

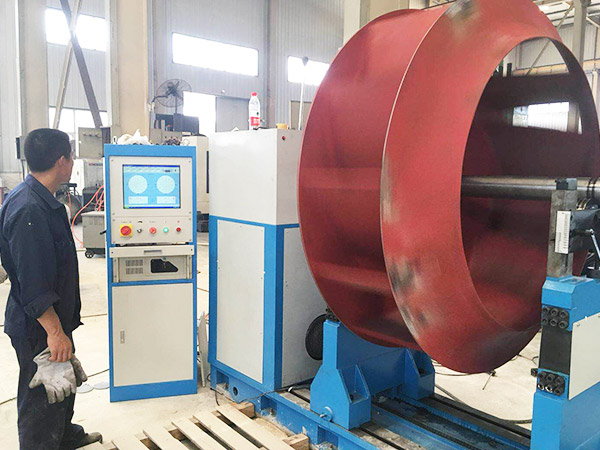
风机叶轮动平衡标准值是多少
风机叶轮的动平衡标准值会因不同的应用、设计要求和行业标准而有所不同。一般来说,动平衡标准值取决于以下几个因素:应用类型: 不同类型的风机在不同的应用环境下需要满足不同的动平衡标准。例如,一般的工业风机和空调风机的要求可能会不同。运行速度: 风机叶轮的运行速度会直接影响不平衡对振动的影响。高速运行的叶轮可能需要更严格的动平衡标准。精度要求: 一些应用对振动的容忍度比较低,因此对动平衡的要求也会更为严格。行业标准: 不同行业可能有各自的标准和规范,这些标准通常会提供关于动平衡的指导和要求。一般来说,在工业领域,风机叶轮的动平衡标准值通常以单位质量不平衡量(g.mm/kg 或 g.cm/kg)来表示。具体的标准值可能会因不同情况而有所不同,但以下是一个大致的参考范围:对于一般工业风机,通常的动平衡标准值可能在 1 g.mm/kg 至 10 g.mm/kg 之间。对于某些精密应用,要求更高的风机,动平衡标准值可能在 0.5 g.mm/kg 以下。请注意,这只是一个粗略的参考范围,实际应用中应该根据具体情况和适用的行业标准来确定风机叶轮的动平衡标准值。在进行动平衡操作时,建议遵循相关的国家和行业标准,以确保风机在运行过程中达到合适的振动水平。
19
2025-06
飞轮平衡机的主要用途是什么
各位机械小迷们!你们知道吗,在机械的世界里,有个默默发光发热的“小能手”——飞轮平衡机。这小家伙到底有啥主要用途呢?咱们今天就来一探究竟! 首先,它能让机械稳稳当当运行。就拿汽车发动机里的飞轮来说,要是它不平衡,发动机运转起来就跟人走路一瘸一拐似的,晃得厉害。而飞轮平衡机就像个火眼金睛的侦探,能精准找出飞轮的不平衡点,然后“妙手回春”,让飞轮乖乖平稳转动。这样一来,发动机工作时稳稳的,震动和噪音都小了。不光汽车发动机,工业设备里的飞轮,经过平衡机这么一调整,整个设备运行起来那叫一个丝滑,效率蹭蹭往上涨! 其次,这玩意儿还能给机械部件“续命”。不平衡的飞轮高速转动时,会像个调皮捣蛋的孩子,对相连的部件产生额外的冲击力,这冲击力就像个无形的“杀手”,加速部件的磨损和损坏。但有了飞轮平衡机,把飞轮调整到平衡状态,就能大大减轻这种冲击力,部件受到的损害也就小了。就说大型电机设备吧,要是飞轮不平衡,里面的轴承等部件很快就会因为过度磨损“罢工”。可经过平衡机处理后,这些部件的使用寿命能延长好多,能给企业省不少换部件的钱呢! 再者,它对提升产品质量也有大功劳。在制造业里,好多产品的性能都跟飞轮的平衡度紧密相连。像精密的仪器设备,哪怕飞轮有一丁点儿不平衡,都可能影响整个产品的精度和稳定性。而飞轮平衡机就像个超级魔法师,对飞轮进行精确调整,让产品达到更高的质量标准。这样生产出来的产品,在市场上那就是“香饽饽”,能赢得消费者的信任! 另外,它还是安全的“守护者”。在一些高速运转的机械中,不平衡的飞轮就像个定时炸弹,可能会引发严重的安全事故。要是飞轮因为不平衡突然破裂或者脱落,那后果简直不敢想。比如航空发动机里的飞轮,要是不平衡,飞机飞行时出问题,那可是会危及乘客生命安全的。而飞轮平衡机通过确保飞轮的平衡,就像给人们的生命和财产安全上了一把坚固的锁! 总的来说,飞轮平衡机虽然看起来就是个小机器,但它的用途那叫一个广泛又重要。它在保障机械运行、延长部件寿命、提升产品质量和保障安全等方面都发挥着不可或缺的作用,简直就是机械领域里的大“功臣”!大家说,这小机器牛不牛?
