

激光找点动平衡机:精密制造的平衡艺术
- 分类:行业新闻
- 作者:申岢编辑部
- 来源:上海申岢动平衡机制造有限公司
- 发布时间:2025-03-20
- 访问量:86
在高速旋转的工业世界里,微米级的失衡足以引发灾难性后果。当传统动平衡技术遭遇精度瓶颈时,激光找点动平衡机以革命性姿态登场,凭借激光的精准穿透力,为旋转机械的平衡校正开辟了全新维度。这种融合了光电检测与智能算法的先进设备,正在重新定义精密制造的精度标准。
一、激光测控的物理革命
传统动平衡技术依赖接触式传感器采集振动信号,在高速旋转场景中易受电磁干扰和机械振动影响。激光找点系统采用非接触式测量原理,通过多束激光构成的立体监测网络,能够以0.1μm的精度捕捉转子的三维振动轨迹。当转子转速达到每分钟数万转时,激光相位干涉仪仍可稳定追踪表面特征点的位移变化,形成精准的振动矢量图谱。
动态平衡算法在激光数据加持下实现突破性进化。系统通过傅里叶变换将时域信号转换为频域特征,结合转子材料的弹性模量和惯性参数,建立多自由度动力学模型。这种智能算法可在30秒内完成传统设备需要5分钟才能完成的数据处理,且平衡精度提升3个数量级。
相较于机械配重块的物理校正方式,激光系统开创了数字化配平新纪元。高能脉冲激光可在钛合金表面实现纳米级烧蚀,通过材料去除法完成质量补偿。这种无接触加工方式彻底消除了传统配重块带来的附加离心力干扰,特别适用于微小型精密转子的平衡修正。
二、工业场景的精准赋能
在微电机生产线上,直径不足5mm的微型转子对动平衡要求达到毫克级。激光找点系统凭借其亚微米级分辨率,成功解决了手机振动马达的寿命难题。某智能穿戴设备制造商引入该技术后,产品故障率下降82%,平均使用寿命延长3倍,创造了显著的商业价值。
航空航天领域见证了这项技术的极致应用。涡轮发动机叶片在1500℃工作环境下,需要承受自身重量10万倍的离心力。激光动平衡系统通过高温视窗进行在线监测,配合耐高温陶瓷材料的激光修正工艺,使航空发动机的维护周期从200小时延长至2000小时。
能源装备领域获得突破性进展。某核电站的主循环泵采用激光动平衡技术后,振动值从8mm/s降至0.5mm/s以下,设备运行噪音下降15分贝。这种静音化改进不仅提升了设备可靠性,更为工作人员创造了更安全的工作环境。
三、智能制造的进化方向
设备正在向全自动化方向演进。最新型号已集成机械臂自动上下料系统,配合视觉定位装置,可实现24小时无人化作业。当检测到转子不平衡量时,系统自动生成激光修正路径,整个过程无需人工干预,单件产品加工时间压缩至90秒以内。
云端协同平台的出现打破了设备孤岛。多台激光动平衡机通过工业物联网连接,实时上传检测数据至云端数据库。机器学习算法通过分析百万级样本数据,不断优化平衡参数,使系统具备自学习能力,校正精度随运行时间呈现指数级提升。
材料科学的进步推动技术边界持续扩展。针对碳纤维复合材料,科研人员开发出低温激光烧蚀工艺,在-50℃环境下仍能保持加工稳定性。石墨烯涂层的应用使激光修正表面粗糙度达到Ra0.02μm,满足光学镜面转子的苛刻要求。
在工业4.0的浪潮中,激光找点动平衡技术正从精密检测工具进化为智能制造的神经中枢。当激光束在旋转部件上描绘出精确的平衡轨迹时,我们看到的不仅是物理世界的完美平衡,更是人类追求极致精度的智慧闪光。这项技术将继续推动高端装备制造向着更精密、更智能、更可靠的方向发展,为现代工业体系注入持久的创新动力。
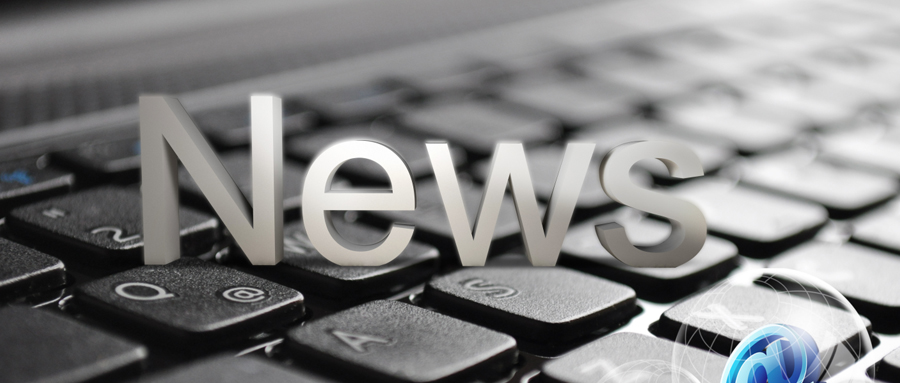