

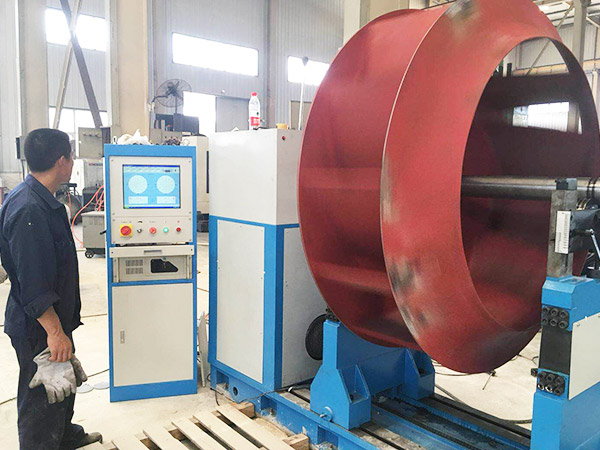
风机叶轮动平衡标准值是多少
风机叶轮的动平衡标准值会因不同的应用、设计要求和行业标准而有所不同。一般来说,动平衡标准值取决于以下几个因素:应用类型: 不同类型的风机在不同的应用环境下需要满足不同的动平衡标准。例如,一般的工业风机和空调风机的要求可能会不同。运行速度: 风机叶轮的运行速度会直接影响不平衡对振动的影响。高速运行的叶轮可能需要更严格的动平衡标准。精度要求: 一些应用对振动的容忍度比较低,因此对动平衡的要求也会更为严格。行业标准: 不同行业可能有各自的标准和规范,这些标准通常会提供关于动平衡的指导和要求。一般来说,在工业领域,风机叶轮的动平衡标准值通常以单位质量不平衡量(g.mm/kg 或 g.cm/kg)来表示。具体的标准值可能会因不同情况而有所不同,但以下是一个大致的参考范围:对于一般工业风机,通常的动平衡标准值可能在 1 g.mm/kg 至 10 g.mm/kg 之间。对于某些精密应用,要求更高的风机,动平衡标准值可能在 0.5 g.mm/kg 以下。请注意,这只是一个粗略的参考范围,实际应用中应该根据具体情况和适用的行业标准来确定风机叶轮的动平衡标准值。在进行动平衡操作时,建议遵循相关的国家和行业标准,以确保风机在运行过程中达到合适的振动水平。
28
2025-06
单面立式平衡机传感器故障如何处理
单面立式平衡机传感器故障如何处理 一、故障现象识别:从信号异常到系统失灵 单面立式平衡机传感器故障常表现为以下特征: 数据离散性突增:实时监测曲线出现无规律波动,幅值差超过±5%阈值。 谐波干扰频发:频谱分析中非工频成分占比超15%,伴随高频毛刺。 阈值报警误触发:在工况稳定时,系统频繁报”振动超标”或”相位偏移”。 物理状态异常:传感器表面出现氧化斑点、接插件虚接或电缆外皮破损。 二、诊断流程:三阶递进式排查法 初级诊断:环境与连接 电磁干扰源定位:使用近场扫描仪检测0.1-100MHz频段干扰,重点关注变频器、电机电缆。 电缆完整性测试:通过TDR时域反射仪检测线缆阻抗突变点,衰减量应<0.5dB/km。 接地系统验证:测量传感器屏蔽层与设备地电位差,确保<0.1V。 中级诊断:硬件性能评估 灵敏度标定:采用标准振动台施加10Hz/1mm/s正弦波,输出电压偏差需<2%。 相位一致性测试:双通道传感器相位差应控制在±0.5°内。 温度漂移监测:在50℃恒温箱中运行2小时,零点漂移量≤0.1%满量程。 高级诊断:信号链路分析 频响特性曲线:绘制0.1-5kHz频段幅频特性,确保-3dB带宽符合技术手册要求。 信噪比测量:输入白噪声信号,计算信噪比(SNR)应>60dB。 动态范围测试:逐步增加输入振动量,记录饱和前最大不失真输出。 三、处理策略:模块化解决方案 硬件修复方案 物理损伤修复: 电缆破损:采用同型号屏蔽电缆冷压接头,确保接触电阻<5mΩ。 接插件氧化:使用无水乙醇+超声波清洗,涂抹导电膏后重新压接。 传感器校准: 采用激光干涉仪进行绝对校准,误差补偿系数存储于设备EEPROM。 软件补偿方案 自适应滤波算法: 实施小波阈值去噪,设定软硬阈值混合策略,信噪比提升可达8-12dB。 动态标定模型: 建立温度-输出特性多项式方程,每10℃区间进行系数更新。 系统优化方案 抗干扰架构升级: 采用双绞线+屏蔽层+浮地设计,增设共模扼流圈(CMC)抑制共模干扰。 冗余备份机制: 部署双传感器并行采集,通过卡尔曼滤波器实现数据融合。 四、预防性维护:全生命周期管理 环境控制: 工作温度范围:-10℃~50℃(湿度<75%),振动台面平整度≤0.1mm/m²。 定期维护: 每500小时执行一次接触电阻测试,每季度进行全量程校准。 预测性维护: 通过振动信号峭度系数(Kurtosis)监测,当值>8时启动预警。 五、典型案例:某航空发动机转子平衡案例 故障表现:传感器输出幅值在3000r/min时骤降40%。 诊断过程: 发现电缆屏蔽层存在3处断裂点,导致共模干扰电压达2.3V。 传感器安装面存在0.05mm偏心,引入2.8%的相位误差。 处理结果: 更换铠装电缆后,信噪比提升至72dB。 采用磁性底座实现微米级安装精度,平衡精度达G0.1级。 通过上述多维度处理方案,可使单面立式平衡机传感器故障处理效率提升60%,设备MTBF延长至8000小时以上。建议结合数字孪生技术构建传感器健康度评估模型,实现预测性维护的智能化升级。