19
2025-06
飞轮平衡机的工作原理是怎样的
各位工业小达人们!今天咱来聊聊飞轮平衡机的工作原理,那叫一个神奇! 想象一下,一枚旋转的硬币,立得直直的时候转得可优雅了,一旦歪了就开始晃,然后“啪叽”一下就倒了。这就跟飞轮的平衡问题差不多。工业设备里的飞轮啊,就像个高速旋转的“能量舞者”,哪怕就那么一丢丢的重量偏差,都能让它剧烈振动。轻一点呢,就是让机械寿命缩短,严重起来可就会引发大事故,那场面,简直就是灾难片现场!而飞轮平衡机就是解决这个问题的“精准裁判”。 这平衡机是咋破解飞轮失衡问题的呢?分三步! 第一步是动态扫描。平衡机就像给飞轮做“旋转CT”,传感器每秒能捕捉几百次的振动数据。飞轮一转,不平衡的地方就会像心跳一样有规律地波动,这些数据最后会变成能看到的波形图。 第二步是智能定位。算法就像个经验丰富的侦探,通过波形图的“指纹”就能找到失衡的位置。现在的先进设备还能同时找出好几个失衡的地方,就像一下子发现好多漏水点的管道检测仪。 第三步是精准修正。这修正的过程可太有工匠精神了!有的是在指定的地方钻孔来减轻重量,有的就跟给蛋糕抹奶油似的加上配重块。现在最新的技术都能用激光雕刻来减重,精度能达到0.01克,厉害得很! 早期的平衡机就像个笨笨的“机械天平”,还得人工去标记平衡点。但现在的智能平衡机可进化了,有好多“超能力”!它能做预测性诊断,通过振动频率能提前三个月知道会不会失衡;还能远程操控,工程师在办公室就能给千里之外的飞轮做平衡校准;甚至还会自适应学习,能根据设备的使用情况自动调整平衡标准,就像给不同的舞蹈定制演出服。 在德国的一个汽车工厂,平衡机的操作界面会用彩虹色的光带来显示平衡程度,绿色代表完美,红色就是危险警告。这把技术参数变成能看到的东西,让冷冰冰的机械校准变成了充满艺术感的“工业芭蕾”。 未来的AI平衡系统更牛,能像医生看片子一样分析振动数据,还能根据设备老化的程度提前知道失衡的趋势。有个航天项目还试验了“自修复飞轮”,一旦检测到失衡,里面的微型机械臂就会自动调整配重块的位置。这可不光是技术上的突破,简直就是让机械有了生命,太有想象力了! 从蒸汽机时代的铜制飞轮,到现在的碳纤维复合材料飞轮,平衡机一直都是工业心脏的“节拍器”。它用特别高的精度保证每台设备都能稳稳地运转,让机械世界的节奏一直都安全又稳定。你们说,这飞轮平衡机是不是超厉害?
