

光针找点动平衡技术:精密制造的隐形守护者
- 分类:行业新闻
- 作者:申岢编辑部
- 来源:上海申岢动平衡机制造有限公司
- 发布时间:2025-03-26
- 访问量:72
在现代化工业生产线上,一台台高速旋转的金属部件正接受着肉眼不可见的精密检测。当航空发动机转子以每分钟万转的速度飞旋,当精密机床主轴进行纳米级加工时,光针找点动平衡技术正以光子为笔,在旋转机械的振动谱线上描绘着平衡的轨迹。这项融合了光学传感与智能算法的尖端技术,正在重塑工业制造的质量标准。
一、光学传感开启平衡检测新纪元
传统动平衡检测依赖机械式传感器采集振动数据,犹如盲人摸象般难以捕捉完整的运动状态。光针找点技术采用非接触式光电检测系统,通过高精度激光束在旋转部件表面形成动态光斑阵列。当转子出现质量偏心时,这些光子探针能实时捕捉0.1微米级的形变位移,其灵敏度相当于在百米外检测头发丝的摆动幅度。
多光谱成像技术的应用让检测维度产生质的飞跃。系统能同时获取旋转部件的三维形貌、表面应力分布和温度场数据,构建出多维度的动态平衡模型。这种全息化的检测方式,使得隐藏的微观缺陷无所遁形,即便是纳米级的材料不均匀性也能被精准定位。
智能算法的引入将检测效率提升至新高度。自适应滤波技术能有效剔除环境干扰,深度学习网络通过百万级样本训练,可在0.3秒内完成传统方法需要数分钟的计算分析。这种实时反馈能力,让平衡校正从离线检测转变为在线监控。
二、动态平衡的智能化实现
在汽车轮毂生产线上,智能平衡系统正展现惊人效率。当工件进入检测工位,32束定位激光瞬间完成空间坐标标定,高帧频CMOS传感器以每秒20万次的速度采集振动频谱。系统自动识别轮毂的安装偏角,动态补偿夹具误差,将检测精度控制在0.01g·mm级别。
振动频谱解析技术突破传统配重计算的局限。系统不仅能给出精确的配重位置和重量,还能预测不同转速下的振动演变趋势。在精密电机转子校正中,这种预测能力可将产品使用寿命提升30%以上,有效避免共振引发的隐性故障。
自学习校正系统持续优化工艺参数。每次检测数据都进入知识库,通过强化学习算法不断改进配重策略。某风电叶片制造商应用该系统后,单件平衡时间缩短58%,材料损耗降低42%,年节约合金材料达120吨。
三、技术突破带来的产业变革
在航空航天领域,涡轮转子平衡精度直接决定发动机寿命。某型号航空发动机采用光针找点技术后,振动烈度降低至原有标准的1/5,大修周期延长3倍。这种提升不仅意味着更安全的飞行,更代表着国产航发技术的重要突破。
新能源汽车行业正在经历静音革命。驱动电机采用新型平衡方案后,车内噪音降低12分贝,相当于将闹市环境转换为图书馆级别的静音效果。这种突破不仅提升驾乘体验,更为智能驾驶系统提供更纯净的声学环境。
随着工业4.0的深入发展,动平衡技术正与数字孪生深度融合。某智能工厂通过虚拟调试系统,在新产品试制阶段就能预测平衡特性,将研发周期压缩60%。这种数字优先的制造模式,正在重新定义精密制造的标准流程。
在高端装备制造领域,0.1微米的平衡误差可能决定着一个国家工业体系的高度。光针找点动平衡技术不仅填补了我国在超精密检测领域的多项空白,更推动着中国制造向质量效益型转变。当光子与金属的对话持续深入,这场关于旋转精度的微观革命,正在书写中国智造的新篇章。
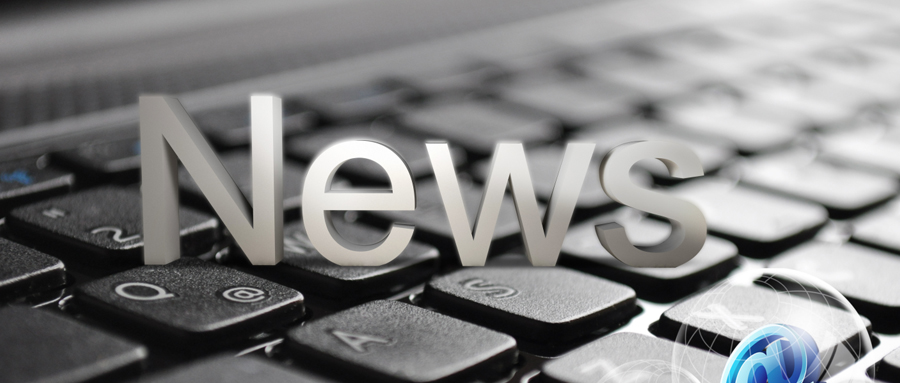