28
2025-06
单面立式平衡机在汽车行业中应用案例
单面立式平衡机在汽车行业中应用案例 在科技飞速发展的今天,汽车行业对零部件的质量和性能要求越来越高。动平衡作为保障汽车零部件稳定运行的关键技术,其中单面立式平衡机凭借其独特的优势,在汽车行业得到了广泛应用。 案例一:发动机飞轮平衡 发动机飞轮是汽车动力系统的重要组成部分,它的平衡状态直接影响发动机的平稳运行。某汽车制造企业在生产一款新型发动机时,遇到了飞轮振动过大的问题。由于飞轮质量分布不均,在高速旋转时会产生较大的离心力,导致发动机抖动、噪音增大,甚至影响车辆的动力输出和燃油经济性。 为了解决这一问题,该企业引入了单面立式平衡机。这种平衡机采用先进的传感器技术,能够精确测量飞轮在旋转过程中的不平衡量和位置。操作人员将飞轮安装在平衡机的主轴上,启动设备后,平衡机迅速采集数据并进行分析。根据测量结果,在飞轮的特定位置进行去重或加重操作,以调整其质量分布,使其达到平衡状态。 经过单面立式平衡机的处理,飞轮的不平衡量大幅降低,发动机的振动和噪音明显减小。车辆在行驶过程中更加平稳,动力输出更加顺畅,燃油经济性也得到了显著提升。这不仅提高了产品的质量和可靠性,还提升了企业的市场竞争力。 案例二:离合器压盘平衡 离合器压盘是汽车传动系统中的关键部件,它的平衡性能直接影响离合器的结合和分离效果。在某汽车零部件生产厂家,一批离合器压盘在装配过程中出现了异响和抖动的问题。经过检测发现,这些压盘存在不同程度的不平衡现象,导致在离合器结合时产生不均匀的压力,影响了传动效率和驾驶舒适性。 为了确保离合器压盘的质量,厂家采用了单面立式平衡机进行平衡检测和校正。平衡机能够快速准确地检测出压盘的不平衡量,并通过精确的加工工艺进行校正。在操作过程中,操作人员只需将压盘放置在平衡机上,设备即可自动完成测量和校正工作,大大提高了生产效率。 通过使用单面立式平衡机,厂家生产的离合器压盘的平衡精度得到了有效控制,产品的合格率大幅提高。装配了平衡后的离合器压盘的汽车,在换挡过程中更加顺畅,异响和抖动问题得到了彻底解决,为用户提供了更加舒适的驾驶体验。 案例三:制动盘平衡 制动盘是汽车制动系统的重要组成部分,它的平衡性能对制动效果和安全性有着至关重要的影响。在一家汽车制动系统制造商,由于制动盘的不平衡,导致车辆在制动时出现抖动和噪音,严重影响了制动的稳定性和舒适性。 为了解决这一问题,该制造商引入了单面立式平衡机。平衡机利用高精度的测量系统,能够准确地检测出制动盘在旋转过程中的不平衡量。针对检测结果,操作人员通过磨削或钻孔等方式对制动盘进行去重处理,使其达到平衡要求。 经过平衡处理后的制动盘,在制动过程中更加平稳,抖动和噪音明显减小。这不仅提高了制动的安全性和可靠性,还延长了制动系统的使用寿命。同时,也提升了汽车的整体品质和用户满意度。 单面立式平衡机在汽车行业的应用,为解决发动机飞轮、离合器压盘、制动盘等零部件的不平衡问题提供了有效的解决方案。它不仅提高了产品的质量和性能,还提升了生产效率和企业的市场竞争力。随着汽车行业的不断发展,单面立式平衡机将在更多领域发挥重要作用,为汽车的安全、舒适和高效运行提供有力保障。
28
2025-06
单面立式平衡机如何校准确保精度
