Copyright © 2003-2019 上海申岢动平衡机制造有限公司, All Rights Reserved 沪ICP备16012006号-5 友情链接:
上海动平衡机
搜索


如何通过动平衡机加工提升主轴的使用寿命
- 分类:行业新闻
- 作者:申岢编辑部
- 来源:上海申岢动平衡机制造有限公司
- 发布时间:2025-04-17
- 访问量:78
通过动平衡机加工提升主轴使用寿命的关键在于减少主轴的振动和动态载荷,从而降低磨损和疲劳损伤。以下是具体的实施步骤和技术要点:
1. 动平衡前的准备工作
- 主轴清洁与检查
确保主轴表面无杂质、锈蚀或损伤,避免因外部因素导致的不平衡误差。 - 安装精度校准
将主轴正确安装在动平衡机上,保证夹具和传感器的精度,避免因安装误差引入虚假不平衡量。 - 初始不平衡量检测
通过动平衡机测量主轴原始不平衡量的位置(相位角)和大小(克·毫米),确定校正需求。
2. 动平衡校正方法
- 校正方式选择
- 加重法:通过焊接、粘贴配重块(如平衡胶泥或螺钉)补偿不平衡量,适用于低转速主轴。
- 去重法:通过钻孔、铣削或激光去除材料,更适合高精度或高速主轴(避免配重块脱落风险)。
- 加重法:通过焊接、粘贴配重块(如平衡胶泥或螺钉)补偿不平衡量,适用于低转速主轴。
- 校正平面选择
根据主轴结构选择单面(短轴)或双面(长轴)平衡,确保在多个平面上消除振动模态。 - 分步校正
- 粗平衡:在较低转速下初步调整,消除大部分不平衡量。
- 精平衡:在额定转速下进行微调,确保达到目标精度等级(如ISO G1.0或更高)。
- 粗平衡:在较低转速下初步调整,消除大部分不平衡量。
3. 动平衡精度控制
- 遵循国际标准
根据主轴用途选择平衡等级(如ISO 1940-1标准)。例如:
- 精密机床主轴:通常要求G1.0或更高(残余不平衡量≤1g·mm/kg)。
- 普通电机主轴:G6.3或G2.5即可满足。
- 精密机床主轴:通常要求G1.0或更高(残余不平衡量≤1g·mm/kg)。
- 动态平衡验证
在动平衡机上模拟实际转速,验证主轴在运行中的振动值(如振动速度≤1.5mm/s为合格)。
4. 延长主轴寿命的配套措施
- 材料与工艺优化
- 采用高强度、耐疲劳材料(如合金钢或陶瓷轴承)。
- 校正时避免过度去重导致应力集中,需保证去除部位的表面光洁度。
- 采用高强度、耐疲劳材料(如合金钢或陶瓷轴承)。
- 热稳定性控制
对高速主轴进行动平衡时考虑温度影响(如热膨胀导致的形变),必要时在恒温车间操作。
- 定期维护与复测
- 每运行500-1000小时后重新检测动平衡状态,防止因轴承磨损或配重脱落导致失衡。
- 使用振动监测系统实时跟踪主轴运行状态,提前预警失衡问题。
- 每运行500-1000小时后重新检测动平衡状态,防止因轴承磨损或配重脱落导致失衡。
5. 实际应用案例
- 案例1:数控机床主轴
通过双面动平衡将残余振动从8μm降至1.2μm,轴承寿命提升40%以上。
- 案例2:航空发动机主轴
采用激光去重法实现G0.4级平衡,减少高速下的微动磨损,延长大修周期。
总结
通过精确的动平衡加工,主轴的振动能量可降低70%-90%,从而显著减少轴承、密封件和齿轮的磨损。结合定期维护和材料优化,主轴整体寿命可提升30%-50%,同时提高加工精度和设备可靠性。
上一个:
如何通过动平衡机加工提升曲棍的疲劳寿命
下一个:
如何通过优化动平衡机加工流程提升生产效率
上一个:
如何通过动平衡机加工提升曲棍的疲劳寿命
下一个:
如何通过优化动平衡机加工流程提升生产效率
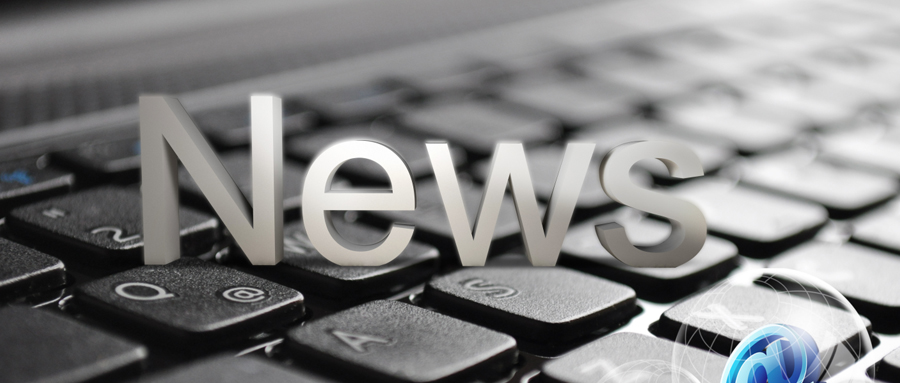