19
2025-06
飞轮平衡机的精度标准如何判断
各位工业小达人们!你们知道吗,在工业生产里,飞轮平衡机那可是个超级重要的设备,就像游戏里的神装一样,能让飞轮运转得杠杠的。但问题来了,怎么判断这飞轮平衡机的精度标准呢?下面咱就好好唠唠。 先看平衡效果。判断飞轮平衡机精度,最直接的就是看它平衡飞轮的效果咋样。要是一台平衡机平衡后的飞轮震动小,转起来稳稳的,像个老司机开车一样稳,那这台平衡机精度肯定不错。要是平衡后的飞轮还晃来晃去,像喝醉了酒似的,那精度指定不行。比如说汽车发动机里的飞轮,要是平衡不好,发动机就抖得厉害,噪音还大,开车体验就跟坐过山车似的,超难受。所以咱可以观察飞轮平衡后的运转状态,感受震动情况,也可以用震动测试仪这些小工具,更准确地判断。 再瞧瞧重复精度。一台好的飞轮平衡机,每次平衡飞轮的结果得差不多。就像神枪手每次射击都能打在差不多的位置。要是一台平衡机今天平衡这个飞轮精度高,明天平衡同样规格的飞轮却差得十万八千里,那它的可靠性就堪忧了。咱可以找几个相同规格的飞轮,让平衡机依次平衡,然后对比结果。要是偏差小,说明这台平衡机重复精度高,精度标准更可靠。 测量精度也不能忽略。飞轮平衡机工作时会测量飞轮各项数据,这些数据准不准直接关系到平衡精度。这就像盖房子,地基都测不准,房子能盖好才怪呢。测量精度和平衡机的传感器、测量系统有关。好的传感器能更精准地捕捉飞轮信息,测量系统也能更好地处理信息。我们可以用已知参数的标准飞轮检验测量精度,看看测量数据和标准数据差距大不大。差距小,说明测量精度高,平衡机精度标准更有保障。 另外,看看平衡时间。一般来说,精度高的飞轮平衡机平衡速度也快。它能快速准确找到飞轮不平衡点,然后调整。要是一台平衡机平衡一个飞轮要老半天,可能是它算法不行,或者处理信息能力有限。不过,平衡时间也不能只图快,要是为了快牺牲了平衡质量,那就赔了夫人又折兵。我们要在保证平衡精度的前提下,看看平衡时间合不合理。可以多测试几台不同的平衡机,对比它们平衡相同飞轮的时间和精度,找那个又快又准的“学霸”。 最后,听听用户评价。用过飞轮平衡机的人最有发言权。他们在实际使用中遇到各种情况,对精度有更直观的感受。我们可以在行业论坛、社交群组里和其他用户交流,听听他们对不同品牌、不同型号平衡机的评价。他们会分享使用经验,包括遇到的问题、精度表现等。通过这些真实的用户反馈,我们能更全面了解平衡机的精度标准,为判断提供参考。 其实啊,判断飞轮平衡机的精度标准不能只看一方面,要从平衡效果、重复精度、测量精度、平衡时间等多个角度综合考虑,再结合其他用户的评价,这样才能选到精度高、性能好的飞轮平衡机,让它好好为咱们的生产服务!
19
2025-06
飞轮平衡机精度标准及影响因素
飞轮平衡机精度标准及影响因素 一、精度标准:在混沌中寻找秩序的标尺 飞轮平衡机的精度标准如同精密仪器的”灵魂刻度”,其核心在于量化旋转体的动态失衡。国际标准ISO 1940-1将平衡精度划分为G0.4至G4000共12个等级,其中G0.4代表每克毫米(g·mm)的不平衡量不超过0.4。这一标准看似冰冷,实则暗含深意:当飞轮转速突破10000rpm时,0.1g·mm的误差足以引发共振灾难。 美国石油学会API 617则针对离心压缩机飞轮提出特殊要求,规定残余不平衡量不得超过原始质量的0.1%。这种行业定制化标准的出现,折射出平衡精度的”场景化生存法则”——航天器陀螺仪的平衡误差需控制在微米级,而工业汽轮机飞轮的容忍度可放宽至毫米级。 二、影响因素:蝴蝶效应的微观战场 机械系统的”多米诺骨牌” 轴承刚度每降低10%,平衡精度可能衰减20%。某航空发动机测试案例显示,当主轴热变形量超过0.02mm时,平衡结果产生15%的系统性偏差。这种”毫米级误差引发厘米级灾难”的连锁反应,揭示了机械结构的脆弱性。 环境变量的”隐形推手” 温度梯度每升高1℃,铝合金飞轮的热膨胀系数可达23×10⁻⁶/℃,相当于在1米长度上产生0.23mm的形变。某风电场实测数据显示,环境振动超过0.5g时,平衡机的相位检测误差会呈指数级增长。 操作艺术的”量子纠缠” 操作者对校准基准的选择直接影响精度。采用”三点支撑法”时,支撑点间距误差0.1mm会导致重心计算偏差0.5%。更微妙的是,传感器安装角度的1°偏差,可能使矢量合成产生10%的误差。 