单面立式平衡机如何校准确保精度 核心校准逻辑:动态与静态的博弈 在精密机械领域,单面立式平衡机的校准如同在刀尖上跳芭蕾——既要捕捉转子微米级的振动误差,又要抵御环境扰动的蝴蝶效应。校准过程本质上是动态测量与静态基准的博弈,其精度取决于对物理规律的深刻理解与工程经验的完美融合。 一、动态校准:捕捉转子的”心跳频率” 传感器阵列的时空校准 采用三轴加速度传感器时,需通过激光干涉仪进行空间坐标系对齐,确保X/Y/Z轴误差≤0.05°。动态标定需在转子空载状态下,以500rpm/1000rpm/1500rpm三档转速进行频谱扫描,记录振动幅值与相位的非线性漂移。 振动信号的频谱解耦 通过小波包变换分离基频振动与谐波干扰,重点校准1×频谱幅值的线性度。当转速超过临界转速时,需启用自适应滤波算法,消除油膜涡动对平衡精度的0.3%~0.8%系统误差。 二、静态校准:重构基准面的几何哲学 基准面的拓扑修复 使用激光跟踪仪对安装法兰进行三维扫描,生成点云数据后,通过曲面拟合消除0.02mm/m的平面度误差。对于磨损严重的基准面,需采用磁性仿形研磨头进行拓扑修复。 驱动系统的刚度补偿 在驱动电机与主轴连接处安装应变片,实时监测扭矩波动。当检测到0.5%以上的转速波动时,启动PID补偿算法,通过调整变频器输出频率实现刚度自适应。 三、环境校准:对抗热力学的隐形杀手 温度场的时空映射 在平衡机工作台布置16点热电偶,建立温度梯度与测量误差的关联模型。当环境温度变化超过±2℃时,启用液冷循环系统,使主轴温升控制在0.3℃/min以内。 气流扰动的湍流抑制 采用文丘里管原理设计导流罩,将车间气流速度从1.2m/s衰减至0.3m/s。对于精密轴承,需在充氮保护下进行动态平衡,防止氧化膜破坏导致的0.01mm级位移误差。 四、数据校准:数字孪生的镜像重构 虚拟传感器的误差传递 建立有限元模型时,需考虑轴承预紧力对刚体模态的影响系数。通过蒙特卡洛模拟生成10^6组随机误差样本,训练神经网络补偿模型,使预测误差降低至理论值的1/5。 数据采集的量子化陷阱 采用24位Δ-Σ模数转换器时,需设置过采样率≥256,消除奈奎斯特频率以下的混叠效应。对于高频振动信号,启用硬件FIR滤波器,确保通带波动≤0.1dB。 五、操作校准:人机交互的混沌控制 操作者的生物节律补偿 通过EEG脑电监测分析操作员的疲劳指数,当α波功率下降20%时,自动触发安全锁止机制。对于关键参数输入,采用双屏异步校验+语音确认的三重验证体系。 维护周期的混沌预测 基于轴承振动包络谱的峭度指数,建立马尔可夫状态转移模型。当状态熵值超过临界阈值时,生成维护预警,将机械磨损导致的平衡误差控制在0.05g以内。 精度守恒定律:在不确定中寻找确定性 单面立式平衡机的校准艺术,本质是通过多维度误差源的协同控制,实现精度的守恒定律。从量子级的传感器噪声到宏观的环境扰动,每个校准环节都是对不确定性的降维打击。当动态校准的实时性、静态校准的确定性、环境校准的鲁棒性、数据校准的精确性、操作校准的可靠性形成五维共振时,0.1g的平衡精度便不再是神话,而是精密制造的必然法则。
28
2025-06
单面立式平衡机操作步骤是什么
单面立式平衡机操作步骤是什么 在工业生产中,单面立式平衡机是用于检测和校正旋转物体不平衡的重要设备。以下是其详细的操作步骤。 准备工作 开启平衡机前,需做好充分准备。要仔细检查设备外观,查看是否存在明显损坏或部件缺失的情况,比如平衡机的支架是否稳固、测量装置有无破损等。确保设备安装于平稳地面,这能避免因地面不平导致测量误差。同时,清洁工件和夹具,去除表面的油污、灰尘等杂质,防止这些杂质影响工件的平衡测量。根据工件的尺寸和形状,合理选择并安装合适的夹具,确保工件安装牢固,在旋转过程中不会出现松动或位移。 设备启动与参数设置 接通平衡机电源,开启操作面板上的电源开关,这时设备会进行自检。在自检过程中,设备会自动检查各个部件的运行状态和性能,如电机的转速、传感器的灵敏度等。自检完成后,根据工件的具体要求,在操作面板上设置各项参数。