

旧动平衡机升级改造:让传统设备焕发智能新生
- 分类:行业新闻
- 作者:申岢编辑部
- 来源:上海申岢动平衡机制造有限公司
- 发布时间:2025-03-21
- 访问量:140
在智能制造浪潮席卷全球的今天,众多企业车间里服役多年的动平衡机正面临新的机遇。这些见证工业发展历程的”老兵”,虽机身沉稳依旧,却因核心部件老化、检测精度衰减等问题逐渐显露疲态。面对产业升级压力,通过系统性技术改造唤醒设备潜能,已成为工业企业提质增效的重要突破口。
一、传统动平衡机的技术瓶颈
机械式动平衡机普遍采用模拟量传感器采集振动信号,这类接触式测量装置存在零点漂移、抗干扰能力弱等固有缺陷。某汽配企业实测数据显示,使用超过10年的设备测量重复性误差可达±8g·mm,超出新设备标准值3倍以上。传统设备的数据处理单元多基于单板机架构,运算速度仅能支持简单滤波算法,面对复杂工况时平衡修正方案往往不够精准。
操作界面的数字化程度不足是另一个显著痛点。某风电设备制造商的技术人员反馈,老式设备的机械式仪表盘读数误差率高达5%,且参数设置依赖物理旋钮调整,每次换型需耗费30分钟重新校准。更关键的是,这些设备缺乏数据存储功能,难以追溯历史检测记录,制约着产品质量的持续改进。
二、智能化改造的技术路径
传感器升级是改造工程的首要环节。将原有的机械式振动传感器替换为MEMS数字传感器,配合激光位移测量模块,可将采样频率提升至20kHz级别。某改造案例显示,这种复合传感方案使相位检测精度从±3°提升至±0.5°,有效解决了叶轮类复杂构件的平衡难题。数据处理系统采用嵌入式工控平台,搭配专用信号处理芯片,运算速度较传统设备提升20倍以上。
智能化改造的核心在于软件算法创新。通过引入机器学习模型,系统能自动识别不同转子的振动特征谱,智能推荐最优配重方案。某压缩机生产企业实测数据显示,AI算法的应用使平衡效率提升40%,材料损耗降低15%。人机交互界面的升级同样关键,10英寸工业级触摸屏配合图形化操作界面,使设备调试时间缩短70%。
三、改造升级的价值维度
经改造的设备测量精度可恢复至出厂标准的90%以上,某汽车传动轴生产线的实测数据表明,产品动平衡合格率从改造前的86%提升至98.5%。能耗表现方面,升级后的永磁电机驱动系统较传统异步电机节能30%,设备整体功耗下降25%,年节约电费超过8万元。
设备兼容性扩展带来显著经济效益。通过增加模块化夹具系统和多协议通信接口,同一设备可兼容加工直径200-1200mm的各类转子,设备利用率提升60%以上。数据管理系统的升级实现了检测数据云端存储,质量追溯响应速度从小时级缩短至分钟级,为工艺优化提供数据支撑。
站在工业4.0的门槛回望,动平衡机的智能化改造不仅是设备本身的涅槃重生,更是传统制造向智能制造跃迁的微观写照。这种以最小资源消耗获取最大效益提升的技术路径,正在重新定义工业设备的全生命周期价值。当最后一台机械仪表完成数字化蜕变,我们看到的不仅是车间里焕然一新的设备阵列,更是一个产业在转型升级中的智慧觉醒。
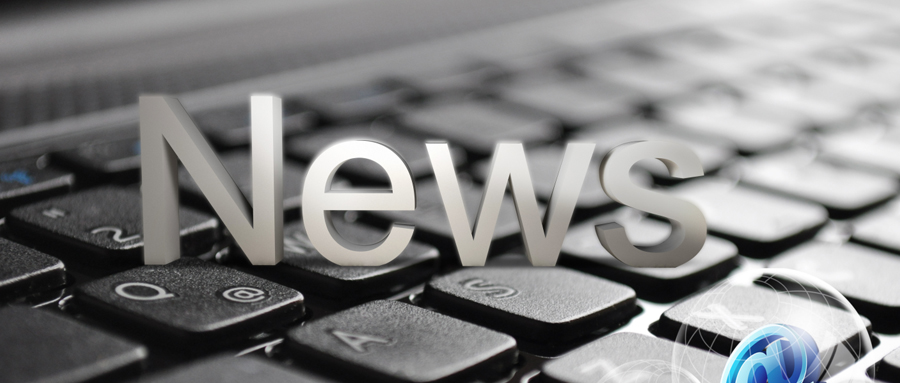