

精密制造的"稳定器":主轴动平衡技术解析
- 分类:行业新闻
- 作者:申岢编辑部
- 来源:上海申岢动平衡机制造有限公司
- 发布时间:2025-03-26
- 访问量:107
在高速旋转机械领域,微米级的振动偏差足以引发灾难性后果。某型号航空发动机曾因主轴失衡导致试车失败,经检测振动幅值仅超出标准值3%,这个案例揭示了旋转机械动态平衡的重要性。作为精密制造领域的核心技术装备,主轴动平衡机正在重塑现代工业的质量标准体系。
一、动态平衡技术的核心价值
机械主轴在每分钟数万转的高速运转中,0.1克的质量偏差就会产生数百牛顿的离心力。这种微观失衡会导致轴承过热、密封失效、噪音超标等问题,严重时可能引发设备解体。动态平衡校正可将残余不平衡量控制在毫克级别,使振动幅度降低90%以上。
精密制造领域对平衡精度的要求持续提升。半导体制造设备主轴要求平衡等级达到G0.4级,相当于每公斤转子允许的残余不平衡量不超过0.4克·毫米。风电主轴则需要在装配现场完成百吨级转子的在线动平衡,确保20年使用寿命周期内的稳定运行。
二、智能平衡系统的技术突破
现代动平衡机采用激光相位检测技术,分辨率达到0.1μm级位移量。多通道振动传感器阵列可同时采集XYZ三轴向振动数据,结合有限元分析建立的转子动力学模型,实现亚微米级的平衡校正。
智能化补偿系统开创了新的技术维度。基于机器学习算法,设备可自主识别转子类型,记忆历史校正数据,自动优化配重方案。某汽车传动轴生产企业引入智能系统后,单件校正时间缩短40%,材料损耗降低25%。
工业物联网技术实现远程监控与预测性维护。通过振动频谱分析,系统可提前30天预警轴承磨损趋势,结合数字孪生技术模拟不同工况下的设备状态,使维护周期从季度级提升至实时监控。
三、行业应用的技术革新
在新能源装备制造中,8MW海上风电主轴的现场动平衡成为技术突破点。工程师开发出模块化配重系统,可在百米高空完成直径4.2米转子的配重调整,将传统需要返厂维修的工期从45天压缩至现场3小时完成。
精密机床领域正在经历静压主轴革命。采用气体静压轴承的主轴转速突破20万转/分钟,其平衡精度要求达到纳米级。新型非接触式测量技术配合主动电磁补偿装置,使残余振动控制在50nm以内,满足超精密加工需求。
微型化设备带来新的技术挑战。医疗微型电机转子直径仅1.2mm,传统动平衡方法完全失效。微机电系统(MEMS)平衡技术应运而生,通过离子束刻蚀实现μg级质量修正,将微型电机的使用寿命延长3倍以上。
随着磁悬浮轴承、智能材料等新技术的发展,动平衡技术正在突破物理修正的局限。自平衡转子系统通过实时应力感知和形状记忆合金调节,预示着一个零振动机械时代即将来临。这种技术演进不仅改变着制造标准,更在重塑整个精密机械工业的生态体系。
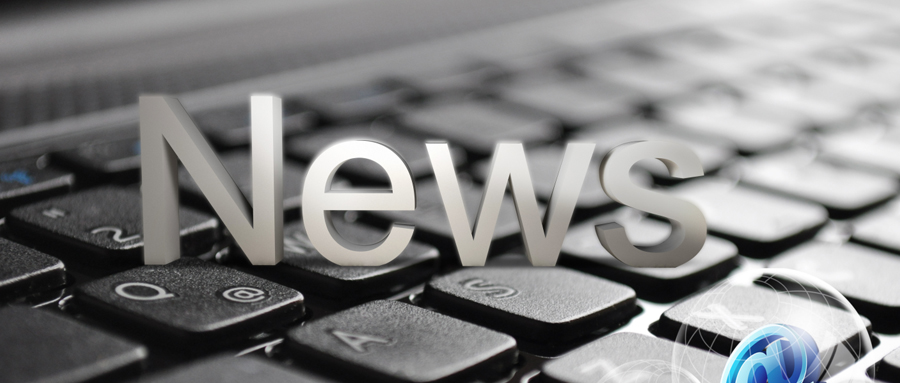