

车床加工动平衡:精密制造的隐形守护者
- 分类:行业新闻
- 作者:申岢编辑部
- 来源:上海申岢动平衡机制造有限公司
- 发布时间:2025-03-19
- 访问量:80
在高速旋转的车床加工场景中,一个直径为200mm的钢制飞轮以3000rpm运行时,仅需0.01mm的质量偏心就会产生超过500N的离心力。这个惊人的数字揭示了动平衡技术在精密加工中的核心价值,它不仅关乎加工精度,更是设备安全和生产效率的重要保障。
一、动失衡的物理本质与工程影响
旋转体质量分布不均会产生周期性离心力,这种动态失衡具有矢量叠加特性。当主轴转速接近系统固有频率时,失衡引发的振动会呈指数级放大。某航空发动机叶轮在动平衡缺失情况下,仅运行30分钟就导致主轴轴承温度飙升70℃,振动烈度超出安全阈值8倍,充分说明动平衡对设备保护的关键作用。
在精密车削加工中,动失衡引发的振动波纹会直接影响工件表面粗糙度。实验数据显示,G6.3级动平衡可使车削表面Ra值降低40%以上。对于高精度光学元件加工,动平衡等级需达到G0.4级别才能满足纳米级表面要求。
二、动平衡校正的技术体系
现代动平衡校正采用矢量分解原理,通过相位传感器捕捉振动信号,运用傅里叶变换分离各阶谐波分量。某大型电机转子采用三点校正法,通过矢量合成将残余不平衡量控制在0.5g·mm/kg以内,使整机振动速度降至1.2mm/s以下。
智能化校正系统集成激光测量与自动配重装置,可在加工过程中实时修正平衡状态。最新研发的在线动平衡模块响应时间缩短至0.1秒,使高速车削的振动幅度降低60%,加工效率提升25%。
复合材料工件的动平衡需考虑各向异性特征,采用分层补偿策略。碳纤维增强复合材料通过密度梯度配比设计,可使动平衡校正效率提升3倍。形状记忆合金在温控条件下的相位自调节特性,为智能动平衡提供了新思路。
三、动态平衡的精度控制实践
动平衡参数的工程计算需综合材料密度、几何尺寸及转速因素。对于非对称异形件,采用等效质量矩法进行模拟计算,配合三维扫描逆向建模,可将计算误差控制在±5%以内。某曲轴加工案例显示,基于应力分布仿真的动平衡优化使产品寿命延长30%。
现场动平衡校正需遵循ISO1940标准体系,建立从粗平衡到精平衡的多级校正流程。采用最小二乘法的迭代校正算法,通过三次配重即可将平衡精度提升至G1.0级别。校正过程中温度补偿机制的引入,可使系统稳定性提高40%。
质量补偿策略需考虑配重方式的物理特性。电磁配重系统可实现非接触式动态调整,特别适用于超精密加工场景。某半导体晶圆切割设备采用压电陶瓷微调机构,实现了0.01g级别的精准配重。
随着数字孪生技术的发展,动平衡控制正从被动校正转向主动预防。基于深度学习的振动预测模型,可提前3个加工周期预判平衡状态变化。未来,量子传感技术的应用有望将动平衡检测精度提升至原子量级,为极端制造领域开辟新的可能。在精密制造向亚微米级迈进的今天,动平衡技术将持续发挥其不可替代的核心作用。
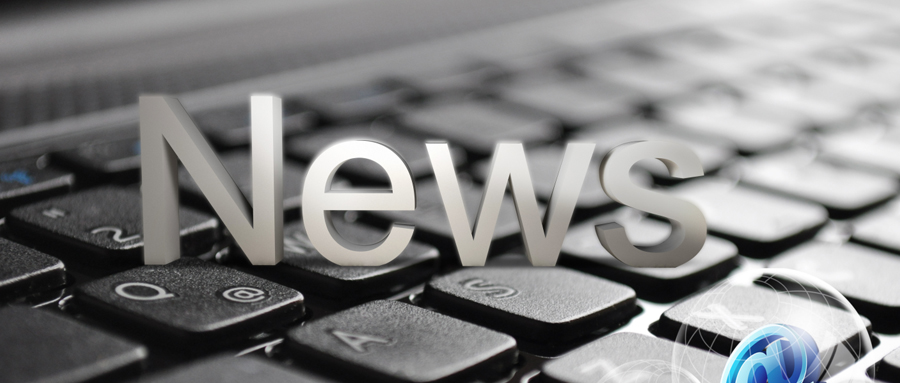