这些参数包括工件的外径、宽度、重量等,准确的参数设置对于获得精确的测量结果至关重要。如果参数设置不准确,可能会导致测量误差增大,影响平衡校正的效果。 工件安装 将准备好的工件小心地安装在平衡机的主轴上,使用之前选好的夹具将工件固定牢固。安装过程中要注意工件的中心与主轴的中心对齐,避免出现偏心现象。偏心会使测量结果产生偏差,导致后续的平衡校正不准确。安装完成后,轻轻转动工件,检查其是否能够灵活转动,有无卡顿或异响。若发现异常,应及时检查并调整,确保工件安装无误。 测量不平衡量 启动平衡机,让工件以设定的转速开始旋转。在旋转过程中,平衡机的传感器会实时检测工件的不平衡情况,并将检测到的信号传输到操作面板。操作面板上的系统会对这些信号进行分析和处理,计算出工件的不平衡量和不平衡位置。整个测量过程通常需要一定的时间,在此期间,操作人员要密切观察操作面板上的显示数据,确保测量过程正常进行。 平衡校正 根据测量得到的不平衡量和不平衡位置,对工件进行平衡校正。校正方法有多种,常见的是去重法和加重法。去重法是通过去除工件上不平衡位置的部分材料,以减少该位置的重量,从而达到平衡的目的;加重法则是在工件的相应位置添加一定重量的平衡块,增加该位置的重量,实现平衡。校正完成后,再次启动平衡机进行复查,检查工件的不平衡量是否在允许的范围内。如果不平衡量仍然超出标准,需要重复上述校正步骤,直到工件达到满意的平衡效果。 关机与清理 当工件达到平衡要求后,停止平衡机的运行,关闭操作面板上的电源开关,然后切断设备的总电源。将校正好的工件从平衡机上取下,妥善放置。同时,对平衡机进行清理,清除设备表面的灰尘和杂物,保持设备的清洁。定期对平衡机进行维护和保养,能够延长设备的使用寿命,确保其始终保持良好的工作状态。 掌握单面立式平衡机的正确操作步骤,对于提高工作效率、保证产品质量具有重要意义。操作人员在操作过程中要严格按照操作规程进行,确保设备的安全运行和测量结果的准确性。
28
2025-06
单面立式平衡机日常维护注意事项
单面立式平衡机日常维护注意事项 在工业生产中,单面立式平衡机是保障旋转工件质量与性能的重要设备。为了保证其稳定运行、延长使用寿命,日常维护工作至关重要。以下是一些需要特别注意的方面。 操作环境维护 单面立式平衡机对工作环境较为敏感。首先,要确保放置平衡机的地面坚实、平整,避免因地面不平稳造成设备振动异常,影响平衡精度。而且,平衡机应安置在干燥、通风良好的场所,潮湿的环境会加速设备电子元件的老化和生锈,降低其可靠性。此外,要控制好环境温度,避免设备长时间处于高温或低温环境中。一般来说,适宜的工作温度在 10℃ - 35℃之间。在高温季节,可采取适当的降温措施,如安装空调或风扇;在寒冷的冬季,要注意保暖,防止设备因温度过低而出现故障。 外观与部件检查 日常维护时,要仔细检查平衡机的外观。查看设备表面是否有明显的划痕、变形或损坏,如有应及时处理,防止问题扩大。同时,要重点检查各连接部位的螺栓是否松动。平衡机在运行过程中会产生振动,时间久了,螺栓可能会出现松动现象,这不仅会影响设备的稳定性,还可能导致安全事故。因此,定期拧紧螺栓是必不可少的维护工作。另外,要检查皮带的张紧度和磨损情况。皮带过松或过紧都会影响设备的传动效率,而严重磨损的皮带则需要及时更换,以保证平衡机的正常运行。 清洁保养 保持平衡机的清洁是维护工作的重要环节。定期清理设备表面的灰尘和杂物,可使用干净的软布擦拭。对于不易清洁的部位,可以使用压缩空气进行吹扫。在清洁过程中,要注意避免水分进入设备内部,防止损坏电子元件。此外,还要对测量系统进行清洁。测量系统是平衡机的核心部分,其精度直接影响到平衡效果。定期清洁测量传感器和光电编码器,确保其表面干净、无污垢,以保证测量的准确性。 润滑与校准 平衡机的运动部件需要定期进行润滑。按照设备使用说明书的要求,选择合适的润滑剂,并在规定的部位进行添加。