

砂轮动平衡校准:精密加工的核心保障
- 分类:行业新闻
- 作者:申岢编辑部
- 来源:上海申岢动平衡机制造有限公司
- 发布时间:2025-03-20
- 访问量:126
在高速旋转的砂轮系统中,直径超过200mm的砂轮转速可达每分钟6000转以上。这种极限运转状态下,0.1克的微小质量偏差就会产生超过20N的离心力。砂轮动平衡校准技术正是通过精准的质量分布调整,将这种破坏性力量控制在安全阈值内,成为现代精密加工领域不可或缺的关键技术支撑。
一、动平衡校准的物理本质
砂轮系统的动态不平衡源自材料密度差异、装配误差、磨损不均等多重因素。当旋转轴心与质量中心不重合时,离心力矢量会在轴承系统形成周期性冲击载荷。这种载荷具有谐波特征,其幅值随转速平方呈指数增长,在特定频率下可能引发设备共振。
动态平衡的数学本质在于建立三维坐标系下的质量矩平衡方程组。通过测量系统在特定相位上的振动矢量,构建包含不平衡量大小和方位的矩阵方程。现代动平衡仪可自动求解该方程,精确给出配重块的安装参数。
不平衡状态的危害具有渐进性特征。初期可能仅表现为加工表面波纹度异常,随着时间推移,轴承磨损加速会导致主轴温升异常,最终可能引发砂轮破裂等严重事故。某金属加工厂的数据显示,规范实施动平衡后设备故障率下降67%。
二、校准系统的技术演进
传统三点平衡法采用试重-测量的迭代调整模式,要求操作人员具备丰富的经验。操作者需在砂轮法兰三个等分位置依次添加试重,通过振动幅值变化计算校正质量。这种方法对操作环境要求较低,但调整周期长达40-60分钟。
智能化校准系统集成相位检测和自动计算模块,采用激光干涉仪进行非接触测量。最新设备可实时显示不平衡矢量的极坐标参数,通过触摸屏直接输入补偿方案。某实验数据显示,智能系统可将校准时间缩短至8-12分钟,精度提升至0.5g·mm级别。
特殊工况下的校准挑战主要来自极端环境。高温加工场景需采用耐热型传感器,湿式磨削环境需要防水设计的测量系统。对于组合式砂轮组件,需建立多自由度动力学模型,采用多点同步补偿技术实现整体平衡。
三、校准工艺的质量控制
预处理阶段必须完成砂轮的静平衡检测,确保初始不平衡量不超过允许值的70%。安装基准面的清洁度需达到Ra0.8μm以下,紧固螺栓的扭矩偏差应控制在±5%范围内。实践表明,规范的预处理可使校准效率提升30%以上。
补偿配重的安装需遵循矢量合成原则。当采用多组配重块时,其合成力矩应等于计算值的矢量和。对于树脂结合剂砂轮,建议使用专用粘接剂固定配重块,固化时间不少于30分钟。补偿后的残留振动值应小于ISO1940-1标准的G6.3级要求。
校准验证需在三个不同转速下进行全相位扫描测试。建议设置基准转速的80%、100%、120%三个测试点,验证系统在变速工况下的稳定性。某汽车零部件企业的数据表明,完整验证流程可使设备使用寿命延长40%。
随着智能制造技术的演进,砂轮动平衡校准正朝着在线监测方向发展。嵌入式传感器和预测性维护系统的结合,将实现加工过程中的实时平衡调整。这种技术突破不仅提升加工精度,更将设备维护模式从被动检修转变为主动预防,为精密制造领域带来革命性进步。规范化的校准流程配合先进的技术装备,正在重塑现代工业生产的质量基准。
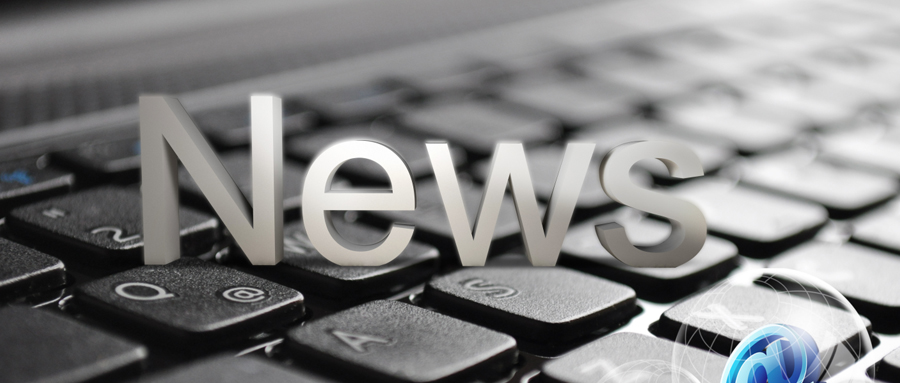