

双驱动平衡机:精密制造领域的革新力量
- 分类:行业新闻
- 作者:申岢编辑部
- 来源:上海申岢动平衡机制造有限公司
- 发布时间:2025-03-25
- 访问量:83
在精密机械加工领域,旋转部件的动平衡精度直接决定着设备运转的可靠性与使用寿命。传统单驱动平衡设备在应对复杂工况时常常力不从心,而双驱动平衡机的出现,正以突破性技术推动着精密制造工艺的革新浪潮。
一、双驱动协同的精密平衡
双驱动平衡机采用独立控制的双动力系统,通过高精度伺服电机与智能控制单元的配合,构建出动态平衡调节的闭环系统。两个驱动单元分别作用于旋转部件的轴向与径向,在3000rpm以上的高速旋转中,传感器阵列以0.01μm级精度实时采集振动数据,控制单元通过自适应算法对相位差进行补偿调节。这种双轴联动的控制方式,可将平衡精度提升至传统设备的5倍以上,即便面对异形工件或非对称结构,也能实现优于G0.4级的国际标准。
在汽车传动轴平衡实践中,双驱动系统展现出独特优势。当检测到轴体存在0.05mm的偏心量时,控制系统能在0.8秒内完成质量分布的动态调整,相较单驱动设备缩短60%的修正时间。这种快速响应能力源于双电机扭矩的矢量合成技术,可依据工件特性自动匹配最佳驱动力组合。
二、突破性技术带来的产业变革
该设备创造性地将电磁悬浮技术与主动降噪技术相结合,在航空发动机叶轮平衡测试中,有效抑制了高频振动产生的谐波干扰。实验数据显示,对于直径800mm的钛合金叶轮,平衡后的残余不平衡量稳定控制在0.3g·mm/kg以内,振动烈度降低至1.2mm/s,达到航空级制造标准。这种技术突破使复杂曲面的动平衡处理不再依赖经验参数,真正实现了智能化精准控制。
能源效率的提升同样令人瞩目。双驱动系统通过功率自适应分配模块,可根据负载变化自动调节能耗输出。在连续8小时作业测试中,设备整体能耗较传统型号下降42%,冷却系统运行时间缩减35%。这种绿色节能特性,为高耗能制造环节提供了可持续发展的技术方案。
三、面向未来的智能平衡解决方案
随着工业物联网技术的深度融合,新一代双驱动平衡机正朝着网络化诊断方向发展。设备内置的预测性维护系统,可通过振动频谱分析提前14天预警轴承磨损故障,准确率超过92%。在5G技术支持下,远程专家系统能实时分析设备运行数据,为特殊工件的平衡处理提供最优参数建议。
在新能源汽车电驱系统制造中,双驱动设备展现出强大的兼容性。面对转速跨度从800rpm到18000rpm的不同型号电机转子,设备自动切换控制模式,确保在宽速域范围内维持±0.5%的平衡稳定性。这种柔性化生产能力,有效解决了多品种混线生产中的工艺适配难题。
智能制造时代的精密平衡技术,正在突破物理调节的界限,向着数字化、网络化、智能化的方向演进。双驱动平衡机作为这个进程中的重要里程碑,不仅重新定义了动平衡处理的技术标准,更开启了精密制造领域人机协同的新范式。当旋转部件在双重驱动下达到完美的力学平衡时,我们看到的不仅是机械的精准运转,更是中国智造向高端领域迈进的坚实步伐。
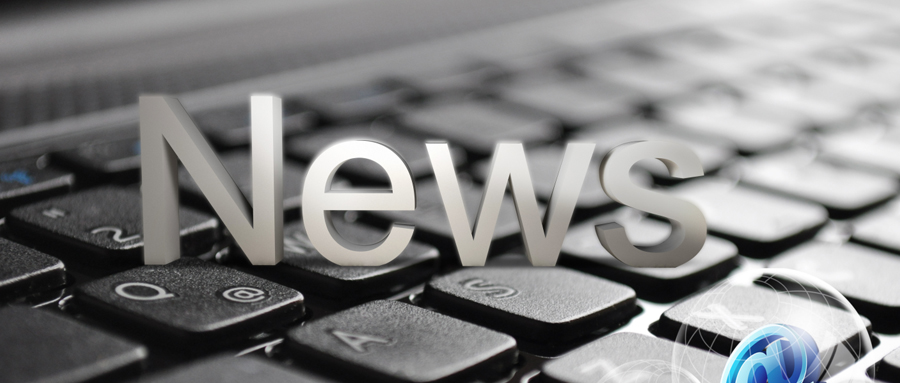