Copyright © 2003-2019 上海申岢动平衡机制造有限公司, All Rights Reserved 沪ICP备16012006号-5 友情链接:
上海动平衡机
搜索


主轴动平衡机加工时安装定位精度对结果的影响
- 分类:行业新闻
- 作者:申岢编辑部
- 来源:上海申岢动平衡机制造有限公司
- 发布时间:2025-04-25
- 访问量:120
主轴动平衡机在加工过程中,工件的安装定位精度对动平衡结果有显著影响,主要体现在以下几个方面:
1. 虚假不平衡量的引入
- 同轴度偏差:若工件安装时与主轴轴线不同轴(偏心或倾斜),会导致旋转离心力的不对称分布。这种由安装误差引起的离心力会被动平衡机误判为工件本身的不平衡量,造成虚假的校正需求。
- 端面跳动误差:安装面与主轴端面贴合不紧密或存在异物时,旋转中会产生轴向振动,影响动平衡测量的准确性。
2. 重复性降低
- 定位不一致:若工件的定位基准(如锥面、法兰孔等)存在磨损或污染,每次安装位置可能发生微小变化。这种不一致性会导致多次动平衡测量的结果波动,难以保证校正的稳定性。
- 夹具刚性不足:夹具刚性差会导致工件在高速旋转时发生位移或振动,影响测量的重复性。
3. 测量信号干扰
- 振动传递误差:安装松动或间隙会引发额外振动,这些振动信号会被动平衡机的传感器捕捉,干扰对真实不平衡量的判断。
- 共振风险:定位偏差可能导致系统临界转速改变,诱发共振现象,严重时可能损坏设备或工件。
4. 校正效果失效
- 过校正或欠校正:若安装误差导致的虚假不平衡量被误判,实际校正时可能在校正面上添加或去除过多/过少的质量,反而加剧不平衡。
- 实际工况偏差:动平衡结果虽在机上合格,但因安装误差的存在,工件在真实工作环境中仍可能因受力不均导致振动超标。
5. 长期稳定性问题
- 磨损加剧:长期使用低精度安装定位可能导致主轴轴承、夹具等部件加速磨损,进一步降低动平衡精度和设备寿命。
解决方案
- 提高安装精度:
- 使用高精度定位基准(如HSK锥柄、液压膨胀芯轴)。
- 定期清洁和维护夹具、定位面,避免异物或磨损。
- 采用激光对中仪检测安装同轴度,确保公差(通常要求≤0.005 mm)。
- 优化夹具设计:
- 选择刚性材料(如碳化钨)并优化结构,减少变形。
- 使用气动或液压夹紧技术,确保夹持力均匀稳定。
- 过程控制:
- 在动平衡前进行“空转测试”,排除主轴自身不平衡或夹具问题。
- 实施标准化安装流程,记录每次安装参数(如扭矩值、定位标记)。
- 数据修正:
- 对于批量工件,可通过统计分析建立安装误差补偿模型,在动平衡算法中修正偏差。
总结
安装定位精度是影响动平衡结果的核心因素之一。通过提升工艺规范、优化夹具设计、严格过程控制,可显著降低安装误差对动平衡的影响,确保校正结果的可靠性与工件的长期运行稳定性。在精密加工(如航空航天、高精度机床主轴)领域,安装定位精度甚至需达到微米级要求。
上一个:
主轴动平衡机加工在高速电主轴制造中的难点
上一个:
主轴动平衡机加工在高速电主轴制造中的难点
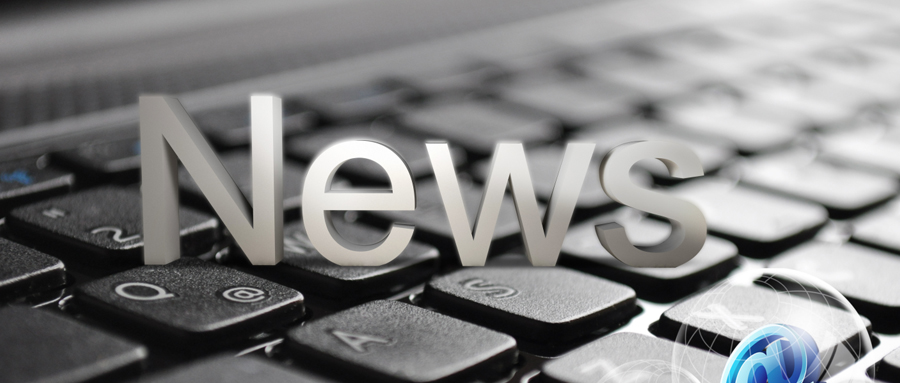