

汽轮机转子动平衡技术:工业心脏的精密调律
- 分类:行业新闻
- 作者:申岢编辑部
- 来源:上海申岢动平衡机制造有限公司
- 发布时间:2025-03-20
- 访问量:112
在现代化火力发电厂轰鸣的汽轮机舱内,一台重达200吨的汽轮机转子正以每分钟3000转的速度高速旋转,其轮缘线速度突破音速,表面温度超过600℃。这样的庞然大物要实现稳定运行,关键在于转子的动平衡精度必须控制在微米级——这个数值仅是头发丝直径的百分之一。汽轮机转子动平衡机正是实现这一工程奇迹的核心装备,它如同一位技艺高超的调音师,为工业心脏奏响完美乐章。
一、动力之源的平衡奥秘
汽轮机转子的失衡问题源于复杂的物理本质。当转子质量分布与几何中心轴存在偏差时,旋转产生的离心力会在轴承系统形成周期性激振力。这种微小至数克的不平衡量,在高速旋转状态下会被几何级数放大。以1000MW超临界机组为例,1克的质量偏心在3000rpm时产生的离心力相当于300公斤静载荷,足以引发轴承系统剧烈振动。
现代动平衡机采用复合传感技术,通过高精度振动传感器与相位检测系统的协同工作,能够捕捉纳米级振动信号。先进的数字滤波算法可以从复杂的背景噪声中分离出有效振动分量,其灵敏度相当于在百米外检测到一枚硬币落地的震动。动态补偿系统通过三维建模实时计算配重方案,误差控制达到微牛·米量级。
在核电站主泵转子动平衡案例中,技术人员采用热态平衡技术,在模拟实际工况的真空高温环境下,成功将残余不平衡量控制在0.5g·mm/kg以内,振动幅值降至25μm以下,为机组安全运行提供了可靠保障。
二、技术革新的进化之路
早期动平衡采用静态平衡法,通过在重力场中寻找质心的原始方法,精度仅能达到克级。随着激光干涉测量技术的引入,动平衡精度提升了三个数量级。现代全自动平衡机集成工业机器人技术,实现了从测量、计算到修正的闭环控制,单次平衡时间缩短至传统方法的1/5。
智能化技术的突破彻底改变了动平衡领域。基于深度学习的振动模式识别系统,能够自动诊断转子故障类型,准确率超过98%。数字孪生技术构建的虚拟平衡系统,可在实际修正前预测平衡效果,减少试重次数达70%。某型燃气轮机转子的智能平衡系统,通过大数据分析优化配重方案,使平衡效率提升40%。
在航空发动机领域,自适应平衡技术取得重大突破。采用形状记忆合金制作的智能配重块,能够根据转速自动调整质量分布,实现全工况范围内的动态平衡。这种技术将高压涡轮转子的振动值降低了60%,显著提升了发动机使用寿命。
三、极限工况下的平衡挑战
超临界二氧化碳循环系统转子的平衡面临极端工况考验。在700℃高温和25MPa超临界压力下,传统配重材料会发生蠕变失效。科学家研发出陶瓷基复合配重块,其耐温性能突破1000℃,同时保持优异的尺寸稳定性。磁流体平衡技术的应用,实现了非接触式动态补偿,特别适用于微型燃气轮机转子的在线平衡。
复合材料的广泛应用带来了新的平衡难题。碳纤维增强转子的各向异性特征,使得传统平衡理论不再适用。研究人员建立了基于材料各向异性的平衡模型,开发出多自由度补偿算法。在新型海上风电增速箱的碳纤维转子平衡中,该技术成功将振动烈度控制在2.8mm/s以内。
微型化趋势对平衡技术提出新要求。微型燃气轮机转子直径仅50mm,转速却高达120000rpm。微机电系统(MEMS)平衡装置应运而生,采用压电陶瓷驱动器实现纳米级质量补偿,平衡精度达到0.01mg·mm,相当于在米粒上精确调整百万分之一的重量分布。
站在工业4.0的门槛上,汽轮机转子动平衡技术正在向智能化、自适应方向发展。量子传感技术的突破将测量精度推向新高度,超材料配重装置有望实现动态质量重构。当智能制造遇上极端工程,动平衡技术将继续突破物理极限,为人类文明提供更强大、更可靠的动力之源。在这个精密与力量交织的领域,每一次技术突破都在重新定义工业制造的精度边界。
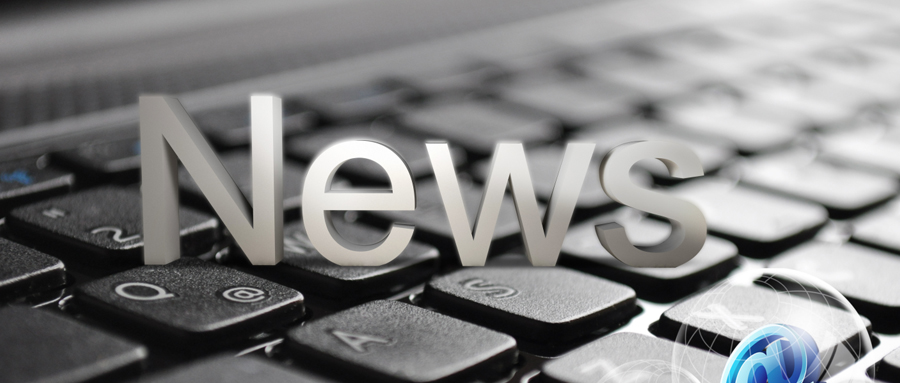