

叶轮动平衡机校准:精密机械的无声守护者
- 分类:行业新闻
- 作者:申岢编辑部
- 来源:上海申岢动平衡机制造有限公司
- 发布时间:2025-03-25
- 访问量:85
在高速旋转机械领域,叶轮动平衡机的校准精度直接决定着关键设备的命运。当航空发动机以每分钟数万转的速度切割空气,当巨型离心压缩机在石化装置中持续运转,支撑这些设备平稳运行的核心技术,正是隐藏在背后的动平衡校准体系。这项看似简单的技术,实则是现代工业文明的精密基石。
一、平衡校准的技术本质
任何旋转体都存在质量分布不均的先天缺陷,这种微观层面的不平衡在高速旋转时会引发几何级数增长的离心力。精密校准的本质就是通过数学建模将这种不平衡量控制在允许范围内。工程实践中,技术人员运用傅里叶变换对振动信号进行频谱分析,精确锁定不平衡相位,通过配重计算建立三维平衡方程,这个过程需要同时考虑旋转体结构强度、材料特性及工作环境等多重变量。
现代动平衡校准已发展出激光对中、相位跟踪等先进技术,传感器系统能够实时捕捉0.1微米级的振动变化。双平面动态平衡法通过建立空间向量模型,可同时消除静不平衡和动不平衡,使校正精度达到毫克级。这些技术突破使得现代叶轮的平衡精度比二十年前提升了两个数量级。
二、校准工艺的实践密码
校准前的设备状态诊断如同精密手术前的全面体检。技术人员需检查传感器线性度误差是否在0.5%以内,验证驱动系统的同轴度偏差不超过2μm,确认环境振动值低于ISO标准规定的背景值。温度补偿模块需要根据材料热膨胀系数进行预设,这对高温工况下的燃气轮机叶轮尤为重要。
动态参数设定阶段需要输入精确的几何尺寸数据,包括叶轮直径、轴系刚度、支撑跨距等26项关键参数。相位基准的确定要求使用激光定位装置反复验证,角度误差必须控制在±0.5°以内。配重执行环节中,质量块的安装必须遵循矢量叠加原理,采用数控加工确保配重孔的定位精度达到0.01mm。
校准验证流程包含空载测试和模拟负载测试双重验证。技术人员通过Bode图分析系统共振频率,使用瀑布图观察不同转速下的振动特性。完整的测试数据包需记录包括初始不平衡量、校正量、残余振动值等58项参数,这些数据将构成设备运行的终身档案。
三、精度控制的工程哲学
在微观尺度上,0.1克的配重偏差可能导致百米外检测到异常振动。这种蝴蝶效应要求工程师建立全生命周期的精度管理思维。某核电站主冷却泵的案例显示,经过三次迭代校准后,轴承寿命从8000小时延长至24000小时,验证了精度控制的倍增效应。
动态平衡标准的进化史印证着工业文明的进步。从最初的静态平衡到现在的全息动平衡,允许残余不平衡量标准每十年下降一个数量级。正在研发的量子平衡仪有望突破现有物理极限,利用超导技术实现纳米级平衡控制,这将是旋转机械领域的又一次革命。
精密校准创造的隐形价值远超直观认知。研究表明,叶轮平衡精度提升1个等级,可使整机能效提高3%-5%,维护周期延长40%。在十年生命周期中,这种改进可节约的能源成本相当于初始投资的12倍,这种隐性收益正是现代工业追求极致精度的核心动力。
在这个追求极限精度的时代,叶轮动平衡校准已超越单纯的技术范畴,演变为衡量工业文明高度的标尺。每一次校准数据的记录,都是对机械生命的郑重承诺;每微克配重的精确调整,都在续写人类驾驭旋转力量的智慧篇章。当超级计算机与量子传感器赋能传统校准技术,我们正在见证机械精密度的又一次维度跨越,这场无声的技术革命将持续推动工业文明向更高维度演进。
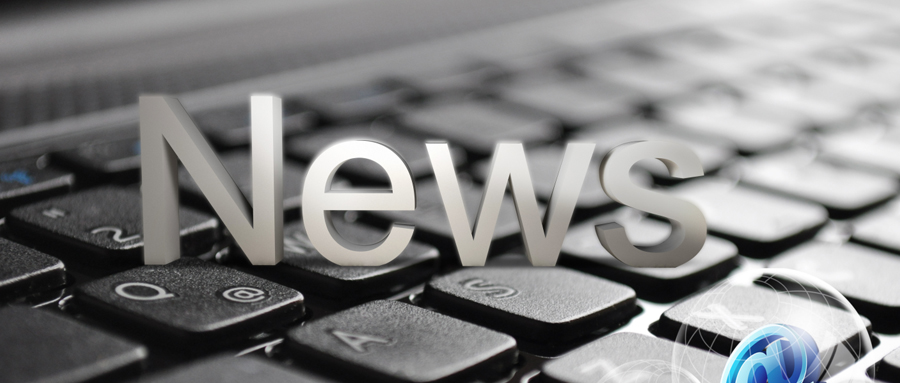