略。要建立振动档案,每月记录关键参数,画趋势变化曲线。每季度拆检轴系,做定期清洁保养,清除积碳、油泥这些脏东西。润滑管理也很重要,得根据ISO 8068标准选合适的润滑剂,让油位在视窗1/2 - 2/3区间。关键轴系备件要做预平衡处理,精度等级不低于G6.3。 真的是,要是发现轴系有裂纹、材质疏松这些结构性缺陷,动平衡调整也只是暂时缓解症状,必须马上换部件。建议每年至少做两次专业动平衡检测,预防性维护成本就只是故障维修的1/10,太划算了!大家可别嫌麻烦,赶紧行动起来,让轴健健康康的!
23
2025-06
如何判断风扇需要动平衡校正
如何判断风扇需要动平衡校正 在工业生产与日常生活中,风扇是极为常见的设备。然而,随着使用时间的增加,风扇可能会出现各种问题,其中动平衡失调是一个容易被忽视却又影响重大的问题。那如何判断风扇是否需要动平衡校正呢?下面为大家详细介绍。 观察风扇的运行状态 风扇正常运行时,应当是平稳且安静的。要是在启动风扇之后,明显察觉到风扇有剧烈的振动,那很可能就存在动平衡问题。想象一下,当你打开风扇,整个风扇装置都在抖动,甚至这种抖动还会传递到与之相连的设备或支架上,这就如同一个舞者在跳舞时身体总是无法保持平衡,那舞姿肯定是混乱不堪的。而且,振动还会随着风扇转速的提高而加剧。另外,风扇在运行过程中发出异常的噪音也是一个重要的信号。正常的风扇运转声音是比较均匀且轻微的,但如果听到刺耳、尖锐或者不规则的噪音,那就像美妙的音乐中突然出现了不和谐的音符,很有可能是风扇的动平衡出现了问题。 查看风扇的外观情况 仔细检查风扇的外观,看扇叶是否有损坏、变形或者污垢堆积。扇叶就好比风扇的“翅膀”,一旦“翅膀”出了问题,风扇自然难以平稳飞行。如果扇叶有明显的弯曲、裂缝或者缺失部分,这会直接导致风扇在旋转时质量分布不均匀,就像一辆汽车的轮胎磨损不均匀,行驶起来肯定会颠簸。此外,长时间使用后,扇叶上可能会积累大量的灰尘和污垢,这也会改变扇叶的质量分布,破坏风扇的动平衡。就好像一个人身上一边挂了很多重物,另一边却很轻,走路的时候肯定会东倒西歪。 参考风扇的使用时长和环境 风扇的使用时长也是一个重要的判断因素。一般来说,使用时间越长,风扇出现动平衡问题的概率就越大。这就像一台机器,经过长时间的运转,各个零部件都会有一定程度的磨损。如果风扇已经使用了很长时间,而且没有进行过定期的维护保养,那么它很可能需要进行动平衡校正。另外,风扇的使用环境也会对其动平衡产生影响。如果风扇是在多尘、潮湿或者有腐蚀性气体的环境中使用,扇叶更容易受到损坏和污染,从而导致动平衡失调。比如在工厂的车间里,灰尘很多,风扇的扇叶就容易沾满灰尘,久而久之就会影响动平衡。 判断风扇是否需要动平衡校正需要综合考虑多个方面。通过观察风扇的运行状态、查看外观情况以及参考使用时长和环境等因素,我们可以较为准确地判断风扇是否需要进行动平衡校正。及时发现并解决动平衡问题,不仅可以延长风扇的使用寿命,还能提高其工作效率,减少能源消耗。
23
2025-06
如何判断风机叶轮是否需要动平衡校正