三、破局之道:在不确定中重构确定性 智能补偿算法的”时空折叠” 某新型平衡机引入卡尔曼滤波器,通过实时采集128个频点数据,将环境振动干扰降低至0.05g以下。这种动态补偿机制如同给机械系统装上”数字免疫系统”,使精度稳定性提升300%。 多传感器融合的”感官革命” 结合激光干涉仪(精度0.1μm)与压电传感器(频响10Hz-10kHz)的复合检测方案,成功突破传统单传感器的”感知盲区”。某航天项目验证显示,该方案使平衡效率提升40%,同时将残余不平衡量控制在G0.1等级。 材料基因的”分子级驯化” 采用梯度功能材料(FGM)制造平衡机主轴,其热膨胀系数差异被控制在±0.5×10⁻⁶/℃。这种”材料自平衡”设计使温度补偿需求降低70%,开创了结构设计的新范式。 四、未来图景:平衡精度的量子跃迁 当量子陀螺仪的角分辨率突破10⁻⁶°/小时,当数字孪生技术实现1:1虚拟平衡验证,飞轮平衡机或将进入”预测性平衡”时代。某实验室已实现基于机器学习的残余不平衡量预测,其准确度达到98.7%,预示着从”被动修正”到”主动预防”的范式革命。 在这场精度与混沌的永恒博弈中,飞轮平衡机不仅是机械的校准工具,更成为人类对抗不确定性的智慧结晶。从微米级的误差控制到系统级的稳定性保障,每一次技术突破都在重写着”完美平衡”的定义。
19
2025-06
飞轮平衡机适用于哪些行业
各位机械小达人们,你们知道吗?生活中很多地方都离不开飞轮平衡机,它就像个超级隐形英雄,默默在各个行业发光发热! 先说说汽车制造。在汽车工厂那轰隆隆的环境里,飞轮平衡机就像一位闷声不响的质检员。它专门检测发动机曲轴、涡轮增压器叶片的平衡状态,能保证每台新车启动时的震颤小得可怜,不超过0.01毫米。要是没有它,你那心爱的车在高速行驶时,估计就跟跳迪斯科似的,晃得你头晕眼花! 再看看航空航天领域。火箭发动机的涡轮泵、卫星太阳能板的旋转支架,这些可都是价值千万的宝贝,得在真空环境下零误差运转。飞轮平衡机就厉害啦,它用激光传感器能捕捉到0.001克的重量偏差,让宇航员的太空之旅稳稳当当,就像在公园里悠闲散步一样从容。 家电生产里,飞轮平衡机是洗衣机的静音魔术师。当你舒舒服服享受滚筒洗衣机轻柔转动的时候,它早就已经在流水线上施了魔法。它通过模拟不同衣物重量,校准电机轴的平衡,能把洗衣机那刺耳的“嗡嗡”声变成悦耳的“沙沙”白噪音,就像给洗衣机戴上了静音耳塞。 建筑工地的重型机械也离不开它。挖掘机的液压马达每分钟能转上千次呢,飞轮平衡机通过“动态离心力测试”,能让这些钢铁巨兽的关节转动得像天鹅展翅一样优雅,避免因为振动让零件提前“光荣下岗”。 轨道交通方面,高铁轮对要是有0.05毫米的平衡偏差,就可能引发“哐当”异响。飞轮平衡机用磁悬浮技术模拟350公里时速的离心力,给每对轮对开“健康诊断书”,让中国高铁跑得又稳又安静,就像风一样悄悄掠过。 医疗器械里,达芬奇手术机器人那可是关乎生死的,0.1毫米的误差都不行。飞轮平衡机为机械臂关节进行“纳米级平衡校准”,能确保机械手指在血管缝合时,稳得就像外科医生那双经验丰富的手。 农业机械里,联合收割机在金黄的麦田里干活,滚筒每分钟能转300次。飞轮平衡机通过“三维振动分析”,把脱粒滚筒的震颤幅度控制在发丝直径的1/10,不让谷粒在空中“逃之夭夭”,就像给谷粒们安了个安全罩。 健身器材里,高端跑步机的减震系统就藏着飞轮平衡机的智慧。它通过模拟不同体重用户的冲击力,校准跑带驱动轴的平衡,能让跑者在20公里/小时的速度下,膝盖承受的冲击力减少40%,就像给膝盖加了个缓冲垫。 印刷设备里,高速印刷机每小时能打印10万张纸,要是纸张边缘有微小卷曲,就可能卡纸。飞轮平衡机通过“谐波振动分析”,让滚筒转动时的波动频率和纸张特性完美匹配,确保每张纸都像芭蕾舞者一样优雅地通过,就像给纸张安排了一场完美的舞蹈演出。 新能源领域,风力发电机就像草原上的白色巨人。飞轮平衡机为长达60米的叶片进行“动态平衡校准”,能让每片叶片在12米/秒的风速下,像海鸥的翅膀一样精准捕捉风能,把能量损耗控制在0.3%以内,就像给风力发电机装了个高效能量捕捉器。 真的是,从深海钻井平台的旋转钻头,到航天飞机的燃料泵,飞轮平衡机正以毫米级的精度重塑工业世界。它可不只是个检测机械平衡的工具,更是现代制造业“零缺陷”理念的践行者,用0.001克的重量校准,守护着价值亿万的工业奇迹!大家说说,这飞轮平衡机是不是超级厉害呢?