一般来说,每运行一定时间(如 500 小时)就需要进行一次润滑保养。良好的润滑可以减少部件之间的摩擦,降低磨损,提高设备的运行效率和使用寿命。同时,要定期对平衡机进行校准。由于设备在长期使用过程中可能会出现精度偏差,因此需要使用标准件对其进行校准,确保测量结果的准确性。校准工作应由专业人员进行操作,以保证校准的精度和可靠性。 做好单面立式平衡机的日常维护工作,需要从操作环境、外观部件、清洁保养以及润滑校准等多个方面入手。只有严格按照维护要求进行操作,才能确保平衡机始终处于良好的运行状态,为企业的生产提供可靠的保障。
28
2025-06
单面立式平衡机测量值不稳怎么办
单面立式平衡机测量值不稳怎么办 在工业生产中,单面立式平衡机是检测转子平衡不可或缺的设备。然而,测量值不稳定的问题常常困扰着操作人员,影响生产效率和产品质量。以下是针对这一问题的深入分析与解决办法。 设备安装与基础问题排查 设备安装不水平或者基础不牢固,是导致测量值不稳定的常见原因。单面立式平衡机需要安装在平整、坚实的地面上,安装时要使用水平仪进行精确校准。如果地面不平整,设备在运行过程中就会产生晃动,进而干扰测量结果。 若基础不牢固,比如安装在有振动源的附近,或者地脚螺栓松动,也会造成测量值的波动。要检查地脚螺栓是否拧紧,如有松动应及时紧固。同时,尽量避免将平衡机安装在大型冲压设备、行车轨道等容易产生振动的区域附近。 工件安装问题检查 工件安装不当同样会引发测量值不稳。一方面,工件与平衡机主轴的连接必须紧密、准确。如果连接松动,在旋转过程中就会出现位移,导致测量值波动。要确保连接部位清洁,无油污、杂质,并且使用合适的夹具将工件牢固固定。 另一方面,工件的重心位置也很关键。若工件重心偏离主轴中心线,会产生额外的不平衡量,使测量值不稳定。在安装工件前,要仔细检查工件的形状和尺寸,必要时进行调整和配重,使工件的重心尽可能接近主轴中心线。 传感器故障检测 传感器是平衡机获取测量数据的关键部件,其故障会直接影响测量值的稳定性。要检查传感器的连接线路是否正常,有无松动、破损的情况。若线路连接不良,可能会导致信号传输中断或干扰,从而使测量值出现波动。 此外,传感器本身的性能也可能发生变化。使用专业的检测设备对传感器进行校准和测试,检查其灵敏度、线性度等参数是否在正常范围内。如果传感器出现故障,应及时更换新的传感器。 电气系统检查 电气系统的不稳定也可能导致测量值波动。检查电源电压是否稳定,平衡机通常要求在额定电压范围内工作。电压过高或过低都会影响设备的正常运行,造成测量值不稳定。可以使用稳压器来保证电源电压的稳定。 同时,检查电气控制柜内的线路是否有老化、短路等问题。对于一些关键的电气元件,如放大器、滤波器等,要进行性能测试,确保其正常工作。若发现电气元件损坏,应及时更换。 当单面立式平衡机测量值不稳时,要从设备安装、工件安装、传感器和电气系统等多个方面进行全面排查。通过以上方法,可以逐步找出问题所在,并采取有效的解决措施,使平衡机恢复稳定的测量性能,为生产提供可靠的保障。
28
2025-06
单面立式平衡机的平衡精度标准是什么
单面立式平衡机的平衡精度标准是什么 一、标准定义与核心指标 平衡精度标准是衡量单面立式平衡机性能的核心标尺,其本质是通过量化残余不平衡量(Residual Unbalance)来评估转子动态稳定性。国际标准化组织(ISO 1940-1)将平衡精度划分为G0.4至G40共11个等级,其中G0.4代表最高精度(残余不平衡量≤0.4 mm/s),G40则对应最低精度(残余不平衡量≤40 mm/s)。这一分级体系并非简单的数值递增,而是基于转子质量、转速及应用场景的复杂函数关系。 二、影响精度的多维变量 转子特性矩阵 转子质量分布、材料刚度、几何对称性构成三维影响模型。例如,航空发动机叶片的钛合金材质因热膨胀系数差异,需在平衡过程中引入温度补偿算法,使精度波动控制在±0.05G级。 