如何判断风机叶轮是否需要动平衡校正 在风机的运行过程中,叶轮的平衡状态至关重要。它不仅影响风机的性能,还关乎设备的使用寿命和运行安全。以下几种方法可以帮助判断风机叶轮是否需要进行动平衡校正。 观察振动情况 振动是判断风机叶轮是否失衡的最直观表现。如果风机在运行时出现异常振动,那么很可能是叶轮的平衡出了问题。你可以通过手感去感受风机的振动程度,经验丰富的专业人员能够凭借手感大致判断振动是否在正常范围内。不过,更精确的方法是使用振动测试仪。将测试仪安装在风机的关键部位,如轴承座等,它能实时监测振动的频率、振幅等参数。当振动值超过了设备的允许范围,就需要进一步检查叶轮的平衡情况。一般来说,振动频率较高且振幅较大时,很可能是叶轮存在不平衡问题。例如,当振动频率接近叶轮的旋转频率时,这种共振现象会加剧设备的损坏,必须及时进行动平衡校正。 倾听运行声音 风机正常运行时,声音应该是平稳且有规律的。如果在运行过程中听到异常的噪音,如尖锐的呼啸声、沉闷的撞击声等,这可能暗示着叶轮存在不平衡。尖锐的呼啸声可能是由于叶轮旋转时气流分布不均匀,而不平衡的叶轮会导致这种气流紊乱加剧。沉闷的撞击声则可能是叶轮与其他部件发生了轻微的碰撞,这往往是因为叶轮在旋转过程中出现了摆动,偏离了正常的运行轨迹。当听到这些异常声音时,要及时停机检查,判断是否是叶轮不平衡引起的。 分析转速与功率变化 风机的转速和功率之间存在着一定的对应关系。在正常情况下,当风机的负载稳定时,其转速和功率应该保持相对稳定。如果发现风机的转速出现波动,或者功率消耗异常增加,可能是叶轮不平衡导致的。叶轮不平衡会增加风机的运行阻力,为了维持正常的转速,电机就需要消耗更多的功率。通过监测风机的转速表和功率表,对比设备的设计参数和历史运行数据,就能发现这些异常变化。例如,当功率突然比正常情况高出 10% 以上,而负载并没有明显增加时,就需要怀疑叶轮的平衡状态。 查看磨损状况 定期对风机进行检查时,要仔细观察叶轮的磨损情况。不平衡的叶轮在旋转过程中,各部位受到的力是不均匀的,这会导致叶轮局部磨损加剧。检查叶轮的叶片表面是否有明显的磨损痕迹,如磨损的深度、宽度等。同时,还要注意叶轮的轮毂、轴孔等部位是否有变形、裂纹等情况。如果发现叶轮的磨损不均匀,或者某些部位的磨损程度明显超过了其他部位,这很可能是叶轮不平衡造成的。因为不平衡的叶轮在旋转时,会对磨损部位产生更大的压力,加速磨损的进程。 判断风机叶轮是否需要动平衡校正需要综合运用多种方法。通过观察振动、倾听声音、分析转速与功率变化以及查看磨损状况等手段,能够及时发现叶轮的不平衡问题,确保风机的安全、稳定运行。一旦确定叶轮需要动平衡校正,要及时采取措施,避免设备进一步损坏,降低维修成本。
23
2025-06
如何判断风机叶轮需要做动平衡
各位风机小粉丝们!今天咱来聊聊怎么判断风机叶轮需不需要做动平衡。风机叶轮就像个不知疲倦的舞者,一旦它平衡没掌握好,那整台设备就跟抽风似的跟着瞎晃悠,跟跳危险的舞一样。咱怎么才能发现那些细微的“失衡信号”呢?下面我就用大白话给大家说5个关键的观察点。 第一,设备突然“抖腿”了?说不定是叶轮在抗议呢!就好比你坐个椅子一直晃,身体本能就觉得不对劲。风机叶轮要是失衡了,整台设备就跟得了帕金森似的抖个不停。你用手背摸摸设备外壳,要是感觉一直在高频震动,或者听到“哒哒哒”的敲击声,那可能就是叶轮在喊救命啦!得注意哈,这震动强度会随着转速变快而更厉害,转速低的时候可能不太容易发现。 第二,噪音从“嗡鸣”变成“尖叫”啦!正常运转的风机就跟个老式冰箱似的,发出低沉的“嗡嗡”声。要是突然传来刺耳的“吱吱”声、金属摩擦声,甚至像破音一样的高频啸叫,那说明叶轮可能在空中抽风呢!这里有个关键细节,噪音一变,温度也会跟着升高,你小心点伸手靠近设备表面,能感觉到热得不正常。 第三,效率突然“断崖式下跌”!