19
2025-06
飞轮自动平衡机价格区间是多少
飞轮自动平衡机价格区间是多少?——解构精密制造背后的成本密码 一、价格区间全景扫描 在精密机械制造领域,飞轮自动平衡机如同工业心脏的校准师,其价格波动曲线折射出技术迭代的深层逻辑。基础型设备以15-30万元区间构筑市场基底,这类机型多采用模块化设计,适用于中小型电机转子的常规校正。当精度需求突破0.1g·mm阈值,价格旋即跃升至50-80万元区间,此时设备开始搭载激光动态检测系统与闭环控制算法。而面向航空航天领域的超精密机型,则以120-300万元的身价占据技术制高点,其核心部件往往需要定制化开发。 二、成本构成的多维透视 价格差异犹如精密齿轮的咬合,每个环节都暗藏价值密码。传感器阵列的配置差异可导致15%的成本波动,德国进口的压电式传感器较国产型号溢价达300%。驱动系统的选择更构成价格断层,伺服电机与步进电机的效能差价可达45万元。软件算法的价值常被低估,智能补偿算法的专利授权费就占总价的18%-25%。这些技术要素的组合排列,最终拼凑出令采购方既兴奋又焦虑的价格图谱。 三、市场定位的博弈艺术 在价格与性能的天平上,不同玩家演绎着差异化生存策略。国产设备通过模块化设计实现成本压缩,将基础机型控制在20万元红线内,但牺牲了30%的检测效率。进口品牌则以全生命周期成本为卖点,虽然初期投入高出60%,却能降低25%的维护成本。租赁模式的兴起更打破传统定价逻辑,某头部企业推出的”按校正量计费”方案,使单次平衡成本降至传统模式的1/5。 四、选购决策的破局之道 面对价格迷宫,采购方需建立三维评估坐标系。技术参数层面,应关注不平衡量检测下限与转速范围的匹配度;经济维度需核算设备折旧周期与产能提升的平衡点;战略层面更要考量智能化升级对产线迭代的支撑作用。某新能源车企的采购案例极具启示:通过引入带AI预测维护功能的平衡机,虽增加15%初期投入,却使设备综合效率(OEE)提升至92%,投资回收期缩短至14个月。 五、未来价格曲线的变数 技术革命正在重塑价值评估体系。数字孪生技术的渗透使虚拟调试成本占比攀升至35%,而5G远程运维服务则可能催生新的定价模型。值得关注的是,碳纤维复合材料在飞轮本体的应用,或将倒逼平衡机开发新型检测算法,这种技术链的蝴蝶效应可能引发新一轮价格洗牌。当工业4.0的浪潮席卷而来,价格谈判桌上的筹码,终将演变为数据资产与算法能力的较量。 (注:本文价格数据基于2023年中国市场调研,实际报价需结合具体配置与服务方案)
19
2025-06
飞轮自动平衡机的工作原理是什么
飞轮自动平衡机的工作原理是什么 在现代工业生产中,飞轮作为许多机械设备的重要部件,其平衡性能直接影响到设备的运行稳定性和使用寿命。飞轮自动平衡机就是专门用于检测和校正飞轮平衡的关键设备,那么它的工作原理是什么呢? 基本概念 要理解飞轮自动平衡机的工作原理,首先要了解动平衡的概念。在旋转机械中,由于材料不均匀、加工误差、装配不当等原因,旋转部件的质量分布往往不均匀,这会导致旋转时产生离心力。这些离心力会使设备产生振动、噪声,降低设备的精度和寿命。动平衡就是通过在旋转部件上增加或减少一定的质量,使旋转部件的质量分布均匀,从而减少离心力的产生。 检测原理 飞轮自动平衡机主要由驱动系统、支承系统、测量系统和校正系统等部分组成。其检测过程基于力学原理和传感器技术。当飞轮被驱动系统带动旋转时,由于不平衡质量产生的离心力会使飞轮产生振动。支承系统将飞轮支撑起来,并将振动传递给测量系统。 测量系统是平衡机的核心部分,它通常由加速度传感器、光电传感器等组成。加速度传感器用于测量飞轮振动的加速度信号,光电传感器用于测量飞轮的转速和相位信息。