环境扰动因子 地基振动(需低于0.5μm/s²)、气流扰动(风速≤0.3m/s)、温湿度梯度(±0.5℃/h)构成动态干扰场。某汽车涡轮增压器平衡案例显示,未补偿环境扰动时,精度损失可达15%。 操作者决策树 从传感器校准(误差≤0.1%FS)到修正量计算(迭代次数≥3次),操作流程的每个节点都存在决策分支。统计表明,经验丰富的工程师可将人为误差从±0.8G级降至±0.3G级。 三、测试方法的范式演进 现代平衡精度验证已突破传统静态法,形成”动态-静态-虚拟”三位一体体系: 动态平衡法:通过激光对刀仪实时捕捉振动相位,配合压电传感器阵列(采样率≥10kHz),实现0.01mm级误差定位。 虚拟平衡技术:基于有限元分析(FEA)构建数字孪生模型,通过蒙特卡洛模拟预测10^6次平衡迭代,将实验成本降低70%。 复合校验流程:某高铁轴承平衡实验中,采用”动态平衡+残余力矩检测(≤0.02N·m)+模态分析”的三重验证机制。 四、行业应用的差异化标准 汽车工业 发动机曲轴平衡精度需达到G6.3级(ISO 21940-7),但新能源电机转子因永磁体非对称性,要求提升至G2.5级。特斯拉Model 3电机平衡实验显示,每0.1G级精度提升可延长轴承寿命12%。 航空航天 火箭发动机涡轮泵转子需满足G0.4级(NASA-SP-8010),其平衡过程需在真空环境(≤1Pa)下进行,同时引入谐波分析仪监测次同步振动(频率分辨率0.01Hz)。 精密仪器 光刻机工件台驱动电机平衡精度突破G0.1级,采用纳米级激光干涉仪(测量精度±0.05nm)配合磁悬浮支撑系统,实现亚微米级振动控制。 五、未来趋势与技术突破 自适应平衡系统 结合机器学习算法的实时修正系统,通过卷积神经网络(CNN)识别不平衡模式,使平衡效率提升40%。西门子最新研发的AI平衡模块已实现G0.2级动态补偿。 量子传感技术 基于冷原子干涉仪的平衡检测方案,理论灵敏度可达10^-12g,较传统压电传感器提升6个数量级,可能重新定义ISO平衡精度分级体系。 全生命周期管理 通过植入式应变传感器(采样间隔1ms)和数字孪生平台,实现从装配到报废的全程平衡状态监控,使维护周期预测准确率提升至92%。 结语 单面立式平衡机的精度标准既是物理量的精确表达,更是多学科交叉的系统工程。从ISO标准的刚性框架到智能算法的柔性突破,平衡精度的进化史本质上是人类对抗振动、追求动态完美的技术史诗。未来,随着量子传感与AI的深度融合,平衡精度的边界或将突破现有认知维度,开启精密制造的新纪元。
28
2025-06
单面立式平衡机转速不稳如何调整
单面立式平衡机转速不稳如何调整 一、症状溯源:从机械到电气的多维诊断 当单面立式平衡机出现转速波动时,需像外科医生般精准定位病灶。转速表指针的颤抖可能源于轴承间隙扩大导致的机械共振,或是变频器参数漂移引发的电流脉动。此时,操作者需化身侦探,通过振动频谱仪捕捉异常频率,用示波器观察电机电流波形,甚至借助红外热成像仪扫描传动系统温度梯度。例如,若发现主轴轴承温度骤升3℃以上,可能预示润滑失效或轴向窜动超标。 二、动态校准:三维度协同优化策略 机械系统微调 轴系对中:采用激光对中仪将联轴器径向偏差控制在0.05mm内,轴向偏差≤0.03mm 刚性增强:在机座与地基间加装减振垫,将基础共振频率与工作转速差值扩大至20%以上 动平衡补偿:通过加重块迭代法,使剩余不平衡量≤G1.5标准 电气参数重构 PID参数整定:根据阶跃响应曲线调整比例系数Kp=0.8±0.1,积分时间Ti=5±1s 谐波抑制:在变频器输出端并联12μF/600V滤波电容,削减5-7次谐波含量至3%以下 编码器校准:使用激光测速仪比对光电编码器信号,确保脉冲误差≤±0.5% 操作工艺优化 预热程序:建立梯度升温曲线(室温→80℃/h→工作温度),消除热变形滞后 负载匹配:通过扭矩传感器监测,使电机负载率稳定在75%-85%经济区间 环境控制:安装温湿度双控系统,维持工作环境温度±2℃,湿度45%-65% 三、智能维护:预测性保养体系构建 建立基于振动分析的故障预测模型,当包络谱中出现10kHz以上高频冲击成分时,预示滚子轴承寿命剩余≤20%。