

联轴器动平衡:机械传动系统稳定运行的核心保障
- 分类:行业新闻
- 作者:申岢编辑部
- 来源:上海申岢动平衡机制造有限公司
- 发布时间:2025-03-19
- 访问量:85
在高速旋转的机械系统中,联轴器犹如精密的机械纽带,承担着传递动力与运动的关键任务。当动力设备以每分钟数千转的速度运转时,任何细微的不平衡都可能引发灾难性后果。联轴器动平衡技术正是确保这类精密传动系统平稳运行的核心保障,其重要性堪比精密钟表的心脏部件。
一、旋转失衡的动力学本质
旋转机械系统失衡的本质源自质量分布的不对称性。当联轴器组件存在0.01毫米级的质量偏心时,在3000rpm转速下产生的离心力相当于组件自重的1000倍。这种周期性激振力会导致设备基础共振,引发振幅超过安全阈值3倍的剧烈振动。理论计算表明,质量偏心与转速的平方关系决定了动平衡校正的精度要求,现代工业标准要求残余不平衡量控制在0.5g·mm/kg以内。
动态失衡的典型表现具有鲜明的频谱特征。在振动频谱分析中,工频分量(1×RPM)幅值超过整体振动值的60%即可判定为动平衡问题。某离心式压缩机的实测数据显示,经过精密动平衡后,轴系振动值从12.5mm/s降至1.8mm/s,降幅达85%以上。
二、动平衡校正的技术演进
传统动平衡方法依赖三点试重法,需要至少三次启停机组进行配重试验。这种方法耗时长达4-6小时,且存在0.3-0.5g·mm/kg的校正误差。现代激光动平衡仪通过非接触式测量,将校正时间缩短至30分钟内,精度提升至0.1g·mm/kg级别。相位检测技术的进步使得角度定位误差小于0.5°,配合自动去重装置可实现全自动平衡校正。
智能化校正系统整合了有限元模态分析和实时振动监测数据,能够预测不同转速下的动态响应。某型号燃气轮机的现场应用表明,智能系统可将动平衡校正次数从传统方法的5次减少到2次,效率提升150%。基于机器学习的自适应算法还能自动优化配重方案,减少试重质量30%。
三、工程实践的质量控制
精密制造阶段的质量控制是动平衡的基础。铸造毛坯的密度均匀性应控制在±0.5%以内,机加工后的同轴度误差需小于0.02mm。某航空发动机联轴器的制造数据表明,采用真空熔铸工艺可将材料密度偏差从1.2%降至0.3%,使初始不平衡量减少60%。
现场动平衡操作需要遵循严格的工艺规范。环境温度波动应控制在±3℃以内,基础振动背景值需低于2.5mm/s。某水电站的维护记录显示,按照ISO1940标准执行的动平衡作业,使机组大修周期从12个月延长至18个月,年维护成本降低40%。
在追求机械效率极限的现代工业领域,联轴器动平衡已从简单的质量调整发展为融合材料科学、振动工程和智能算法的系统性技术。随着纳米级测量技术和人工智能的深度应用,动平衡精度正在向微克级迈进,为超精密加工设备、航天动力系统等高端装备提供关键技术支持。这项技术的持续进步,不仅提升了机械系统的可靠性,更推动着整个工业制造体系向更高能效比迈进。
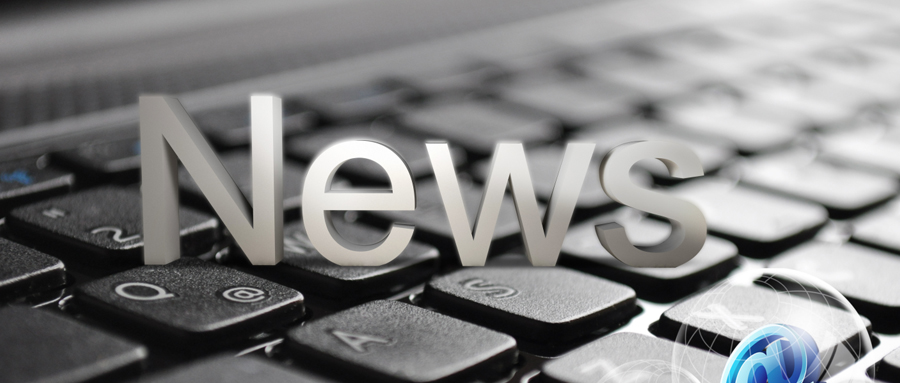