

风机叶轮动平衡校正技术解析
- 分类:行业新闻
- 作者:申岢编辑部
- 来源:上海申岢动平衡机制造有限公司
- 发布时间:2025-03-18
- 访问量:99
风机叶轮动平衡校正技术是保障旋转设备稳定运行的核心工艺,其校正精度直接影响设备寿命和运行效率。当叶轮质量分布不均时,高速旋转产生的离心力将引发强烈振动,这种振动不仅加速轴承磨损,更可能引发机械共振导致结构损坏。据工业现场统计数据显示,超过60%的风机异常停机事件与叶轮失衡直接相关。
一、动平衡异常成因分析
叶轮失衡主要源于制造装配误差与运行损耗两大因素。精密测量显示,铸造工艺导致的壁厚差异通常会产生0.5-3mm的质量偏差,这类细微差异在3000rpm转速下即可形成超过200N的动态不平衡力。运行过程中,粉尘颗粒的粘附堆积具有明显方向性特征,某电厂引风机叶轮实测数据表明,单侧积灰厚度达8mm时,振动值从2.1mm/s激增至8.7mm/s。
金属疲劳引发的叶片变形具有渐进性特征。某化工厂离心风机连续运行18000小时后,激光检测发现叶轮端面跳动量超差0.35mm,动平衡配重需增加至原始值的3倍。轴系配合间隙扩大形成的二阶振动具有频率时变特性,这种隐性失衡往往难以通过常规检测手段及时发现。
二、动平衡校正方法体系
单面平衡法适用于盘状转子的修正,其理论依据为静力学平衡方程Σmiri=0。实际操作中采用三点试重法,通过矢量分解确定配重相位角,精度可达ISO1940标准的G6.3等级。双面平衡法则运用矩阵方程解算力偶平衡,校正后残余不平衡量可控制在转子质量的0.1‰以内。
激光辅助动平衡系统通过多普勒效应实时捕捉叶轮形变,结合有限元分析构建三维质量补偿模型。某风场测试案例显示,该技术使校正效率提升40%,特别适用于海上风电等恶劣工况。智能化平衡仪内置DSP处理芯片,采用影响系数法自动生成配重方案,振动抑制效果较传统方法提升30%以上。
三、现场校正实施规范
预处理阶段需执行轴系对中检测,确保联轴器径向偏差小于0.05mm。振动传感器安装须遵循ISO10816标准,测点布置采用正交双通道模式,采样频率应大于旋转基频的8倍。相位标记装置需保证±1°的定位精度,对于防爆环境应选用光纤式编码器。
试重法实施时,建议选用叶轮质量0.2%-0.5%的试验配重块。影响系数法要求至少完成三次不同相位的试重测试,通过最小二乘法建立系统响应矩阵。某水泥厂风机校正记录显示,采用模态分离技术后,残余振动值从7.2mm/s降至1.5mm/s,达到ISO10816的B级振动标准。
风机叶轮动平衡校正已从经验作业转向精密控制工程,现代检测技术将校正精度推进至微米级。随着MEMS传感器的普及,嵌入式动态平衡系统可实现实时在线补偿。未来发展趋势显示,基于数字孪生的预测性平衡维护将彻底改变传统校正模式,使旋转设备可靠性提升至新的维度。运维人员需掌握频谱分析等先进诊断技术,建立全生命周期平衡管理体系,方能有效应对复杂工况挑战。
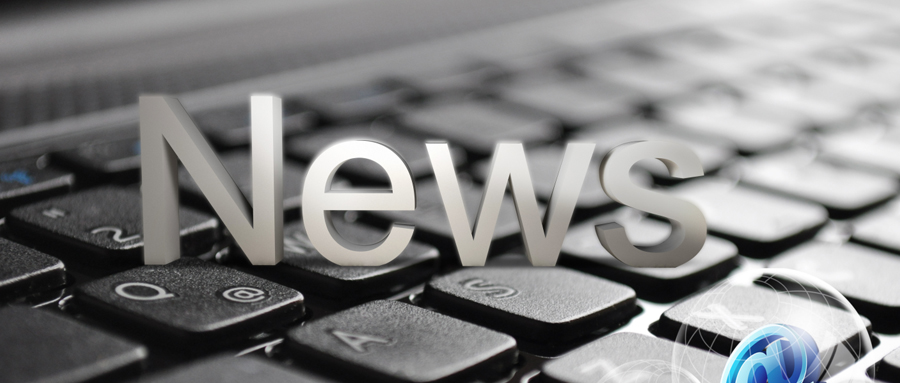