

曲轴动平衡机制造:精密机械背后的核心技术
- 分类:行业新闻
- 作者:申岢编辑部
- 来源:上海申岢动平衡机制造有限公司
- 发布时间:2025-03-21
- 访问量:85
在发动机的核心部件中,曲轴犹如精密的人体骨骼,承担着将活塞往复运动转化为旋转动力的关键使命。这个长度可达数米的金属构件,其质量分布均匀程度直接影响着整机的运行效能。制造环节中0.01克级别的质量偏差,在每分钟数千转的高速运转下,会产生数百公斤的离心力,这种力量足以引发设备振动、噪音加剧甚至结构损伤。确保曲轴的动态平衡性能,成为动力机械制造领域不可忽视的技术挑战。
一、精密制造的工艺革命
现代动平衡检测设备采用非接触式激光测量系统,通过高灵敏度的振动传感器阵列,能够在曲轴旋转过程中实时捕捉三维空间的振动频谱。先进的相位分析算法可将检测精度提升至毫克级,相当于在十米长的钢构件上找出相当于一粒细沙的质量偏差。全自动校正系统搭载五轴联动加工单元,根据检测数据自动计算配重方案,通过精密铣削或增材配重的方式,实现微米级的质量补偿。
智能化控制系统整合了工业物联网技术,每台设备可存储上千种曲轴型号的工艺参数。自适应学习功能使设备能够根据实时加工数据动态优化切削参数,确保不同材质工件都能达到最佳平衡效果。云端数据管理平台实现生产全流程追溯,每个工序的检测数据自动生成三维质量图谱,为工艺改进提供可视化支持。
二、技术创新的多维突破
双面立式平衡技术突破传统卧式布局限制,采用对称式支撑结构将检测效率提升40%。模块化设计允许设备根据工件尺寸快速更换工装夹具,转换时间缩短至15分钟以内。针对新能源领域开发的复合平衡系统,可同时处理曲轴与电机转子的耦合平衡问题,满足混合动力系统的特殊需求。
核心驱动系统经历革命性升级,永磁同步伺服电机替代传统异步电机,扭矩波动系数降低至0.5%以下。主动式空气弹簧隔振平台将环境振动干扰衰减90%,确保检测过程不受外界因素影响。纳米级表面处理技术应用于传感器接触面,使信号传输稳定性提升三个数量级。
三、行业发展的未来图景
新一代设备集成机器视觉系统,通过深度学习算法自动识别工件表面缺陷。三维扫描建模技术可在平衡修正前预判结构强度,避免过度切削导致力学性能下降。远程诊断系统运用数字孪生技术,实时监控全球范围内设备的运行状态,提前预判维护周期。
绿色制造理念推动设备向节能方向进化,再生制动系统可回收80%的制动能量。低耗能主轴单元采用陶瓷混合轴承,摩擦损耗降低至传统结构的1/3。环保型切削液循环系统实现零废水排放,处理后的金属碎屑可直接回收利用。
在工业4.0时代背景下,曲轴动平衡技术正在经历从精密机械向智能系统的跨越式发展。制造企业通过持续的技术迭代,不仅提升了动力机械的可靠性,更推动了整个装备制造业向高效、智能、环保方向转型升级。这种变革正在重塑传统制造模式,为高端装备的国产化进程注入新动能。
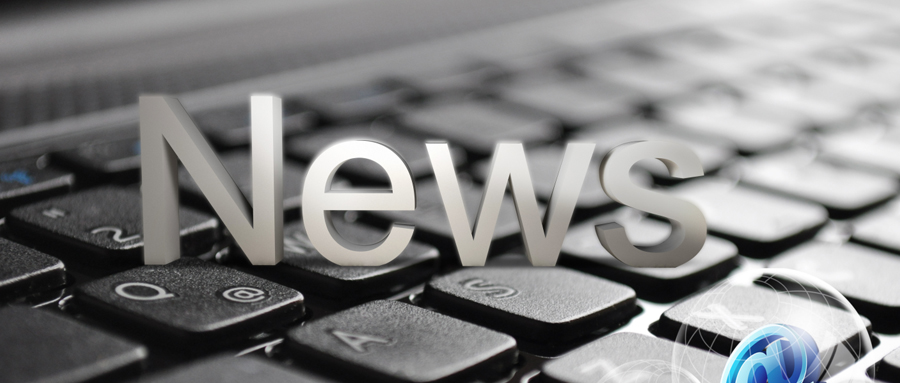