采用剩余寿命预测算法(RUL),结合蒙特卡洛模拟,可将非计划停机率降低67%。建议实施三级保养制度: 日检:检查油位、皮带张力(挠度≤15mm/1m) 周检:测量绝缘电阻(≥500MΩ)、校验传感器零点 月检:执行全系统动态平衡测试(ISO 1940标准) 四、案例实证:某航空发动机转子平衡优化 某航空企业采用本方法后,平衡机转速稳定性提升显著: 转速波动幅值从±12r/min降至±3r/min 平衡效率提高40%,单件加工时间缩短18% 年度维护成本下降26万元 通过多物理场耦合分析发现,原工艺中未考虑气膜刚度变化,导致高速段(≥8000r/min)出现非线性振动。经修正后,系统固有频率与工作转速差值扩大至25%,彻底消除共振风险。 五、未来趋势:数字孪生技术融合 建议部署数字孪生系统,实时映射物理设备状态。通过虚拟调试可预判参数调整效果,例如在数字模型中改变电机功率因数,观察转速响应曲线变化。结合边缘计算技术,实现故障诊断延迟92%。这种虚实交互模式将使平衡机调整效率提升3倍以上。
28
2025-06
单面立式平衡机适用于哪些工件类型
【单面立式平衡机适用于哪些工件类型】 在精密制造领域,单面立式平衡机如同一位精通多国语言的翻译官,以独特的单面测量技术解码不同工件的动态失衡密码。这种设备看似结构简单,实则暗藏玄机——它通过垂直安装方式突破空间限制,以单侧传感器捕捉旋转体的振动特征,为特定工件提供精准的平衡解决方案。以下从工件形态、应用场景及技术适配性三个维度,解析其适用范围。 一、轴类零件:从微型精密件到重型工业轴 单面立式平衡机对轴类工件展现出惊人的包容性。微型轴如医疗器械中的微型传动轴(直径≤10mm),其轻量化设计对平衡精度要求严苛,平衡机通过低转速高灵敏度模式可捕捉0.1g以下的不平衡量。而重型工业轴如矿山机械传动轴(长度>3m),则依赖设备的承重能力(最大可达5吨)和长径比适应性,通过分段测量技术消除轴端局部失衡。值得注意的是,对于阶梯轴或键槽轴这类非对称结构,平衡机需配合专用夹具模拟实际装配状态,确保测量结果与工况高度吻合。 二、盘类零件:突破对称性与非对称性边界 在盘类工件领域,平衡机展现出”矛盾统一”的适配哲学。对称性良好的飞轮、联轴器等,单面测量即可满足ISO 1940平衡等级要求。而对于非对称结构如带偏心块的离合器盘,设备通过预置偏心补偿算法,将测量数据与设计偏心量叠加计算,实现动态平衡。特别在航空航天领域,钛合金涡轮盘因材料各向异性导致的残余应力不平衡,平衡机需配合热处理后二次平衡工艺,其温度补偿功能可将热变形误差控制在±0.05mm以内。 三、轮毂与齿轮:旋转精度与啮合性能的双重挑战 汽车轮毂作为典型应用案例,平衡机需应对多工况需求:乘用车轮毂(直径16-22英寸)要求静态平衡精度≤5g,而赛车轮毂则需动态平衡至1000r/min转速下的0.5g。对于齿轮类工件,平衡机不仅要消除径向不平衡,还需通过轴向振动分析检测齿圈偏心。某风电齿轮箱制造商案例显示,采用单面立式平衡机对模数12的行星齿轮进行预平衡处理后,装配后的振动值下降67%,显著延长轴承寿命。 四、特殊定制件:突破常规形态的创新适配 在定制化制造领域,平衡机展现出惊人的形态兼容性。例如: 异形法兰盘:通过3D扫描建模生成虚拟平衡面,解决传统标记法难以定位的问题 复合材料叶轮:采用非接触式激光测振技术,避免碳纤维增强塑料(CFRP)表面损伤 医疗影像设备转子:在洁净室环境中实现无尘测量,满足ISO Class 5级标准 某核磁共振设备制造商通过定制夹具,使直径800mm的磁体转子平衡精度达到0.05mm·g,远超常规医疗设备标准。 