Copyright © 2003-2019 上海申岢动平衡机制造有限公司, All Rights Reserved 沪ICP备16012006号-5 友情链接:
上海动平衡机
搜索


动平衡机加工与数字孪生技术的结合前景
- 分类:行业新闻
- 作者:申岢编辑部
- 来源:上海申岢动平衡机制造有限公司
- 发布时间:2025-04-21
- 访问量:75
动平衡机加工与数字孪生技术的结合是工业智能化转型中的前沿方向,其前景广阔且具有显著的协同效应。以下是这一技术结合的核心价值、应用场景及未来趋势的分析:
1. 技术结合的核心价值
- 实时优化与预测性维护
数字孪生通过实时采集动平衡机的传感器数据(如振动、转速、不平衡量),构建虚拟孪生体,模拟加工过程。结合AI算法可预测设备故障(如轴承磨损、刀具偏移),主动调整加工参数,减少停机时间。 - 精度与效率提升
传统动平衡依赖人工经验调整校正参数,而数字孪生通过仿真优化,可自动生成最优配重方案,缩短调试周期,降低废品率(例如在电机转子、涡轮叶片加工中提升微米级精度)。 - 全生命周期管理
从设计、加工到服役阶段,数字孪生可追溯历史数据,分析设备性能退化规律,为改进工艺提供闭环反馈。
2. 典型应用场景
- 航空航天领域
高精度叶轮、发动机转子的动平衡加工要求严苛,数字孪生可模拟极端工况下的动态响应,验证校正方案的可靠性。 - 新能源汽车
电机转子动平衡不良会导致噪声和寿命缩短,数字孪生结合边缘计算可实时优化加工参数,适应大规模柔性生产需求。 - 能源装备制造
风力发电机主轴、燃气轮机转子的动平衡需兼顾材料变形和环境干扰,数字孪生通过多物理场耦合仿真(如热-力耦合)提升校正精度。
3. 关键技术挑战
- 数据融合与模型精度
需解决传感器数据噪声、多源异构数据(振动、温度、视频)的融合问题,并建立高保真度的物理-数据混合模型。 - 实时性与算力平衡
加工过程的毫秒级响应需依赖边缘计算与云端的协同架构,避免因延迟导致控制滞后。 - 标准化与兼容性
不同厂商的动平衡机数据接口和协议差异大,需推动数字孪生平台标准化以降低集成成本。
4. 未来发展趋势
- AI驱动的自适应控制
结合深度强化学习(DRL),数字孪生系统可自主学习优化策略,适应复杂工况(如非对称转子、非线性材料)。 - 虚实联动的闭环控制
数字孪生与动平衡机形成“感知-决策-执行”闭环,实现加工参数的动态调整(如基于振动反馈的实时配重修正)。 - 产业链协同扩展
从单机数字化向车间级、工厂级孪生网络延伸,打通动平衡加工与上下游工艺(如热处理、装配)的数据流,优化整体生产节拍。
5. 经济效益与行业影响
- 降本增效
通过预测性维护减少设备故障率30%以上,加工效率提升20%~50%(具体数据因行业而异)。 - 绿色制造
减少试错性加工带来的材料浪费和能耗,符合“双碳”目标下的可持续发展需求。 - 商业模式创新
推动动平衡机制造商向“设备+服务”转型(如提供基于数字孪生的远程运维订阅服务)。
结论
动平衡机加工与数字孪生的深度融合将重塑精密制造领域的竞争力。短期内需突破数据建模与实时控制的技术瓶颈,长期来看,其与5G、边缘计算、AI的协同将推动工业设备从“被动响应”向“主动智能”跃迁。企业需尽早布局技术验证和人才储备,抢占高附加值制造领域的先机。
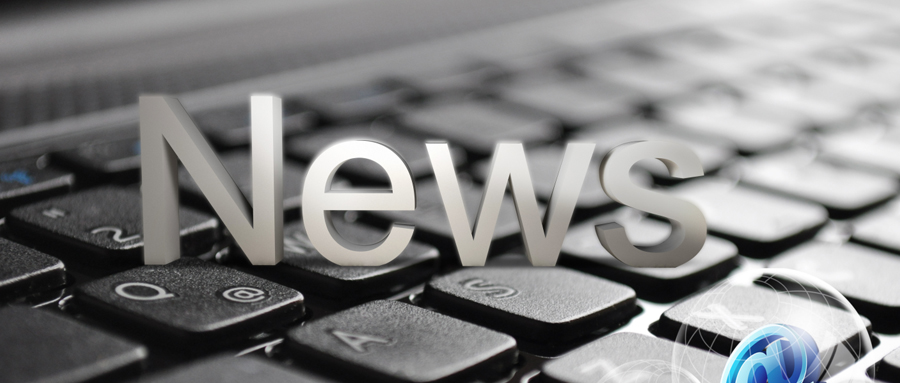