

带叶轮的电机转子动平衡技术解析
- 分类:行业新闻
- 作者:申岢编辑部
- 来源:上海申岢动平衡机制造有限公司
- 发布时间:2025-03-24
- 访问量:93
在机电设备领域,带叶轮的电机转子动平衡是保证设备平稳运行的核心技术。当高速旋转的转子系统存在质量分布不均时,会产生周期性离心力,这种不平衡力不仅会引起设备振动和噪音,更会加速轴承磨损,严重时甚至引发机械故障。针对这类特殊转子的平衡校正,需要采用科学的工艺方法和技术手段。
一、动平衡失衡机理分析
叶轮与转子的复合结构存在多个质量分布点,其不平衡量往往呈现空间分布特征。当转子以角速度ω旋转时,即使微小的质量偏心也会产生F=mω²r的离心力。例如直径300mm的叶轮,在3000rpm转速下,10g的偏心质量可产生约150N的动态载荷。
安装误差是引发动平衡问题的重要因素。叶轮与转子的装配同轴度偏差超过0.05mm时,就会造成明显的二阶振动分量。实际案例显示,某离心风机因叶轮定位销磨损导致的0.12mm径向偏差,使整机振动速度值从2.8mm/s激增至8.5mm/s。
材料缺陷对动平衡的影响具有隐蔽性。铸造叶轮的壁厚差异超过设计值5%时,即使经过初平衡校正,在高速运转时仍会出现动态变形。某型号水泵叶轮在超速试验中,因铸造残余应力释放导致的0.3mm变形,使平衡等级从G6.3降级至G16。
二、动平衡校正实施方法
双面动平衡法是处理叶轮转子的标准工艺。通过在两个校正平面(通常位于叶轮两侧)添加或去除质量,可有效消除静不平衡和偶不平衡。实验数据表明,采用ISO1940标准G2.5平衡等级时,残余不平衡量应控制在U=9549·G·m/(n)以内,其中m为转子质量(kg),n为工作转速(rpm)。
现场动平衡技术解决了传统方法的局限性。使用便携式振动分析仪,通过三次试重法可快速确定校正质量和相位。某污水处理厂曝气机采用此方法,在不停机情况下将振动值从7.1mm/s降至1.8mm/s,校正精度达到0.5g·mm/kg。
激光去重法代表了精密平衡的发展方向。采用数控激光设备在特定位置进行材料烧蚀,可实现±0.1g的质量修正精度。对比传统钻孔去重法,这种方法可使叶轮强度保持率提高15%以上,特别适用于钛合金等难加工材料。
三、动平衡工艺优化要点
平衡前的预处理工序至关重要。包括:使用三坐标测量仪检测叶轮型线偏差,控制在±0.1mm以内;采用磁粉探伤检查轮毂裂纹;使用加热炉进行时效处理消除残余应力。某压缩机组大修时,通过预处理使后续平衡效率提升40%。
平衡转速的选择需要遵循1:1原则。对于工作转速在5000rpm以下的转子,动平衡转速应等于工作转速;超高速转子可采用80%额定转速进行平衡。特别注意临界转速区的避让,通常要求平衡转速避开临界转速的±15%范围。
校正量分配需要综合考虑结构特性。对于悬臂式叶轮,建议按3:7比例分配前后平面的校正量;双支撑结构则采用1:1分配。使用有限元分析软件进行模态仿真,可优化配重位置,避免引发新的共振问题。
随着智能制造技术的发展,动平衡工艺正在向智能化方向演进。采用机器视觉自动识别叶轮标记点,结合AI算法优化配重方案,可使平衡效率提升3倍以上。未来,数字孪生技术的应用将实现虚拟平衡与实际操作的深度融合,为精密制造开辟新的可能。在实际操作中,工程人员需要根据具体工况灵活运用各种平衡方法,同时建立完整的质量追溯体系,确保每个校正环节都达到工艺标准要求。
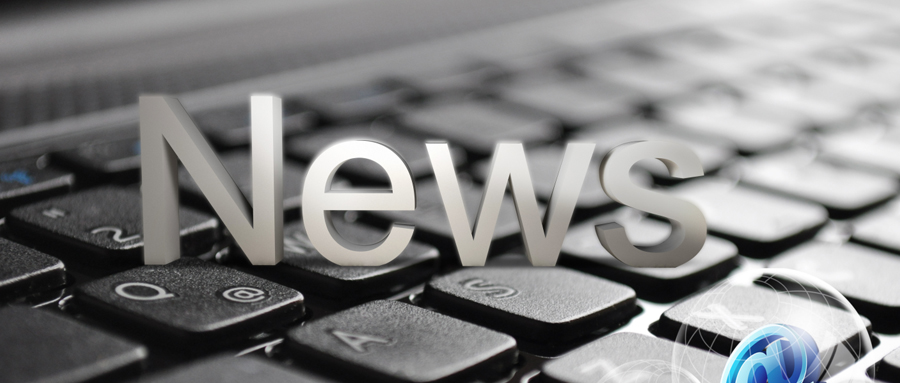