风机就像个挑食的小孩,要是它“吃得多,产出少”,那可能是叶轮在偷懒。你看看电流表,要是电机电流比平时高了10%以上,可风量却明显变小,那就说明叶轮在白白浪费能量。而且啊,长期这么低效运转,就跟慢性病一样,会把设备寿命给耗没了,早点处理还能省不少电费呢。 第四,轴承成了“过热警报器”!轴承就像是风机的关节,叶轮失衡了,轴承就得被迫“超负荷工作”。你用红外测温仪测测轴承那块,要是温度比环境温度高15℃以上,或者你用手背靠近感觉烫手,那可能是叶轮在拖累轴承。高温还会让润滑油老化得更快,最后轴承就得罢工啦。 第五,肉眼可见的“不对称”!叶轮转得快的时候咱不好直接看,不过停机后还是能看出问题的。你检查下叶片,看看有没有这些情况:叶片根部和轮毂连接的地方有明显缝隙,这就像人“偏头”了;某片叶片边缘磨损得厉害,或者补过之后有凹陷,就跟“瘸腿”似的;叶片材质不均匀,有铸造气泡啥的,导致局部太重,这就是“体重差异”。 要是上面这些情况都出现了,你可以来个“动态诊断”。先让风机以1/3的转速慢慢启动,看看会不会周期性晃动。再用手电筒照照旋转的叶轮,要是影子晃动幅度超过叶片厚度的1/10,赶紧停机。 记住哈,动平衡可不是等出了问题再补救,就好比给风机戴上“防抖护膝”。定期检查能让设备别从“亚健康”变成“重症患者”。下次风机发出“求救信号”,别磨蹭,说不定它就差一次精准的“平衡校正”啦!
23
2025-06
如何快速判断设备是否需要动平衡校验
如何快速判断设备是否需要动平衡校验 一、捕捉设备的”求救信号”:直接征兆的多维解读 当旋转机械发出不规则颤动时,这绝非偶然的机械”叹息”。高频振动传感器捕捉到的0.5G以上加速度波动,往往预示着转子质量分布的隐秘失衡。更值得警惕的是,振动频谱中若出现显著的工频谐波成分,这如同设备在用数学语言诉说其动态失衡的痛苦。 听觉感知同样不可小觑。当设备运转时突然混入类似金属刮擦的高频啸叫,这可能是轴承与轴颈间因不平衡力引发的异常接触。若伴随周期性”咔嗒”声,需立即排查联轴器对中偏差与动平衡失效的叠加效应。 二、解码间接信号:系统异常的连锁反应 温度监测仪显示的轴承温升超过3℃临界值时,需警惕不平衡力引发的异常摩擦生热。红外热成像仪捕捉到的局部热点分布,往往与转子质量偏心存在空间对应关系。此时应同步检查润滑油的金属磨屑含量,金属颗粒的几何形态可能揭示不平衡导致的异常磨损模式。 生产效率的神秘下滑常是动平衡失效的”沉默证人”。当电机电流表指针出现规律性摆动,或功率因数突然恶化,这可能是不平衡力矩与机械系统共振的征兆。此时需结合振动频谱分析,确认是否存在与转速相关的特征频率成分。 三、智能诊断工具的协同作战 手持式振动分析仪的频谱图中,若1X频成分占比超过70%,且存在显著的2X、3X谐波,这构成动平衡需求的初步证据。更先进的相位分析功能可揭示振动矢量的空间分布特征,当相位角波动超过±15°时,需启动动平衡校验程序。 激光对中仪的精密测量往往能发现隐藏的关联问题。若联轴器径向偏差超过0.05mm,角向偏差超过50arcsec,需同步进行对中调整与动平衡校验。此时应采用动态平衡法,将联轴器偏差对平衡质量的影响纳入计算模型。 四、决策树模型:构建科学判断流程 建立包含5个关键节点的决策树:①振动烈度是否超标(ISO 10816标准);②频谱特征是否符合不平衡故障模式;③温度/效率异常是否伴随振动加剧;④历史维修记录中是否频繁出现类似问题;⑤模态分析是否显示低阶弯曲振型参与。