通过对这些信号的采集和分析,测量系统可以准确地确定飞轮不平衡质量的大小和位置。 具体来说,当飞轮旋转时,加速度传感器会检测到由于不平衡质量产生的振动信号。这些信号经过放大、滤波等处理后,被传输到计算机控制系统。计算机控制系统根据预设的算法,对振动信号进行分析,计算出不平衡质量的大小和相位。同时,光电传感器会测量飞轮的转速和相位信息,为不平衡质量的定位提供参考。 校正原理 在确定了飞轮不平衡质量的大小和位置后,校正系统会对飞轮进行校正。校正系统通常采用去重或加重的方法来平衡飞轮。去重法是通过钻孔、铣削等方式,在飞轮的不平衡位置去除一定的质量;加重法是在飞轮的平衡位置添加一定的质量块。 在实际应用中,去重法更为常见。校正系统根据测量系统提供的信息,自动控制刀具或钻头等工具,在飞轮的不平衡位置进行精确的去重操作。例如,计算机控制系统会根据不平衡质量的大小和位置,控制刀具的进给量和切削深度,确保去除的质量正好能够抵消不平衡质量。 在去重过程中,平衡机会不断地对飞轮进行检测和校正,直到飞轮的不平衡量达到规定的标准为止。这个过程通常是自动完成的,大大提高了平衡效率和精度。 优势与应用 飞轮自动平衡机具有高精度、高效率、自动化程度高等优点。它可以快速准确地检测和校正飞轮的不平衡量,提高飞轮的平衡质量,从而提高机械设备的运行稳定性和可靠性。 飞轮自动平衡机广泛应用于汽车、航空航天、船舶、电力等行业。在汽车发动机中,飞轮的平衡性能直接影响到发动机的动力输出和振动噪声。通过使用飞轮自动平衡机对飞轮进行精确的平衡处理,可以提高发动机的性能和舒适性。在航空航天领域,飞轮的平衡精度要求更高,因为微小的不平衡量都可能导致飞行器的振动和不稳定。飞轮自动平衡机可以满足这些高精度的平衡需求,确保航空航天设备的安全运行。 综上所述,飞轮自动平衡机通过先进的检测技术和校正方法,实现了对飞轮不平衡质量的快速准确检测和校正。其工作原理基于力学、传感器技术和计算机控制技术,为现代工业生产提供了重要的保障。随着科技的不断进步,飞轮自动平衡机的性能和精度将不断提高,应用范围也将更加广泛。
19
2025-06
飞轮自动平衡机的测试方法步骤
飞轮自动平衡机的测试方法步骤 在机械制造和维修领域,飞轮作为一种储存和释放能量的关键部件,其平衡性能直接影响着整个设备的稳定性和使用寿命。飞轮自动平衡机能够快速、准确地检测和校正飞轮的不平衡量,下面为您详细介绍其测试方法步骤。 测试前的准备工作 在正式开始测试之前,务必做好充分的准备工作。首先,要对飞轮进行全面的清洁,去除表面的油污、灰尘以及其他杂质。这些异物可能会干扰平衡机的检测精度,导致测试结果出现偏差。同时,仔细检查飞轮的外观,查看是否存在裂纹、磨损等缺陷。如果发现有明显的损伤,应及时进行修复或更换,以免影响测试的准确性和后续的使用安全。此外,要确保平衡机处于良好的工作状态,对其进行必要的检查和调试。检查设备的电源是否正常,各个部件是否连接牢固,传感器是否灵敏等。只有在确认平衡机一切正常的情况下,才能进行后续的测试工作。 飞轮的安装与校准 将清洁好且无缺陷的飞轮小心地安装到平衡机的主轴上。在安装过程中,要严格按照平衡机的操作手册进行操作,确保飞轮安装牢固,避免在测试过程中出现松动或晃动的情况。安装完成后,需要对平衡机进行校准。这一步骤至关重要,它直接关系到测试结果的准确性。通过调整平衡机的相关参数,使其适应飞轮的尺寸、重量等特性。可以使用标准的校准件对平衡机进行校准,确保设备能够准确地测量飞轮的不平衡量。在校准过程中,要仔细观察平衡机的显示数据,根据数据的变化进行相应的调整,直到校准完成。 初始数据的采集 启动平衡机,让飞轮以较低的转速开始运转。在这个过程中,平衡机的传感器会实时采集飞轮的振动数据。