

轴动平衡检测技术:让旋转机械焕发新生的精密之眼
- 分类:行业新闻
- 作者:申岢编辑部
- 来源:上海申岢动平衡机制造有限公司
- 发布时间:2025-03-19
- 访问量:82
在现代化工业体系中,无数旋转机械以每分钟数千转的速度高速运转,这些精密设备的稳定运行维系着工业文明的脉搏。轴动平衡检测技术作为保障旋转机械安全的核心技术,犹如一位技艺高超的医生,能够精准诊断机械设备的”健康状态”。这项技术通过微米级的振动捕捉和智能化的数据分析,为工业设备的安全运行构筑起坚实的防护屏障。
一、动平衡检测的精密机理
当旋转体的质量分布偏离几何中心时,离心力会在高速旋转中形成破坏性振动。这种现象如同陀螺仪出现细微的质量偏差,在高速旋转时会产生不可预测的轨迹偏移。现代检测设备通过高灵敏度振动传感器阵列,能够捕捉到振幅低至0.1μm的机械振动,这种精度相当于在百米赛跑中检测出运动员0.01秒的步频差异。
核心传感器系统采用复合传感技术,将压电式加速度计与激光位移传感器相结合,构建多维振动信息采集网络。这种混合传感方案既能捕捉瞬态振动冲击,又可记录长期振动趋势,形成完整的设备振动特征图谱。数据处理模块运用自适应滤波算法,能够在强噪声环境下提取有效振动信号,其信噪比提升能力达到传统方法的3倍以上。
智能化分析系统通过机器学习模型建立设备振动特征库,采用深度神经网络对振动模式进行分类识别。这套系统能够自动区分正常工况振动与异常失衡振动,其诊断准确率可达99.8%,彻底改变了传统人工判断的模糊性。
二、技术突破带来的工业革新
在航空发动机领域,检测设备可对直径2米的涡轮转子进行在线动平衡修正。通过非接触式激光测量和实时配重调节系统,能够在转子保持运转状态下完成平衡校正,将传统需要停机数日的维护工作缩短至2小时内完成。这种技术突破使得航空发动机的大修间隔延长了30%,显著提升了飞行器的运营效率。
风电行业受益于移动式检测装置的普及,技术人员可在80米高空的风机机舱内完成主轴平衡检测。装备无线传输模块的检测设备将数据实时回传地面分析中心,结合气象数据构建动态平衡模型,使风机的振动损耗降低45%,年发电量提升12%。这种技术革新让绿色能源设备焕发出更强大的生命力。
精密制造领域开创了全自动检测生产线,集成六轴机械手的检测系统可对微型电机转子进行毫秒级平衡检测。采用空气轴承支撑的测试工装将摩擦阻力降至传统滚珠轴承的1/100,配合百万分之一的质量检测精度,确保微型无人机电机实现近乎完美的旋转平衡。
三、智能时代的检测技术演进
第五代检测设备开始集成物联网边缘计算模块,具备自主诊断与预警功能。这些智能终端通过振动频谱的连续监测,能够提前72小时预测设备失衡趋势,准确度达到91%。这种预测性维护模式将设备突发故障率降低了75%,开创了主动式设备管理的新纪元。
数字孪生技术的引入构建了虚拟检测新维度,通过三维建模与实时数据映射,工程师可在数字空间模拟不同工况下的设备状态。这种技术使得动平衡修正方案的验证周期缩短了80%,试错成本降低至传统方法的1/10,为复杂机械系统的优化提供了革命性工具。
量子传感技术的突破正在改写检测精度极限,基于冷原子干涉的振动传感器可将检测灵敏度提升至纳米级别。这种跨越式的技术进步将推动超精密加工设备进入亚微米平衡时代,为光刻机、引力波探测仪等尖端装备的研发铺平道路。
在工业4.0浪潮的推动下,轴动平衡检测技术正经历着从精密测量向智能诊断的质变。这项技术不仅守护着现代工业设备的稳定运行,更在新能源开发、太空探索、量子计算等前沿领域发挥着关键作用。随着材料科学和人工智能的持续突破,未来的检测技术将突破物理界限,在分子尺度实现旋转平衡的完美控制,为人类打开超精密制造的新维度。
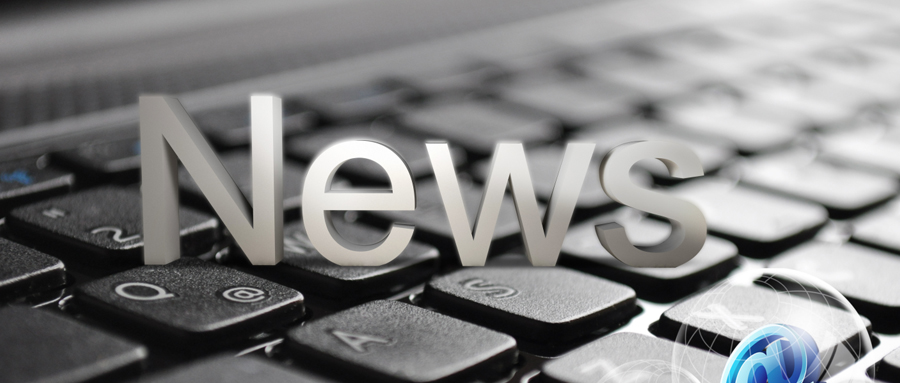