当满足3个以上条件时,应启动动平衡校验程序。 五、预防性维护的智慧:从被动响应到主动防御 建立设备健康档案,记录每次动平衡校验后的振动基线。采用趋势分析法,当振动幅值呈现指数级增长时,需提前进行预防性校验。对于高精度设备,建议实施周期性动平衡维护,将校验周期设定为MTBF(平均故障间隔时间)的1/3。同时推广柔性平衡技术,在线监测系统可实现不平衡量的实时补偿。 这种多维度、跨参数的综合诊断体系,犹如为设备装上”智能听诊器”。通过融合振动分析、热力学监测、生产数据关联分析,构建起立体化的动平衡需求判断模型。记住,每一次精准的动平衡校验,都是对设备寿命的延长,更是对生产连续性的庄严承诺。
23
2025-06
如何快速校正车床主轴动平衡
如何快速校正车床主轴动平衡 在机械加工领域,车床主轴的动平衡状况直接影响着加工精度和设备的使用寿命。快速而准确地校正车床主轴动平衡,是提高生产效率和产品质量的关键环节。以下将详细介绍一些有效的方法。 前期准备要充分 在进行车床主轴动平衡校正之前,细致的准备工作不可或缺。首先,需对车床主轴进行全面检查,查看是否存在磨损、裂纹等缺陷。因为这些问题可能会影响动平衡校正的效果,甚至在后续加工过程中引发更严重的故障。同时,确保主轴的安装牢固,各个连接部位紧密无松动。松动的连接会导致在旋转过程中产生额外的振动,干扰动平衡的测量和校正。另外,要清洁主轴表面,去除油污、铁屑等杂质,以保证测量设备能够准确获取数据。 此外,准备好专业的动平衡测量设备,如动平衡仪。不同的动平衡仪具有不同的精度和功能特点,要根据车床主轴的具体要求和实际情况选择合适的设备。并且,要对测量设备进行校准,确保其测量结果的准确性和可靠性。 精确测量找失衡 使用动平衡仪对车床主轴进行精确测量是校正的重要步骤。在测量时,要按照动平衡仪的操作说明进行规范操作。通常需要在主轴上安装传感器,以准确获取主轴旋转时的振动信号。将传感器安装在合适的位置,能够更精准地捕捉到振动信息。 测量过程中,要多次进行测量,取平均值以提高测量的准确性。同时,注意观察动平衡仪显示的数据和波形,分析振动的频率、幅度等参数。通过这些参数,可以判断主轴失衡的位置和程度。一般来说,振动幅度较大的方向往往对应着失衡的位置。 合理配重巧校正 根据测量结果,确定需要添加或去除的配重。配重的选择和安装位置至关重要。如果失衡较轻,可以选择较轻的配重块;如果失衡较为严重,则需要选择较重的配重块。配重块的材质和形状也要根据实际情况进行选择,以确保其能够牢固地安装在主轴上。 在安装配重块时,要严格按照计算和测量得出的位置进行安装。可以使用胶水、螺栓等方式将配重块固定在主轴上。安装过程中要确保配重块安装牢固,避免在主轴旋转过程中脱落。另外,安装完成后,要再次进行测量,检查动平衡是否得到有效改善。如果仍然存在失衡情况,需要重新调整配重块的位置或重量,直到达到满意的动平衡效果。 反复验证保效果 完成配重安装后,不能直接投入使用,需要进行反复验证。启动车床,让主轴以不同的转速运行,观察振动情况。在不同转速下,主轴的动平衡状况可能会有所不同,因此需要进行全面的测试。 使用动平衡仪再次进行测量,对比校正前后的数据。如果振动幅度明显减小,说明动平衡校正取得了良好的效果;如果仍然存在较大的振动,则需要重新检查测量和配重过程,找出问题所在并进行调整。 反复验证的过程虽然繁琐,但能够确保车床主轴在各种工况下都能保持良好的动平衡状态,从而提高加工精度和设备的稳定性。 快速校正车床主轴动平衡需要充分的前期准备、精确的测量、合理的配重和反复的验证。只有每一个环节都做到严谨细致,才能高效地完成动平衡校正,为车床的稳定运行和高质量加工提供保障。