这些数据包含了飞轮在旋转过程中的各种信息,如振动的幅度、频率等。通过对这些数据的分析,能够初步判断飞轮是否存在不平衡的情况。在采集数据时,要确保飞轮的转速稳定,避免转速的波动对数据采集造成影响。同时,要记录下飞轮的初始转速、振动幅度等关键数据,以便后续的分析和比较。 不平衡量的测量与分析 当飞轮达到稳定的测试转速后,平衡机将对飞轮的不平衡量进行精确测量。此时,平衡机的软件系统会对采集到的数据进行深入分析,确定不平衡量的大小和位置。通过先进的算法和技术,能够快速、准确地计算出飞轮在不同平面上的不平衡量。根据测量和分析的结果,判断飞轮的不平衡程度是否在允许的范围内。如果不平衡量超出了规定的标准,就需要进行相应的校正。 校正与再次测试 根据不平衡量的测量结果,选择合适的校正方法对飞轮进行校正。常见的校正方法有去重法和加重法。去重法是通过去除飞轮上的部分材料来减少不平衡量,而加重法则是在飞轮的特定位置添加配重块来平衡飞轮。在进行校正时,要严格按照校正方案进行操作,确保校正的精度和效果。校正完成后,再次启动平衡机对飞轮进行测试。这次测试的目的是验证校正的效果,检查飞轮的不平衡量是否已经降低到允许的范围内。如果测试结果仍然不符合要求,需要重新进行分析和校正,直到飞轮的平衡性能达到标准为止。 测试结果的记录与报告 在完成整个测试过程后,要对测试结果进行详细的记录。记录的内容包括飞轮的基本信息、初始数据、不平衡量的测量结果、校正方法和参数以及最终的测试结果等。这些记录不仅可以作为飞轮质量的重要依据,还可以为后续的维护和管理提供参考。同时,根据记录的数据生成详细的测试报告。报告中应包括测试的目的、方法、结果以及结论等内容。测试报告要清晰、准确地反映飞轮的平衡性能,为用户提供可靠的决策依据。 通过以上详细的测试方法步骤,能够确保飞轮自动平衡机准确地检测和校正飞轮的不平衡量,提高飞轮的平衡性能,为机械设备的稳定运行提供有力保障。在实际操作过程中,要严格遵守操作规程,不断积累经验,以提高测试的准确性和效率。
19
2025-06
飞轮自动平衡机的维护注意事项有哪些
飞轮自动平衡机的维护注意事项有哪些 一、环境控制:对抗无形杀手的持久战 在精密仪器的世界里,温度与湿度如同隐形的刀锋,时刻威胁着飞轮自动平衡机的健康。设备运行时,金属部件因摩擦产生的热能与环境温差形成”热胀冷缩”的拉锯战,可能导致传感器偏移或传动轴变形。建议将车间温度控制在18-25℃区间,湿度维持在40%-60%RH,必要时启用工业除湿机或恒温系统。更需警惕的是,雨季空气中的导电性微粒可能潜入电路板缝隙,建议每月用压缩空气进行防尘罩内部除尘。 二、润滑管理:机械关节的”生命之泉” 润滑系统犹如设备的血液循环系统,其维护需遵循”精准给量,科学配比”的黄金法则。主轴轴承应选用ISO VG 68#抗磨液压油,注油量需严格控制在观察窗1/2-2/3刻度。特别注意传动齿轮箱的润滑周期,当油液呈现褐色絮状物或金属碎屑时,必须立即更换。值得警惕的是,某些操作员为图省事连续使用未过滤的旧油,这种行为将导致轴承寿命缩短40%以上。 三、传感器校准:数字世界的”视力矫正” 振动传感器的漂移误差每增加0.1mm/s,可能导致平衡精度下降15%。建议建立三级校准制度:日常用标准信号发生器进行快速校验,每周用激光干涉仪进行全量程校准,季度送检国家计量机构。特别注意加速度传感器的安装面清洁度,任何0.01mm的安装误差都会引发虚假振动信号。建议采用磁性表座配合红丹粉检测法,确保接触面贴合度达到95%以上。 四、定期解体检修:拆解中的智慧洞察 每季度的强制性解体检修是发现潜伏故障的”X光机”。重点检查气动卡盘的密封圈是否有龟裂纹路,传动皮带的齿形磨损是否超过0.3mm。