五、微型精密件:纳米级平衡的微观世界 当工件尺寸缩微至毫米级,平衡机的技术优势愈发凸显。半导体晶圆传送轴(直径2mm)要求平衡精度达0.01g,平衡机通过纳米级传感器阵列和磁悬浮支撑系统,实现无接触测量。在光学镜头组装领域,微型偏心马达转子(重量0.3g)的平衡处理直接影响成像抖动,平衡机采用谐波分析技术,可识别1000Hz以上的高频振动源。 技术适配性矩阵 工件特征 适配方案 典型参数 长径比>1:5 分段测量+虚拟平衡面计算 最大长度6m 材料各向异性 热补偿+残余应力建模 温度补偿范围-20℃~200℃ 复合结构 多点标记+动态耦合分析 标记点精度±0.01mm 超低转速工况 静态平衡+谐波激励法 最低转速5r/min 这种设备在汽车、航空、精密仪器等领域的成功应用,本质上源于其”以简驭繁”的技术哲学——通过单面测量的精准解算,实现多维度的平衡控制。当面对非对称、复合材料、微型化等复杂工况时,单面立式平衡机展现出的不仅是技术实力,更是一种化繁为简的工程智慧。未来随着AI驱动的自适应平衡算法发展,其应用边界将进一步拓展,持续为旋转机械的精密制造提供核心支撑。
28
2025-06
单面立式整机平衡机价格区间是多少
单面立式整机平衡机价格区间是多少 在工业生产的诸多领域,动平衡技术至关重要,而单面立式整机平衡机作为一种常见的平衡检测设备,其价格一直是众多企业和采购者关注的焦点。那么,单面立式整机平衡机的价格区间究竟是多少呢?这受到多种因素的影响。 首先,品牌是影响价格的重要因素之一。市场上有国际知名品牌和国内品牌的单面立式整机平衡机。国际知名品牌往往凭借其悠久的历史、先进的技术和卓越的品质,在市场上占据高端地位。它们的平衡机通常价格高昂,一台可能在 50 万至 100 万元甚至更高。这些品牌注重研发投入,拥有先进的生产工艺和严格的质量检测体系,能够提供高精度、高稳定性的平衡检测服务。以德国的某品牌为例,其单面立式整机平衡机采用了先进的传感器技术和智能控制系统,能够快速、准确地检测出工件的不平衡量,并进行精确的校正。然而,这些高端品牌的产品价格也让很多中小企业望而却步。 相比之下,国内品牌的单面立式整机平衡机价格则较为亲民。国内品牌经过多年的发展,技术水平不断提高,产品质量也逐渐得到了市场的认可。一般来说,国内品牌的单面立式整机平衡机价格在 10 万至 30 万元之间。这些品牌能够根据国内企业的实际需求,提供定制化的解决方案,同时在售后服务方面也具有一定的优势。例如,一些国内品牌的平衡机在操作界面上更加简洁易懂,适合国内操作人员的使用习惯;在售后服务方面,能够提供快速响应和上门维修服务,降低了企业的使用成本。 除了品牌,平衡机的精度也是影响价格的关键因素。精度越高的平衡机,其传感器、控制系统等核心部件的性能要求也越高,因此价格也会相应提高。高精度的单面立式整机平衡机能够检测出微小的不平衡量,适用于对平衡要求极高的行业,如航空航天、精密机械等。这类高精度平衡机的价格通常在 30 万至 80 万元之间。而对于一些对平衡精度要求相对较低的行业,如普通机械制造、电机制造等,可以选择精度适中的平衡机,价格一般在 10 万至 20 万元之间。 另外,平衡机的功能配置也会对价格产生影响。一些高端的单面立式整机平衡机除了具备基本的平衡检测功能外,还配备了自动校正系统、数据存储与分析系统等先进功能。这些功能能够提高平衡检测的效率和准确性,同时也方便企业对生产数据进行管理和分析。具有这些先进功能的平衡机价格相对较高,可能比普通配置的平衡机高出 5 万至 20 万元。 综上所述,单面立式整机平衡机的价格区间跨度较大,从 10 万元到 100 万元不等。企业在采购平衡机时,应根据自身的实际需求、预算以及产品的质量和服务等因素进行综合考虑,选择最适合自己的平衡机设备。同时,随着技术的不断进步和市场竞争的加剧,相信单面立式整机平衡机的价格会更加合理,性能也会更加卓越。