23
2025-06
如何手工校正风扇动平衡
如何手工校正风扇动平衡 在风扇的使用过程中,动平衡问题至关重要。当风扇动平衡不佳时,会产生振动和噪音,降低风扇的使用寿命,甚至影响整个系统的性能。虽然动平衡机是校正风扇动平衡的常用设备,但在某些情况下,我们可能需要手工校正。下面将为大家详细介绍手工校正风扇动平衡的方法。 准备工作 要进行手工校正风扇动平衡,首先得做好充分准备。需要准备一些常用工具,如卡尺、百分表、扳手、平衡块等。卡尺用于精确测量风扇的尺寸,百分表则能精准检测风扇的跳动情况。扳手用来拆卸和安装风扇的零部件,而平衡块是校正动平衡的关键材料。此外,清洁风扇也是必不可少的步骤。用干净的布擦拭风扇叶片和轮毂,去除表面的灰尘、油污等杂质。这些杂质可能会影响风扇的动平衡,导致校正不准确。同时,仔细检查风扇的叶片是否有损坏、变形等情况。若叶片存在损坏,应及时更换,以免影响校正效果。 初步检测 完成准备工作后,接下来要对风扇进行初步检测。将风扇安装在一个平稳的轴上,确保风扇能够自由转动。然后,用手轻轻转动风扇,观察其转动情况。若风扇转动不平稳,出现明显的晃动或卡顿,这就表明风扇存在动平衡问题。此时,使用百分表测量风扇的径向跳动和轴向跳动。径向跳动是指风扇在旋转过程中,叶片尖端相对于轴心的跳动量;轴向跳动则是指风扇在轴向方向上的跳动量。通过测量这两个参数,可以准确了解风扇的动平衡状况。 确定不平衡位置 根据初步检测的结果,确定风扇不平衡的大致位置。一般来说,风扇的不平衡位置通常出现在叶片较重的一侧。可以在风扇的叶片上做好标记,以便后续进行校正。为了更精确地确定不平衡位置,可以采用试加平衡块的方法。在风扇的叶片上选择一个位置,粘贴一个小的平衡块,然后再次转动风扇,观察其转动情况。如果风扇的转动变得更平稳,说明平衡块的位置接近不平衡位置;如果风扇的转动反而更不稳定,那么就需要调整平衡块的位置,重新进行测试。反复进行这个过程,直到找到风扇不平衡的准确位置。 校正不平衡 确定不平衡位置后,就可以进行校正了。根据不平衡的程度,选择合适的平衡块。平衡块的重量应根据风扇的大小和不平衡程度来确定。将平衡块粘贴或焊接在风扇叶片的较轻一侧,以增加该侧的重量,从而达到平衡的目的。在粘贴或焊接平衡块时,要确保平衡块牢固地固定在叶片上,避免在风扇运转过程中脱落。校正完成后,再次转动风扇,检查其动平衡情况。如果风扇的转动仍然不平稳,可以重复上述步骤,继续调整平衡块的位置和重量,直到风扇转动平稳为止。 最终检测 完成校正后,还需要进行最终检测。使用动平衡仪对风扇进行精确测量,确保风扇的动平衡指标符合要求。动平衡仪能够准确测量风扇的不平衡量和不平衡位置,并给出相应的校正建议。如果风扇的动平衡指标不符合要求,需要再次进行校正,直到达到标准为止。同时,在风扇正常运转一段时间后,再次检查其动平衡情况。因为在风扇运转过程中,平衡块可能会因为振动等原因而松动或移位,导致动平衡再次出现问题。所以,定期检查风扇的动平衡是非常必要的。 手工校正风扇动平衡需要耐心和细心,每一个步骤都要认真对待。通过以上方法,可以有效地校正风扇的动平衡,提高风扇的运行稳定性和可靠性,延长风扇的使用寿命。