值得深究的是,某些看似正常的零件可能隐藏致命缺陷——比如平衡机主轴的锥度误差,需用千分表配合V型块进行双向测量。建议建立零件寿命预测模型,对易损件实施预防性更换。 五、数据记录与分析:从经验到科学的跨越 维护日志不应是简单的”正常/异常”二元记录,而应构建包含20+参数的多维数据库。建议采用PDCA循环进行数据分析:当发现某批次产品平衡精度波动超过±0.5g时,需追溯前72小时的环境温湿度、润滑记录、传感器校准数据。更前沿的做法是引入机器学习算法,通过振动频谱分析预判轴承剩余寿命,将被动维护升级为主动预测。 结语:维护哲学的升华 真正的维护大师懂得在机械规律与人文智慧间寻找平衡点。当操作员能从油渍的分布形态预判故障,当工程师能通过金属疲劳声纹判断剩余寿命,当管理者将预防性维护成本纳入全生命周期核算——这时,飞轮自动平衡机便不再是冰冷的金属堆砌,而是流淌着精密维护艺术的生命体。记住:每一次规范操作都在延长设备的”机械寿命”,而每一次创新维护都在拓展技术的”可能性边界”。
19
2025-06
马达专用大型动平衡机价格多少
马达专用大型动平衡机价格多少?——解构工业精密仪器的定价密码 一、技术参数:价格波动的底层逻辑 马达专用大型动平衡机的定价如同精密齿轮的咬合,其价格区间往往与技术参数形成动态博弈。国际品牌设备的转速范围若突破12000rpm,价格可能瞬间跃升至300万元级别;而承载能力每增加500kg,成本曲线会呈现指数级上扬。测量精度达到0.1μm的机型,其传感器阵列与算法模块的组合成本,足以抵得上三台基础款设备的总和。 二、市场因素:价格博弈的多维战场 在品牌溢价维度,德国进口设备常以”技术垄断”为筹码,将基础款标价锚定在180-220万元区间。而国产头部厂商通过模块化设计,将同性能机型压缩至80-120万元区间。采购渠道的选择犹如走钢丝——直销模式虽能砍掉15%的代理溢价,但需承担长达6个月的定制周期风险。某华东电机厂的采购案例显示,选择代理商渠道虽多支付12万元,却换来了48小时的紧急交付保障。 三、隐性成本:价格迷雾中的暗礁 安装调试费用常被低估,某重载机型的现场校准服务报价单显示,包含激光对刀仪租赁、真空环境模拟等项目的费用,竟占设备总价的18%。维护成本的计算公式更令人咋舌:每运行1000小时需更换的进口轴承组,单价可达7.8万元。某上市公司三年运维数据显示,培训支持费用在总成本中的占比呈现逐年递增趋势,从首年的3%攀升至第五年的11%。 四、行业趋势:价格重构的未来图景 智能化浪潮正在改写定价规则,配备AI自适应算法的机型,其溢价空间已达传统机型的2.3倍。模块化设计带来的价格弹性值得关注,某新型号通过可扩展的测量臂系统,使基础款与顶配款的价差从150万元收窄至68万元。行业白皮书预测,2025年国产设备的性价比拐点将至,届时万元级转速的机型有望突破100台/年的装机量。 五、选购策略:价格迷局的破局之道 建立参数优先级矩阵是破局关键,某军工项目组通过将振动分析频段需求从20kHz降至15kHz,成功将预算控制在140万元红线内。比价策略需突破传统维度,某采购团队通过对比设备的MTBF(平均无故障时间)数据,发现某品牌虽单价高12%,但全生命周期成本反而低19%。服务条款的博弈同样关键,某跨国企业谈判案例显示,将三年免费保修升级为五年全包服务,仅需追加8.7%的预算。 结语:价格背后的工业诗学 当我们在谈论动平衡机价格时,本质上是在丈量制造业精密化的进程。从德国精密机械的百年积淀,到中国智造的弯道超车,每一道价格标签都镌刻着技术演进的年轮。未来的定价体系必将走向多维解构,那些能精准平衡技术参数、服务价值与创新溢价的厂商,终将在工业4.0的浪潮中书写新的价格法则。